数值优化在整车轻量化中的应用
“ 轻量化的主要手段包括创新设计、轻量化材料迭代和结构优化设计。其中结构优化设计是基于仿真驱动设计的理念,并结合轻量化设计对结构进行优化设计,结构优化设计主要通过数值优化方法进行基于性能约束的轻量化优化设计,包括拓扑优化、形貌优化、尺寸优化、形状优化、参数优化和多学科优化等等。数值优化是最合理的手段,在不增加成本的前提下进行结构轻量化优化设计”
本文主要介绍数值优化在汽车轻量化优化中的应用。涉及的内容多是数值优化工程师的日常工作内容。亦是数值优化工程师需要掌握的工作技能。
概念设计阶段
概念阶段主要的数值优化分析内容包括拓扑优化分析、SFE参数模型优化分析、梁壳模型优化分析、形貌优化分析等内容。
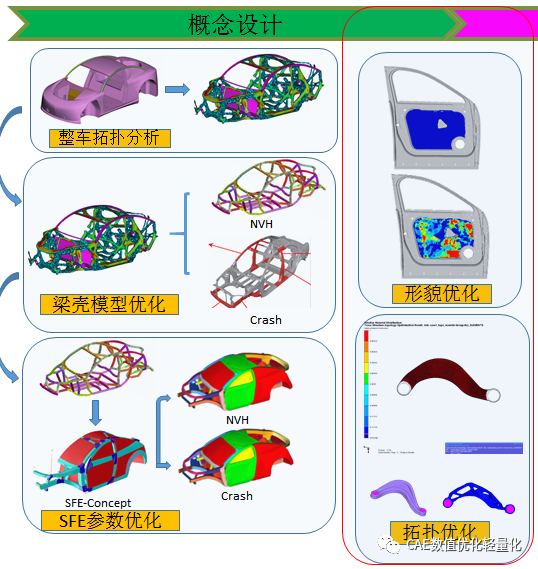
根据外CAS概念数据定义整车拓扑外边界,将布置空间数据(包括座椅、发动机、底盘、行李箱空间等)从整车拓扑空间中去除,形成拓扑设计空间。定义拓扑设计域和非设计域。根据考察的分析工况施加载荷条件并更加不同的工况设置权重因子。最终根据拓扑结果进行方案解读。

A.全局工况:正碰、侧碰、后碰、顶压、弯扭刚度、弯扭模态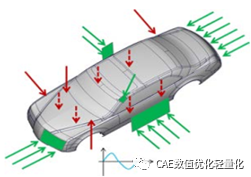
B.局部工况:安装点刚度、接附点动刚度
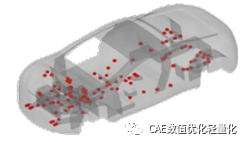
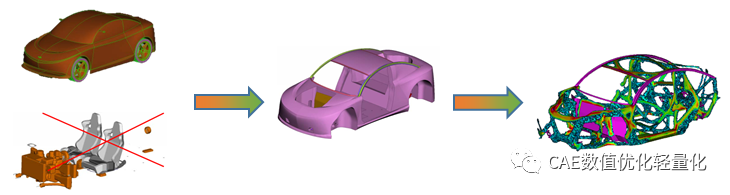
概念阶段只有初步的结构数据,不具备完整的数据用于建立整车有限元分析模型。同时,在这一阶段可能会经常进行方案的调整,完整的有限元模型无法灵活地随着方案变动而做更改。梁壳单元模型具有建模快速、求解时间短,修改方便等特点。在概念设计阶段,可以快速地建立梁单元模型,进行刚度、NVH和碰撞分析。通过对截面形状,截面组成部件料厚以及接头刚度进行灵敏度分析,在保证性能的基础上进行参数化优化。经过参数化优化,求得最优的截面形状和部件料厚,以重量最小为优化目标,进而达到轻量化优化设计的目的。 主要分析步骤:①基于CAD模型创建关键截面→②根据关键截面属性创建梁单元整车模型→③根据对标车的接头刚度修改分析模型的接头属性→④进行静态刚度、NVH、碰撞分析获得基础性能→⑤以接头刚度、截面形状、截面部件料厚等作为设计参数进行灵敏度分析→⑥以接头刚度、截面形状、截面部件料厚为设计变量进行参数优化→⑦针对某特定截面进行参数优化。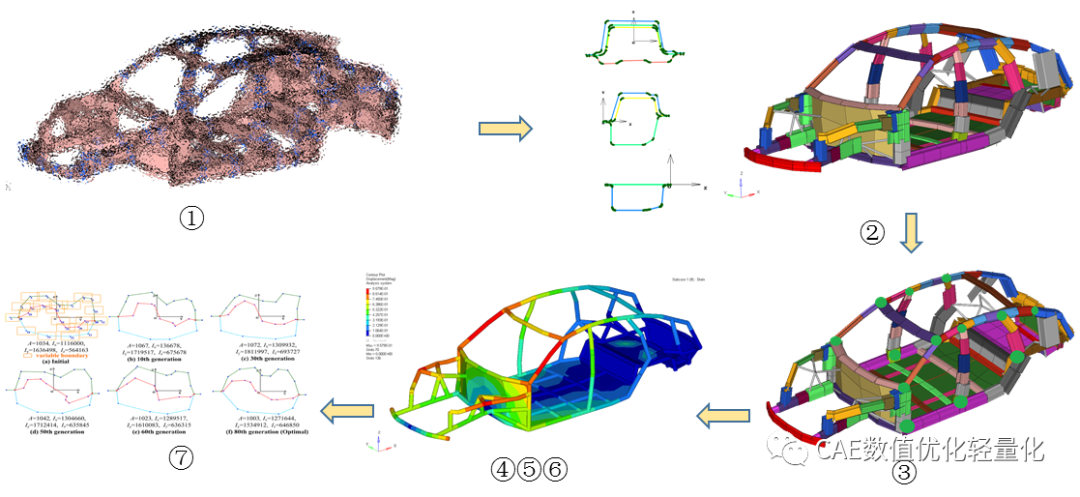
基于Optistruct做优化时的限制:需要进行模型等效.
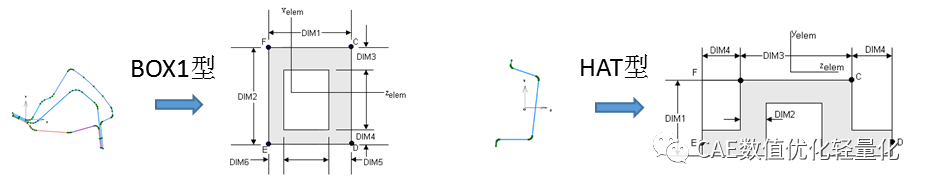
SFE-CONCEPT是一个参数化的CAD工具;可以快速实现模型的变更;同CAE无缝衔接,可以实现设计方案的快速验证分析;极其适合平台开发项目,能快速完成平台衍生车型的更新与迭代分析通过项目累计的截面、接头等数据库对后续车型开发有极大的帮助,大大缩短了开发周期及成本。可以胜任接头优化、详细断面优化、尺寸优化、多学科优化等等。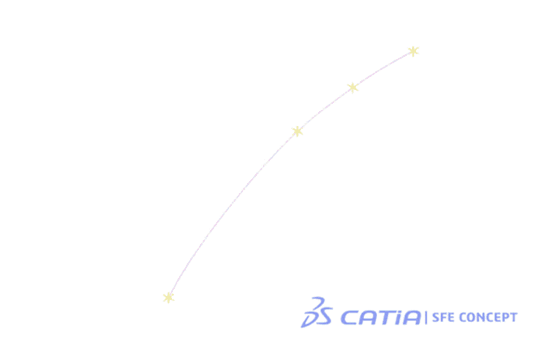
工程设计阶段
工程设计阶段的主要数值优化方法包括形状优化、拓扑优化、尺寸优化、参数优化、多学科优化等。
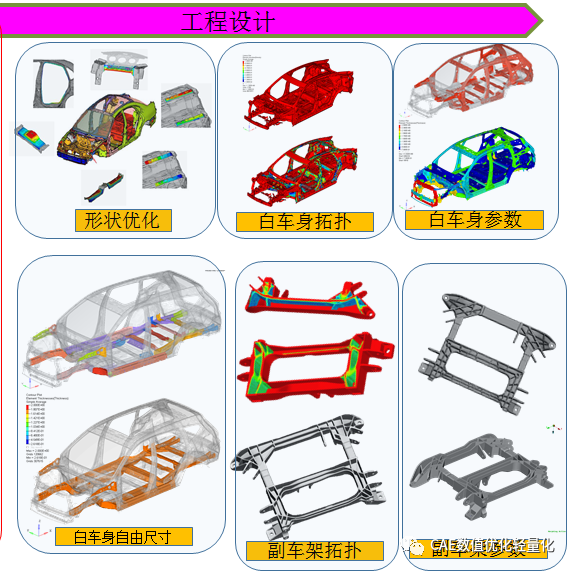
车身参数优化包括针对材料牌号、料厚等优化。针对不同的优化策略可以选择不同的优化方法。基于软硬件资源,对于参数化优化通常使用的是基于梯度算法的Optistruct求解器进行。所以参数化一般只考虑白车身弯扭模态/弯扭刚度。只考察这几项内容如何保证其他性能满足要求?如何保证轻量化方案的有效性?车身的设计是刚度设计、强度校核。良好的白车身弯扭刚度/弯扭模态,是车身强度耐久、NVH性能的基础。在做参数化优化时,对于碰撞关注区域(如正碰的前舱纵梁、前围加强板)、强度耐久关注区域(如前后地板与侧围连接处、前减震塔、后轮毂包)等位置的结构件慎重设置优化范围,其他位置部件合理设置优化范围,即可保证在车身整体刚度/模态性能的基础上其他的性能也得到保证。对于其他点位置,往往是局部的,如静强度/动强度(耐久),静刚度/动刚度往往都是通过局部优化即可。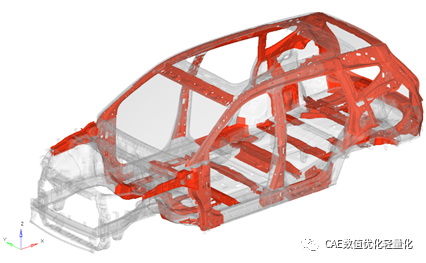
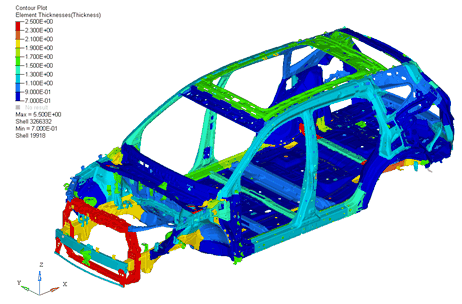
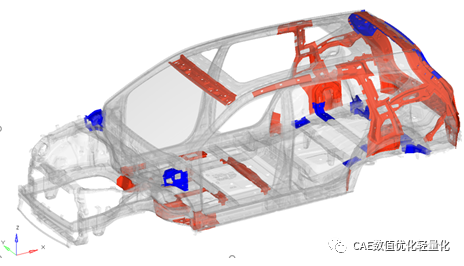
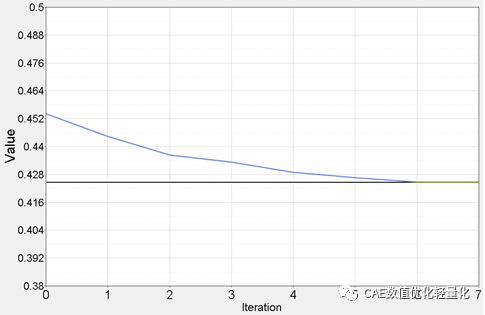
优化对象:所示的带颜色显示的部件
设计约束:1阶扭转模态>xx.x Hz、1阶弯曲模态>xx.x Hz、弯曲刚度>xxxx.x N/mm、扭转刚度>xxxx.x N/mm
设计目标:最小化质量
性能验证:
模态:
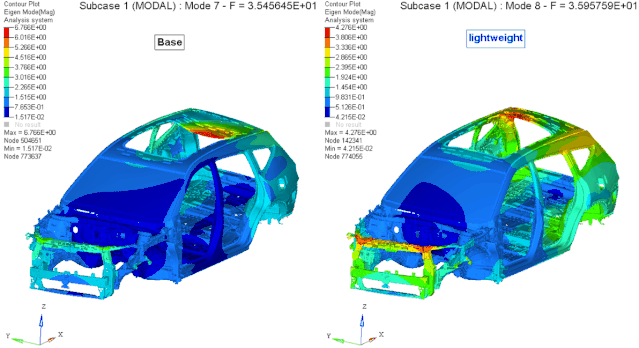
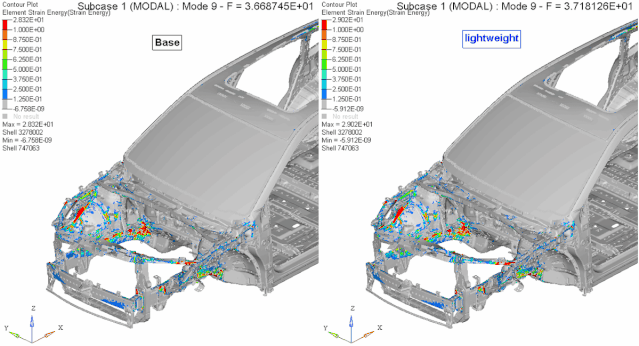
正碰:
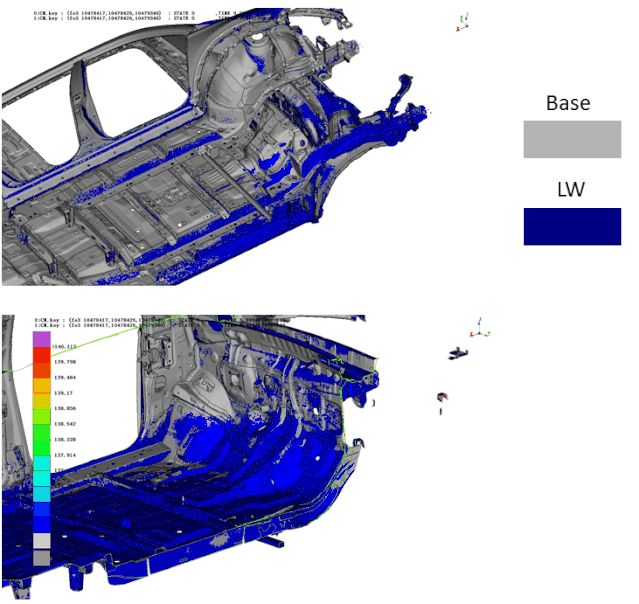
侧碰:
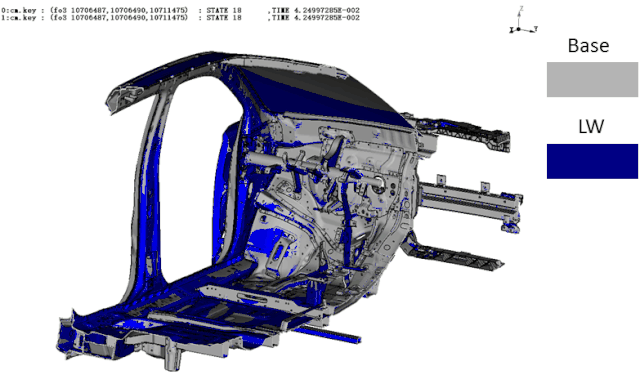
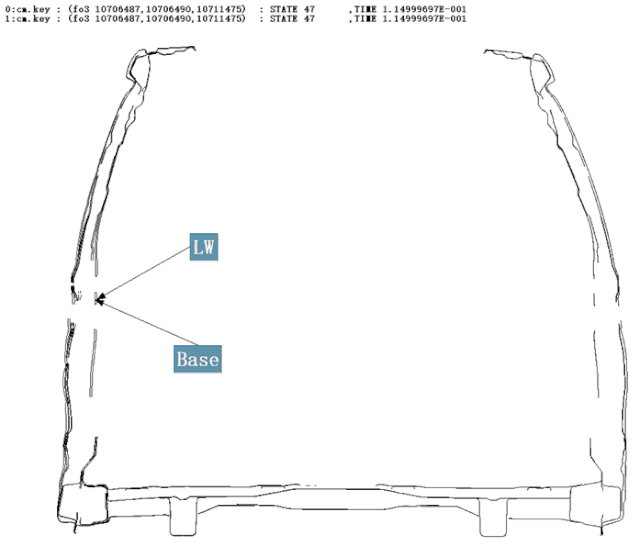
顶压:
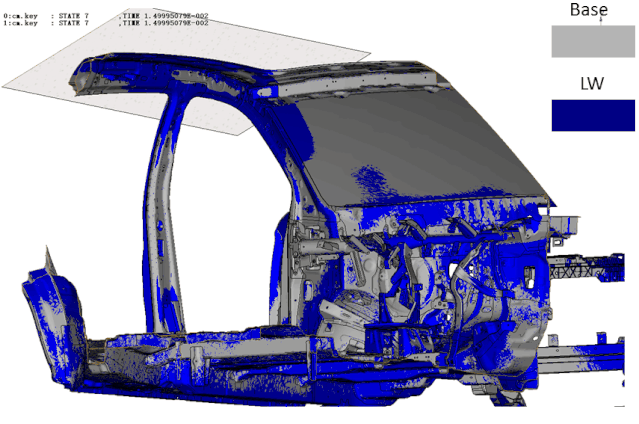
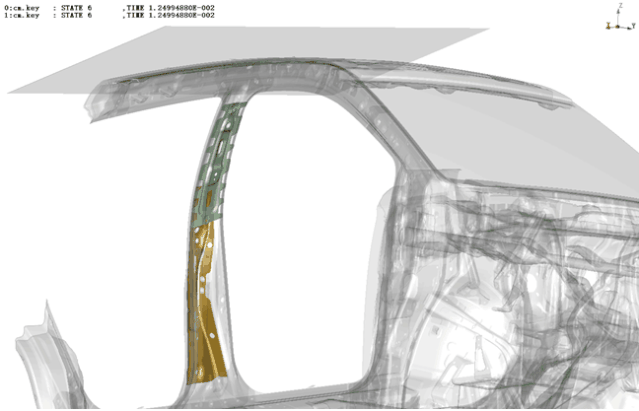
参数优化(尺寸优化)在满足所有性能的要求下,一般可以减重15-25Kg左右。
车身拓扑优化分析主要用于工程数据阶段,针对于白车身结构,主要是加强件和承力件等结构的拓扑开孔减重分析。车身在实际使用过程中承受非常复杂的载荷,这些载荷对车身的影响各不相同,有的影响局部,有的影响整车。基于刚度设计,强度校核的理念,保证车身的基本刚度性能,对于整车的NVH性能、碰撞性能、疲劳耐久性能均具有提升作用。因此,白车身拓扑分析可以选择白车身刚度相关的主要性能项,如弯扭刚度、弯扭模态等。拓扑分析有两种思路,一种是约束刚度、模态等性能,以最小化质量为设计目标;另一种是约束模态、质量(小于原模型质量),以最大化加权柔度为设计目标。两种方法均可用。对于不同的模型,两种方法的效果可能各有优缺点。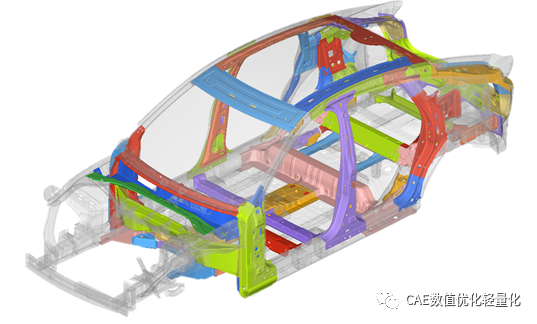
优化对象:所示的带颜色显示的部件
设计约束:1阶扭转模态>xx.x Hz、1阶弯曲模态>xx.x Hz、顶盖前横梁局部模态>xx.x Hz、弯曲刚度>xxxx.x N/mm、扭转刚度>xxxx.x N/mm
设计目标:最小化质量
制造约束:XZ平面对称约束、最小单元尺寸约束
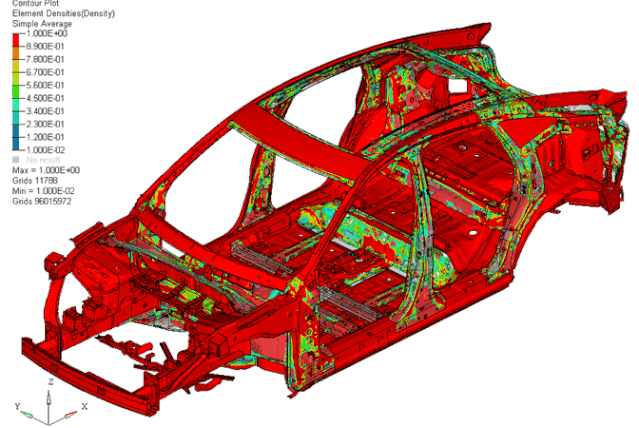
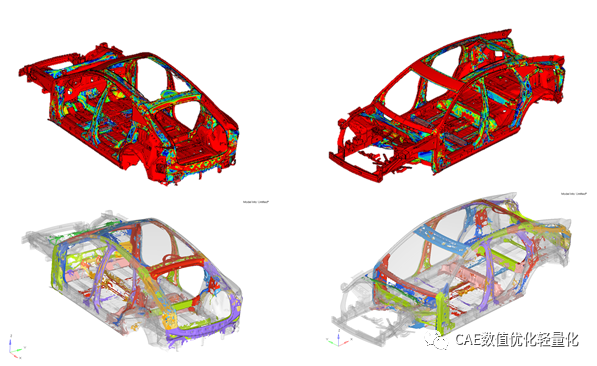
需要根据拓扑分析的结果对计算模型进行更新,白车身拓扑优化分析的结果解读主要包括三个维度:1.开孔减重方案,为大多数的情况;2.删件方案,对于某些拓扑结果中,某个部件几乎所有的单元密度都是小于0.3的情况,且该位置的单元(部件)不是设计必须保留的,则此时该件可以做删除减重方案;3.减薄方案,对于某些拓扑结果中,某个部件几乎所有的单元密度都是小于0.3的情况,且该位置的单元(部件)是设计必须保留的,则此时该件可以做减薄减重方案,厚度可以使用可选的最小厚度。对于开孔减重方案,需要更新计算模型,然后验证分析更新后的计算模型。在更新模型时,需要同设计工程师一同解读拓扑方案,保证开孔方案是满足设计、制造、工艺等要求的。同时,对于一些开孔可以增加翻边提高性能,此时需要设计工程师提供翻边高度、角度等设计输入条件。 整车多学科优化是性能、重量的一种协同优化的手段。整车的结构性能包括NVH、碰撞安全、刚强度等。通常的分析优化过程都是按不同学科单独进行的,然后在验证优化方案对其他性能的影响。多学科优化可以同时考察各项性能,并可以将整车质量作为设计目标,在满足各项性能的基础上进行最优化轻量化设计。关于整车多学科优化有不同的优化策略,这涉及到软硬件资源、性能要求、项目开发周期等等各方面的影响。 整车多学科优化过程的实现可以使用优化软件来实现,包括Isight、LSOPT、Optimus、modeFrontier等。具体的实现过程基本上是大同小异。1.模型的同步更新:多学科优化过程中需要同时考虑强度耐久、刚度、NVH、碰撞安全等性能,对于某个一个设计变量,需要保证在所有学科同时同步更新。因此,要保证模型的同步更新。做好设计变量表格的统计十分重要。2.计算资源的规划:对于强度耐久、刚度、NVH等分析计算一般需要的计算资源没有结构碰撞的需求高。一次DOE计算,刚度、强度、NVH等需要几十分钟或者几个小时,而结构碰撞往往需要几个小时或十几个小时。因此,对于计算资源的分配,协调是十分重要的。当然,过程中还涉及的高性能的计算设置,比如Nastran-HPC设置,LSDYNA-Decomposition设置等,一次计算提升效率10-20%,则整个项目计算时间可能会节省1-2两天。3.结果后处理:多学科优化涉及到不同的学科,因此需要工程师对于不同学科的分析计算内容都要十分的了解,尤其是对于结果的后处理用于创建设计响应,如应力强度、动刚度、模态频率、刚度、加速度、侵入量等等。这方面,建议使用Meta、Python环境进行后处理设计响应的创建。4.DOE方法、RSM方法、优化方法的选择:DOE用于空间探索,响应面或者元模型的创建包括多项式、径向基函数、kriging、神经网络等,或者比较新的ML法等。优化算法一般选择全局优化算法-遗传算法或通过优化策略组合局部和全局优化算法等。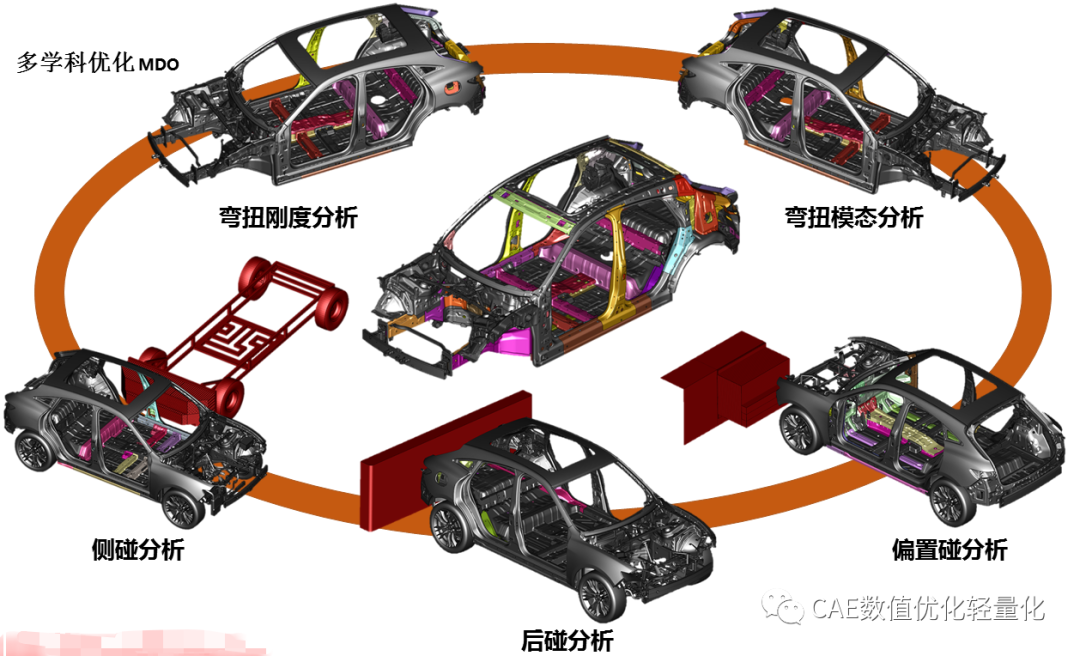
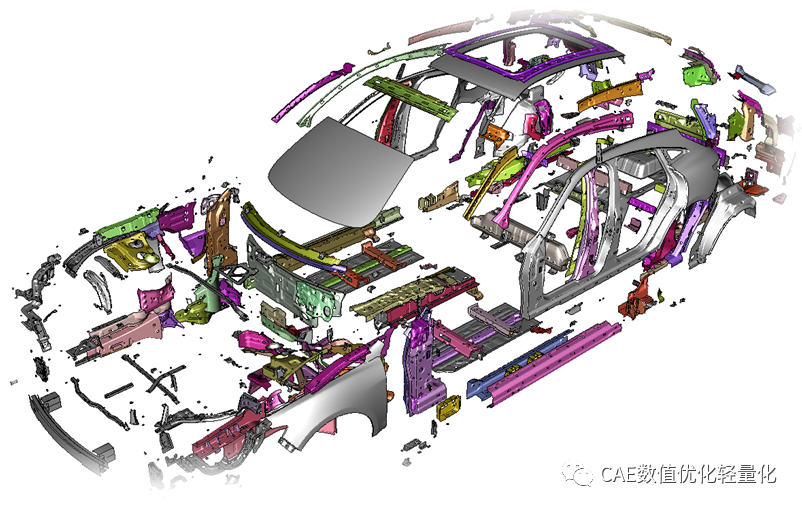
底盘结构件
底盘结构件的数值优化方法包括尺寸优化、拓扑优化、形状优化以及拓扑联合形状参数优化等。
3.1 拓扑优化
拓扑优化一般用于铸件、锻件等零部件、包括转向节、控制臂、副车架等等。根据底盘件的受力特点、需要根据当前受力/应力状态选取关键工况进行拓扑工况的选择。但在进行拓扑优化时,我们往往不以应力作为约束,而是选择加权柔度和体积分数/质量分数为设计响应。约束体积分数以柔度最小为设计目标。具体的参数设置需要根据工程经验以及当前的性能现状综合考察。
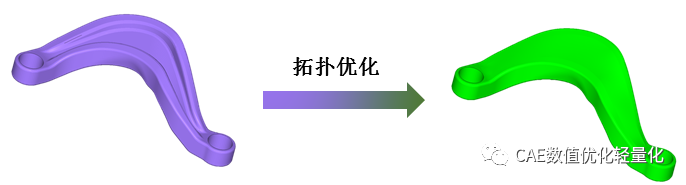
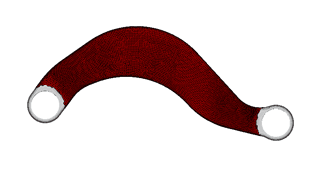
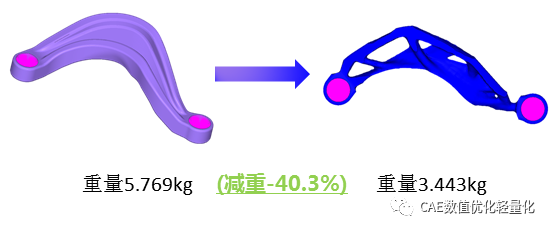
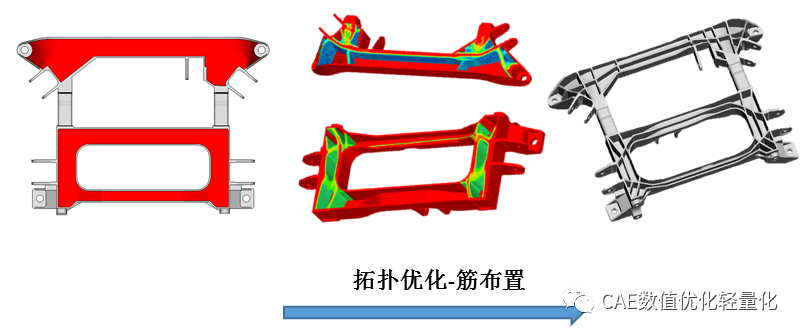
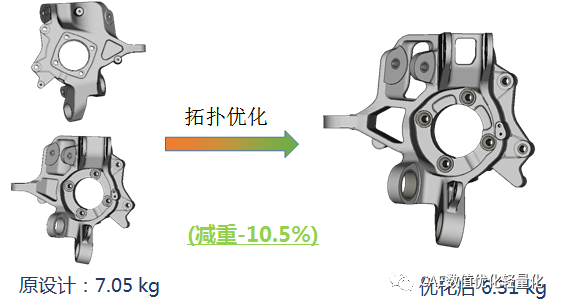
形状优化可以对厚度、高度、截面特征等等形状参数进行优化。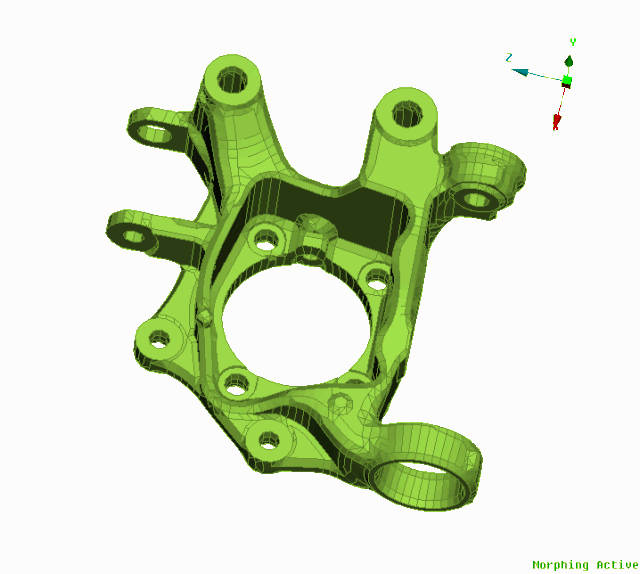
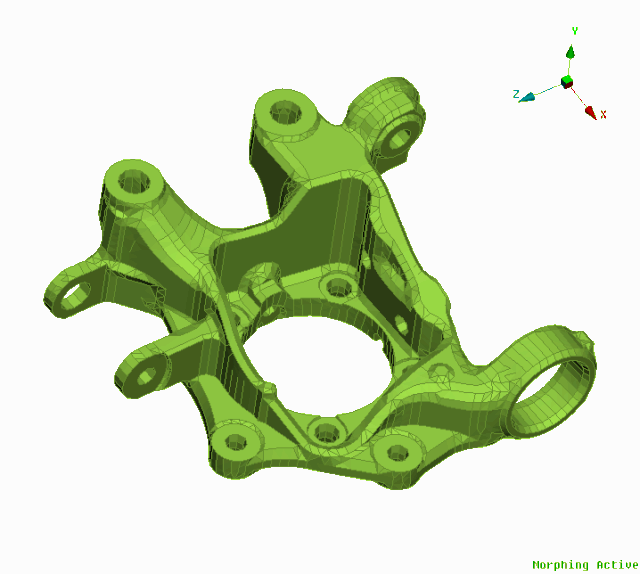
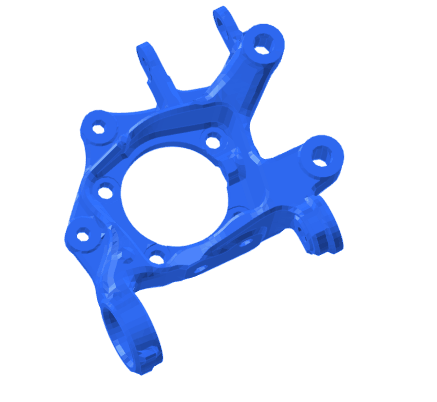
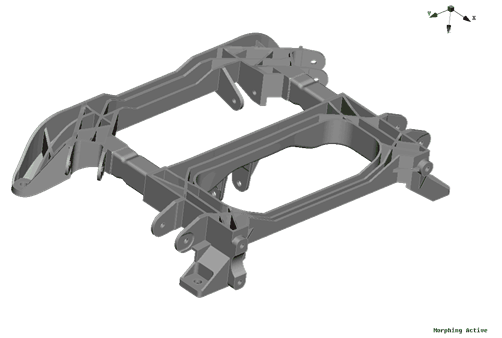
根据上文所述,拓扑优化时不以应力作为约束,不同的体积分数约束的减重效果所有差异。同时,应力往往是局部集中,因此在拓扑的结果基础上继续进行形状参数优化可以进一步地进行轻量化优化及性能优化。底盘件的数值优化一般可以做到10%-20%的减重。
面对同一个部件,不同专业的工程师关注的方向不尽相同:
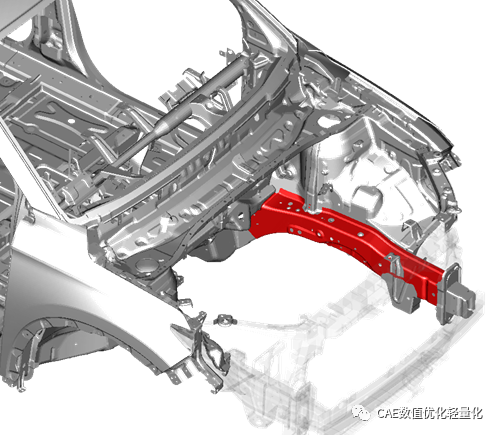
结构碰撞关注:·变形模式 ·力的传递
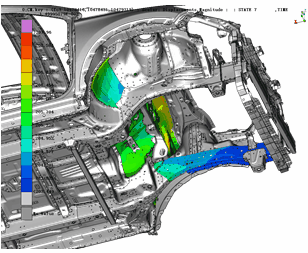
NVH关注 ·应变分布 ·模态频率 ·安装点IPI
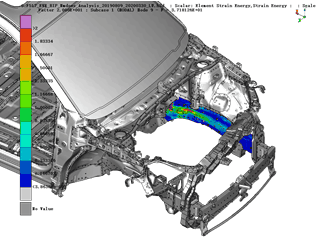
强度耐久关注 ·应力分布 ·应力流/力流 ·疲劳损伤
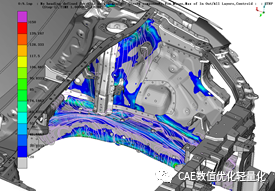
轻量化工程师关注:·性能余量 ·轻量化方法 ·轻量化方案可行度
前后处理自动化、优化流程自动化:
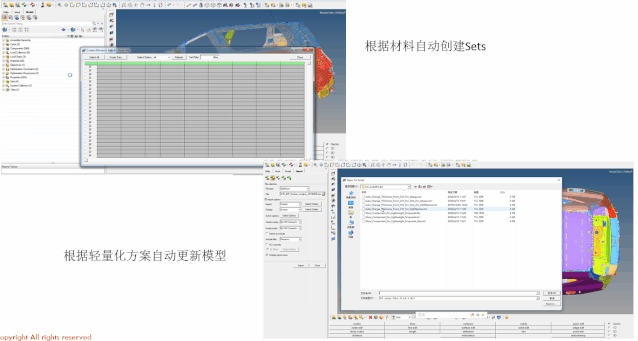
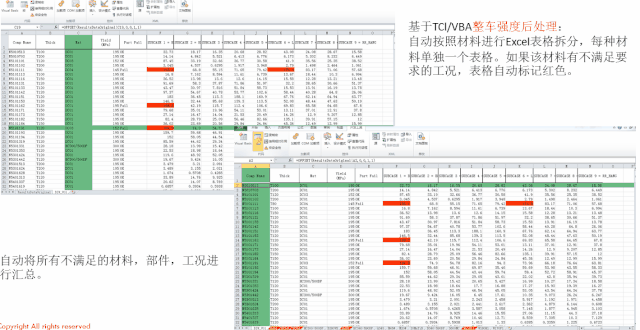
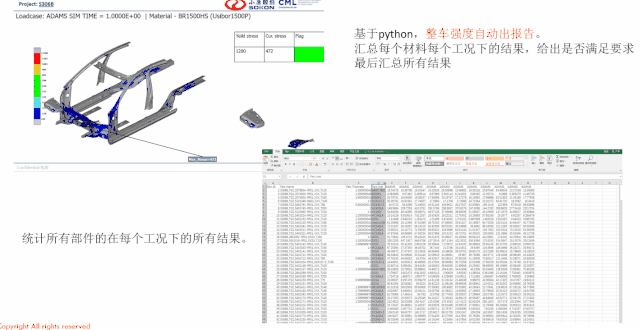
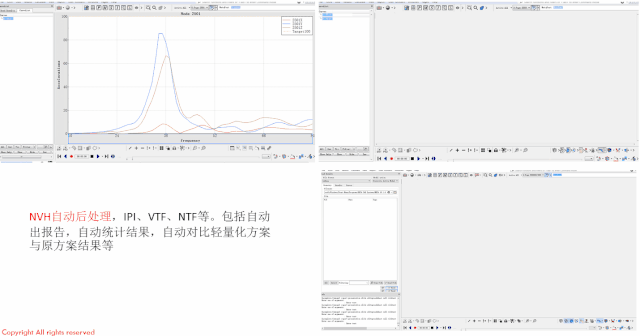
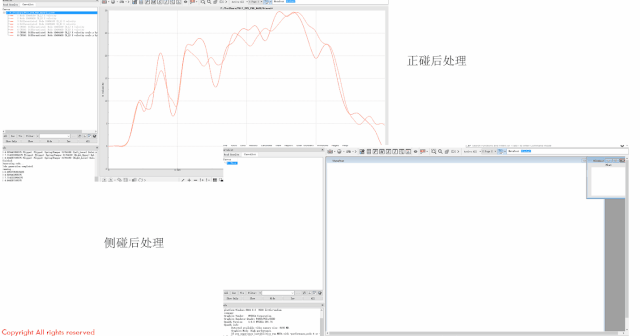
以上只是简单介绍了几种数值优化方法在整车轻量化中的应用,实际工作过程中还有更多的优化方法和工作内容。在进行轻量化优化过程中,需要数值优化工程师掌握强度耐久、NVH、碰撞安全的分析优化能力,具备数值优化分析能力。需要掌握的软件包括常用的前后处理软件(hypermesh、ANSA、Hypergraph、Hyperview、Primer、Animator、SFE-concept、depmeshworks、Hypermorph、ANSA-morph、SCDM等)、求解器(ANSYS、ABAQUS、Nastran、LSDYNA、ncode、Femfat等)、优化软件(Optistruct、TOSCA、LSOPT、Isight、Modefrontier、Heeds、Optimus等)。同时,还需要掌握二次开发的能力,往往在做优化是需要约束各种性能,包括刚度、强度、疲劳损伤值、侵入量、加速度、损伤值、频响结果等各种性能约束,往往需要数值优化工程师具备完成自动提取以上所有结果用于联合优化的能力。需要掌握的常用语言包括Python、Tcl/Tk、VBA、JavaScript等等,用于优化模型自动生成、结果自动后处理、报告自动生成、优化集成等。