从油冷到超导:一文看透电动车电机技术路线之争
一. 轴向磁通永磁电机
技术原理:
与传统径向磁通电机(磁场方向垂直于转轴)不同,轴向磁通电机的磁场方向平行于转轴,采用盘式结构,定子和转子以轴向堆叠方式排列。这种设计大幅缩短磁路长度,减少磁阻损耗,同时允许更高的绕组填充率。
核心优势:
功率密度
:可达5.8 kW/kg(传统电机约3.2 kW/kg),体积缩小30%,适用于空间紧凑的车型。 效率
:在宽转速范围内效率提升3%~5%,尤其适合高扭矩需求场景(如越野或高性能车)。 散热能力
:双面散热设计可降低温升15%,支持持续高功率输出。
应用案例:
法拉利SF90 Stradale
:采用英国YASA公司轴向磁通电机,系统峰值功率达160kW,助力车辆0-100km/h加速仅需2.5秒。
挑战:
制造成本
:精密叠片工艺要求高,量产成本较传统电机高20%~30%。 供应链成熟度
:全球仅少数企业(如YASA、Magnax)具备规模化生产能力。
未来前景:
预计2025年后,随着冲压工艺改进和材料成本下降(如无取向硅钢应用),轴向磁通电机将逐步渗透至30万元级乘用车市场。
二. 轮毂电机分布式驱动
技术原理:
将电机直接集成至车轮内部,通过电子控制实现每个车轮独立驱动,取消传统传动轴、差速器等机械部件。
核心优势:
空间利用率
操控性能
:扭矩矢量控制精度达±0.5°,支持“坦克转向”、“螃蟹模式”等特殊行驶功能。 能量回收效率
应用案例:
ProteanDrive轮毂电机
:已在英国Arrival电动商用车中应用,单电机峰值功率75kW,系统总质量仅36kg。
挑战:
簧下质量
:增加非簧载质量可能影响悬架响应,需匹配主动悬架系统(如CDC连续阻尼控制)。 密封与散热
:IP67防护和油冷散热设计增加成本,量产难度较高。
未来前景:
商用车和高端乘用车率先应用,2025年后线控底盘技术成熟将推动普及。
三. 第三代半导体(SiC/GaN)电驱系统
技术原理:
碳化硅(SiC)和氮化镓(GaN)材料具有高击穿电场、高热导率特性,可制造高频、高温、低损耗的功率器件。
核心优势:
效率提升
:SiC MOSFET逆变器损耗较硅基IGBT降低70%,电机系统效率突破97%。 高压适配
:支持800V平台,充电效率提升30%(如保时捷Taycan的800V架构)。 轻量化
应用案例:
产业化进展:
中国已形成完整SiC产业链(如三安光电、天岳先进),2024年国产6英寸SiC晶圆成本降至400美元/片,推动渗透率快速提升。
四. 非稀土永磁材料
技术原理:
通过改进铁氧体磁性或开发新型复合磁材(如钕铁硼+铁氧体),减少对稀土元素的依赖。
核心优势:
成本优势
资源安全
:中国稀土储量占比37%,但面临国际供应链风险,非稀土技术可提升产业链韧性。 高温性能
:某些铁氧体材料在150℃下退磁率低于5%,适用于高温环境。
应用案例:
广汽钜浪混动系统
:采用低成本铁氧体电机,磁能积提升至45MGOe(接近低端钕铁硼水平)。 日本日立金属
:开发出“无重稀土”钕铁硼磁体,耐高温性能提升50%。
挑战:
磁性能瓶颈
:铁氧体磁能积上限约50MGOe,难以满足高端车型需求。 工艺复杂度
五. 智能控制算法——多目标实时优化控制
技术原理:
基于模型预测控制(MPC)和数字孪生技术,动态调整电机参数以适应不同工况。
核心优势:
能耗优化
:高速巡航时,通过弱磁控制降低铁损,综合能效提升5%。 热管理
:实时预测绕组温度,调整冷却策略,峰值功率持续时间延长20%。
案例:
蔚来ET7
华为DriveONE
:采用AI寻优算法,电驱效率MAP图覆盖率达92%。
六. AI驱动的健康管理
技术原理:
利用机器学习分析振动、电流信号,实现故障预测与寿命优化。
核心优势:
故障预警
:LSTM网络预测轴承故障,准确率超92%,减少非计划停机。 寿命延长
案例:
特斯拉OTA升级
:2023年通过软件更新优化电机控制逻辑,召回风险降低70%。 西门子Sidrive IQ
七、全域高效热管理技术
技术原理与分类
双面油冷技术
成本增加
:需高精度油泵和密封设计,系统成本提高8%~12%。 维护复杂度
持续功率提升
:相比传统水冷技术,持续输出功率提高25%(如蔚来ET7搭载该技术后电机峰值功率达480kW)。 温升控制
:定子绕组温升降低15~20℃,允许更激进的控制策略(如连续弹射模式)。
原理
:在电机定子绕组内部布置冷却油道,同时对转子轴心进行喷油冷却,实现定子和转子的同步高效散热。
相变材料散热技术
循环寿命限制
:相变材料经过5000次相变后储热能力下降10%~15%。 低温启动问题
瞬态热冲击缓冲
:在急加速或高负荷工况下,可吸收200kJ/kg热量,延缓温升速率达40%。 轻量化
:相比传统散热片,重量减少30%(如宝马iX电机采用该技术减重5.2kg)。
原理
:在电机外壳或定子槽内填充石蜡基、金属有机框架(MOF)等相变材料,通过吸热熔化实现缓冲散热。
应用前景:
短期
(2025年前):双面油冷技术将在30万元以上高性能车型普及(如特斯拉Plaid、蔚来ET9),渗透率预计达35%。 长期
(2030年):相变材料与液冷结合方案将成为主流,尤其在800V高压平台车型中解决局部过热问题。
八、多合一电驱系统
技术原理
将电机、减速器、逆变器、DC/DC转换器、车载充电机(OBC)、PDU(电源分配单元)、VCU(整车控制器)、BMS(电池管理系统)等模块高度集成,形成紧凑化电驱总成。
核心优势:
体积与重量优化
:比亚迪八合一系统体积减少40%,重量降低20%,功率密度达2.5kW/kg。 效率提升
:减少线束长度后能量传输损耗降低3%,综合效率突破91%(如华为DriveONE系统)。 成本控制
:模块化生产使制造成本下降15%,装配工时缩短50%。
劣势:
维修难度
:高度集成导致故障件更换需整体拆卸,维修成本增加30%。 热管理挑战
:紧凑布局下局部热点温度可能升高8~10℃,需强化散热设计。
应用前景:
乘用车市场
:2025年多合一系统在A级及以上车型渗透率将超60%,比亚迪、特斯拉、吉利为主要推动者。 商用车适配
:重卡领域因空间限制较少,推广速度较慢(预计2030年渗透率30%)。
九、超导电机技术
技术原理
利用超导材料在低温下零电阻特性,制造高电流密度线圈,大幅提升功率密度和效率。
核心优势:
功率密度跃升
:MgB₂超导线圈在20K(液氮温区)下扭矩密度达200Nm/kg(传统电机约30Nm/kg)。 效率突破
:无电阻损耗使电机效率理论值接近99.5%,实际工程化目标为98%。 轻量化
:同等功率下重量仅为传统电机1/3,适合飞行汽车等特殊场景。
劣势:
制冷系统复杂
:液氮循环装置增加体积(占电机系统40%)和能耗(制冷功耗占输出功率5%)。 成本高昂
:超导材料+制冷系统成本为传统电机10倍以上,商业化难度大。
应用前景:
短期试验
:丰田计划2025年推出搭载超导电机的燃料电池重卡原型车,续航提升至1000km。 长期潜力
:若高温超导材料(如钇钡铜氧)突破液氮温区(77K),2035年后或进入高端乘用车市场。
十、磁齿轮复合电机
技术原理
通过磁场调制原理实现无机械接触的变速传动,将电机与磁齿轮一体化设计。
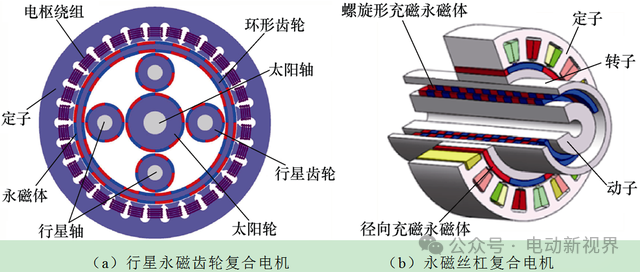
核心优势:
传动效率提升
:取消齿轮摩擦损耗,机械效率达98.5%(传统减速器约95%)。 免维护设计
:无接触传动避免润滑油更换,生命周期维护成本降低70%。 NVH优化
劣势:
转矩密度限制
:当前实验室样机转矩密度仅为50Nm/kg,需提升至80Nm/kg才具竞争力。 控制复杂度
:需开发新型磁场定向控制算法,软件研发成本增加200%。
应用前景:
特定场景突破
:2030年前可能应用于豪华电动车(如劳斯莱斯Spectre迭代车型),主打静音与平顺性。 技术替代路径
:若永磁材料成本下降,磁齿轮技术或逐步替代两档变速器。
十一、可回收电机设计
技术原理
通过模块化结构、易拆解连接工艺和生物基材料,实现电机组件的高效回收与再利用。
核心优势:
稀土回收率提升
:分段式磁钢设计使钕铁硼回收率从60%提升至95%(宝马iX电机实测数据)。 碳足迹减少
:生物基绝缘材料(如聚乳酸)全生命周期碳排放降低40%。 法规适应性
:满足欧盟《新电池法案》对电机回收率≥90%的要求,避免贸易壁垒。
劣势:
性能妥协
:可拆卸结构导致定子刚度下降10%,高速振动风险增加。 成本上升
:模块化设计使制造成本提高8%~12%,需规模效应摊薄。
应用前景:
政策驱动市场
:欧盟、中国等法规严格地区将率先普及,2027年回收型电机占比或超25%。 材料创新突破
:石墨烯增强生物基材料有望将耐温等级提升至200℃,拓展至高性能车型。
总结:技术商业化路径与挑战
免责声明:以上观点仅代表作者个人看法,与本平台无关。如有不妥请于30日内联系平台删除或者商讨版权授权事宜。