深度 | 降本设计:塑料代替金属(中)
如上一篇文章所述,与金属相比,塑料具有很多优点。但是塑料不是金属,如果以传统金属零件的思维来设计塑胶件,就会出现很多问题。与金属相比,塑料还有很多很多缺点,这些缺点包括:
1)机械强度较低;大多数的塑料其机械强度小于金属,下图显示了普通塑料(高性能塑料除外)与金属材料的机械强度对比。2)最高使用温度低;金属在高温下依然可以正常工作;而大多数塑料其最高使用温度在150度以下,只有极少数塑料的最高使用温度能达到350度左右,如下图所示。如果塑胶件在其最高温度下长期工作,会发生变形失效,带来产品质量和安全问题。而在低温下会失去弹性而变脆。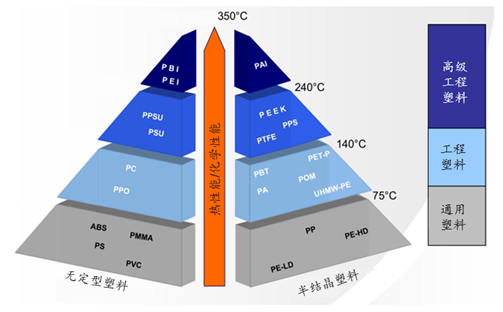
3)抗化学腐蚀性差;有些塑料会对特定化学物质敏感,如果在使用过程中接触这些化学物质,塑胶件很容易因为化学攻击而发生破裂和变形,最终失效。4)多数塑料不具有导电性,不能起着电磁屏蔽的作用;少数塑料添加添加剂后可具有导电性,但存在着原材料价格高的缺点。塑料在作为电子产品的外壳时,常常需要在塑胶件上额外固定一个金属冲压零件、导电布或导电海绵、或者在塑胶件表面通过表面喷涂导电漆,以起着电磁屏蔽的作用,这会导致额外的成本。当选择使用塑料代替金属时,并不是针对某个单独的金属零件进行一对一的材料替代,而是从整个产品DFA的角度,把多个金属件合并成一个塑胶件,这样才能最大限度的降低产品成本。一对一材料替代很少能够成功,其忽视了塑胶件可以具有复杂结构、设计自由度高的特点,并不能发挥最大的经验效益。金属件大多是通过压铸加工、机械加工或者冲压加工等而得,而塑胶件是通过注塑成型加工等而得。不同的制造工艺对零件设计有着不同的设计要求,不能以金属的思维来设计塑胶件,更不能把金属零件直接进行材料替代而不作任何设计修改。在进行塑胶件设计时,零件的壁厚、拔模斜度、加强筋、圆角、支柱和孔洞等都有不同于金属的设计要求。详细的塑胶件DFM设计可参考《面向制造和装配的产品设计指南》一书。
使用塑料代替金属的流程如图所示,其中关键的步骤包括组建团队、明确应用需求、技术可行性分析、塑胶材料选择、有限元分析、成本分析和验证测试等。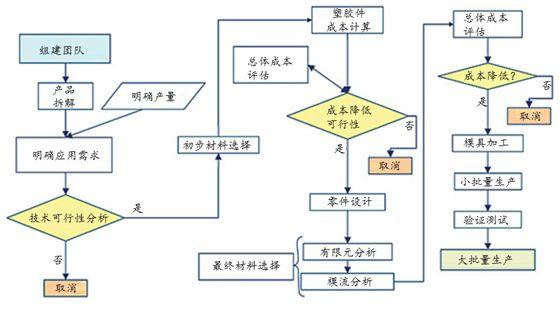
塑料能够大幅降低产品成本,这已经获得共识;但是使用塑料代替金属不是一件容易的事情,面临着多个领域的挑战,稍有失误就有可能对产品性能、安全和可靠性等造成危害。组建一个强有力的团队显得非常有必要,利用团队成员的专业知识,进行有效的团队合作,有助于提高效率、减少错误和提高产品质量。一般来说,团队应当包括4~6个成员:
具有丰富经验的工程师或专家。
各个功能团队的代表,包括设计、制造、市场、销售、采购以及质量管控等。
公司管理层的大力支持。
外部成员的支持,例如塑胶材料供应商、模具供应商和紧固工艺设备供应商等。相对于内部团队,他们对塑料性能、优缺点和具体应用范围更加清楚,可以参与到材料选择、零件设计、样品测试以及试生产等中,为内部团队提供建议。塑胶材料供应商可提供塑料的特性和性能数据。模具供应商从注塑成型的角度,为零件的详细设计提供建议,使得塑胶件具有很好的可注塑性,从而高效、低成本和高质量进行注塑加工。紧固工艺设备供应商,例如超声波焊接机供应商,评估零件是否可以正确地装配,并提供相关建议,包括导熔线的设计等,使得零件装配效率高、质量好。
零件和产品的应用环境需求贯穿塑料代替金属的整个过程,会影响塑胶材料的选择、零件设计、模具设计、零件制造和装配等,因此必须明确定义清楚。零件和产品的应用环境需求包括(不局限于):在明确应用需求的基础上,从技术上分析判断是否可以利用塑料来代替金属,包括塑料是否满足使用环境要求、是否具有足够的机械强度、是否具有足够的使用寿命等。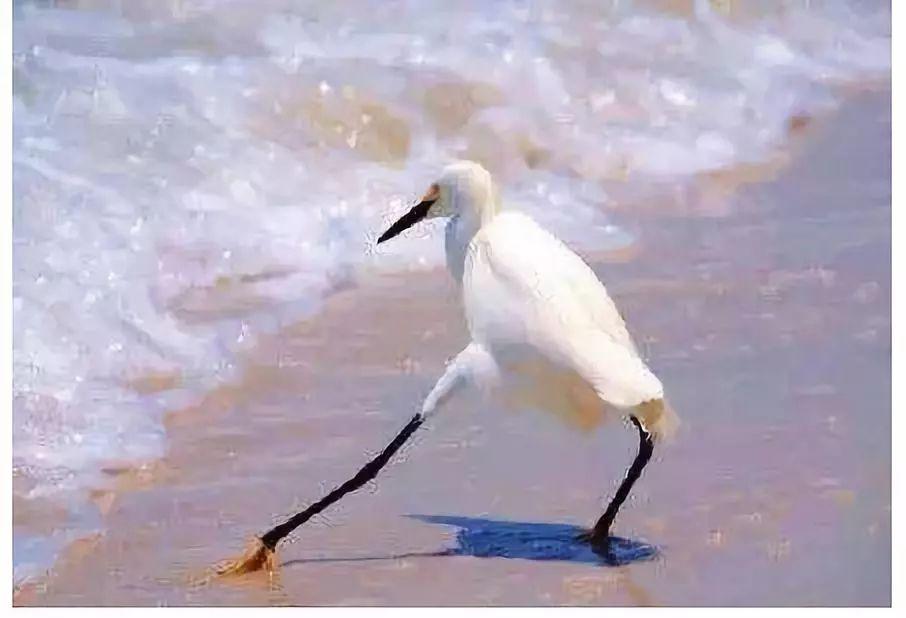
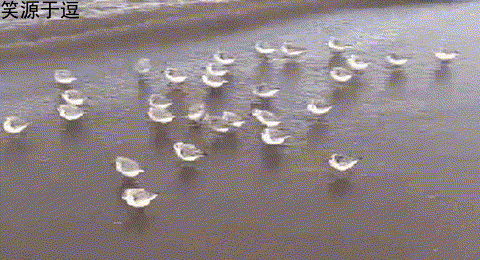
塑胶材料大约有25000种,而不同塑胶材料的各种性能,包括物理性能、力学性能、热性能、耐环境性能、耐化学性能、阻燃性能以及电性能等,都存在不同的差异。即使同一种塑胶材料,其性能会随着添加剂的不同、或增强纤维添加与否以及比例不同而产生差异。塑胶材料的不同性能差异造成了针对特定的应用环境选择一个合适的塑胶材料变得非常困难。但是,一旦塑胶材料选择错误,就会造成产品在使用过程中产生质量和可靠性等问题。例如某产品的应用环境为高温高湿,如果此时选择易水解的PC塑胶材料,则在使用时产品会因为水解而造成机械性能降低甚至发生破裂等缺陷。在选择塑胶材料时,必须了解所选塑胶材料的所有性能,例如耐化学性,即零件在移动、装配、外观处理和使用过程中,是否具有足够的耐化学性从而不会发生破裂、龟裂、变色、软化和熔化等。- 载荷。产品在实际应用场合承受载荷的情况,包括载荷的大小、类型和时间,然后对比塑胶材料的力学性能,选取合适的材料。
- 温度。高温会使得塑胶材料对应力敏感、更容易受到化学攻击;而低温则使得其延展性降低、更脆。
- 环境。考虑环境中存在的溶剂、酸、碱、油以及其它化学物质对塑胶材料的影响,考虑环境中化学物质的密度、暴露时间以及温度,同时还需要考虑紫外线、湿度和辐射对材料的影响。
- 安全规范。塑胶材料选择时考虑产品是否需要满足某种安规或某种认证的要求,比如3C认证、FDA、USDA、UL等;同时也要考虑产品是否需要满足UL94阻燃等级的要求,阻燃等级分为5VA、5VB、V-0、V-1、V-2、HB。
- 装配。根据产品装配要求选择塑胶材料。例如,有些材料适用于胶粘紧固,有些材料使用超声波焊接,而采取卡扣紧固的产品则要求产品具有很好的强度、延展性和尺寸稳定性。
尽管塑胶材料众多,但能够从性能上替代金属的塑胶材料并不多,这些能够替换金属的塑胶材料大多是属于高性能工程塑料,通过在基材中添加添加剂来提高物理性能、机械性能、化学性能、热性能、电性能以及可加工性等,常见的添加剂包括:- 长玻纤添加剂用于提高强度和硬度,增加耐热性到150°C。
- 短玻纤添加剂用于提高硬度,增加耐热性,零件外观较含长玻纤添加剂好,含量低于30%以下时外观质量与无增加塑料无差异。
- 矿物填充剂用于提高电性能,隔音,尺寸稳定性和增加比重。
塑料相对于金属最大的缺点是机械强度较差,因此在使用塑料代替金属时,必须在产品设计阶段针对设计好的零件进行有限元分析,评估塑胶件是否能够承受相关载荷。如果不能,则需进行设计优化,例如增加加强筋等来补强零件强度,甚至更换机械性能更好的塑胶材料。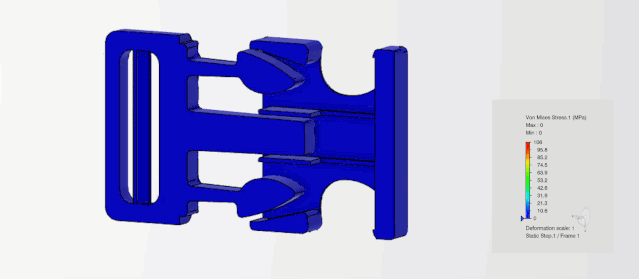
塑料代替金属的目的之一是降低产品成本。那么,一旦塑胶材料选定、相关的零件设计完成以及制程与装配工艺确定,则需要对塑胶件的成本进行计算和评估。通过计算,可评估是到达成本降低的目的,只有当真正的成本降低目的达到以后,才会进行下一步的模具制造等动作。塑胶件的成本计算和分析在《面向成本的产品设计:降本设计之道》会有详细描述,很快就会出版了,请大家再耐心等等。
为确保产品在其生命周期中能够安全可靠地使用,必须针对使用环境中出现的各种因素,例如紫外线、温度、湿度以及各化学物质等,对加工制造好的塑胶件或产品进行相关的验证测试,这些测试可能包括温度循环测试、腐蚀性测试(例如盐雾测试以及有害气体测试等)、阻燃测试、蠕变测试和疲劳测试等。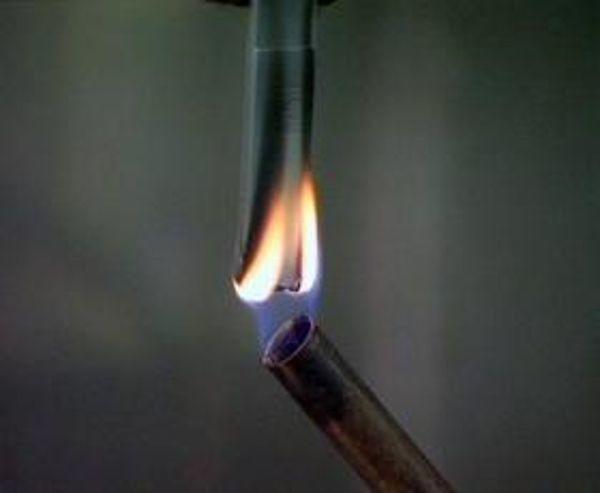
最大的挑战是如何定义测试中的加速因子,即短时间内的测试能够模拟整个产品生命周期。材料供应商提供的实验数据作为参考,但绝不能代替实际的产品测试。
1. 免责声明:部分图片来源于网络,仅供学习用,侵权删。
2. 原创作品,欢迎转载,抄袭必究。如需转载,请联系作者,转载要求不能修改内容和保留文末作者及公 众号信息。