铝及其合金具有密度低、比强度高、导电性和导热性好、热膨胀系数低、耐腐蚀性高等特点。其中,2024铝合金是可热处理强化的Al-Cu-Mg合金中应用最广泛的变形铝合金之一,它主要用于高载荷的零部件,如飞机骨架部件和蒙皮。激光熔化沉积(laser melting deposition, LMD)技术是一种涉及热输入、能量传递、粉末输送、粉末冷却和凝固的直接沉积制造工艺。成熟的选择性激光熔化(SLM)和传统制造技术相比,LMD具有生产周期短、材料利用效率高、污染少等优点。然而,采用LMD技术制备Al-Cu-Mg合金存在柱状晶粒粗大、气孔和微裂纹等问题,导致整体沉积性能较差,严重影响工件的抗拉强度和抗疲劳性能。
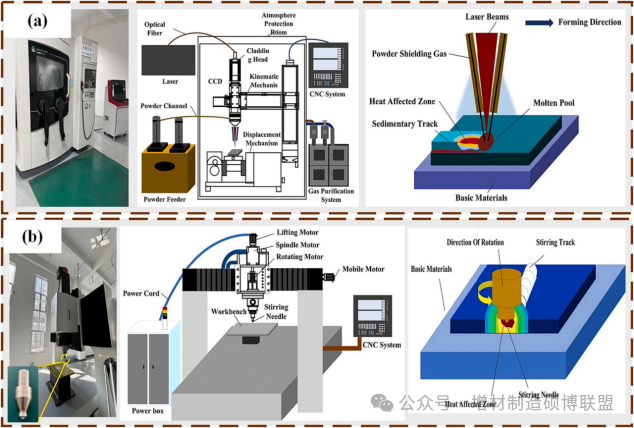
图1 (a) LMD实验装置及其原理图 (b) FSP实验装置及其原理图 为了减少上述缺陷的发生,南京工业大学联合中国运载火箭技术研究院,提出了一种基于搅拌摩擦焊(FSW)的搅拌摩擦加工(FSP)技术。在搅拌针引起的强烈的晶粒机械破碎和肩摩擦引起的显著热效应的双重作用下,热塑性材料发生剧烈的塑性变形,产生动态再结晶,使晶粒明显细化。因此,采用多次循环和搭接FSPs来研究其对LMD 2024铝合金组织的影响,并探讨层间FSPs变形后的组织演变和强化增韧机制。相关研究成果发表在Journal of Manufacturing Processes 杂志上
论文研究了搅拌摩擦加工(friction stirring processing ,FSP)和激光熔化沉积(laser melting deposition ,LMD)相结合的混合增材制造(HAM)技术。为铝合金增材制造部件提供了一种极具吸引力和成本效益的方法。然而,不同搅拌策略对微观结构和机械性能的影响机制仍不清楚。研究了多次重复 FSP 过程对 LMD 制备的Al-Cu-Mg合金微观结构和机械性能的影响,通过重复 FSP 消除了不可避免的缺陷,如气孔和裂纹,从而细化了微观结构并提高了性能。特别是经过两次循环全域搭接摩擦搅拌加工(2C-FSP)后,晶粒细化达到了最佳状态,晶粒大小为 2.57 μm,平均显微硬度也达到了最佳水平(153.3 HV)。同时,与沉积层相比,极限拉伸强度 (UTS) 提高了 49.3%,屈服强度(YS)提高了 44.8%,伸长率(EL)提高了 8.39%。同时,还揭示了混合增材制造产生的微结构演变和拉伸性能增强的主导机制。
试验结果表明,LMD制造的2024铝合金构件的沉积区存在许多可见的缺陷,如孔隙和微裂纹,它们分散在整个基体中。层间引入单道次FSP后,气孔和裂纹等缺陷的显著减少。此外,FSP区域呈现不规则的物质流动形状,这是由于FSP过程中热塑性变形导致金属在前进侧(AS)和后退侧(RS)的不对称相对运动造成的。将FSP区分为沉积区(DZ)、焊核区(NZ)、轴肩影响区(SAZ)、热-机械影响区(TMAZ)和热影响区(HAZ)。如图2所示,DZ表现为粗大柱状晶形态,最大晶粒尺寸约为20.6 μm,而NZ在搅拌针的剧烈搅拌下,由于晶粒的机械破碎,动态再结晶为细等轴晶粒,最小晶粒尺寸为0.5 μm。此外,由于强塑性变形,TMAZ区域的微观组织呈现出沿变形方向变化的拉长晶粒形态。此外,热影响区表现出与DZ相似的晶粒形态,因为它只受相对较小的热影响而没有明显的塑性变形。图2 2024 铝合金单道次 FSP 的宏观/微观图:(a)单道次FSP 全景;(b)TMAZ;(c)NZ;(d)DZ;(e) b区层间变形的IPF图;(f) b区的晶粒尺寸NZ 发生了严重的塑性变形。为了进一步研究 FSP循环次数对 LMD 样品的影响,在上述搅拌参数的基础上进行了以下实验:全域搭接FSP(搭接率为 80%)、一次循环全域搭接摩擦搅拌加工(1C-FSP)、两次循环全域搭接摩擦搅拌加工(2C-FSP)和 三次循环全域搭接摩擦搅拌加工(3C-FSP)。所得结果如图3所示。图3(a-d)中红线范围内的样品由图3(e)可以看出,在重叠式快熔表面处理过程中,晶粒流动的范围很大,重叠式FSP表面处理材料的流动比单道次FSP表面处理材料的流动更剧烈。重叠率为 80% 的全面积 FSP 所产生的塑性变形从微观结构上看更为广泛,因此粗晶粒会破碎并再结晶成细小晶粒,且分布均匀。同时,由于晶粒流动,气孔和裂纹等缺陷也被填充和消除。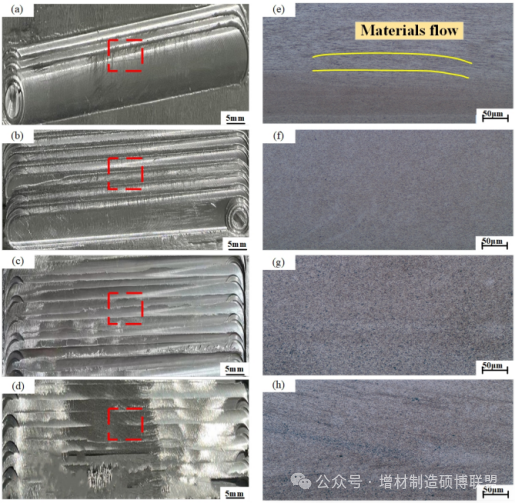
图3 多次循环FSP:(a-d)表示多道次FSP、1C-FSP、2C-FSP 和 3C-FSP 的宏观图像;(e-h)表示多道次 FSP、1C-FSP、2C-FSP 和 3C-FSP 的微观结构对图3(b-d)中观察到的 OM 样品区域进行了 EBSD 分析,其反极图(IPF)和晶粒尺寸图如图4所示。如图4(d-f)所示,样品的 1C-FSP 晶粒大小经线性截取法测定为 3.39 μm,2C-FSP 和 3C-FSP 的晶粒大小分别为 2.57 μm 和 3.21 μm。因此,2C-FSP 后的晶粒大小达到最细化(晶粒的变形达到最大,如图 6所示),而在 1C-FSP 和 3C-FSP 过程中形成的晶粒大小则显得略粗,这是因为在 2C-FSP 过程中,晶粒在 1C-FSP 的基础上再次机械破碎,并发生动态再结晶,从而使晶粒再次细化。3C-FSP 后的晶粒粗化是由于搅拌过程中的许多热效应导致晶粒发生动态回复并逐渐变粗。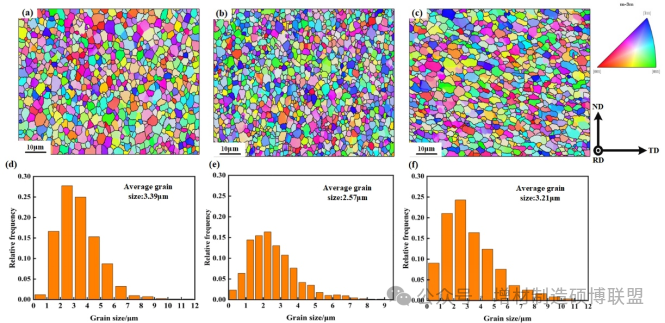
图4 多次循环 FSP 的 IPF 图和晶粒尺寸图:(a-c)1C-FSP、2C-FSP、3C-FSP 的 IPF 图;(d-f)1C-FSP、2C-FSP、3C-FSP 的晶粒尺寸晶粒的再结晶和特殊晶粒纹理的形成是由于 FSP 过程中强烈的塑性变形和显著的热效应造成的 。晶粒的演变主要是由外应力的塑性变形机理和回复再结晶现象引起的。根据 FSP 循环次数引起的剪切应力和温度的不同,微观结构中的晶粒组成与其他区域相比也有所不同。极点图显示了 FSP 的循环次数,如图5所示。如图 5(a)所示,同一区域不同方向的纹理强度变化显著,其中(100)>(111)>(110)。然而,不同区域的最大纹理强度也不同,1C-FSP 的最大纹理强度为 1.8,2C-FSP 为 1.5,3C-FSP 为 2.0,这是由于在 FSP 过程中反复搅拌导致晶粒明显再结晶。同时,在 FSP 区域,编织结构取向均匀,几乎没有各向异性,这也增强了细粒组织的增韧机制。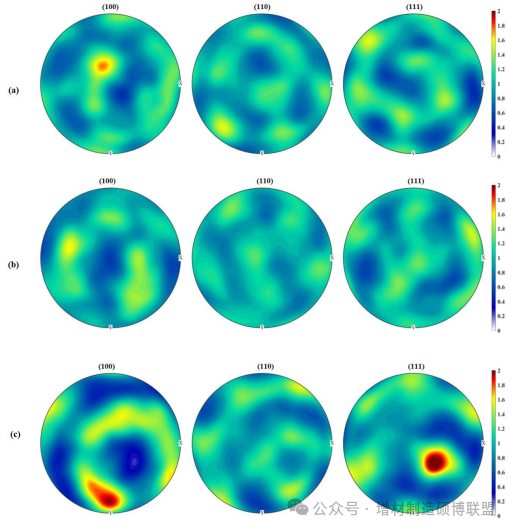
图5 不同循环次数FSP 的极图:(a)1C-FSP;(b)2C-FSP;(c)3C-FSP图6显示了 FSP 不同循环次数下再结晶晶粒、亚晶粒和变形晶粒的分布。在 1C-FSP 过程中,位错发生了重新排列和变形,并相互缠绕形成了更稳定的亚晶粒。由于它们都是多道次全域 FSP,其区域均如图6(b-d)中的 NZ 所示。在 1C-FSP、2C-FSP 和 3C-FSP 过程中,再结晶晶粒逐渐增大,而亚晶粒先减小后增大。与亚晶粒相反,变形晶粒先增大后减小,并在 2C-FSP 中达到最高值。这表明在多个 FSP 周期中,晶粒发生了不同程度的塑性变形和连续动态再结晶。随着连续动态再结晶的进一步发展,亚晶粒在 2C-FSP 和 3C-FSP 的搅拌剪切力和热循环作用下,通过位错的重新排列,逐渐成为再结晶晶粒和变形晶粒。因此,再结晶晶粒远高于变形晶粒和亚晶粒,这与一般的 FSP(>70%)结果一致。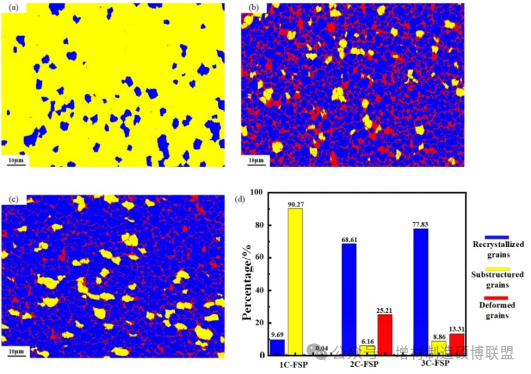
图6 晶粒结构的特征:(a)1C-FSP;(b)1C-FSP;(c)1C-FSP;(d)晶粒演化统计图为了研究由多个 FSP 构成的微观结构对机械性能的影响,对每个样品的 FSP 区域进行了显微硬度测试。结果见图7中的显微硬度分布。图7(a) 显示,沉积层的平均显微硬度为 82.1 HV。如图7(b-d)所示,在 1C-FSP 之后,显微硬度大大增加,平均显微硬度为 141.2 HV。如图7(c)所示,经过 2C-FSP 后,其平均硬度可达 153.3 HV,比沉积层高出 45.3%,最大硬度可达 165.8 HV。此外,3C-FSP 的平均硬度达到 146.1 HV,其显微硬度与 2C-FSP 相比略低。这是由于在 FSP 过程中,晶粒受热影响而变粗,进而导致硬度下降。总之,晶粒发生了动态再结晶,其硬度与 FSP 后的沉积层相比有了很大提高。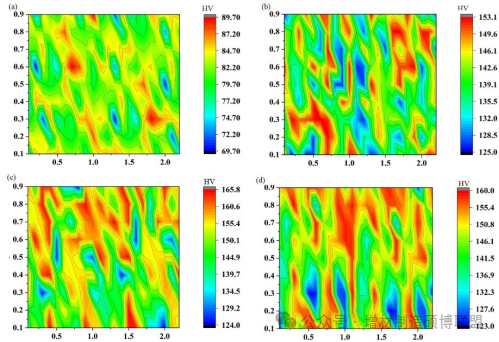
图7 显微硬度分布:(a)沉积层;(b) 1C-FSP;(C) 2C-FSP;(d) 3C-FSP为了确定多个 FSP 对拉伸性能的影响,还进行了进一步的研究。图8所示的实验结果表明,用 LMD 制备的沉积层样品的屈服强度 (YS) 为 167.1 MPa,极限拉伸强度 (UTS) 为 204.1MPa,伸长率 (EL) 为 2.88%。FSP 区域表现出各向同性,1C-FSP 的 YS 为 264.3 MPa,UTS 为 301.4 MPa,EL 为 4.43%。2C-FSP 的 YS 为 289.4 MPa,UTS 为 342.7 MPa,EL 为 7.75%,令人印象深刻。值得注意的是,3C-FSP 的 YS 为 302.8 MPa,UTS 为 402.6 MPa,EL 为 11.27%。随着 FSP 循环次数的增加,拉伸强度和塑性也相应增加,从而形成了坚固的增韧结构。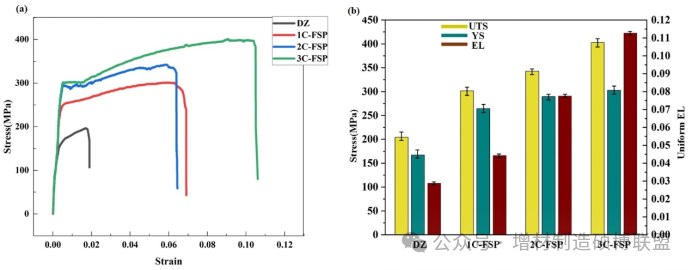
图8 (a) 拉伸试样的应力-应变曲线;(b) 不同拉伸试样的 UTS、YS 和均匀 EL 的比较在 DIC 技术的帮助下,通过对拉伸试验过程中力和位移的精确测量,捕捉到了平面内的表面变化。图 9(a)中的结果表明,在拉伸过程的各个阶段,材料的应变分布并不均匀。然而,如图9(b-c)所示,在对材料进行多次循环摩擦搅拌处理后,应变分布逐渐变得更加均匀。值得注意的是,经过 3C-FSP 处理后,材料的整体应变分布几乎完全相同。最终,材料在中心部分断裂。这归因于 FSP 期间的材料流动,孔隙缺陷和裂纹位置通过多次搅拌循环被填充和消除,随着搅拌循环次数的增加,缺陷几乎消失,晶粒逐渐变得完全等轴和均匀。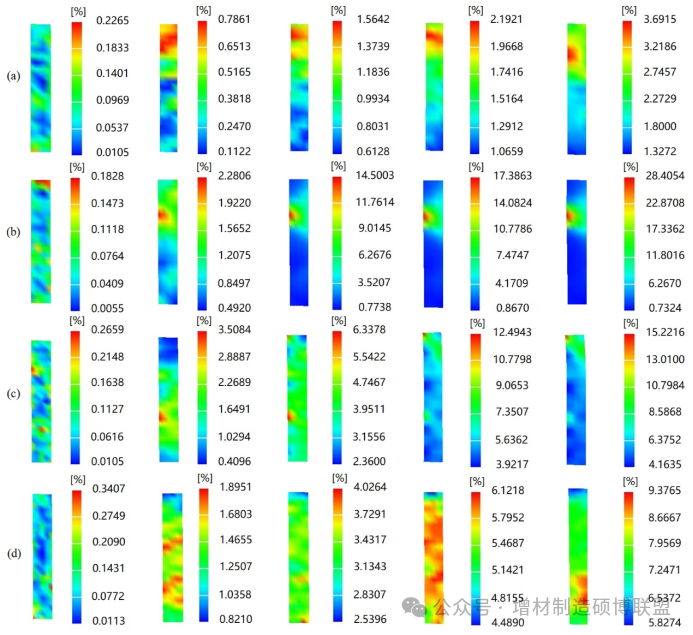
图9 通过 DIC 方法确定的应变图 (a) DZ;(b) 1C-FSP;(c) 2C-FSP;(d) 3C-FSP
图10显示了晶粒演变的示意图,以及整个混合工艺增材制造过程中最终微观结构的放大方位视图。最初,在 LMD 之后,晶粒主要呈现柱状形态,并存在裂纹和极点缺陷。然而,在 FSP 工艺之后,该区域因多道次 FSP 而发生了显著的塑性变形,导致晶粒细化并消除了缺陷和裂纹。
具体来说,在 3C-FSP 之后,由于变形层内的热效应和摩擦搅拌,晶粒进一步细化。这导致了等轴和细化晶粒的生长,同时也填充和消除了剩余的缺陷和裂纹。因此,获得了无缺陷的理想微观结构,同时也提高了机械性能。
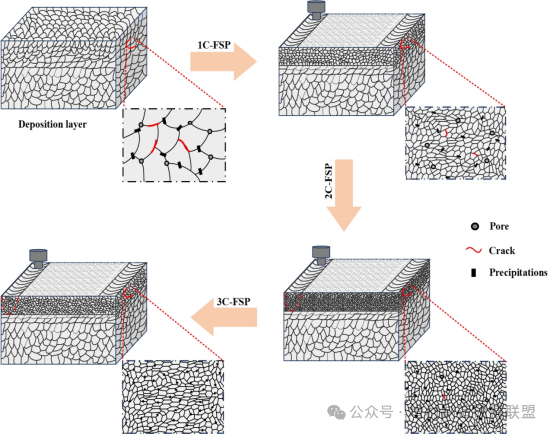
图10 多次循环摩擦搅拌加工过程中微观结构演变机制本文基于摩擦搅拌加工(FSP)和激光熔化沉积(LMD)相结合的复合增材制造技术,研究了摩擦搅拌对Al-Cu-Mg合金微观组织演变和力学性能的影响。利用FSP消除了增材制造过程中的缺陷。此外,构建了各种FSP方法来探索多循环搅拌对沉积层的影响。主要研究结论如下:
(1)摩擦搅拌加工可消除激光熔化沉积引起的气孔、微裂纹等缺陷。反复循环搅拌可以使材料在搅拌过程中流动均匀,从而消除缺陷,使微观结构更加均匀。
(2)在经过2次FSP后,经过反复摩擦搅拌,得到了最细的晶粒(2.57 μm)。同时,该工艺获得的最大硬度为165.8 HV。
(3)摩擦搅拌有利于晶粒细化,3次摩擦搅拌后晶粒尺寸为1 ~ 5 μm。同时,经过3次FSP处理后,与沉积层相比,综合力学性能显著提高,极限抗拉强度(UTS)由204.1 MPa提高到402.6 MPa,屈服强度(YS)由167.1 MPa提高到302.8 MPa,伸长率(EL)由2.88%提高到11.27%。
(4)阐述了FSP对细晶体系构建的影响,通过反复摩擦搅拌为材料提供充分的塑性变形,从而提高构件的强度和韧性。