导读:通过添加元素或颗粒来促进增材制造的钛和钛合金的晶粒细化,脆性金属间化合物的形成会导致延展性降低。本研究通过适当控制选区激光熔化(SLM)参数来实现商业纯钛(CP-Ti)的原位晶粒细化。发现较高的输入能量密度有助于晶粒细化。这归因于SLM工艺固有的循环再加热导致的固有热处理(IHT)效果。制备的CP-Ti表现出34.3%的极高延展性。这项工作证明了利用增材制造(AM)的热循环来细化金属晶粒而不改变成分的可行性。
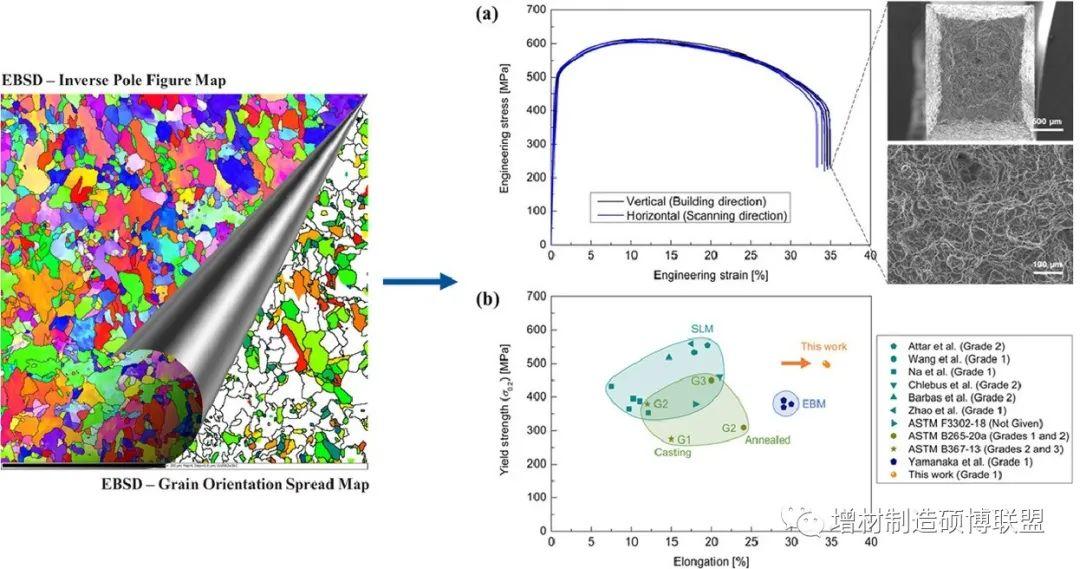
增材制造(AM)中金属和合金的晶粒细化引起了人们的浓厚兴趣,因为它可以促进细小的等轴微观结构并降低热裂趋势,从而在制造状态下实现均匀和改进的机械性能。通常,AM工艺中的晶粒细化可以通过材料相关或工艺相关的策略来实现。前者通常涉及添加成核剂颗粒(孕育剂)和/或限制生长的溶质,这在轻金属和合金的常规铸造中得到了很好的研究。在过去三年中,通过孕育细化晶粒已成功扩展到增材制造的铝合金。然而,对于钛和钛合金,由于缺乏有效的成核剂,在AM工艺中实现显着的晶粒细化已被证明极具挑战性。尽管如此,已经表明,增材制造的CP-Ti和Ti-6Al-4V合金的微观结构可以通过添加微量或大量具有高生长限制因子(Q)的溶质(例如硼)来细化、钨、铜和铁。尽管晶粒显着细化并因此提高了强度,但由于脆性金属间化合物的形成,在高添加水平下通常会牺牲所产生的延展性。此外,大量添加外来元素或颗粒会导致与“标准”成分的显着偏差,从而导致开发新的钛基合金或复合材料,而不是微量改性合金。 此外,可以通过在AM过程中改变外部和内部加工参数来控制晶粒尺寸。有学者将高强度超声应用于直接能量沉积(DED),证明Ti-6Al-4V合金的柱状晶粒可以转化为等轴形态。不幸的是,这项技术不能扩展到粉末床熔融(PBF)工艺,例如SLM和电子束熔化(EBM),因为超声波会破坏重涂粉末层。因此,控制增材制造加工参数(如激光功率、扫描速度、层厚、扫描间距、扫描图案等)仍然是细化晶粒的常用做法。与SLM制造的Ti-6Al-4V合金不同,后者通常在原位或非原位进行热处理,以控制组成相,因此通过调整机械性能,SLM生产的CP-Ti在室温下显示出单一的α/α'相,并且机械性能在很大程度上取决于晶粒尺寸。有据可查的是,SLM制造的CP-Ti的微观结构通常以沿构建方向的柱状晶粒为特征,从而导致机械性能的各向异性。相比之下,EBM制造的CP-Ti的微观结构由细小的等轴晶粒组成。然而,没有讨论晶粒细化的机制。请注意,在该研究中,基板最初预热至650°C,并在制造过程中保持在500-600°C的范围内。EBM的这一独特特征导致了与SLM不同的微观结构形态,其中基板只能预热到较低的温度(通常高达200°C)。最近,有学者通过仔细控制SLM加工参数,固化层的温度可以升高到600-850°C的范围,这类似于EBM。这些结果提出了一个问题,即是否有可能在SLM制造的CP-Ti中实现原位晶粒细化。
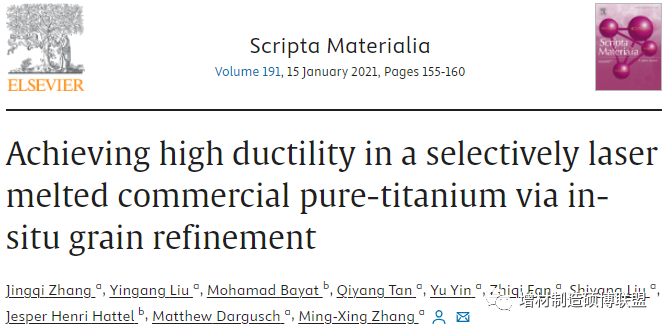
澳大利亚昆士兰大学的一项研究探索了在SLM制造的CP-Ti中实现原位晶粒细化的可能性及其潜在机制。SLM制造的CP-Ti的机械响应也通过拉伸测试进行评估。相关研究以 “Achieving high ductility in a selectively laser melted commercial pure-titanium via in-situ grain refinement” 为标题发表在《Scripta Materialia》期刊上。
试验方案
使用的CP-Ti粉末(1级)由AP&CAdvancedPowdersandCoatingsInc.提供,粒径范围为20-63μm。原样粉末的化学成分(重量百分比)为0.04%Fe、0.11%O、0.01%C、0.02%N、0.002%H、0.4%其他和余量Ti。对于微观结构演变的参数研究,使用配备400WIPG光纤激光器的SLMSolutions125HL机器制造尺寸为10mm×10mm×10mm的立方体样品。波长和激光光斑直径分别为1070nm和80μm。实验参数如表1所示。在SLM之前,基板预热至200°C。所有样本都是使用“棋盘”扫描策略构建的。每层的构建时间(曝光时间加涂层时间)保持在15秒不变。 表1. 研究中使用的SLM处理参数和测得的样品密度 图1显示了SLM制造的CP-Ti的微观结构演变,激光功率和扫描间距在1400mm/s的恒定扫描速度下。SLM参数组合对应于49.6至92.6J/mm3的体积能量密度,如表1所示。在250W的激光功率和120µm(Ev=49.6J/mm3)的孵化间距下,微观结构为沿建筑方向以粗柱状晶粒为主(图1a)。这种类型的微观结构通常在SLM制造的Ti-6Al-4V合金中观察到[25]。此外,主要在柱状晶界处可以识别出少量细晶粒。将激光功率提高到300W,同时保持舱口间距不变,体积能量密度增加到59.5J/mm3,导致部分晶粒细化(图1b)。如图1c所示,在350W的激光功率和相同的120µm孵化间距(Ev=69.4J/mm3)下观察到具有细等轴晶粒的相当大的晶粒细化。样品的相对密度也达到最大值(如表1所示,ρr=99.6±0.2%)。显微CT图像显示非常低的缺陷体积比为0.001体积%,进一步证实了在此条件下制造的样品的高密度。在350W的激光功率下,由于体积能量密度(Ev=55.6J/mm3)的降低,舱口间距从120μm增加到150µm再次导致柱状晶的形成,而舱口间距减小到90由于高热输入(Ev=92.6J/mm3),µm会产生细晶粒。将激光功率连续增加到400W,同时保持孵化间距为120µm(Ev=79.4J/mm3),也产生了与350W时晶粒尺寸相似的精细等轴晶粒。从图1中可以清楚地看出较高的体积能量密度有利于晶粒细化。似乎存在临界体积能量密度(Ev=69.4J/mm3),高于该临界体积能量密度就会发生完全晶粒细化。
图 1. SLM 制造的 CP-Ti 的微观结构演变,激光功率和扫描速度为1400 mm/s:(a) 250 W 和 120 µm (Ev = 49.6 J/mm3),(b) 300 W 和120 µm (Ev = 59.5 J/mm3),(c) 350 W 和120 µm (Ev = 69.4 J/mm3),(d) 350 W 和150 µm (Ev = 55.6 J/mm3),(e) 350 W 和90 µm (Ev = 92.6 J/mm3),以及 (f) 400 W 和120 µm (Ev = 79.4 J/mm3)。用改进的 Weck 试剂(100毫升蒸馏水、25 毫升乙醇和 2 克氟化氢铵)蚀刻样品。光学显微镜图像是使用偏振光显微镜从 SLM 制造的样品的相同位置拍摄的。 为了探索晶粒细化的潜在机制,对在Ev=69.4J/mm3下制造的样品c进行了详细的微观结构分析。图2(a)-(c)显示了对应于补充图S2中分别用A和B标记的顶部和下部区域的EBSD图。从EBSD反极图(IPF)图中可以看出,样品沿构建方向呈现梯度微观结构,粗晶粒位于顶面(图2a1),细晶粒位于下部区域(图2a2).由于空间温度梯度的存在,这种梯度微观结构类似于CP-Ti焊缝的熔合区(FZ)和热影响区(HAZ)。为了更好地理解梯度微观结构的形成,在350W的激光功率和1400mm/s的扫描速度下对CP-Ti进行了单轨模拟,如图2d1-d3所示。很明显,由于熔体蒸发和Marangoni对流产生的反冲压力的综合作用,在激光光斑正下方的熔池表面形成了一个凹陷区。熔池深度由CP-Ti的液相线温度(1669.85°C)决定,并在图2d1和d3中以黑色等高线突出显示,约为150µm。与EBSDIPF图相比,预测的熔池深度接近顶面附近粗晶区域的厚度(图2a1)。此外,预测的HAZ与与梯度粒度分布相关的区域非常匹配。图2b1中的核平均取向误差(KAM)图表明顶部区域的特征是较高的KAM值,表明几何必要位错的密度较高。在增材制造工艺或淬火后生产的钛合金中经常观察到高密度位错,这与高冷却速率有关。相反,下部区域的细晶粒显示出较低的KAM值(图2b2)。 图 2. 样品 c 顶部和底部附近区域的EBSD 图:(a1) 和 (a2) IPF 图(黑线表示取向误差≥15°的边界),(b1) 和 ( b2) KAM 图,(c1) 和(c2) GOS 图(GOS 值 <1.5° 的晶粒被视为再结晶晶粒)。通过 SLM 对 CP-Ti 进行多物理场模拟:(d1) Z-X 平面(平行于扫描方向)的温度等值线和速度场,其中黑色等值线表示熔池边界,(d2)处的温度等值线和速度场 Z-Y 平面(横向于激光束下方的扫描方向),以及(d3) SLM 过程中计算域的 3D 视图
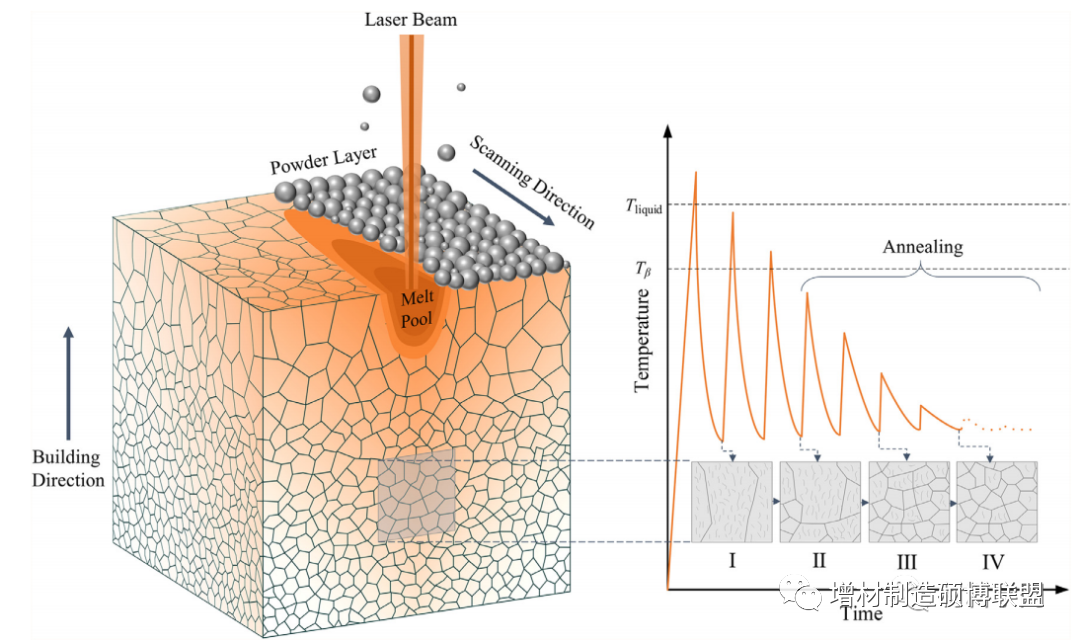
图3. SLM过程中原位晶粒细化的示意图
图4.(a)SLM以Ev = 69.4 J / mm3制作的CP-Ti的工程应力-应变曲线(沿构造方向和扫描方向进行测试),以及断层表面的SEM图像和(b)(b)通过不同制造工艺制造的CP-Ti的屈服强度与伸长率
鉴于SLM过程的逐层性质,沿构建方向的KAM梯度表明位错的湮灭是重复热循环的结果。粗晶粒区域没有经历任何或足够的激光重熔,因此表现出相对高的位错密度。相反,下层暴露于广泛的循环再加热,这反过来导致凝固层的“本征热处理”(ITH)。CP-Ti常用的热处理包括应力消除和退火。前者通常在480-595°C下进行几分钟到几个小时,而后者需要更高的温度,在该温度下可能会发生恢复、再结晶以及晶粒长大。再结晶退火通常对变形的CP-Ti进行,其中来自位错积累的储存能量为再结晶提供驱动力。然而,在AM工艺中,如果热条件有利,高冷却速率产生的高密度位错也应该会触发再结晶。晶粒取向分布(GOS)测量晶粒内局部取向错误的偏差,用于区分再结晶晶粒与母晶粒。正如预期的那样,与顶部区域相比,下部区域显示出更高比例的再结晶晶粒,如图2c1和c2所示。使用Ev=55.6J/mm3的体积能量密度,固化层的温度可以升高600-850°C。鉴于该研究中使用的能量密度较高(Ev=69.4J/mm3)并且每层的构建时间较短(15s)允许热量积聚,因此预计凝固的CP-Ti层的温度可以是保持在再结晶退火的温度范围内。结果,由于再结晶,在下部区域原位实现了显着的晶粒细化。