Graphical Abstract
相关综述以题为 “Multi-scale defects in powder-based additively manufactured metals and alloys” 发表在材料领域顶刊 Journal of Materials Science & Technology上。
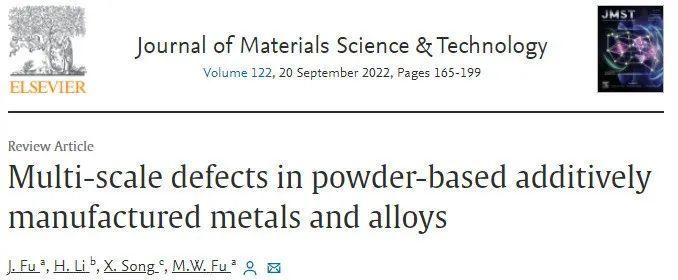
论文原文下载见本文末
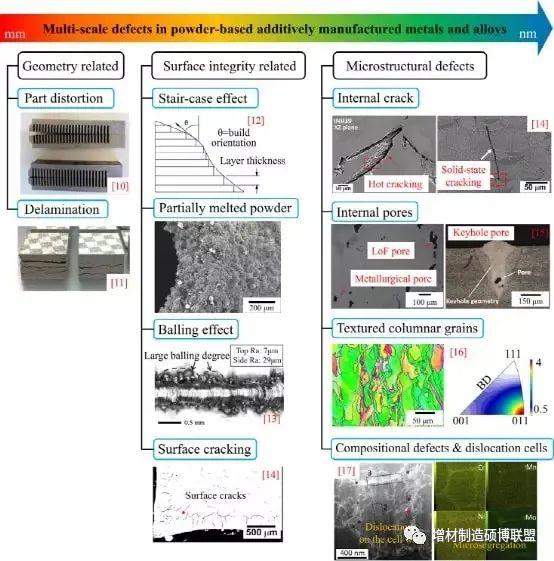
基于粉末的增材制造金属和合金中多尺度缺陷的分类
1.2 表面完整性相关缺陷
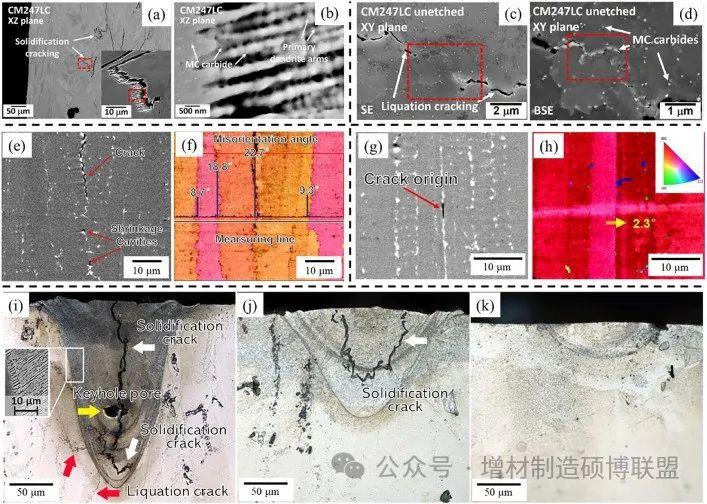
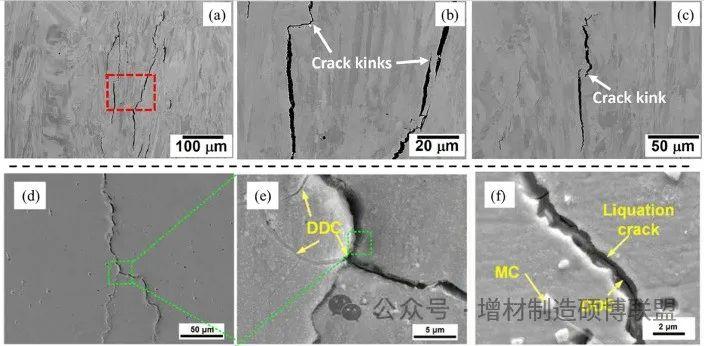
1.3.2 内部孔隙
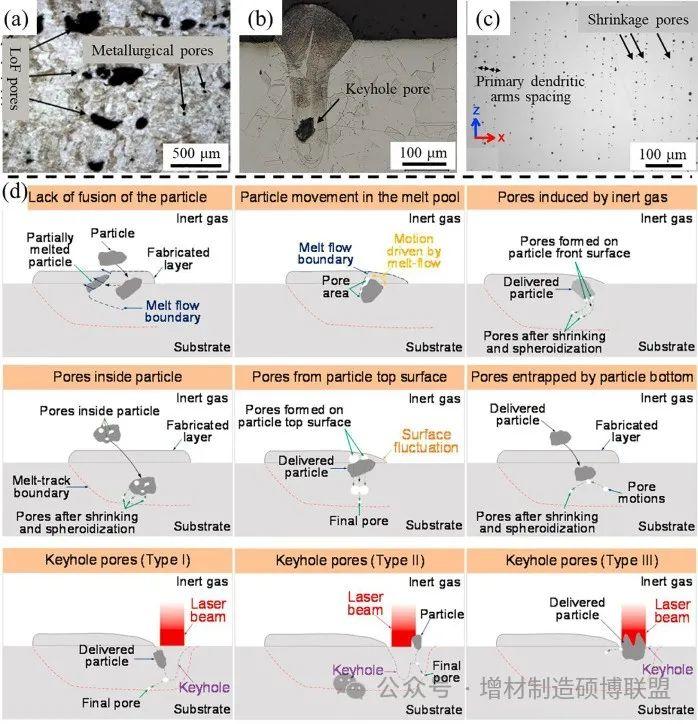
1.3.3 组织缺陷
1.3.4 成分缺陷
2. 多尺度缺陷调控方法
2.1 残余应力控制
控制成形部件内部的残余应力和变形可有效提高成形部件的精度和质量。残余应力消除主要通过热处理来实现,热处理按照其加工过程可分为:(1) 原位热处理;(2) 传统热处理。 原位热处理主要是通过设置更为合理的过程参数 (如改变扫描策略),降低成形过程熔池与凝固组织间的温度梯度和冷却速度,在成形平面产生更为均匀的热分布。此外,传统热处理也可被用来消除成形部件内部的残余应力和提高孔隙率,但在处理过程中应注意设置合理的保护气氛以防止活性金属氧化。此外,近年来有研究人员将超声强化、激光冲击强化等新型手段与增材制造相结合,促使成形部件内部残余应力转变为有益的拉应力,极大地增加了金属部件的疲劳性能。
降低铺粉层厚可有效减少台阶效应对于成形部件表面精度的影响,但同时会延长打印时间,增加打印成本。此外,打印过程中合适的摆放位置。现有研究表明成形方向与打印生长方向夹角小于30°可有效抑制台阶效应对于成形样品表面精度的影响。未熔粉末和球化效应所引起缺陷可通过调控过程参数来进行调整和优化。为提高表面光洁度,可筛分出粒度分布较为集中的粉末颗粒进行打印。采用较低的扫描速度和较高的激光功率可有望实现粉末完全熔化,消除球化缺陷,降低表面粗糙度。然而,过多的能量输入也可能导致热应力和冷却速度不均匀造成部件变形等缺陷。因此,需对工艺参数进行广泛研究,优化各种工艺参数,包括激光功率、扫描速度和舱口距离等,以达到粉末完全熔化条件。
(a, b) 表面粗糙度作为分析粗糙度模型预测的倾斜角和颗粒分数的函数;(c) 多层 PBF 工艺模拟的侧面,以及 (d) 实验和预测侧面粗糙度的比较
此外,为降低金属增材制造部件表面粗糙度,对于结构简单的金属部件,可采用常规机械光整加工方法对于成形部件进行加工处理,如:机械抛光等。但传统加工技术难以对增材制造复杂结构部件表面进行有效处理。对于具有复杂结构的异形金属部件,常采用化学抛光、磨粒流抛光等先进物理、化学抛光方法进行处理。 微观组织缺陷控制主要通过合金成分设计和过程参数控制来实现。通过在打印体系中添加新型合金元素或增强相颗粒,可有效改善部件加工性能,消除缺陷,提高打印质量和材料性能。目前,用于裂纹敏感合金的附加陶瓷颗粒包括氧化物( Al2O3 , Y2O3 )、氮化物( TiN )、碳化物( TiC , SiC )、水合物( TiH2 )和硼化物( TiB2 )等,这些亚微米或纳米级颗粒增强相可以作为异质形核点,诱导等轴晶生长,共调更多的应变,进而消除热裂纹缺陷。
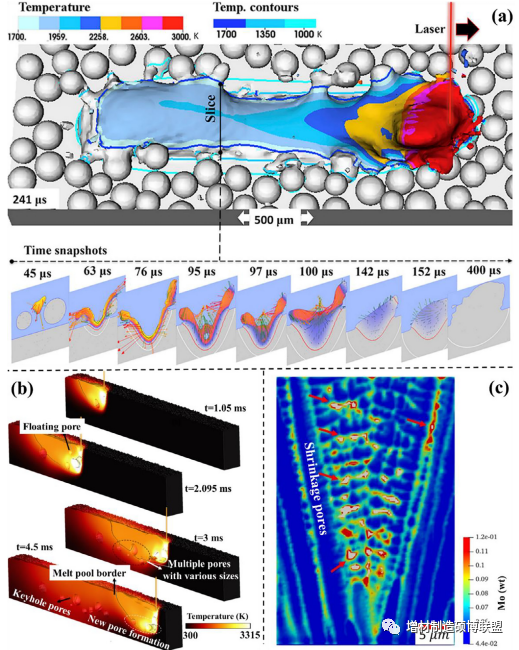
SS316L和 (b) Ti6Al4V LPBF 中熔池演化和孔隙形成的数值模拟;(c) Ni-Mo二元合金的AM中缩孔形成的模拟
Al7075合金的PBF打印:(a)标准原料粉末(b)加入纳米颗粒的粉末(c,d)树枝状生长模式从柱状生长向等轴生长的转变(e,f)添加纳米颗粒的晶粒细化和裂纹消除
工艺参数优化是目前最为常用的显微组织缺陷控制方法,主要是通过体能量密度公式来确定合理的加工参数窗口。但随着对能量密度公式的研究逐渐深入,研究人员发现现有能量密度公式已难以对工艺参数进行精确调控,急迫需要对其进行修正。为解决PBF成形金属部件因其内部粗大柱状晶所造成的严重的各向异性,研究人员期望将其转变为细小等轴晶来提高其机械-力学性能,主要有以下四种方法: (1) 对打印过程参数进行调整(包括:激光功率、扫描速度、扫描策略等); (2) 添加晶粒生长限制元素或增强相对合金进行合金设计,促使熔池中过冷液体在凝固时形核成为细小等轴晶; (3) 混合处理,在PBF过程中引入原位轧制或超声振动处理,以外来能量输入干涉熔融金属液体的凝固过程,促进等轴晶的形核与长大; (4) 热处理,通过对成形部件进行原位热处理或者后期传统热处理,改变晶粒形态。显微组织偏析与位错胞行为的控制主要通过控制打印过程参数来实现。此外,通过在PBF过程中施加原位扰动(如电磁搅拌)也可实现对微观组织与成分偏析的控制。
来源:增材制造硕博联盟