电弧熔丝增材制造(WAAM)已成为装备制造领域的重要发展方向之一,通过电弧加热熔化金属丝材,可在预设路径上逐层叠加堆积完成三维实体金属构件的增材制造成形,具有效率高且成本低的优点,尤其适合大尺寸铝合金构件的一体化增材制造成形。但由于铝合金固有的冶金行为特征,电弧熔丝增材制造中易出现冶金缺陷,如气孔、裂纹等问题,较大程度限制了产品力学性能的进一步提升,也严重制约了铝合金电弧熔丝增材制造技术的高效高质量发展。本文主要综述了电弧熔丝增材制造铝合金的气孔、裂纹等冶金缺陷问题,总结了缺陷形成机理、影响因素和抑制措施等方面的研究进展,并对铝合金电弧熔丝增材制造技术的未来发展方向进行了展望。 绿色、高效、智能制造是装备制造领域的发展方向,也是我国“制造强国”战略的发展要求。增材制造(Additive manufacturing, AM)的设计思路及制造流程完全不同于传统等材、减材制造,能够通过材料逐层累积实现低成本、高效率的三维成形。电弧熔丝增材制造(Wire arc additive manufacturing, WAAM)是近年来发展最为迅速的增材制造技术之一,也被世界发达国家视为一场崭新的技术革命。电弧增材是通过电弧加热熔化金属丝材,结合机器人系统和计算机控制,在预设路径上逐层叠加堆积完成三维实体金属构件的增材制造成形,具有效率高且成本低的优点,尤其适合大尺寸铝合金构件的一体化增材制造成形。 铝合金具有比强度高、质量轻、耐蚀性好的特点,作为轻质高强结构材料在汽车、船舶、航空航天等领域有着广阔的应用前景。由于铝合金对激光能量的吸收率低,以及电子束真空加工易使铝合金挥发,因此这两种方式用于铝合金增材制造有着一定的局限性。电弧增材因其效率高、成本低的特点,特别适合大型复杂铝合金结构件的增材制造。在复杂及薄壁构件的轻量化制造中,铝合金电弧增材制造优势突出,也引起了国内外学者的广泛关注,开展了大量的铝合金电弧增材制造技术的应用研究,并试制了多种类型的铝合金零件,如图1所示。 图1 电弧增材制造的铝合金零件(a) 沉积态框梁;(b) 机加工后框梁;(c) 筒体;(d) 半球
电弧增材制造技术是在传统电弧熔丝焊接方法的基础上发展而来,铝合金电弧焊接中的冶金缺陷也同样会在电弧增材制造中出现,由于铝合金自身材料的特性以及电弧增材制造工艺的特点,电弧增材的铝合金存在气孔、裂纹等冶金缺陷,难以满足铝合金构件的性能要求,也限制了铝合金电弧增材制造的发展和应用。
由于电弧增材制造的热输入具有循环特性及局部不均匀特征,同时其冶金过程、缺陷形成机理及构件力学性能与传统制造工艺有着较大区别,需要引起格外关注并进行深入研究。为了推动铝合金增材制造技术的高效高质量发展,解决电弧增材制造中的冶金缺陷问题,国内外学者进行了大量的相关研究并取得了显著成果。 本文对铝合金电弧增材制造的冶金缺陷(如气孔、裂纹等)的研究成果进行了梳理和总结,重点阐述了缺陷形成机理、影响规律和抑制措施等方面的研究进展,旨在推动铝合金电弧熔丝增材制造的进一步发展。尽管电弧增材制造铝合金具有较多优点,但目前为止,气孔仍是增材制造铝合金的常见缺陷,会对构件的力学性能产生重要影响,往往成为构件的裂纹源,严重降低构件的承载能力和疲劳极限。 电弧增材制造铝合金的气孔缺陷主要分为氢气孔和凝固气孔这两种类型。氢原子在液态铝和固态铝中的溶解度差别较大。液态铝中氢的溶解度(0.69 mL/100 g)是固态铝中氢溶解度(0.036 mL/100 g)的将近20倍,如图2所示,这种较大的溶解度差异是造成电弧增材制造铝合金出现氢气孔的主要原因。即使液态铝中含有微量的氢,但凝固后也很容易超出固态铝中的溶解极限,导致形成大量气孔。也有研究学者根据气体来源不同,将气孔分为原材料引入类型和工艺过程引入类型。 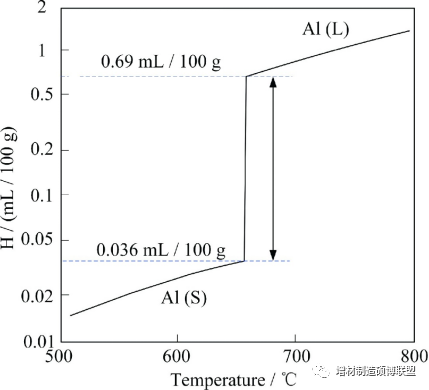
图2 氢在铝中的溶解度
电弧增材是一个快速冷却凝固的过程,在冷却过程中,氢原子的溶解度急剧下降,在固/液界面前沿,氢原子从铝合金固相中析出进入液相,当氢含量到达了其溶解度的极限时,便会以气泡的方式析出,如气泡来不及排出,则在凝固过程中形成氢气孔。在凝固过程中,由于固态铝合金密度大于液态铝合金密度,密度差异使得铝合金在凝固时发生收缩,液态金属无法及时填充收缩部位,便会形成收缩气孔,也称作凝固气孔。
保护气体种类、纯度、水分及流量对气孔都有着较大影响,保护气体中的水分会增大气孔形成的几率,同时气体的流量也会影响气孔的形成,气体流量主要通过改变熔滴过渡形式及熔池形态来影响气孔形成。与纯氩气相比,氩气与氦气的混合保护气体能够降低气孔率,当氦气含量提高到70%时气孔明显减少,再进一步添加CO2时气孔可进一步减少,但是当CO2含量达到3%以上时气孔又显著增加。氦气作为保护气,与氩气相比其质量较轻,因此氦气的速度快,能够改善熔池的流动性,有利于液态金属中的气体排出。同时氦气还使电弧的能量更加均匀,导热性好,因此冷却效率好,避免了气孔的形核长大。CO2会与气体中的氢形成不溶于铝合金的OH-,从而减少了环境中的氢进入熔池形成气孔,同时CO2的增加会减小熔滴的尺寸,加速熔滴的过渡,避免了熔滴过渡过程中氢原子的进入,减少气孔的形成率。有研究发现采用97.5%的氩气加上2.5%的CO2气体保护时气孔基本得到消除。 增材制造的原材料表面氧化物薄膜容易吸收空气中的湿气,将氢引入到熔池中,另外焊丝表面的水分、油脂也是氢的来源。金属丝材的表面粗糙度严重影响气孔率,这是由于粗糙的表面易于杂质的聚集,同时杂质中含有大量的氢,会在电弧增材制造中产生氢气孔。 铝合金丝材中的合金元素也对气孔的形成有影响,与纯铝相比,铝合金更加容易形成气孔,这是由于合金元素影响了氢元素的最大溶解量以及合金元素的挥发。在Al-Zn-Mg-Cu高强度铝合金中,由于Zn、Mg元素熔点低易挥发,极易产生气孔,在Al-Zn-Mg-Cu铝合金加入Zr以及Ti等细化晶粒的元素,抑制了气孔的形成,降低了气孔率,这表明微量元素的加入有利于抑制气孔的形成。 在气孔形核后,部分气体可以排逸出去,另一部分无法排逸,最终留在铝合金构件内形成气孔缺陷。因此,通过对工艺方法及参数的优化,使气体排逸的速度大于气孔的形核速度,有利于抑制气孔缺陷的形成。 以7系铝合金电弧增材制造为例,通过工艺方法改进和参数优化,可降低气孔率,有效提高电弧增材制造铝合金的力学性能,冷金属过渡(CMT)技术以及熔化极气体保护焊得到的铝合金力学性能较好,从气孔缺陷角度分析这两种方法得到的铝合金综合性能较好的可能原因如下: 1)熔化极气体保护焊增材制造得到的铝合金力学性能较好,可能原因是,熔池相对较宽,有利于气体的排出,气孔较少;并且其热输入高,液态金属的流动性较好,气体易排出,所以熔化极气体保护焊得到的铝合金气孔率低且力学性能较好。 2)CMT工艺的热输入较低,有利于提高力学性能,其原因是氢在铝中的溶解度随着温度的升高而增加,热输入低,使得铝合金中氢的含量降低;并且对于7系铝合金而言,Mg和Zn的易挥发形成气孔,因此热输入低也减少了由于元素挥发带来的气孔。表1是不同工艺方法的CMT电弧增材制造铝合金的气孔率,对比发现脉冲+变极性CMT(CMT+PA)的热输入最低,气孔率也是最低的,可见降低热输入有利于降低气孔率。另外,虽然脉冲CMT(CMT+P)的热输入高于变极性CMT(CMT+A),但其气孔率低,这是由于脉冲CMT的熔滴流动性更好,气体易排出,所以气孔率较低。在力学性能试验中发现,变极性CMT试样的力学性能较差,这是因为其熔滴流动性差,不利于气体的排出,因此形成了较大的气孔从而裂纹易在该处扩展,使其力学性能变差。 表1 CMT电弧增材制造气孔率
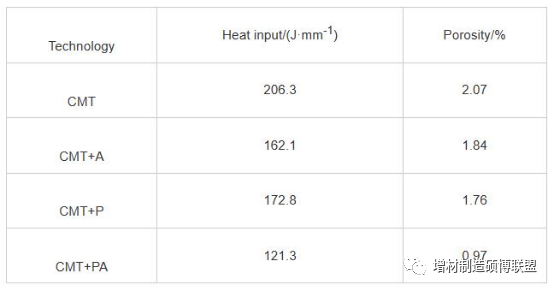
脉冲频率对于气孔的形成也有着较大的影响,在低频率时,随着频率的增加气孔率会减少,并在50 Hz时达到最小,之后随着频率增加气孔率增加。这是由于低频时随着频率的增加熔池变宽,凝固时间增加,熔池中液态金属的流动性较好,利于气体排出,同时较低的热输入利于降低气孔形核率,而频率继续增加后,热输入变大,此时气孔形核率大于气体排出的速率,气孔率进一步增加。 气孔易于分布在电弧增材铝合金的结合层间,如图3所示,后热处理并没有消除气孔,反而增加了气孔数量,并且热处理后气孔沿着层间聚集分布。对电源及熔滴过渡形式进行优化调整,形成较低热输入的熔滴过渡模式,如冷金属过渡模式(CMT)、冷金属+脉冲喷射过渡模式(CMT+P)、变极性冷金属过渡模式(Adv CMT)和变极性冷金属+脉冲喷射过渡模式(Adv CMT+P),可有效减少气孔,如图4所示。层间温度也对气孔率也有着重要的影响,电弧增材制造是循环受热的过程,研究表明层间温度的降低有利于抑制气孔的形成,较低的层间温度抑制了气孔的形核与长大。 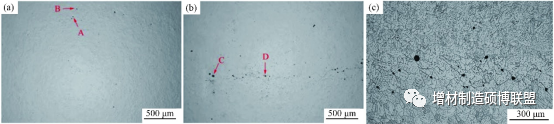
图3 热处理对气孔的影响(a) 无热处理;(b) 热处理;(c) 气孔在层间聚集分布
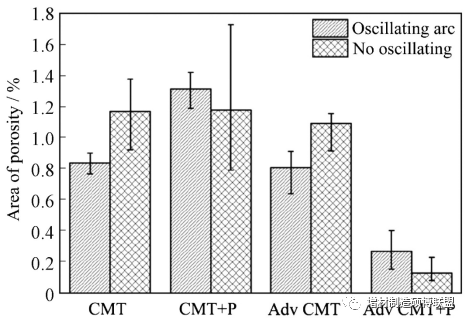
图4 不同工艺对气孔的影响
气孔缺陷会对铝合金构件的力学性能产生严重影响,铝合金内部的气孔尺寸差异较大,如图5所示。大尺寸气孔(如直径>50 μm)极易形成裂纹源,也显著降低构件的疲劳性能和强度,显微气孔是较为常见的冶金缺陷。气孔在收缩应力作用下会产生内应力,造成应力集中,裂纹极易萌生扩展使构件发生失效。 何鹏等指出气孔对于构件的硬度也有一定的影响,熔化极惰性气体保护焊(MIG)电弧增材制造铝合金的硬度在结合层处发生显著降低,这是由于电弧增材制造铝合金的结合层处气孔率较高并且气孔尺寸较大。对电弧增材制造的Al-Cu-Mg合金进行热处理强化后,虽然强度得到了提高但其延伸性变差,这是由于气孔在热处理过程中发生了聚集和长大,而裂纹极易在气孔处萌生和扩展。 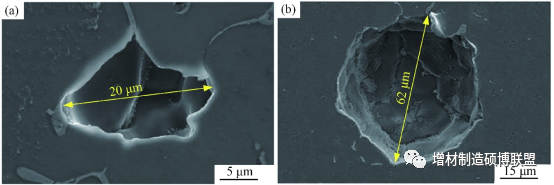
图5 电弧增材制造2319铝合金内部气孔(a) 小尺寸气孔;(b) 大尺寸气孔 气孔缺陷的有效抑制对于提高WAAM铝合金质量和性能具有重要意义,气孔缺陷的抑制机理及措施研究也成为WAAM铝合金高效高质量发展和工程应用面临的关键问题。针对CMT电弧增材制造铝合金,有学者研究了工艺参数及保护气体流量对气孔的影响,如图6所示,提高保护气体流量并适当降低热输入可对铝合金丝材端部表面实现高效清理,显著降低了气孔率。 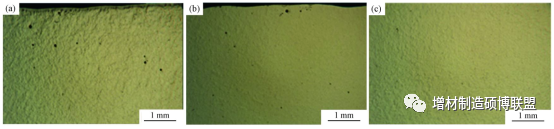
图6 保护气流量对2319铝合金变极性复合脉冲CMT(CMT-PADV)增材构件气孔的影响(a) 15 L/min; (b) 20 L/min; (c) 25 L/min
研究学者开发了可精确控制层间温度及热循环的冷却装置,通过对层间温度的控制,抑制了气孔的形成。Gu等通过层间冷加工的方式,使气孔在外力的作用下闭合,达到抑制气孔的目的,主要通过施加层间碾压使微气孔被压扁,随着碾压力的增加,微气孔数量减少,当碾压力达到45 kN时,微气孔消失。
还有学者研究了多场耦合对气孔的抑制效果。张骥俊等利用CMT与超声波外场进行耦合,利用超声振动的空化及声流效应使熔池中的气泡破裂,促进气泡逸出,达到抑制气孔缺陷的作用。 综上所述,目前对于气孔缺陷抑制的研究,可总结为以下几个方面:1)基于交流MIG或CMT的工艺优化;2)高纯度的保护气体环境;3)原材料和基板的清洁;4)改善堆积层的形态;5)增材过程中温度检测及控制;6)层间碾压。 裂纹在铝合金电弧增材制造中也是较为棘手的冶金缺陷,不仅恶化构件的力学性能,也极易造成重大安全事故。因此,克服裂纹缺陷是推动铝合金电弧增材制造快速发展面临的关键技术问题,下面对裂纹形成机理及影响因素和抑制措施等方面进行了梳理分析。 铝合金电弧增材制造中的裂纹主要为热裂纹,较为常见的有凝固裂纹和液化裂纹两种。凝固裂纹是由于铝合金在快速凝固的过程中,固相迅速收缩,而液相来不及填充,凝固末期在收缩所形成的拉应力作用下,形成了沿晶开裂。凝固裂纹不仅与材料的凝固特征有关,还受到构件形状尺寸特征的影响。液化裂纹是由于晶界处的低熔点共晶物所引起的裂纹,电弧增材制造是受热循环多次作用的过程,前一堆积层完成后的热量相当于对后一层预热,而后一层堆积时又对前一堆积层有热处理作用,这种循环热作用会引起晶界处的低熔点共晶物熔化形成液态薄膜,又由于加热冷却循环过程中会产生热应力,在应力作用下,液态薄膜开裂形成了液化裂纹。 堆积层的非充分熔化也会造成层间开裂,主要由于相邻堆积层之间未能实现有效结合,在应力作用下出现层间分离。这种层间开裂很难通过后续处理进行消除,对基板进行预热可有效避免层间开裂。电弧增材制造异质结构时,在异种材料堆积层之间也易形成开裂,如图7所示,主要由于异质层之间收缩不一致,形成应力集中,同时界面脆性相的生成也促使开裂。高强铝合金的热裂纹敏感性比较高,主要是由于其含有合金成分较多且含量较高,如7系铝合金含有Cu、Mg、Zn等元素,其中Mg及Cu元素在晶界处易偏聚,形成低熔点共晶物,增大热裂纹倾向,严重限制了电弧熔丝增材技术在制备7系高强铝合金中的应用。张宇豪等研究表明,在7075铝合金电弧增材制造中加入Zr以及Ti等细化晶粒的元素有利于抑制热裂纹。这是由于细化晶粒的同时也改善了成分偏析,避免了元素在晶界处形成低熔点共晶物而产生液化裂纹,但是快速凝固下,液相来不及补缩而引起的凝固裂纹仍未得到较好的解决。如图8所示,气孔处有较大的应力集中,在收缩应力作用下,可能导致气孔处出现微裂纹。Gu等在进行Tandem双丝增材制造过程中,用Al-Cu和Al-Mg丝材进行合金元素的调控,改善增材制造铝合金的裂纹敏感性,研究表明Cu元素含量在4.2%~6.3%和Mg元素含量在0.8%~1.5%范围内时,可有效降低裂纹敏感性。 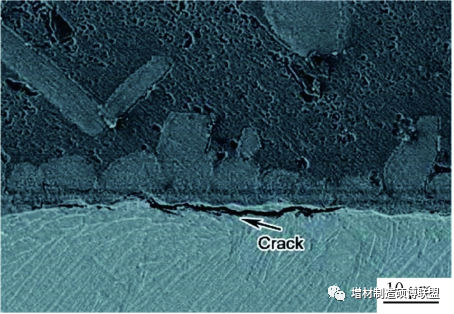
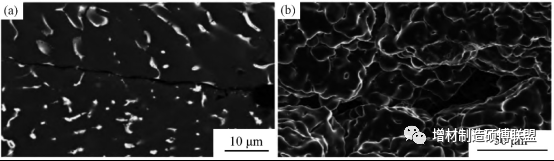
图8 电弧增材制造7075铝合金中的裂纹(a) 裂纹及气孔;(b) 断口表面形貌
王俊等研究表明,丝材中的Si元素含量对裂纹敏感性有较大影响,随着Si含量的增加,裂纹敏感性先升高后降低,在Si含量为12%时得到的试件无裂纹。这是由于随着Si含量的增加其晶粒度先增加后减小,其凝固温度区间宽度也是先增加后减小。此外Si含量的增加也可通过改变微观组织形貌从而影响裂纹敏感性。Bi等通过激光熔化沉积成功制备了TiB2增强7075铝合金,TiB2的添加也降低了铝合金的热裂纹敏感性。用纳米TiC颗粒强化丝材后,细化了激光熔化沉积制造铝合金的晶粒,大大降低了铝合金的热裂纹敏感性。纳米增强相有利于减小晶粒尺寸,从而降低铝合金的热裂纹敏感性。
热源特性的调整可通过多热源复合来实现,激光与电弧的复合在抑制裂纹方面具有显著效果,可提高构件的力学性能。激光与电弧复合增材工艺如图9所示,借助于激光的高能量密度,有利于细化晶粒,改善元素的分布均匀性,降低晶间低熔点共晶物形成的液化裂纹倾向。
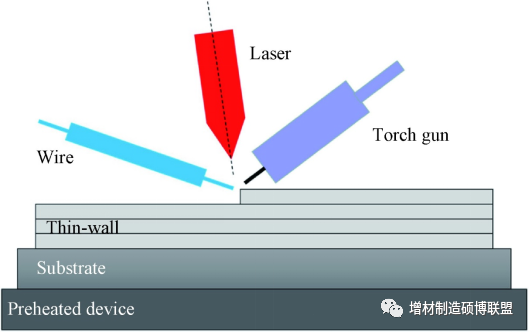
图9 激光-电弧复合增材制造工艺示意图
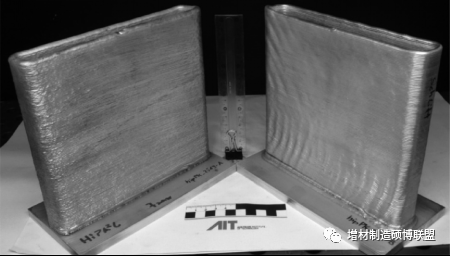
图10 冷金属过渡(CMT)电弧熔丝增材制造的无裂纹 Al-Zn-Mg-Cu铝合金试样 也有研究学者通过CMT技术实现了Al-Zn-Mg-Cu铝合金的电弧增材制造,构件如图10所示,未发现裂纹。CMT热输入较低并且熔滴过渡平稳,可有效降低电弧增材制造铝合金的裂纹敏感性。也有研究学者利用三丝钨极氩弧焊(TIG)技术电弧增材制造铝合金,在底部的粗大柱状晶区出现裂纹。
针对裂纹缺陷的抑制,主要从优化合金成分和调整工艺方法及参数等方面采取相应措施,如可采用多丝混合方式实现成分优化,对基板进行预热从而降低电弧增材过程中的冷速。另外,通过添加纳米相来细化晶粒也是抑制电弧增材铝合金裂纹的重要途径。 综上所述,铝合金电弧增材制造中的气孔及裂纹等冶金缺陷已成为严重影响结构质量及技术发展的主要难点,冶金缺陷形成机理和抑制及消除措施的研究成为增材制造领域的关键研究热点,因此对电弧增材制造铝合金的冶金缺陷进行基础理论和工艺控制研究尤为重要,通过对相关研究现状和进展进行回顾梳理,从理论模型、微观机理等多个角度阐释冶金缺陷的形成机理,从工艺改进、材料成分优化、多场协同调控等多个途径探索冶金缺陷的抑制方法,本文总结了上述多个方面的最新研究进展,并对未来的研究方向进行了展望: 1) 针对气孔缺陷形成机理和影响规律的研究已取得较大进展,但气孔缺陷的抑制还有较大的研究空间,工艺方面的改进在抑制气孔方面已展示出较好的效果,不论是基于热输入控制的工艺设备优化还是碾压后处理,都能够有效抑制气孔,但相关抑制机理还需要进一步研究;面向工程应用的气孔抑制措施仍是今后研究的重点,在气孔缺陷的抑制措施方面,还应结合其他缺陷抑制及构件性能等综合考虑,笔者认为可尝试预处理及多场协同的抑制措施; 2) 高强铝合金的电弧增材制造备受关注,也是当前增材领域的研究热点,电弧增材高强铝合金的热裂纹问题亟待解决,这也将推动电弧增材用新型抗裂丝材的研制;基于多主元的合金元素含量协同调控及纳米增强相的抗裂优化是未来可考虑的研究方向,如何将纳米增强相的内生或原位复合与电弧增材技术更有效地结合起来,增强相对凝固特征的影响规律及增强相与基体相的匹配调控也是未来可考虑的研究方向; 3) 除文中涉及的气孔和裂纹等冶金缺陷外,应力和变形控制也成为铝合金电弧熔丝增材制造领域中困扰技术突破的难题,电弧增材中的局部加热和冷却引起材料非均匀形变,构件成形后内部残余应力较大,工艺参数对残余应力及变形的影响较为复杂,对残余应力及变形进行有效调控也是保证铝合金电弧熔丝增材成形精度的重要前提,未来研究可在残余应力及变形的监测和调控措施方面开展更多的工作。