摘要
如何在当今竞争激烈、快速迭代的电动汽车市场中确保今天的正确决策在未来仍然适用?随着技术的快速发展、需求的不断增加和供应链的不确定性,制造商必须在考虑产品范围和性能的同时,还要考虑材料的可获得性和成本的波动性。工具和流程不仅需要适应改良后的部件,还要帮助制造商及其供应链构建强大健全的产品策略。Drive System Design (DSD) 开发了一种系统主导的方法,即电动传动优化流程 (ePOP),它使制造商客观意识到其决策对未来可能产生的成本影响,从而开发出与部件规格相匹配的动力系统架构概念,以实现最佳车辆目标。ePOP 使给定的应用程序的潜在系统设计空间得以完全映射。经过验证子系统和组件的特性以及快速生成概念,可以模拟大量完整的动力系统变体。同时,可以分析每个系统的性能和范围,并使用智能权衡算法进行比较,以研究成本变化的敏感性。本文将论证使用该流程进行探索的意义;潜在原材料成本波动的影响(例如稀土磁体成本的不稳定性)、电池和变频器技术中其他成本轨迹的影响、钢材价格变化是否会导致研究电气化的新方法。ePOP 将用于证明目标系统成本和性能分析在架构概念阶段的重要性,以及如何帮助制造商及其供应商在另项投资市场方案中创建稳健的产品策略。尽管目前纯电动汽车 (BEVs) 在整个市场中所占的份额相对较小[1],但预计在未来 5 至 10 年内,纯电动汽车 (BEVs) 将开始取代传统动力系统,并在 2040 年后主导市场[2]。然而,要实现这一目标,制造商面临着诸多挑战,不仅需要大规模建设适用于纯电动车的设施应用,同时还要在快速增长和不断变化的环境下抢占市场份额。许多研究和调查表明,阻止消费者进入市场的三大障碍是成本、“里程焦虑”以及与充电和相关基础设施的担忧[1] [2] [3]。为了抢占市场份额,制造商必须制定能够解决这些问题的产品战略,提供更具成本效益的解决方案,同时提供能满足消费者日益增长的续航里程需求的纯电动汽车。在纯电动汽车总成本上,电池的成本不可小觑(代表贮能解决方案中相对价值的巨大变化),高达 75%[4],因此将电池容量降至最低将带来巨大的成本效益。然而,由于“里程焦虑”的普遍存在,保证能令人满意的车辆行驶里程可能会适得其反。因此,了解如何有效利用电池容量,同时仍能达到操作范围目标,是稳健产品战略的必要条件之一。在这种情况下,需要我们更全面地看待动力成本优化,因为传统的以部件为中心的成本工程实际上可能会产生不利影响。从一个组件中移除成本会增加另一个组件的成本。例如,选择高能量密度电机可以降低电机成本,但对更高电流的需求可能会导致变频器成本增加。为了有效地做到这一点,我们需要审慎考虑每个动力子系统[5]。如图图 1 所示,缩小每个子系统、逆变器、电机和变速器以及电池中部件的尺寸可以节省成本。提高这些子系统的效率还可以在给定范围内减少所需的电池容量,从而进一步提高降低成本的可能性。或者,通过提高车辆行驶里程提升产品竞争优势。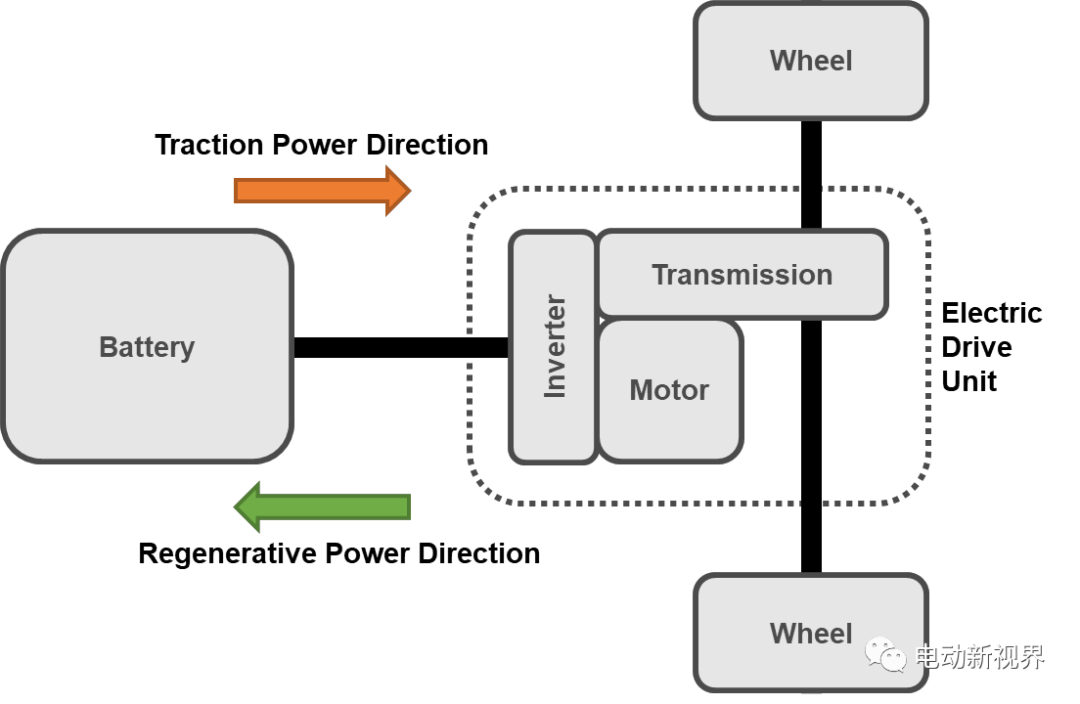
图 1 - 电气化动力系统原理图
用于设计和优化动力系统的传统工具和流程不一定适用于日益复杂的子系统交互,也不一定能满足行业不断变化的需求。这可能会使开发概念架构变得十分耗时、分散,并且过度依赖主观观点,或者偏向于“已知的解决方案”。因此,客观地确定“某种车型的最佳部件组合”以及“一个长期电气化产品战略内容”,这些问题的答案将变得十分困难。
回答此类问题需要一种全面考量过的系统性方法,正是这种理念推动了 Drive System Design (DSD) 工具的开发。促成 ePOP 流程的关键因素是子系统和组件的独特设计,该设计使得流程构建完整的动力变体以进行模拟。
ePOP 可快速生成一系列可行的动力候选方案,适用于各种拓扑结构和布局设计。ePOP 可快速生成包含部件和子系统尺寸、质量以及效率图等输入数据,允许模拟数千种独特的动力组合,并通过智能成本功能和权衡算法进行比较。这使得对成本和效率(或车辆行驶里程)的权衡评估成为可能,而这二者对电动汽车的未来发展至关重要。
这些问题间相互联系,并通过将优化电气化动力系统和电动汽车视为一个整体来解决。例如,通过使用大容量电池组可以轻松解决“里程焦虑”问题。然而,考虑到英国高级推动研发中心(UK Advanced Propulsion Centre) [2]2017 年计算的典型电池成本约为 280 美元/千瓦时,将此作为一个单一问题处理可能会导致成本增加,因为电池占车辆总成本的比例可高达 75%[4]。因此,用这种方式处理问题显然是不合适的。动力成本和效率的优化必须与整车的优化同步进行。这可能以最小化电池容量和后续成本的形式出现,或者在某指定车辆平台上最大化增加车辆续航里程。这些措施都解决了有关纯电动汽车高级市场的担忧。然而,为了创建健全的产品策略,还必须对关键成本因素的潜在成本波动进行充分考量。
高级推动研发中心公布的预期成本轨迹示例如图 2 所示。制造商在开发产品时应该考虑到未来材料成本的潜在趋势,同时准备好控制未成功降低成本带来的风险。
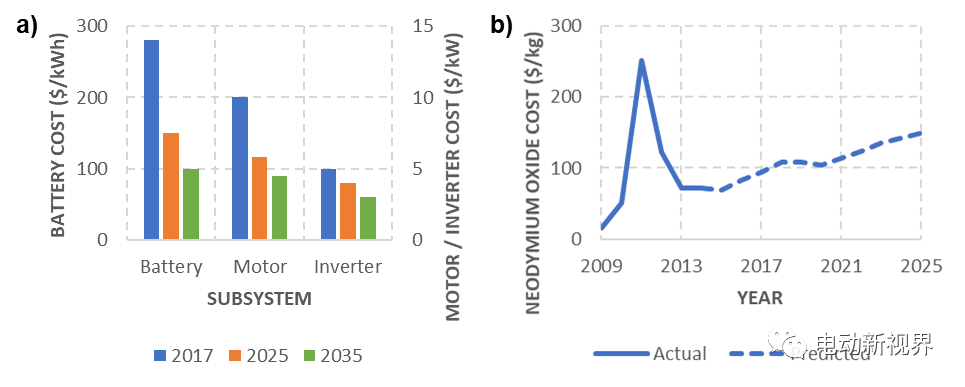
图 2 - 电气化动力子系统和材料的成本趋势;a) 英国高级推动研发中心的成本预测[2],b) 氧化钕成本,2009 - 2025 年 [6]
图2b 展示了钕的价格是如何在 2011 年大幅飙升(钕是众多汽车发动机部件的主要材料)[6]。稳健的产品战略将这些成本波动的潜在影响和其他成本的潜在价值考虑在内,同时它们对系统的相对效益也被纳入考量。例如,利用更高级的稀土磁体,同时考虑材料成本波动影响的产品设计,也可能减少变频器电流需求,并创建更有效的系统。反过来,这又可以减少电池容量并进一步提高成本效益。本文将论证 ePOP 在为工程师提供数据时所使用方法的价值,以便工程师在选择概念策略时对权衡研究有一个明智的看法。
ePOP 流程的一个关键特性是能够快速准确地模仿子系统和组件,从而为变频器、电机和变速器变体创建输入数据,并根据应用的需求进行定制 [7]。该过程为每个子系统都生成一个模拟车辆和成本函数所必需的专属特性。
变速子系统建模程序能够为任何特性传输架构生成输入数据。采用模块化方法,将变速器拆分成由轴、轴承以及必要的套管支撑的平行轴系统和行星齿轮组。每一个都是根据所需的扭矩和比率来确定大小,从而可以确定代表性质量和功率损耗,然后生成效率图。也可以通过在系统中添加离合器等来添加多速变速器装置,使用类似的方法确定其尺寸。
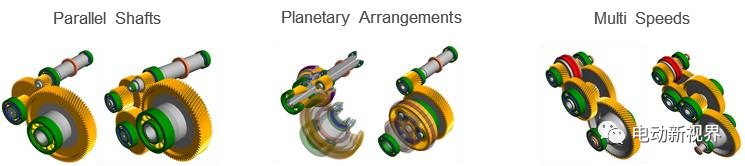
图 3 - 可添加的一系列变速系统装置
图4所示为两个变速架构的单操作点的功率损失。三级平行轴变速器比两级变速器成本更高,功率损失更大。然而,由于个别齿轮啮合比较低导致功率损失的原因也各不相同。最后,三级设计实现了更高的总传动比,进而使更小、高速、低扭矩的电机变得可行。
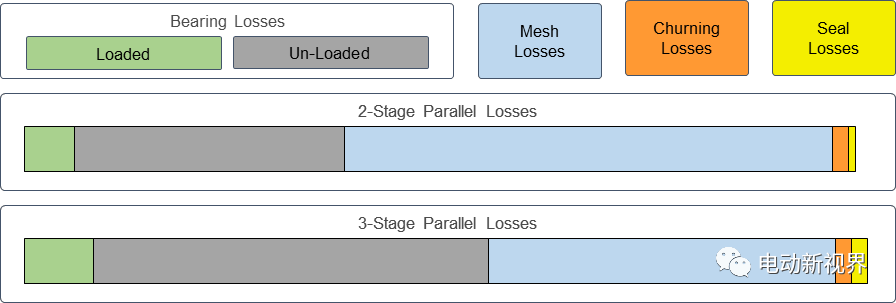
图 4 - 给定工作点的两种变速器设计的功率损耗示例
电机模型
电机模型是通过 Python 内部开发的子程序生成的,该子程序调用 Motor-CAD,并自动参数化模型以生成效率图、材料质量和惯量。如图5所示,电机生成程序能够利用适当的 Motor-CAD 模块产生多种电机设计类型,包括具有多转子拓扑结构的永磁同步电机 (PMSM) 【表面磁钢(SPM) 和嵌式永久磁体 (IPM)】、感应电机和开关磁阻电机 (SRM)。
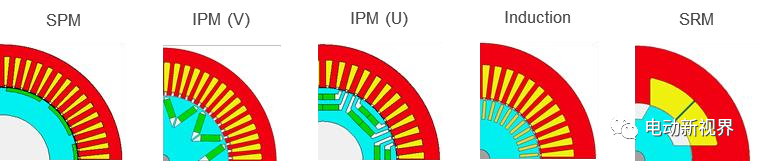
图 5 - 可以使用一系列不同的电机类型和拓扑结构
该程序接收其他目标的拓扑需求,如峰值或连续扭矩或功率。接着,该程序选择合适的基础几何体,以符合热限值和结构限制内的目标,并迭代多个变量,以生成一系列满足所需规格的可行设计。一旦生成一个 Motor-CAD 模型,就可以相应地确定质量和功耗。
图 6所示为永磁和感应电机单工作点损耗示例。正如预期,减少铜和铁的损耗与磁体损耗相互抵消,这使得永磁电机效率更高。然而,由于磁体含量缺失,感应电机的成本可能会更低,但如果没有完整的系统方法,就不清楚这种较便宜的电机选择是否会因此被对系统的影响所抵消。
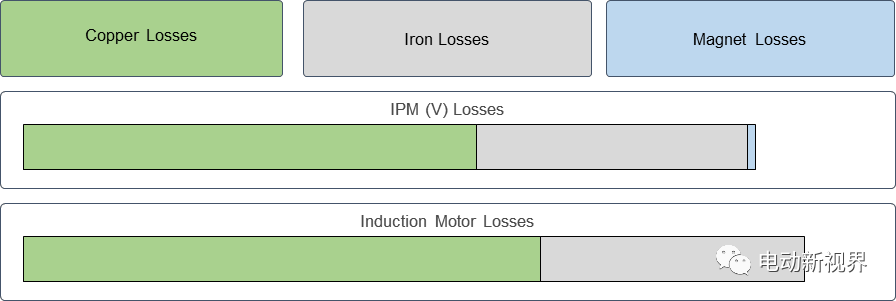
图 6 - 给定工作点的两种电机设计的功率损耗示例
变频器模型
目前正在考虑使用的两大变频器技术是传统的绝缘栅双极晶体管 (IGBT) 和最近研发成功的碳化硅 (SiC) 金属氧化物半导体场效应晶体管 (MOSFET)。ePOP 采用 DSD 公司开发和验证的定制变频器模型,计算变频器效率图、质量和成本,所有这些都是优化过程必需的输入数据。图7为 IGBT 和 SiC 变频器的损耗示例。通过降低栅极损耗、消除二极管开关损耗,可以发现 SiC 变频器比标准的 IGBT 更高效。然而,这一好处需要增加额外的成本。这一额外增加的成本使得用户的自己权衡利弊:对于给定的应用程序,SiC 变频器何时成为可行的解决方案,以及可以利用动力系统的其余部分做些什么来实现这个决策?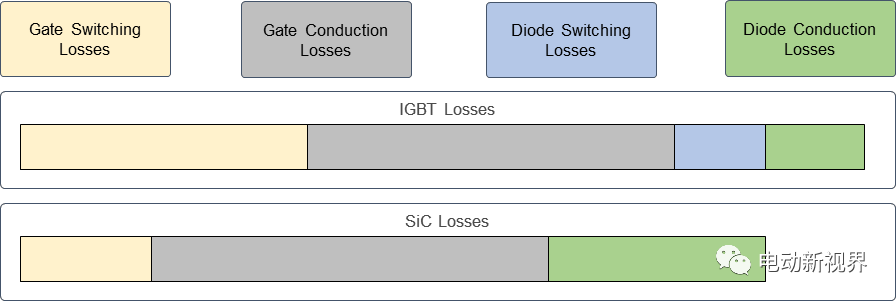
图 7 - IGBT 和 SiC 变频器在给定工作点的损耗分析实例基于 Matlab/Simulink 的车辆模型,使用后向模型进行汽车循环工况模拟,同时使用前向模型进行性能模拟。后向车辆模型考虑了车辆和部件惯性、滚动阻力、气动阻力、坡度和效率图,以计算运行条件和汽车循环工况能耗。
车辆模型将子系统性能与车辆属性直接相关,例如加速度、最高速度或汽车循环工况效率,并允许在公平对比情况下评估和比较不同系统的运行条件。这允许用户识别导致可量化性能优势的趋势。
采用理想化方法模拟多速变速器,对动力传动系统结构进行最公平的比较,避免预定义控制策略的影响。因此,在每一个汽车循环工况期间,车辆每次都能以最佳档位运行。在后置处理过程中才计算换档能耗,以便将所有能量损失/再生考虑在内,同时还考虑了换档效率。
基于每个动力传动子系统的材料成本计算而得出成本函数,该函数针对所涉及的每个子系统架构进行了精确估算。额外成本和重量可根据超过或不达到重量和/或性能目标而增加,或因导致与 NVH 相关风险或超过给定的包装体积或形状而受到处罚。
电动汽车成本的关键因素之一是电池。在成本函数中,该过程将比较由给定的电池容量和汽车循环工况能耗确定的车辆续航里程,并将其与车辆或应用的目标里程进行比较。随后每个动力系统都会收到成本处罚或成本降低,与已实现的里程短缺或过剩成比例。罚款金额是根据每公里行驶成本来确定的,使用的是电池的估计成本,如之前在 APC 图2中所示。此方法允许用户量化动力总成效率投资的优势。
为了了解上述系统方法的优势,我们将定义一个车辆案例研究,并探索电气化动力系统的潜在设计空间。本研究旨在为动力系统及其子系统确定一系列替代解决方案,以及如何权衡几个特定应用,以确定满足能耗和成本目标的最佳解决方案。
本例选择了一款全电动四门轿车,并设定了市场典型性能指标;最低最高速度为 160 公里/小时,在 7.5 秒或更短时间内从 0 加速到 100 公里/小时,固定电池容量为 100 千瓦时。其他应用典型车辆模拟参数见表 1。
表 1 - 车辆模拟参数
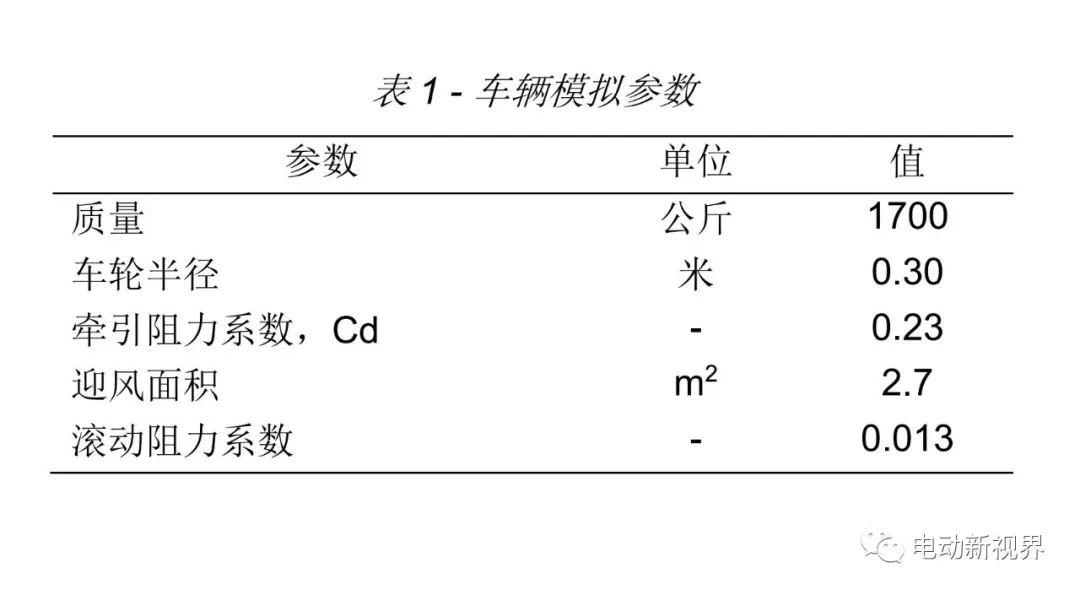
我们将研究一系列其他可选的动力系统方案,并将主要子系统、变频器、电机和变速器的变化考虑在内。对于电机,我们考虑了两种内部永磁拓扑结构,“V”形和“U”形,以及感应电机。各电机峰值功率均在 170 至 200 千瓦之间,极数和相电流均不相同。每台电机都与 IGBT 或基于变频器的 SiC MOSFET 配对。最后,将每种电机 - 变频器组合与三种替代变速器进行匹配。为了降低本案例研究的复杂性,我们只考虑了平行轴配置,并且仅限于单速或双速变速器。单速变速器由两个或三个档位组成,而双速仅限于两个档位。为了评估能耗和成本的最佳配置,我们模拟了大量不同的操作条件,每个齿轮啮合的比率都有大幅度的变化。
结果
在 WLTC 上分析了每一种满足案例研究车辆性能标准所设定的约束条件的动力系统,共计超过 17,500 种可行方案。每个潜在变体所产生的能源消耗和动力成本如 图 8 所示,其中可以看到大量已分析的独特动力系统。图 8a 显示独立于储能装置的动力系统,而图8b 将电池成本的组合影响视为动力系统整体成本中的一部分。图 8 中两个清晰的群集表示了本研究分析的两种变频器类型,橙色为 SiC 变频器,蓝色为IGBT 变频器。我们看到两个可以预料到的特征:由于减少开关和二极管损耗,所以 SiC 变频器消耗更少能源,但使用这种新技术的成本较高。然而,如图 8b 所示,一旦考虑到电池成本的影响,两种变频器选项之间的相对系统成本差异将明显变小,这说明动力系统其余部分的电池成本是主要影响因素。每个模拟变量的能耗差异需要进一步注意。许多一级供应商和车辆制造商要么利用 SiC 变频器,要么使用这些变频器以提高效率。然而,最好和最差的 IGBT 系统之间的差异远大于换用 SiC 变频器所产生的收益,这突出了在概念阶段进行系统等级分析的潜在好处。图 9 展示了与图 图 8 相同的数据集,但分析了所考虑的其他变速器设计的影响;均基于平行轴齿轮的二、三级单速和二级双速。对于更简单的单速配置,我们可以看到齿轮啮合和轴承的数量减少及其相关损失,从而降低了整个汽车循环工况的能源消耗。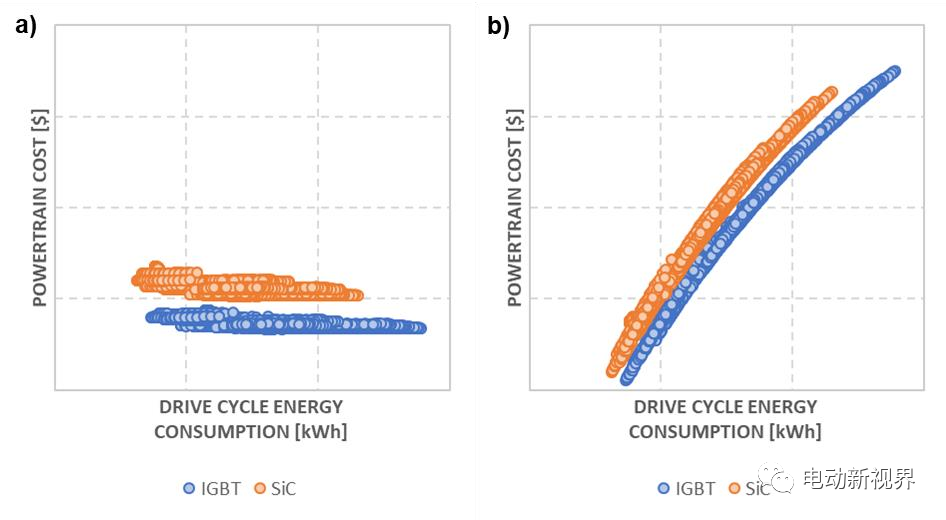
图 8 - 汽车循环工况能耗与可选变频器设计的动力成本;a) 仅动力系统成本,b) 包括当前电池成本的动力成本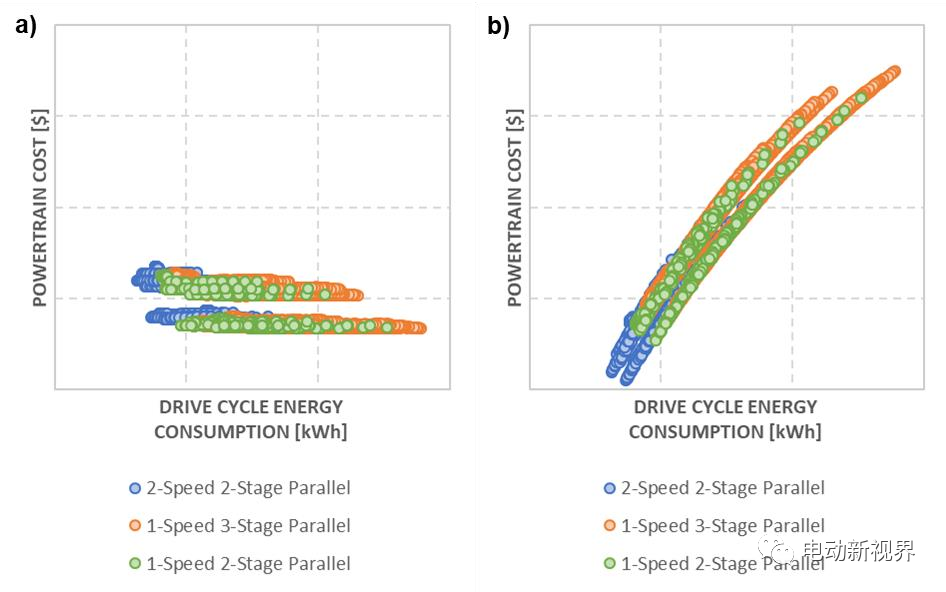
图 9 - 汽车循环工况能耗与可选变速器设计的动力总成成本 a)动力总成成本仅限,b) 动力总成成本包括当前电池成本然而,双速变速器在两种单速配置下都消耗更少的能源。双速变速器使动力系统的峰值效率区得到更高效的利用,当效率降低时,更易于换档。这将降低能源消耗,并缩小最高效和最低效动力系统之间的差异。正如上文变频器的选择,这种性能的提高是以更高的成本为代价。在这种情况下,选择不同的双速变速器不仅会导致与附加回转构件相关的额外成本,还会导致换档机构以及其后的控制要求。图 9a 可以清楚看见仅考虑动力系统的成本,但是一旦将电池成本考虑在内,如图 9b 所示,这种差异就被抵消了,这表明双速变速器的效率优势可以有效地实现资本回报。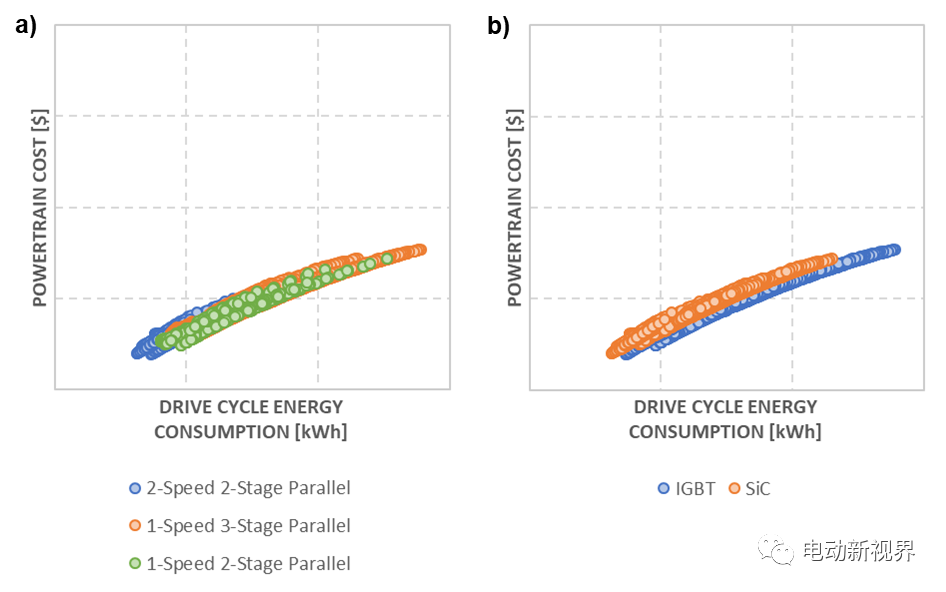
图 10 - 汽车循环工况能耗与 2035 年预计动力成本(包括电池)对比;a) 其他变速设计,b) 其他变频器设计此阶段仅从典型模式考虑动力系统和电池的成本。然而,今天所做的决策是关于未来几年将要生产的产品,产品战略决策可能会为投资决策提供信息,这些决策阐明了更长期的技术选择(例如生产线投资)。图 10a 和图 10b 考虑了成本变化对之前所探讨的两个研究领域——变频器和变速器的影响。如 图2a 所示,APC 预计到 2035 年,电池成本将比 2017 年降低 60% 以上,同时变频器成本也将降低约 40%[2]。可以预计,虽然目前选择使用 SiC 变频器的成本比 IGBT 高,但随着该技术被更广泛地采用,这一成本差异将会缩小。图 10 结果表明,电池成本的影响已经大幅降低,不同变频器之间的差异也相应地逐渐缩小。这可能导致对人们数据有另一种解释,从而做出另一种决策。例如,图10a 表明,双速变速器的效率益处不再明显,因此与其他单速变速器的差异也已大大减小。在此例中,已经考虑了单辆车的应用,但是当考虑多辆车或平台时,使用单速变速器的决策可能会更有吸引力。图 10b 结果表明,SiC 与 IGBT 的成本差异已经很小了。这种分析可以与目前的技术评估结合使用,以当前的成本来衡量新技术的潜力,以及何时投资可以获得长期收益。另一个需要考虑的领域是磁体成本的影响。图2b 显示了自 2009 年以来钕成本的波动变化,作为影响众多汽车发动机成本的主要因素,我们必须考虑这种变化的影响。图 11a 显示了使用当前典型磁体成本的汽车循环工况能耗与动力系统成本的关系(不包括电池)。图 11b 显示了相同的结果,但是使用 2011 年钕的峰值成本来代替磁体成本进行计算的。这引起永磁电机的两种动力系统配置的成本变化。没有磁体的感应电机不受影响。如 图 11a 所示,使用感应电机的动力系统通常在上文讨论过的每种类型的变频器中成本较高。其中一个原因是在可接受包装体积中,为了达到性能要求而需要增加相电流。然而,这种增加的相电流会导致变频器成本增加。因此,尽管没有磁体的电机成本较低,但净效应会导致成本增加。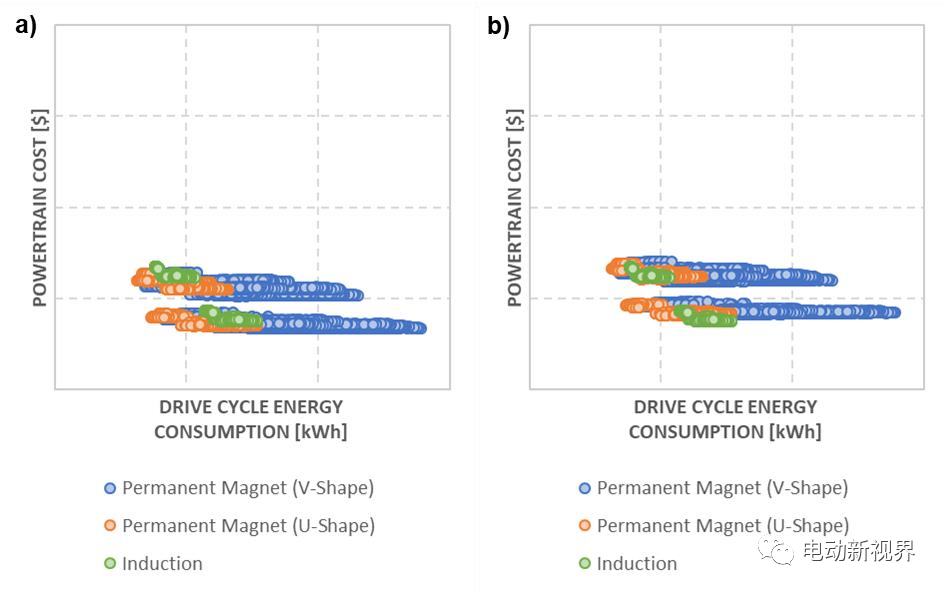
图 11 - 汽车循环工况能耗与动力成本(不包括电池);a) 当前磁体成本,b) 2011 年磁体成本峰值如果 2011 钕的成本峰值按 图 11b 发展,则这一趋势将会改变。磁体成本越高,永磁动力系统的成本也就越高。现在,可以在变频器的成本末端找到基于感应电机的变体。这种特征行为在 图 12 中得到进一步证明(包括电池成本的影响)。图 12a 中使用的是能代表当今动力系统和电池典型成本的成本数据。在这种情况下,尽管竞争激烈,但基于永磁电机的动力系统仍在能源消耗和成本方面比感应电机性能好。图 12b 提出了一个与上文所探讨情况类似的方案,即到 2035 年,电池和变频器的成本都将大幅降低。然而如图 11 所示,在这种情况下,磁体成本已增加到与 2011 年相同的成本峰值。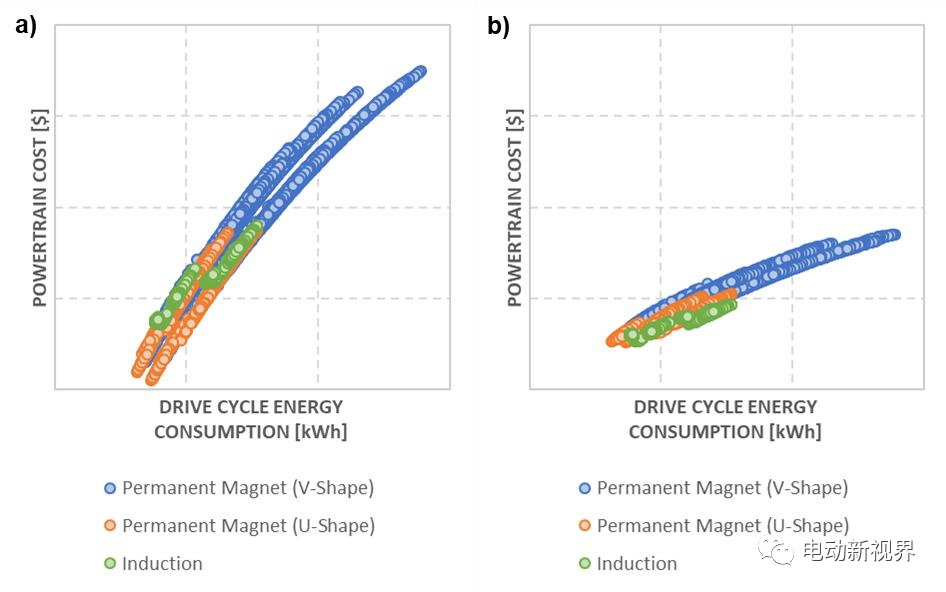
图 12 - 汽车循环工况能耗与动力成本(包括电池);a) 当前成本,b) 预计 2035 年电池和变频器成本将达到 2011 年磁体成本的峰值预计到 2035 年,电池成本将下降,这将减少提高效率对总成本的相对影响,从而缩小基于永磁和感应电机的动力系统之间的差异。同样,随着变频器成本的降低,感应电机使用较高电流所带来的影响也会降低。结合 2011 年的磁体成本峰值,在 图 12b 中我们可以看到一个完全不同的走向。效率最高的永磁动力系统和感应电机动力系统在能耗和成本上的差异变得很小,这表明未来制定电气化动力系统策略时感应电机动力系统将发挥极大作用。混合动力电动汽车和纯电动汽车技术种类繁多,发展迅速。因此,在这样一个快速发展的行业中,制造商和供应商在制定产品战略方面面临巨大挑战。现在所做的产品战略决策最终将影响未来几年专注于特定技术的制造业的大规模投资。制造商可利用的决策数据越多,效果就越好。为了制定稳健的产品策略,这些决策应该充分考虑现在和未来的市场状况。DSD 采用的 ePOP 系统方法有助于以这种方式评估动力系统产品概念,并可确定其未来的影响。电池成本高低对当前市场中的系统成本有着巨大影响,为 SiC 变频器、多速变速器和永磁电机等能提高效率的技术提供了重要价值。然而,当前流行的技术不一定仍能在未来成为最强大的解决方案。如果预期的电池成本轨迹是可信的,那么可以预测,在未来10 到 20 年内,高效率技术的相对价值将会降低。然而,这是在当前汽车续航里程不会增加的假设下所做的判断。如果此类预期持续增长,那么电池成本将仍旧是主要影响因素,因为增加续航里程的费用将抵消每千瓦时的潜在成本,而提高效率的技术仍将很有价值。ePOP 等系统方法能将这些发展的总体影响考虑在内,并进行潜在的权衡分析。本文还介绍了其他几个例子,从而说明这种方法的潜力价值。尽管已证明提高效率的技术是有益的,如 SiC 变频器、多速变速器或永磁电机,但为车辆应用选择正确的整体动力系统概念的价值是至关重要的。选择相关的任何子系统或组件级别可以提高效率并降低潜在成本。[1] Deloitte, “New market. New entrants. New challenges. | Battery Electric Vehicles,”2019.[2] Advanced Propulsion Centre UK, “The Roadmap Report - Towards 2040: A Guide to Automotive Propulsion Technologies,” Automotive Council UK, 2018.[3] Great Britain. Department for Transport, “Public attitudes towards electric vehicles: 2016 (Revised),” 2016.[4] A. Wolfram and N. Lutsey, “Electric Vehicles: Literature Review of Technology Costs and Carbon Emissions,” 2016. [5] S. Fraser, “Commerical EVs: Applying a systems engineering approach to optimise the powertrain in order to tackle the total cost of ownership challenge,” in 17th International CTI Symposium Automotive Transmissions, Berlin, 2018. [6] Statista, [Online]. Available: https://www.statista.com/statistics/450152/global-reoneodymium-oxide-price-forecast/. [Accessed 22 August 2019].[7] M. Bryant and T. Holdstock, “Gearing up for lower cost electric drives: accelerating the development of optimal electrified powertrain architectures,” in 32nd Electric Vehicle Symposium (EVS32), Lyon, France, 2019.