4680电池为特斯拉推出的直径为46mm,高度为80mm的新一代圆柱电池,相比于其他圆柱电池,4680电池采用无极耳设计,又称全极耳,电池直接从正极/负极上的集流体引出电流,从而大大增加了电流通路,并缩短了极耳间距,进而大幅提升了电池功率。其实方形卷绕电池也有全极耳设计结构。
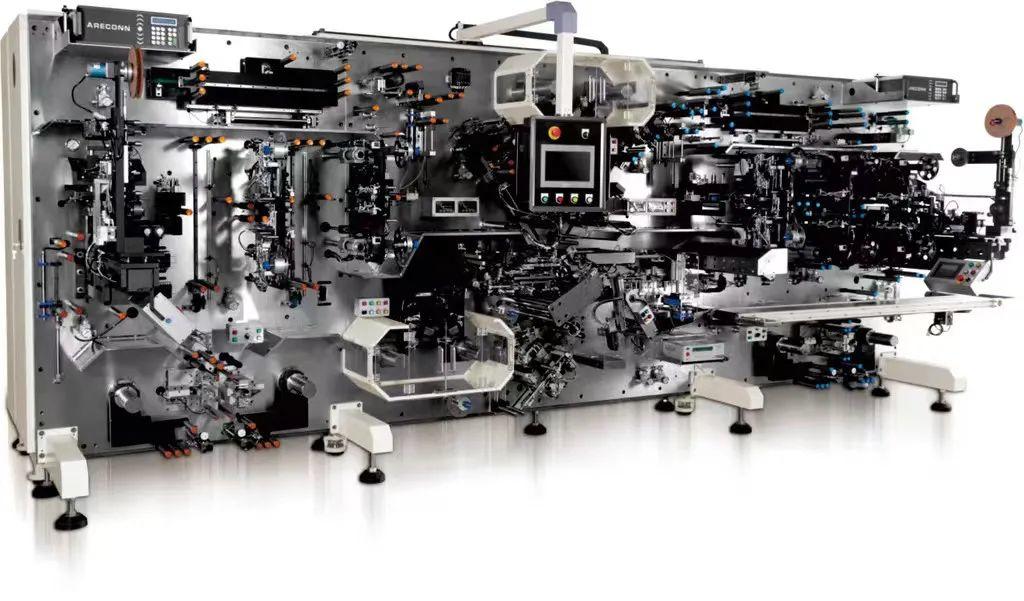
全极耳电池设计
如图1所示,方形卷绕动力锂电池结构设计方面常用的提高电池倍率的方法是改变集流体中电流流动路径,增加极耳载流面积,主要有两种方案:一种是全极耳设计方案,另一种是多极耳设计方案。全极耳方案不需要对未涂布集流体模切处理,通过超声焊接把正或负极留白处与极耳焊接,组装焊接工艺更简单。本文简单介绍全极耳方形卷绕电池组装过程。 全极耳电池卷绕时,极片和隔膜的布置方式如图2所示,正极极片在涂敷正极材料(30)时一侧边缘不涂布的侧面(15)和负极极片涂覆负极材料(40)时留白的一侧面(14)都作为极耳分别焊接在正、负极导流体上,正负极极片之间通过隔膜(170)隔离开,卷芯两侧分别漏出正、负极集流体,直接通过集流体与电池正负极连接。从极耳角度提高了电池功率特性,这样电流流经的距离短,在大倍率下电流密度分布均匀,可以实现高功率密度,极片发热量也小。 卷绕过程对隔膜施加一定的张力,以确保正极片、隔膜、负极片之间的整齐程度,然而工艺过程中的张力会使隔膜在走带方向被拉长,隔膜在走带方向的收缩量很大,会使得隔膜严重挤压极片,从而导致绕卷后电芯发生变形,变形后的电芯不仅外观平整度差,内部还会存在隔膜褶皱等缺陷,如图3所示,这会导致容量低、循环性能差及自放电快等质量问题,尤其是卷绕较厚的电芯,卷绕后的变形问题尤为突出。另外,松散状态的电芯厚度一致性也差,会影响电芯入壳工艺,增加入壳工艺的难度,甚至导致入壳时电芯损伤。因此,卷绕张力控制非常重要。 在卷绕工艺实验中,卷芯需要大量的检测,确保产品质量,主要包括: (1)电芯外形尺寸,包括高度,宽度,厚度,胶带宽度和位置,留白集流体整齐度等。这些尺寸可以直接测量,和卷绕工艺以及设备精度相关。 (2)极片和隔膜长度,为了正极扩散过来的锂离子在负极有对应接纳嵌入晶格,负极必须全部包裹正极,并有一定尺寸余量。同时为了避免短路,隔膜必须包裹负极。因此,如图2所示,卷绕电芯在长度方向必须保证负极与正极相比具有余量,隔膜也要包裹负极。极片相对位置非常关键,具体参数包括隔膜长度,以及与负极的相对尺寸,正负极之间的相对位置等。这些尺寸受到极片涂布规格、卷绕工艺等影响。 (3)极片宽度,在宽度方向负极也需要超出正极一定余量,隔膜超出负极一定余量。宽度方向的对齐度直接由卷绕工艺精度决定,精度高时,余量尺寸可以更小,电池能量密度更高。但是,电池安全性系数降低,必须确保工艺精度,否则对电池存在巨大安全隐患。卷芯每层极片的对齐度一般采用X-射线全部检测卷芯四个边角,如图4所示,当正负极之间的宽度相对尺寸不满足要求时设备自动报警剔除不良品。 (4)卷芯质量,极片在加工过程中,对于单面涂层、漏箔等缺陷极片会做出标记,在卷绕时单极片卷曲扔出。但是,仍旧常常出现缺陷极片出现在卷芯中,对卷芯作质量检测,剔除质量不合格品,能够进一步确保品质。质量检测异常主要的原因还是极片加工过程产生的不良品,比如涂布面密度不满足要求,单面涂层,极片存在胶带等缺陷。 (5)极片切断毛刺,极片切刀长期使用会出现磨损,影响切断效果,因此切刀需要进行寿命管理,定期检测切断质量,避免毛刺。一般切断毛刺观察过程为:取切断极片,在光学显微镜下观察切断面,检测是否存在毛刺。关于毛刺的管控标准,一般毛刺尺寸小于隔膜厚度的一半,但是有些厂家控制要求更加严格,毛刺不超出涂层。 (6)卷芯内部其它缺陷,如极片弯折、涂层阴阳面、异物等。 采用卷绕方式将正、负极极片和隔膜组装成基本的卷芯。随后,一般会对电芯进行预压整形。通过至少一次热压和/或至少一次冷压的方式,对卷芯进行定型。预压整形工艺过程如下:将卷绕或叠片好的电芯放在模板上,设定增压缸压力和模板温度,然后上下模板在一定压力和温度作用下使电芯定型,达到电芯厚度一致,使电芯弹性减小,降低装芯合格率并保证成品电芯厚度的一致性。热压温度为70~100℃,时间为30~120s,卷芯压力为0.1~1MPa。电芯热压整形的主要目的包括: (1)改善锂离子电池的平整度,使电芯厚度满足要求并具有高的一致性; (2)消除隔膜褶皱,赶出电芯内部空气,使隔膜和正负极极片紧密贴合在一起,缩短锂离子扩散距离,降低电池内阻。 预压工艺实验中,检测项目主要包括隔膜的透气性、厚度变化;电芯厚度是否满足入壳要求;极片是否发生断裂等。隔膜上的微孔结构是离子往返于正负极的重要通道,隔膜的透气性能会直接影响到电池的性能,隔膜透气性是指隔膜在一定的时间压力下透过的气体量。如果隔膜的透气性不好,将影响锂离子在正负极之间的传递,继而影响锂电池的充放电。在热压过程中,隔膜可能被严重压缩,隔膜厚度变化大,导致微孔被堵塞,肉眼观察隔膜会变成透明色,这种情况说明热压整形对电芯作用超限,会影响锂离子传输。卷绕电芯如图3所示,如果极片比较脆,电芯折弯处在热压整形中容易发生掉粉甚至断裂,这会导致电子传输受限,增加电池内阻。因此,电芯热压整形也必须避免这种情况发生。这两个方面要求热压整形压力越小越好,时间越短越好。而另外一方面,热压整形又必须使电芯定型,电芯厚度满足工艺要求,电芯弹性减小,并保证成品电芯厚度的一致性。因此,压力,时间和温度等工艺参数需要优化。 一般,在电芯热压整形时,同时对电芯进行绝缘耐电压测试,检测电芯内部是否存在微短路。如果电芯内部存在微小金属异物颗粒,在电芯被压下状态,电芯隔膜刺穿,很容易检测出微短路不合格品。绝缘耐电压测试一般采用安规仪,测试时,仪器给电芯加一个电压,这个电压持续一段规定的时间,然后检测其漏电电流量是否保持在规定的范围内,判断电芯正负极有无短路。一般,施加电压如图5所示: ③测试完成后,切断测试电压,并对电芯杂散电容放电。 在测试中,正负极极片由于相互靠近,仅仅隔膜隔开15-30μm,裸电芯内部会形成一定的电容(杂散电容),由于电容量存在,测试电压必须由“零”开始,缓慢上升,以避免充电电流过大,电容量越大所需的缓升时间t1越长,一次所能增加的电压也越低。充电电流过大时,一定会引起测试器的误判,使测试的结果不正确。一旦被测电芯的杂散电容被充满,只会剩下实际的漏电电流。由于直流耐压测试会对被测电芯充电,所以在测试后,一定要对被测电芯放电。 隔膜都存在一定的耐电压强度,当加载电压过高时肯定能够击穿隔膜,形成漏电流。因此,首先电芯绝缘测试电压要低于击穿电压。如图6所示,当正负极之间不存在异物时,在测试电压下漏电流小于规定值,判定电芯合格。而如果正负极之间存在一定尺寸的异物,隔膜被挤压,正负极之间的间距减小,正负极之间击穿电压会下降,如果还加载相同的电压,漏电流可能超过设定的警报值。通过设定测试电压等参数,就可以统计分析判断电芯内部的异物尺寸,然后根据实际产品生产现状和品质要求,可以设定测试参数,制定品质判断标准。 在测试中,主要的参数包括电压缓升时间t1,电压保持时间t2,加载电压U,以及报警漏电流。前面所述,t1和U与电芯杂散电容有关,电容量越大所需的缓升时间t1越长,加载电压U越低。而且U也与隔膜本身的耐电压强度有关,一般地,隔膜越薄,耐电压强度越低,测试电压U也应该更低。报警电流设定需要考虑电容充电电流,充电电流越大,报警电流也应该设定大些,否则会引起误判,将合格产品判定为不合格,影响产品合格率。隔膜水分含量大时也容易形成较大的漏电流。如果测试电芯内部存在异物,造成内部短路,隔膜被击穿,具体情况如图7所示。 因此,裸电芯的绝缘耐电压测试是产品过程检验的一个重要步骤,可以检测出不合格产品,提高最终电池产品的安全系数。实际测试需要考虑参数设定,判定标准等众多因素。 如图8所示,组装好顶盖,利用激光焊接或电阻焊的方式将正极留白集流体与正极汇流排焊接在一起,将负极留白集流体与负极汇流排焊接在一起,当设计容量比较大时,可以两个卷芯并联在一起。焊接时,可以先将多只卷芯并联在一起焊接,或者每个卷芯分别焊接(如两个卷芯分别焊接在232汇流片上),在激光焊接之后将多只卷芯并联在一起。焊接工艺需要根据集流体材料、形状、厚度、拉力要求等选择合适的激光器和焊接工艺参数,包括焊接速度、波形、峰值、焊头压力等来设置合理的焊接工艺参数,以保证最终的焊接效果满足动力电池的要求。 顶盖如图9所示,其结构主要由顶盖板,正、负极柱,防爆装置,注液孔等组成,一般极柱部分包含翻转片装置(OSD),电流切断结构(CID)和短路装置(Fuse)等机构。一般电池顶盖上对应正极极柱和负极极柱处有两个极柱穿孔,正极极柱从一个极柱穿孔中穿出并与顶盖片电导通,负极极柱从另一个极柱穿孔穿出并与顶盖片电绝缘,负极柱附近设置有短路部件,当动力电池内部压力增大时,短路部件向上动作,使动力电池的正负极形成回路,并在回路中产生较大的电流,使得连接部件熔断,从而切断主回路。 在激光焊接和入壳之间包绝缘膜,采用绝缘膜包覆焊接极耳的卷芯,如图10和11所示,包括:(1)与正极汇流排和负极汇流排接触的绝缘膜,其厚度要更大一些,比如厚度不低于0.1mm;(2)卷芯其余的绝缘膜,厚度可薄一些,比如0.05mm。然后,将卷芯放入壳体中,如图11所示。 采用激光方式将顶盖和壳体焊接在一起,如图12所示。激光焊接具有能量密度高,功率稳定性好,焊接精度高,易于系统化集成等诸多优点。顶盖封口焊接焊缝是方形铝壳电池中尺寸最长的焊缝,也是焊接耗时最长的焊缝。焊接速度相对较低,焊缝热循环时间相对较长,熔池有足够的时间流动和凝固,且保护气体能较好的覆盖熔池,易获得表面光滑饱满、一致性好的焊缝。提速使得焊接热循环时间缩短,金属的熔化过程更剧烈、飞溅加大、对杂质的适应会更差,更易形成飞溅孔洞,同时熔池凝固时间的缩短,会导致焊缝容易表面粗糙、一致性降低。当激光光斑较小时,热输入量不大,飞溅可以降低,但焊缝深宽比较大,焊缝熔宽不够;当激光光斑较大时,需要输入较大的激光功率,使焊缝宽度增大,但同时又会导致焊接飞溅增加,焊缝表面成型质量差。 目前,电池壳和顶盖主要是铝合金材料,其焊接的难点在于铝合金对激光的反射率极高, 焊接过程中气孔敏感性高, 焊接时不可避免地会出现一些缺陷,最主要的是气孔、热裂纹和炸火。焊接实验中,一般检查焊缝外观、焊接强度(拉伸法)、熔池尺寸和形貌(金相观察)、密封性等。另外,焊接之后,采用x射线对电池内部各部分进行检查。 电池干燥之后进行注液和预充化成,注液预充工艺如图13所示。 (1)一次注液:第一次注液,注液量为全部电解液的80%,注液机首先对电解液抽真空脱气泡,再对放置电池腔室抽真空,然后氮气加压注入电池内部,全自动分两次注入电解液。 (2)抽真空:注液完成后,对电池抽真空3min,让电解液充分浸润。 (4)开口预充电:充放电设备放置在环境露点-60℃的预充室,室内抽风机排风,另外不断补充干燥空气。预充电程序为0.2C充电60min,SOC约20%。 (5)二次补注液:注入总电解液量的20%,再次抽真空2min。 锂电池电解液作用就是正负极之间导通离子,担当充放电的介质,就如人体的血液。如何让电解液充分而均匀地浸润到锂电池内部,成为重要的课题。因此,注液工艺是非常重要的过程,直接影响电池的性能。注液分两步:1)注液 将电解液注入电池内部;2)浸润 将注入的电解液吸收到电芯,这个非常耗时,这样极大增加锂离子电池生产成本。 如图14所示,电解液通过定量泵注入密封腔室内,将电池放入注液室,然后真空泵对注液室抽真空,电池内部也形成了真空环境。然后注液嘴插入电池注液口,打开电解液注入阀,同时用氮气加压电解液腔室至0.2-1.0Mpa,保压一定时间,注液室再放气到常压,最后长时间静置(2-36h),从而让电解液与电池正负材料和隔膜充分浸润。当注液完成后,将电池密封,电解液理论上会从电池顶部渗入到隔膜和电极中,但实际上大量的电解液向下流动聚集在电池底部,再通过毛细压力渗透到隔膜和电极的孔隙中,如图15所示。 通常,隔膜由多孔亲水材料组成,孔隙率一般比较大,而电极由各种颗粒组成的多孔介质。普遍认为,电解液在隔膜中的渗透速度比在电极中更快,因此,电解液的流动过程应该是先渗透到隔膜,随后穿过隔膜渗透到电极中,如图15所示。 如图16所示,电解质在电极孔隙中扩散的机理可看作是三种力之间的相互作用:来自电解质流动的压力Fl,由于表面张力Fs而产生的毛细管力,以及孔中空气产生的阻力Fg。注液时,对电池抽真空可以降低空气产生的阻力,而对电解液加压注入则可以增加液体流动的驱动力。因此,抽真空-加压注液有利于电解液的浸润。 在锂离子蓄电池首次充放电 (预充) 过程中,电解液在负极表面还原,不溶性的还原产物在负极材料表面沉积,形成一层钝化层,即固体电解质界面膜 (SEI) ,这层钝化膜具有固体电解质的特性,是电子的绝缘体却是Li+的优良导体,Li+可以自由的地通过钝化层嵌入和脱出。SEI 膜开始形成的电压并不是固定的,有可能是2 V,1 V或者0.8 V;而且,SEI膜在电池的充放电循环中会不断地形成,还与很多因素有关,例如,负极材料,电解液成分,添加剂,充电倍率,温度等。同时,预充反应产生乙烯、氢气、一氧化碳等部分气体。 方型电池内部残存气体对厚度有较大影响, 因此必须将预充产生的气体排出。预充排气方式一般有两种:一种方式是在预充过程中用胶纸、胶套棉花将注液孔贴住,负压封口时将气体一次排出;另一种方式是在预充过程中将注液孔敞开, 让气体自由排出, 此种方式对环境温湿度要求较高, 投资较大, 但工艺较为简单。闭口工艺在封口时有一股较大的气流,会将电解液冲出,并且冲出的量不可控制。但开口工艺预充时气体缓慢排出, 不会带出电解液, 封口时也无电解液排出, 注液量一致性好。将电芯充至满电,解剖电芯后观察极片外观,发现:闭口工艺极片表面有很多斑迹, 开口工艺极片表面很干净,这是由于闭口工艺预充时电芯内部密布气泡,锂离子不能穿过气泡, 在负极片表面发生不均匀的电化学反应。开口工艺预充过程中,气泡被排出, 锂离子在负极片表面均匀反应,极片表面颜色表现出很好的一致性,SEI膜形成得较为致密。为了提高锂离子电池的生产效率,需要优化电池预充电流和时间,从而在最短的时间内充分地将电池内的气体排出来。预充电排气工艺为:预充电SOC约为30% (0.2C,1.5h),预充后抽真空10min,真空度 -96KPa。 将开口化成后的电池注液口封好胶钉,覆盖铝质注液栓,之后将注液栓焊接在电池顶盖上进行封口,使电芯内部完全被密封起来,焊接质量关系电池的密封程度,焊接不良会导致电池漏液、析锂、电池外观不良等。对于目前现有的激光封口设备,CCD拍摄效果及焊接波形设置对焊接有一定的影响;保护气的种类和保护气参数合理设定可以提升焊缝均匀一致性及宽度一致性;保证焊接区域的清洁度,减少杂质异物引入,可有效降低焊渣产生的概率;机械配合方式上间隙配合优于过盈配合,先点焊后连续焊的方式能够在很大程度上解决间隙配合时翘起的问题;增加注液孔凹台倾角的尺寸管控能够提升焊接熔深的一致性;焊接速度、输出功率及光斑直径是影响焊接强度的主要工艺参数。 最后,电池经历化成(电池进行几次完整的充放电程序)与老化(在4.0V荷电状态下45℃保存7天,再25℃保存2天,再分选),完成制造过程。