锂电池模组膨胀位移分析方法!
文章摘要
本文提出了一种锂电池模组膨胀位移分析方法,以解决电池充放电过程中产生的膨胀问题。通过前期规划、仿真计算和膨胀实验,文章详细阐述了如何评估和优化电池模组的膨胀位移。前期规划阶段,通过DCC尺寸链分析软件和CAE仿真分析软件评估模组膨胀,确保预留适当的膨胀空间。仿真计算阶段,使用CATIA建立三维模型,并通过ABQUAS软件进行仿真分析,评估模组在生命周期末期的膨胀力和位移。实验测试阶段,搭建了综合测试平台,通过加速老化循环测试验证模组的实际膨胀情况。最终结论表明,模组设计满足系统级别的膨胀要求,且实际性能优于理论预测,为锂电池模组的膨胀位移设计提供了系统的方法和参考。
正文
动力电池在充放电过程中会产生膨胀。电池单体的膨胀会带动整个电池模组发生形变,影响模组外观,如果膨胀较大,壳体材料无法抵抗膨胀力,甚至可能造成安全问题。
目前很多研究者主要分析了膨胀力和预紧力对于电池寿命的影响,但是针对模组级别的膨胀位移的分析,并没有提出系统的方法。膨胀位移分析的缺失,如果预留膨胀空间过小,可能导致电池模组外轮廓超标,不满足客户要求;如果预留膨胀空间过大,可能导致电池模组的体积密度设计保守,没有竞争优势。 针对上述不足,本文提出了一种锂电池模组膨胀位移分析方法,结合DCC尺寸链分析软件和CAE仿真分析软件综合评估模组膨胀,最后通过实验验证模组的实际膨胀。 1 前期规划
膨胀分析的前期规划是按照模组功能设计要求,布局核心部件的尺寸。如表1所示,通过电性能和模组的空间布局,可以初步确定电芯的基本尺寸。通过化学体系结合之前的开发经验,可以初步确定电池从生命初期(BOL)空电-生命末期(EOL)满电的变形量。通过挤压、冲击、振动等机械性能测试要求,可以初步确定模组的壳体厚度。通过安全防护的功能要求,可以初步确定隔热材料的厚度。
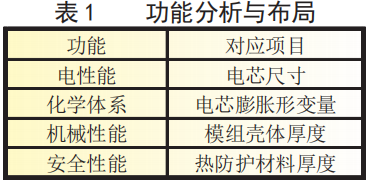
经过初步的规划和布局,可以基本确定模组在宽度方向的主要部件,如图1所示。

通过图1可以看出,模组主要包含电芯、气凝胶、云母、壳体绝缘膜、壳体等部件。剩余间隙主要用来填充缓冲垫,通过压缩缓冲垫来调节电芯入壳时候的预紧力。然而,各个部件都有一定的尺寸公差,考虑尺寸公差的影响,对应求出来的剩余间隙也会有一定的差异。因此需要进行尺寸链分析,确定剩余间隙的范围。如图1所示,将核心部件拆解为不同的尺寸环,导入到 DCC 尺寸链分析软件中进行求解计算。软件自动生成方程组如下:

因为组成环个数大于3,采用概率法进行计算,软件计算出A0,如图2所示。
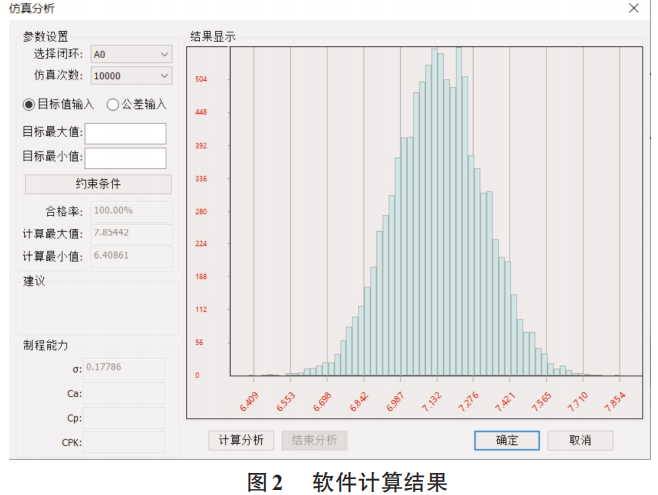
根据3s分布的准则,A0的尺寸为(7.14±0.54)mm,对应预留给缓冲垫的空间范围为[6.6 7.68]。确定缓冲垫压缩范围后,下一步是选择合适的缓冲垫厚度和缓冲垫类型,以确保缓冲垫吸收装配公差,压缩后反作用力的范围正好能落在电芯最佳循环预紧力的范围之内。另外缓冲垫的类型还需要确保后期电芯膨胀过程中能平稳且最大限度地吸收膨胀。基于此要求,选取了某款聚氨酯泡棉,其在压缩前期可以快速达到电芯预紧力的要求,压缩中期压力也是平缓地提升,压缩后期拐点来得较慢,且80%压缩量下压力未超过400kPa,确保泡棉可以最大限度吸收电芯的膨胀。泡棉曲线如图3所示。
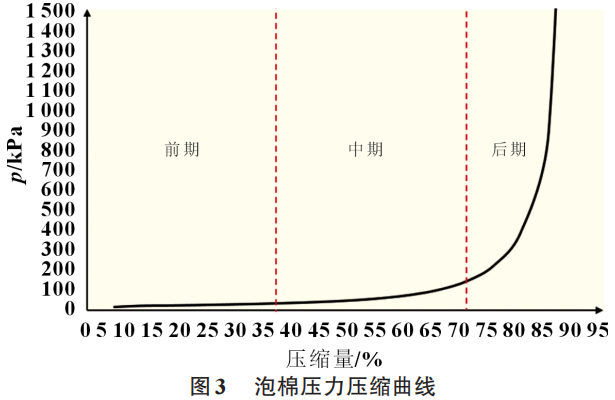
选取缓冲泡棉初始厚度为8mm,结合预留给缓冲垫的压缩空间,可以计算出初始入壳时候,缓冲泡棉压缩的范围为4%~17.5%,结合图3的曲线,计算出的预紧力范围为16~24kPa,满足电芯输入的15~30kPa预紧力要求。 前期规划初步布局了整体结构,确保电芯入壳后满足最佳预紧力的要求,保证了模组的循环特性满足要求。 2 仿真计算
基于前期的布局和规划,采用了CATIA建立了模组的三维模型。其中泡棉按照原始厚度进行建模,电芯的厚度根据泡棉的厚度进行等分调整。确保仿真过程中,电芯膨胀到对应尺寸,泡棉的反馈力符合实际情况。仿真模型如图4所示。
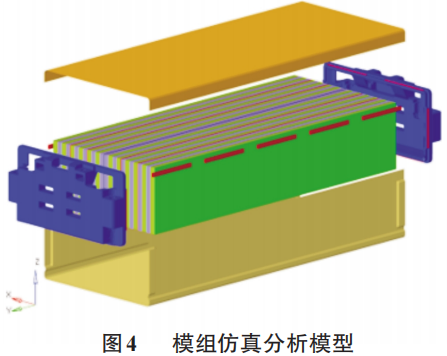
按照图4的模型,通过Hypermesh划分网格,以电芯的厚度变化作为变量,采用ABQUAS进行仿真,计算出来EOL下壳体膨胀位移和强度是否满足要求。分析结果如图5、图6所示。 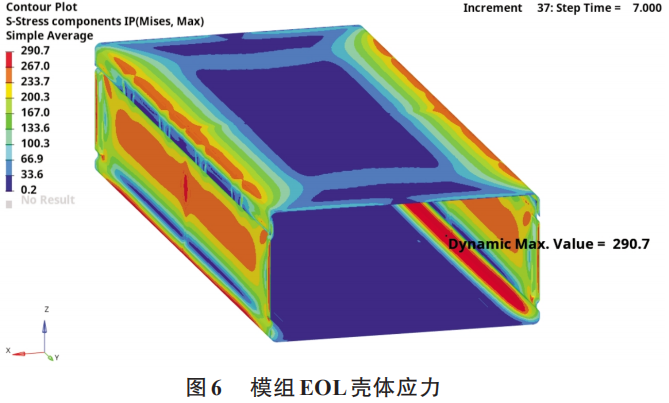
由图5可以看出,模组EOL状态下单边膨胀3.46mm,累计6.92mm,基本满足系统预留给模组10mm的膨胀空间。由图6可以看出,EOL状态下壳体应力主要集中在折弯区域,最大应力达到290MPa,未超过壳体抗拉强度。 另外,通过软件,导出了不同状态厚度的电芯变形量和壳体形变的关系数据,如图7所示。 通过图7可以对标出电芯厚度变化和壳体厚度增量的关系,结合不同荷电状态(SOC)和健康状态(SOH)下的电芯变形可以推断出模组变形,为相似的布局提供参考和借鉴。
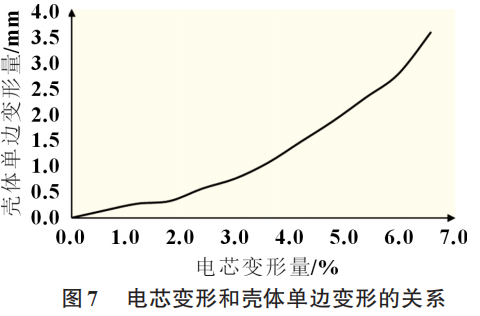
通过仿真计算,完成了EOL下模组的膨胀力和膨胀位移的评估,结果表明模组的设计和布局满足系统级别膨胀的要求,同时壳体变形与电芯变形的关系也为相似项目提供了参考。 3 膨胀实验
为了测试模组的膨胀位移,搭建了综合测试平台。平台主要包含恒温测试箱、充放电测试仪、位移检测工装、实验模组等部件。实验模组选取和仿真分析一致的模组,将模组放置在特制的膨胀位移检测工装之中,模组的定位和系统之中的定位方式一致。
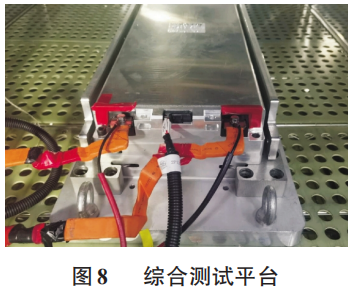
然后把工装放置在恒温测试箱中,设定温度45℃,接通充放电测试仪,采用1C/1C的充放电方式,进行模组加速老化循环测试,记录每100周模组的膨胀量,直至记录到模组循环到800周以后,系统层级认为模组达到了EOL状态。平台的整体布局如图8所示,测试结果如图9所示。
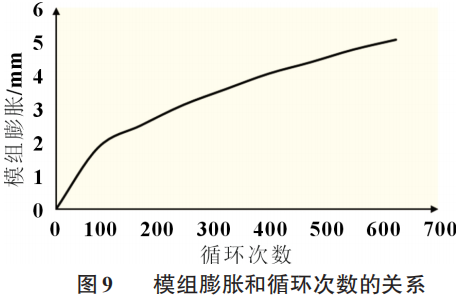
由图9可以看出,前200周,电池模组膨胀较快,后面膨胀放缓。初步分析是由于膨胀后期壳体反作用力较大,限制了电芯的膨胀趋势。到达800周后,模组总体膨胀达到了5.028mm,实际膨胀小于仿真的6.92mm。差异的来源是800周后模组电芯的实际SOH并未达到EOL状态下的SOH,因此还有继续充放电的能力,因此未达到最大膨胀。但是,按照系统要求已经满足EOL的测试要求。 膨胀实验验证了模组整体膨胀的趋势,对比仿真,实测的膨胀位移小于仿真估算的膨胀位移,满足系统测试的要求;另外也从侧面证明模组及电芯的性能优于理论性能。后续将进一步安排实验资源,将模组循环到实际EOL的状态,观察并记录最终的模组外壳的膨胀变形量。 4 结论
本文提出了一种系统的膨胀分析的方法,通过前期规划、仿真分析和实验测试得出如下结论: (1)基于系统层级的设计要求,规划了模组宽度方向主要零件的尺寸,并基于 DCC 尺寸链分析软件,以概率法的分析思路评估剩余缓冲垫的安装空间。提出缓冲垫的选型方法,确保模组电芯安装预紧力。为初期模组膨胀设计和规划提供参考。 (2)完成了模组的膨胀分析,提出了优化模型,消除泡棉预紧力对仿真结果的影响。仿真结果表明EOL下最大应力为290MPa,满足壳体应力要求。最大膨胀位移6.92mm,未超过系统预留的膨胀边界。通过仿真数据绘制出的电芯形变和模组膨胀的关系曲线为相似结构的布局提供参考。 (3)搭建了膨胀位移测试平台,按照系统要求,达到800周循环,结果表明模组生命末期的膨胀位移为5.028mm,小于仿真分析的6.92mm,并分析了差异的原因是由于模组的实际性能优于理论性能。最终的膨胀位移满足系统边界的要求。