算例丨基于ANSYS的螺杆式空压机橡胶减震垫的设计和选型优化
摘要:介绍了螺杆式空压机驱动机构减震垫设计选型的优化。通过ANSYS的辅助分析,预测减震垫的最大变形,寻找最优的安装位置和最合适刚度K值减震垫,同时提到的该方法也适用于一般的减震垫的设计和选型优化。关键词:减震垫;支座反力;重心;刚度K值;压缩量
螺杆式空压机在运行时,压缩机主机和主电动机本身会发生振动,传至连接的底架、机组罩壳,引起整个系统的振动和噪声。通过使用橡胶减震垫可有效阻隔振动的传递,这种减震方法通常称之为主动减震法。文中基于ANSYS的辅助分析,试算出螺杆式空压机驱动机构橡胶减震垫的压缩量和支座反力,从而进行设计选型。1)通过ANSYS模拟计算得到的每个减震垫的支座反力小于减震垫的名义承载载荷;2)最大压缩量与最小压缩量之间的压缩量差距通常不宜超过35%,否则容易造成整个系统结构产生摆动;3)压缩裕量通常控制在50%~70%(工程经验值)之间。螺杆式空压机的驱动机构是由主机头和主电动机组成,驱动机构是空压机主要的振动源和机械噪声源。它在运转过程中产生的振动会通过其他地脚和管路传递到空压机的各个部件,产生振动及噪声。如果在驱动机构和底架之间增加橡胶减震垫,就能将驱动机构作为振源所产生的振动与空压机的底架和箱壳隔离开来,从而减少驱动结构振动对底架和箱体的影响,同时也可以通过减振垫吸收一部分振动能量来减小驱动结构的振动幅值。驱动机构有4个支撑点,主机头下方2个,主电动机下方两个,如图1所示。从整机结构中选取减振系统的主要零部件的三维模型,该减振系统是主机头、主机头支架、齿轮箱、主电动机和橡胶减震垫的装配模型。三维模型的建立是使用CRO/E4.0的三维建模软件的环境,对主机头、主电动机等质量较大部件进行重心的分析,计算得到整个刚性连接的重心位置。然后依次在CRO/E中建立橡胶减震垫的模型,并完成各个减震垫的装配,如图2所示。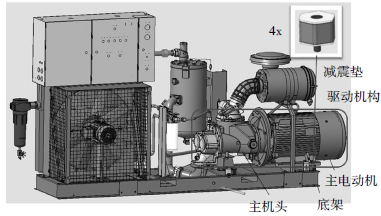
图1 整机结构
表1 零件属性
文中采用的是在Cro/E 4.0中建立三维模型,另存为IGES格式,然后在ANSYS软件中运用import命令导入其中。利用有限元分析法,定义边界条件及划分网格的大小,对螺杆式空压机驱动结构的三维模型进行预处理,如图3所示。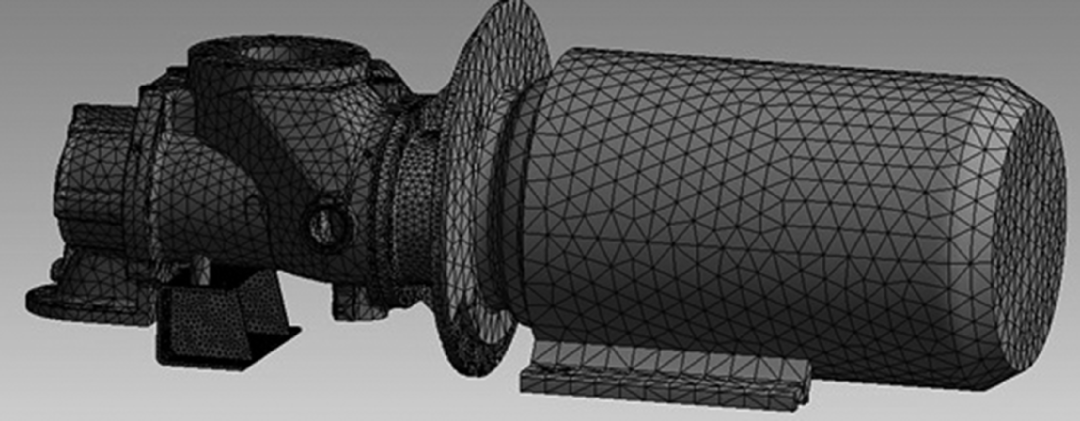
在典型有限元模态分析中唯一有效的“载荷”是零位移约束,其他载荷可以在模态分析中指定,但在模态提取时将被忽略,因而只给有限元模型施加约束边界条件。本例在ANSYS软件里约束X轴和Z轴方向的位移,用弹簧模拟减震垫,使整个驱动机构在运行时只可能在Y轴方向振动来求得减震垫的最大压缩量。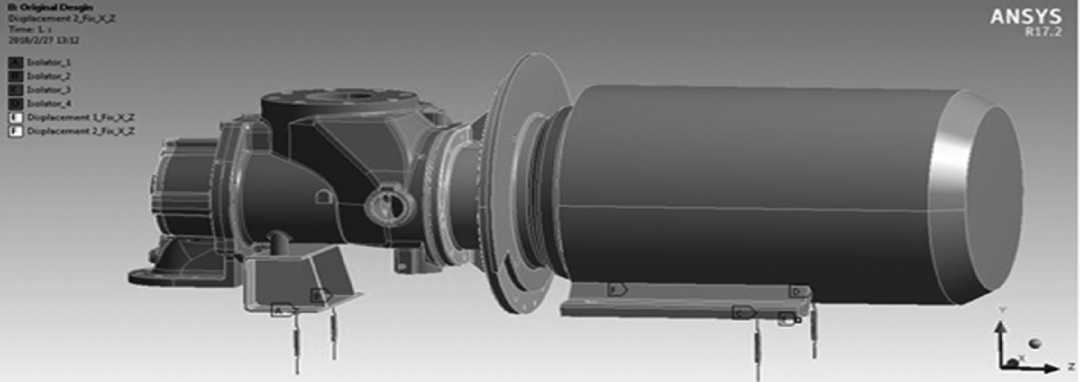
输入各主要零部件的材质、质量、重心等属性信息后,得到驱动机构的重心位置。主机头下方的两个减震垫分别为F1、F2,主电动机下方的两个减震垫分别为F3、F4,减震垫布置如图5所示。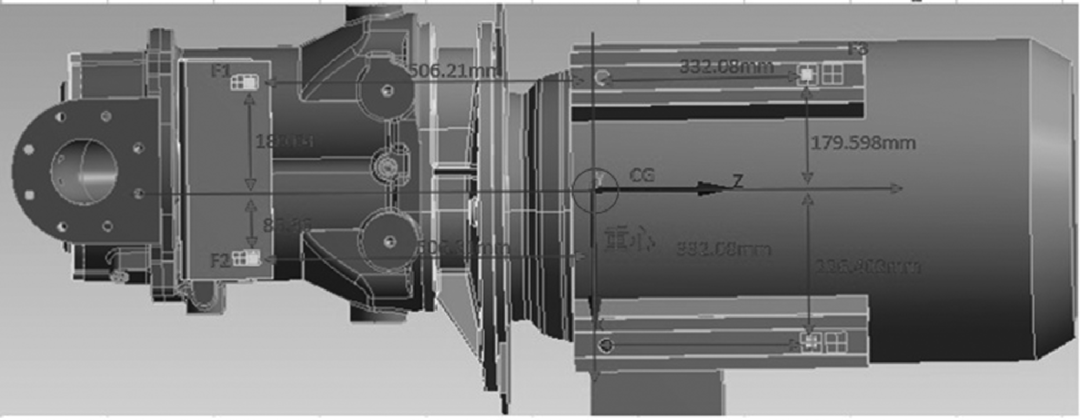
表2 计算结果
计算结果分析:1)根据计算,4个减震垫的支座反力在最大挠度值以下。减震垫能满足负载要求;2)电动机下方的减震垫F4的最大压缩量与主机下方的减震垫F1的最小压缩量比值为062,减震垫压缩不均匀度达到了62%(目标是不超过35%),否则会导致系统摇摆。需要对初始设计进行优化。1)方法一:调整减震垫的位置,以改变减震垫到重心的距离;2)方法二:较大负载侧(主电动机侧)采用较大K值的减震垫,减小压缩差。1)方案A:基于初始设计,保持主机头下方的减震垫的位置不变,将主电动机下方的减震垫向+Z的方向移动38 mm,远离重心,如图6所示。2)方案B:在方案A的基础上,减震垫F1和F2分别沿着+Z方向移动5 mm, 然后F1 沿+X方向移动10 mm,F2沿-X方向移动10 mm,如图7所示。方案C:基于初始设计,保持主机头和主电动机下方的减震垫位置不变,只把主机头下方的减震垫A替换成刚度K 值更大的减震垫B,如图8所示。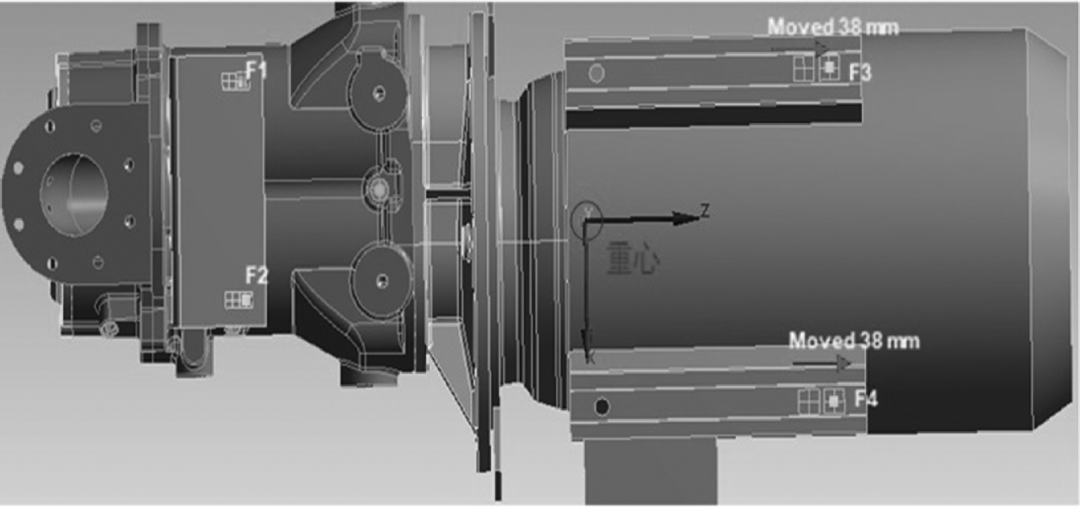

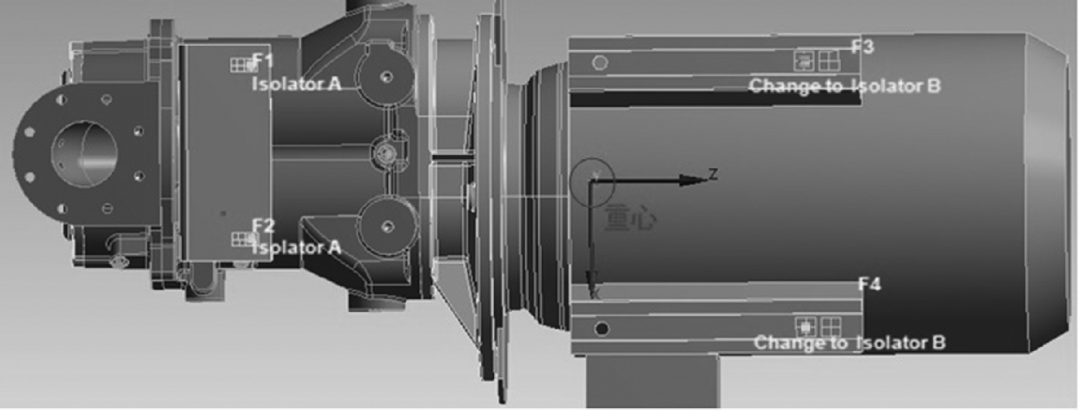
表3 方案A计算结果
计算结果:1)4个减震垫的支座反力都小于减震垫本身的最大挠度值;2)减震垫之间的压缩比差值太大,仍有47%。压缩差改善效果不明显。表4 方案B计算结果
计算结果:1)4个减震垫的支座反力都小于减震垫本身的最大挠度值;2)减震垫之间的压缩比差值有进一步缩小,仍有46%。压缩差改善效果同样不明显。表5 方案C计算结果
计算结果:1)4个减震垫的支座反力都小于减震垫本身的最大挠度值;2)减震垫的最大压缩量和最小压缩量的差值只有20%,而且4个减震垫的压缩裕量全都接近50%,因此方案C为最佳优化方案。根据ANSYS软件得出的最优方案,在螺杆式空压机上进行振动试验验证。振动试验依据《GB/T 7777-2003容积式压缩机机械振动测量与评价》5.2进行测点布置。测试点排布至少3处:主轴上一处,主轴轴承座上2处。另外,在电动机的驱动端和非驱动端各布置一处,将测得值作为补充参考值。振动测试结果根据《GB/T 7777-2003 容积式压缩机机械振动测量与评价》6.4 回转压缩机振动烈度因不大于表6的规定。表6 回转压缩机振动烈度要求
本次振动试验选取的是75 kW的螺杆式空压机,即振动烈度不超过7.1 mm/s。实际试验结果见表7。各测点的测试结果均小于7.1 mm/s,即满足GB/T7777-2003的机械振动测量的要求。表7 振动试验测试结果
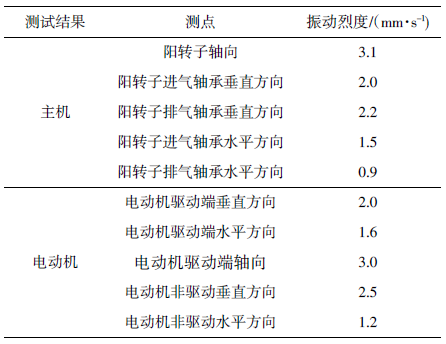
本例中,基于ANSYS的计算结果,优化设计方案C为最佳方案。方案C中4个减震垫之间的压缩量是最相近的,且每个减震垫的压缩裕量全都接近50%。方案C对应整机设计需要变动的影响最小,只需要将主电动机下方的减震垫A替换成减震垫B。由于减震垫A和减震垫B的外形尺寸、安装方式完全一样,仅轴向K值和最大负载不同。对于减震垫的关联零部件不产生其他影响。另外,提醒一点,也因为减震垫A和减震垫B外观一模一样,为了避免生产线上误装,必须在减震垫另增区别设计,比如在减震垫上追加不同颜色的色标以示区别。经过驱动结构振动测试验证,采用C方案后的振动水平都远低于要求(振动烈度不大于7.1 mm/s), 完全符合预期,再次验证前面计算的合理和有效性。本次论文对螺杆式空压机的驱动机构模块和减震垫支反力进行研究,侧重于研究减震垫的设计选型,在项目设计前期即给出了很好的风险评估及控制。此研究借助ANSYS 软件,建立模型,实际上收集了大量的零件信息,包括电动机的轴系参数、质量、尺寸等等。从结果来看,实际的减震垫选型是完全正确的。