空气悬架压缩机振动噪声优化
摘要:以某SUV为研究对象,分析了该车空压机工作时车内产生严重的低频噪声的原因;通过传递路径分析,对空压机位置、空压机支架模态、空压机支架衬套刚度进行优化;针对各优化措施,进行了方案试制,并实车验证,最终优化了空气悬架压缩机振动噪声。随着汽车行业的发展,人们对车辆的安全性和舒适性要求越来越高,目前行业内较先进的车型均配备空气悬架,在车辆行驶时能够获得良好的平顺性和道路通过性。但是在空气悬架工作时,压缩机会持续工作给存储器罐充气,在此过程中,空气压缩机本体产生连续振动,激起车身振动,产生车内噪声,严重时会让人无法接受,这是空气悬架的一项重要NVH问题。1 空气压缩机产生噪声的原理
1.1 空气压缩机结构介绍
空气悬架系统,主要是由空气弹簧、控制阀门、车高传感器、压缩机、ECU 等构成的车高调整系统。根据ECU提供的控制指令,来控制压缩机与各个阀门,通过吸入与排出空气悬架内的空气来调整车辆的高度。空气压缩机是以总成形式安装在车身上,如图1所示,物理模型可简化为图2的简化图,压缩机本体用螺栓固定在内支架上,内支架与外支架通过减振弹簧总成连接,外支架用螺栓或弹性元件固定在车身上。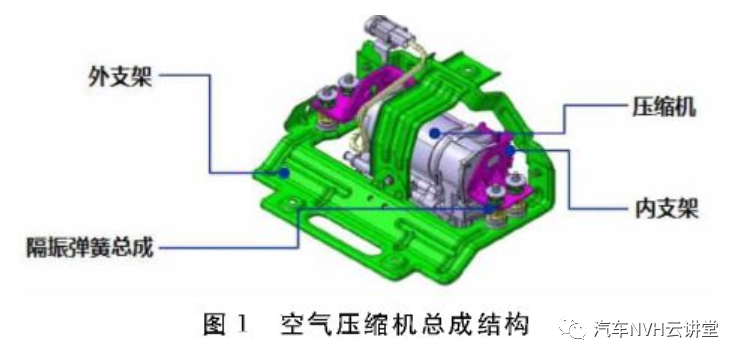
压缩机的作用为干燥压缩空气,吸收经过压缩机的空气中的水分;内支架的作用为固定压缩机,连接到外支架上;减振弹簧总成的作用为连接内支架与外支架,缓冲压缩机启动工作时的大位移冲击;外支架的作用为固定压缩机总成,将压缩机总成固定到车身上。1.2 空压机噪声机理分析
空压机是利用其内部的活塞在汽缸中的往复运动来压缩空气的,在这个运动的过程中,活塞与空气摩擦能激发物体振动并发声,此外活塞与一些附属的机械结构连接,产生机械振动和噪声,因此,空压机在工作时,不仅产生振动,还会发出噪声。空压机产生的噪声通过空气传播,进入车辆内部,这部分噪声称为空气噪声。压缩机产生的振动,在经过压缩机内支架、弹簧总成、外支架后,传递到车身,激起车身的振动并产生噪声,这部分噪声称为结构噪声。因此,空压机引起的车内噪声可表达为公式。其中,P为空压机工作时产生的车内噪声,Ps为结构噪声,Pa为空气噪声,Hs为车辆振动传递函数,Ha为车辆空气传递函数。因此,改善空压机工作时产生的噪声,主要从两方面考虑,一方面改善压缩机本体激励,主要是其自身的噪声和振动水平;另一方面是优化从压缩机到车内的传递路径。笔者主要研究的是500Hz以内的结构噪声,具有一定的项目背景,空压机和车身在问题出现时已经不能进行设计变更,因此,车辆的振动传递函数优化成为主要措施。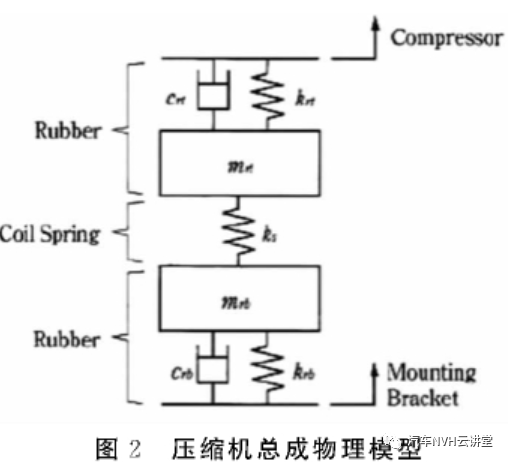
压缩机总成可简化成图2所示的物理模型,从图中可知,优化空压机振动的传递路径,可从以下几个方面考虑:①相连结构间的连接属性,即刚度阻尼特性;②关键结构的质量。2 空压机原始状态振动噪声分析
对文中所研究的SUV进行测试,其500Hz内的噪声进行分析,发现其车内噪声频谱呈阶次特性,如图3所示,在117Hz处车内产生最大噪声峰值,20Hz~500Hz噪声RMS值48.6dB(A)。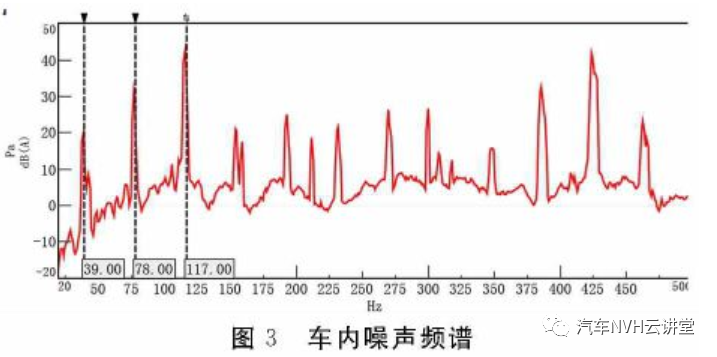
空压机端振动信号如图4所示,由于空压机电机的振动主要因其内部转子旋转振动引起,所以其频谱呈阶次特性,空压机主阶次各振动与车内噪声频谱特性对应,因此,可以判断车内的噪声峰值是由空压机振动传递到车身引起的结构噪声。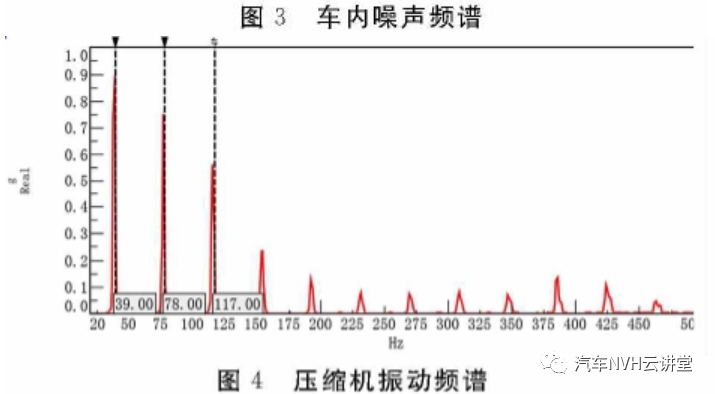
将空压机本体振动作为主动端振动,车身端振动作为被动端振动,计算主被动端隔振率,有较多的主阶次隔振率未达到20dB的参考标准,说明空压机的本体振动未经衰减,就传递到了车身响应端,是引起车内结构声的主要原因。3 空压机振动噪声优化
如前文所述,笔者所研究的内容是基于实际产品开发过程产生的,所以要考虑实际项目中的众多因素,空压机的振动噪声优化主要考虑在传递路径的优化,制定了针对性的实际措施,并予以实车试验验证。3.1 布置位置优化
空压机总成通过外支架与车身连接,因此,车身端与外支架的连接点处的动刚度会影响振动的传递,动刚度越高,振动传递越小,通过锤击试验对车身各连接点进行动刚度测试。SUV外支架与车身有3个连接点,各连接点50Hz~500Hz动刚度有效值如表1所列。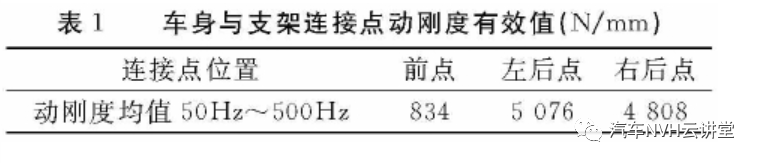
车身与支架前连接点动刚度为834N/mm,远低于8 000N/mm的参考值,应对前连接点动刚度进行优化,经研究,前连接点离车身一根纵梁较近,此横梁动刚度经测量可达到8 000N/mm,因此考虑将空压机布置位置进行优化,将空压机外支架形状重新设计,前连接点延伸至车身横梁。对原空压机外支架进行模态分析,其一阶模态为115Hz,与空压机的第三节主阶次117Hz较接近,因此在空压机外支架形状重新设计时,考虑对其进行加强,并将前连接点变为两个,如图5所示,经过CAE分析优化,新的空压机外支架一阶模态达到125Hz。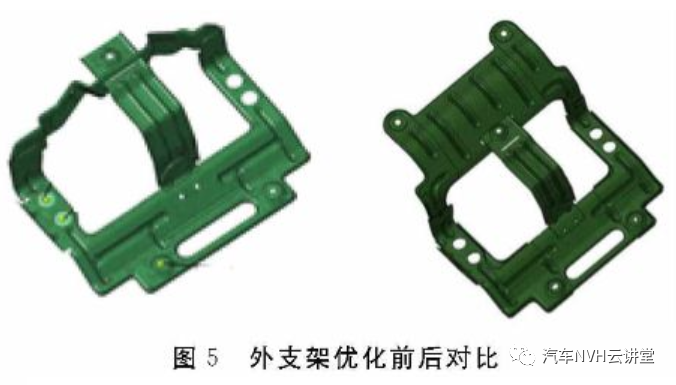
外支架优化后,其车内噪声频谱如图6所示,78Hz及117Hz处噪声频率发生峰值明显降低,20Hz~500Hz噪声RMS值由48.6dB(A)降低到47.1dB(A)。
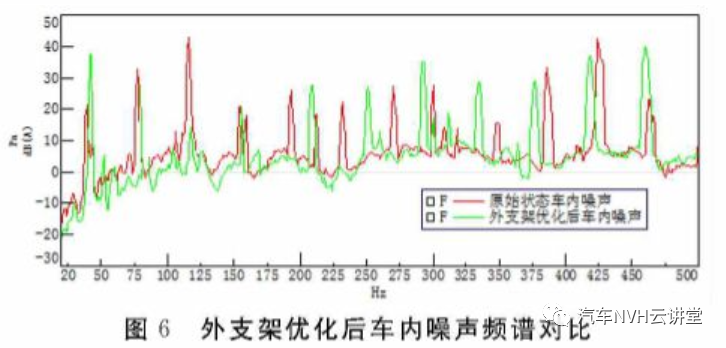
3.2 隔振特性优化
此SUV的空压机外支架与车身通过螺栓连接,空压机总成的振动会直接传递到车身上,采取增加橡胶元件的措施,可衰减压缩机总成传递到车身的振动,在已优化的4点连接支架基础上,增加橡胶衬套,如图7所示。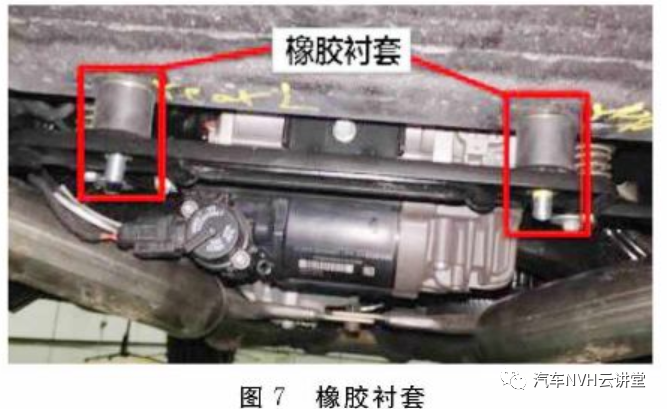
将空压机总成视为一个质量总成,其外支架与车身连接点的振动作为对车辆的激励输入,车身端的振动作为相应,要求其主、被动端隔振率达到25dB,建立优化模型,经多体优化分析,确定橡胶衬套的刚度,试制的橡胶衬套样件经台架试验测量,其刚度结果,如表2所示。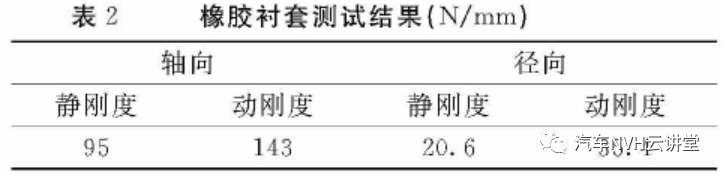
安装橡胶衬套后,对车辆进行测试,车内噪声频谱与安装橡胶衬套前对比如图8所示,100Hz内低频噪声峰值降低,150Hz以上各噪声峰值均明显降低,20Hz~500Hz噪声RMS值由47.1dB(A)降低到41.4dB(A)。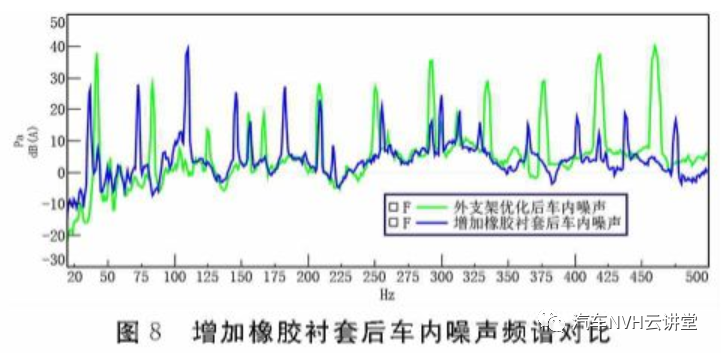
3.3 关键质量布置优化
根据工程实际经验,增加质量会产生抑制振动的效果,经过实车研究,发现车辆的电瓶位置可移动至空压机与车身的后连接点,并不会产生较大的设计变更。对变更后的车辆进行噪声测试,其车内噪声频谱与变更前又发生了较大变化,如图9所示,350Hz以内的各噪声峰值均降低,350Hz以上噪声的噪声曲线有略微升高,20Hz~500Hz噪声RMS值由41.4dB(A)降低到39.2dB(A)。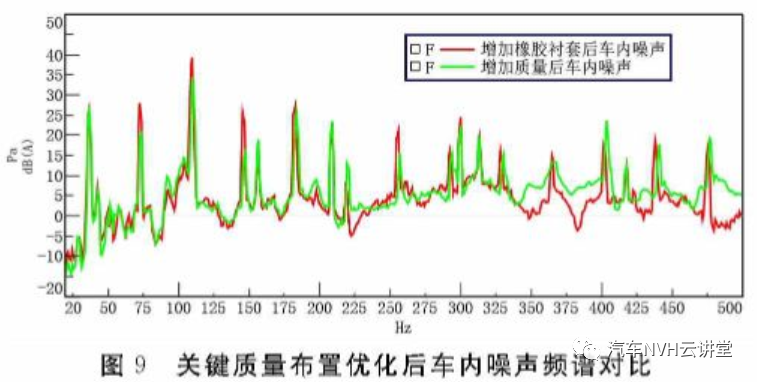
3.4 优化结果总结
通过3.1~3.3的各方案的优化,空压机引起的车内噪声由48.6dB(A)降低到39.2dB(A),车内测点优化前后的1/3倍频程对比,如图10所示,经过优化后低频段的车内噪声明显降低。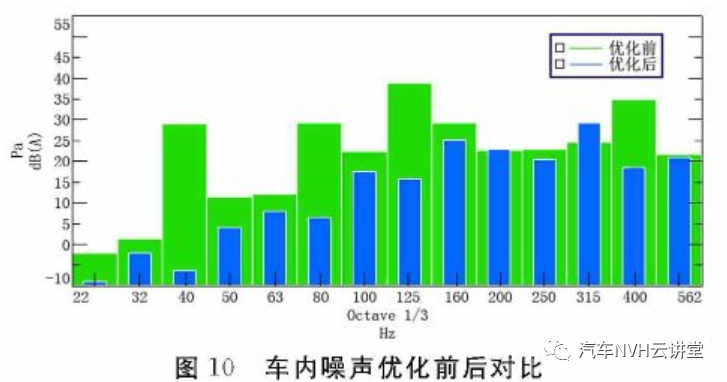
经过优化后,空压机主动端与车身被动端的主阶次隔振率达到25dB。4 总结
通过对空压机的结构及工作原理的研究,分析了压缩机产生的振动及噪声原因,基于实际产品问题,对可行的优化方案进行研究,对压缩机布置位置、外支架模态、连接点衬套隔振特性以及关键质量位置进行优化,有效地改善了压缩机引起的车内噪声,其工作时引起的结构噪声由最初的48.6dB(A)降低到39.2dB(A)。作者:刘 涛,杨树凯
中国第一汽车集团有限公司
著作权归作者所有,欢迎分享,未经许可,不得转载
首次发布时间:2023-12-18
最近编辑:1年前