激光沉积制造技术为航空航天等大型难加工金属构件的制造提供了可能,然而激光沉积制造过程由于较大温度梯度所产生的残余应力会导致成形构件变形甚至开裂。如何快速预测大型增材金属构件的变形是实现大型构件变形调控及高质量成形的关键。因此,本文提出了一种基于特征分区和温度函数相结合的大型增材构件变形快速预测方法。首先,在了解激光沉积制造技术原理的基础上,提出了基于典型几何特征的分区方法,建立了十字型、L型、T型和一字型四类特征分区,避免了传统分区随机性大、构件变形数值模拟前处理繁琐的问题。然后,通过数值模拟方法研究了不同起始温度、峰值温度和终止温度等参数对变形预测精度的影响规律,建立了不同特征分区的温度函数曲线,并通过实验和传统的热弹塑性法验证了变形预测的精度。该方法在保证大型增材构件变形预测精度的前提下极大提高了预测效率。 网格模型
二、影响因素分析
1. 温度函数起始温度
多次热循环是增材制造与焊接的最大差别之一,激光沉积制造过程热量不断累积,温度逐渐升高,因此需要考虑不同的层间起始温度是否会影响最终的计算结果。为了探明温度函数起始温度对变形预测精度的影响,分别设置起始温度为20℃、180℃、300℃、350℃、420℃、450℃模拟各特征分区的变形结果,并在基板背面设置沿x和y方向的变形提取路径。各特征分区在不同起始温度下,x方向和y方向的变形对比结果如图2(a)-图2(h)所示。
对比结果表明:各特征分区在不同起始温度下,x方向和y方向的变形随温度的升高逐渐减小。其原因为起始温度升高,温度梯度降低,沉积过程的热应力减小。对比十字型、T型和一字型特征分区的变形,当起始温度为300℃时,x方向的变形与传统方法预测结果吻合良好;当起始温度为180℃时,y方向的变形与传统方法预测结果吻合良好。对于L型特征分区,当起始温度分别为420℃和300℃时,x方向和y方向的变形与传统方法预测结果吻合良好。由于x方向的变形远大于y方向的变形,因此将300℃设置为十字型、T型和一字型特征分区的起始温度,将420℃设置为L型特征分区的起始温度。 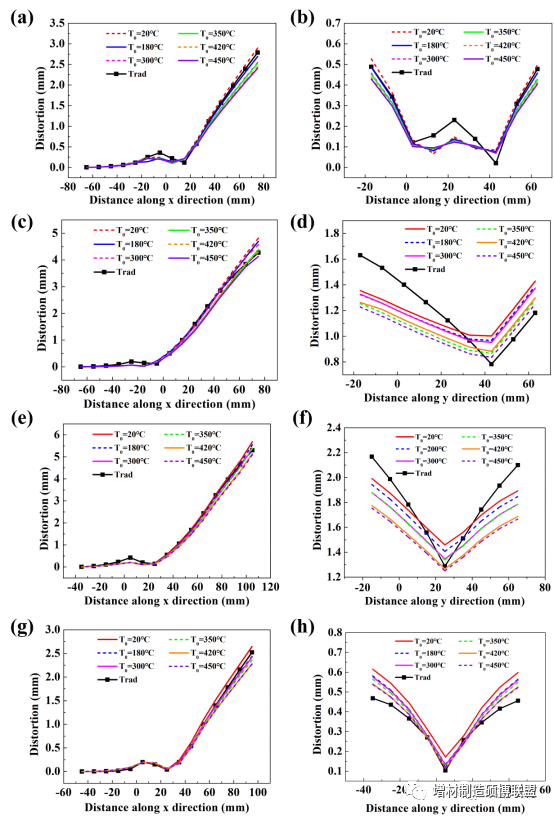
图2 起始温度对各特征基板变形的影响 (a)十字型沿x向(b)十字型沿y向(c)L型沿x向(d)L型沿y向(e)T型沿x向(f)T型沿y向(g)一字型沿x向(h)一字型沿y向 2. 温度函数峰值温度
激光沉积制造构件的塑性变形由材料所经历的峰值温度所决定。采用温度函数法预测增材构件变形时,峰值温度的取值严重影响其预测精度。为了研究不同峰值温度对变形预测的影响,分别设置1700℃、1800℃、1900℃、2000℃、2100℃作为峰值温度,利用温度函数法模拟各特征分区在x方向和y方向的变形与峰值温度的关系曲线,如图3(a)-图3(h)所示。对比结果表明:各特征分区在不同峰值温度下,x方向和y方向的变形随温度的升高逐渐减小。其原因为随着峰值温度升高,温度梯度增大,基板所产生的反变形增大,导致冷却后的基板变形减小。对比十字型、T型和一字型特征分区的变形,当峰值温度为1900℃时,x方向与y方向的变形与传统方法预测结果吻合良好。对于L型特征分区,温度函数峰值温度需在传统方法提取的基础上加以修正,当峰值温度在1950℃时, x方向和y方向的变形与传统方法预测结果吻合较好。由于x方向的变形远大于y方向的变形,因此将1900℃设置为十字型、T型和一字型特征分区的峰值温度,将1950℃设置为L型特征分区的峰值温度。 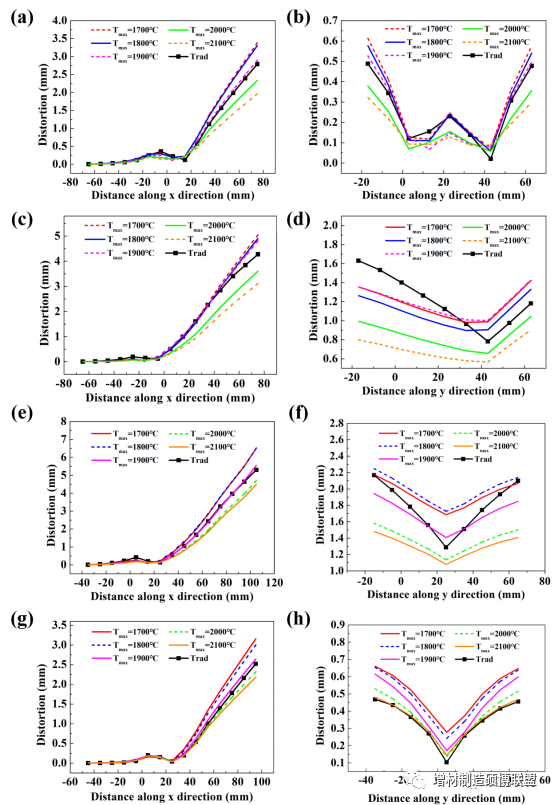
图3 峰值温度对各特征基板变形的影响 (a)十字型沿x向(b)十字型沿y向(c)L型沿x向(d)L型沿y向(e)T型沿x向(f)T型沿y向(g)一字型沿x向(h)一字型沿y向 3. 温度函数终止温度
温度函数终止温度的高低直接影响了层间温度梯度的大小,本节将起始温度与峰值温度作为定量,研究温度函数终止温度对变形预测精度的影响,分别设置终止温度为20℃、180℃、300℃、350℃、420℃、450℃模拟各特征分区的变形结果,并提取基板沿x和y方向的变形数据。各特征分区在不同终止温度下,x方向和y方向的变形对比结果如图4(a)-图4(h)所示。
对比结果表明:各特征分区在不同终止温度下,x方向和y方向的变形随温度的升高逐渐减小。其原因为终止温度升高,温度梯度降低,沉积过程的热应力减小。对比十字型、L型特征分区的变形,当终止温度为420℃时,x方向的变形与传统方法预测结果吻合良好;当终止温度为180℃时,y方向的变形与传统方法预测结果吻合良好。对于T型和一字型特征分区,当终止温度为420℃时,x方向的变形与传统方法预测结果吻合良好;当终止温度分别为350℃和450℃时,y方向的变形与传统方法预测结果吻合良好。由于x方向的变形远大于y方向的变形,因此将420℃设置为十字型、T型、L型和一字型特征分区的终止温度。 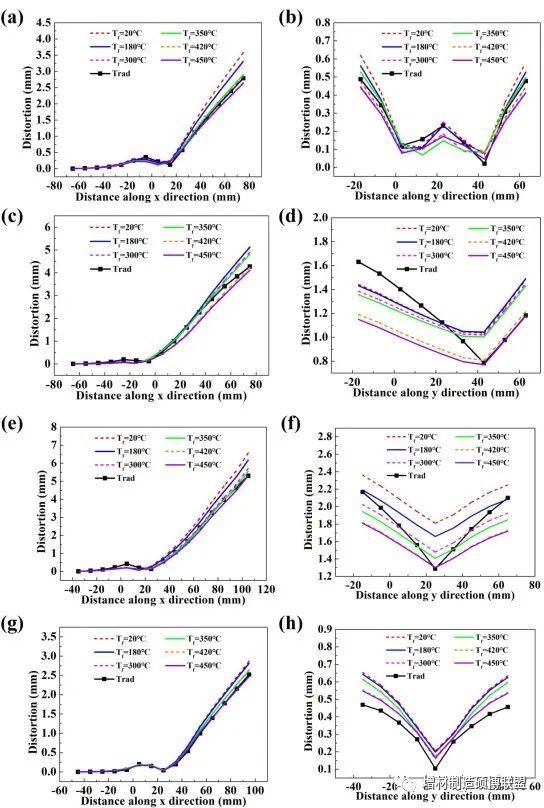
图4 终止温度对各特征基板变形的影响 (a)十字型沿x向(b)十字型沿y向(c)L型沿x向(d)L型沿y向(e)T型沿x向(f)T型沿y向(g)一字型沿x向(h)一字型沿y向 三、验证
1. 特征分区预测精度及效率
各特征分区冷却后的应力云图如图5所示。可以看出:四类特征分区应力分布趋势一致,且等效应力的幅值水平相同;最大应力均出现在基板与沉积区过渡位置,但温度函数法预测增材构件沉积区的应力稍高于传统热弹塑性法,主要是由于没有考虑扫描策略对应力的影响。此外,对于沉积层应力偏高的问题,可以通过分段成形法来离散整体应力,但分段会使模型在分段连接处产生明显的应力断点,且随着分段数的增多,会损失一定的计算效率。 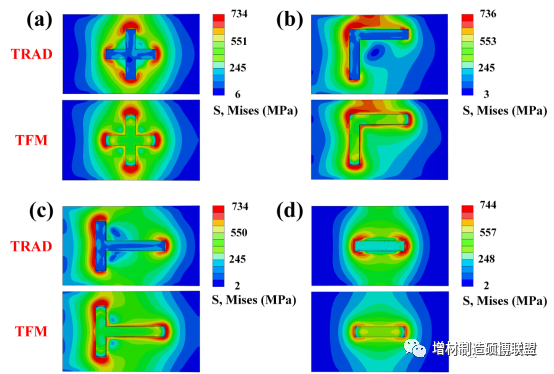
图5 不同方法预测的应力云图 (a)一字型 (b)T型 (c)L型(d)十字型 各特征分区冷却后的变形云图如图6所示。可以看出:四类特征分区不同模拟方法获得的变形趋势基本一致,且最大变形量与实验测量结果吻合;此外,由于温度函数法没有考虑扫描路径的影响,使得沉积区的局部变形稍大于传统方法预测的变形,但基板的变形两种模拟方法均与实验结果吻合较好,表明温度函数法可以准确预测激光沉积增材构件的变形,其中基板变形对比曲线如图7所示。对比结果表明:两种模拟方法所预测的基板变形结果均与实验结果吻合良好,其中温度函数法预测的各特征沿x方向基板翘曲变形与实验的误差如表1所示。在计算效率方面,对于各典型特征分区模型,不同方法的计算时间如表2所示,温度函数法可以显著减少计算时间,四种不同特征模型都可以减少95%以上的计算时间。 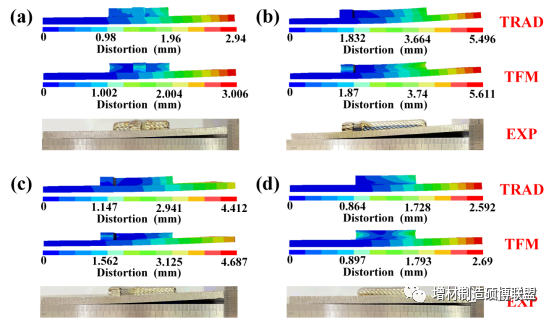
图6 实验与不同模拟方法的变形对比 (a)十字型 (b) T型 (c) L型 (d)一字型 图7 不同方法获得的基板变形曲线 (a)十字型沿x向(b)十字型沿y向(c)L型沿x向(d)L型沿y向(e)T型沿x向(f)T型沿y向(g)一字型沿x向(h)一字型沿y向 2. 大型构件预测精度及效率
为了进一步说明基于特征分区和温度函数法在激光沉积增材构件变形快速预测研究中的优势,本文选择尺寸为200mm×150mm×8mm的钛合金框类构件作为研究对象,基板尺寸选择为250mm×200mm×10mm。采用温度函数法和传统热弹塑性法模拟激光沉积制造过程中该构件的应力及变形分布。采用温度函数法和传统热弹塑性法预测该钛合金框类构件的残余应力和变形分布如图8-图10所示。由图8残余应力云图对比表明:两种分析方法预测增材构件的残余应力分布趋势一致,最大应力出现区域一致,且等效应力的幅值水平相同。由图9和图10增材构件的变形对比可知:基于特征所修正的温度函数法可以准确预测大型增材构件变形,且最大变形误差为9.57%。在计算效率方面,温度函数法计算用时为42.68h,而传统方法需要1309.29h。基于特征分区的温度函数法极大的提高增材构件的变形预测效率,为大型增材构件的变形快速预测提供了有效途径。 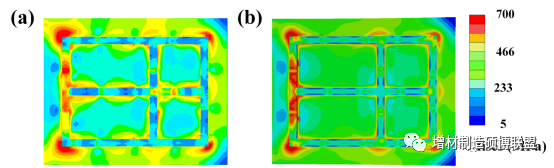
图8 典型框梁预测应力云图 (a)热弹塑性法应力云图 (b) 温度函数法应力云图 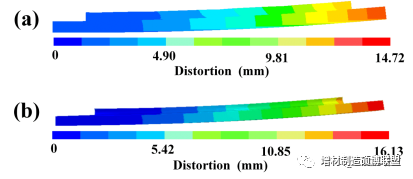
图9 典型框梁预测变形云图 (a) 热弹塑性法变形云图 (b) 温度函数法变形云图
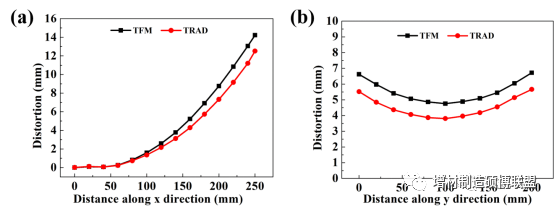
图10不同预测方法基板变形曲线 (a)沿x方向变形曲线 (b) 沿y方向变形曲线 四、结论
在本研究中,针对航空航天大型钛合金框梁构件,提出了基于典型几何特征的分区方法,将各分区归类为十字型、L型、T型和一字型四类典型特征分区。首先,通过传统的热-力学有限元模型,分析了峰值温度在层内和层间的分布规律,确定了温度函数的提取及添加方法;其次,系统地研究了温度函数关键参数对变形预测精度的影响,确定了各特征分区的最优温度函数曲线;最后,利用修正的温度函数法对各特征模型和大型框梁构件的变形及残余应力进行预测,并与传统方法预测结果及实验测量结果进行对比。对比结果表明:基于特征分区的温度函数法能够在满足预测精度的前提下(最大变形误差均小于10%),极大的提高计算效率(计算时间减少了96%),为大型增材构件的变形预测提供了一种新方法。
来源:增材制造硕博联盟