现代E-GMP驱动总成技术分析
现代E-GMP平台目前规划两款电驱系统,三点悬置布置。驱动电机均为采用油冷的扁线永磁同步电机 。
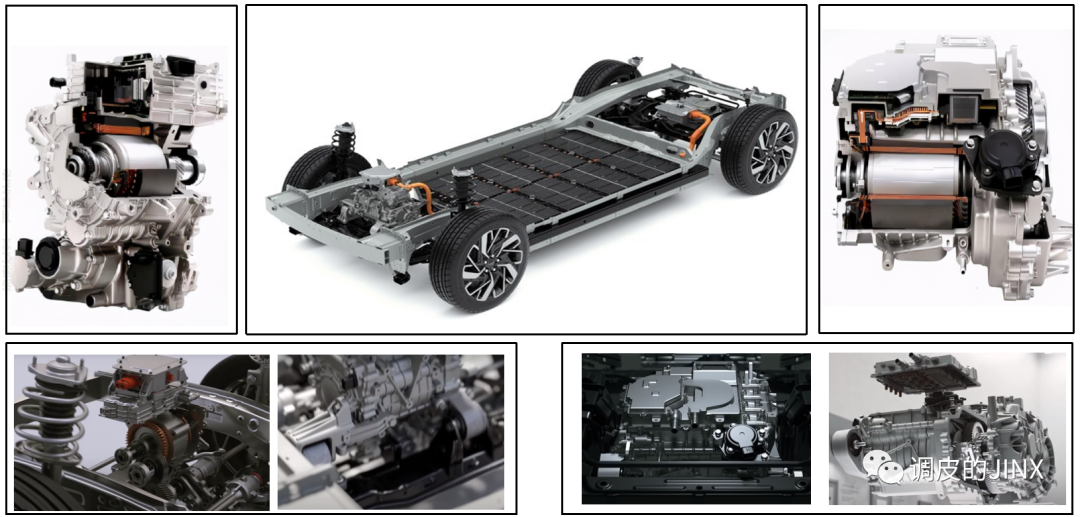
前驱总成73.754kg,宽高长分别为427x518x386。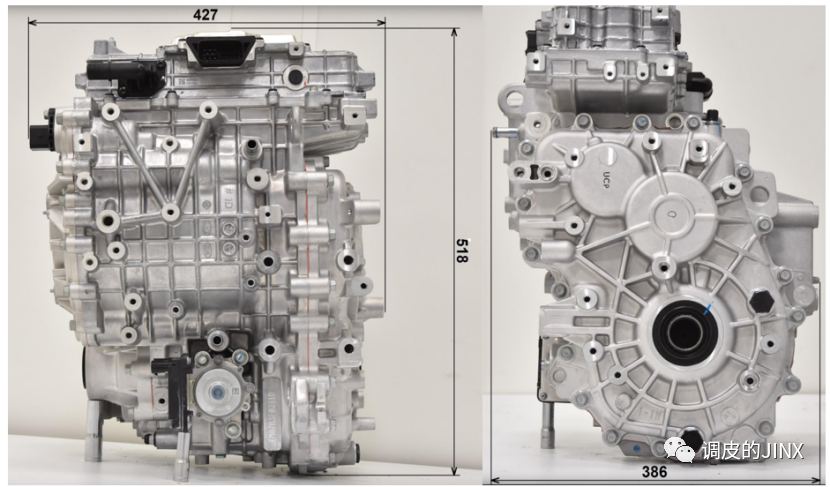
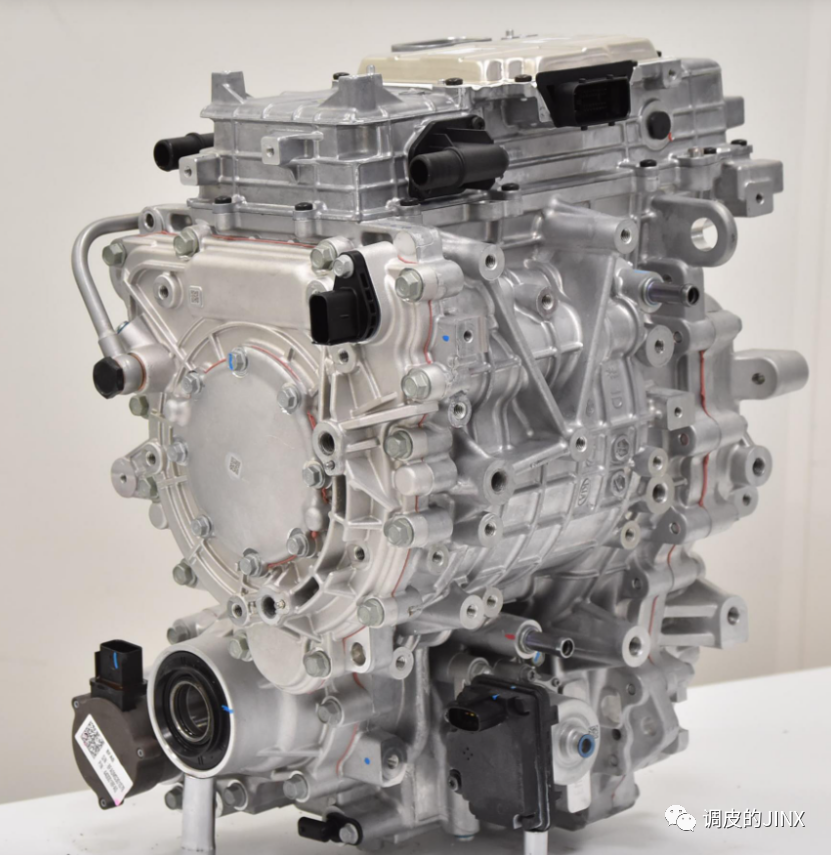
后驱总成101.4kg,宽高长分别为545x360x680。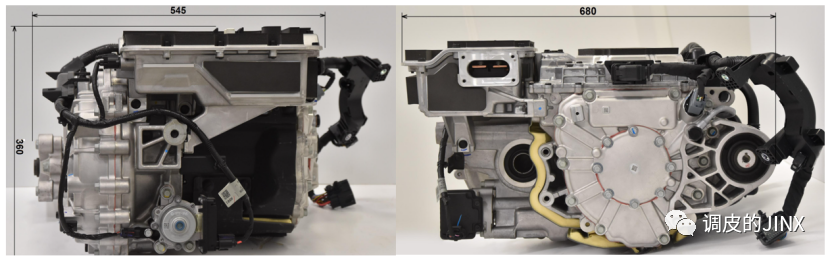
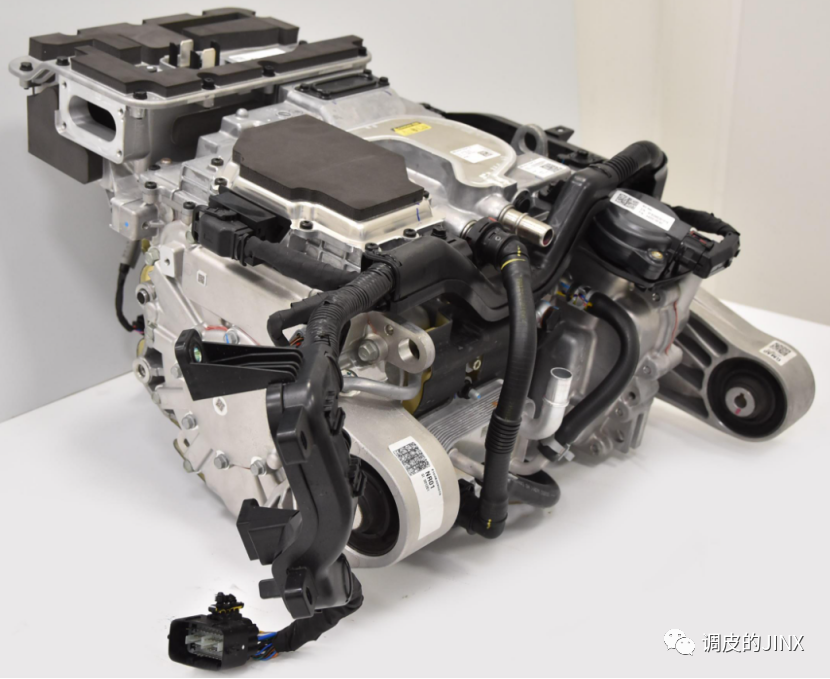
电机冷却系统
无论是前驱系统还是后驱系统,两者的电机冷却方案都是一样的。冷却系统分为主动强制冷却和间接强制冷却。主动强制冷却回路有两个,一个是定子铁芯上面的两个油管,另外一个是转子铁芯两端的圆环;间接强制冷却则是绕组底部泡油(两个油管+油环的冷却方案还是无法保证电机绕组360°冷却,最下面的绕组外层即是盲点,为了解决这个问题,增加了泡油方案)。
定子铁芯上面的两个油管(AI材质,点焊+钎焊)开有一定数量油孔,通过油孔向铁芯两端绕组以及铁芯中部进行喷油冷却。
油管通过焊接支架,采用一个M6螺栓固定在变速箱壳体。需要注意的是,油管上的特殊支架结构。一方面,在装配过程中进行预定位;另外一方面,减少支架在打螺栓过程中的偏移。对于这个结构的设计,有那么一点意思。
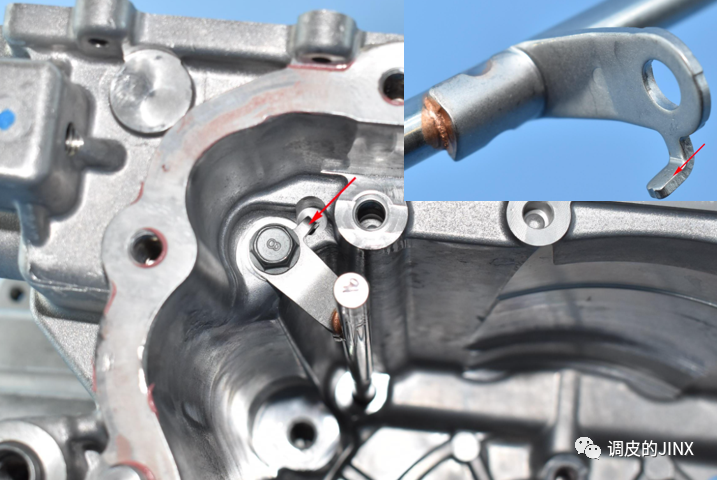
由于油孔数量及位置受限,铁芯两端绕组只有上半部分区域得到了冷却。当绕组层数较少时,上面的冷却油可以通过绕组之间的间隙淋到下面;当绕组层数较多时,基本上绕组内层几乎无冷却。而E-GMP采用的是8层绕组方案,因此,如果仅仅依靠两根油管喷油冷却,那么两端绕组内层是危险的。为了解决这个问题,E-GMP在铁芯两端(绕组内层)增加了两个外置金属油环(AI材质,点焊+钎焊)。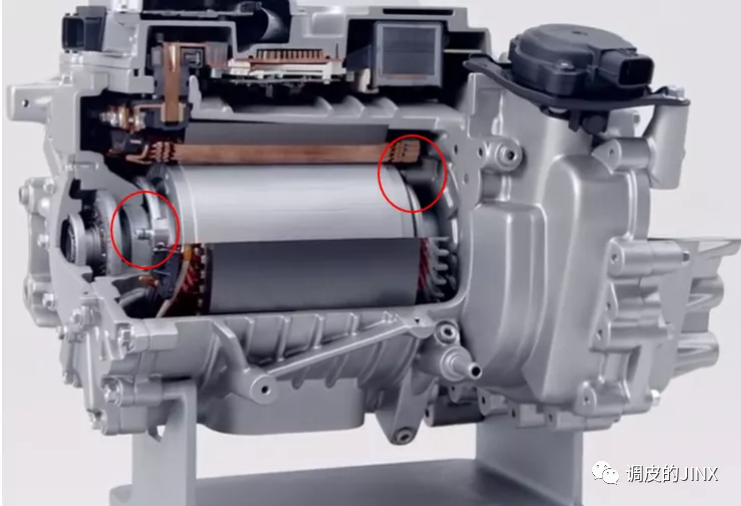
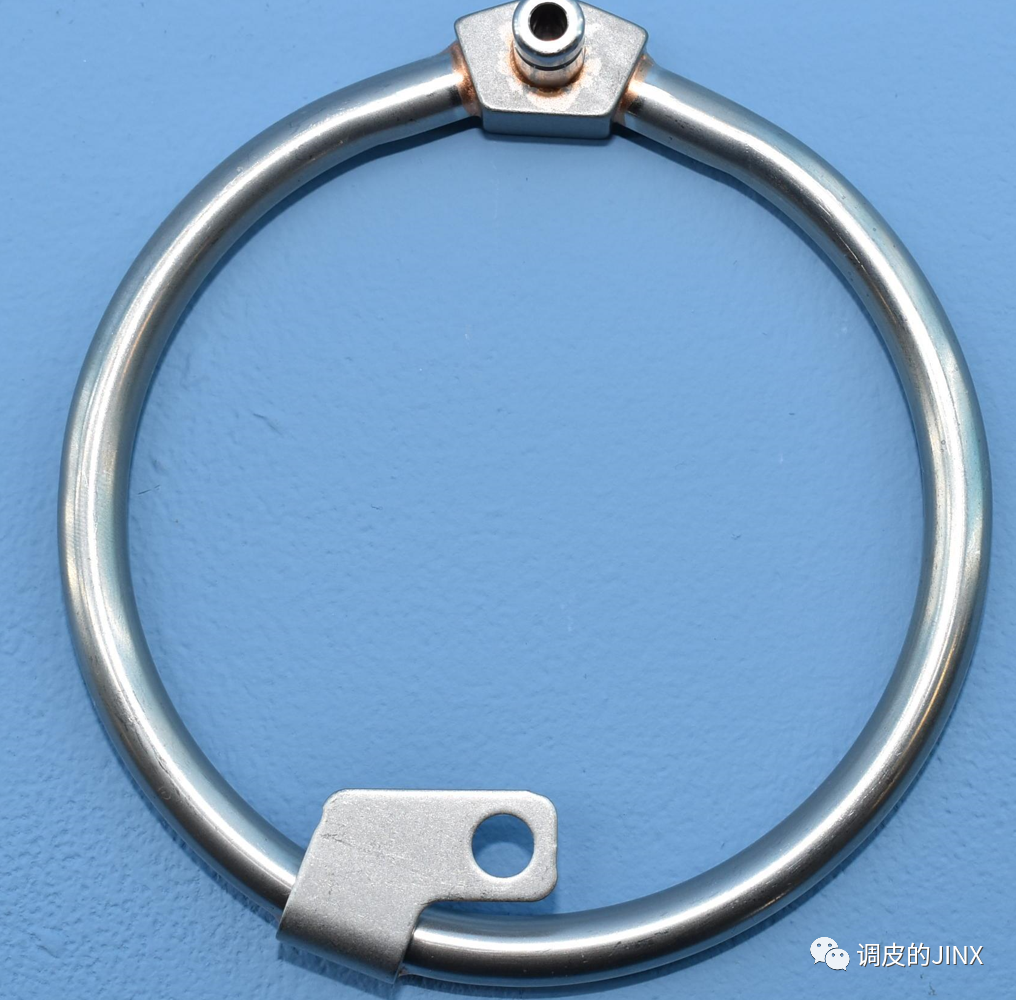
前、后油环均只通过一个M6螺栓,分别固定在变速箱壳体底部和后端盖轴承室外圈。油环外侧开有一定数量油孔。两个油管外径均为106mm。
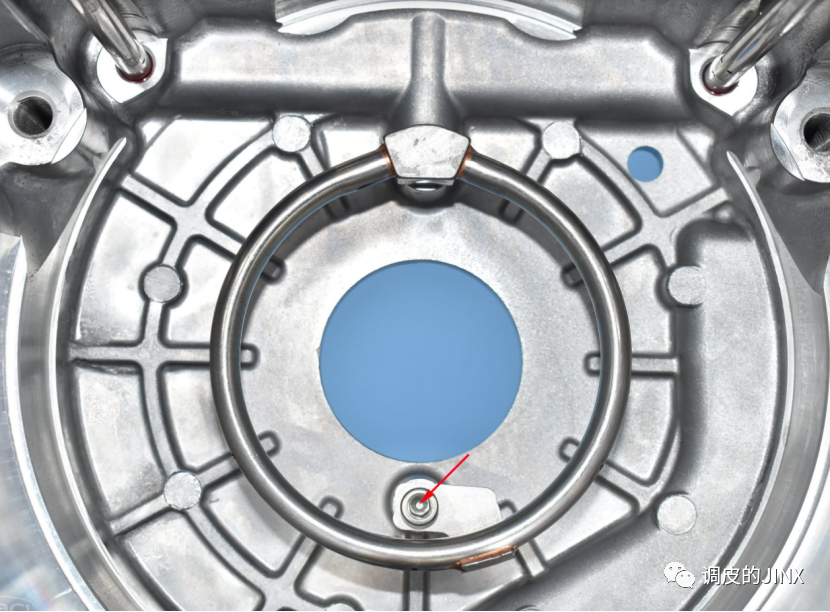
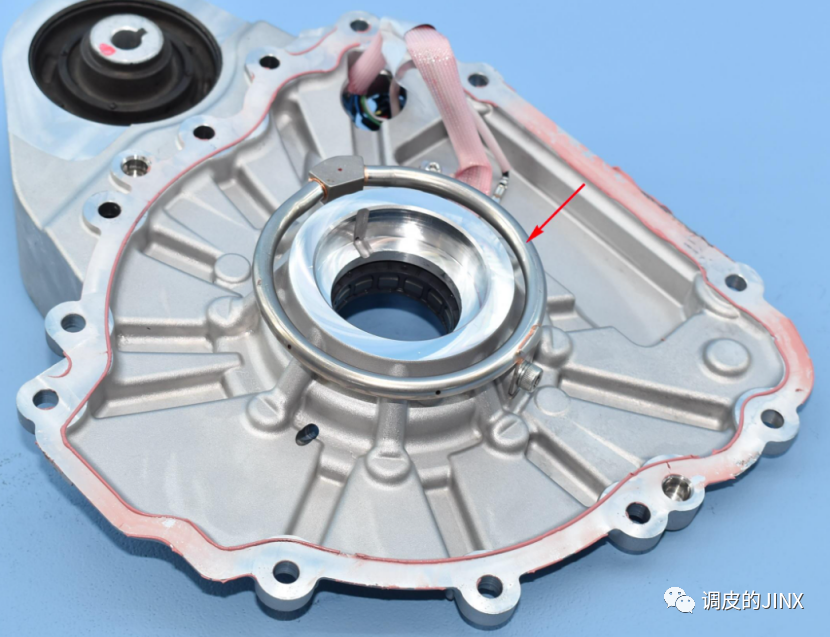
由于铝材质较为柔软,因此相较碳钢更容易弯圆成型。但是即便采用了铝材质,也可以清晰的看到油环在弯圆结合处的变形。同样是金属油管,上汽EDU 二代电机冷却油管采用不锈钢材质。虽然韧性更强,但从拆机出来的照片来看,无论是圆度还是连接处的处理,都更胜一筹。令人惊讶的是,油冷的大小居然只有0.7mm,不得不佩服上汽在电机油管方面的设计能力和制造能力。
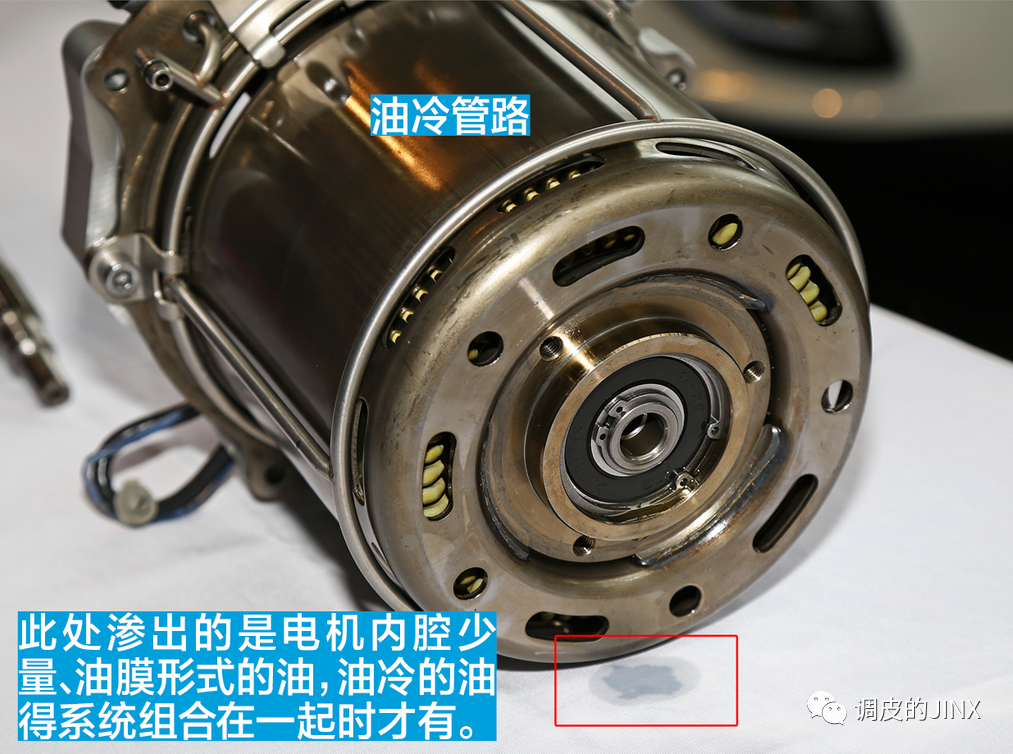
前面谈到的冷却更多倾向于电机定子冷却,接下来看下转子冷却。E-GMP转子设计思路一致。
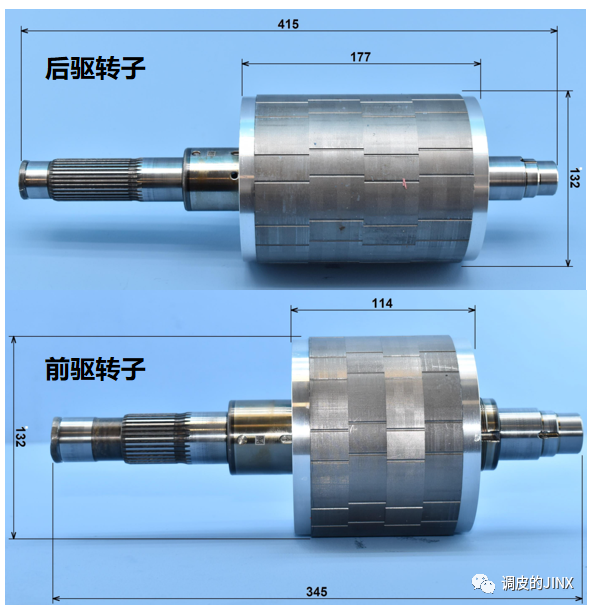
以后驱电机转子进行说明,电机轴和动平衡板均开孔,油冷的可能性非常大。但由于没有更详细的局部特征,暂不进行深入。
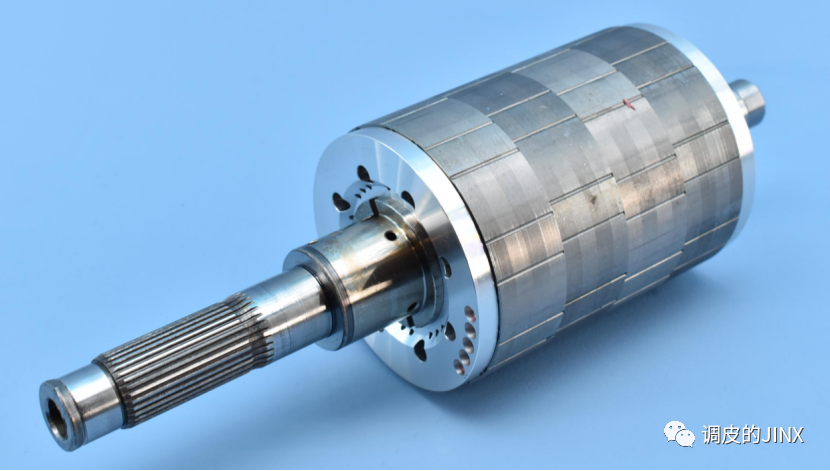
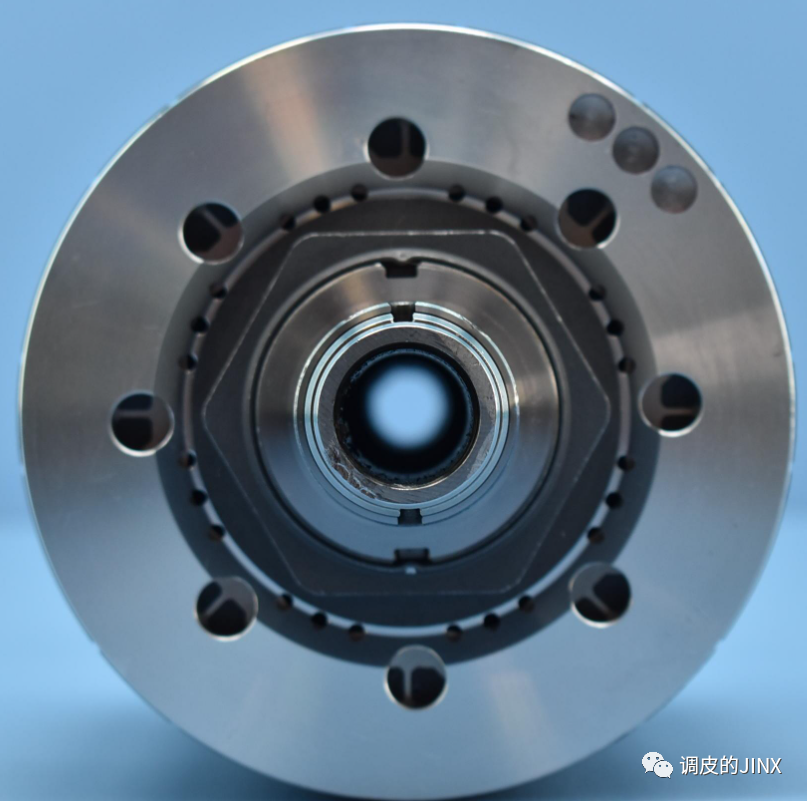
对比前驱、后驱电机定子,可以发现后驱电机并不像前驱电机一样常规的“三相出线”,而是独特的“四相出线”。通过早期文章的介绍,我们知道“四相出线”实际上是将电机中性点引出,目的是为了“升压”充电。E-GMP选用功率更大的后驱电机进行升压。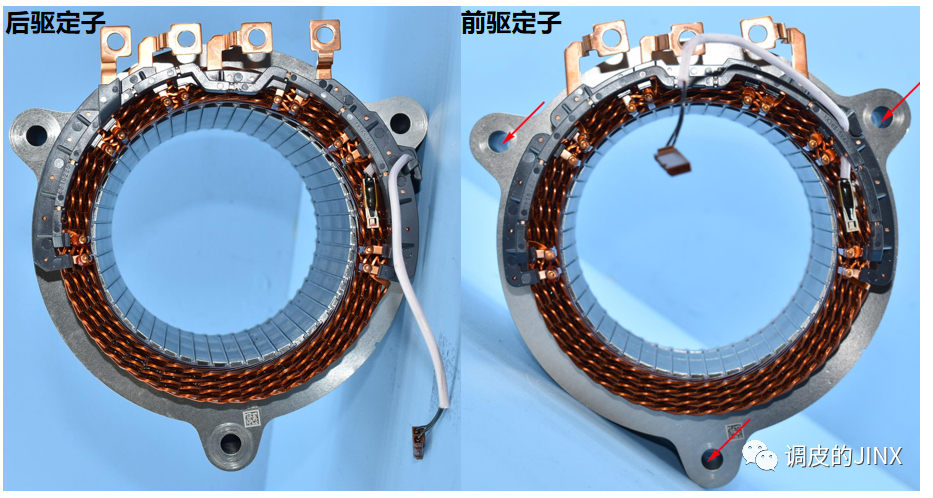
首先,电机出线的4PIN固定在电机绝缘座上。
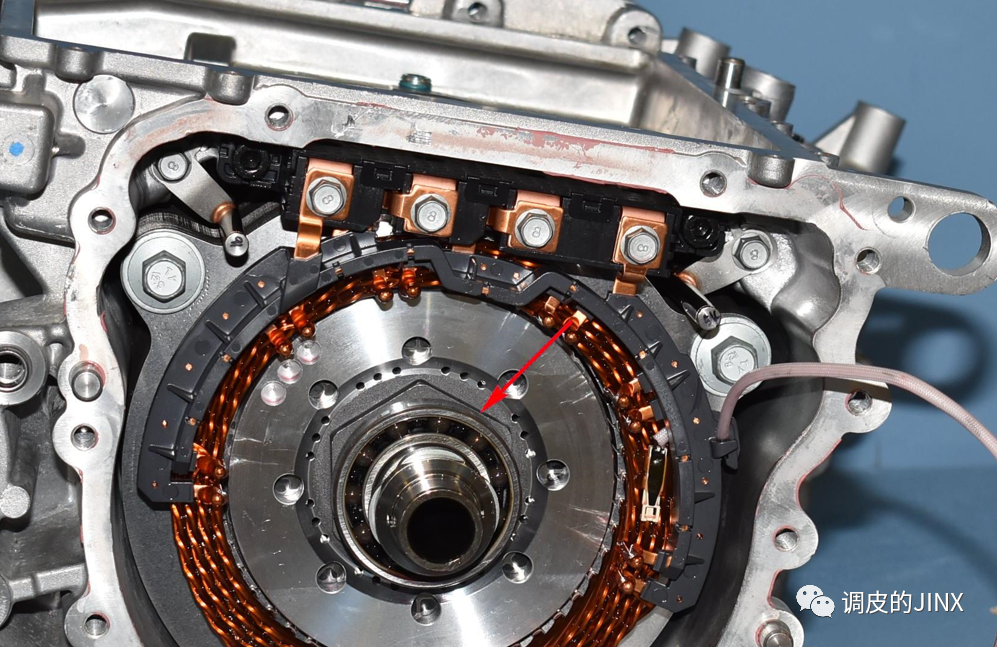
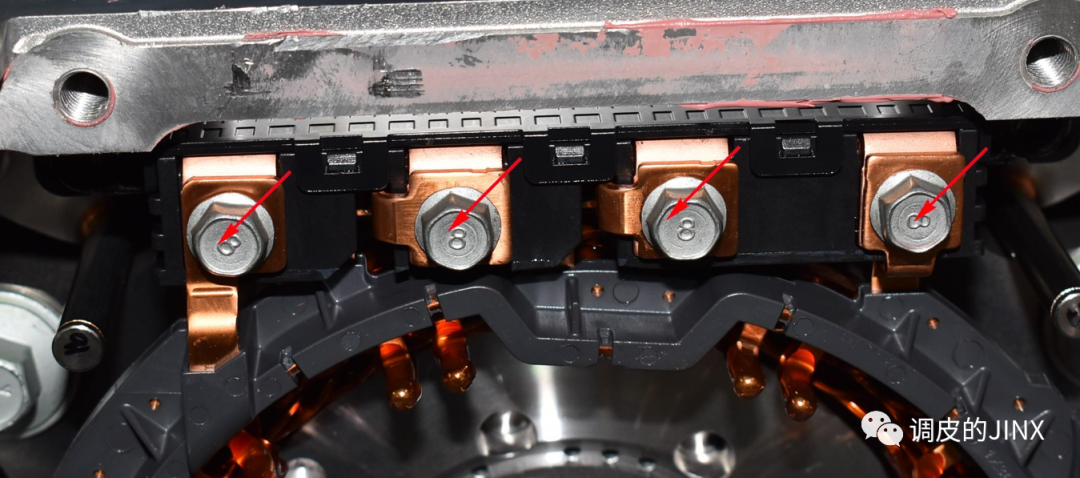
需要注意的是,此处的E-GMP的高压连接比较独特。电机绝缘座铜牌与塑料不是一体注塑,塑料与铜牌分开,通过卡扣实现组装固定。制造难度降低,装配稍微复杂点。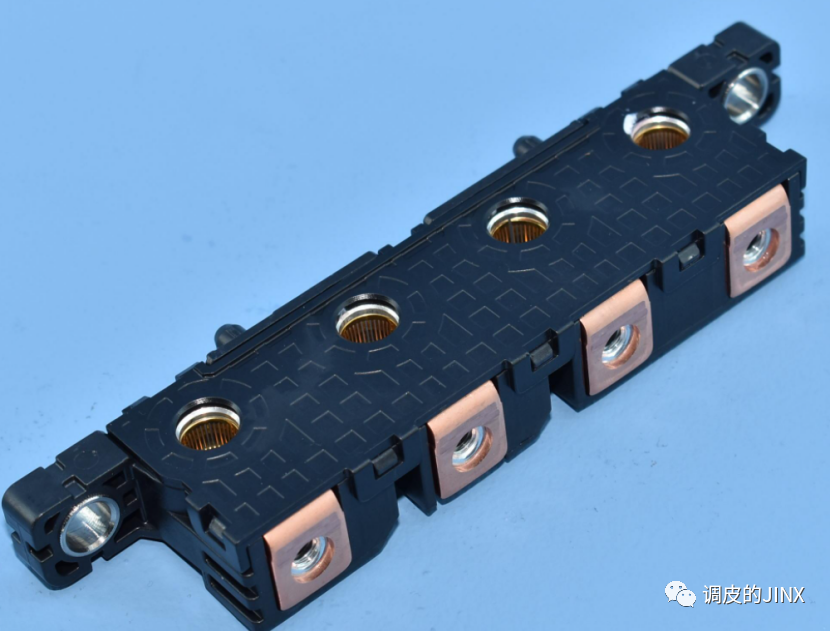
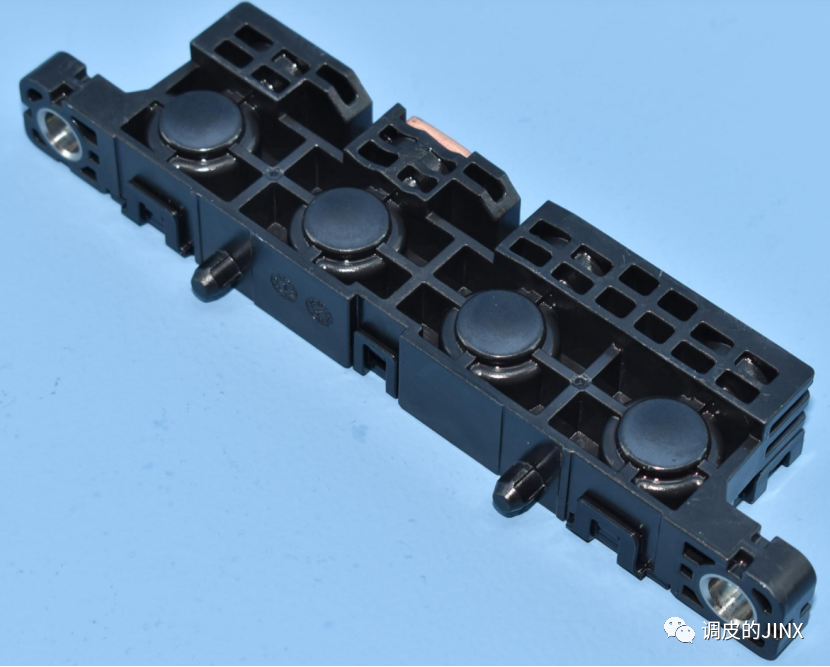
然后,控制器三相与电机绝缘座上三相连接。在这里,控制器三相不再是铜牌,而是导电柱。这种设计给原本自由度不足的高压出线难题提供了新的思路。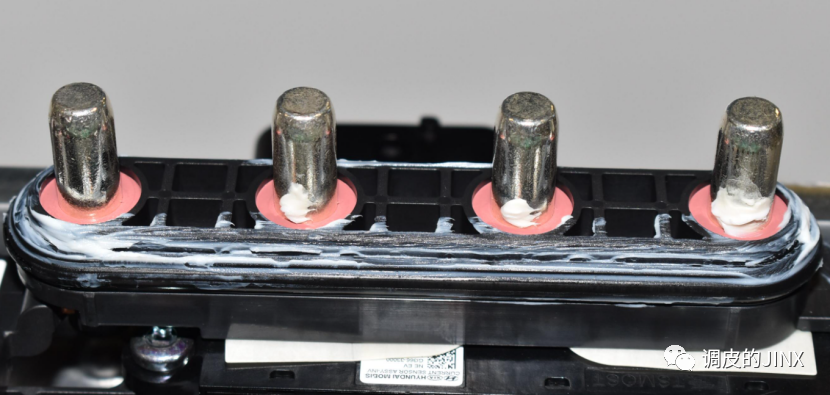
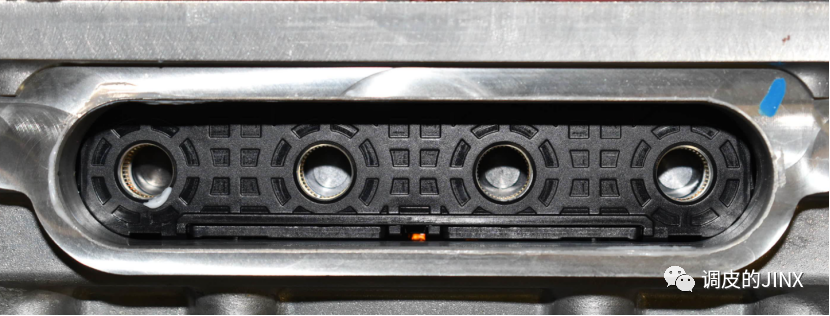
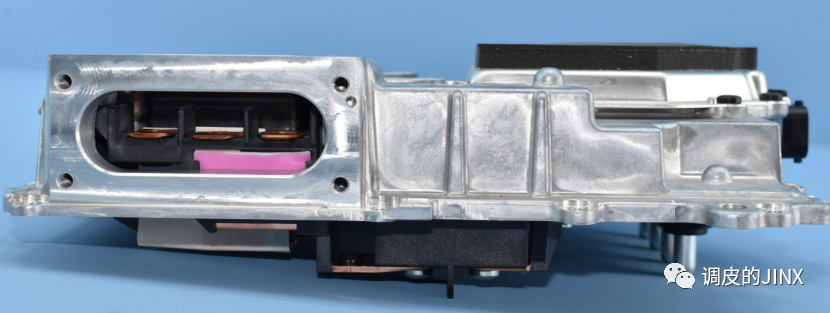
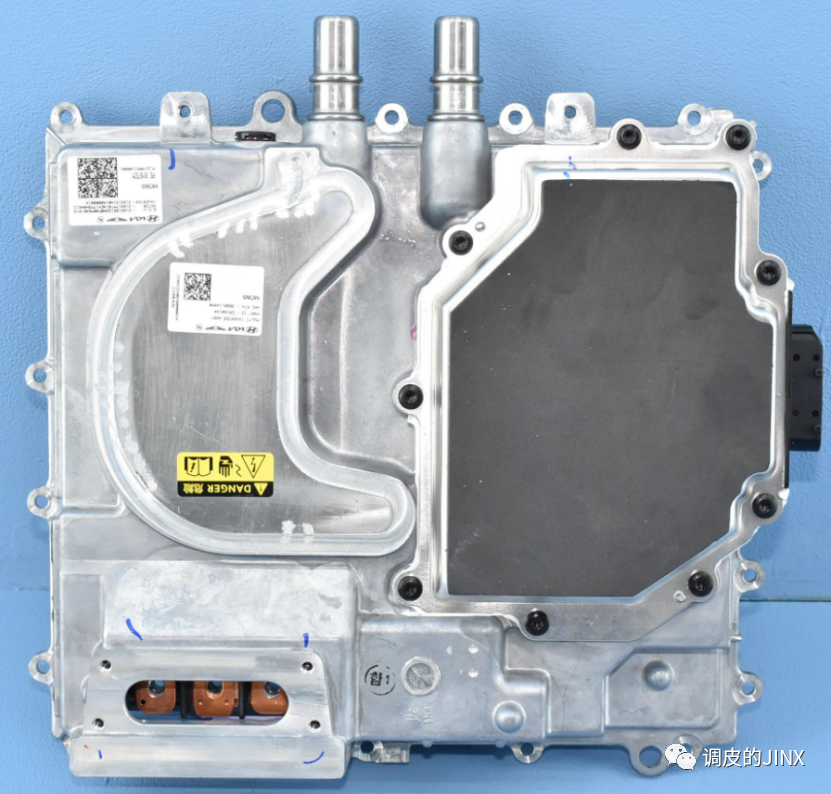
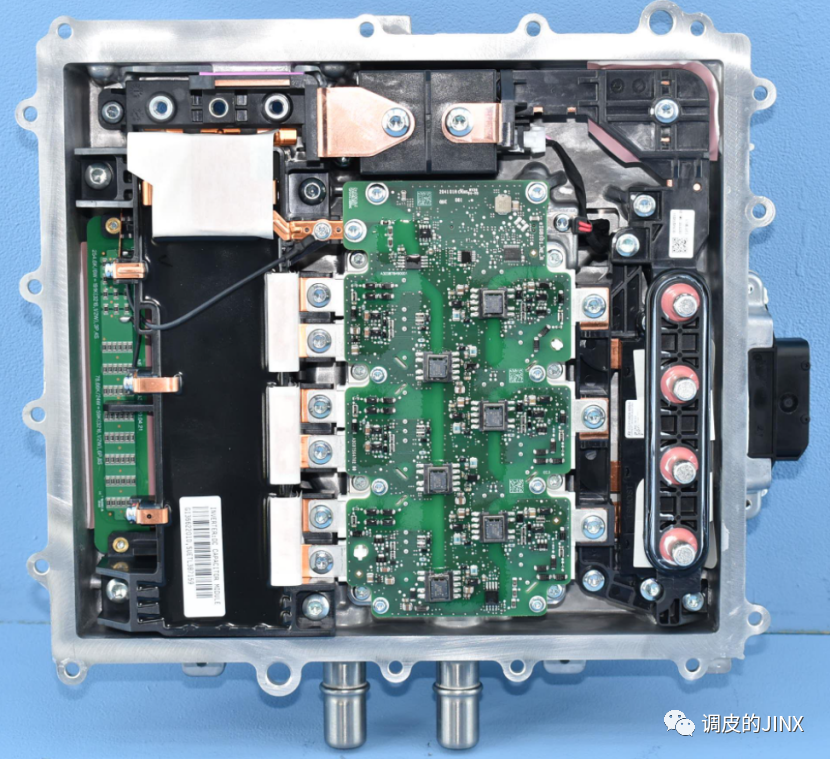
最后,充电机与电机控制器直连。充电机、控制器、电机、齿轴、壳体最终形成高度集成。
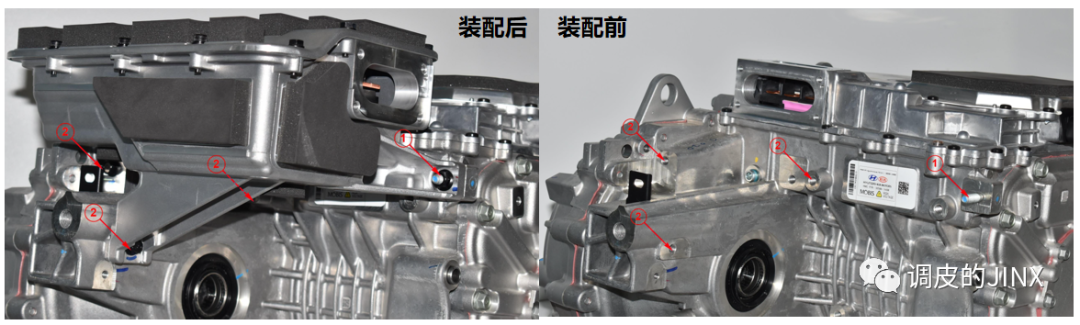
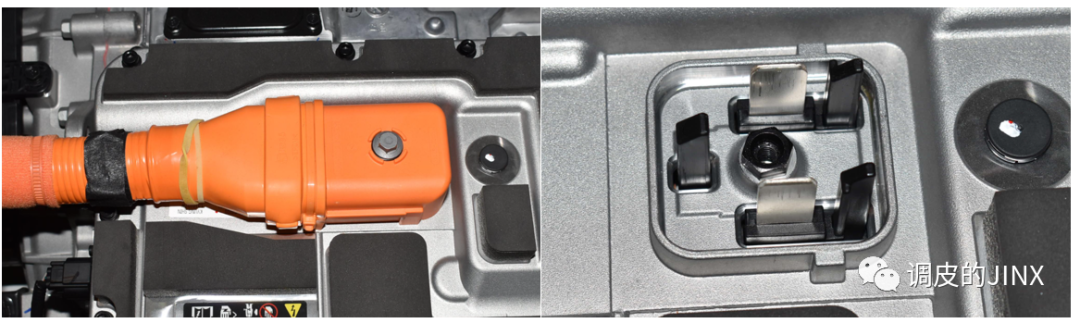
通过电机进行升压,背后的动因是为了使800V系统能够兼容400V的充电桩。这种做法并不是只有E-GMP在做,已量产的产品还有比亚迪汉。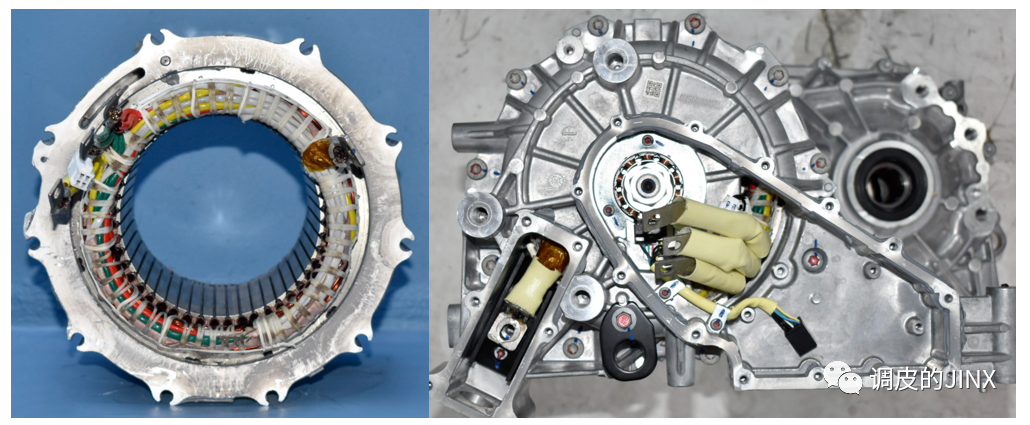
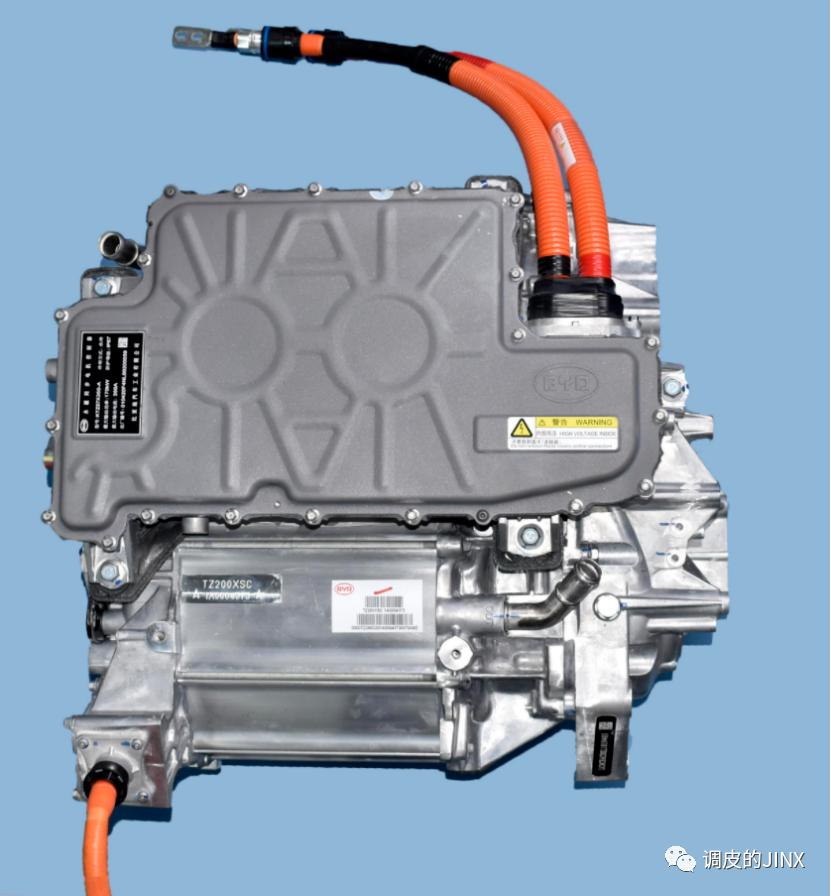
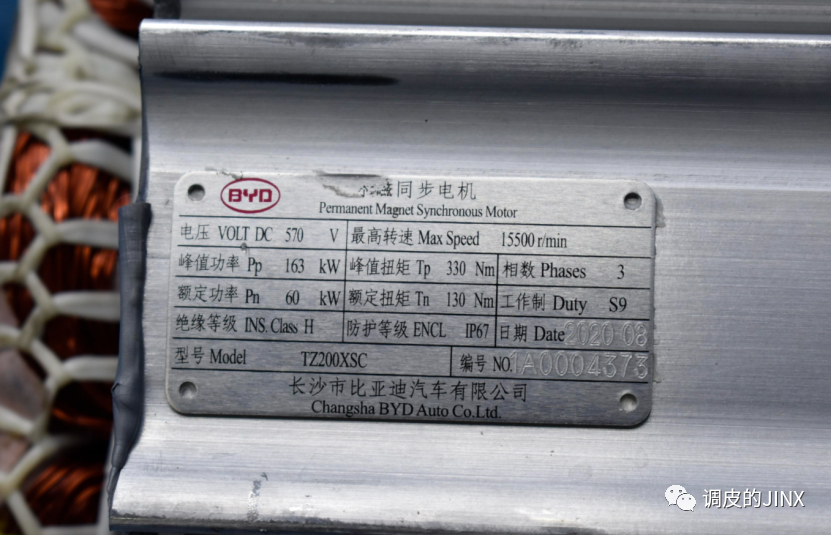
与现代相比,比亚迪汉的升压方案更加直接明了。从EDU直接拉出一条高压线(一头接电机中性点)直接插入充电器。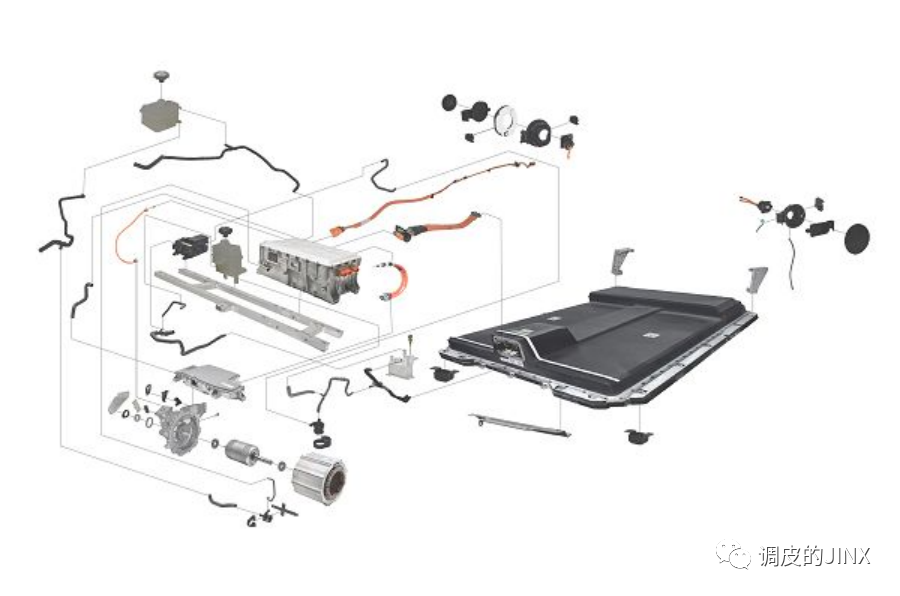
现代E-GMP采用的是Semitec旋变,旋变定子与壳体之间有一个金属薄壁件。它的作用是“隔磁”。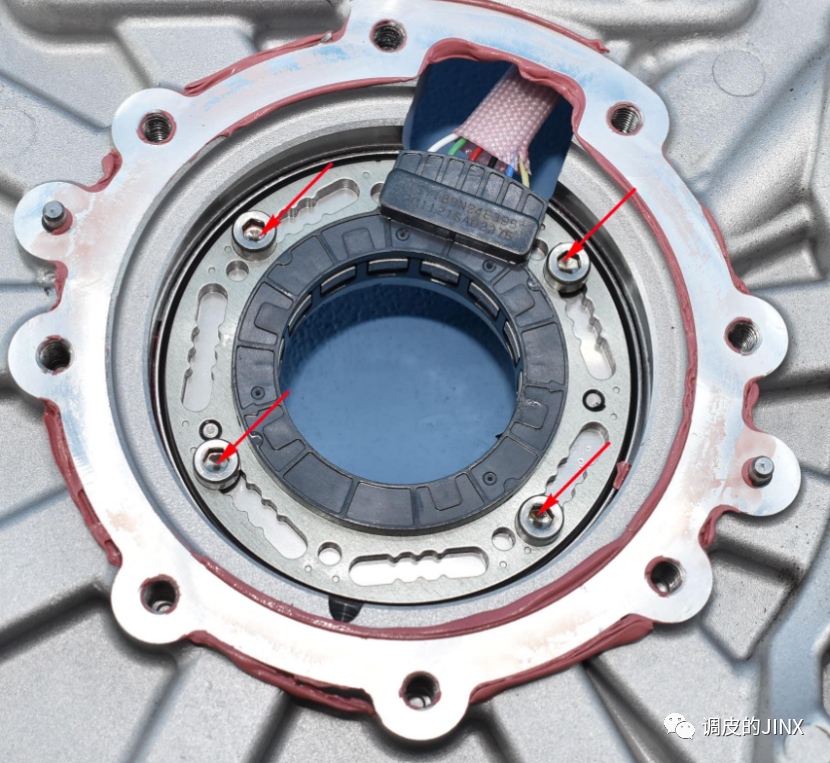
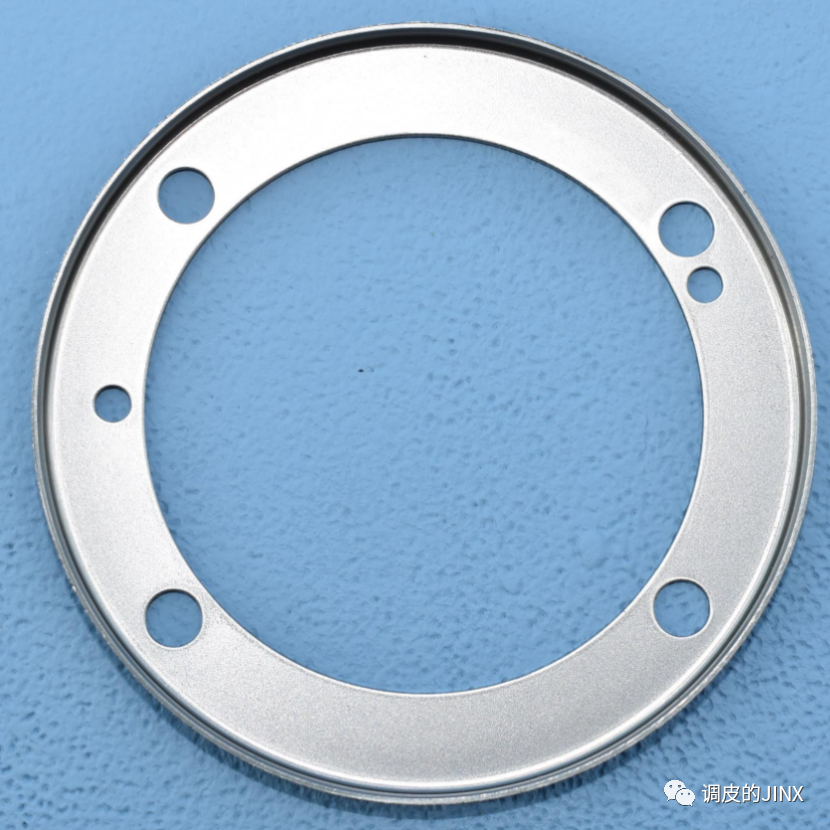
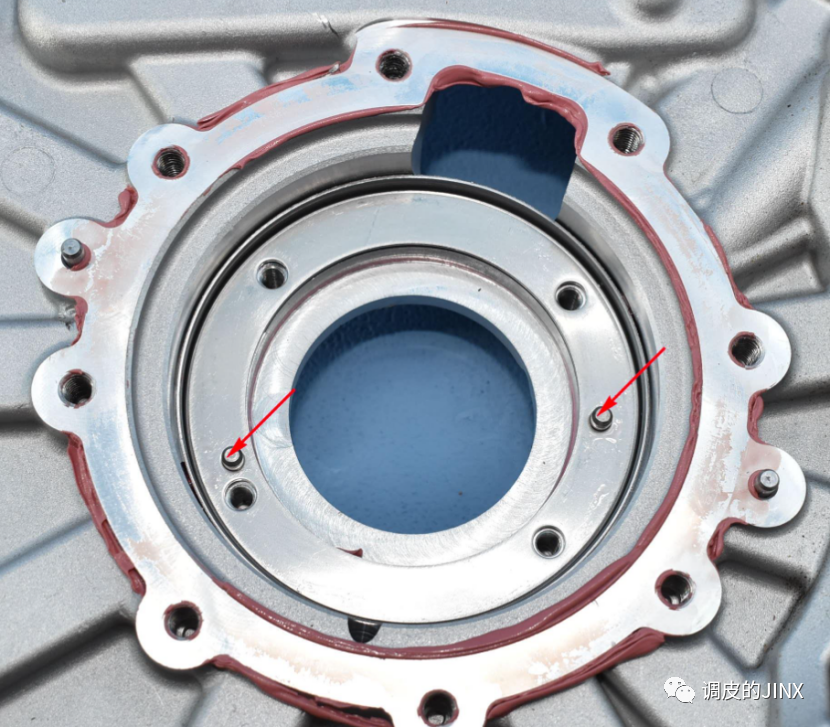
任何介质对外磁场都有响应。有些材料响应较弱,我们称之为弱磁性,如:顺磁性、反铁磁性物质;有些材料响应较强,我们称之为强磁性,如:铁磁性、亚铁磁性物质;当然还有一些是特殊响应,如抗磁性(磁化率为负)。我们所熟知的铁、钴、镍等都属于强磁性物质,对磁场有较强响应,可以被磁铁吸引。旋变这个隔磁套隔磁的原理就是磁力线都跑到这种材料内部去了,不愿意去其他地方,因此也就隔磁了。与上期文章中电机隔磁桥的原理是一样的。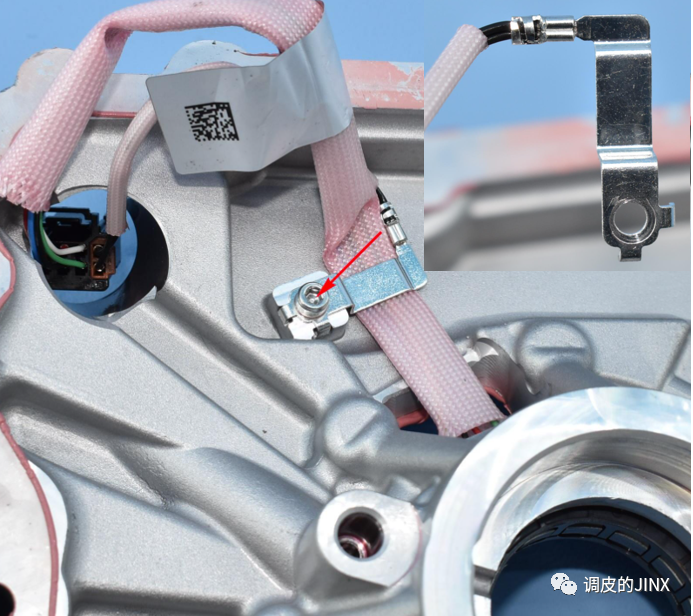
除了旋变,另外一个需要关注的零件就是防轴承电腐蚀的导电环。关于轴承电腐蚀相关知识,可翻阅之前文章,此处不做拓展。前驱电机和后驱电机均采用了该解决方案。从结构来看,属于Aegis SGR系列产品。
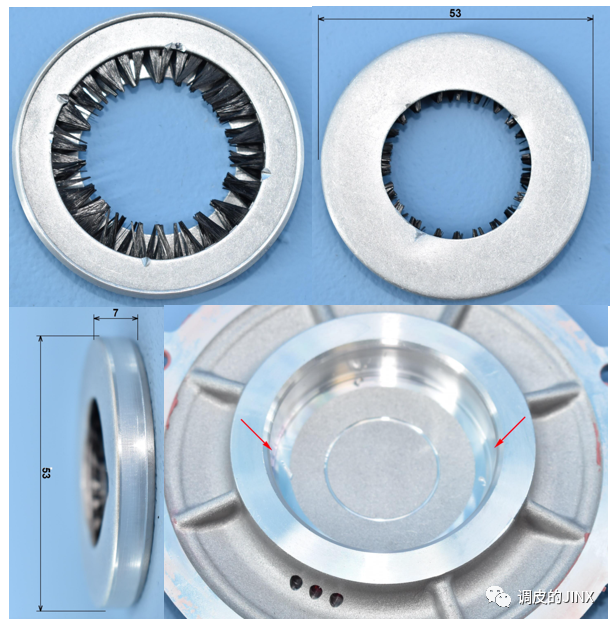
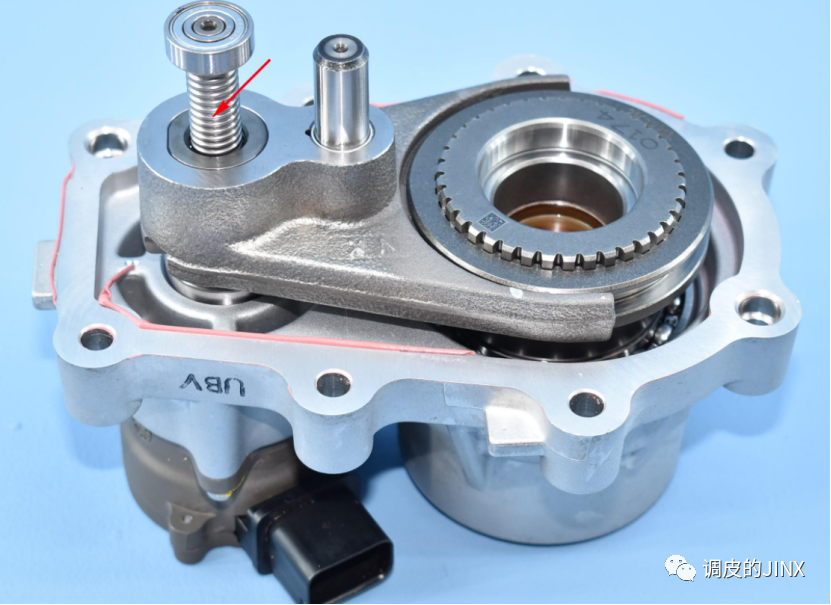
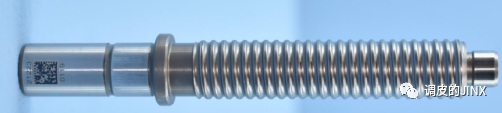
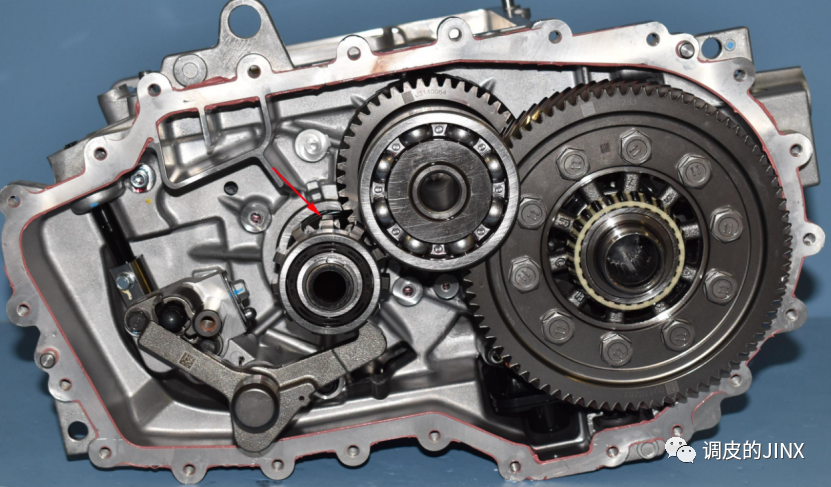
最后,再来看下电机定子。Busbar采用PPS-(GF+MD)50。除了增加玻纤增加强度以外,还增加了增韧剂提高韧性,减少温度冲击带来的开裂风险。当然,目前常用的PPS+40GF也是比较好的选择。从结构上看,Busbar兼备集油分流的作用。
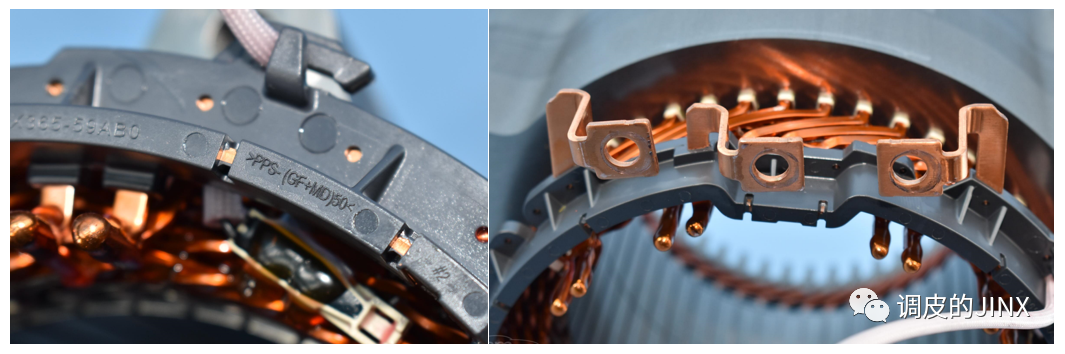
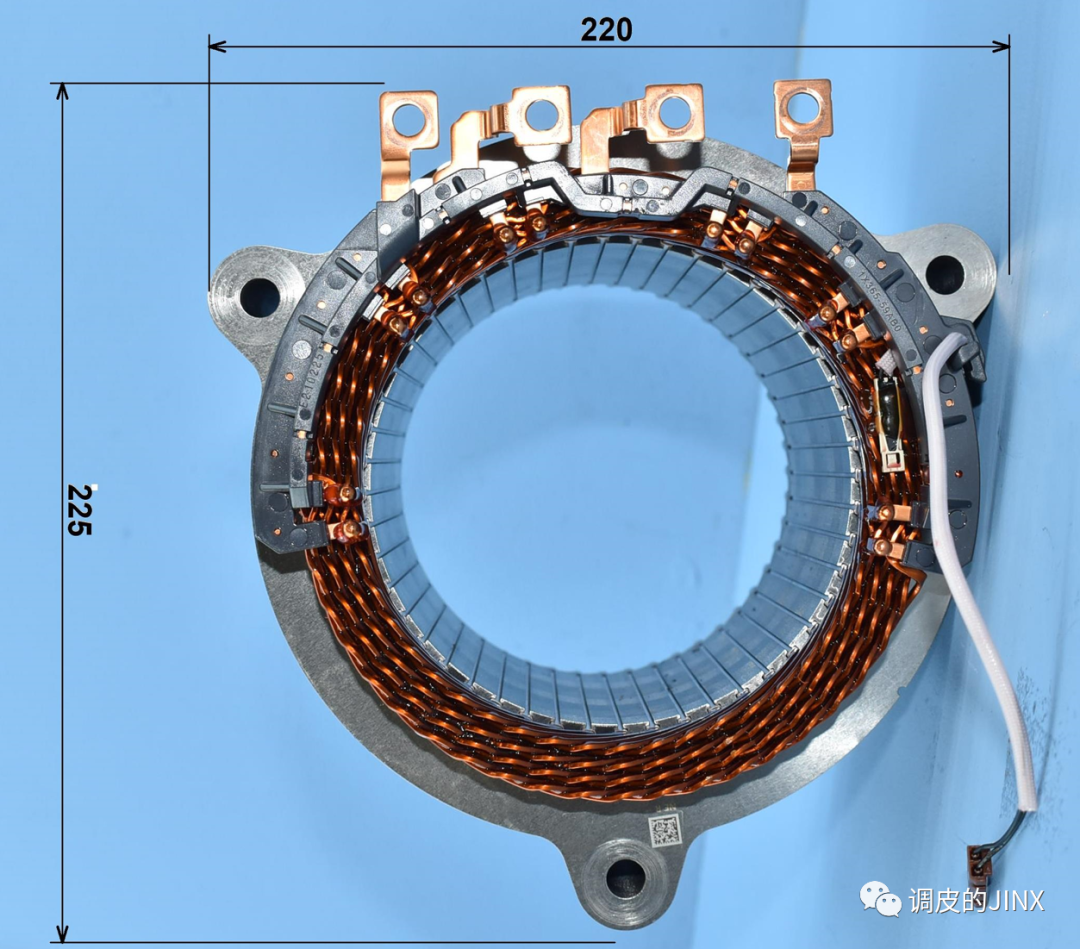
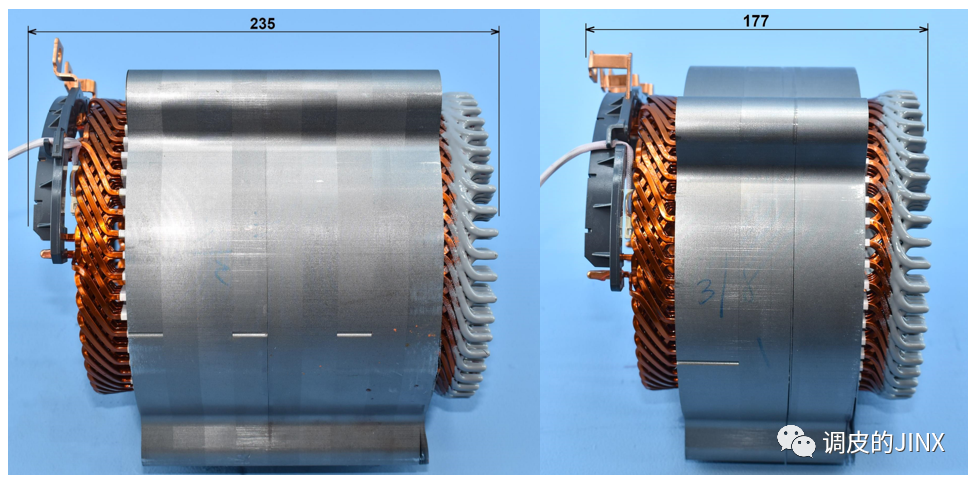
来源:电动新视界
来源:电动新视界