高效的冷却结构是避免气冷涡轮叶片受热损坏的关键,直接影响叶片冷却效率和航空发动机稳定性。但是高效冷却结构导致主流与冷气流的相干效应更加复杂,并且高效冷却结构的发展一直受到加工工艺的制约。本文从控制冷气流动的角度,将涡轮叶片分为前缘、中弦和尾缘区域,重点综述了近十年气冷涡轮叶片冷却结构的研究进展以及涡轮旋转状态下的气动传热特性,包括涡旋冲击冷却、气膜孔形状、尾缘内部强化换热结构与分隔肋形状等。在此基础上,对比了各个结构的冷却效果,并且指出各类冷却结构的缺陷。最后提出气冷涡轮叶片未来的发展方向和难点。 涡轮叶片冷却结构的设计是航空发动机制造的重要环节。随着耐高温材料研究的持续推进以及采用更加复杂高效的冷却结构,涡轮叶片可耐受的工作温度已达到2200K左右。截至目前,先进的冷却技术包括发散冷却、气膜冷却、冲击冷却、内部强化对流冷却、层板冷却和热障涂层等,“十二五”期间,国内挂片实验有效温降已达到700K。另一方面,涡轮叶片受高温燃气冲刷后极易蠕变伸长,导致涡轮其他部件断裂。因此,为提高发动机效率和避免出现事故,航空发动机涡轮叶片冷却技术的深入研究具有重要意义。本文总结了近十年涡轮叶片冷却结构的研究现状,整理并分析前人的研究成果。值得注意的是,燃气轮机涡轮叶片的尺寸较大、工作温度较低,导致其冷却结构的设计侧重于相对简单、成本较低和自由度较高的方向,F级和G级燃气轮机的冷气流量占压气机进口流量的16%~20%,燃气轮机涡轮叶片上气膜孔孔径为0.5~1mm。而航空发动机涡轮叶片的内部冷却结构更加紧凑,航空发动机冷气流量的占比可达20%~30%,并且气膜孔数量较多且孔径只有0.1~0.8mm。尽管燃气轮机与航空发动机冷却结构的设计细节差别较大,但是二者的设计原理是通用的。因此,燃气轮机冷却结构的若干研究工作被讨论,这些归纳结果不仅可作为涡轮叶片气热耦合研究的基础,而且可作为改善冷却技术的参考,进而为航空发动机气冷叶片气热耦合实验与设计提供支持。
表1 涡轮叶片冷却技术分类
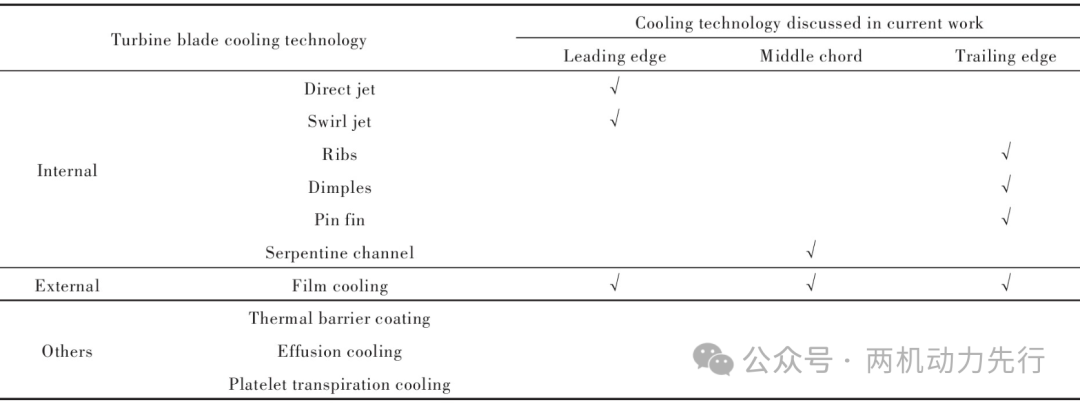
虽然发散冷却具有较高的冷却效率,但是发散冷却结构制造困难,并且强度较低,导致其不能被应用到工程领域;层板冷却与发散冷却原理相似,冷气从层板中的微型通道穿过,吸收热量后从气膜排出;热障涂层属于高温材料领域,不符合本文研究范围;此外,涡轮叶尖区域的冷却换热可参阅文献,本文研究内容不包括此方面。因此,除上述冷却技术,本文着重讨论了涡旋冲击冷却,气膜孔参数,尾缘内部强化换热结构与扩展板形状等,如表1所示。由于几何形状的限制,叶片不同区域采用不同的冷却结构。如图1所示,冲击冷却与气膜冷却被广泛用于叶片前缘区域;气膜冷却和内部强化对流冷却被用于中弦区域,中弦区域包括吸力面和压力面;由于尾缘较薄,一般采用劈缝气膜冷却或倾斜冲击冷却混合内部强化对流冷却的方式。另外,由于涡轮动、静叶片的工作环境存在差异,动叶中每个区域的冷却结构(尤其是内部冷却通道)在旋转状态下的气动传热特性需单独分析。 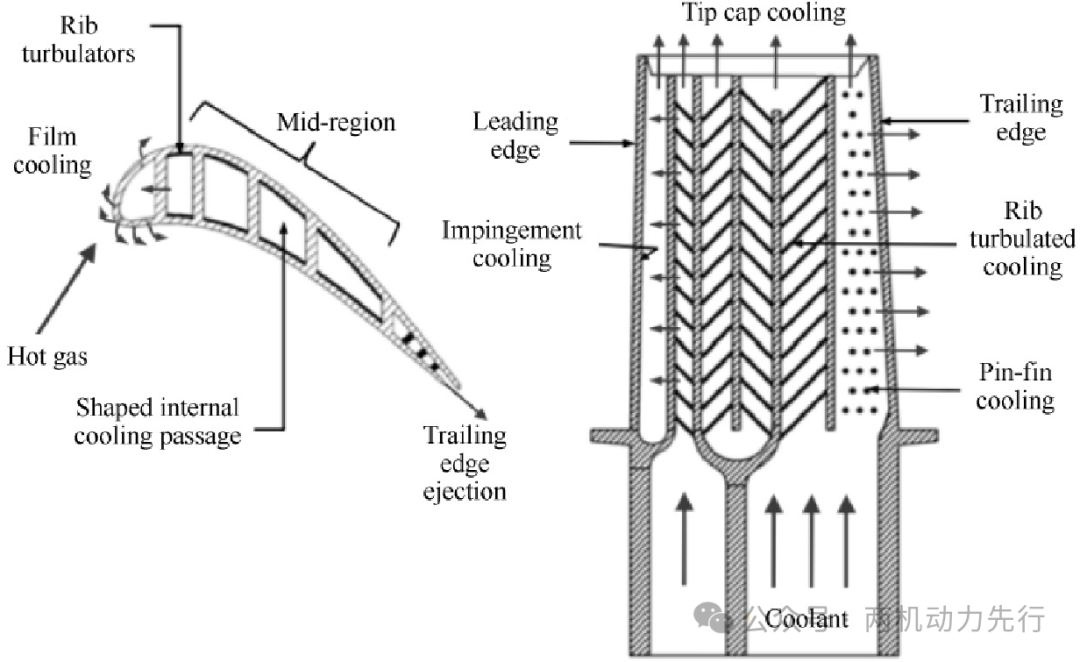
图1 叶片复合冷却结构
本文将叶片分成前缘、中弦、尾缘区域,着重论述了每个区域冷却结构、冷却结构参数以及旋转作用等因素对冷却效率的影响,发现各结构影响机理和不足,并提出针对性建议,最后展望了航空发动机气冷涡轮叶片冷却结构的发展趋势。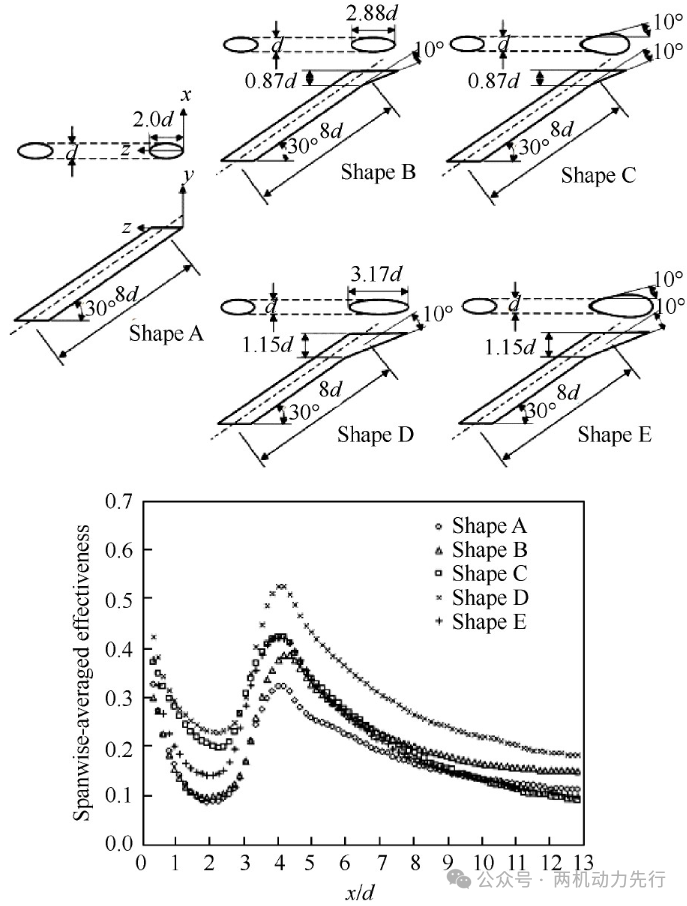
图 三脚架孔和轮廓的冷却效果
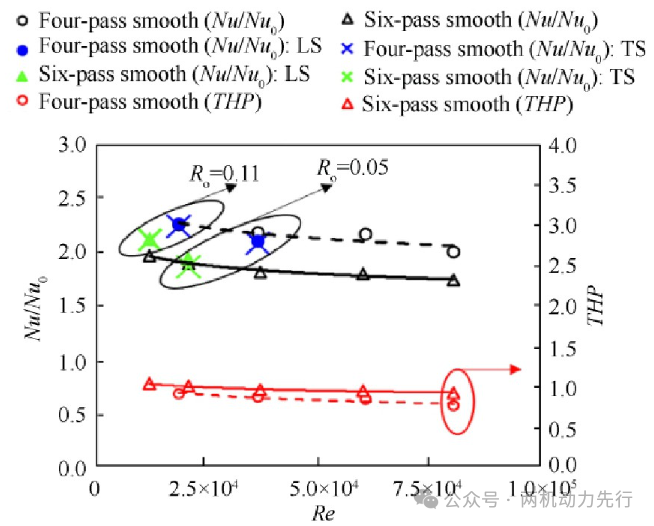
本文总结了近十年涡轮叶片冷却结构的研究现状,整理并分析前人的研究成果。将叶片分成前缘、中弦、尾缘区域,着重论述了每个区域冷却结构、冷却结构参数以及旋转作用等因素对冷却效率的影响,发现各结构影响机理和不足,并提出针对性建议,最后展望了航空发动机气冷涡轮叶片冷却结构的发展趋势。 20世纪50年代,美国首先采用熔模铸造方法制造航空发动机空心涡轮叶片,随后涡轮叶片的制造工艺不断提高,从有余量加工到无余量加工,再到目前最优良的单晶无余量空心叶片加工,冷却结构的复杂度也随之提高。但是提高航空发动机的推重比是科学家们永恒的追求,不断提升的工作温度迫使涡轮叶片冷却结构更加复杂,同时对涡轮叶片的制造工艺提出更高的要求。20世纪末先后出现铸冷技术和3D增材制造技术,铸造工艺的革新一方面使航空发动机零件的加工成本降低,例如2020年7月,俄罗斯3D打印的轻型航空发动机通过飞行实验,与常规制造相比,其生产时间缩短为原来的1/20,成本降为原来的1/2,并计划在2021年开始量产;另一方面使更复杂和狭小的内流通道加工成为可行,涡轮冷却的研究方向开始向复合冷却结构倾斜,例如受限空间冲击/涡旋+气膜+扰流肋、微型肋/销翅+凹坑等。因此,随加工工艺的进步,未来气冷涡轮叶片的发展趋势依然是优化冷却结构,以适应不断提高的工作温度;另外,探究受限空间内复合冷却结构在静止和旋转状态下的气动传热特性将是主要研究方向之一;但是依然存在挑战和难点。具体分为以下三点。 (1)在内部冷却方面,需要改善内部冷却结构,合理控制冷气流动,在提高冷却效率的同时,要兼顾冷却效率均匀分布。例如,涡旋冷却、蛇形通道及微尺度通道等结构具有这方面的优势,但是,涡旋冷却效率低于冲击冷却效率,因此,未来可以在二者结合的基础上进行优化研究,实现优势互补,并且与气膜冷却和扰流肋组成复合冷却结构;蛇形和微尺度通道的气动损失较大,未来可以借助气热耦合方法改进兼顾冷却效率和气动损失的内冷通道,并且3D打印技术的出现使狭长通道内布置凸起、凹坑和肋片的复合结构成为可行。 (2)在叶片前缘、中弦和尾缘区域,优化外部冷却结构的形状和排列方式依然是研究热点,使气膜的覆盖面积更大,贴壁能力更高。例如,与传统圆柱形孔相比,异形孔和浅槽孔等冷却结构产生的气膜在展向上分布更广,并且流向上延伸距离更长,但是在前缘滞止区,气膜孔的位置需要谨慎选择,这将影响冷气量流向吸力面和压力面的比例,进而影响前缘的气膜覆盖程度;并且,在靠近叶肩和轮毂的区域,由于涡系的影响,气膜容易从壁面抬升,热应力较大;另外,吸力面上较大曲率处的逆压梯度易导致气膜分离,这一问题至今没有得到有效解决。 (3)在优化冷却结构的进程中,气膜孔的总体出口面积增大,叶片内部空心腔室更多,在未研发出超耐温材料和制造工艺受限的状态下,提高冷却效率的同时,减少冷气量和保证叶片结构强度依然是涡轮叶片冷却的难点。值得思考的是,在冷气流量和温度相同的前提下进行复合冷却优化是一个悖论,以冲击+气膜复合冷却结构为例,此时冷气流的热容量被固定,若冲击冷却效率较高,则被气膜孔抽出的冷气流温度升高,气膜冷却效率便会降低。因此,在复合冷却优化时应着重考虑冷却效率的分配,才能获得最佳综合冷却效率。 另外,由于转动实验的难度和成本高于静止实验,旋转状态下动叶冷却结构气动传热性能的研究尚不充分,尤其是涡旋冷却、复合冷却和尾缘内部冷却。为避免或利用哥氏力和浮生力的影响,动叶中的冷却结构需要单独优化,并且随航空发动机推重比增大,动叶的工作温度必然提高,迫使其应用更复杂的冷却结构。 (1) 前缘内部冷却结构采用冲击冷却可以获得较高换热系数,但是分布不均匀,而涡旋冷却可以有效减小叶片前缘区域的高温区,因此涡旋冷却和冲击冷却的优势互补成为改善前缘冷却效率的焦点。随着加工工艺革新,弦中区的冷却通道和湍流器更复杂,其细节优化依然是研究热点。尾缘内部喷嘴与肋的相对位置,冷气流出口位置以及销翅的排列方式、形状都深刻影响冷却效率,在大小和形状相同的前提下,凸起比凹坑获得的冷却效率高,但凹坑的气动损失更小。 (2) 前缘和中弦外部气膜孔设计原则为:增大气冷出口面积,减弱冷气流出口动量,增加气膜覆盖面积,减少冷气流与主流的掺混损失。尾缘外部安装扩展孔可以增大冷却效率,而扩展孔形状、大小、位置和排列方式依然存在研究潜力。(3) 孔距过大导致气膜覆盖率降低,过小则需要更多冷气量,因此特定冷却结构存在最佳孔距。并且改良劈缝上唇板形状、减小上唇板厚度可以增大冷却效率。采用高效和低成本的遗传算法寻找最佳孔排布置或劈缝参数是未来研究方向之一。
(4) 受旋转影响,前缘和尾缘的平均冷却效率增大,压力面冷却效率降低,但是需要继续深入研究旋转对吸力面冷却效率的影响。并且,由于转动实验的难度和成本较大,关于旋转状态下动叶冷却结构气动传热机理的研究尚不充分,尤其是涡旋冷却和复合冷却。 (5)随航空发动机的发展和制造工艺的革新,气冷涡轮叶片冷却结构向单种冷却结构优化和复合冷却结构发展,但是气动损失和叶片结构强度等潜在问题也凸显出来。