新能源汽车双电驱系统架构 NVH 技术研究
摘 要:某新能源车型搭载双电驱系统架构,其双电驱系统总成搭载在 NVH 台架试验及整车上均出现有拍频现象和双电驱系统总成噪声大,主观评价不可接受。本文针对双电驱系统 架构产生特有的拍频现象和双电驱系统总成噪声大从主动降噪激励源电磁激励、齿轮激励以及被动降噪优化双电驱系统壳体、声学包装等多方案介绍,并识别出其主要贡献来源,通过降低激励源及传递路径主要贡献量来有效抑制双电驱系统架构特有的拍频和降低双电驱系统总成噪声大。关键词:新能源 双电驱系统架构 拍频 NVH 性能全球新能源汽车行业一路高歌猛进不可逆的发展,电动化成为中国乃至全球新能源汽车产业发展的趋势。无论是传统燃油车主流汽车厂还是造车新势力都出现中高端新能源品牌产品,在新能源方向上取得突破,目前市场上新能源汽车占比逐渐增多。
本文以新能源汽车双电驱系统架构搭载整车为例,在传统的动力系统架构里,主要以电机、减速器、电机控制器组合技术方案,简称三合一。或通过传统的发动机加电混系统组合技术方案,其中电混系统主要包括电机、离合器、减速器的集成式电子控制器等方案搭载在整车上,以上方式的组合技术方案其转速、扭矩等性能很难发挥到极致,为了提高三合一或多合一电驱系统产品的性能开发,提升产品在全球市场上的竞争力,为消费者带来更加极致的用户体验,从而各大汽车主机厂开始研发高性能、高效率产品不断迭代,开发各种高性能指标参数的双电驱系统架构产品。
双电驱系统架构,其驱动架构主要由双电机、双减速器、集成式控制器等组合而成的双电驱系统技术方案,其布置形式为双电机对立在两端布置,每个电机连接一个减速器。这样双电驱系统布置形式可以实现单边驱动或双边同步驱动,轮端可同时实现最大转速或最大扭矩输出,其双驱动系统架构搭载在整车上能将其性能发挥到极致,这样的双驱动系统架构特性会带来独有的 NVH 拍频现象和双电驱集成双激励下噪声大的 NVH 难题,通过开发出样件搭载 NVH 台架试验及在整车上均有出现拍频现象和双电驱系统总成噪声大,主观评价不可接受。为解决其 NVH难题,同时也为开发人员及整个双电驱架构带来前所未有巨大挑战。对双电驱系统架构特性独有的拍频现象以及双电驱系统总成噪声大问题,并对能引起双电驱拍频现象产生的机理进行详细分析,通过电磁优化、齿轮优化、壳体优化、声学包装优化等技术方案方法进行介绍。双电驱系统架构左右两电机、齿轮参数相同,在车辆行驶时当两电机存在转数差,激励频率、幅值相近,当出现两个幅值和频率相近的简谐波进行叠加时,会出现幅值忽高忽低的现象即“拍现象”,波形的幅值随时间作强弱周期变化,单位时间内出现的拍数称为拍频,如图 1 所示。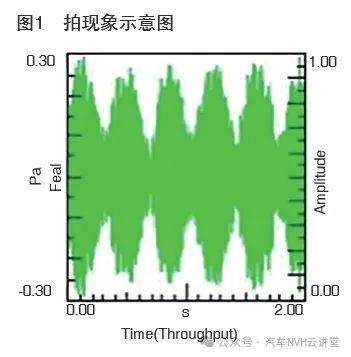
在双电驱系统搭载 NVH 台架试验过程中,模拟整车路况使得左右电驱有转速差匀速工况,主观评价拍频现象很明显,不可接受,如图 2 所示。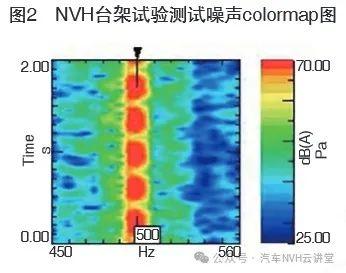
当整车状态下在道路上行驶转弯时,左右轮产生转速差,如下道路转弯示意图 3 所示。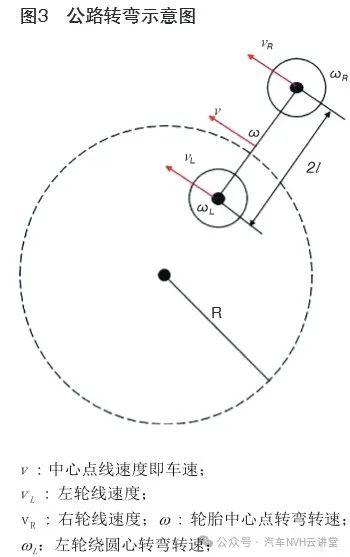
根据公路设计规范,例如车速 v=80km/h=22m/s 时, 设 计 最 小 转 弯 半 径 范 围 为250m-400m;当 R=250m-400m 时,假设总速比 13.6,带入上式计算得: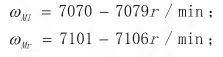

双电驱系统独有的架构特性搭载在整车上,行驶工况下存在左右车轮转速不一致的情况,存在拍频的风险。为排除拍频风险及降低双电驱系统噪声,需进一步分析影响拍频及双电驱系统噪声大的因素。
搭载双电驱系统 NVH 台架试验结合整车测试数据,排查产生拍频机理分析,通过滤波信号分析,发现拍频现象和噪声大主要贡献出现在电机阶次激励、齿轮阶次激励,且齿轮激励贡献量大于电机激励,其中电机激励为低阶次和电磁力阶次。为了抑制双电驱系统拍频现象及降低双电驱噪声优化解决思路,双电驱系统方向来讲从激励源(电磁力、齿轮)- 传递路径(壳体)方向上去优化,整车方向来讲激励源(双电驱系统声学包装)- 传递路径(空气传声整车声学包装)方向去优化。本架构双电驱系统以汽车运用常见的永磁同步电机为例,其主要有转子、定子及其绕组、壳体和端盖组成。其转子上布置高质量的永磁体磁极,由于永磁体和定子绕组产生的磁场相互作用,产生切向力供电机输出驱动扭矩,同时还会产生各种阶次频率的旋转径向电磁力,此力将引起电机壳体振动,由结构振动引起的结构表面空气的压力脉动,并向外传播,形成辐射噪声,因此优化电磁力可以降低双电驱系统振动噪声。通过试验数据分析低阶次以及电磁力阶次在低转速噪声较为突出,低阶次明显,可优化同轴度来降低低阶次贡献量,其中同轴度与样件生产、制造、工艺、装配相关联连,一般要求同轴度< 0.2mm,低转速噪声较为突出可通过谐波注入方式解决优化电磁力在低转速贡献量。齿轮在电驱传递系统中起着重要作用,在传动过程中,由于制造加工误差、啮合错位量等因素的影响使得传动过程中存在齿轮传递误差、弹性变形等现象,导致齿轮副在啮合与啮出时偏离理论啮合线,造成内部激励和外部激励的冲击产生动态激励力,通过传动路径传递轴、轴承到电驱壳体,从而振动噪声异常偏大。在追求更高性能参数指标的同时对齿轮的要求时越来越苛刻,降低齿轮的激励力是有效降低总成振动噪声的重要因素。其中在前期 CAE 仿真阶段齿轮 NVH 性能指标项的有重合度、啮合错位量、轴扰度、传递误差、接触斑、齿顶滑移率等参数指标需满足目标要求。针对齿轮激励产生的拍频现象,可采取避频或降低齿轮啮合激励两种方案改善拍频现象及因齿轮阶次贡献的总成噪声大。在前期齿轮设计阶段,一方面设计齿轮总速比不变调整各级齿数,可以错开拍的频率。另外一方面或齿轮齿数相同优化齿轮宏观参数 & 微观参数修形,通过齿面修形参数优化,使齿面接触位置受力居中减小齿轮传递误差,降低啮合激励,如图 4 所示。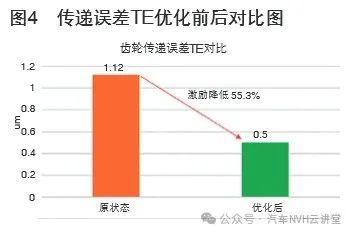
双电驱系统壳体设计开发要求,需同时满足 NVH、可靠性、轻量化等相关性能目标要求,使得在设计壳体过程中不只是简单的堆料。其中总成模态、轴承座动刚度、壳体振动响应及辐射噪声等是衡量 NVH 性能开发仿真分析过程中重要指标项。其中壳体的振动噪声的响应是有许多不同的模态响应叠加而来,通过模态贡献量计算,可以评估对于某些局部振动噪音峰值,主要参与振动的模态有哪些,可以针对性的进行弱点优化分析,从而可以降低振动噪声局部峰值。在前期数据设计阶段,通过 CAE 仿真方法不断迭代计算壳体模态、轴承座动刚度、振动响应及辐射噪声,可拓扑优化方法来提高壳体 NVH 性能。本双电驱系统在前期数据 CAE 建模仿真阶段总成一阶弯曲模态、电控盖板、轴承座动刚度不达标,且存在如一阶弯曲、电控盖板局部呼吸模态,通过仿真计算壳体振动响应及辐射噪声进行弱点分析,并通过拓扑结构优化加筋及其拱形结构等方式来解决优化壳体,使其壳体 NVH 达标,性能更优。声音在空气介质以声波的形式传播,在汽车行业中需对噪声进行吸隔声处理,其材料主要涉及吸声材料和隔声材料,一般吸声材料、隔声材料运用装配在整车机舱盖、前围板、地板、集成在饰件上等车身位置,其中衡量吸声材料的重要指标吸声系数,吸声材料在不同的频率段下其吸声性能不同,声波通过吸声材料里细小的孔状结构逐渐缓解振动,并转换为热能,从而达到吸声的作用,一般而言吸声材料在高频段效果相比低频段吸声性能更好。同理衡量隔声材料的重要指标隔声系数,隔声材料在不同的频率段下其隔声性能不同,声波传播通过高密度隔声材料结构反射出去,一般隔振材料在低频段效果较好。根据吸声材料和隔声材料的结构声学特性,设计适合新能源汽车的声学包装,新能源车相比传统车来讲高频噪声占比多一些,根据双电驱系统的结构特性设计声学包装技术方案,本双电驱系统采用吸声材料与隔声材料结合,吸声材料采用 PU 发泡,隔声材料用 PET 或 EVA 材料,采用内吸外隔的方式集成一体随电驱系统边界包络成型,一般厚度25cm 左右覆盖面积 95% 左右,同时双电驱系统总成声学包需满足防水、耐腐蚀等性能要求。整车声学包装设计技术方案除了传统的声学包装位置布置外在双电驱系统正上方车身地板下方需覆盖电驱位置其吸声材料厚度不低于 25cm 左右。根据双电驱系统本身激励源噪声频率贡献特性和整车车内噪声特性优化调整其声学包装吸隔声系数方案。将优化技术方案样件零部件检测合格后装配总成完成,搭载 NVH 台架试验测试,其结果如图 5 所示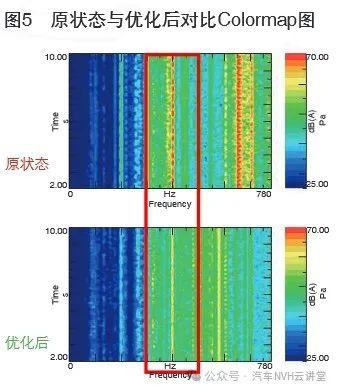
根据上图 5 原状态双电驱系统总成与优化后双电驱系统总成 NVH 台架试验测试结果对比,拍频现象改善效果明显。如图 6 所示,原状态与优化后的最大幅值及波动量对比,拍频的最大幅值从 65dBA 降低到 55dBA,拍频的上下波动缩减了 60%。在 NVH 台架试验模拟道路差速各工况下主观评价拍频声明显变小,且总噪声明显降低。将该 NVH 台架试验的双电驱系统总成样件搭载在整车上主观评价和客观测试,车内无拍频现象且双电驱总成噪声对车内贡献小可接受。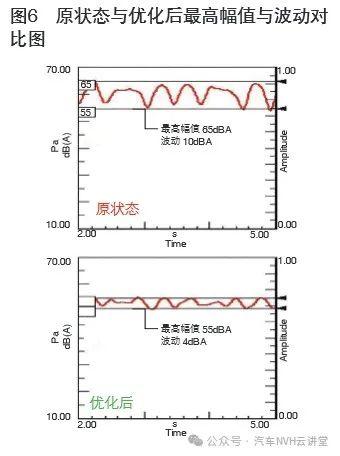
新能源汽车双电驱系统架构且在 NVH 性能领域里特有的拍频现象及双激励下总成噪声大的难题。在前期开发阶段 NVH 台架试验及整车样车阶段主观评价及客观测试均存在拍频现象及双激励下总成噪声大等问题并通过电磁力优化、齿轮优化、壳体优化、声学包装优化等各技术方案,同步结合生产、制造、工艺、装配等严格把控样件质量等一系列的方案来解决该难题,因此解决双电驱系统架构所带来的 NVH 难题是 NVH 领域系统工程。从前期 CAE 仿真分析到样车搭载台架试验阶段及整车验证阶段去识别双电驱系统架构所带来的 NVH 难题,通过系统性技术方案优化及生产、制造、工艺、装配把控质量相结合,有效解决该架构所带来特有的 NVH 难题。新能源汽车行业内相同或类似新能源乘用车双电驱系统架构车型在前期设计阶段及后期样车调校阶段主观评价存在拍频现象及双电驱系统总成噪声大等难题及 NVH 性能优化提供参考。作者单位:比亚迪汽车工业有限公司 广东省深圳市 518118