高效轻量化的连续波绕组扁线电机技术介绍
本文主要介绍了一种名为超级紧凑波绕组(SCWW)的新型电机设计,这种设计能够为电动汽车和无人机等移动应用提供高效率和轻量化电机。超级紧凑波绕组具有极高的铜填充因子,最小化的绕组头长度和高度,并且在制造上具有高精度、短生产时间和高自动化水平等特点,从而实现低成本高质量的生产。这种设计的电机架构具有非常高的体积密度,显著超过了现有电动机的扭矩密度和效率。为了证明这种新设计的力量并验证其可行性,作者还展示了轮毂电机、车辆驱动电机和无人机电机等实际应用案例。1. 引言
本文提出了一种基于新型波形绕组的电机结构,它具有良好的封装密度,显著优于现有电机的转矩密度和效率。本文介绍了该绕组的结构设计以及其低成本、大规模的制造方法。为了证明这种新设计的强度和可行性,提出了一种带齿轮箱的轮毂马达的设计过程。这款相对较小的电机的有效质量只有1公斤,它提供了14纳米的扭矩,最大效率为96%。为验证了该概念的可行性,本文展示了一个原型机的构造过程,并验证了计算的结果。为了实现更高的功率和效率,我们使用了一个车辆驱动电机的设计示例,该电机在最大效率为98%的情况下可提供350牛米的扭矩,其有效质量仅为6.3公斤。一个特殊的轻量化设计示例是带有气隙绕组的无人机电机,它在最大效率为95%的情况下可提供3牛米的扭矩,其有效质量仅为0.2公斤。本文总结了提出的电子电机结构,并对新结构和新制造工艺的可能性进行了展望。2. 先进的技术
电机应提供尽可能高的扭矩和尽可能高的效率,同时保持最低的有效质量和制造成本。转子的任务是提供尽可能强的磁场。永磁系统通常具有较低的有效质量和损耗的优势,但必须始终考虑用于此目的的稀土磁铁的成本和可用性。定子承载产生扭矩的电流线圈,它传导在转子中产生的磁场,其横截面积应尽可能大以增加电导率,同时导致磁导率的增加。为了提高磁导率,它通常含有较大比例的铁。因此,在定子中,铜线圈的铜与定子铁之间的空间冲突是由必要的磁场传导决定的。剩余的空间应尽可能充满铜,即铜填充因子应尽可能高,以便降低线路电阻,从而减小电阻损耗。此外,还应注意,只有放置在定子中的线圈部分才有助于扭矩。突出轴向外部的绕组头和其他连接不贡献扭矩,但只会增加损耗、质量和成本。这些绕组的部件必须最小化。
此外,线圈必须在工业过程中安装在定子中,该过程通常适用于大规模生产。虽然集中绕组的成型线圈易于制造和组装,但由于铜填充因子非常低,它们不能用于需要非常高效率的应用。分布式绕组提供了更高的铜填充因子。通过使用波形绕组[1],制造分布式绕组的复杂绕组过程得到了极大的简化。波形绕组经常使用预制的绕组垫,然后只需将其插入定子槽[2]。
[3]中描述的非常紧凑的波形绕组代表了市场上大量可用的解决方案。通过在空间上弯曲绕组头,可以使其相对较小,从而更接近对小尺寸和高效率的需求。然而,生产需要一个复杂的弯曲和插入过程。通过使用发夹技术,通过仅将具有特殊形状的缠绕头的缠绕杆插入插槽[4],可以显著简化插入过程。然而,所有开放的绕组头都必须焊接,这导致了大量的接头,需要精心的质量保证
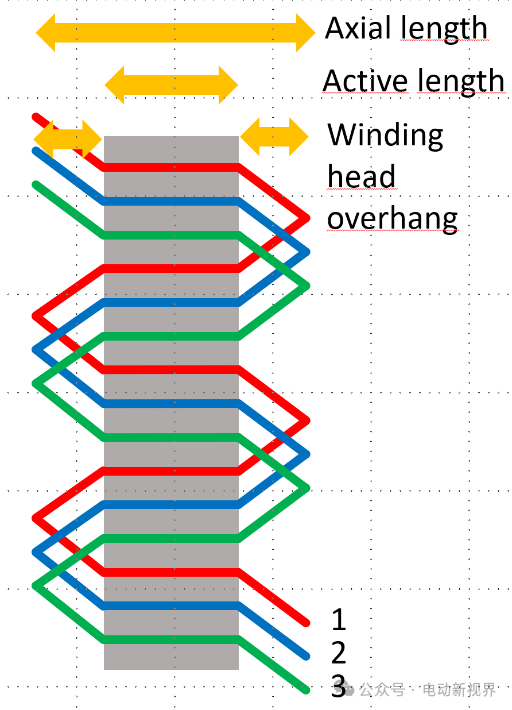
图1:波形绕组的特点
一种由叠层气隙和槽绕组组成的复合绕组,显著减少了效率的降低[6]。定子中相对较小的齿部增加的有效质量是可以接受的。因此,这种复合绕组对于特殊轻量化应用来说是非常好的折衷方案,这些应用仍然需要非常高的效率。因此,最高效的要求总是需要一个能够承载所需铜量的槽绕组。根据目前的现有技术,轴绕组提供了最具前景的绕组技术,它结合了高效率、小尺寸、有效质量和低成本。
在生产过程中,整体上波绕组会导致线圈电阻略微增加。总的来说,波绕组是一种实现紧凑设计、填充系数良好并且在很大程度上可以自动化制造电机的方法。通过采用气隙绕组,可以实现减少或完全消除定子中的铁含量的愿望。通过将绕组放置在气隙中并使用无槽定子,可以避免齿部的铁含量。然后,这些气隙绕组仍然靠在定子的一侧。自支撑的气隙绕组不需要任何铁制部件。通过将绕组嵌入基板和/或在绕组头部加入稳定环,可以为气隙绕组提供必要的稳定性和刚度。气隙绕组可以实现相当大的重量节省,但总是以增加气隙为代价,这意味着可用的磁场略微减小,或者必须通过增加磁性材料来补偿。无论如何,电机的效率都会受到一定影响。一个结合了叠层气隙和槽绕组组成的组合绕组明显降低了效率损失。在定子中以相对较小的齿的形式增加了有效质量是可以接受的。因此,这种综合绕组对于特殊的轻量级应用来说是一个非常好的折衷选择,尽管需要非常高的效率。因此,对于需要非常高效率的应用,总是需要一种能够承载所需铜量的槽绕组。根据当前的技术水平,轴绕组提供了最具有前景的绕组技术,可以同时实现高效率、小尺寸、有效质量和低成本。尽管波绕组具有许多优点,但现有的波绕组存在显著的缺点,主要是由于以下原因导致的:高绕组头部悬挂。这直接导致了较大的轴向总长度,对尺寸和重量产生了负面影响,因为所有的外壳部件也受到了影响。另一个后果是高绕组头部长度,它增加了相位电阻,这直接导致了效率的恶化,并且还增加了总重量和铜成本。在一些绕组变体中存在困难,比如多层绕组,由于堆叠绕组层数受到限制或难以生产,因此难以进行堆叠。有时,选择最佳的线材型号受到限制,因此在槽填充系数方面不得不进行妥协,尤其是在直立格式的情况下。最后,许多波绕组的制造是一个复杂且昂贵的过程,这会带来显著的成本。本文介绍的超紧凑波绕组正是为了解决这些问题,进一步优化电机的效率、尺寸和成本,并使其适应现代移动系统的需求。3. 超紧凑波绕组(SCWW)
本节介绍了一种新的超紧凑波绕组,它能够实现电动机械所需的高效率和轻量化,适用于电动出行。超紧凑波绕组在拓扑结构/特点方面具有重要的独特卖点:- 最大铜填充系数
- 几何上最小的绕组头长度
- 轴向上最小的绕组头悬挂
- 径向上最小的绕组头高度
这些特点显著提高了功率/扭矩密度和效率。同时,在制造领域也具有以下优势:- 高精度
- 短生产周期
- 高度自动化
- 低材料使用量
- 高产能,可实现低成本高质量的生产
3.1 设计和拓扑
图2显示了一个外转子电机的定子的径向视图,其中插入了单层超紧凑波绕组。通过开放的槽口可以看到具有矩形或梯形剖面的绕组棒。这使得在槽口区域实现了可能的最大铜填充系数。由于开放的槽口而增加的齿槽力矩可以通过对磁铁进行斜切来有效地减小。绕组到定子的内部绕组头距离被限制在最小值,这出于制造性和绝缘安全的考虑而制定的。实际设计的范围在0.5到1.5毫米之间,这取决于电机的尺寸。这导致了在一个定子侧的总绕组头悬挂小于3-5毫米。在沿轴向离开槽口后,绕组头以直角弯曲,并且沿定子的周长平行运行,大约持续一个磁极角度,直到在第二个直角弯曲后,最终在轴向方向重新进入槽口。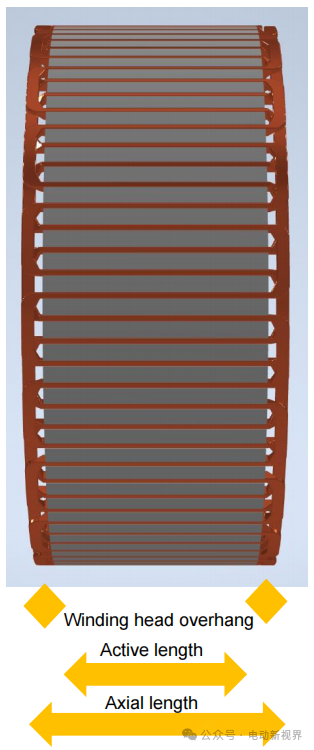
图2:超紧凑波绕组的径向视图
这种设计代表了两个相连绕组棒之间可能的最短几何连接,从而导致了可能的最短绕组头长度。定子的总轴向长度仅略大于有效长度,该长度积极参与扭矩产生。短绕组头还将欧姆损耗降至最低,因为它们与导体长度成正比。绕组棒和绕组头中导体的横截面积相同,因此电阻没有增加,从而减少了电阻损耗。图3显示了一个外转子电机的定子的轴向视图,其中插入了超紧凑波绕组。绕组头位于定子周长内的一个窄环中。该环的高度与绕组棒中的导体高度相对应,因此即使是多层绕组也可以非常容易地堆叠,而无需担心碰撞。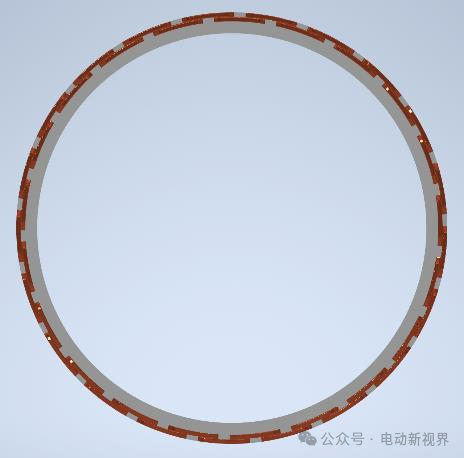
图4详细说明了超紧凑波绕组的轴向视图,可以看到绕组头的交替排列,上绕组头横扫两个下绕组头,反之亦然。在绕组头的切线区域,导体的径向高度减少到绕组棒高度的一半,因此它们可以轻松地径向堆叠。切线区域中绕组头的轴向宽度相应增加,以提供导体的恒定横截面积。因此,绕组头能够最佳地利用径向安装空间,而不会在任何地方留下空隙。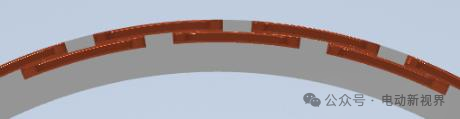
图 4:超紧凑波绕组轴向视图的细节
超紧凑波绕组的最优几何结构确保了其卓越的性能。类似于这里展示的槽式绕组设计,超紧凑波绕组也可以像[7]中所示的那样设计为气隙绕组。3.2 实施方式/制造
为了最佳地满足电机尺寸或数量的不同需求,有几种制造工艺可用于生产超紧凑波绕组:
3.2.1 型材线材弯曲
起始材料是涂覆的矩形线材,呈竖直格式,通过多次弯曲形成绕组头。在关于切线轴的90°扭转后,分别在两个径向轴上进行两次90°弯曲。图5显示了底部绕组头的弯曲设计。扭转弯曲轴的位置决定了是弯曲底部绕组头还是顶部绕组头。底部和顶部绕组头交替弯曲会形成一个完整的相位(图6)。相位末端可以由绕组头的一部分构建,该部分还用作星形点桥的一部分。
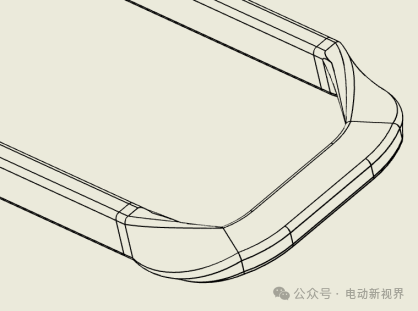
图5:由弯曲矩形线制成的绕线头

图6:由弯曲的矩形线材制造的一个相位
这三个阶段然后交织在一起形成整个绕组。在这个步骤中,产生了图7所示的绕组头的特征交替位置。产生的绕组垫非常坚固且易于处理。然后像往常一样将其插入定子槽内,用于波形绕组。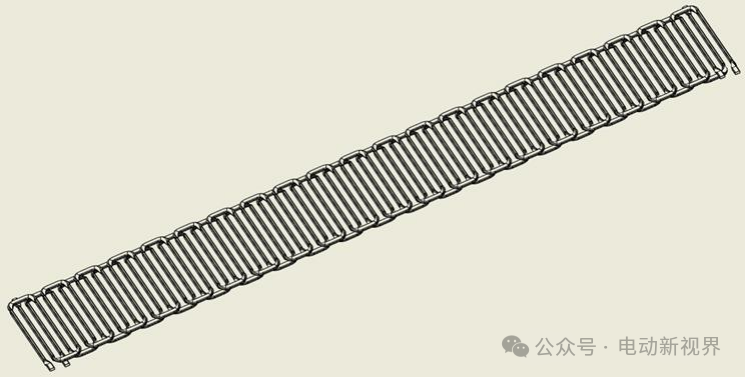
图7:由弯曲矩形线编织成绕组垫的三种阶段制造过程
所展示的弯曲过程适用于所有数量的产品。小批量生产时可以使用更简单的弯曲设备。所有的必要生产步骤都可以实现自动化,因此即使是大批量生产也可以使用合适的绕线机来完成。形成的绕线头具有所需的形状和几何结构,因此也能在效率、扭矩密度和尺寸方面带来预期的改进。然而,由于需要保持的弯曲半径,实际实现的绕线头比可能的最低值稍大一些。通过直接成型绕线头可以完全避免这种限制。但是,这里介绍的弯曲过程有其存在的理由,因为它提供了显著的改进,并且可以无缝集成到现有的生产线中。3.2.2 成型
可以通过对裸铜进行实心成型来生产尺寸最小的绕组头。成型过程可以通过模具或适应的自由成型工艺进行。在两种变体中,制造精度都足够高。绕组可以由适当形状的线材制成。在这种情况下,只需形成绕组头,而型材线直接形成绕组条。图8显示了一个下绕组头的成型版本。另一方面,绕组头和绕组条都可以由圆线制成,例如。这就在绕组条的形状上提供了进一步的自由度,可以用来增加铜填充因子。在这里,一个相位也是通过交替形成底部绕组头和顶部绕组头来产生的。成型过程完成后,相位可以经过退火处理,以消除增加欧姆电阻的任何内部应力。由于使用软铜进行制造,经过退火后的电导率高于58 MS/m。退火后,相位会进行涂覆。有几种工业验证的涂覆过程可用于此(例如,浸涂、粉末涂覆、喷涂等)。其优点在于,在涂覆时,绕组的所有机械加工都已完成。在选择涂覆时,诸如介电强度或温度抗性之类的标准可以比机械特性更加强烈地评估。这使得在正常的击穿电压下可以实现更高的温度等级超过220°C。然后,三个相位被编织成一个绕组垫。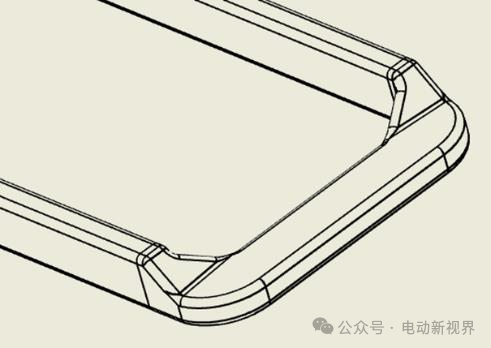
图 8:通过成型制造的绕线头
所提出的成型工艺适用于所有数量。较小的数量可以使用更简单的成型设备生产。所有必要的生产步骤都可以自动化,因此甚至可以非常轻松地生产大量产品。通过成型生产超紧凑波绕组特别适用于中小型电机,因为相位和绕组的处理可以非常容易地自动化。对于非常大型的电机,必须考虑到模具成本。在这种情况下,超紧凑波绕组可以使用连接技术制造。3.2.3 连接
另一种生产具有最佳几何形状的绕组的可能性是通过连接技术,特别是焊接技术。按照众所周知的针形过程,直绕组条首先插入槽中,然后与绕组头连接。在这种情况下,槽也可以部分或完全关闭。与针形过程相比,所提出的方法具有显著的优点:● 绕组条由任何横截面的直线型材组成,
● 绕组头可以通过简单的成型工艺单独制造,
● 绕组条和绕组头之间的连接可以通过简单的焊接工艺实现(例如,电弧焊接,电容放电焊接等),
● 由于焊接可能导致的欧姆电阻增加可以通过增加绕组头的横截面积来补偿。
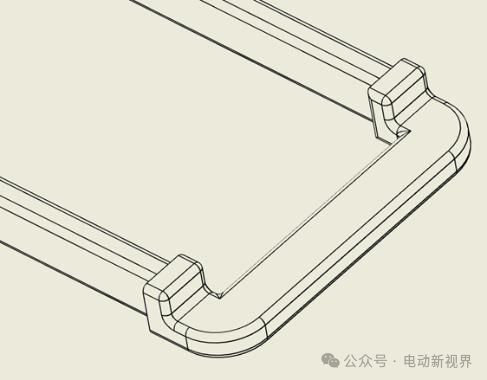
图 9:通过焊接制造的绕线头
图9显示了底部绕组头的焊接设计。在连接过程中,底部绕组头和顶部绕组头的交替排列完成了相位,并提供了一个完整的插入绕组。图10显示了一个外转子电机定子的截面,其中插入了焊接的超紧凑波绕组。通过这种工艺,也可以在绕组条的塑形方面获得进一步的自由度,这可以用来增加铜填充因子。通常,在连接之前,绕组条和绕组头已经被涂覆,因此在连接后只需对接头进行涂覆。所介绍的连接工艺适用于所有数量。较小的数量使用特殊的焊接枪进行生产。所有必要的生产步骤都可以自动化,因此甚至可以非常轻松地生产大量产品。所使用的连接技术用于制造超紧凑波绕组,特别适用于大型发动机,因为无需处理、成形或插入长导线,也不会遇到特殊的工装成本。在轴向和径向尺寸或导体横截面上没有限制。除了上述三种用于制造槽式绕组的方法外,文献[7]中还描述了其他方法,由于篇幅有限,这里无法进一步讨论。此外,[7]还描述了一种用于制造超紧凑波绕组作为气隙绕组的工艺。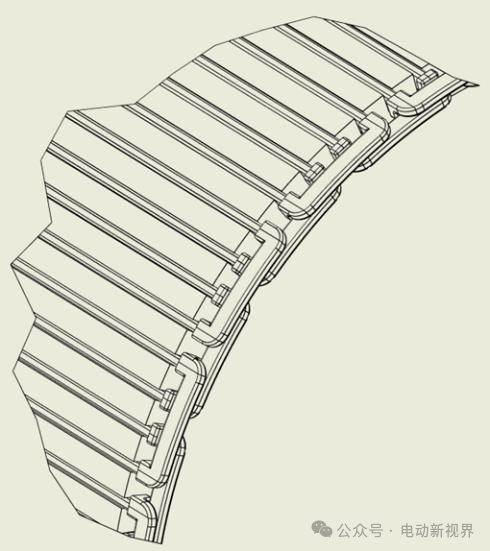
图 10:通过焊接制造的超紧凑波绕组定子细节
4. 货运电机
为了验证具有超紧凑波绕组的新电机设计,使用表1中列出的货运电机的规格,该电机带有齿轮箱版本。带有*标记的数据描述了当前竞争对手。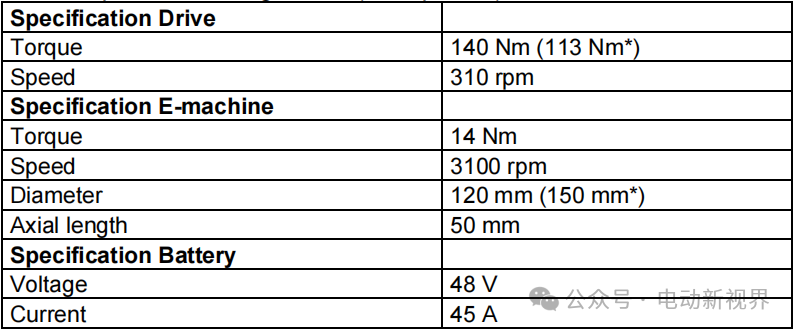
4.1 设计货运电机
与竞争对手相比,货运电机要提供约20%的更大转矩,直径缩小约20%。由于货运电机通常是风冷的,因此效率应尽可能高。为了尽可能简化原型构造,选择了单层绕组。图11显示了所选设计的效率和转矩-速度特性。14 Nm的扭矩可在最大速度的约45%处使用。在此之上,功率限制为2 kW。最大效率为96%。在扭矩降低开始时的效率约为84%。所需的主动质量为1 kg,其中磁铁占100 g。双层绕组会将扭矩降低开始时的效率提高至91%,主动质量增加至1.3 kg。这显示了该电机概念具有高效率、紧凑性和良好的适应性。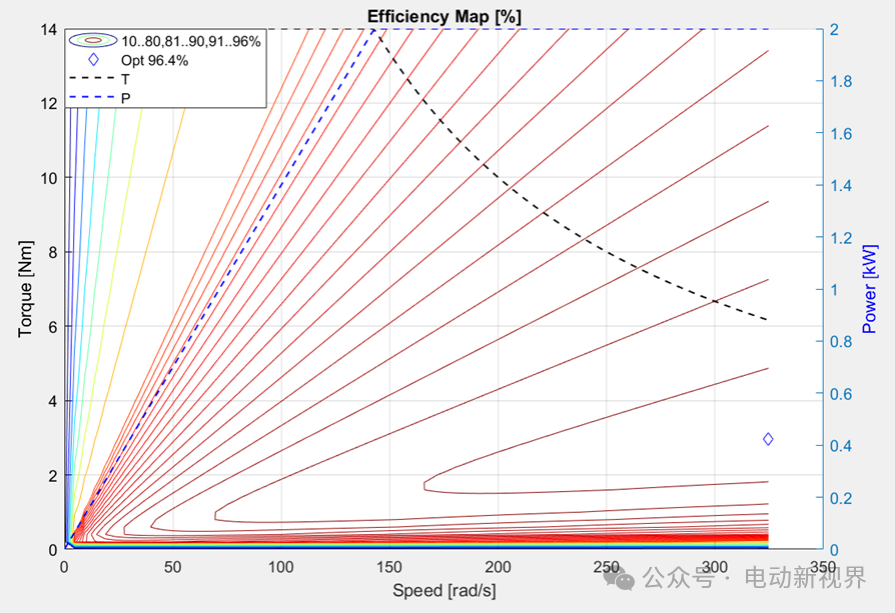
图11:货运电机的模拟效率/转矩-速度特性
4.2 CAD模型货运电机
出于设计原因,货运电机设计为具有交替磁化的外转子。图12显示了通过拆下的前盖看到的电机内部的视图。由于定子较低(绕组高度2.5 mm,背铁高度3 mm),可用于容纳例如齿轮箱或控制单元的宽敞内部区域的环形电机可用。可以看到非常紧凑的绕线头,这使得机器的轴向长度非常短。每侧的总绕线头悬挂量约为3 mm,这使得在50 mm的电机长度下,可以获得40 mm的有效长度。此外,可以看到相连接和星点的优雅且节省空间的设计。星点桥直接由三个缩短的绕线头形成,这些绕线头重叠并连接在一起。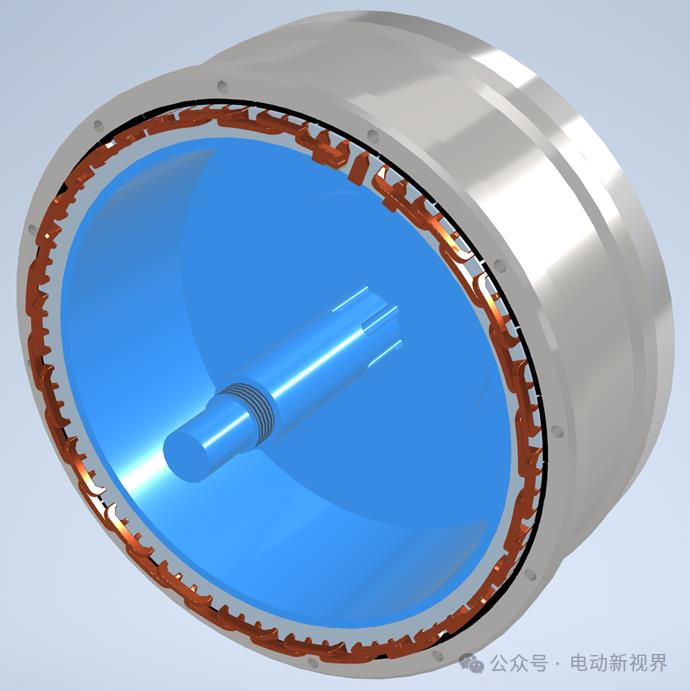
图12:带有打开前盖的货运电动机原型
4.3 原型货运电机
原型货运电机的绕组是在成型过程中生产的。图13显示了成型后的一个相位。
图13:货运电机原型的成型相位
经过退火后,测得相阻抗为12毫欧,这与设计中理论计算的12.1毫欧的值非常接近。将三相进行浸涂后,它们经受高电压测试,然后编织成绕组垫。由于绕线头双侧的多重嵌合,绕组垫非常稳固。它可以非常轻松地运输和处理,并插入定子槽中。绕线头的圆弧形状可以很容易地弯曲在绕线头的窄侧上。最后,将绕组垫插入原型定子中,并检查其尺寸精度(图14)。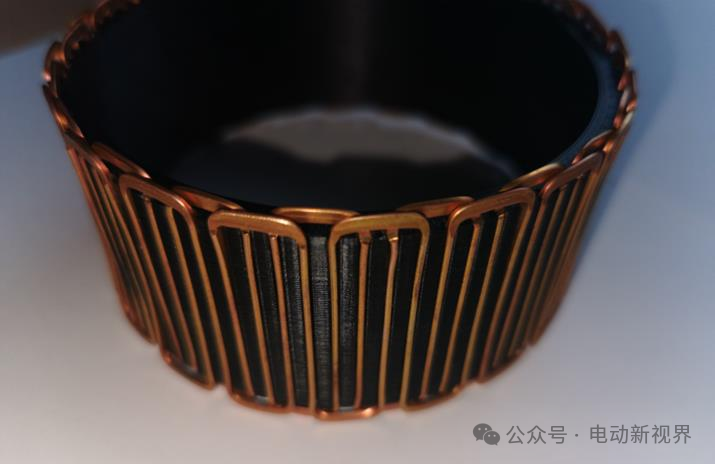
图14:带有插入的超紧凑波绕组的货运电机原型定子
所展示的货运电机原型展示了基于超紧凑波绕组的新电机概念的性能和可行性。通过大规模成型生产超紧凑波绕组证明非常高效。通过原型生产工具已经实现了绕组的目标几何形状和性能数据。选择货运电机作为示例是因为可以以较少的工作量将其原型化为小型电机。5. 设计研究
为了展示电机概念的广泛应用可能性,本节介绍了两个具有不同目标方向的设计研究: ● 以轻量化建设为重点的无人机电机
● 以高效率和紧凑性为重点的电动车驱动电机
无人机在现代移动性中变得越来越重要。特别是,具有中等航程和高载荷能力的较小载荷无人机越来越受到关注。为了尽可能保持载荷高,电机重量必须尽可能低,扭矩输出尽可能高。最高的效率保证了最长的飞行时间。表2中给出的无人机规格作为设计研究的基础。表2:无人机电机规格
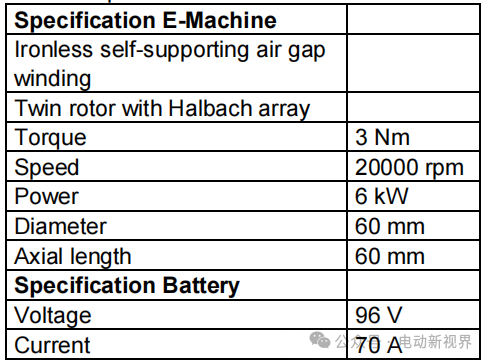
设计研究采用了双转子架构,以实现最高的扭矩质量比。两个同心磁环转子,均排列成哈尔巴赫阵列,位于无铁定子的内部和外部。定子由一个自支撑的三层超紧凑波绕组组成,此外还通过连接超紧凑波绕组暴露的交织绕线头的两个固体环稳定。图15显示了所选无人机设计的效率/扭矩-速度特性曲线。3 Nm的所需扭矩适用于整个速度范围,导致最大功率超过6 KW。效率在大约半最大扭矩和最大速度时达到95%以上的最大值。在非常广泛的扭矩和速度范围内,效率都高于93%,实现了非常节能的运行。所需的有效质量仅为200克,其中144克是磁铁的重量。这种设计生动地展示了超紧凑波绕组的巨大轻量化潜力。
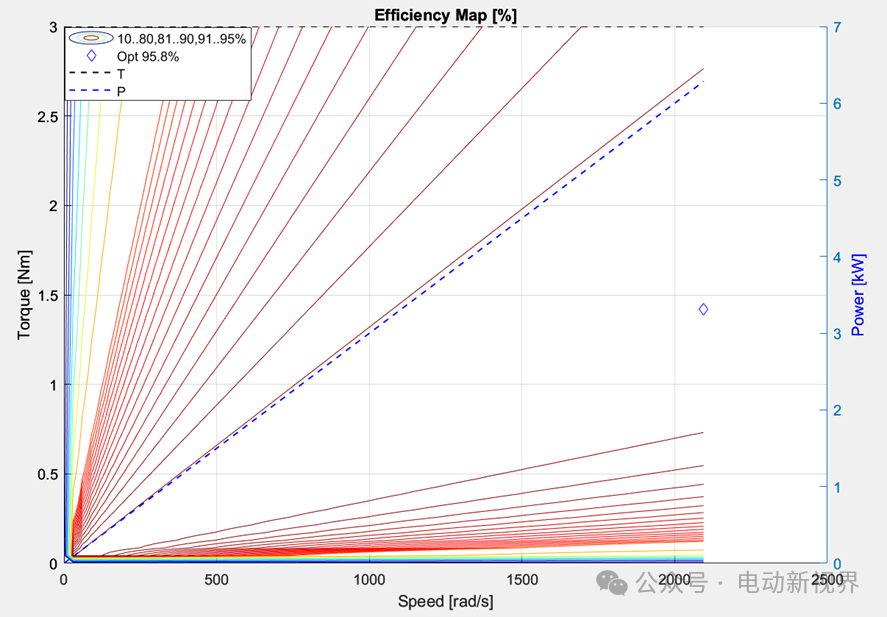
图15:无人机电机模拟效率/扭矩-速度特性
5.2 电动车电机
表3: 电动车电机规格
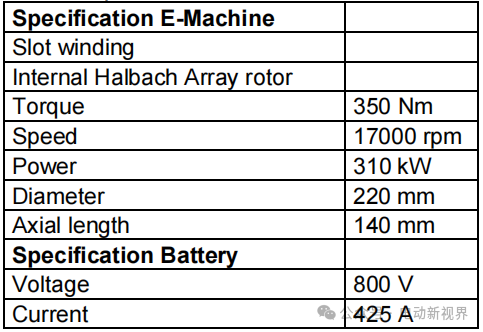
电动车越来越重要。监管措施等因素将在未来几年内使电动驱动成为独家或至少是主要驱动力。为了尽可能延长电动车的续航里程,需要最大程度的效率。为了充分利用电动驱动的封装优势,需要非常紧凑的设计。最后,制造成本必须非常低,而且质量非常好。表3中给出的电动车电机规格是设计研究的基础。
电动车的重要性日益增加。在其他因素中,监管措施将使电动驱动成为未来几年内独占或至少是主导驱动力。为了尽可能延长电动车的续航里程,必须达到最高程度的效率。为了充分利用电动驱动的包装优势,需要非常紧凑的设计。最后,制造成本必须非常低,但质量非常好。表3中给出的电动车电机规格是设计研究的基础。设计研究中采用了具有哈尔巴赫(Halbach array)阵列的内转子架构,以实现可能的最高扭矩与质量比以及目标封装空间要求。定子携带单层超紧凑波绕组,设计为槽绕组。图16显示了所选驱动电机设计的效率/扭矩-速度特性图。在开始场弱化范围之前,施加了所需的350 Nm扭矩,其中最大功率为310 KW。效率达到98%的最大值,而在非常广泛的扭矩和速度范围内,效率超过96%,实现了非常节能的运行。所需的主动质量仅为6.3 kg,其中2 kg由磁铁占用。该设计生动展示了超紧凑波绕组的巨大节能和紧凑性潜力。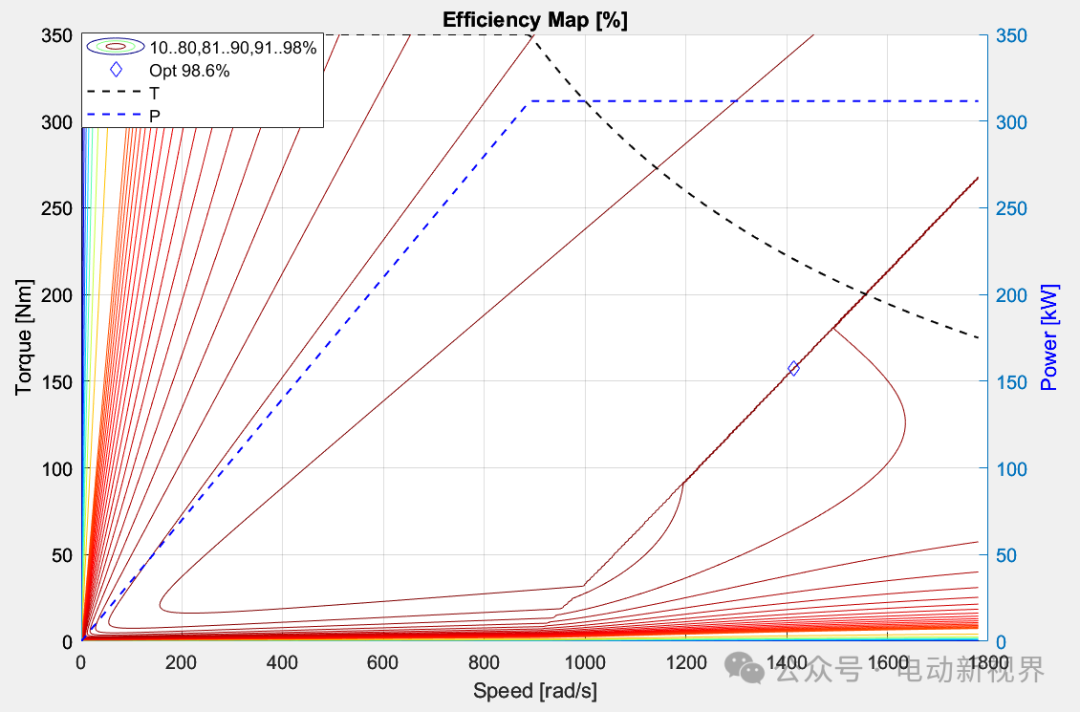
图16:电动车电机的模拟效率/扭矩-速度特性
6. 摘要与展望
本文提出了一种基于超紧凑波绕组的电机新设计。超紧凑波绕组结合了最高效率、最高扭矩和功率密度以及高质量和非常经济实惠的制造。显著性能改进的基础是超紧凑波绕组的最佳几何设计。一方面,这允许在绕组条形的形状上完全自由,以最大化铜填充系数,同时通过将用于绕组头部的铜量最小化以减少线路电阻和损失。这确保了所有条件下的高效运行。另一方面,机器的轴向和在某些情况下也是径向尺寸显著减小。减少的铜使用有助于降低成本。介绍了三种制造过程,其特点是高质量、高精度、短制造时间和低成本。所有三种工艺均可完全自动化,因此也适用于大规模生产。当然,也可以很好地处理小型和中型数量。新设计可以按比例调整到任何电机尺寸,从微型电机到最大发电机,都有相应的制造工艺。 本文介绍了货运电机的设计和构造。这表明了超紧凑波绕组可以使用成型技术制造,同时保持所有的几何和功能特性。另外两个设计示例,无人机电机和电动车驱动电机,分别展示了极轻量级结构和极高效率的示例。制造技术处于发展和测试阶段。通过固态成型可以制造小批量的原型。超紧凑波绕组的焊接技术生产正在准备中。欢迎有兴趣和能力的合作伙伴参与这项工作的下一步。目标是在广泛的环境中推广这项新的电机技术,以使其在经济和社会上的生态和经济优势得到利用。
作者:Prof. Dr.-Ing. Roland Kasper, Otto-von-Guericke-Universität Magdeburg,IPK Ingenieurbüro Prof. Kasper
References
Cai, W., C., Congdon, C., F., Fulton, D., A.: DE10321956A1, Hairpin woundstator for electric machine, has two windings in stator slots, where eachwinding has hairpin forming layers of conductors, with each hairpin havingtwo legs of unequal length, Delco Remy America, Inc., Anderson, Ind., US
Detela, A.: EP2695284B1, COMPACT MULTIPHASE WAVE WINDING OFA HIGH SPECIFIC TORQUE ELECTRIC MACHINE, Elaphe PropulsionTechnologies Ltd., SI (2020)
Sadiku, S.: DE 000019909026 A1 Verfahren und Vorrichtung zur Herstellung von Spulen in Form einer Wellenwicklung für elektrische Maschinen,ELMOTEC Elektro-Motoren-Technik GmbH, DE (2000)
Lüttge W.: EP 3 182 568 A1 SHAFT WINDING DEVICE, AUMANN GMBH,DE (2017)
Kasper, R., Heinemann, W., Borchardt, N.: DE102011111352B4 Elektromotor mit eisenloser Wicklung, Otto-von-Guericke-Universität Magdeburg,DE (2015)
Kasper, R., Borchardt, N.: DE10 2016100744B3 Elektrische Maschine,Otto-von-Guericke-Universität Magdeburg, DE (2016)
Kasper, R.: DE102022113127 Wicklung, elektrische Maschine und Herstellungsverfahren (angemeldet 2022)