2013年,在美国的TED会议上,麻省理工学院的Tibbits首次提出4D打印概念,并展示了一根绳子在水中转变为“MIT”立体字样的过程,4D打印技术自此在学术界掀起了广泛的研究热潮。从此,增材制造技术便由原来的点线面体空间维度(3D)扩展到了时空维度(4D)。 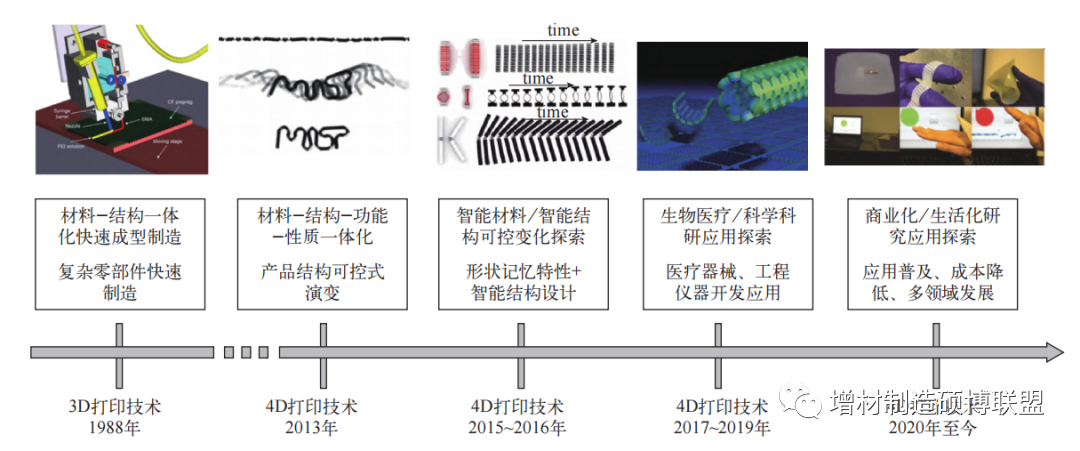
4D打印发展历程及技术特点(来源:冯韬等,《4D打印智能材料及产品应用研究进展》) 4D打印技术的诞生可追溯至2007年美国国防高级研究计划局(DARPA)开展的“可编程物质”项目研究,该项目旨开发出一种可在软件控制或外界刺 激的条件下转变成理想或有用形态的智能材料,实现根据需求在现场快速制造物资,并使军事装备能够根据指令改变形状。DARPA设想中的可编程物质是一种智能材料,包含驱动及传感机制,可以在软件控制或者外界条件的刺 激下变形成为有用的形状。可编程物质的设想应用包括三维实体显示、可变形天线、可重构电子设备以及多功能现场制造设备等。 DARPA计划从模块化机器人、新型材料、纳米技术、微机电系统等多个领域对可编程材料开展研究,共有包含麻省理工学院在内的5所大学的研究团队参与该项研究。麻省理工学院研究团队在此项目支持下开发出可编程物质执行机构,能够根据温度的变化展开或折叠,并以此为基础制造出可自动折叠成飞机或舰船形状的机器人。 此后,麻省理工学院在DARPA的资助下继续开展一系列可编程物质方向的研究,并于2011年建立了自组装实验室,最终促成4D打印技术的问世。
4D打印其实是在3D打印技术的基础上,增加了一个时间维度,通过可编程原理控制3D打印物体中的可变形要素,成型后物体的形状、性能等在受到光、热声、磁等环境刺 激下可随时间再次发生变化,实现自动形变、自动修复、自动组装等功能,因此4D打印成为一种新型的以智能材料为驱动的变形实现技术。 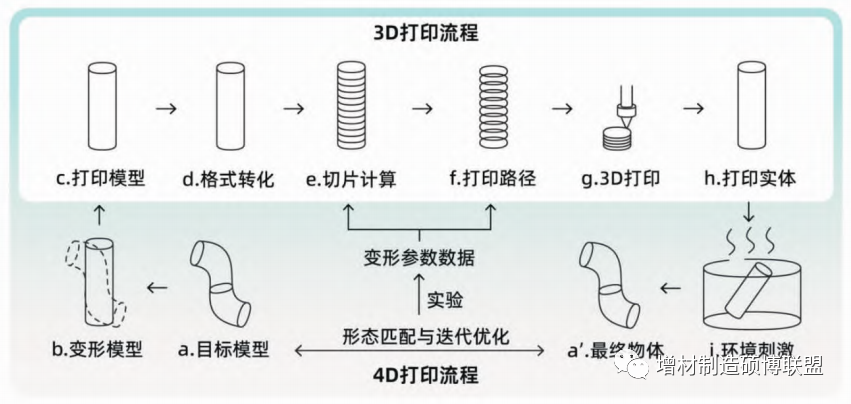
3D打印与4D打印的技术关联性(来源:王冠云等,《4D打印变形设计策略研究》) 与3D打印相同,4D打印是一种集材料科学、机械科学以及计算机科学等诸多学科高度交叉融合的先进制造技术。但又与3D打印不同,4D打印是一种具备动态演变能力的智能制造技术,是在3D打印基础上结合智能材料与智能结构设计,针对制造产品的形态、性能和功能方面的进一步发展。 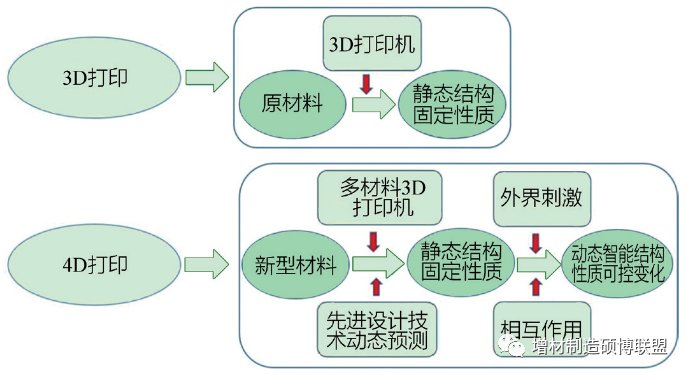
3D打印与4D打印技术的区别对比(来源:军事文摘,《4D打印技术及其军事应用前景》) 4D打印作为新一代增材制造技术,其依赖于时间,独立于制造设备,并且其演变过程完全可预测、可设计和可控制。4D打印的先进性在于可以快速成型制造出具有环境自适应性动态演变的智能产品,从而区别于传统3D打印产品的功能单一、无变化的稳态特性。针对悬空、螺旋和中空等曲边曲面复杂结构,4D打印可以先快速成型制造出相应简单结构后,再由智能演变实现最终的产品形态和性质,从而达到减少加工时间和材料的目的。此外,4D打印直接将产品的“功能性”与产品的制造工艺相结合,在保留材料特殊性质的同时将其快速成型制造,从而实现智能产品的一体化成型制造。 要实现4D打印技术有四个关键要素,分别为智能材料、3D打印、数学建模与刺 激条件。 常见的智能材料包含形状记忆合金、形状记忆聚合物、光驱动型聚合物、水驱动型智能材料、磁驱动型智能材料、电驱动智能材料等,如Ni-Ti合金通过有机胶和溶剂粘合作用打印出的金属结构即有一定的形状记忆效应,其在低温下发生的形变可以通过加热升温恢复其原有形状;形状记忆聚合物是在4D打印技术研究中应用最多的材料,例如通过熔融成型方式获得可抓取螺丝钉的机械手、能够舒展的花瓣模型、可以折叠的纸盒以及飞鸟模型等。 4D打印通过对智能材料的数学建模可以实现多种材料的打印,借助多种材料的相互作用使得制品展现结构功能的转化,将多种材料的3D打印短板转化为优势,扩展了设计思路;且4D打印制品自我修复与自我组装特点能够将大型制品初始打印小型化,克服了3D打印设备能力与空间体积的限制。
3D打印技术是4D打印技术的制造基础,是将4D变形设计实体化的重要过程。比较常见的可用于4D打印的3D打印技术包括熔融沉积式、挤压喷墨式、烧结与固化式。 熔融沉积成型技术是将各种热熔性线状材料加热融化、打印粘连、再冷却成型,例如常见的可熔融沉积打印的热塑性塑料(PLA、ABS、PCL等)。该种技术打印简单、材料易得,因此成为近年来发展较快的低成本4D打印技术。 挤压喷墨成型技术包括半液态材料的挤压成型和液态墨水的喷墨成型,其特点在于在打印过程中不改变材料物理状态,但由于每种材料物理差异性较大,3D打印机通常需要定制化,因此该种技术在4D打印领域并未获得广泛应用。 烧结与固化成型技术包括粉末烧结固化和紫外线光固化,其打印特点在于依靠粉末状或液态材料自身的支撑作用,可制造悬空、层叠等复杂的立体造型。但该技术打印成本相对较高,因此在4D打印领域获得广泛应用。 无论传统的制造业还是3D打印,其造物过程一般是先模拟、后制造,或者一边建物,一边调整模拟效果。由于4D打印结构体具有基于时间变化的特性,设计和制作流程中存在一个或多个中间形态。 传统的3D打印技术,可以通过专业扫描仪或者DIY扫描设备获取对象的3D数据,也可以使用3D制作软件从零开始建立三维数字化模型。不同于3D打印先建模、后生产的制造流程,4D打印由于其能够变化的特性,在数字化建模之初,就将材料的触发介质、时间等变形因素,以及其它相关数字化参数预先植入打印材料中。 Gladman等人认为,4D打印过程中需要适当的数学模型的支持。在该过程中存在的数学问题包括:如何预测结构体基于时间的形态变化过程,包括变化后的形态;如何提供避免自组装行为过程中组件发生碰撞的理论模型;如何减少自组装过程中的试错性行为。这些需要考虑的数学问题,必须通过智能化的计算芯片加以判断、解决。 刺 激条件是驱动4D打印物体发生形变的触发器,需针对材料进行选择。常见的刺 激条件包括热刺 激、水刺 激、光 刺 激、电刺 激、磁刺 激等。 热刺 激4D打印技术主要基于热敏型聚合物作为打印材料。形状记忆功能源于分子链组成单元的玻璃化转变或熔融转变和马氏体正逆相变。热刺 激4D打印技术的驱动过程如下:首先3D打印出具有初始形状的组件,当组件温度高于聚合物的玻璃化转变温度时,将组件从初始形状调整为临时形状,保持临时形状并将其冷却至玻璃化转变温度以下,以使临时形状稳定;当再次加热至玻璃化转变温度以上时,组件可恢复为初始形状,实现形状记忆功能。在实际应用中,还可以使用具有不同玻璃化转变温度的材料控制部件的局部变形。 水刺 激4D打印的材料通常以亲水性材料作为基质,其与水分子结合时体积发生变化,进而产生形变。由于水环境往往属于全局刺 激,因此,实现水刺 激4D打印需要考虑的主要问题是制备具有水环境中溶胀各向异性的打印材料,使变形的方向得到准确控制。水刺 激4D打印技术往往可以实现很大程度的变形,且打印材料相对容易制造,不需要复杂的打印设备,因此在医疗康复、水下设备等领域有着很大的应用价值。 光刺 激4D打印的材料通常是由光敏型形状记忆聚合物构成,可通过吸收光波能量转化为热量,进而引发形状记忆效应。与热刺 激4D打印技术相比,光刺 激由于便于能量聚焦具有更高的灵活性和区域性,可有选择地对局部或整体实施光照产生驱动。此外,光刺 激4D打印技术更便于实现远程控制,多用于二维记忆材料的自动展开和折叠动作设计。 电刺 激4D打印可分为直接电刺 激和电热刺 激。直接电刺 激利用材料的逆压电效应,也称电致伸缩效应。当材料被施加电场时,晶体被激发产生振动,从而使材料产生机械变形,去除电场后,材料恢复原状;电热刺 激要素是利用电流的电阻发热效应使材料产生变形,其本质仍为热刺 激要素。电刺 激的优势在于可以实现4D打印的内部控制,将电热材料嵌入到热敏材料内部,可实现材料内部的局部变形控制。此外,此类刺 激方式可排除环境温度的影响,比如可以实现在寒冷等特殊工作环境下的行为控制。 磁刺 激4D打印通过在聚合物中区域性地添加磁性颗粒,利用外部磁场实现变形控制。由于磁力的非接触特性,磁刺 激的4D打印技术对环境的依赖性小,可以实现“远程控制”。已有研究表明,由于磁场可以实现快速变化,因此磁刺 激的变形界面组件通常具有更快的响应速度。磁刺 激要素同样可分为直接响应和间接响应两种实现方式。直接响应是使用混合有磁性颗粒的基质3D打印成初始形状,当其置于磁场中时,基体中的磁性颗粒的磁场会对施加的磁场做出响应,从而实现变形。众所周知,磁性本身就具有良好的记忆功能,尤其是具有较大的矫顽力和饱和磁化强度的永磁材料,可使4D打印产品具有更长的使用寿命和更大的变形响应,而且磁性材料大多具有较高的各向异性,有利于控制4D打印变形的方向;间接响应法是基于磁性颗粒在磁场中的磁热效应,当磁性颗粒被施加交变磁场时,由于磁畴的运动会产生热量,进而驱动元件,该方法的本质属于热刺 激要素。 由于陶瓷有熔点高的特性,因此难以用传统的激光打印方法来制造陶瓷。而现在用3D打印的陶瓷前驱体通常难以变形,因此阻碍了一些形状复杂陶瓷的生产。 2018年,香港城市大学吕坚教授研究组全球首次实现了陶瓷的4D打印。吕坚教授研究组从材料出发,开发了不同系统的硅胶基质纳米复合弹性体材料作为陶瓷前驱体。这些弹性体材料的特性使其可以完成从3D打印到变形的过程,并且最终转变为陶瓷结构,从而逐步实现打印陶瓷折纸结构和4D打印陶瓷。 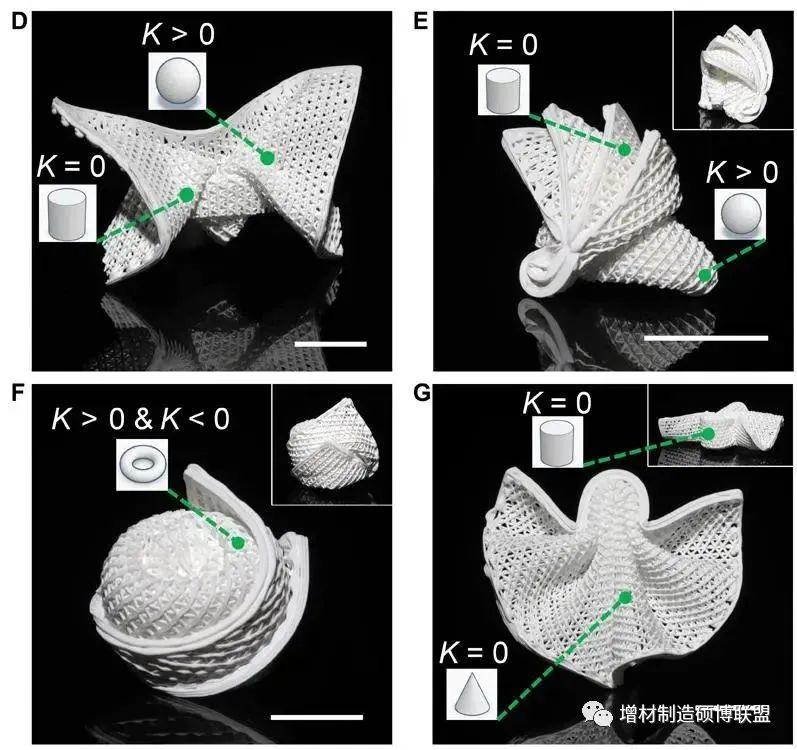
通过陶瓷折纸打印获得的结构(来源:Liu, Guo, et al.《Origami and 4D printing of elastomer-derived ceramic structures》) 在陶瓷折纸打印技术基础上,研发团队将陶瓷折纸技术中手动的步骤进行数字化和自动化,进一步实现了陶瓷的4D打印。这一过程可以通过多种方法实现。 第一种方法是通过拉伸机对前驱体进行拉伸,并在拉伸后的基底上打印连接点,再将另一个打印好的拓扑结构进行固定。当拉伸机解除作用于基底的应力后,拓扑结构发生屈曲变形,再由热处理后进而形成4D打印的陶瓷结构。 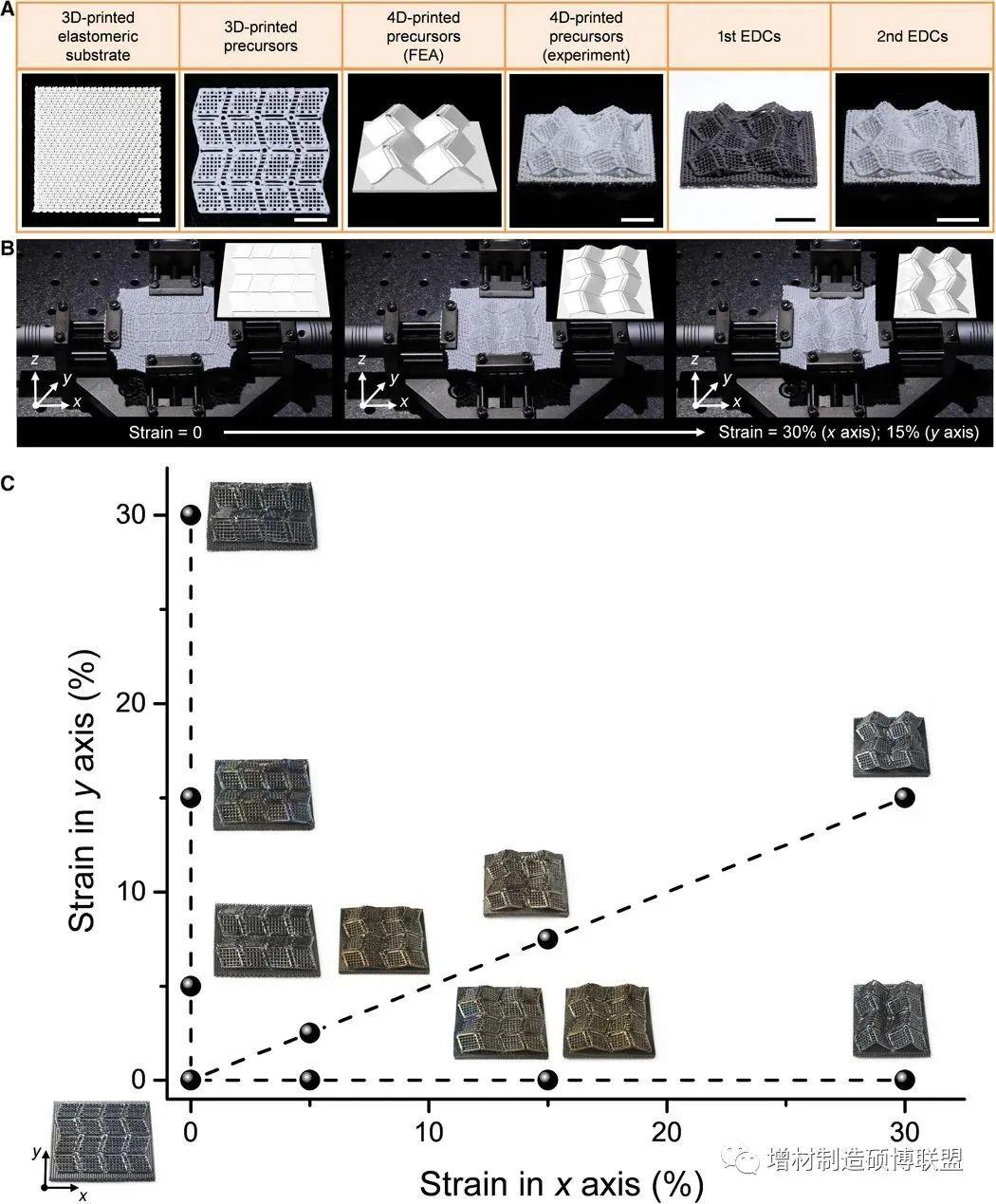
方法一(来源:Liu, Guo, et al.《Origami and 4D printing of elastomer-derived ceramic structures》) 第二种方法是通过将陶瓷前驱体按照设计好的纹路打印在预拉伸的陶瓷前驱体上,在预应力被释放时,就会发生4D变形。通过设计在预拉伸表面打印的路径可以控制应力释放后的4D变形。文中以几个有代表性的拓扑结构作为例子,展示了弯曲,螺旋和马鞍面的打印过程。 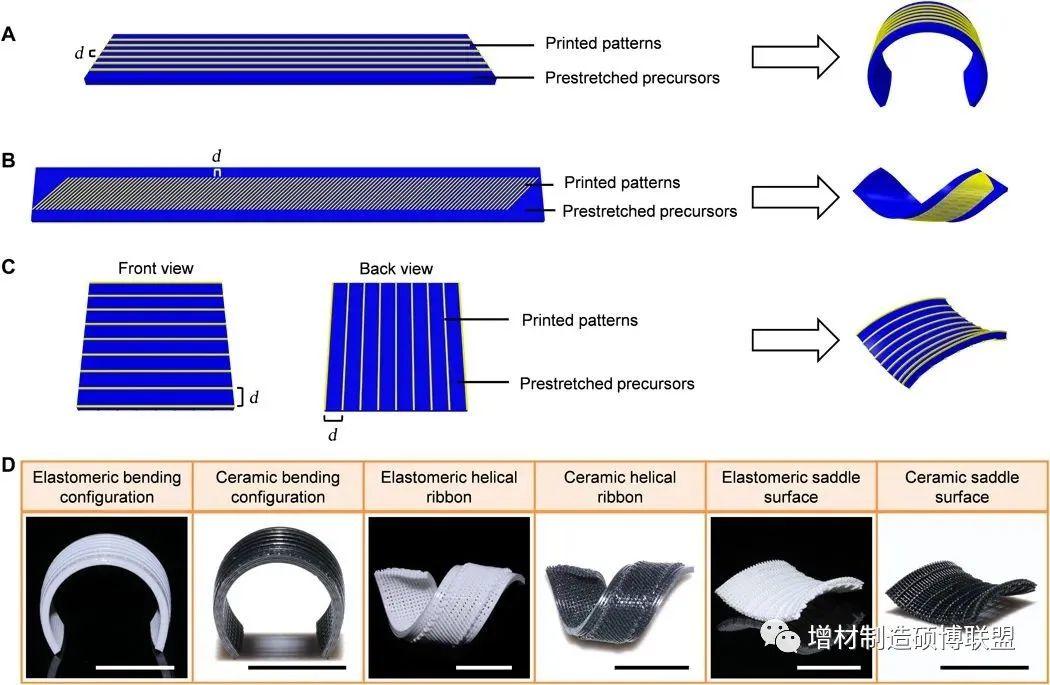
方法二(来源:Liu, Guo, et al.《Origami and 4D printing of elastomer-derived ceramic structures》) 相关研究工作以“Origami and 4D printing of elastomer-derived ceramics”为题发表在《Science Advances》上。 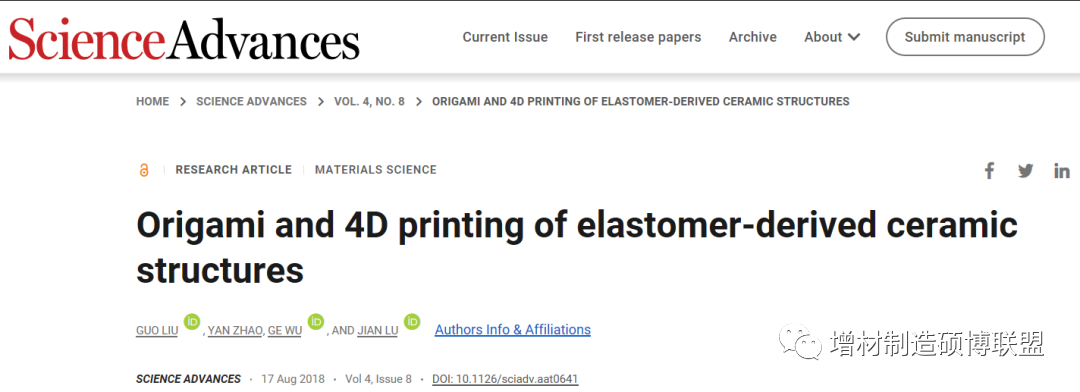
在此工作的基础上,同时受中国传统陶艺启发,吕坚教授研究组利用陶瓷前驱体材料的易加工性,集成陶瓷4D打印系统与减材制造、异质工程、表面工程等技术,提出了4D增减材复合制造陶瓷的新概念。相关研究成果于2023年7月30日以“4D additive–subtractive manufacturing of shape memory ceramics”为题发表在国际著名期刊《Advanced Materials》上。 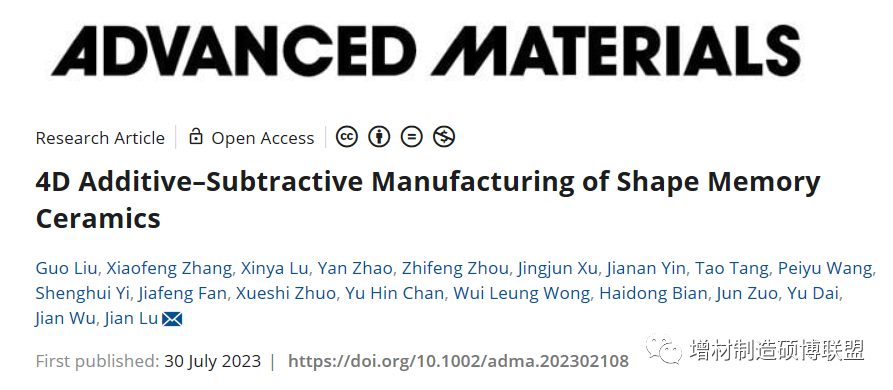
该工作首次实现了4D增减材复合制造陶瓷,亦首次实现了4D打印形状记忆陶瓷。该工作提出的4D增减材复合制造形状记忆陶瓷技术可实现高精度(十微米级),大尺寸(十厘米级),超快的前驱体转变为陶瓷的速度(几秒钟内),以及前驱体材料的快速制造(批量生产能力),有力推动了陶瓷4D打印技术的潜在应用发展,有望应用于航空航天(全陶瓷整体涡轮叶盘、可变形热防护系统,太空折叠系统,在轨制造和修复,原位太空打印和殖民等)、3C电子(可折叠陶瓷手机背板、微机电系统等)、生物医疗(生物植入物等)、和艺术(文物研究和修复、首饰、装饰品等)等领域。 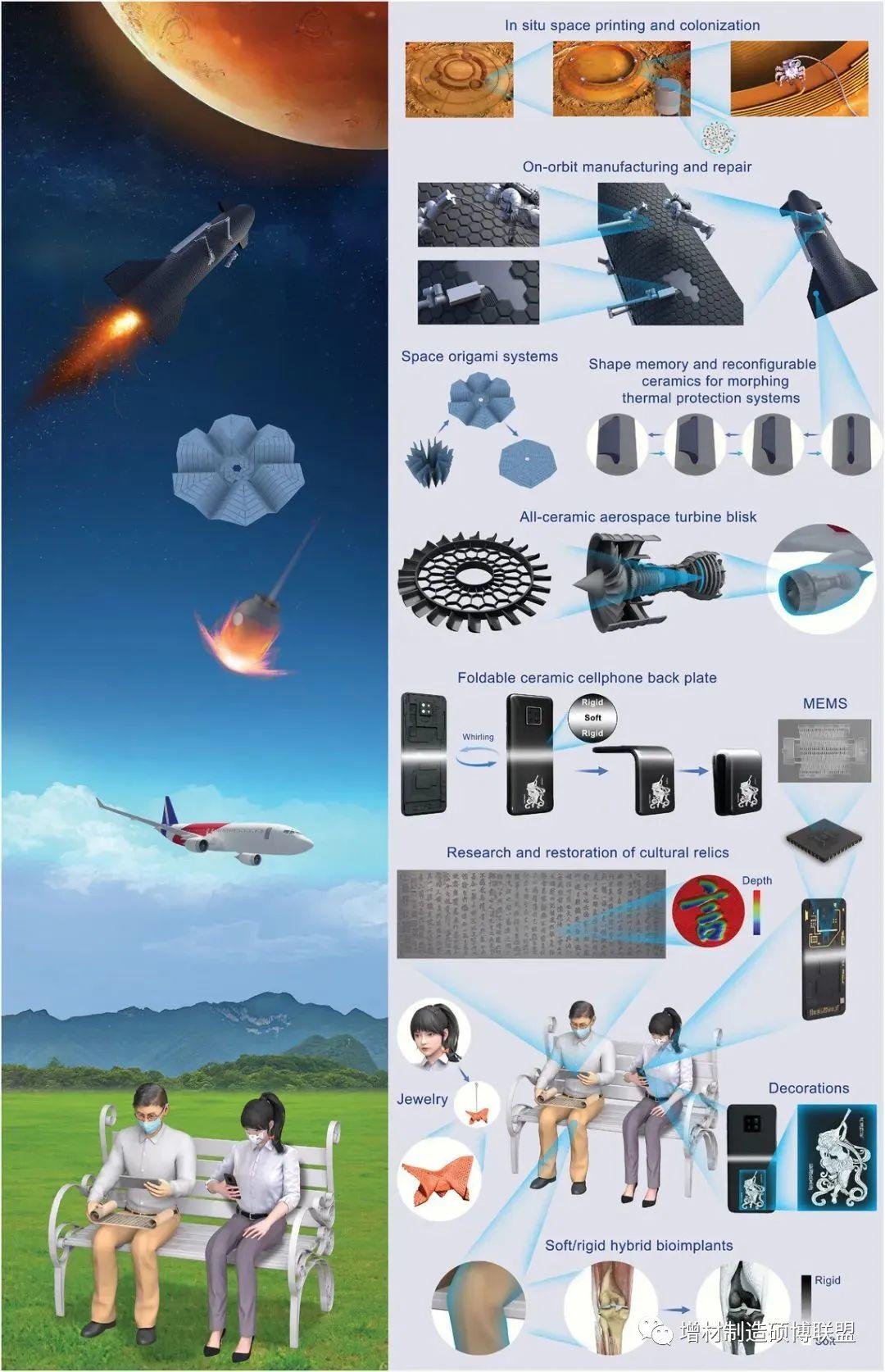
(来源:Liu, Guo, et al.《4D additive–subtractive manufacturing of shape memory ceramics》)