某电动总成悬置NVH改进案例
某电动汽车急加速过程中抖动显现明显,主观评价无法接受,且急加速过程伴随明显撞击噪声。图1是急加速过程车内噪声测试结果,电机1100r/min左右存在明显宽频噪声,是典型冲击现象,与主观感觉相吻合。该电动总成采用了图 2 所示的三点式布置形式。其中悬置2和悬置3主要起到平衡电机扭矩的作用,而悬置 1 主要起到支撑作用。这种布置与传统动力总成的三点悬置布置思路完全不同。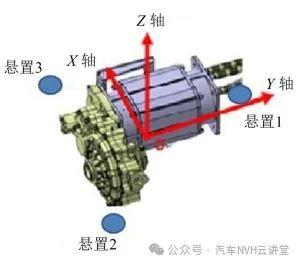
该电动总成惯性参数见表1。 悬置整车坐标系下位置见表2。整车坐标系的定义:从车头指向车尾为X正方向,竖直向上为Z,Y方向由右手定则确定。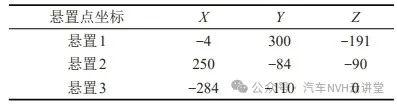
悬置系统局部坐标轴的定义见图3,本案例中悬置局部坐标轴 u、v、w 的方向分别与整车坐标系 X、Y、Z轴方向平行。悬置的初始刚度见表3。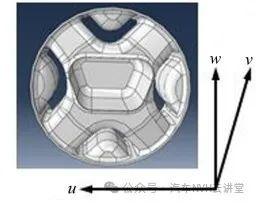
表4是初始状态下6阶刚体模态仿真结果,第6阶模态的频率为29.4 Hz,远低于标杆车的43.6 Hz。可见与标杆车相比该悬置系统的刚度明显不足,很容易产生加速抖动和运动干涉的问题。

为此,又进行了电动总成的瞬态响应分析。分析工况为急加速工况,电机的峰值为200 Nm,减速器的速比为8.1:1。在绕电机的轴线方向施加1 620Nm的扭矩。图4是电动总成悬置系统动力学模型。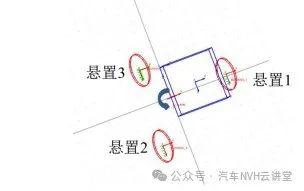
图 4 动力学仿真模型
考虑电机的响应需时间,施加的扭矩随时间变化曲线如图5所示;整车的加速度约为2 m/s2,在质心位置施加162.8 N的惯性力。图 6是急加速工况下电动总成质心位移的仿真结果。电动总成质心位置沿整车X方向最大位移为11.5 mm,易与周围的部件发生干涉而产生撞击。
因此,在工程可行范围内对悬置的位置和刚度进行了改进设计,以提高悬置系统抗扭矩能力,减小电动总成质心位移,避免运动干涉。具体改进措施如下:1)调整了悬置2、3在整车X方向的位置。加大两个悬置与电机轴线之间的距离,提高悬置 3 的安装位置。改进后悬置的悬置系统的安装位置见表5。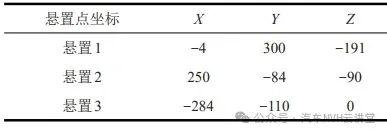
2)提高了悬置2和悬置3的刚度,提升悬置系统对电动总成的位移控制作用。改进后悬置系统的动刚度见表6。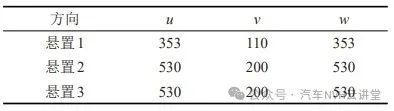
表7是改进设计后电动总成悬置系统的固有频率,改进设计后系统的固有频率有较大幅度的提升,与标杆车的结果接近。
图 7 是改进设计后动力总成质心位移的仿真结果。急加速工况下电动总成质心X方向的最大位移减小到1.6 mm左右,显著地降低了发生运动干涉的风险。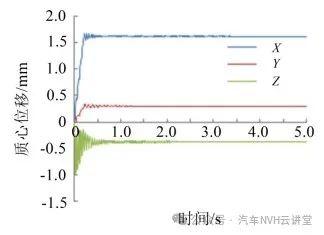
对改进后的悬置方案进行了装车验证,图8是改进的后车内加速车内噪声的测试结果。改进后加速车内车辆的抖动主观评价改善明显,金属撞击声消失。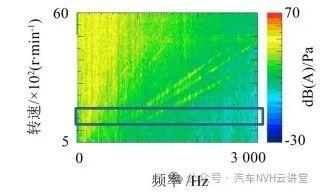
图 9是改进前后车内前排驾驶员耳旁噪声对比,电机1 100 r/min附近的车内噪声降低4 dB以上。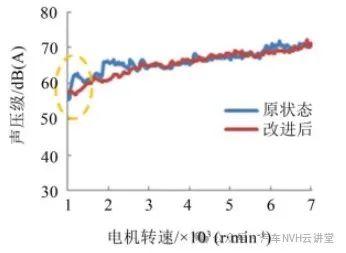
著作权归作者所有,欢迎分享,未经许可,不得转载
首次发布时间:2024-02-22
最近编辑:1年前