文章摘要
TREMEC正在开发一款名为第一代的高性能电动汽车驱动单元(EDU),以满足车辆电动化的需求。这款600千瓦的EDU具有两个电机的空间,优秀的效率和热稳定性。设计特点包括行星和拉轴齿轮组、IPM和SPM电机、SiC逆变器和集成断开离合器等。通过全面的系统模拟和优化,TREMEC确保了EDU在WLTP和性能驾驶循环中的高效表现。原型测试正在进行中,以验证模拟结果。TREMEC的第一代EDU旨在提供高功率密度和驾驶乐趣,为电动汽车市场带来新的可能性。
正文
导读:
TREMEC正在开发一款名为第一代的第一代高性能电动汽车驱动单元,以满足车辆向电动化转变的需求。这款600千瓦的EDU具有两个电机的空间,优秀的效率,热稳定性等关键属性。
设计特点:这款EDU的关键特点是其空间内有两个电机,以及在WLTP和性能驾驶循环中的优秀效率,热稳定性。此外,它还采用了行星和拉轴齿轮组,IPM和SPM电机,SiC逆变器和集成断开离合器等技术成分。
系统模拟和优化:TREMEC在设计和开发过程中进行了全面的系统模拟,效率模型显示IPM和SPM技术都可以提供优秀的效率,达到90%的WLTP效率和95%的峰值系统效率。对于全轮驱动车辆,集成断开选项可以通过断开后驱单元来实现高达2千瓦/100公里的WLTP驾驶范围提升。
原型测试:2022年第四季度正在进行原型测试,以确认所有模拟结果。
总结内容:TREMEC的第一代是一款旨在提供高功率密度和驾驶乐趣的高性能电动汽车驱动单元。通过其独特的设计和优化,以及全面的系统模拟,这款EDU有望为电动汽车市场带来新的可能性。
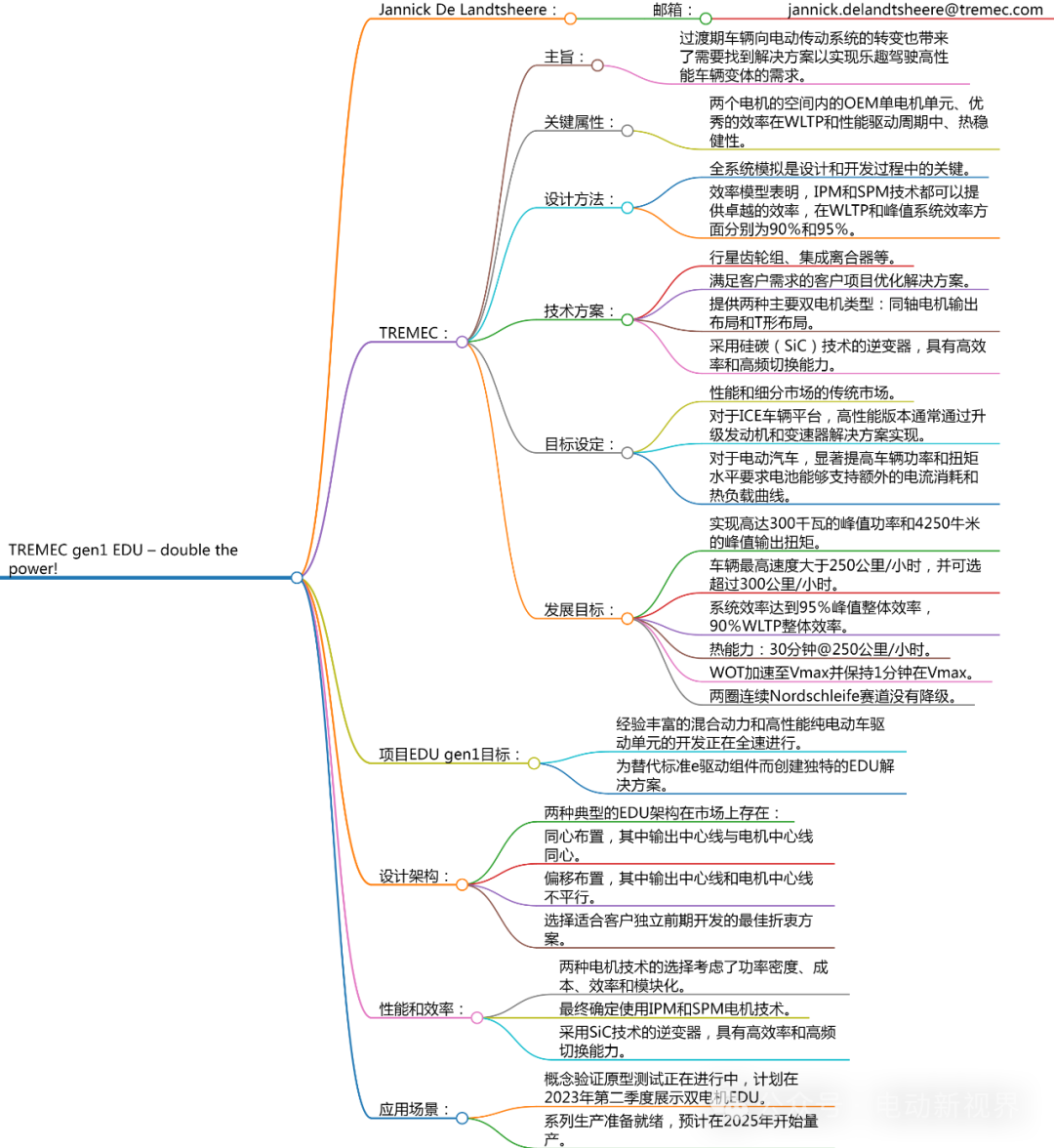
摘要:
随着车辆向电动驱动系统的转变,也需要为高性能车型找到解决方案。这些车型需要专门的性能导向型电驱动单元(EDU)。TREMEC正在开发第一代这样的EDU。这款600千瓦的EDU的关键特性包括:在原始设备制造商单电机单元的空间内安装两个电机、在WLTP和性能驾驶循环中具有出色的效率、热稳定性强。已经进行了广泛的分析以找到适合设计要求的技术成分。而不是声称一个通用的解决方案,提出了一个针对客户项目的优化方案,该方案使用一组关键成分:行星齿轮组、轴传动齿轮组、永磁体(IPM)和开关磁阻(SPM)电机、碳化硅(SiC)逆变器和集成的断开离合器。在整个设计和开发过程中,全系统仿真在TREMEC起着关键作用。效率模型显示,无论是永磁体还是开关磁阻技术都可以提供卓越的效率,在WLTP中的效率约为90%,峰值系统效率高达95%。对于四轮驱动车型,集成断开选项可以在WLTP驾驶范围内实现高达2kWh/100公里的增益,通过断开后置驱动单元来实现。热模拟显示,EDU及其先进的冷却概念能够持续进行高绩效驾驶。从目标设定到建模再到验证测试,NVH优化也在整个系统中处理。原型测试正在进行中,以确认所有模拟结果,预计在2022年第四季度完成。TREMEC简介
TREMEC是一家全球性的传动和驱动解决方案公司,总部位于墨西哥奎雷塔罗,并在美国密歇根州怀索姆和比利时泽德尔盖姆设有生产基地(欧盟)。历史上一直是北美市场高性能乘用车和商用车手动变速箱的领先制造商,近年来,TREMEC已确立了自己在高性能双离合器变速箱(DCT)领域的龙头地位,应用范围包括C8克尔维特、福特Mustang GT500和玛莎拉蒂MC20。TREMEC开发方法的关键特点是从组件设计、制造到完整的变速箱系统组装以及电子控制单元(包括软件和校准)开发的垂直整合。面对不断变化的市场的推动力,TREMEC已经进入了高级开发计划,以建立在其DCT经验的基础上并迈向电动化驱动解决方案。从混合动力项目[1, 2]中吸取教训,纯电动驱动单元的开发正在全速进行。第一代EDU项目的目标
性能和细分市场车辆一直是TREMEC的传统市场。对于内燃机(ICE)车辆平台,主流车辆的性能版本通常是通过升级发动机和变速箱解决方案实现的,例如更大的发动机排量、增压、更高的扭矩传输甚至不同的变速箱架构。以福特野马GT500为例,它采用的是一台增压V8发动机和双离合变速器(DCT),而不是标准野马上的涡轮增压I4或自然吸气V8以及行星自动变速器。为了提高车辆性能,不需要改变能源来源,即油箱。对于纯电动汽车来说,创建高性能衍生品并不那么直接了当。首先需要一个能够支持额外电流和热负载配置文件的电池。可以预见的是,标准平台电池将需要进行重大改变。电动驱动单元(EDU)也是如此。虽然更高的电流逆变器可能会从电动机中解锁一些额外的性能,但要想在功率和扭矩上有大幅提升,只能通过……一个定制的教育解决方案,专门设计和系统优化为高性能单元。
体验到许多OEM厂商需要找到这样的定制高性能解决方案来替代特定平台中的标准edrive组件,TREMEC正在为此目的开发第一代EDU产品,首先推出的是带有扭矩矢量控制的后置EDU。下表概述了针对第一代TREMEC EDU(gen1 EDU)的性能目标和其他特性。
表1:TREMEC第一代EDU开发目标
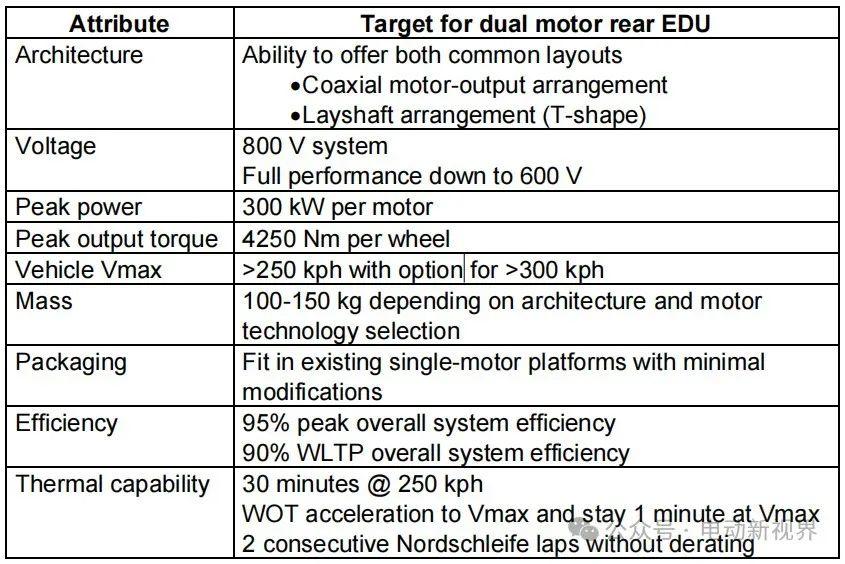
第一代EDU设计架构
市场上存在两种典型的教育机构架构:
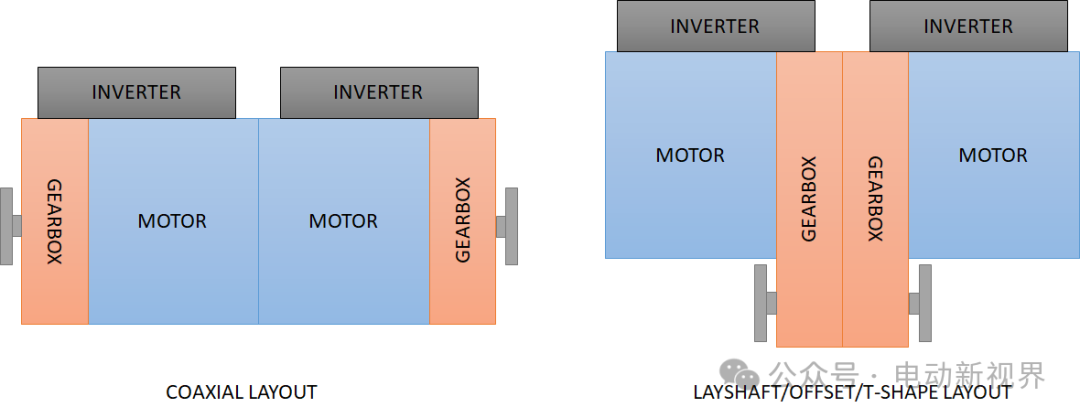
图1:两种主要的双电机EDU类型
可以进行彻底的优化研究,以确定在成本、重量、效率等方面的最佳折衷方案,但现实情况是,这一切都归结于车辆的包装。如果汽车制造商已经针对一种架构设计了底盘,那么在不影响底盘设计的情况下几乎不可能安装另一种架构。因此,与其在两种架构之间做出明确的选择,TREMEC更倾向于提供两种解决方案。同轴布置在其自由度上变化较小(没有选择输出电机中心距离的自由度,也没有选择安装角度/方向的自由度),因此最适合客户独立的前期开发,并且由于这个原因,它被选为内部开发和演示原型构建的方案。
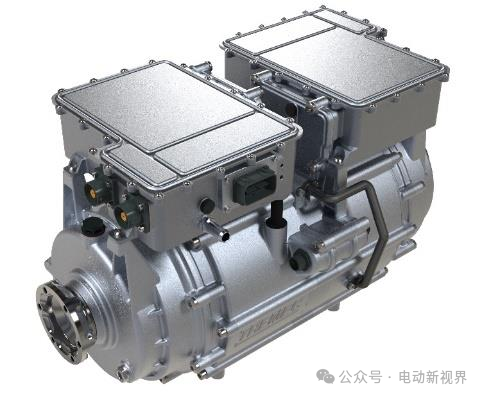
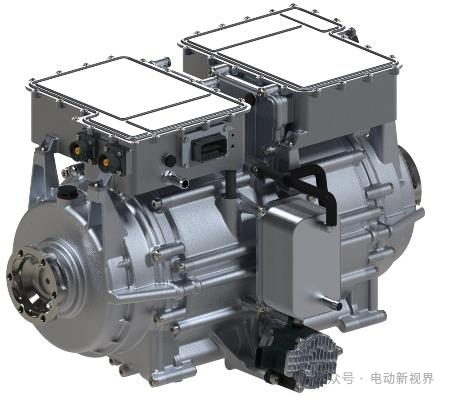
图2:TREMEC双轴后置EDU集成研究
图2展示了一个集成概念研究,用于满足表1中所示目标的完整双电机后端驱动单元(EDU)。该单元通过母线连接逆变器电机,以最小化电磁兼容性风险。两个电机之间的中央壳体部分作为液压歧管,用于引导油和水通道。泵为电机(对于油冷IPM变体)和/或齿轮箱提供油。带级差行星齿轮箱(比率选项在8到10:1之间)得益于强制润滑,以减少其旋转损失并最大化其耐用性和热稳定性。冷却水由车辆供应给两个逆变器,并通过电机的水套串联流动,然后通过热交换器汇合。每个电机通过一个低压布线束(未显示)连接到其逆变器。一个逆变器控制油泵(智能执行器)。紧凑性、功率密度和扭矩密度如图3所示,该图比较了双电机单元与具有不到一半性能(210千瓦,4000牛米总输出扭矩)的原始设备制造商(OEM)单电机单元。整体输出距离可以保持不变,而双电机单元所需的唯一可感知包装体积增长是额外的逆变器。由于所选逆变器的功率密度,额外体积被最小化。如果需要,逆变器的包装和直流/交流接口可以根据特定的底盘环境进一步优化。冷却器和泵在单元上的位置以及连接到中央外壳的连接都是灵活的。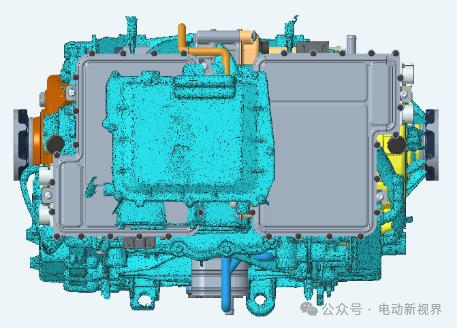
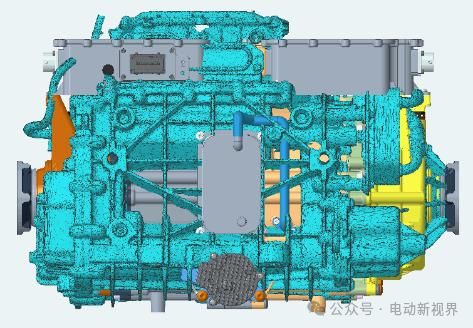
图3:TREMEC双同轴EDU(彩色)包装对比OEM单电机210千瓦EDU(浅蓝色),顶视图(上)和侧视图(下)。
同样令人印象深刻的是,双电机单元的重量与原始设备制造商(OEM)的参考单元相同,均为110公斤(含液体)。
电机技术
• 功率密度与成本:对于双电机EDU来说,电机的功率和扭矩密度对于车辆布局至关重要。与此同时,应避免使用异国情调的电机技术或材料,以确保在任何年产几百辆超跑市场之外的批量生产中保持成本竞争力。
• 效率:不仅要确保最大化的车辆续航里程,还要确保电机产生的热量足够低,以便在不降低功率或扭矩的情况下实现持续的高性能驾驶。
• 模块化:希望能够通过有限的更改来改变电机的功率和扭矩输出,以使EDU的不同变体能够根据客户的目标规格进行优化。
研究发现,没有一种单一的电机技术能够为每个潜在应用的不同要求找到最佳平衡。内部永磁(IPM)发夹电机在功率和扭矩密度、效率与成本之间取得了极好的平衡。然而,大型端绕组所占的空间对紧凑型车辆封装环境所能提供的性能提出了限制,并且该机器相对较重。对于对体积能量密度和重量能量密度有严格要求的应用,一个成本和制造优化的表面磁铁电机(SPM)具有集中的绕组,它提供了最佳的可能功率密度,同时仍然实现了良好的效率结果。这两种电机技术都被选用于开发TREMEC EDU 第一代产品家族。表2:首选电机技术的比较
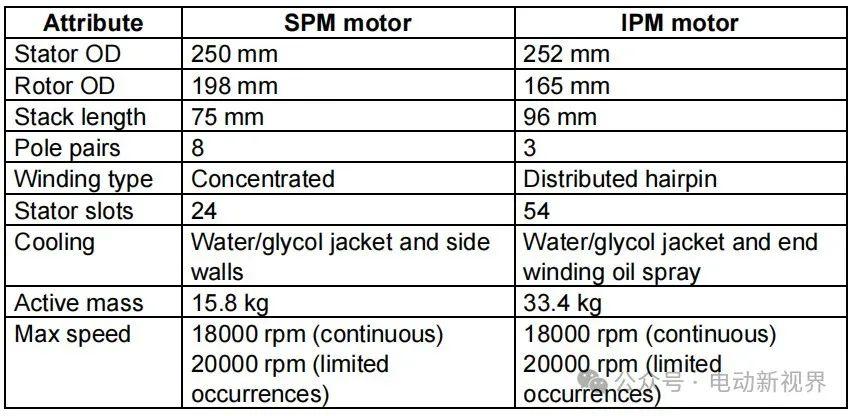
逆变器技术
变频器的关键规格在表3中列出。
表3:逆变器规格
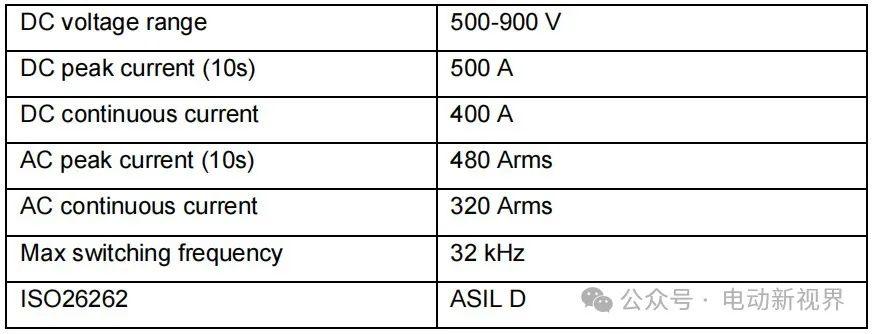

系统性能
两种电机概念都经过优化,以在结合逆变器的情况下最大化功率密度。图4显示了在600V电池电压下的峰值性能曲线,这是从800V电池在全功率输出下预期的输出电压。两个电机的扭矩都超过了450Nm。永磁同步电机的峰值功率达到了300千瓦,由于电机的功率因数,在高转速时略有下降。由于其较高的功率因数,SPM在宽速度范围内允许更高的峰值功率能力,但由于所需的频率较高,限制了最大逆变器相电流,因此在高速时最终会失去一些峰值功率能力。
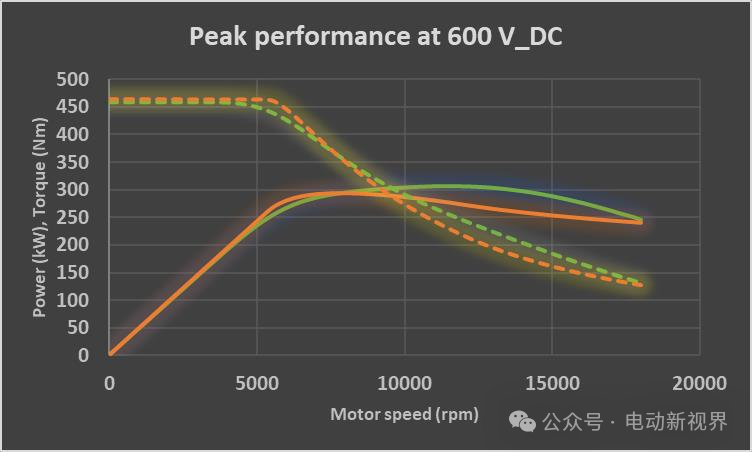
图4:使用IPM和SPM电机的峰值系统性能 SPM
系统效率优化
在分析与优化整个系统效率上投入了大量的努力。图5展示了带有永磁同步电机(SPM)和行星齿轮箱的EDU的总损失和完整系统效率。图6展示了带有内嵌式永磁电机(IPM)和传动轴齿轮箱的EDU的总损失和完整系统效率。从效率图中我们可以看到:与IPM(永磁同步电机)相比,基于SPM(表面贴装永久磁铁)的EDU(电动驱动单元)具有更大的效率最佳区域。
与IPM基EDU相比,基于SPM的EDU在速度函数上会产生更多的损失。这是由于电机的更高极数导致的定子铁损和逆变器开关损耗。
与基于SPM的EDU相比,基于IPM的EDU在扭矩函数上会产生更多的损失。这是由于更高的铜损,包括直流和交流铜损。
换句话说,没有明确的答案哪种技术提供了最佳效率。根据车辆传动布局和驾驶条件,任何一种解决方案都可能被认为是最好的。图7显示了基于SPM和IPM的EDU解决方案的总损失差异,并指出了在WLTP驱动循环(较暗点表示更频繁发生的条件)下的扭矩/速度图上的运行点。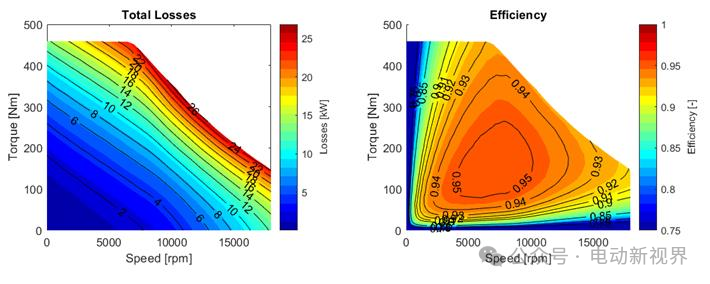
图5:带有IPM和斜齿圆柱齿轮箱的完整EDU的效率和损失图
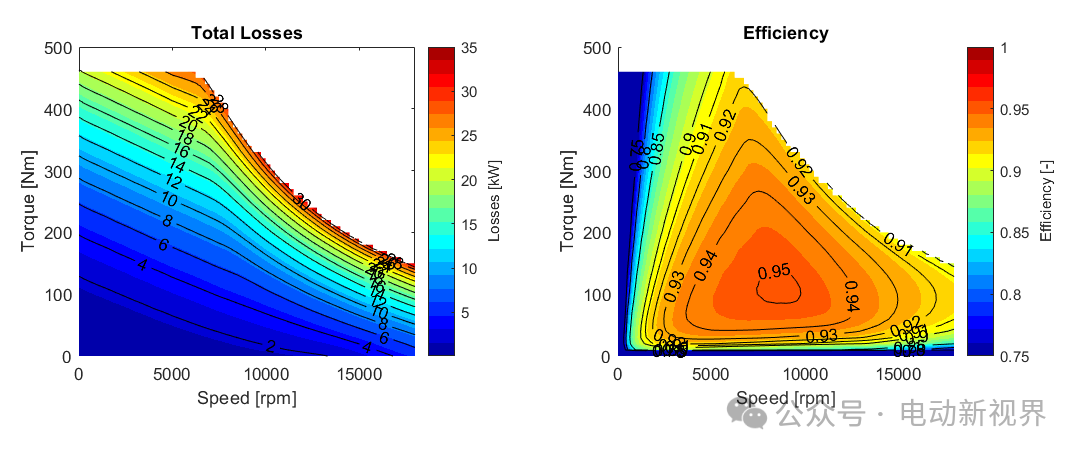
图6:带有SPM和行星齿轮箱的完整同轴EDU的效率和损失图
对于后轮驱动的SUV车型,带有双后置电机EDU(电驱单元)的车辆。请注意零线表示两种EDU系统的损失相等。在WLTP循环中,基于IPM(内插磁阻电机)的EDU具有优势。对于赛道驾驶循环和其他需要系统最大性能的高性能驾驶条件,基于SPM(永磁同步电机)的EDU具有优势。表4显示了由此产生的EDU效率。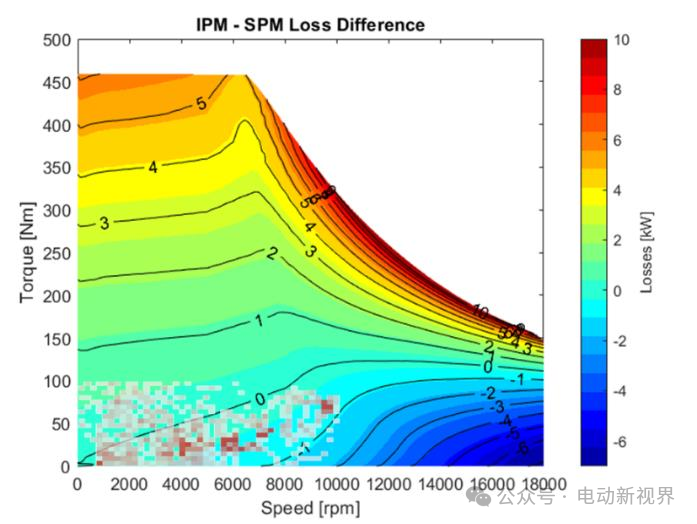
图7:完整EDU损失比较IPM减去SPM,带有指示WLTP操作点的双电机后轮驱动SUV这些驾驶循环。图8显示了两种EDU类型在两个驾驶循环中的损失来源。需要进行开发工作,以使SPM基础的EDU解决方案达到90% WLTP循环效率的目标。
表4:模拟的平均EDU系统效率

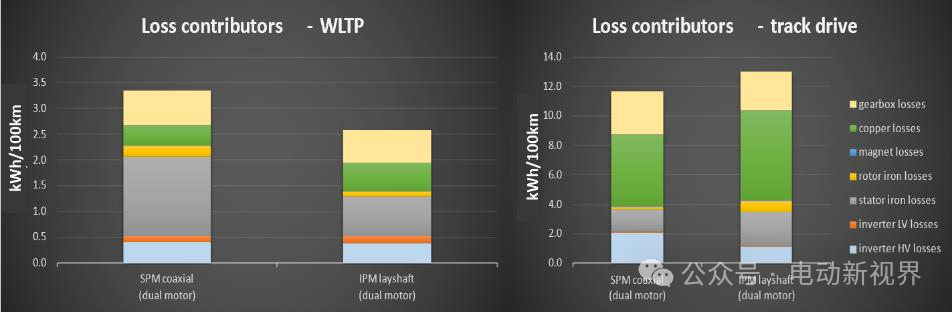
图8:双电机后EDU的损失贡献者,适用于高性能SUV的WLTP和赛道驾驶循环。
场景2:全轮驱动车辆
前部为单电机电子驱动单元(EDU),后部为双电机EDU。预计高性能电动汽车的大多数将会是全轮驱动(AWD)以最大化加速能力。其中一个选项是在前后轴都应用相同的电驱单元(EDU)技术,前轴一个电机,后轴两个电机。这增加了前后扭矩分配的变量,当然还有车辆动力学要求,都在追求最佳驾驶效率的过程中。对于一款900千瓦三电机高性能SUV,已经取得了以下成果。对于基于SPM的EDU来说,WLTP中的关键损失贡献者是定子铁损。在后方EDU中集成一个电机断开系统,并以前轮驱动模式运行WLTP,可以使后EDU的损失接近于零,而前部电机则在高效率区域运行。参考图7,与图中所示的双电机EDU相比,单前电机的负载对于相同的驾驶循环来说是双倍的,这使得WLTP的关键操作点位于SPM和IPM的等效损失线上或其上方。对于基于IPM的EDU来说,空载损耗更低,后轴断开系统对后轴的影响也小得多,因此考虑到断开系统的额外成本和复杂性,这是一个明显较差的解决方案。请注意,图9中基于SPM的三电机解决方案在后轴上具有断开功能,其总体损失与IPM相同。
图9:WLTP损失贡献者,适用于高性能SUV的三电机驱动系统。
基于三电机系统,得益于永磁同步电机(SPM)与内嵌式永磁电机(IPM)相比铜损较低。图10展示了断开系统的集成到行星齿轮箱中。对于具有严格包装要求的双电机系统来说,一个简单的螺栓外接离合器是不可接受的。通过更深层次地整合电磁驱动的断开离合器组件,每个断开所需的额外长度可以限制在25毫米。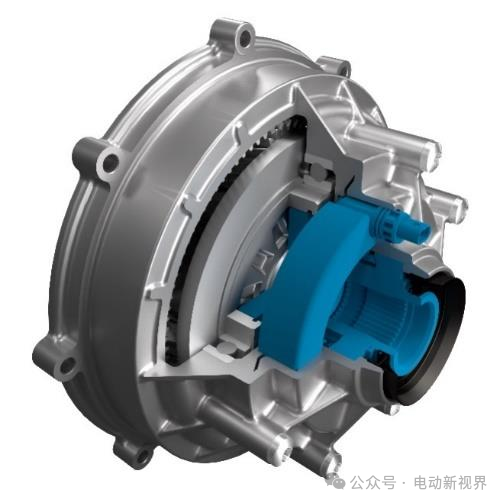
持续热能力
许多电动汽车具有出色的加速能力,然而很多在全力加速至最高速度时却表现不佳,或者在连续加速或在赛车场的几圈比赛中难以保持稳定性能。电池和EDU的冷却对于确保性能的一致性至关重要。对于真正的性能车辆,已经确定了几个目标:需要(接近)连续热负荷进入系统以进行散热的工况:赛道的连续圈数以及持续高速的自动公路驾驶。这些条件驱动冷却系统的设计。表5显示了在50°C冷却剂入口温度下,电动机在250公里每小时的速度下运行30分钟时的温度。永磁体和开关磁阻电机都表现良好。在100千瓦的电机以每分钟16500转运行的情况下,磁铁和绕组的限制范围内。在这种情况下,逆变器也保持在它的连续工作电流能力之下。更具有挑战性的是确保系统能够持续在赛道上使用,因为在这种情况下平均功率传输率甚至更高。例如,图11显示了IPM电机的两圈连续纽博格林北环赛道的模拟电机温度。定子绕组温度保持在可接受范围内,而磁铁温度虽然在两圈后仍然上升,但仍然足够低于任何危险区域。表5:模拟的电机温度在250公里/小时
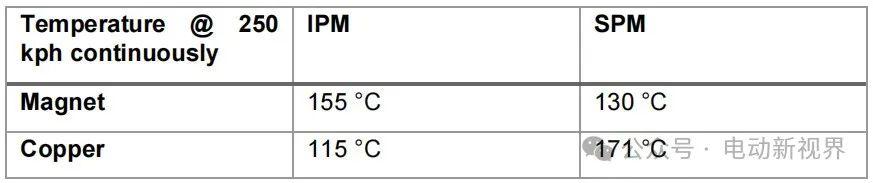
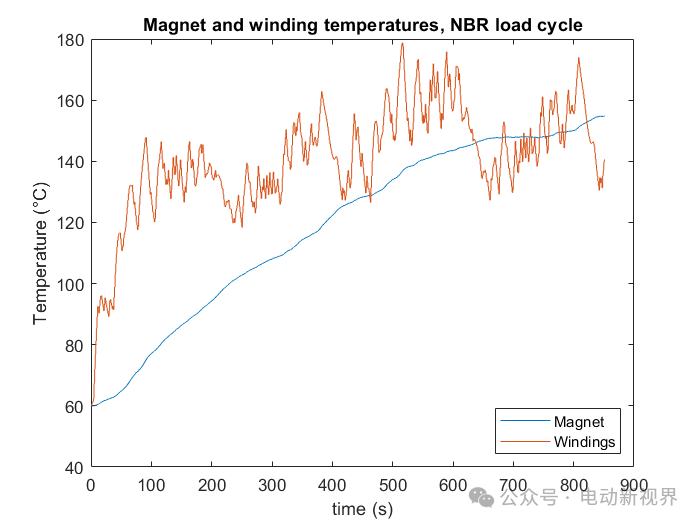
图 11:使用IPM电机模拟的绕北环跑两圈时的电机温度
由峰值热负荷组成的事件,因此大量依赖于系统的热惯性来控制峰值温度:全油门加速和重复的四分之一英里跑。对于这些事件,允许局部定子绕组温度超过耐久性限制,因为此类事件的整个生命周期持续时间非常短。图12显示了在全油门加速后紧接着以最大速度行驶60秒的IPM电机的温度行为。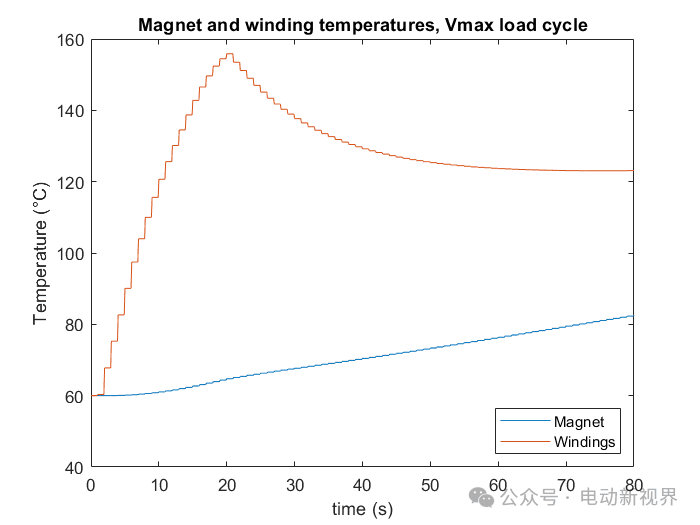
图12:永磁同步电机(IPM)在全油门加速后60秒@最大速度下的模拟温度。
NVH优化
在纯电动汽车(BEV)中,噪声、振动和声振粗糙度(NVH)变得重要起来。缺少了内燃机(ICE)导致车内噪音减少,但也失去了掩盖噪音的作用。因此,道路和风噪非常明显。然而,尽管与内燃机相比,电动驱动单元(EDU)的噪音天生较安静,但仍然相当可观。电动机和变速箱产生的非常谐波噪音被主观地感知为不愉快。在内燃机车辆中,发动机噪音被视为一种特性,许多电动汽车被设计得尽可能安静。然而,TREMEC EDU是专为驾驶乐趣特性而设计的,这意味着质量和动力需要在声音质量上得到体现。因此,创建了特定的目标定义。NVH优化的最终目标是实现最佳的感知车辆噪音。这个目标完全是主观的,并且取决于来源(EDU)、路径(车辆)和接收者(乘客)。TREMEC正在开发基于对车内噪声的主观评估的具体目标。通过车辆的结构传递和空气传播途径,这些目标被转化为EDU对于声学噪音和振动的需求。由于这些目标需要在EDU设计的早期阶段满足,因此需要采用一种结合了CAE仿真模型方法和实验验证的过程。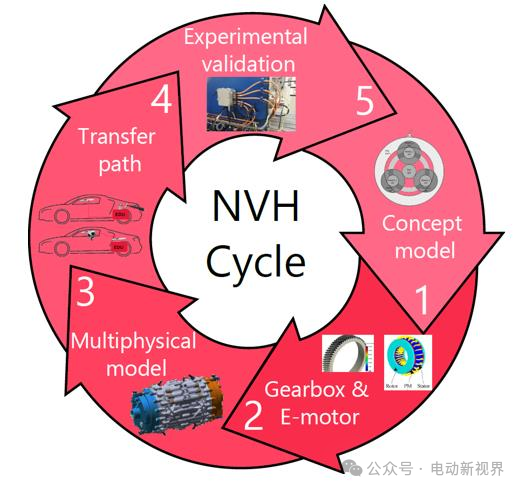
图13:NVH开发周期
该过程在图13中进行了描述。基于概念建模,创建了一个用于耐久性、效率和其他各种计算的CAE模型。这个模型并没有特别针对NVH进行优化。可以识别出两个主要的噪声源:齿轮中的传动误差和电机中的电磁力。首先,使用最佳实践对齿轮的宏观和微观几何形状进行优化。结合最优电机设计,这些特性可以被集成到一个多物理场仿真模型中,该模型可用于预测EDU级别的噪音和振动。通过迭代运行模拟来优化。如果电机和齿轮都是最优的,并且如果目标没有达到,可以处理EDU的其他部分,如住房、轴等。如果这仍然不够,可以通过吸收材料来优化空中噪音的传输路径,并为结构噪音提供最佳安装。在开发的每个阶段,都使用实验验证来支持模拟,从原型到最终结果。结论和展望
TREMEC正在开发第一代高性能电动驱动单元,专注于功率密度、效率和热稳定性。两种电机技术(永磁同步电机和内嵌式永磁同步电机)以及两种齿轮箱架构(轴传动和行星传动)与先进的800V碳化硅逆变器相结合,以实现提供定制解决方案。功率和扭矩密度显示是标准电动汽车驱动系统的一倍以上。效率被视为一个整体系统方面,可以通过紧凑集成后置电机断开系统来提高。最强关注点是双电机后置EDU(电驱动单元),但使用相同的核心成分也可以实现其他架构,例如前单电机EDU或从TR9080 DCT取出的eLSD的单电机后置EDU。原型测试在2022年第四季度进行中,双电机EDU的车辆演示计划于2023年第二季度进行。设计和发展面向系列生产的路线图正在为2025年的SOP(标准作业程序)做准备。作者:Jannick De Landtsheere 贾尼克·德兰特谢尔
参考文献:
[1] TREMEC Hybrid Dual Clutch Transmission (HDCT), de Ruijsscher, Dritev Bonn 2021
TREMEC混合双离合变速器(HDCT),由Ruijsscher、Dritev公司提供,2021年于德国波恩发布。
[2] TREMEC HYbrid DRive Axle – HYDRA, De Landtsheere, Dritev Bonn 2021
TREMEC混合动力驱动轴 - HYDRA,德兰特谢尔,波恩第三能源公司 2021