【案例】某产品薄壁件加工效率提升的工艺改善
来源:西北工业集团
薄壁件易变性、生产效率低是很多制造企业加工过程中常遇到的问题。本文案例选自西北工业集团,看他们是如何提高加工效率的。
公司某重点产品某部件为薄壁零件,一般采用旋压方式加工而成。在批量生产中,发现零件在加工完成后,上下料等待时间较长,辅助时间占到加工总时长的25%以上,机床效率没有得到很好发挥,产品加工效率偏低,严重影响了生产进度要求。
薄壁件装在芯轴上加工时,需要机床尾顶顶紧毛坯末端,旋压完成后零件由于长度较长,而机床尾座的运行速度约为0.02m/s,操作人员卸件时机床尾座需向后运动让开零件,重新装毛坯时,尾座又需向前运动,顶紧毛坯。整个加工过程,尾座顶紧和松开到位的时间较长,从而对产品加工效率造成很大影响。针对上述情况,通过分析确定技术加工要求,在保证工艺条件、参数不变的情况下,通过对工装的改进来提升机床的加工效率。1、顶紧方式的改变。将原本依靠机床尾座顶紧工件末端从而实现工件定位的夹紧方式改为用工装本身来实现夹紧定位。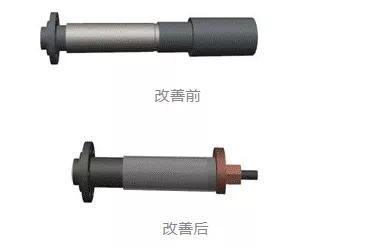
2、旋压芯轴的结构改进。将旋压芯轴结构由原来的尾部光轴改为尾部带螺纹内孔的结构。顶紧装置与旋压工装主要通过芯轴尾部的螺纹内孔连接。
改善后工装使用时,先将螺纹拉杆拧紧到旋压芯轴尾部螺纹孔中,装上工件,用螺纹拉杆上的连接螺卡住工件的内孔后端,再将U型挡板卡到螺纹拉杆上并顶紧工件的后外端面,拧上螺母将U型挡板与工件顶紧,使工件不能转动,从而实现加工时对工件的顶紧。
改善前用机床尾座顶紧工件末端时尾座往返运行所需时间约60多秒,改善后工件末端螺母的紧松时间加上挡板的抽送时间约10秒,节约时间约50多秒,辅助时间提升率约83%。整个加工过程单件加工完成所需时间约10分钟,改善后能节约9%的时间,平均一天加工工件比改善前可多加工13个,生产效率显著提高,满足了加工批量生产的进度要求。通过改进工装的方法,在保证产品质量的基础上,缩短了工件的加工时间,提高了产品加工效率。
获赞 10110粉丝 21606文章 3547课程 219