压力容器制造检验概述
摘要
文章全面阐述了压力容器产品质量检验的全过程,从材料检查到最终的产品出厂技术文件和资料,强调了检验的重要性和严格性。介绍了检验的目的、依据、内容和方法,包括材料审核、外观尺寸检查、焊接和无损检测、热处理、耐压和泄漏试验等关键步骤,以及安全附件和产品合格证明的检查,确保压力容器的安全和可靠性。
正文
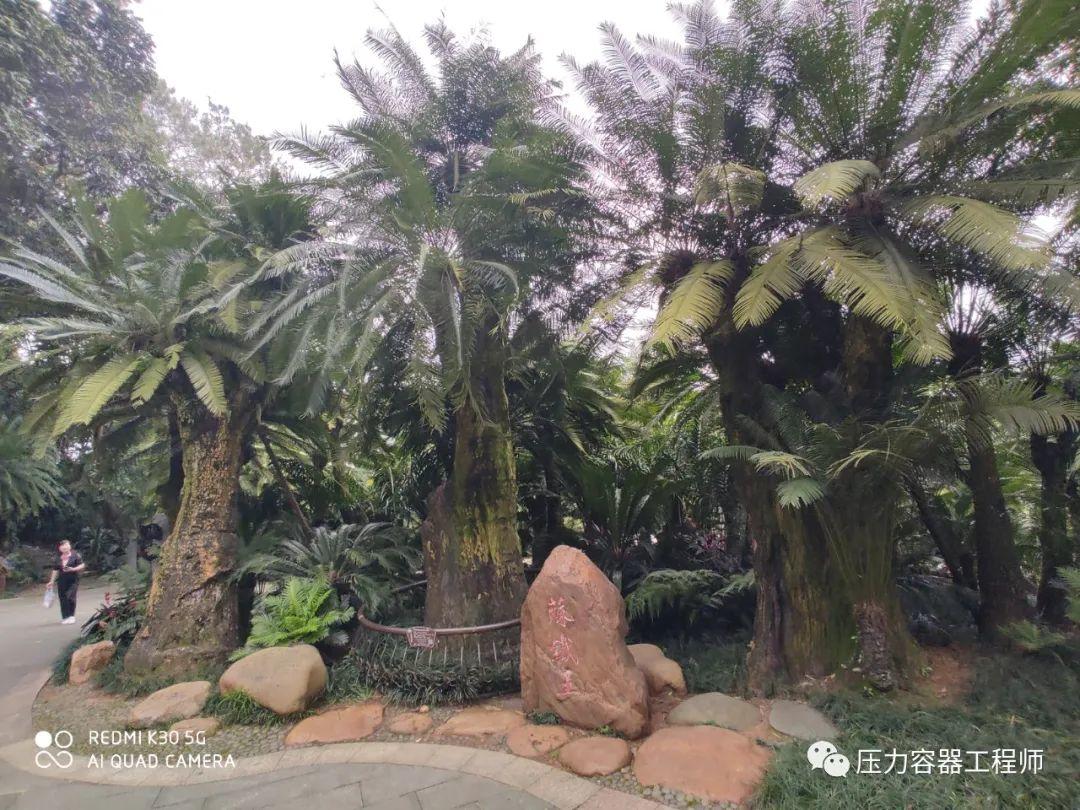
一、目的
通过制造检验,对压力容器产品质量是否符合国家安全技术法规、标准、设计图纸、技术要求、用户合同做出符合性的判断。二、压力容器制造特点
1.不同零部件(形状、材质)分别制造然后组装,组装方法主要是焊接。2.需用多种冷、热加工方法,其中热加工技术与质量是关键(质量影响因素的多样性、检验的难度)。3.涉及安全,是质量检测而不是性能检测,因此要求全过程质量控制。三、检验依据
1)依据法规、标准、有效设计文件、工艺文件、制造单位的体系文件及用户合同技术要求编制检验文件。3)设计变更(材料代用、无损检测方法改变、加工尺寸、机构变更等)、工艺变更调整检验文件。4)对压力容器制造过程中涉及产品质量的所有项目进行检验。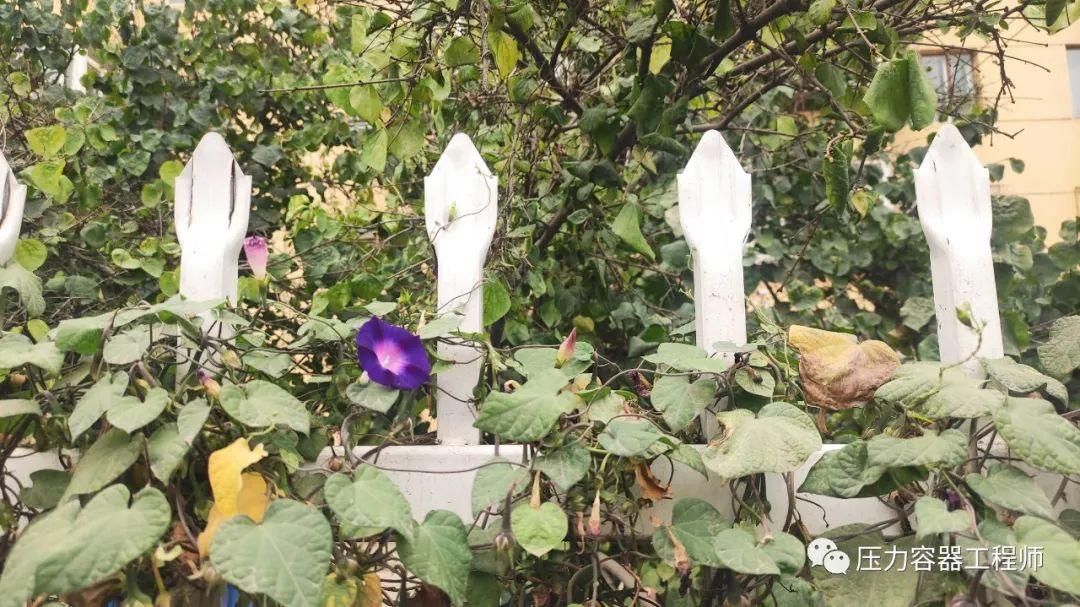
四、材料检查:板材、锻件、管材、焊接材料。
生产单位检验章、(经办人章的有效复印件)、符合法规标准规定、齐全、清晰;③ 其他检验项目:化分、力学、弯曲、硬度、水压试验、超声波、涡流、压弯、扩口等等。④对于有防腐要求以及不锈钢有色金属不得采用硬印标记;5.主要受压元件材料复验的审核下料前按规定复验、是否检查合格。五、外观和几何尺寸检查
a.错边的成因与防治:A 类接头~对齐、B 类接头~外圆周长、局部不圆;5.9 法兰密封面质量、安装垂直度、螺孔与设备中心线、端盖开合及连锁。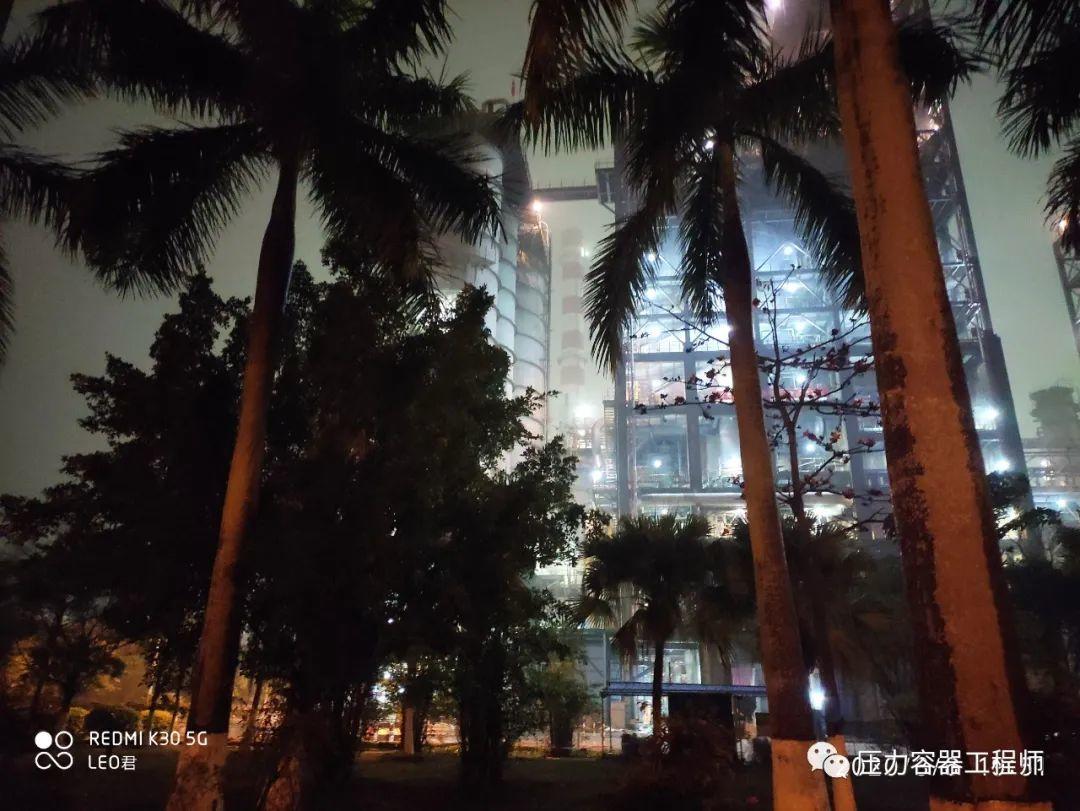
六、焊接检验
焊接质量要素与对策:力学性能-焊接工艺评定、产品焊接试板;焊接缺陷-无损检测;外观质量—宏观检查。6.1 焊接工艺评定、施焊焊工资格(项目和范围)、做法与要求:事先预防与指导、节约。6.2 产品焊接试板:事后检查,确认产品施焊过程是否符合焊接工艺文件。6.3 焊接试件性能报告,确认试验结果和审批手续。6.4 检查主要受压元件焊缝的焊工钢印或焊工代号纪律见图。七、无损检测
b.材质—可焊性、同一缺陷对不同材质的不同影响、重要性、经济性b.局部检测产品中应 100%检测的部位(开孔、被复盖的接头、凸形封头拼缝、嵌入式接管、D≥250mm 的接管对接)。八、热处理:分类(按目的)
特殊条件—图样注明应力腐蚀;盛装毒性极度、高度危害介质;无需进行的条件—奥氏体不锈钢1.焊后热处理方法—整体炉内;分段炉内;局部;现场2.焊后热处理工艺—进、出炉炉温;升、降温速度;炉内气氛;炉外冷却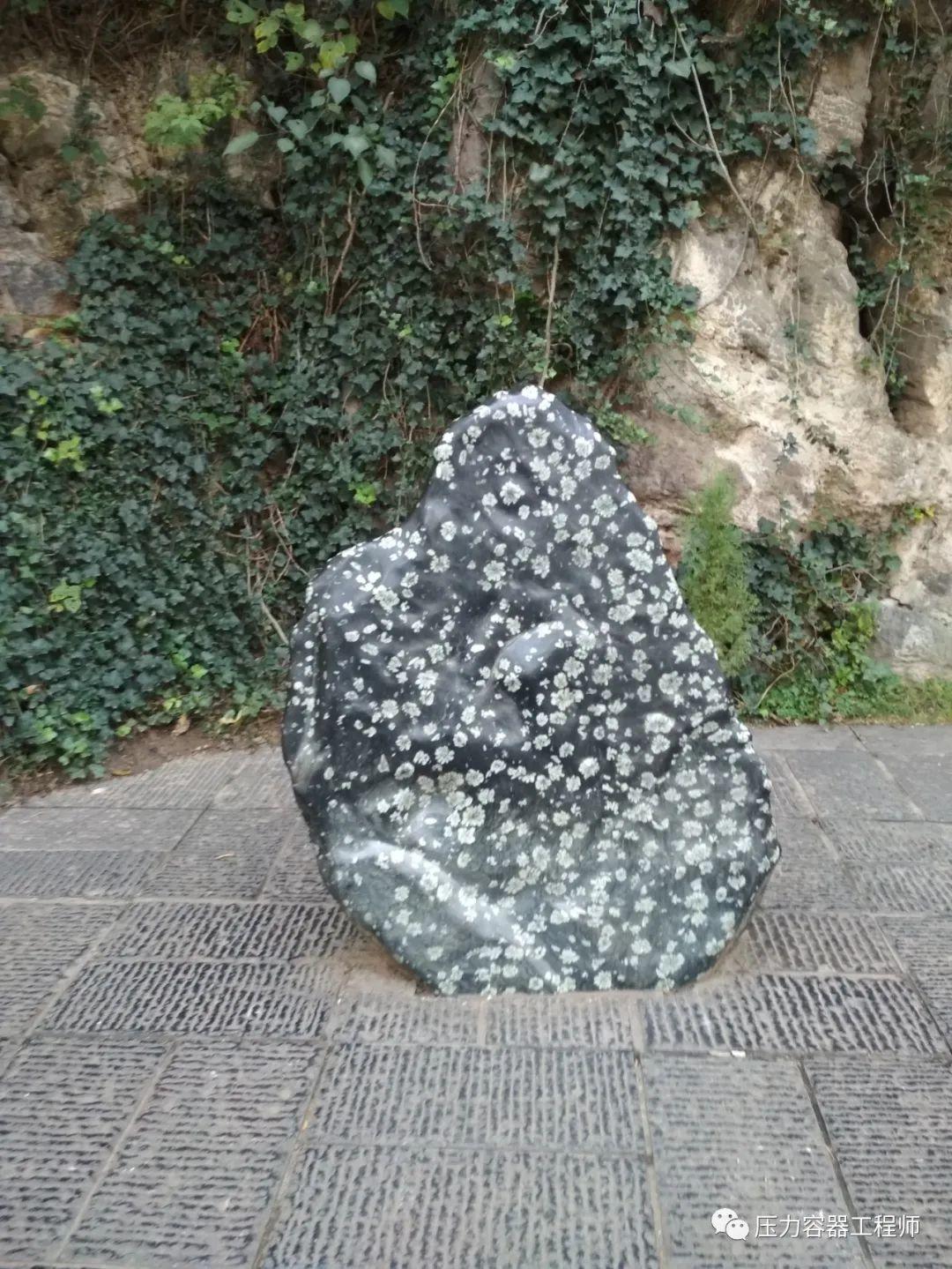
九、耐压试验,
2)确认试验环境条件(安全设施、试验用液体和气体的温度、Cl离子含量);十、泄漏试验
2)确认试验环境条件(安全设施、试验用气体的温度);十一、安全附件
检查安全附件数量、规格、型号及产品合格证,确认符合设计文件。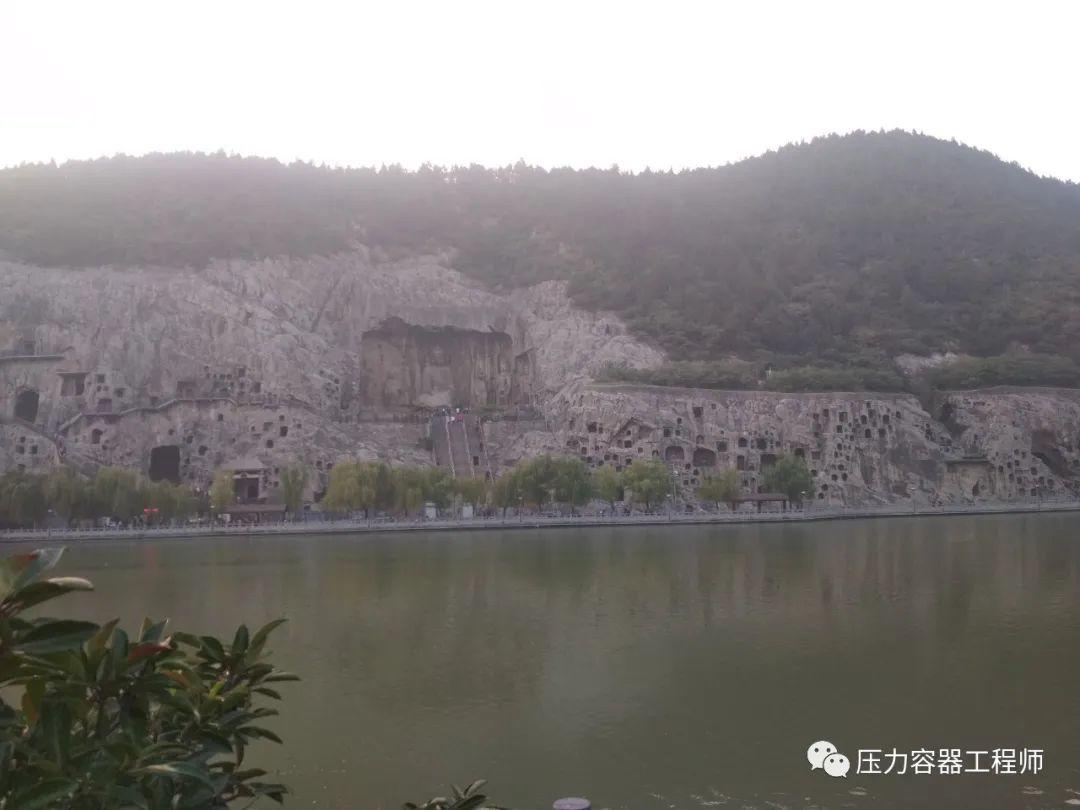
十二、产品出厂技术文件和资料
① 竣工图(设计章、竣工章)标注制造单名称、制造许可证编号、审核人签字;如材料代用、无损检测方法变化、加工尺寸方法变化有设计单位书面文件批准。在竣工图上清晰标注,标注处有修改人签字及修改日期。② 产品合格证(含产品数据表)、产品质量证明文件(主要受压元件的材质证明、材料清单、质量检验计划、结构尺寸检查报告、焊接记录、无损检测报告、热处理报告及自动记录曲线、耐压试验报告、泄漏试验报告、产品铭牌拓印件)。2)检验责任师、质保师在合格证签章、并加盖制造单位质量检验章。3)封头、锻件等受压元件的制造单位,应向其要求提供质量证明文件。十三、铭牌及拓印件(复印):铭牌内容符合《容规》要求。