多源激励下电机-减速器一体化系统 NVH 的研究
摘要:针对电动汽车中的噪声、振动与舒适性问题,对电动汽车电机-减速器组成的动力总成系统进行了振动与噪声的研究。首先提出了一种综合考虑电机-减速器总成系统的建模方法,并针对该模型进行了模态分析; 根据实际需求设计了电机-减速器的基本参数,分析了使得电机与减速器振动与噪声的主要激励源; 然后针对电磁激励与机械激励,对电机-减速器系统的影响进行了振动与噪声分析; 最后进行了多源激励作用下,动力总成振动与噪声特性的仿真与实验验证。研究结果表明: 多源激励下电机-减速器动力总成系统的仿真结果与实验结果相符合,验证了所提出的永磁同步电机与减速器动力总成建模的正确性,说明该模型可以用于实际工程的优化设计。
关键词:电动汽车; 动力总成; 电磁激励; 机械激励; 噪声、振动与舒适性随着电动汽车的快速发展,人们对汽车续航、成本以及舒适性越来越重视。高效率的永磁同步电机成为电动汽车主要驱动电机[1-2]。宽转速区间的电动机作为动力输出,只需要一个固定速比的减速器就可以达到电动汽车日常使用的动力要求。因此,大多数动力总成是由永磁同步电机与固定速比的减速器集成,成为电动汽车中动力系统的发展趋势。动力总成系统中复杂的电、磁、机械以及流体的多物理耦合,使得 NVH 的研究成为重难点。作为电动汽车 NVH 问题的主要来源,动力总成系统的准确建模与优化分析十分重要[3-4]。在电机与减速器振动与噪声方面,国内外许多学者都对振动噪声作了详细研究与分析。文献[5]指出,电机振动噪声源主要来自径向力波、齿槽转矩与转矩脉动,并提出了一种齿槽转矩的计算方法,推导出了转矩脉动的表达式,指出永磁同步电机的空间谐波与时间谐波对转矩脉动的三倍频影响最大,另外指出了激励源与结构模态相近时,永磁同步电机的噪声声压级达到峰值; 文献[6]通过对永磁同步电机的分析,建立了电磁与振动声学的有限元耦合模型,该模型有效地将磁楔磁导率、槽口高度以及转子形状考虑在内,计算出了复杂单元的气隙磁导率,并预测了永磁同步电机的电磁噪声; 文献[7]对永磁同步电机常用齿槽配合的电磁振动作了详细分析,指出了定子表面电磁谐波最小模数为槽极比的最大公约数,且模数较小的电磁力谐波是产生振动的主要原因; 文献[8]分析了不同工况下电动汽车中电磁振动噪声,并指出了低速过载和高速弱磁区气隙谐波含量有所增加; 文献[9]通过对电机模态分析,指出了可以使用定子绕组的简化模型对电机结构的固有频率进行预测分析; 文献[10]介绍了减速器齿轮啸叫噪声与齿轮拍击噪声形成机理,分析了当前齿轮研究的优缺点; 文献[11]对齿轮箱箱体进行了模态分析,指出了合理的结构刚度布置有利于提高齿轮箱模态频率,降低振动响应。目前,国内外学者针对电动汽车动力总成振动噪声研究相对较少,文献[12]采用 4 种螺栓连接方式单元进行了建模,并进行了模态分析与实验,但未给出合理的优化方式; 文献[13]使用 Romax 软件对动力总成模态及振动响应仿真分析,文中研究了悬置及水套对总成模型的影响,但仅将传动啮合作为激励。笔者将建立永磁同步电机与减速器的动力总成有限元模型,并对结构模态进行分析; 然后分别对永磁同步电机电磁力特性与减速器齿轮传动特性进行分析;最后通过施加电磁力与机械力,进行多物理场耦合振动噪声分析,并通过实验分析验证考虑多源激励的动力总成一体化建模的可行性。该动力总成系统由电动机产生转速和转矩,通过轴与减速器齿轮副将转速与转矩进一步转化,因此,可以分成外壳系统与传动系统两个部分。动力总成系统结构如图 1 所示。图1中: 1、2、3、5、6 为动力总成外壳系统; 4、7、8、11 为传动系统; 10 为轴承,用于壳体系统与传动系统的连接,电机通过转子带动输入轴,通过两级齿轮副减低转速增大转矩。传动系统由于存在转矩脉动以及齿轮啮合效应,通过轴承与壳体的连接直接将产生的振动作用在壳体系统上。
因此,该动力总成系统主要噪声来源有: ( 1) 壳体振动; ( 2) 减速器齿轮啮合与啸叫。以往对电机的振动噪声研究仅仅考虑电磁力所引起的振动,而在动力总成中,电机与减速器在外壳结构上是刚性连接的,除电磁力外,传动系统在轴承连接处也可以将振动传递至壳体,从而引起振动噪声。笔者所研究的动力总成由两部分构成: 永磁同步电机和减速器。针对不同模型结构,笔者采用不同单元进行网格划分。螺栓连接使得电机端盖与壳体、减速器与电机之间刚性接触,笔者采用 BEAM + RBE2 单元模拟螺栓结构。模态是系统的固有特性,对于研究系统的振动与噪声有着重要意义。因此,笔者结合有限元分析特点,分别对永磁同步电机与动力总成系统进行模态分析。各系统前十阶模态固有频率如表 1 所示。表 1 中,对比永磁同步电机与动力总成系统进行模态分析结果可以看出,在相同阶次下,动力总成的固有频率更低,更加密集。由此说明: 在动力总成系统的振动噪声分析中,考虑完整的动力总成模型将会有助于获得更丰富、更精确的动力学响应。动力总成系统中,产生振动与噪声的激励主要有:( 1) 永磁同步电机的电磁激励; 电磁激励通过永磁同步电机定子铁芯传递,并引起壳体的振动与噪声; 机械激励主要通过传动系统中轴承与壳体的连接传递。永磁同步电机是通过定子绕组电流产生的气隙旋转磁场与转子永磁磁场相互作用,产生转矩。气隙磁场中,同时也产生作用于定子铁芯内部的电磁力波,通过传递引起整个铁芯与壳体的结构振动,并向外辐射电磁噪声。笔者采用 8 级 48 槽永磁同步电机,采用双“一”字形永磁体结构的电磁方案。永磁同步电机在正弦波供电条件下,忽略定子铁芯磁阻和磁路饱和的影响,电机中气隙磁密的解析式为:
式中: f( θ,t) — 气隙磁通密度; f( θ,t) — 总气隙磁动势; Λ( θ,t) — 气隙磁导。正弦波三相平衡供电作用下,三相永磁同步电机磁动势的时间空间分布可分为转子侧与定子侧,分别如下:
式中: f1 ( θ,t) — 转子侧磁动势空间分布; f2 ( θ,t) — 定子侧磁动势空间分布; fυ,fμ— 谐波峰值; ν— 转子空间谐波次数; μ— 定子的空间谐波次数; ω— 输入电流脉动,ω = 2πf; p— 电机极对数; φ— 定转子谐波矢量之间谐波夹角。根据式( 1 ~ 3) ,可以得出正弦激励下电机气隙磁密为:
由式( 4) 可以看出: 在各种磁场共同作用下,气隙磁密有较为复杂的谐波成分。空间极对数较低的径向电磁力对电磁振动起主要作用; 同时,空间谐波次数较低的径向电磁力主要由永磁体 u 次径向谐波磁场与电枢反应 υ 次径向谐波磁场相互作用产生。对气隙磁通密度分解,可得到径向气隙磁通量密度、切向气隙磁通量密度。根据麦克斯韦定律,可以得到单位面积径向电磁力和单位面积切向电磁力,即: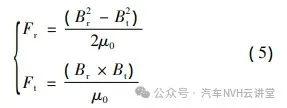
式中: μ0— 真空磁导率; Br— 径向气隙磁通密度; Bt—切向气隙磁通密度; Fr— 单位面积径向电磁力; Ft—单位面积切向电磁力。径向电磁力是引起电机定子及壳体产生振动的主要因素; 作用在定子铁芯上的切向电磁力主要使得铁芯齿部发生形变; 铁芯齿部宽度和刚度适当时,切向电磁力对壳体和铁芯的振动与噪声贡献量很小,可以忽略其影响[14]。在三相 正 弦 电 流 作 用 下,笔者分别对转速为1 000 r/min、2 000 r/min、3 000 r/min、4 000 r/min、5 000 r/min进行电磁力波分析。通过对径向电磁力波阶次进行分析,可得到不同转速下径向力波阶次的分布,如图 2 所示。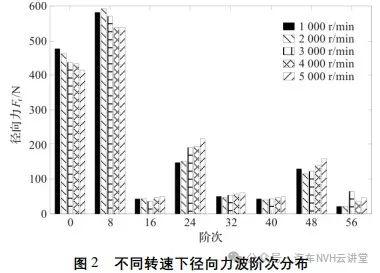
通过分析图 2 可知: 在不同转速下,径向力波阶次分布相似,均为基波,8 次、24 次、48 次谐波含量较大;其中,8 次谐波为引起电磁振动的主要谐波。以电机转速在 3 000 r/min 为例,转子基频 f =50 Hz,电机极对数 p = 4,电机的电磁力峰值频率是以转子基频的 2np 倍为主。定子齿槽受到的电磁力频率主要为: 8f( 400 Hz) 、16f( 800 Hz) 、24f( 1 200 Hz) 、48f( 2 400 Hz) 等。动力总成内部激励是指减速器齿轮在啮合过程中产生的动态激励。齿轮啮合过程中,由于传递误差和时变啮合刚度等因素,使得啮合过程中产生振动,该振动通过轴承传递到动力总成壳体,从而引起振动与噪声。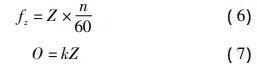
式中: fz—齿轮啮合频率; Z—齿轮的齿数; n—齿轮的转速; O—齿轮副啮合阶次。
通过式( 6 ~ 7) ,可以计算出该参数下齿轮副啮合阶次,如表 3 所示。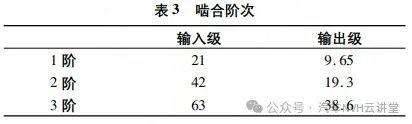
该动力总成由 8 个轴承将传动系统与壳体连接。以二级齿轮副外轴承处的振动加速度为例,通过仿真分析可以得到齿轮副 1 阶振动频率,轴承处 9. 65阶、21 阶振动加速度,如图 3 所示。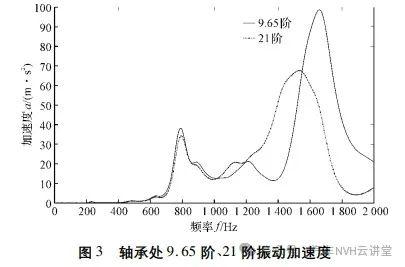
从图3 可以看出: 随轴承处加速度值在9.65 阶分别在800 Hz 与1 710 Hz 出现峰值,21 阶分别在800 Hz与 1 435 Hz 出现峰值,9.65 阶在低频率与高频率均大于 21 阶,为主要振动噪声来源,即二级齿轮副; 在中频段主要噪声来源为 21 阶,即一级齿轮副。动力总成由永磁同步电机与减速器组成,振动响应分析涉及到电磁力激励与机械激励的多物理耦合,需要进行多个工程软件耦合分析。电磁力通过 Maxwell 计算,并施加在定子铁芯齿部; 动力总成机械激励通过 Romax 软件计算,并通过轴承传递至动力总成壳体。根据该系统特性,笔者研究在 0 ~ 5 000 r/min 的工况下,动力总成系统的多源激励振动响应; 并选取壳体系统中两个测试点: 点 1 测试点位于减速器外部壳体,点 2 位于永磁同步电机外部壳体。仅在电磁激励作用下,测试点 1、2 主要阶次电磁力的贡献量主要由 8 阶、16 阶、24 阶、48 阶组成。测试点 1、2 振动响应如图 4 所示。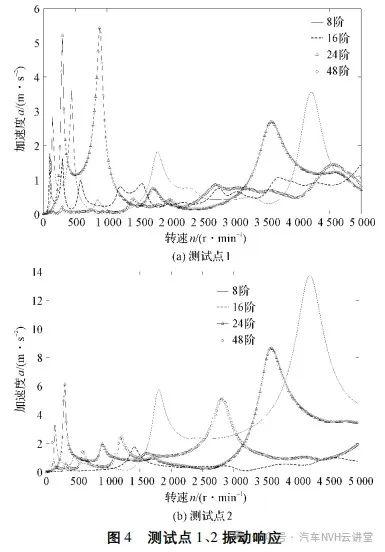
( 1) 根据测试点 1 的结果可以看出: 在动力总成系统中,减速器壳体受到电磁激励的影响。虽然电机定子与减速器结构上没有直接接触,但仍然收到电磁激励的影响。这表明对动力总成系统 NVH 的研究,应一体化建模;( 2) 测试点 1 振动响应明显小于测试点 2,说明电磁激励主要作用点在与定子直接连接的电机壳体,而在减速器端主要是通过外壳振动响应的传递,振动幅值减小,与理论相符;( 3) 从测试点 1 与测试点 2 中可以看出: 8 阶、24 阶会引起较大的振动; 根据测试点 2 的振动响应结果可以看出: 8 阶在 4 000 r/min ~5 000 r/min 有较大的振动响应,对应的 8 阶频率在 2 133. 33 Hz ~ 2 666. 67 Hz; 根据模态分析结果可以看出: 有 11 ~ 19 阶模态在该范围内,引起较大共振。笔者分别以电磁激励、机械激励以及总激励为激励源,测试点 1、2 振动响应,如图 5 所示。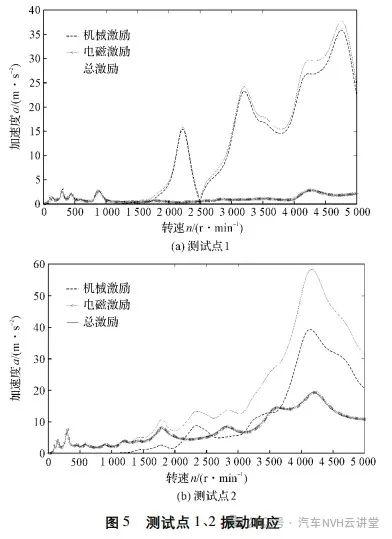
( 1) 在 0 ~ 5 000 r/min 范围内,机械激励为影响振动的主要原因。对比点 1、点 2 可以看出,在电机侧电磁激励仍然会产生较大的振动响应,而在减速器侧电磁激励的影响所占比例较小;( 2) 该动力总成系统中,在3 000 r/min ~5 000 r/min范围内,振动响应幅值较大,会产生较大振动噪声问题。结合前文模态分析与机械激励的分析结果,可以进一步得出以下结论:( 1) 电磁激励与机械激励共同影响着动力总成系统的振动噪声特性; 其中,机械激励为主要影响因素,而二级齿轮副的 9. 65 阶齿轮啮合激励对本研究动力总成系统有着较大的影响;( 2) 一体化结构建模使得系统固有频率降低,且部分固有频率较为集中,容易引起系统共振;( 3) 相较于机械激励,电磁激励具有更多谐波分量,更易产生结构共振,使得动力总成系统在速度较高时产生较为复杂的动力学响应。综上结论可知,应综合考虑上述两个因素,再通过一体化建模,才能得到较为准确的仿真分析结果。为了进一步验证仿真结构的准确性,笔者进行动力总成噪声测试实验。实验相关设备包括: 永磁同步电机与减速器的动力总成系统、控制器、麦克风、LMSTestlab 分析设备等。实验中参考国家标准,在半消音室内,麦克风距离动力总成 1 m 的距离。测试工况为动力总成系统从1 000 r/min到 5 000 r/min 的加速噪声。实验环境与结果如图 6 所示。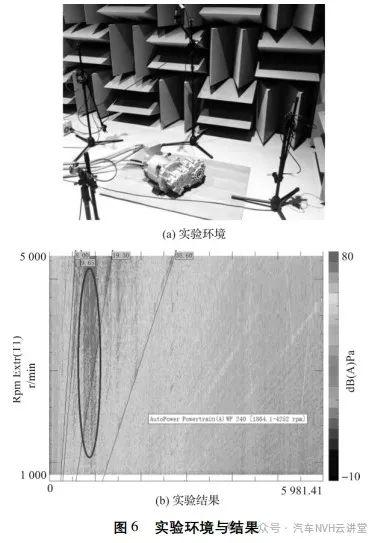
( 1) 在加速过程中,减速器的 9. 65 阶噪声较为明显,电机的 8 阶噪声次之;( 2) 在整个噪声分布中,存在无明显阶次的频域,属于宽频,由冲击激励导致;( 3) 在加速过程中,在高速时有较大的噪声,最大噪声达到 79 dB,这与仿真结果相符合。笔者通过对电机 - 减速器一体化系统建模、仿真以及实验分析,可得到如下结论:( 1) 在相同阶次下,一体化建模固有频率有所降低,并有更丰富的固有模态分布,更易产生共振。经综合考虑,永磁同步电机与减速器的一体化建模能够更加准确地反映电动汽车动力总成的振动响应特性;( 2) 机械激励和电磁激励是引起动力总成壳体结构振动的主要激励源,机械激励为主要影响因素,电磁激励则在特定阶次有较大的影响;( 3) 电磁激励主要引起动力总成电机部分壳体的振动,但在减速器壳体部分也受到电磁激励的影响,齿轮啮合产生的机械激励同样也会使得电机壳体产生振动。因此,在动力总成系统中,需要综合考虑电磁激励、机械激励;( 4) 本研究动力总成系统主要影响因素为二级齿轮副的 9. 65 阶机械激励与电机的 8 阶电磁激励。仿真结果与实验结果相符合,进一步说明多源激励动力总成一体化建模可以有效地分析动力总成 NVH 性能。作者:屈 峰1 ,刘栋良1,2 ,李阿强1 ,杨响攀1作者单位:( 1. 杭州电子科技大学 自动化学院,浙江 杭州 310018; 2. 卧龙电气驱动集团股份有限公司,浙江 上虞 312300)免责声明:分享此文仅为传播汽车底盘相关知识,其版权归原作者所有,感谢原作者的辛苦付出;若有侵权异议等请跟我们联系协商或删除,谢谢!