FEM_SPH仿真 (Workbench/LSDYNA)
仿真目的及意义
通过仿真手段实现对研磨加工硬脆材料如碳化硅衬底中亚表面损伤层(subsurface damage(SSD),如下图所示)的实时观测与控制并结合研磨实验对加工参数进行优化,从而减少亚表面损伤层(主要是裂纹层)的厚度,以提高衬底加工质量衬底加工质量。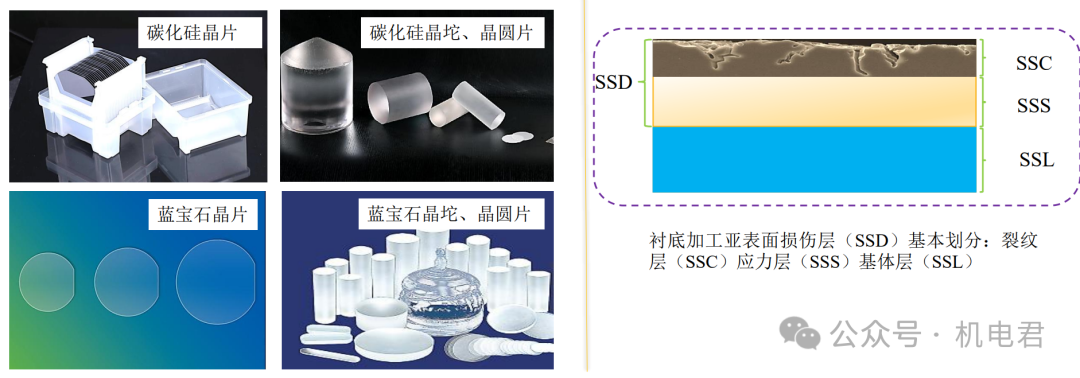
磨粒加工模型
研磨加工系统及其示意图
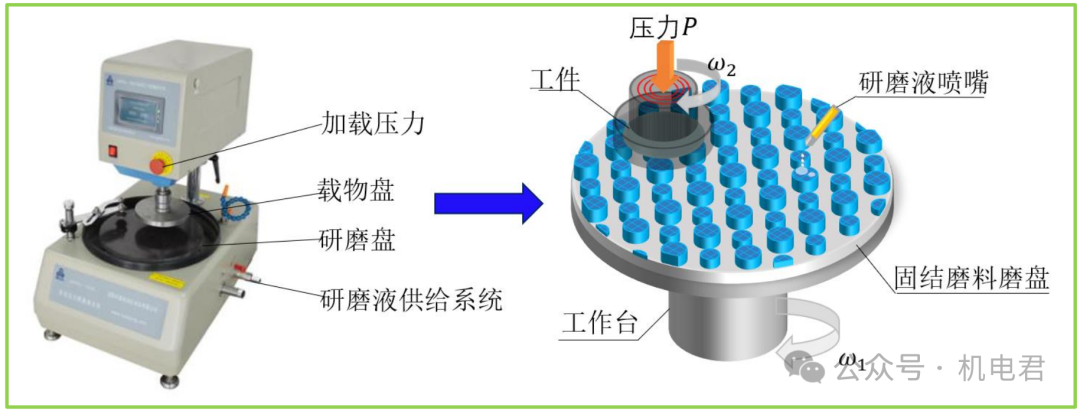
研磨加工原理
固结磨磨料研磨加工系统主要由研磨盘、载物盘、研磨液供给系统组成。研磨时,向下压力P使紧贴上盘面作自转运动的工件与下盘面接触作公转,依靠相对运动实现磨粒对工件的研磨加工。
磨粒加工模型简化
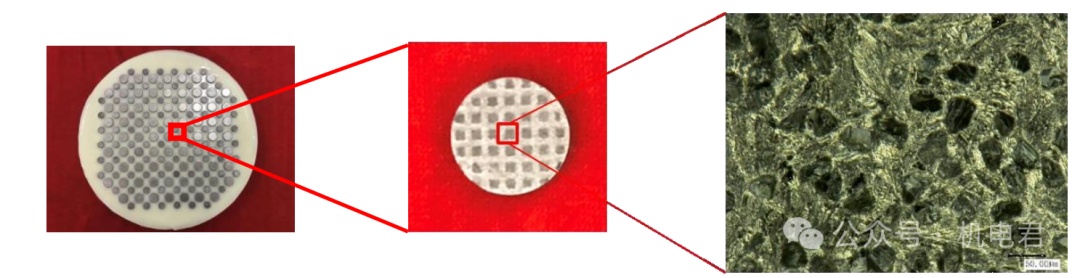
二、单颗磨粒变切深刻划模型建立
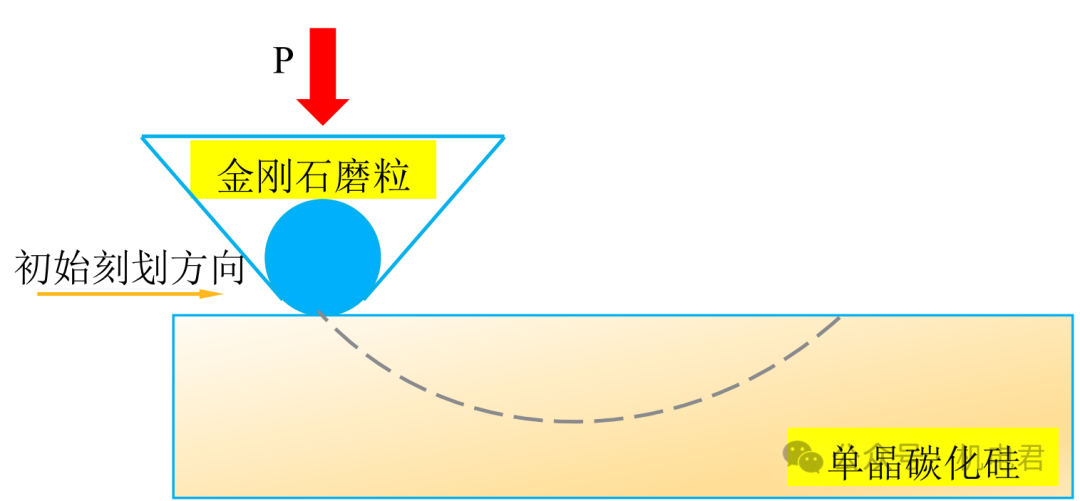
(1)研磨过程简化成单颗磨粒对工件的变切深划擦过程,磨粒设为圆锥状,工件设为长方体。理由:研磨是通过磨盘上的微粉金刚石磨粒与工件之间的相互冲击、划擦等力学物理作用来去除材料,因此,将研磨盘加工等效为单颗磨粒加工;在极短时间内研磨盘的复杂运动可以等效为磨粒的恒定初始速度;此外根据实际金刚石磨粒压头形状,将磨粒设为圆锥形状,工件设为长方体。 (2)忽略加工系统的振动及工件材料的热传导。理由:研磨相对磨削具备更低的转速,在加工过程中的散热及振动很小。(3)磨粒设为刚体。理由:磨粒为金刚石材质,为自然界最硬的物质,其硬度、强度远远大于单晶碳化硅。
有限元算例实现基本流程
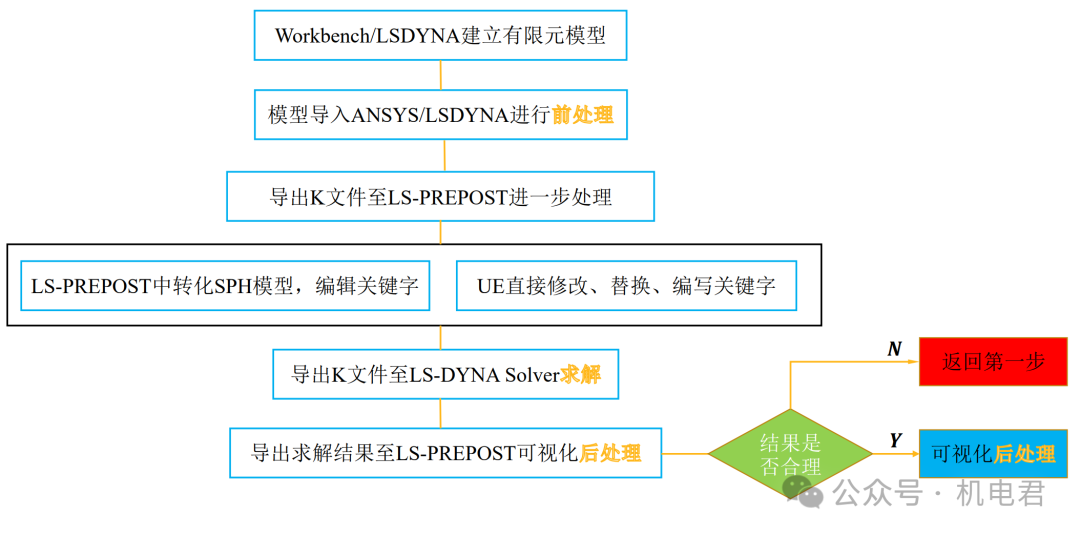
软件操作难点
一、网格粒子转化与粒子间隔控制(前后模型尺寸不变、材料相同(包括本构替换和密度替换)、粒子间隔可控)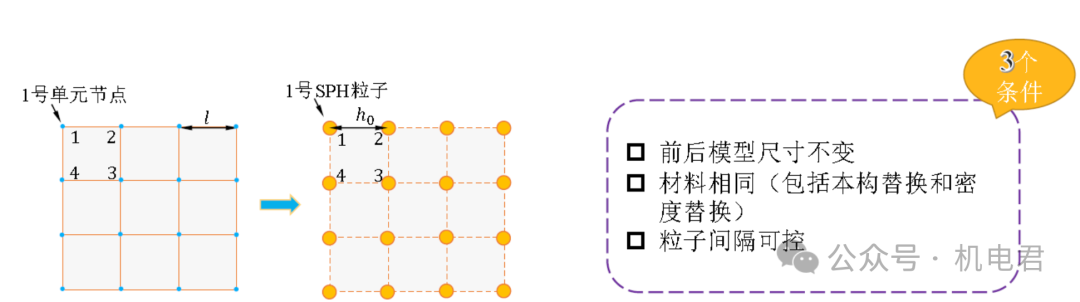
对应软件操作:在LS-PREPOST中编辑SPHGEN关键字创建SPH模型,并选择Solid Nodes创建方法;之后在密度(Den)一栏填入单晶碳化硅的真实密度(g-mm-ms单位制下)完成材料密度的替换;最后通过UE编辑器编辑保存的K文件,将预设的弹塑性材料修改为*MAT_110号材料(JH-2本构)完成本构替换。另外,为保证SPH粒子间隔的可控性,SPH粒子间隔h0与替换前的有限单元网格大小应具有确定的对应关系,图3.2给出了一种对应方法(即上文提及的SolidNodes创建SPH法):有限网格单元的4个节点(分别表示为1、2、3、4)对应转化为4个SPH粒子,同时网格大小𝑙等于粒子间隔长度h0。那么在ANSYS进行网格划分时就可以通过设置不同尺度的网格𝑙来控制SPH粒子间隔h0(𝑙 = h0),这极大方便了本文仿真模型中对于不同切深(ap)的设置。
二、SPH工件边界的处理(“虚粒子约束”法)
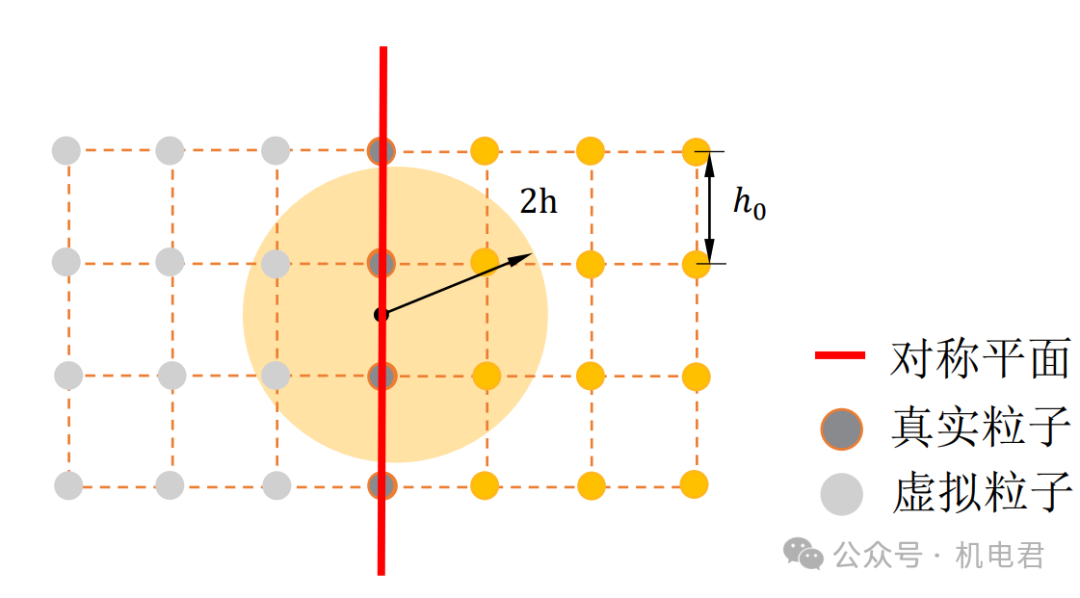
SPH算法是模拟大变形、防止网格畸变的重要手段,但相对FEM算法,其计算效率较低,同时SPH粒子的边界条件较难处理。 上图给出了“虚粒子约束”算法的基本原理:“虚粒子约束”法是对工件可能移动方向进行约束,靠近SPH粒子边界处2h(h为粒子光滑长度)范围内设置出虚粒子。对于靠近边界的SPH粒子,通过对自身的映射,自动创建具有相同质量、压力、绝对速度的虚粒子,使得真粒子能正常进行邻域搜索,以达到约束边界的目。与之对应的关键字是*BOUNDARY_SPC_SYMMETRY_PLANE。三、有限网格磨粒与SPH粒子化工件的耦合接触
不同于FEM算法,本fen'xian中SPH模型以粒子代替网格,相当于有限网格的磨粒与粒子化工件的不连续加工过程。因此,FE的面面接触算法已经不再适用。对于有限元单元与光滑粒子接触界面的相互作用(磨粒与工件),则是通过罚函数算法来定义,耦合接触算法采用自动点面接触算法,主面设为磨粒 ,从面设置为SPH工件(MSTYP=3 ,SSTYP=4),其对应的关键字为*CONTACT_AUTOMATIC_NODES_TO_SURFACE。针对接触算法经过多次仿真实验验证,得出结论:自动点面接触算法(*CONTACT_AUTOMATIC_NODES_TO_SURFACE)、侵蚀点面接触算法均可应用于FEM-SPH耦合模型的接触设置中,但自动点面接触算法的计算效率更高且计算不易报错。故最终选用自动点面接触耦合算法。
四、单晶碳化硅的损伤参数输出、裂纹的云图后处理显示
JH-2本构模型包含有关于硬脆材料的损伤失效模型算法,因此无需另外定义单元失效准则就用模拟出单晶碳化硅的损伤及裂纹扩展现象。这也是JH-2本构能够模拟单晶碳化硅加工裂纹扩展的本质原因。为了更好地输出损伤参数,在仿真计算中首先识别非损伤区与损伤区,将断裂应变满足D1[P*+T*]D2≥Efmin的SPH粒子标红,以示区别,这部分区域就表示加工过程中的损伤。之后将输出裂纹的损伤参数定义附加写入D3PLOT文件的时间历程变量数目(history #2)。软件操作步骤:用UE编辑器编辑关键字*DATABASE_EXTENT_BINARY,将第2个时间历程变量修改为2(即NEIPH=2),该参数就表示陶瓷材料的损伤参数。对应的关键字编辑如下:*DATABASE_EXTENT_BINARY
$NEIPH,NEIPS,
2,0
仿真工件-工具参数设置
仿真参数设置原则
仿真参数的设置原则一般遵循三点:一是计算时间合适,二是结合实际工艺参数,三是适当放大来凸显作用规律。加工参数设置
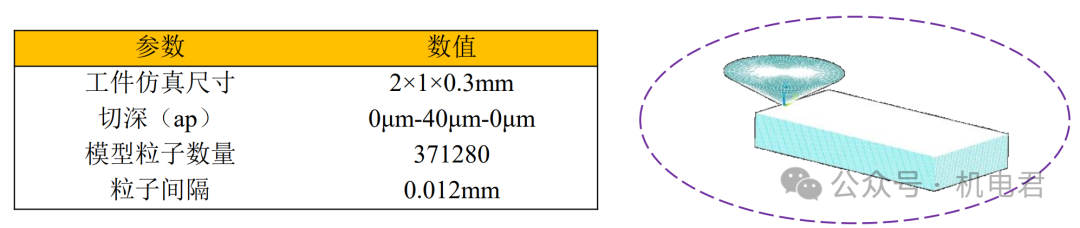
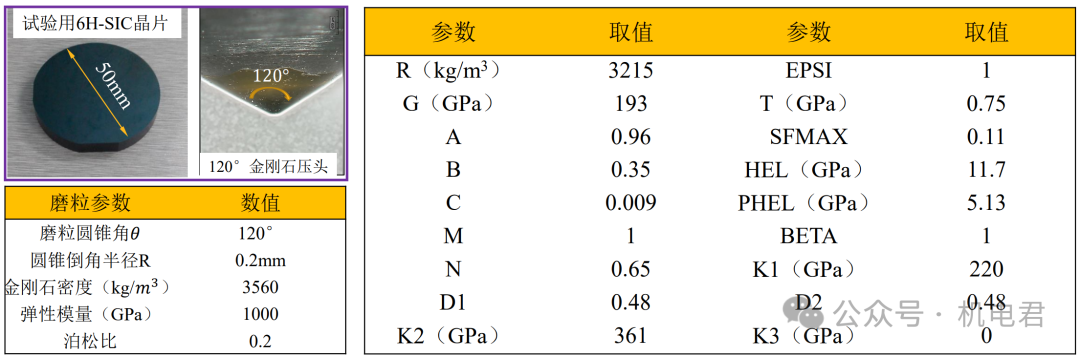
分析与讨论
一、材料去除状态分析
材料去除状态图:
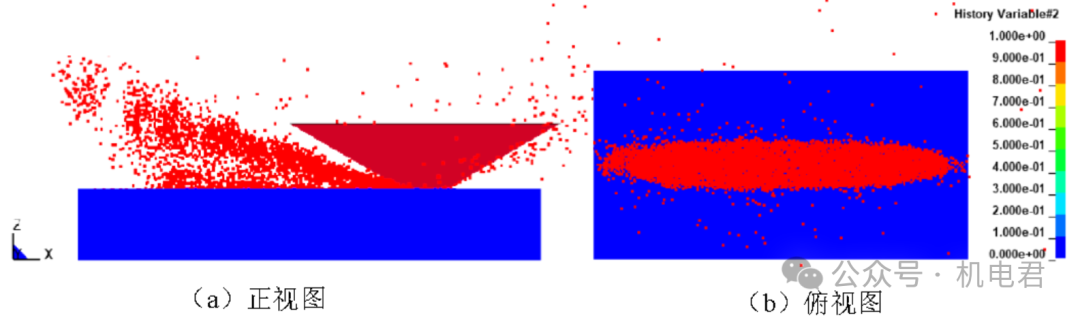
截面设置及截面材料去除态:
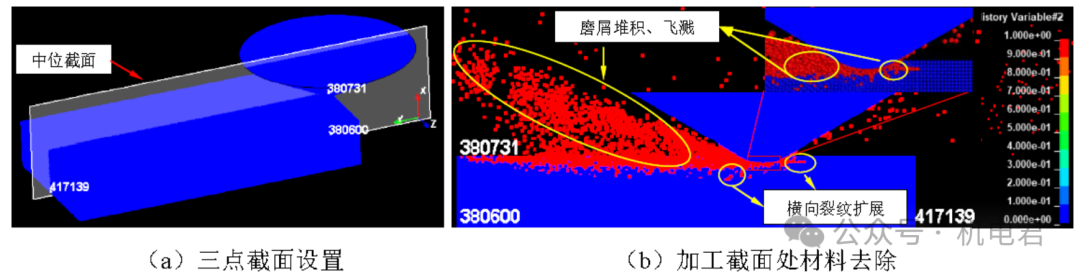
二、裂纹产生及扩展分析
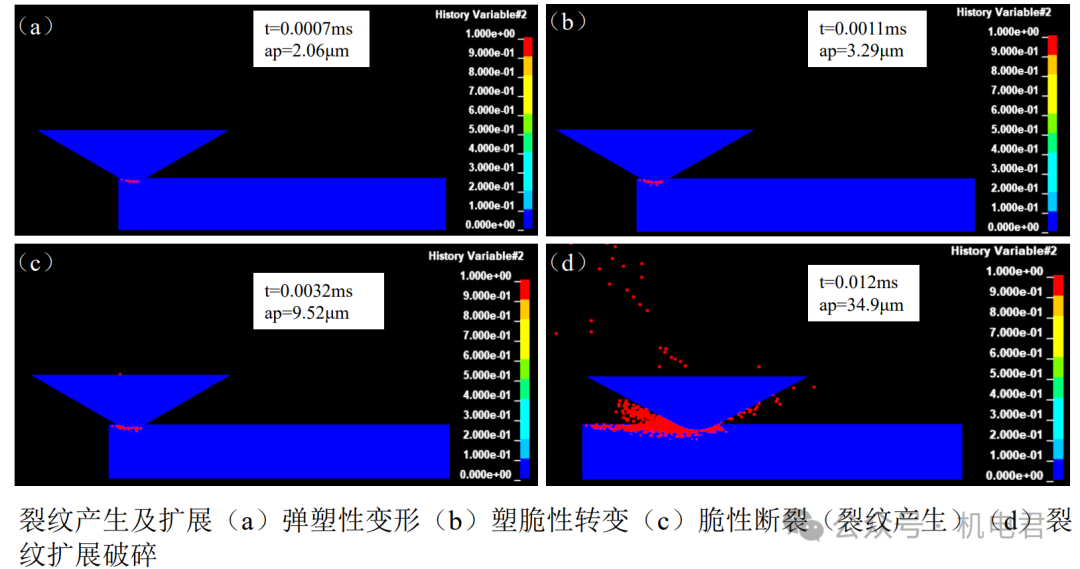
三、不同切深下的裂纹扩展分析
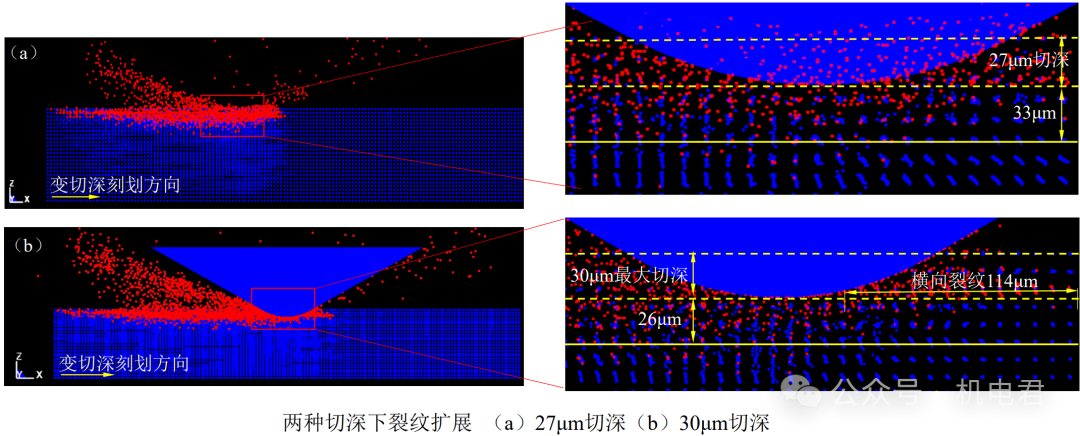
四、划擦力及力比分析
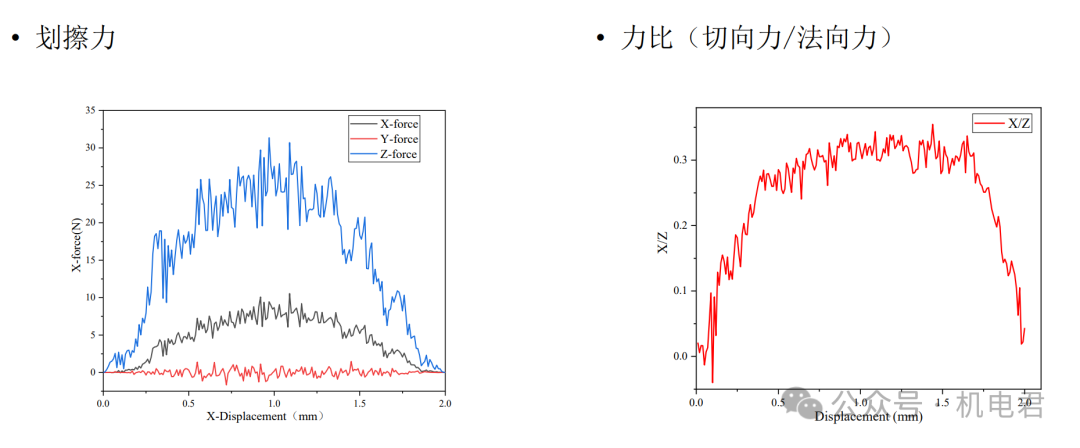
五、能量分析
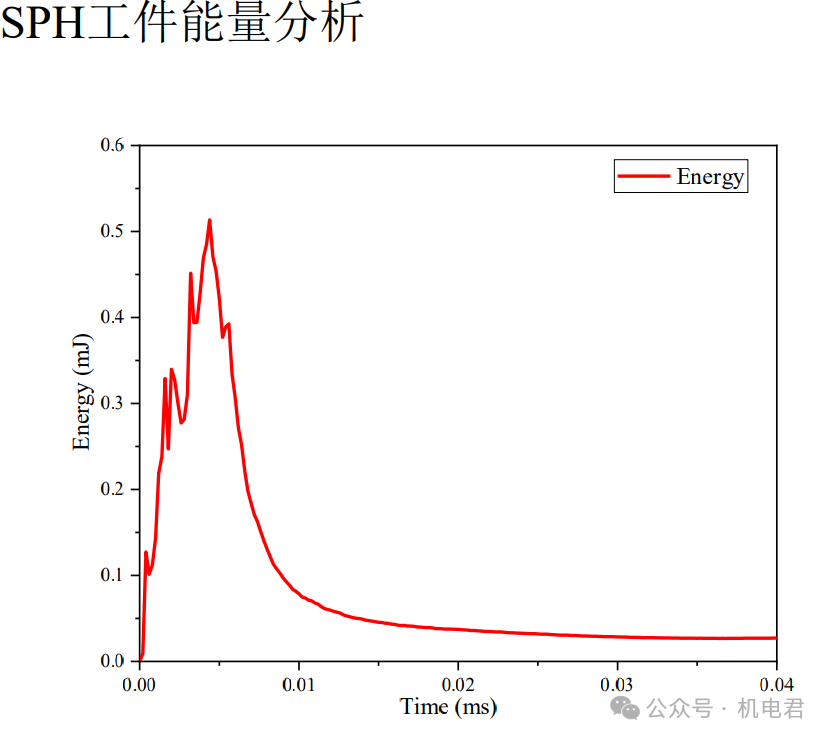
从材料能量变化上来分析材料去除变形及损伤的大小是在仿真中独有的优势和特点。 在LSPP中通过定义𝑚𝑎𝑡𝑠𝑢𝑚可以查看SPH工件的能量变化。
磨粒对材料挤压做功,使材料内部能量逐渐积累,当材料内部增加的能量难以维持平衡,材料开始对外做工,即出现材料变形和去除,而由于变形出现,对外做功,使材料内部能量下降。
由上图得出:磨粒在开始与工件接触后,材工件内部能量迅速增长,形成尖峰,表明在研磨初期,磨粒能量完全被工件吸收且工件没有对外做工,因此表现为塑性变形,没有损伤和脆性断裂出现,之后工件能量急剧下降,表明此时脆性断裂出现,能量释放转化为磨屑动能、工件变形能、热等形式。这与前文通过损伤云图分析所得结果基本一致。
六、单组切深(40μm)条件下仿真结果正确性验证
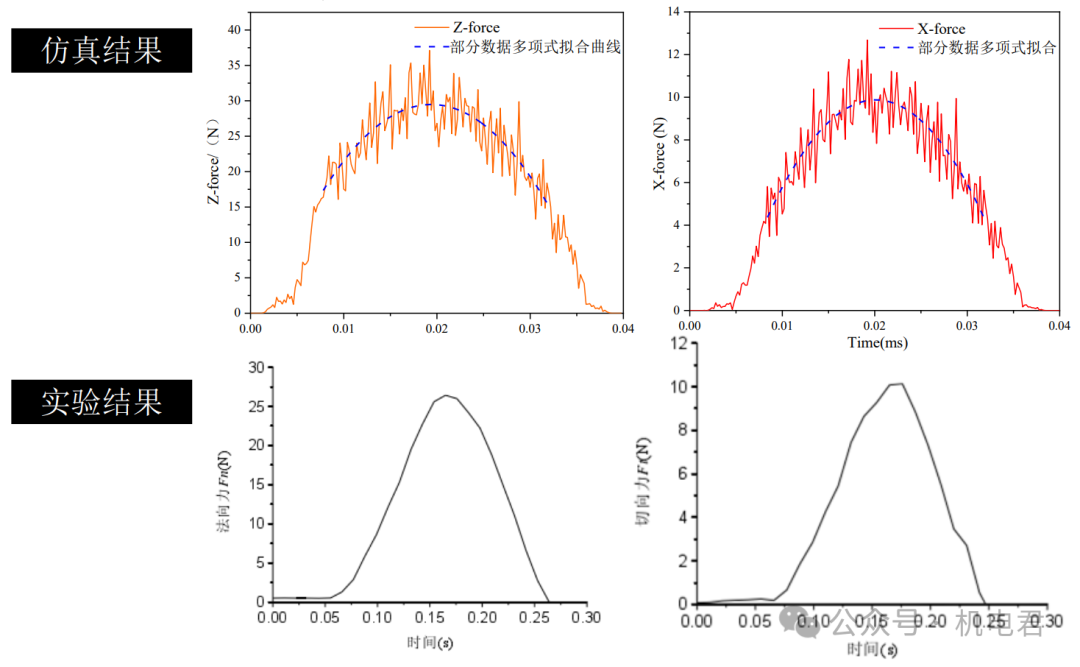
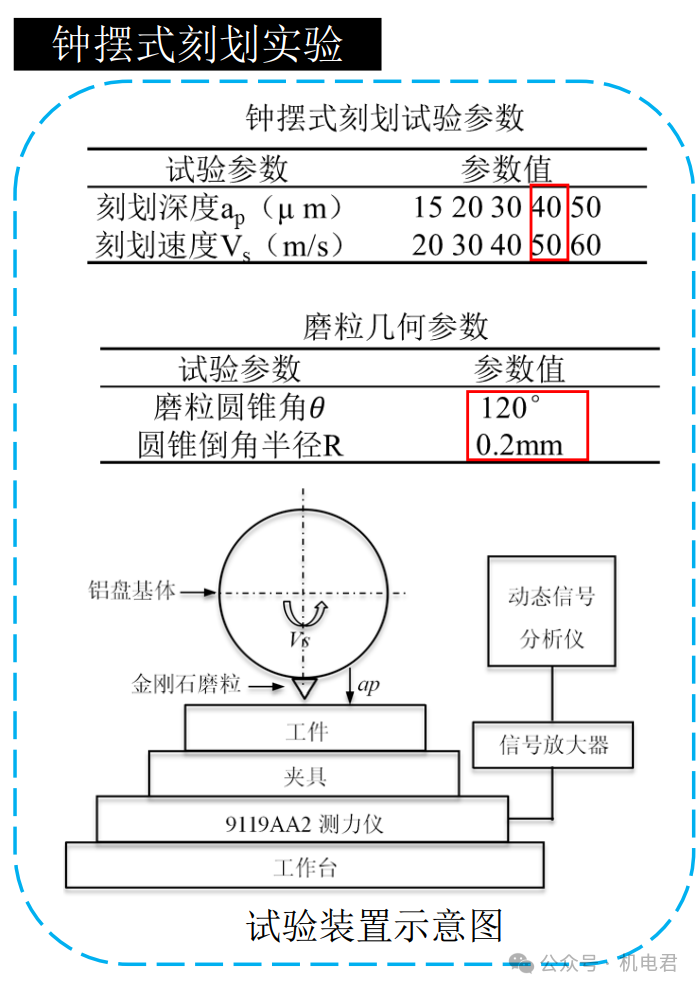
七、多组切深条件下力值正确性验证
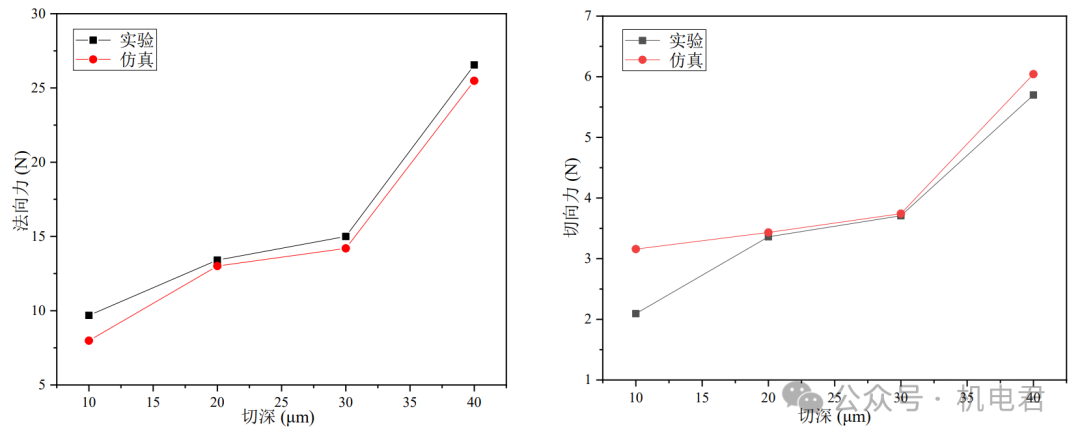
验证仿真结果的可行性,需要3各方面比较:①量的变化趋势相同②量的大小基本相同③量的数值大小在同一个数量级八、算法效率比较
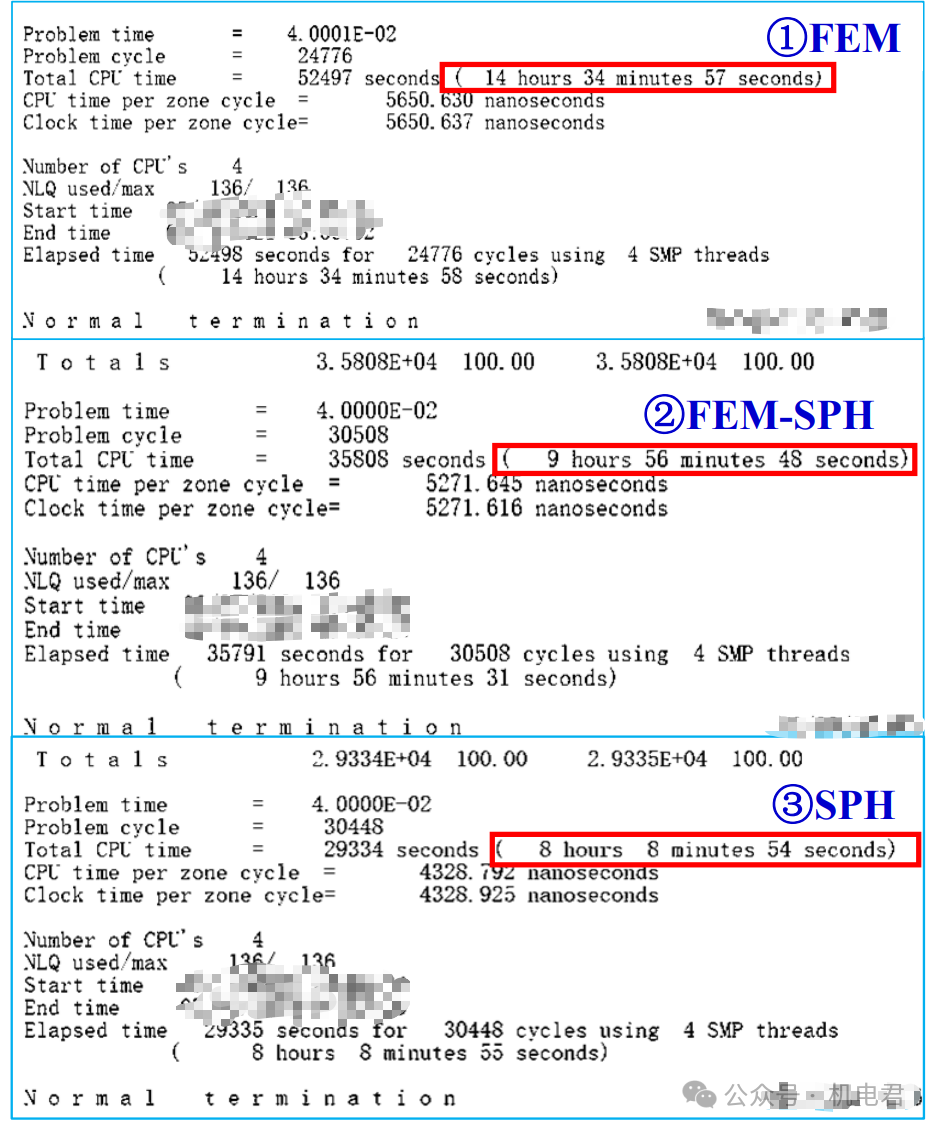
从计算效率来看,FEM>FEM-SPH>SPH,但FEM在处理大变形问题(损伤裂纹扩展等)很容易因为有限网格畸变导致计算终止,因此,单纯用FEM求解大变形问题并不合适,而单纯采用SPH算法 会带来计算时间长、边界不易处理的问题,故就计算效率和仿真模型的准确性,选择FEM-SPH算法模拟单颗磨粒的损伤仿真更为有效合理。
总结与展望
由FEM-SPH仿真结果可知,当磨粒切深为30μm 时,单晶碳化硅以脆性去除为主,工件存在明显的亚表面裂纹和破碎现象,损伤深度约为26μm;当磨粒切深小于9.52μm 时,单晶碳化硅工件不存在明显的亚表面裂纹。因此可以通过控制磨粒切深来实现工件的塑性加工,减小损伤从而提高表面质量。
损伤深度与磨粒的切深并非呈正相关规律,在一定范围内,随着切深的增大,工件损伤深度增大,但切深超过一定值时(30μm)损伤深度有可能减小。
仿真碳化硅衬底所用本构为JH-2模型,此本构可用于模拟硬脆材料加工,但实际实验中碳化硅材料内部不可避免存在缺陷,如空隙、微裂纹等,因此仿真结果与实际实验不可避免存在一定的误差。
裂纹的产生是大量磨粒与工件作用的结果,需从两颗、多颗磨粒建立仿真模型分析,以更加准确符合实际情况。
网络整理,仅限内部分享,禁止商用