压实密度对硅碳电极膨胀和电化学性能影响的模拟研究
本文摘要:(由ai生成)
本文研究了硅氧化物/石墨复合负极材料在锂离子电池中的应用,特别是搭配高镍NCA正极时的性能。实验和模拟发现,提高压实密度虽能增加能量密度,但影响电化学性能,导致电池容量降低、循环性能下降和内阻增大。模拟结果验证了模型可靠性,并指出高压实密度下颗粒开裂增多,内阻增大,库仑效率低。该研究为锂离子电池负极材料选择和结构优化提供了重要参考。
锂离子电池正朝着更高的能量密度方向发展,未来更集中在使用高镍三元材料作为正极材料,以及硅基材料作为负极材料。硅基负极材料具有许多优点,例如,硅(Si)因其高重量比容量(4200 mAh/g)、低电压窗口、低成本和丰富的自然储量而被视为有前途的候选材料。然而,纯硅在电池中的严重体积变化(>300%)和不稳定的固体电解质界面(SEI)形成限制了其广泛的实际应用。相比之下,氧化物(SiO)显示出相对较高的理论比容量(1300 mAh g−1),在充放电过程中体积变化小,满电体积膨胀约为200%。目前,SiO/石墨复合负极可以利用两种材料的优势,已经开始在商业产品上开始应用。然而,由于硅的存在,体积膨胀仍然是一个问题。
本文通过实验和模拟相结合的方法,深入探讨了硅氧化物/石墨(SiO/C)复合负极材料在锂离子电池中的应用行为,特别是在高镍NCA正极材料搭配下的体积膨胀、电化学性能演化及其对电池厚度和内阻的影响。 首先,制备了不同压实密度(CD)的三种SiO/C复合负极,分别为1.38 g/cm³、1.52 g/cm³ 和 1.62 g/cm³,并与NCA正极组装成设计容量约3Ah的软包电池,每种电池制备了3个样品,数据为三者平均值。电池厚度膨胀、内阻和循环性能如图1所示。随着压实的增加,电极中的活性颗粒更紧密地排列,开放孔隙分布减少。这种紧密排列在实际设计过程中可以提高电池的能量密度。然而,过高的压实密度可能导致颗粒破裂和电极内部的裂纹,从而影响电池性能。此外,由于锂离子主要通过电极厚度方向传输,过高的压实密度会增加锂离子在电解液中的传输阻力,从而影响电池的电化学性能。图1 不同压实密度的三种SiO/C复合负极与NCA正极电池行为化成后,电池的厚度显著增加,并且这种变化是不可逆的。厚度变化随着压实密度的增加而增加,且F3(最高压实)的厚度变化最大。在充电过程中(SOC从0%增加到100%),电池厚度持续增加,这主要是由于SiO/C负极的膨胀导致的。放电过程后电池厚度能够恢复到初始状态,表明充放电过程是可逆的。 电池内阻(IR)随着SOC的变化而变化,这一变化趋势与电池厚度的变化相似。特别是在化成过程中,F3电池的IR显著高于F1和F2,这表明在大的厚度变化下电池的内阻也较大。IR的增加主要是由于电极孔隙率的降低和孔隙的曲折度增加,导致锂离子传输路径变长。此外,电极材料之间的接触应力增加,可能导致活性颗粒的破裂,从而破坏了锂离子的传输路径和电子传导网络,最终导致内部电阻的增加。较高的压实密度导致较低的电池容量,高压实电极的孔隙率降低,限制了活性材料的充分利用。在100个循环后,F1、F2和F3三种电池的容量保持率分别为86.2%、78.5% 和 66.4%。此外,电池的库仑效率也随着压实密度的增加而降低,这可能是由于高密度电极在充放电过程中导致活性颗粒破裂,产生过量的固体电解质界面(SEI)膜,消耗了大量的电解液。因此,高压实的电池表现出较低的库仑效率和更多的累积容量损失。为了深入理解SiO/C复合负极在锂离子电池中的电化学和力学行为,采用COMSOL Multiphysics软件,建立了SiO/C||NCA全电池的电化学-力学模型,研究了不同压实密度的影响。几何模型如图2所示,三种压实密度主要通过调节电极的厚度值和活性颗粒之间的间隙来实现的。全电池几何建模包括负极、隔膜和正极。其中,负极由多孔碳胶相、椭圆形石墨颗粒和圆形SiO颗粒组成。而正极由NCA颗粒和多孔碳粘合剂畴组成。在多孔碳粘合剂畴相中,Li通过电解质传输,电子通过导电剂的固相颗粒传输。 首先,计算电化学充放电行为,根据Newman和Doyle开发的经典Newman模型,电化学模拟主要方程如下:其中 Jl是碳胶相域中的锂通量,cl 是液相中的锂浓度,t+是Li迁移数,il和is是液相中Li和固相中电子的局部电流密度,ɸl和 ɸs 分别是液相和固相的势,F、R和T分别是法拉第常数、理想气体常数和温度。有效扩散系数Dl,eff,离子电导率σl,eff 和电子电导率σs,eff都可以使用布鲁格曼关系进行校正。活性颗粒和电解质界面处的电化学反应满足Butler-Volmer方程,以及固相颗粒中锂浓度的演变方程为: 电化学结果计算完成后,将石墨和SiO颗粒的体积变化与SOC之间的函数关系输入到力学模型中,忽略了NCA颗粒的变形(图3)。以固相内某时刻的锂浓度为输入条件,计算锂嵌层过程中颗粒的体积应变,进一步产生电极变形。在力学模型中,石墨、SiO和碳胶相域被视为线性弹性材料。胡克定律用于描述应力和应变张量之间的关系,位移场 u 和应变张量 e关系方程为:其中 Σ 是柯西应力张量,C 是弹性张量,e 是总应变张量,einel是非弹性应变张量。下表中列出了所有使用的参数。模拟充放电曲线与实验对比如图4所示,基本验证了模型的可靠性。 下面展示更多的计算结果,如不同压实密度和不同时刻/SOC下固体颗粒/液相的锂浓度分布,不同SOC和压实密度下全电池的体积变化/厚度变化,以及不同SOC和压实密度下石墨、SiO和碳胶域的应力变化。固体颗粒内的锂浓度分布演变如图5所示。在低压实密度下,颗粒更分散,迂曲度更小,锂输运路径更短,离子浓度发生变化更快。相反,在高压实密度下,孔隙率降低会收紧颗粒之间的间隙,阻碍锂的传输,从而导致传输速度变慢。在恒流充电结束时(图6a,d),石墨与隔膜界面处的点(图1中C,SEP点)三个电池之间的SOC差异非常小,而在集流体附近(图1中C,CC点)观察到较大的差异,其中F3的极化最大。这一结果可归因于高压实导致低孔隙率和受限的锂传输,导致阳极两侧差异较大。在恒压充电结束时(图6b,d),石墨中锂浓度在隔膜和集流体附近的三个压实密度分布相对均匀,因此SOC差异较小,表明状态更一致。通常,恒压充电过程用于消除电极的SOC差异。最后,在放电结束时(图6c,d),所有锂浓度都非常低,代表脱锂结束。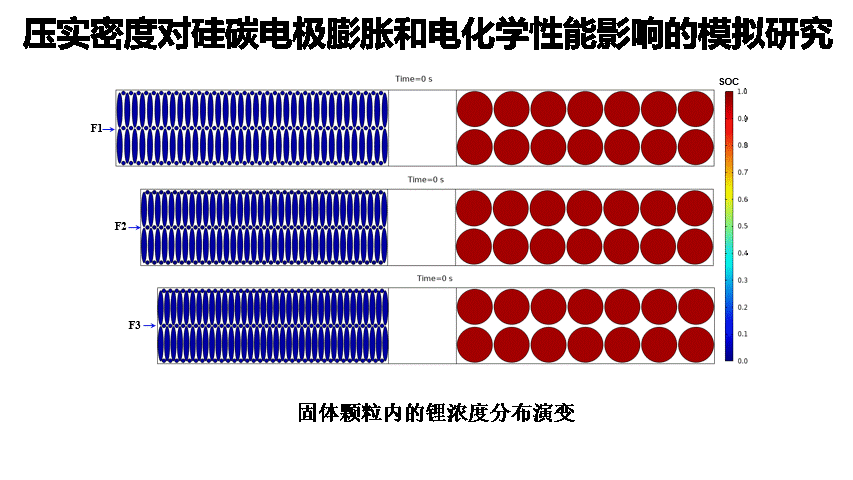
图6 不同CD电极内活性颗粒在不同时间的锂浓度分布对于SiO颗粒,无论是在恒流充电的末端还是在恒压充电的末端(图6e),F1-F3中隔膜和集流体附近的锂浓度分布表现出相对较高的差异。像石墨一样,F3显示出最大的差异,表明极化最大。NCA阴极的隔膜和集流体之间的相对较小的差异(图6f)表明锂的运输动态迅速,不同压实密度之间的SOC差异是由阳极变化引起的。在充放电过程中液相内锂浓度分布的演变如图7所示。F1 的锂浓度在恒流充电结束时最高(图 8a、a1),而 F3 的浓度最低。F3 中的低锂浓度归因于高压实密度电极中锂传输缓慢,特别是在集流体侧,锂浓度显著降低。尽管最初的浓度不同,但在恒压充电结束时,三种电极的锂浓度分布差异很小(图 8b、b1),F3 仍然表现出最低的浓度。然而,在放电过程中(图8c,c1),情况正好相反,F3在集流体侧的锂浓度最高,而F1的锂浓度最低。而低压实电极在放电结束时表现出快速的锂传输和低锂保留率。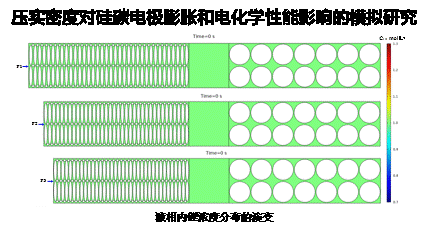
然后再模拟了全电池的厚度变化过程,如图9所示。电池厚度变化的影响如图10(a-c)所示,模拟结果(图10d)与实验结果(图1)相似。在电压充电结束时(∼10,000 s),单个电池的厚度增加了近10 μm,实际电池(10层)增加了近100 μm,这与充放电时的实验值(0.1 mm)吻合,如图1所示。负极的厚度膨胀了约10%,这与实际厚度变化一致。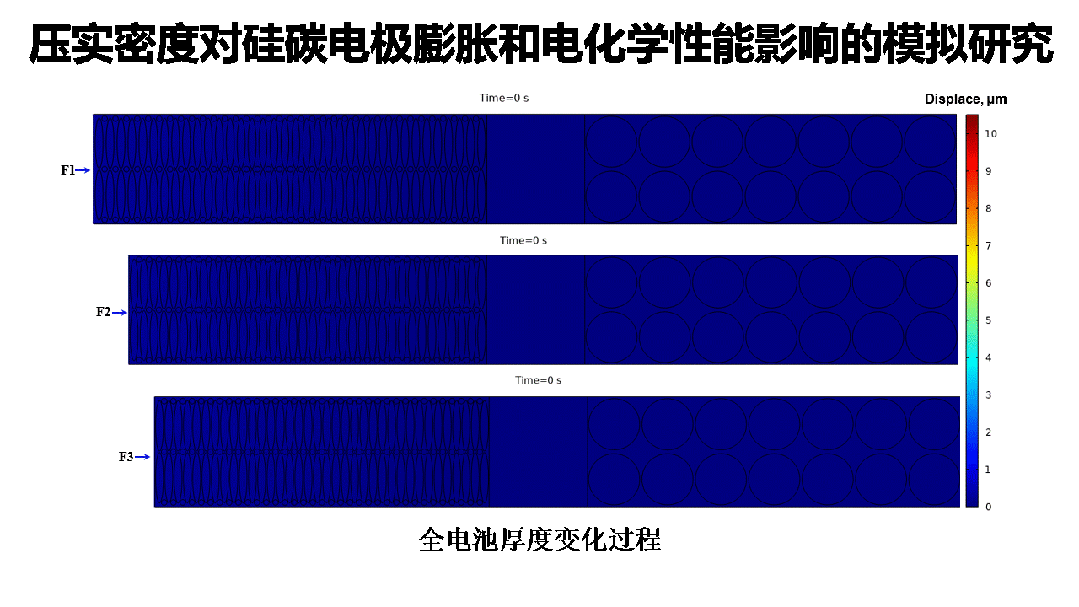
图10 不同压实阳极在不同时间的厚度变化及其厚度变化率F1的电极表现出最高的厚度变化,但厚度变化率最低,而F3电极表现出最小的厚度变化,但厚度变化率最高。与F1相比,F3电极的压实更高,厚度更低,导致充放电时膨胀率更高。von Mises 应力表示电极材料失效或疲劳,用于描述电池在电池和颗粒水平上的膨胀力。在颗粒水平上,石墨、SiO颗粒和碳胶域的应力是不同的,如动画图11和图12所示。最高应力点分布在隔膜侧附近,选择了隔膜附近的颗粒,石墨、SiO和碳胶相在恒压充电末端的von Mises应力分布如图12(a–c)所示。石墨和SiO颗粒的应力曲线与图6(a,b)中的锂浓度分布曲线相似,因为锂从NCA输送到阳极并插入石墨和SiO颗粒中。颗粒膨胀应力增加,特别是对于SiO,表现出比石墨更高的应力(图12a1,b1)。碳胶域也显示出与SiO相似的应力演化曲线。较高的压实阳极在颗粒周围产生更高的应力,颗粒排列越接近,在充电/放电过程中产生的应力就越大,并且产生的裂纹就越多。 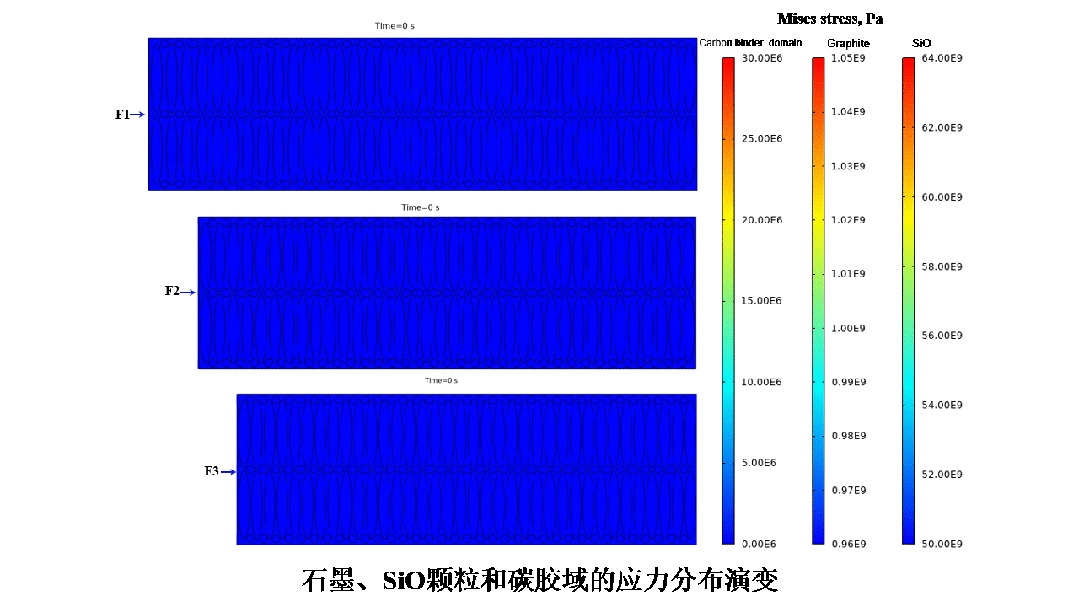
图12 恒压充电末端石墨、SiO和碳胶相的von Mises应力分布(a–c);石墨、SiO和碳胶相结构域随时间变化的von Mises应力变化(a1–c1) 本文全面研究了高Ni阴极电极(NCA)对SiO/C负极电池,并深入分析了负极压实密度对电极膨胀、电化学和力学性能的演化规律。高压实会减少颗粒之间的间隙,从而降低孔隙率并抑制锂的输送。颗粒排列越近,颗粒开裂越多,产生高内阻和低电化学性能。Bing Xue, Haixiang Liu, Xiangkun Wu, Insights into mechanics and electrochemistry evolution of SiO/graphite anode by a composite electrode model, Journal of Energy Storage, 2024,77, 109979.