铝合金前罩外板前挡表面质量改善方案
文章来源:《锻造与冲压》2024年第24期(点击阅读整本杂志)
许文, 张玉成, 江庆顺, 雷洋, 聂国成·重庆赛力斯新能源汽车设计院有限公司
随着汽车行业竞争越来越激烈,车身钣金件的自动化生产程度越来越高,外覆盖件的表面质量和尺寸稳定性对车身外观匹配影响极大,表面质量和产品尺寸越稳定,车身造型就可以更好的体现出来,才能更快更好的上市销售,从而赢得广大汽车消费者的欢迎。通过对铝合金覆盖件的研究,以铝合金前罩外板为例,根据NC 数据阶段的CAE 分析结果,在理论分析阶段,改善零件的表面质量缺陷,验证回弹补偿方案,将优化的结果进行调试验证,得到较好表面质量的铝合金前罩外板。零件回弹导致质量问题
前罩外板采用的是6 系铝合金,料厚为0.9mm,零件尺寸为1745mm×1375mm×107mm,AutoForm分析模拟结果显示,前挡表面(图1)的自由回弹有较大的回弹值,回弹最大值约为17mm,如图2 所示。支撑回弹时前挡表面的回弹值正负交替,出现类似波浪形的变化,如图3 所示。在零件的生产过程中存在零件回弹合格率低的问题,前挡表面有波浪纹缺陷。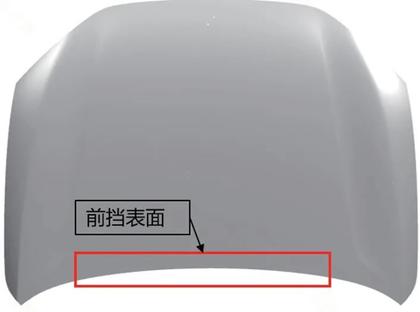
图1 前罩外板前挡表面
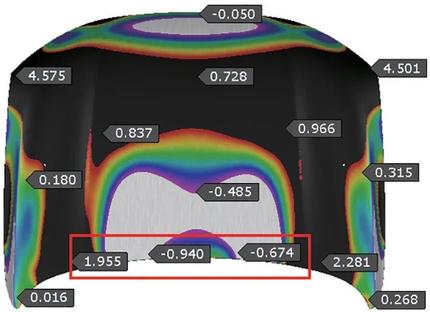
图2 前挡表面的支撑回弹值(红框区域所示)
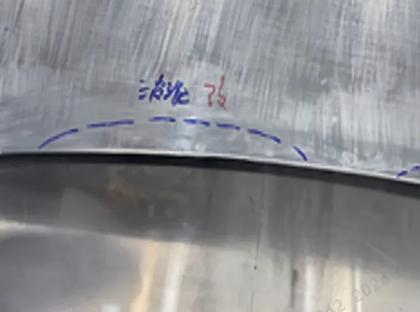
图3 前挡表面波浪纹缺陷
缺陷产生原因分析
前罩外板成形工序
前罩外板一般经过OP10 拉延、OP20 修边侧冲孔、OP30 修边侧修边、OP40 翻边侧翻边等工序完成成形,受铝板材质特性、成形工艺方案、模具结构设计方案、加工制造工艺、调试工艺等多种因素影响,导致最终成形的零件出现表面质量缺陷。图4 所示为前罩外板经过4 道工序成形,前挡表面在OP10 拉延阶段直接成形,前罩外板扣合边界在经过OP20 和OP30 的修边工序后达到尺寸要求,OP40 通过翻边将扣合前的零件成形到位。拉延后的零件在修边完成后应力释放,会有一个零件的变形,经过了OP40 的翻边工序,最终形成了前挡表面的面品效果(图5),其中翻边造成的回弹为主要原因。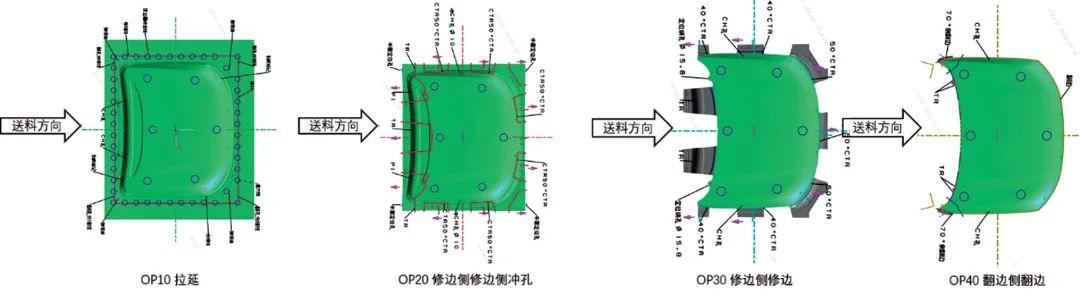
图4 前罩外板成形工序
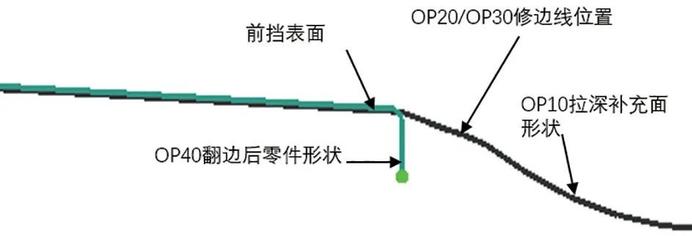
图5 前挡表面拉深、修边及翻边剖面
AutoForm 模拟分析
根据AutoForm 模拟分析结果显示(图6),前挡表面区域的回弹值在OP10 和OP30 为负值,OP20 和OP40 为正值,都是同一方向或正或负,没有出现波浪的变化。在支撑情况下,回弹值出现了正负值交叉情况(图7),与现场实际工序件出现的表面质量缺陷(图8)基本相符。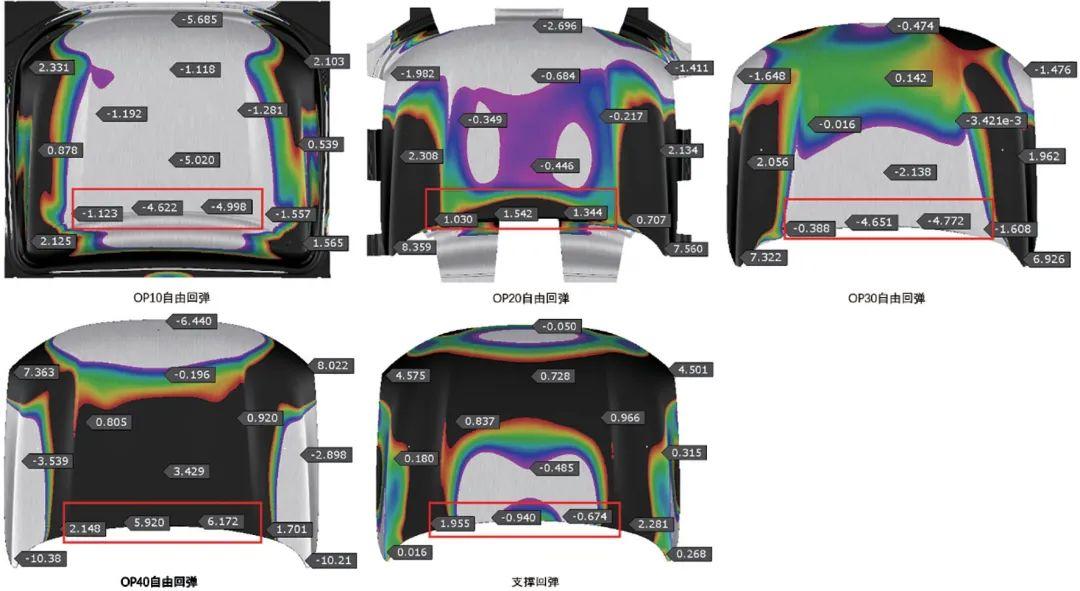
图6 前罩外板前挡表面全工序回弹
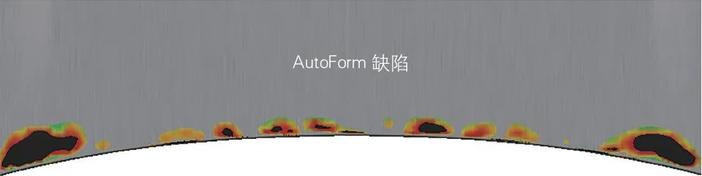
图7 前挡表面AutoForm 理论分析缺陷
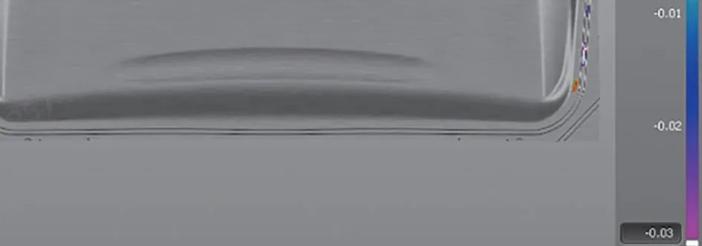
图8 OP10 表面缺陷
整改方案
通过AutoForm 分析软件对零件的全工序进行模拟分析,不断优化并得到理论可行的回弹值,保证零件不会出现波浪且面品达到几乎无缺陷,再从现场对零件进行整改优化。优化理论分析
通过调整OP10 的拉延补充面等参数,使得拉延后的表面缺陷Surface Lows 满足±0.03mm 的合格范围,如图8 所示。然后,调整OP40 翻边镶块的刃入量即刃入顺序,来优化翻边对回弹的影响,使得翻边后的表明缺陷Surface Lows 满足±0.03mm 的合格范围,如图9 所示。优化后的零件自由回弹(图10)和支撑回弹(图11)的值均没有出现正负交替变化的情况,符合要求,可以进行回弹补偿,通过补偿后的值也未产生明显波浪形状的变化,达到了回弹值±0.5mm 的要求(图12)。
图9 OP40 表面缺陷
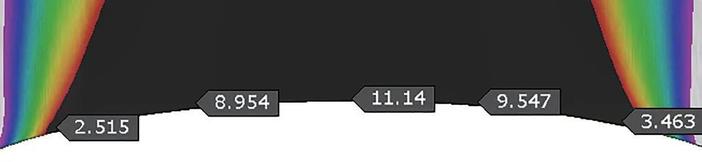
图10 自由回弹值
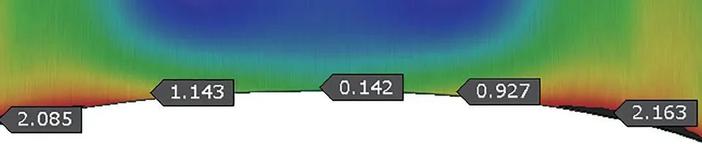
图11 支撑回弹值
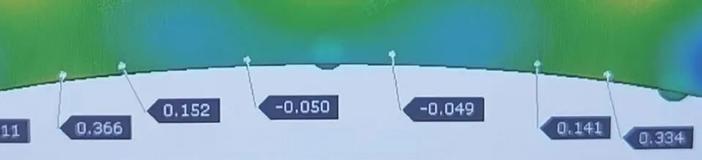
图12 理论回弹值
调试整改
通过更改OP40 压料芯的加工数据,将压料芯在前挡表面区域的压料宽度由原来的110mm(图13)减少至60mm(图14),从而增加了前挡表面区域的压强,并通过多次研合优化提高研合率至85%以上,从而达到了接近于理论的分析结果。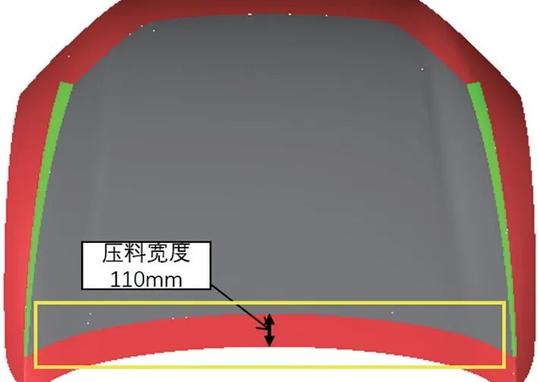
图13 前挡表面原压料面宽度110mm
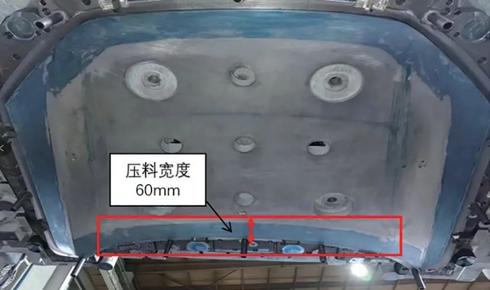
图14 前挡表面压料宽度为60mm 的研合图
通过实施以上整改方案,即利用AutoForm 理论分析验证,同时经过现场调试整改,整改后的零件面品(油石效果)满足质量要求(图15),最终零件无质量缺陷(图16)。
图15 油石效果图
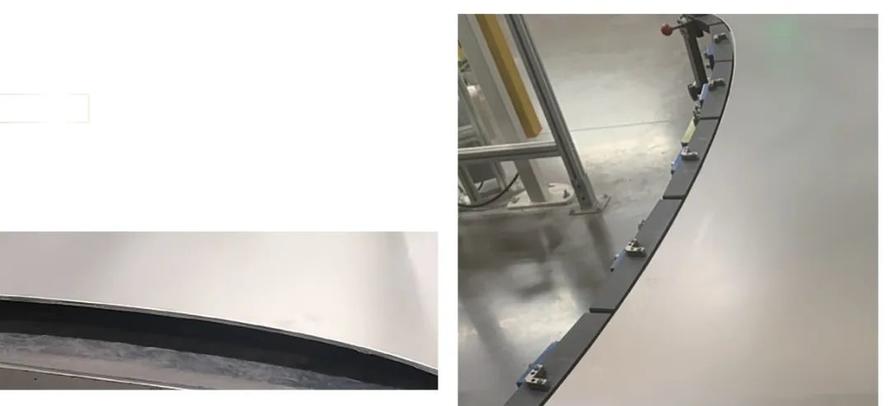
图16 产品效果图
结论
⑴优化表面缺陷参数Surface Lows 满足±0.03mm的合格范围,同时回弹值达到±0.5mm 的要求,满足了产品在理论分析后无波浪形状;⑵降低翻边工序前挡表面的压料面宽度,从而增加压料强度,提升研合率,进一步抑制了波浪纹的产生,提升面品质量。
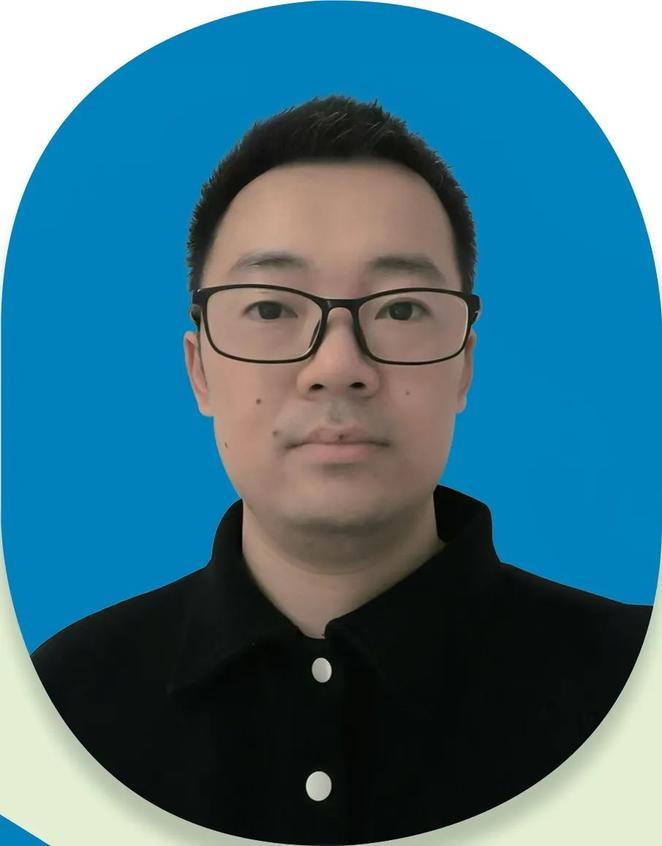
许文
重庆赛力斯新能源汽车设计院有限公司冲压工程部冲压工艺工程师,机械设计制造及其自动化专业毕业,15 年冲压钣金件开发经验,负责开发的冲压件数量超过100 种,具备丰富的铝材、冷轧钢材、高强钢板等材质的冲压件开发经验。
来源:《锻造与冲压》杂志
编辑:贾亚莉
审核:冯忠