锂离子电池膨胀对于电池的寿命会产生明显的影响。在充电过程中Li+在负极中获得电子还原成锂嵌入石墨负极的层状框架结构时,会形成锂碳合金,从而使石墨电极厚度增加;在放电过程中,锂失去电子形成锂离子,并从空穴中逸出石墨层,此时,底片的厚度电极片相应减少。在首次充放电时,负极表面会形成一层固体电解质界面(SEI)膜,在后续的充放电循环过程中,SEI膜因遭到破坏后会再形成新的SEI膜,这将导致石墨电极不断地膨胀。 由于极化现象,锂离子不能被完全激发嵌入石墨层,因此锂离子在负极表面会还原形成锂枝晶。放电过程时,在大电流作用下,靠近负极表面的锂优先进行氧化脱附,导致枝晶锂的断裂,形成“死锂”,因此,锂离子电池的膨胀程度会随着充放电过程的进行逐渐增大。电池膨胀的另一个重要原因是电池内部的气体释放。无论电池处于常温或高温环境,在充放电过程中都会发生膨胀。膨胀的原因可能是锂离子电池在充放电过程中电解液分解产生气体。 在本工作中,来自宁德时代(CATL)的研究人员和中南大学焦飞鹏教授团队共同合作,一方面验证了不同极片数对电池膨胀力的影响,然后组装成电池模块来研究电池膨胀的差异性及其相应模块的作用力和膨胀力对电池和模块寿命的影响;另一方面,研究了溶液的膨胀度对电池模块设计的影响。可以通过实验去计算模块的抗拉强度,模拟模块的膨胀力。最后通过电池模块的充放电循环中产生的膨胀力,可以得到了模块内部的应力分布,从而确定电池模块结构是否存在漏洞和整体强度是否能够满足模块膨胀带来的压力。研究结果对电池系统的设计具有一定的指导意义。 试验方法
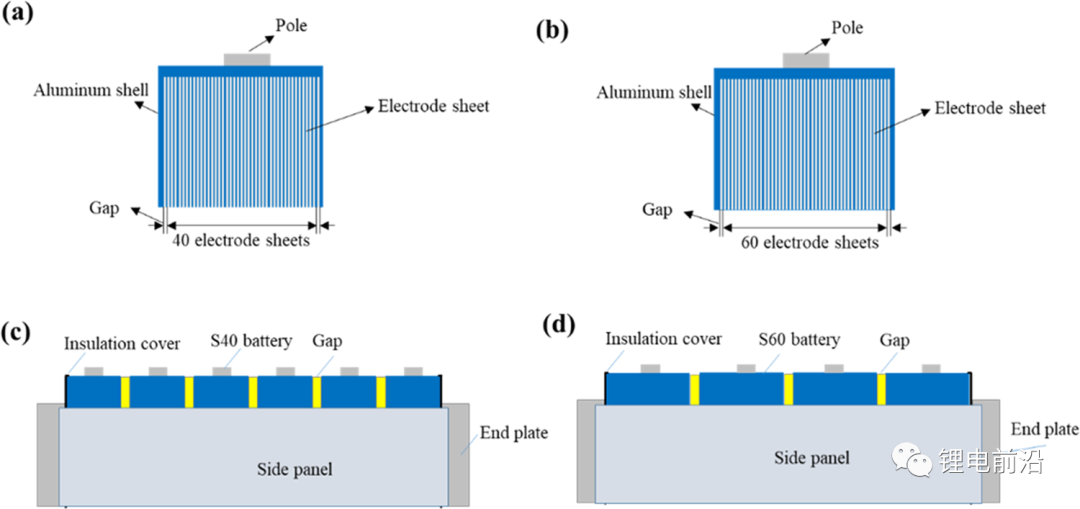
图1. 实验电池及模块示意图:(a) S40电池,(b) S60电池,(c) S40_1P6S模块,(d) S60_1P4S模块。
为了研究由不同数量的电极片组装而成的电池和模块的循环膨胀行为的差异,使用三元正极材料Li-Ni0.5Co0.2Mn0.3O2(NCM523)和负极石墨制备了电极片,并分别用40个电极片和60个电极片组装方形铝壳电池,分别命名为S40和S60。两种电池之间的唯一区别是电极片的数量,并且电极和方形铝壳之间的装配间隙是一致的。方壳的高度和宽度相同,电池的结构如图1a,b所示。S40电池和S60电池组装成相同大小的模块。为了在模块级别上保持相同数量的电极片,S40电池采用六个电池串联组装模块(缩写为S40_1P6S),S60电池采用四个电池串联组装模块(缩写为S60_1P4S)。模块的简化示意图如图1c,d所示。循环期间电极的膨胀和气体的产生增加了电池的内部压力,导致电池或模块的结构变形,这称为膨胀力。在我们的工作中,在电池和端板之间组装了一个压力检测装置,该装置由一个外部固定装置和一个压力传感器组成。外部固定装置由相同的金属材料制成,并具有与端板相同的尺寸,以确保检测装置不会影响电池的作用力。在循环测试期间,电池的膨胀会压缩压力传感器。可以通过压缩量和膨胀力之间的转换来量化模块和电池的膨胀力。为了研究不同电极片数的电池引起的循环膨胀力的差异,S40-1P6S模块和S60-1P4S模块的长度保持在355mm。每个组件的厚度如表1所示。要获得电池和模块的膨胀力数据,必须进行循环测试并记录数据。电池循环的夹紧装置可以模拟模块中电池的状况;也就是说,为电池的每个前表面预留了一定的间隙:S40电池之间的间隙为2.4mm,S60电池之间的间隙为2 mm。在25°C的温度下以1C/1C的充放电电流对这两个电池进行了测试。将模块的循环直接置于25°C的恒定温度下进行1C/1C充放电循环测试。在整个过程中,使用压力传感器检测电池和模块的膨胀力数据。当在设计模块之前获得膨胀力数据时,可以通过模拟模块的膨胀力来计算模块寿命终止时的应力分布,从而提前确定模块各组成部分的强度。符合设计寿命要求。该模拟软件是ABAQUS。模块的三维(3D)模型应形成网格,并通过ABAQUS建立模块与包装之间的连接;然后,将膨胀力参数和材料特性输入到软件中。最后,ABAQUS消除了模块中零件的应力。

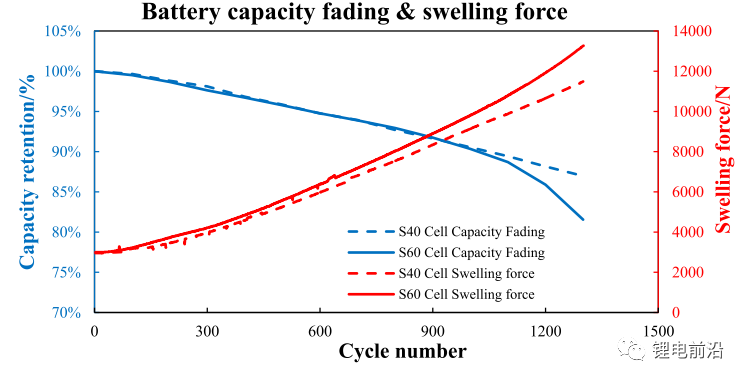
图2. 电池容量衰减和膨胀力
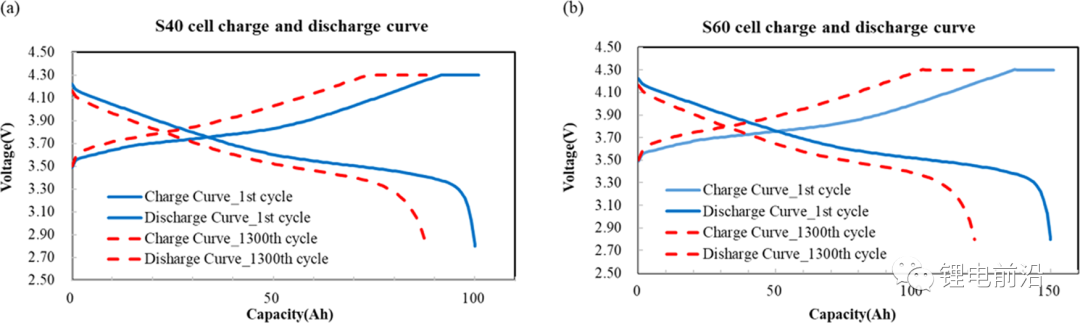
图3. 电池充电和放电曲线,(a)S40,(b)S60。 S40电池和S60电池在25°C下进行循环实验,并记录了循环过程中的溶胀力以及充电/放电过程。得到的相应曲线如图2和3所示。从图可以看出,S40电池和S60电池的容量衰减趋势在大约1000次循环之前基本相同,并且膨胀力的增长也显示出一致。在此期间的趋势。在相同温度下,不同数量的相同设计的电极片组装而成的电池的循环容量衰减趋势和膨胀力增长几乎相同,并且不受电极片数量的影响。此时,电池中电极的溶胀可能仍在电极片和铝壳之间的保留间隙内,并且没有明显的硬溶胀。随着周期的增加,经过约1000次循环后,S60电池容量的褪色趋势比S40电池快,并且膨胀力的增长趋势也加快了。在电池循环的最后阶段,由于S60电池具有更多的电极板,因此电极板的硬溶胀和产气量比S40电池更多。两块电池中的电极片和铝壳之间的间隙相同,因此,S60电池的膨胀首先超过了保留的间隙,并且膨胀力在最后一个阶段上升得更快。同时,因为在膨胀力的作用下,锂离子的传输受到限制,并且电池的内部阻抗也增加,从而导致电池更快的容量衰减.可以看出,当电极和铝壳之间存在间隙时同样,具有更多电极片的电池的膨胀力在循环达到一定阶段后更快地增加,并且膨胀力的加速也导致容量衰减。
模块的膨胀力分析
模块的设计不仅应承受由外部振动和冲击引起的损坏,还应承受由电池产生的膨胀力所引起的应力。为了研究带有不同数量电极片的不同电池模块的膨胀性能,将S40电池和S60电池组装成相同长度的模块。由于S60电池的厚度和容量是S40电池的厚度和容量的1.5倍,为确保两种类型的模块的长度和水平相同,将S40电池组装为1P6S模块,而S60电池则被组装为1P6S模块。组装成1P4S模块。就模块的内部结构设计而言,每个S40和S60电池的前表面之间的间隙分别为2.4和2 mm。S40_1P6S模块的电池之间的总间隙为12毫米,而S60_1P4S模块的电池之间的总间隙为6毫米。
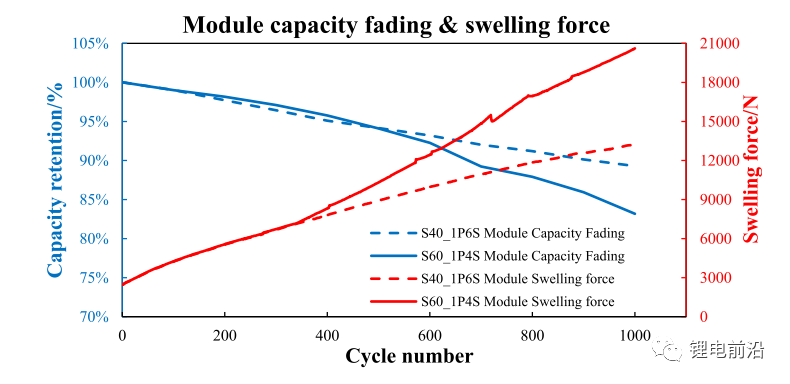
通过循环实验对这两个模块进行了测试,并同步监测了来自模块端板的容量衰减和膨胀力变化。从图4可以看出,两个模块的容量保持率随溶胀力的增加而降低,这再次证明了溶胀力导致容量衰减。在早期,S60_1P4S模块的膨胀力几乎与S40_1P6S模块的膨胀力相同。但是,经过约400个循环后,上升速度明显快于S40_1P6S模块的上升速度,并且随着膨胀力的增加,S60_1P4S模块的容量衰减速度也加快了。第一个原因可能是S60_1P4S模块中的总保留间隙小于S40_1P6S模块中的总保留间隙,因此电池的总溶胀空间较小,并且端板上的溶胀力较大,因此溶胀力也较大更大。另一个原因是,根据之前的电池膨胀力分析,在S40和S60中电极与铝壳之间的间隙是相同的,并且电极片的数量越多,最后一个时期的膨胀力就越大。因此,S60_1P4S模块的膨胀力在400个循环之后会更快地增加。因此,由于S60_1P4S模块具有更大的膨胀力,且电池中的电极片更多,因此需要提高每个结构组件的强度,以确保模块在整个设计寿命中都是安全耐用的。另一方面,为了提高循环寿命,需要在模块中的电池之间设计更大的间隙,这可以减小膨胀力并改善循环寿命。但是,通常没有足够的空间在模块中保留较大的间隙,因此应同时考虑膨胀力和间隙。 模块设计的仿真分析
仿真对于缩短产品开发周期,提高开发效率和质量具有重要意义,这在电池产品设计阶段起着非常重要的作用。对不同数量的电极片和模块的膨胀力电池特性的研究表明,膨胀力不仅影响电池的容量,而且影响模块的结构安全性。先前的研究表明,电池的膨胀力将随着容量的减小而增加,这可以指导模块的设计。因此,电池的膨胀力可能在将电池组装成模块后,例如端板和侧板,对模块的其他结构部件造成一定的损坏。为确保模块的结构在整个生命周期中不会因电池膨胀而损坏,研究模块中电池膨胀所产生的膨胀力尤为重要。本文基于先前的膨胀力数据,通过仿真来评估模块设计的结构强度是否满足要求。主要评估模块的端板,侧板和端侧板焊缝的强度是否可以承受模块的膨胀力。在S40_1P6S和S60_1P4S模块上进行了膨胀力模拟,并评估了由于模块膨胀而导致的端板,侧板和端侧板焊接处的应力。比较了模块设计的强度失效阈值,以评估设计的强度值是否可以承受生命周期内模块中所有电池的膨胀。
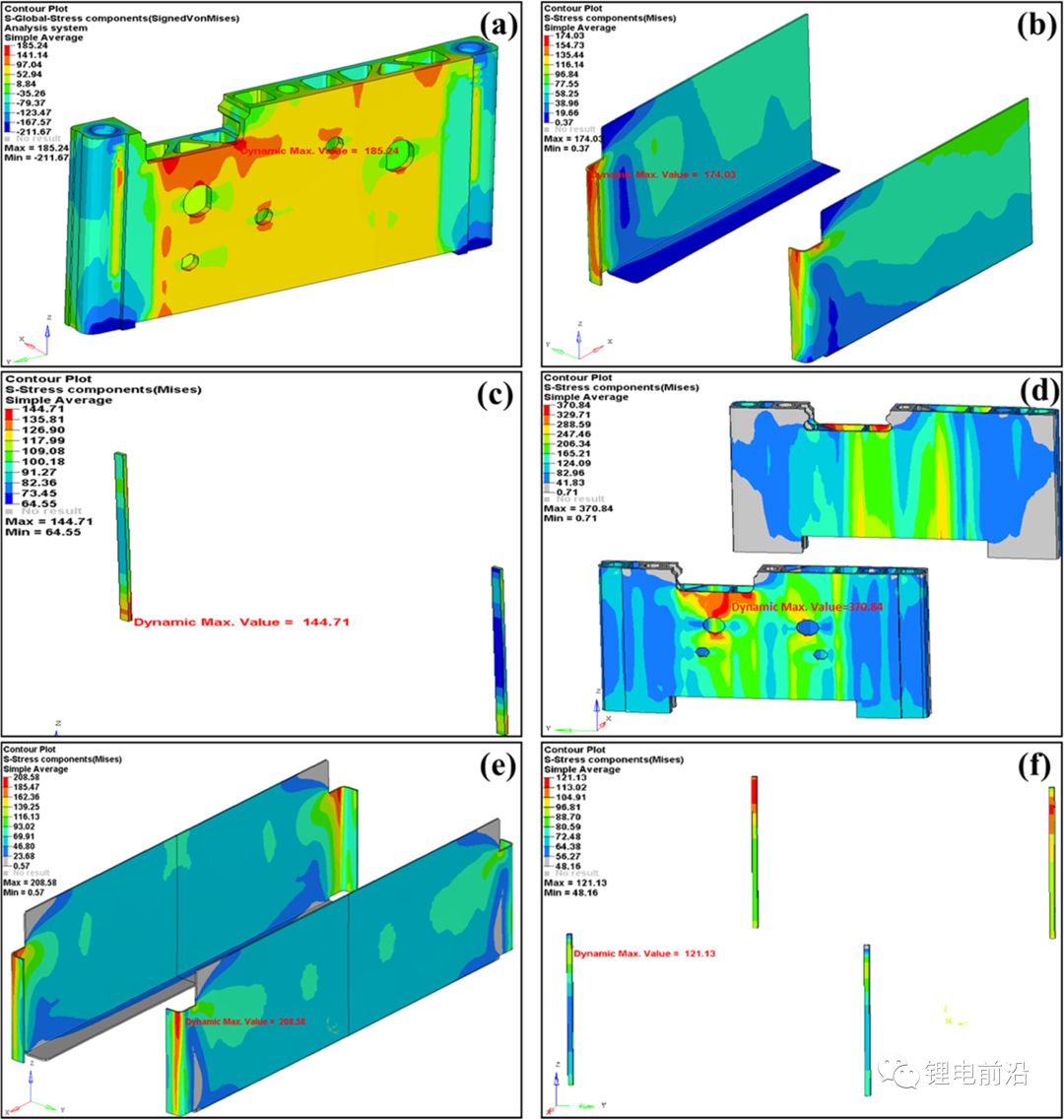
图5. 模块膨胀力仿真:(a−c) S40_1P6S模块仿真,(d−f) S60_1P4S模块仿真。
图5a-f中显示的模拟结果是S40_1P6S和S60_1P4S模块的端板,侧板和端侧板焊缝上的应力值。同时,如表2所示,仿真还可以计算膨胀后整个生命周期(EOL,1000个循环)中模块的长度变化。根据仿真结果,S60_1P4S模块的端板,侧板和焊缝上的溶胀力大于S40_1P6S模块的溶胀力。端板的模拟应力值为370.84 MPa,S40_1P6S模块的端板失效阈值仅为215 MPa,不能满足S60_1P4S模块的端板强度设计要求。因此,S60_1P4S模块的端板设计具有380 MPa的故障阈值。通过对两个模块的溶胀力的仿真分析,还可以证明,当电极与铝壳之间的间隙相同时,电池中的电极片越多,模块中的溶胀力就越大。因此,如果采用具有多个电极片的电池,则将需要更高的模块结构强度。在包装结构的设计中,有必要为模块考虑更大的膨胀空间。从以上分析可以看出,S40电池,S60电池和S40_1P6S模块,S60_1P4S模块的膨胀力的分析结果可以有效地指导模块设计,包括端板,侧板,焊接强度,模块布置等,在包装设计中起着重要作用。
结论
本次工作研究了在充放电过程中电池膨胀对电池模块和电池系统的影响。研究表明,电极片数越多,膨胀力越大,膨胀速度越快,在1000次循环后容量发生衰减。这表明电极片的数量越多的电池,在相同大小的模块电池中产生的膨胀力越大。因此,每个结构组件都需要设计更坚固,确保模块安全可靠经久耐用。具有更多极片的模块电池因其膨胀力较强,会导致电池的容量更快衰减,故应多保留保护模块来免受膨胀力过高以提高产品寿命。
参考文献:Swelling Force in Lithium-Ion Power Batteries;Yongkun Li, Chuang Wei, Yumao Sheng, Feipeng Jiao,* and Kai Wu*..Ind. Eng.Chem. Res