法雷奥外励磁同步电机从圆线绕组到扁线发卡定子技术的发展过程
摘要
外部激磁同步电机(EESM),也称为绕线转子同步电机(WRSM),已经在雷诺集团用于电池电动汽车(BEV)多年。其它汽车厂也考虑采用这种电机,因为它们在高速下(高速公路运行点)具有良好的效率和低拖曳扭矩,不含有稀有材料,同时还具有较高的安全性(故障模式策略可以是开路,而不会在电机的相上产生高压:反电动势)。这些电机的主要缺点是紧凑性较低、转子的热传导性差以及需要向转子施加直流电功率。为了改善这种设计的紧凑性和热传导性能,雷诺集团与法雷奥公司合作开发了一种扁线发卡(也称为HairPin)外励磁同步电机,作为他们的下一代车用电动机。本文将概述外励磁同步电机是如何从圆形绕组定子发展到扁线发卡定子技术的转变过程。
环境问题、监管限制和财政激励推动了纯电动汽车(BEV)的快速发展。目前,这些车型可供选择的范围相当大,汽车制造商之间的竞争也很激烈。纯电动汽车的使用发生了变化,续驶里程成为关注的重点之一。公路效率和系统成本是目前的重点。在这种情况下,雷诺希望突出他的外励磁同步电机在高速效率和无稀土材料方面的优势。结合法雷奥在发夹绕组技术方面的背景,本文将重点介绍从圆线绕组转向与外励磁同步电机技术相结合的发夹绕组的益处。在本文中,我们希望突出在800V解决方案上使用发夹定子绕组的这种技术的优势,并着重与圆线六相电机(所谓的6AM)相比,性能有所提高。针对这种设计需求,我们优先考虑的是开发一个适应广泛性能范围的系列家族,从而无需进行重大工艺修改。我们将展示这个与过程相关的约束,如何在极对数定义、槽的数量以及槽内的层数方面的驱动优化。1.1 背景
为了解决与800V电池兼容性、效率、尺寸限制和成本改进相关的问题,雷诺和法雷奥正在为未来的应用开发800V外励磁同步电机发夹式绕组技术。雷诺电动日的目标是实现一些改进:
图1:在2022年雷诺电动日期间设定的目标
另一个约束是可扩展性需求,以满足高性能(意味着最大峰值扭矩高于300牛·米和最大峰值功率高于150千瓦)和中等性能规格(意味着最大峰值扭矩高于200牛·米和最大峰值功率高于100千瓦),同时考虑400V直流和800V直流电池电压。1.2 外励磁同步电机技术
十多年来,雷诺为其电动车型(Fluence EV、Kangoo EV、Zoe、Megane eTech等)的首选动力一直是外部励磁同步电机。在过去的10到15年里,大多数汽车制造商都专注于开发用于混合动力电动汽车(HEV)或插电式混合动力电动汽车(PHEV)的永磁同步电机(PMSM)。随着雷诺梅甘娜E-Tech车型的推出,雷诺介绍了其最新一代驱动电机,称为六相电机(6AM)。其工作原理基于外励磁同步电机技术,峰值性能超过160kW,扭矩为300Nm,采用圆线绕组定子和油冷却解决方案。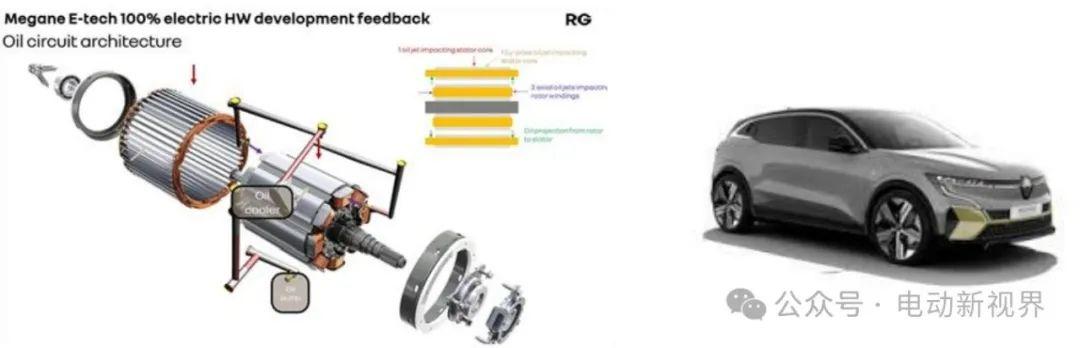
图2 用于梅甘娜E-Tech的六相电机技术
由于转子磁通调节与转子电流和Id电流组件控制磁通的能力有关,外励磁同步电机以高速高效率而闻名,而永磁(PM)技术完全依赖于Id电流的磁通弱化。图3说明了外励磁同步电机在高速公路行驶中的优势,通过比较两种电机(EESM和PMSM)的损耗,它们具有类似的最大性能/设计方法和活动体积。红色 区域对应的外励磁同步电机技术的显示出具有更高的效率。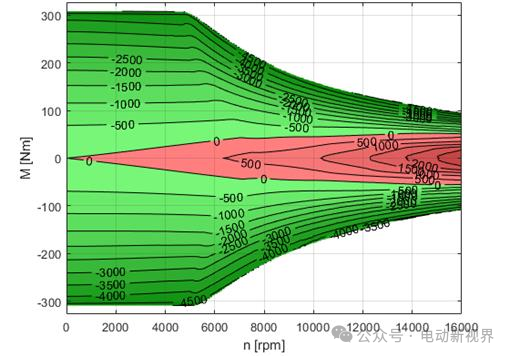
图3 外励磁同步电机和永磁同步电机技术的损失差距说明
由于极槽绕组工艺的限制,外励磁同步电机中的转子磁极对数量是有限的(在外径给定的情况下)。在汽车应用中,这个数字通常在2到4之间。
外励磁同步电机设计的关键点是:
- 定子极对数和每极匝数
- 考虑到定子绕组的工艺限制。
- 最大转子电流(电流密度),与热限制有关
- 最大线圈匝数和层数,与热问题和机械问题有关
图 4:考虑绕组过程约束的转子的绕线示意图
- 转子磁极形状,与扭矩脉动、BEMF波形相关联;
- 定子槽数和每相匝数,与:最大相电流限制、电池电压、请求的最大性能、请求的连续性能、与发卡技术可扩展性相关的约束;
- 整体系统效率:机械损失(包括转子油飞溅效应、温度影响)、转子铜损、定子铜损、铁损、PWM损耗等。
2. 发夹设计
发夹技术使用矩形线材,这些线材最初被制成U形的段落,因此得名。然后为不同的层和连接安排多个Pin版本,将其组装成一个笼子,该笼子包括形成绕组所需的所有引脚。然后将笼子插入定子堆栈中。当笼子插入后,定子就准备好进行扭转过程,在此过程中,开放端将被塑造成准备进行激光焊接的过程。
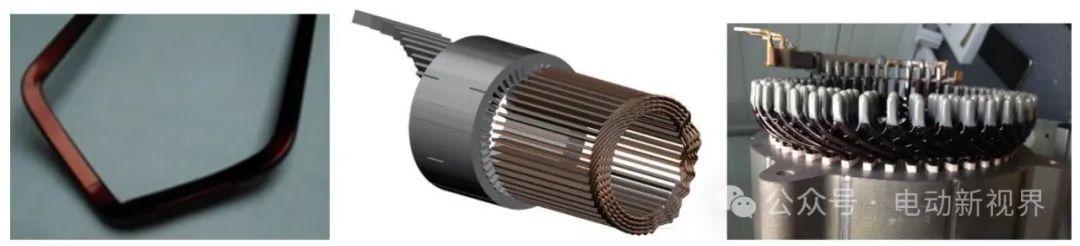
图5:U形销、笼式插入和完成定子焊接侧面的示意图
生产过程可以完全自动化,确保了非常明确的线材定位;有助于提高工艺的可重复性和明确机器特性。
2.1 优点/缺点
优点:
矩形线圈绕线技术与圆形线圈绕线相比,能够实现更高的铜槽满率。槽满率的增加使得可以减小定子相电阻率,减小相电流密度,提高电机功率密度。
由于导体的轴向插入,槽口可以比导线尺寸更小,提高了电磁性能。更高的槽填充因子可以减小槽高,使得转子直径更大,特别有利于外励磁同步电机对转子线圈空间和冷却的需求。对于工艺的可重复性,这种绕线方式允许导体在槽中有良好且熟知的定位。与圆形线圈绕线相比,这减小了交流铜损耗的变化,因为槽中圆形线圈位置的变化会严重影响并联导线之间的电流分布。熟知的线圈位置与矩形线圈上可能采用更厚的绝缘层的组合也是解决800V能力时的关键点之一。定义的线圈位置可以详细了解线圈之间的电压潜力,而矩形线圈的高截面意味着较厚的线圈绝缘对可能的槽满率影响较小。最后,从热学角度看,矩形绕线可以有助于更好地冷却,通过增加端部绕线的可用表面积,改善定子槽内的热导率。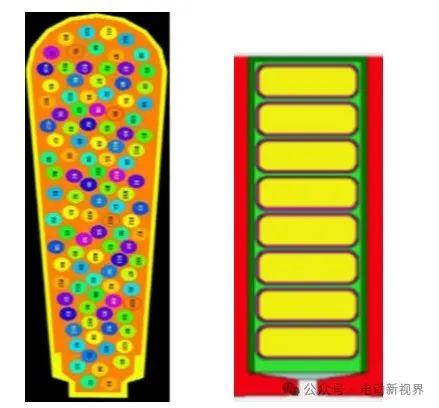
图6:槽填充示意图,圆形线材与线材位置可变性对比发夹形状
图7:圆线绕组与发夹式设计示意图
缺点:
这种发夹式绕组的缺点如下:
在每个相位的匝数方面,可扩展性和优化的可能性较低。表1说明了这个问题:
表1:星形连接中发夹技术电动机绕组(每相匝数)与电机拓扑的示意图
我们将在下一部分详细介绍这种现象。插槽槽满率的增加和端部绕组长度的减少。2.2 交流铜损
正如介绍的,这种现象与电频率有关,它导致导体中电流密度的局部变化,因此也导致了相等相位电阻率的改变和定子铜损的增加。导致这一交流铜损的因素有以下几点:- 导线之间的接近效应
- 趋肤效应
- 与转子旋转和气隙谐波相关的漏磁通和槽的变化
所有这些效应都引入了我们所说的交流铜损 PjAC = PjDC + Pjadd为了近似这些损失,我们可以定义一个系数(Kac 或 Rac),该系数提供了总铜损与直流铜损的比率。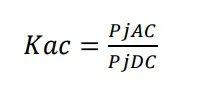
这个比率随着频率和机器操作点的变化而改变。我们在下面的图中展示了高速下导体中的电流密度以及该系数随电机速度(电频率)的变化情况:
图8 卡克铜损系数演变(a)导体中电流密度变化的影响(b)
可以通过优化导体形状和距离以及槽/齿形来最小化这种频率依赖性。图9展示了一个理论研究,采用了一种简化方法来阐述这种改进。
图9:关于导体形状对铜损影响的理论研究
为了校准交流铜模拟结果,设计了一个专门的样机来评估发卡绕组与圆形绕组相比的交流损耗。这台机器从六相电机(梅甘娜E-Tech的电机,带有发夹式绕组的定子)改造而来。目的是在比较圆形绕组解决方案时,尽可能保持最大性能和铁损不变,以便仅保留从圆形线绕组到发卡绕组的变化的影响。
图10:六相发卡绕组设计插图
基于这个设计,已经实现并测试了一个原型机,该原型机在雷诺集团试验台上进行了测试。下面的图示展示了这个原型:
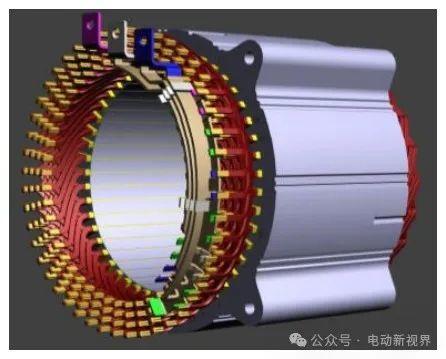
图 11:六相发卡绕组电机原型
测试活动的重点之一是隔离不同工作点上的交流铜损和全局损失。图12展示了交流铜模拟结果的综合分析以及短路测试期间进行的实验测量。这些损失是通过考虑阻性转矩和轴速来获得的。已知机械损耗、直流电阻率、铜温度和在圆线绕组解决方案上定义的杂散损耗(并考虑到这种发夹解决方案的设计方法),可以近似计算Kac系数:
图12 AC铜损(a)实验估算(b)仿真
通过这种设计,我们在样本之间的全局损失偏差上获得了以下结果:
图13:切换到提出的解决方案后,从圆形绕组方案转换为发夹式绕组方案对10个给定工作点的损耗影响
这种方法使我们能够验证交流损耗分量计算并校准热模型。
2.3 与模块化相关的约束,800V/400V可扩展性高性能/中等性能
正如之前介绍的,发夹绕组的一个主要缺点是每相可用的匝数选择有限。为了解决这一问题,需要进行初步研究,以找到最佳设计方案,该方案在性能、效率、成本和绕组修改所需努力之间取得最佳平衡,并满足所有规格要求。目标是在不进行重大修改的情况下(保持相同的转子和定子电磁设计,仅允许对有效长度和平行路径进行修改),针对高性能和中性能规范,以及两个标称直流母线电压值(400V和800V)。
在这项初步研究中,调查了多种电磁设计,包括磁极数量定义、每个槽的导体数量、槽的数量、每相并联组的数量以及最大逆变器电流的变化。在考虑的每个技术定义上,都进行了效率、热性能和最大性能模拟。最受欢迎的是8极和6极版本,它们分别具有6层和8层发卡绕组。然后,在8极和6极之间做出选择是由高性能电机的要求驱动的,该电机需要同时满足800V和400V的需求。这意味着需要一个选项来改变并联组数比为1:2。在800V下,无论是6极还是8极概念都具有2个并联组。对于8极电机来说,改为4个并联组相对容易,而在6极电机中使用4个并联组则不会得到对称解决方案。因此,对电磁设计的进一步优化重点是8极解决方案。图示中仅展示了2个磁极的绕组方案,适用于8个磁极和6层(带有2条并行路径)的机器。
图14:仅2极绕组方案的8极和6层机器(具有2个并行路径)的示意图
2.4 电驱动优化
为了实现准确且有意义的电驱动优化,必须考虑电驱动的所有方面。这包括机械方面、电磁学、热行为以及电子和控制方面的考虑。我们在下面的图中说明了提高机器最大速度时可能对机械修改产生的影响。随着速度的提高,对转子和端盖以及线圈稳定性的要求也随之增加,这反过来又影响了对电磁设计选择等约束条件。
图 15:对高速优化的设计影响
为了改进电驱动设计,可以考虑两种主要方法:1. 直接优化 2. 元模型方法。第一个方法使用求解器与优化算法相结合进行精确优化。这可以用于优化转子的极形以减小扭矩波动或在NVH(噪声、振动和不平顺性)主题中减少气隙中的磁力。第二种方法基于灵敏度分析(基于实验计划)和基于元模型构建的优化。这种方法允许使用基于这些元模型的解析方法进行研究,为首次改进提供大量的技术设计解决方案。此外,如果需要改变优化模型,很容易对其进行更改并重新启动优化,而无需使用有限元求解器。关于扭矩改善和质量减轻的第一个改进可以通过几何变化来实现:
图 16:灵敏度研究定义
图17展示了一种基于这种优化的方法,以获得一个考虑通过元模型进行优化的帕累托前沿:
图 17:元模型示意图
帕累托前沿总结了最佳设计,并提供了在这个前沿上选择设计的机会。当然,所有这些工作流程及其精度取决于对所有计算输出的建模(扭矩、损失、命令优化等)。3 测试活动
在开发过程中,所有组件、组装件和子系统都经过了彻底的测试活动。以下段落重点介绍了其中一些测试,重点关注电机级别及以下的测试。3.1 油品兼容性
所有电机部件和子组件都经过高温油存储。存储温度和附加测试因零件功能和预期操作温度而异。对于大多数靠近活动组件的零件来说,这意味着在高达180°C的温度下进行约1000小时的油存储,并在存储期间及之后定期进行测试间隔。在测试间隔期间,油探头会分析污染物和化学性质,同时对存储的组件进行相关属性测试。对于电线样品,这包括绝缘硬度、灵活性、附着力和断裂伸长率、击穿电压、电阻测试、铜腐蚀测试等测试。在粘接定子叠片的情况下,还包括堆叠粘合性的剪切试验。3.2 定子扭转试验
为了验证定子和外壳之间的配合情况,进行了一系列的扭矩测试。在这些测试中,一个带有内部外壳和定子的组件被安装在一个扭矩试验台上,其中外壳固定在试验台上,通过一个插入堆栈槽口中的轴组件对定子堆施加扭矩。准备了多个具有最小和最大干涉配合的测试组件。为了考虑冷却油对可传递扭矩的影响,这些组件在试验前与冷却油一起储存数周。测试在100°C的环境温度下进行,这是收缩配合的最坏情况。作为测试负载,通过安装在轴上的测试臂施加正弦扭矩模式,峰值的幅度为+/-150%。这个负载总共施加了100万次循环。在成功完成扭转测试和检查后,然后通过逐步增加静态扭矩(以峰值扭矩的10%为步长)来测试收缩配合,直到失效。
图18 扭转试验用转轴和扭转试验组件
3.3 热老化
加速测试模拟了由于车辆使用寿命期间发生的温度变化而导致的定子热机械暴露情况。该测试旨在验证组件的质量和可靠性,特别是针对因热机械暴露而产生的故障,如焊接接头、粘接接头和钎焊接头的老化及裂纹,以及键合连接、密封件或外壳中的问题[MBN LV 1242]。
图19 热老化循环及气候室设置
定子在恒温-30°C的气候室中进行热老化测试,同时定子绕组在激活周期(a)期间通过逆变器供电电流加热。为了模拟实际运行条件下的介电负荷,定子供应电压和逆变器开关特性被设定为接近电机终端在整个服务寿命期间的电压过冲。3.4 电机性能测试
电机性能测试包括几个子测试,这些子测试可以全面表征电机。它们在几个电机测试台上进行,这些测试台配备了负载机,可处理高达355千瓦/640牛米和20000转的功率,电池模拟器能够达到1000伏直流电压,多个冷却回路,气候室以及一整套测量设备。被测设备(DUT)配备了几个热元件,用于全面的热特性分析,包括通过遥测系统连接的转子中的元件。在整个测试过程中,连续测量所有热、机械和电气值以及逆变器值。
图20 电机试验台(巴特诺伊施塔特)&测试设置概述
子测试包括:
- 无主动定子供电的测试:
- 作为转子和电流和速度函数的反电动势测量。
- 作为流体流动和温度函数的拖曳损失测量。
电机/变频器集成:
3.5 进一步测试活动 - 系统、环境、转子
几个进一步的测试正在进行中或计划在项目的后期阶段进行。在部件水平上,雷诺进行了转子超速试验。系统集成和性能测试正在雷诺和法雷奥的测试基地进行。一些进一步的验证测试可以在法雷奥巴德纽施塔特工厂进行。包括背靠背测试台上的系统寿命测试、冲击和振动测试、热冲击测试、IP防护、盐雾、淹没和岩石飞溅测试。4 结论
下一代外励磁同步电驱动系统由雷诺和法雷奥共同开发,与第6代产品相比带来了多项改进。从圆形线材到定子上的发卡绕组,结合改进的冷却概念,使得扭矩和功率密度增加了大约30%。在转子设计上进行了几个小的发展步骤,允许更高的最大操作速度。齿轮箱概念经过重新设计,重点是减少齿轮箱损失,使用800V SiC碳化硅模块显著提高了整个系统的效率。发卡绕组的短端绕组悬垂部分也允许更紧凑地集成电机和齿轮箱。整体结果是一个非常紧凑的系统,功率和驱动循环效率显著提高。对首批样品的测试活动正在进行中,初步结果与模拟结果一致。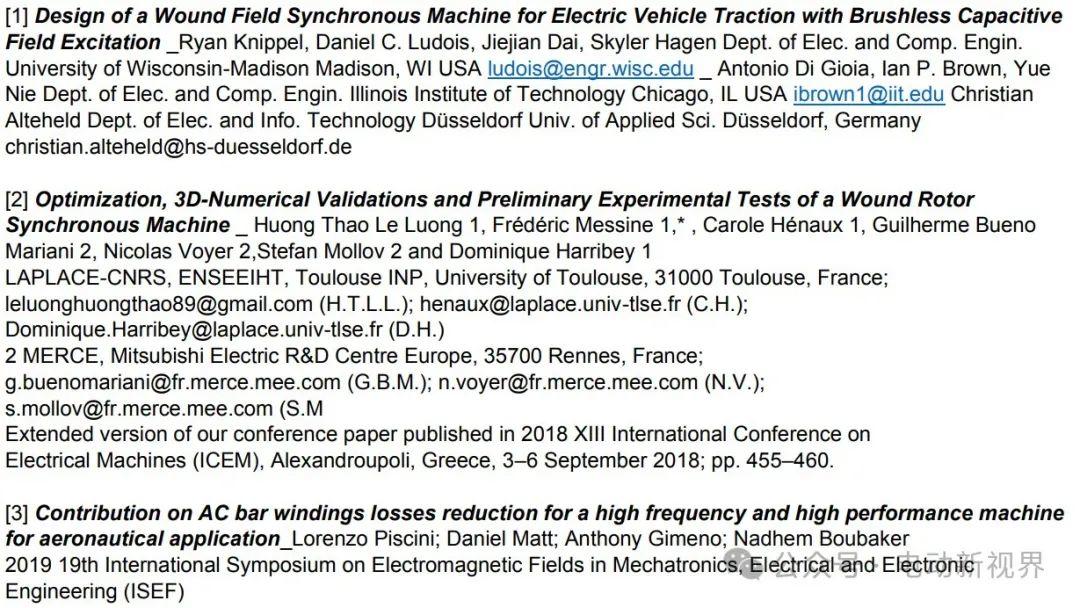