深度 | 塑胶件缩水缺陷:预防比解决更重要(下)
不同塑料的收缩率如表2所示。半结晶塑料,例如PBT、PP等,其收缩率较大,显然会放大缩水的缺陷;无定型塑料,例如PMMA、ABS等收缩率小,会减缓缩水的缺陷。相对于非填充或非增强塑料,填充和增加塑料的收缩率较小,也会在一定程度上减缓缩水的缺陷。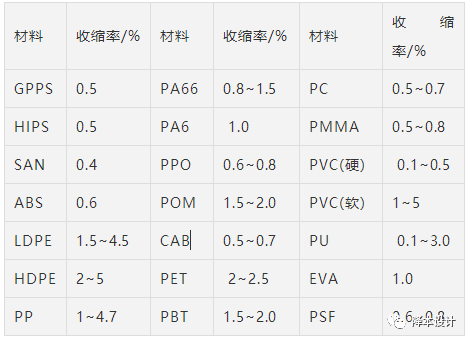
另外,塑料的流动性不好,这也会使得塑胶件在冷却收缩时材料等不到很好的补充,容易造成缩水缺陷的发生,例如PC材料。
当然,这里并不是说为了解决塑胶件的缩水缺陷,有意去选择收缩率低的塑料。塑胶材料的选择受到很多因素的影响,缩水是仅仅其中之一。只有在其它条件都符合的情况下,需要尽量选取收缩率低的塑料。
而对于工程师来说,一旦选择了收缩率高的塑料,特别是对于外观零件,则应当意识到潜在的缩水风险,通过塑胶件设计、模具设计和注塑工艺参数优化等提早预防,做到心中有数。或者尽早把缩水风险与客户进行沟通交流,而不是等到塑胶件缩水发生了,客户看到产品,与预期相差甚远,一脸懵逼。塑胶件的收缩大小与塑胶件的基本壁厚相关,壁厚不同,收缩量则不同。如果基本壁厚过厚,则塑胶件收缩过大,更容易发生缩水的缺陷。当然,壁厚过厚,不但还会造成材料浪费,还会增加注塑成型周期,造成塑胶件成本增加。表3列出了常见塑料的最小的壁厚及常用壁厚推荐值。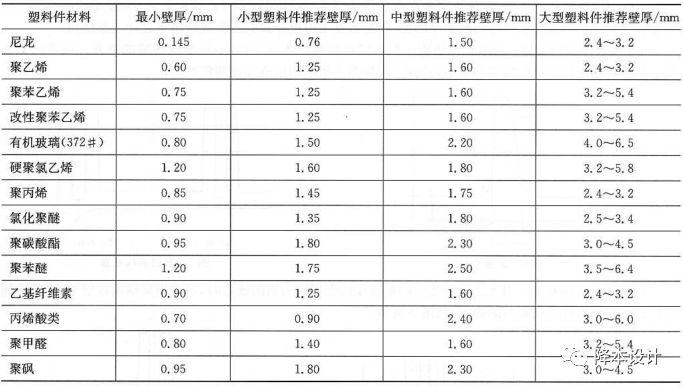
估计很多工程师看到这篇文章的标题,就会嘀咕:将告诉工程师如何在一两天之内快速掌握一门新工艺、或者成为企业常用工艺的专家。
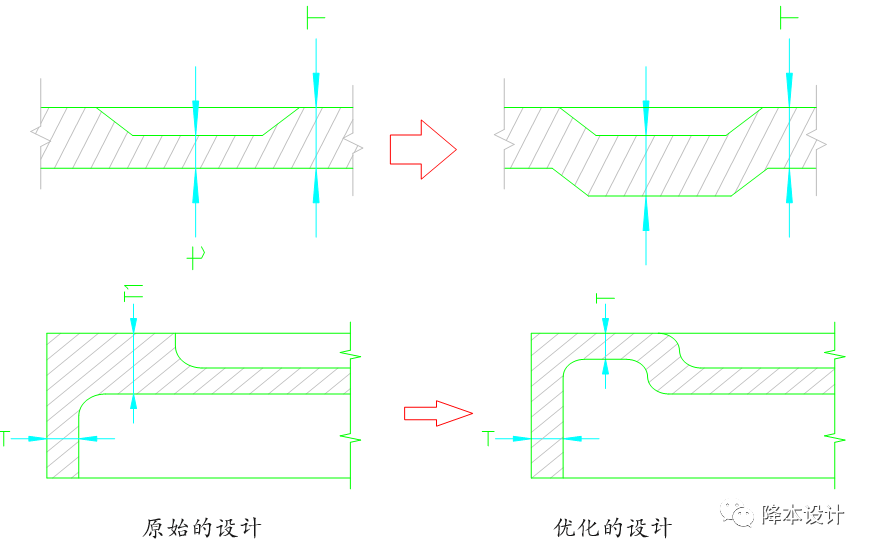
估计很多工程师看到这篇文章的标题,就会嘀咕:将告诉工程师如何在一两天之内快速掌握一门新工艺、或者成为企业常用工艺的专家。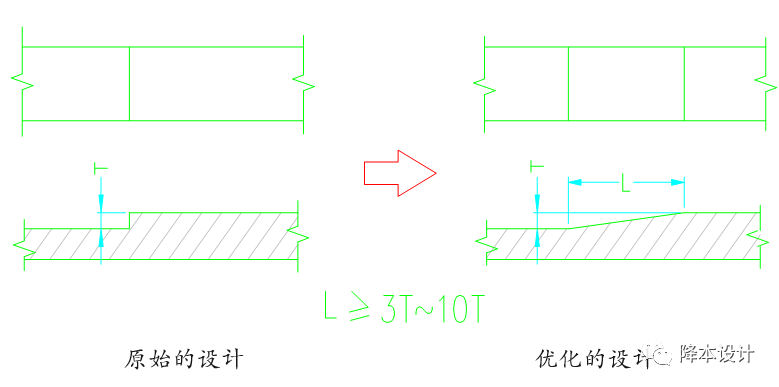
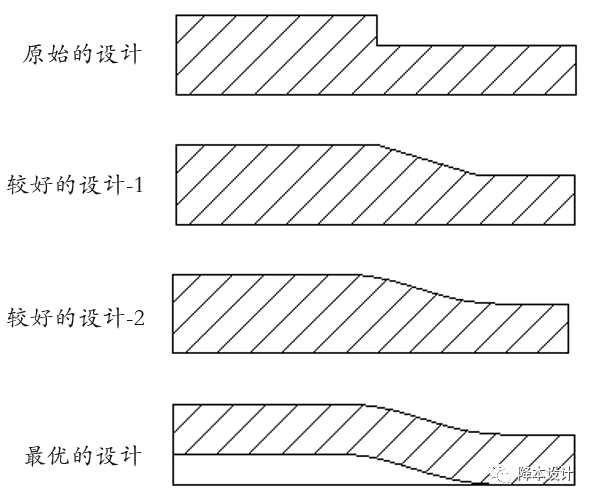
估计很多工程师看到这篇文章的标题,就会嘀咕:将告诉工程师如何在一两天之内快速掌握一门新工艺、或者成为企业常用工艺的专家。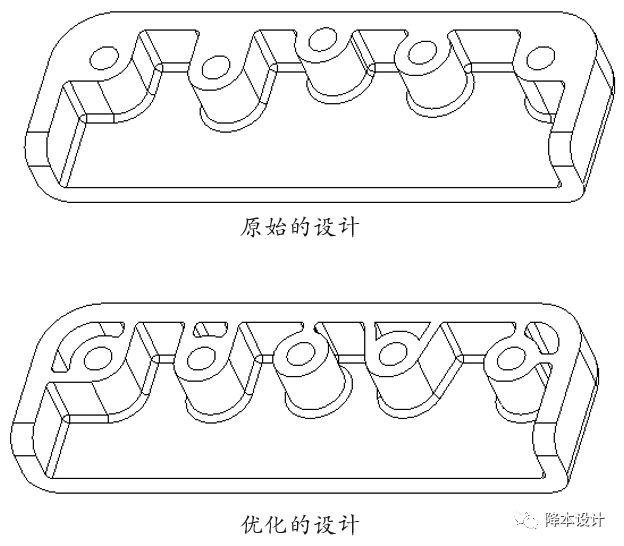
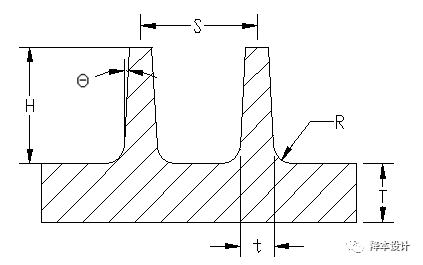
当加强筋厚度较厚时,缩水不可避免,则可以通过一些特殊的设计来掩盖缩水,保留“U”形槽、表面断差和锯齿状槽等。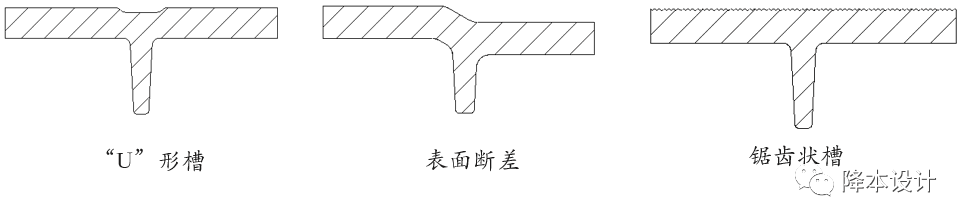
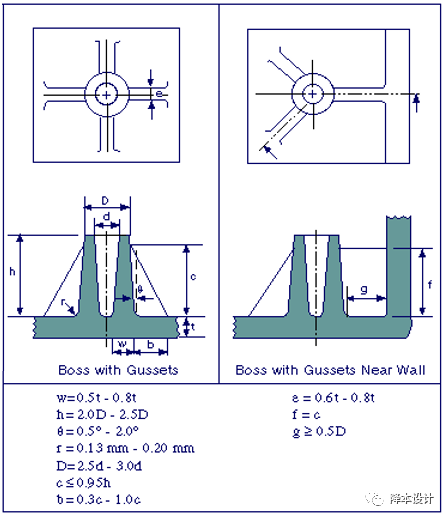
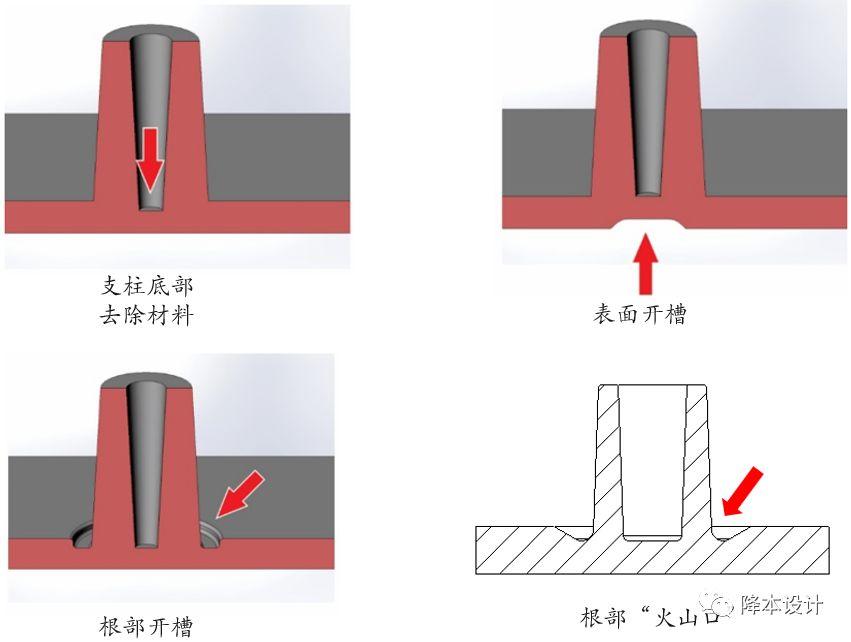
如果模具的浇口和流道截面太小,充模阻力太大,则容易引起缩水的产生。
不过,浇口和流道的尺寸不能随意的增大,因为这会造成塑胶件材料浪费和注塑成型周期加长,使得塑胶件成本增加。
这就是我为何说塑胶件设计是预防缩水问题的最优方案。
6.1 浇口布置应当使得溶料从壁厚的区域流向壁薄的区域:
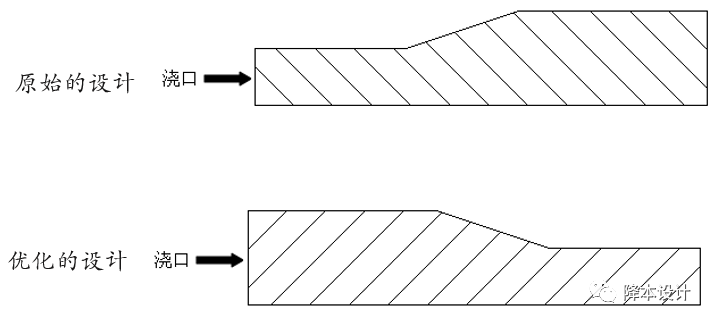
如果模具排气设计不良,或模具磨损引起释压,都会导致塑件表面产生缩水。应经常检查模具是否存在磨耗释压或排气不良,及时更换模具中的易耗易损件或改善模具的排气条件。
6.4 模具冷却系统的设计:
如果模具冷却效果好,模具温度低,则塑胶件容易产生内部的孔洞缺陷;而如果冷却效果差,模具温度高,则塑胶件容易产生外表面的缩水缺陷。对塑胶件的重要外观面来说,如果在塑胶件表面发生缩水即造成不良,那么可以通过模具冷却系统的设计,把外表面的缩水转化为内部的孔洞,则可能转为良品。因此,在容易缩水的地方(例如壁厚过厚处)设计更好的冷却结构,例如采用铍铜等导热性较佳的材料,而在其它其它表面则可以不予冷却或给以较差的冷却,从而把缩水缺陷由塑胶件外表面转化为内部的孔洞缺陷。本文介绍另外两种方法:缩短冷却时间和使用气体辅助成型。缩短冷却时间
在保证塑胶件出模不变形的前提下,采取尽量缩短冷却时间的方法,让塑胶件在高温下提早出模。此时塑胶件外层的温度仍然很高,表皮没有过于硬化,因此内外的温差相对已不是很大,这样就有利于整体收缩,从而减少了塑胶件内部的集中收缩。
由于塑胶件总体的收缩量是不变的,所以整体收缩得越多,集中收缩量就越小,内部缩孔和表面缩水程度因此得以减小。缩水问题的产生,是由于模具表面升温,冷却能力下降,刚刚凝固的塑胶件表面仍然较软,未被完全消除的内部缩孔由于形成了真空,致使塑胶件表面在大气压力的压迫下向内压缩,同时加上收缩力的作用,缩水问题就这样产生了。而且表面硬化速度越慢越易产生缩水,比如PP料,反之越易产生孔洞。因此在将塑胶件提早出模后,要对其作适当的冷却,使塑胶件表面保持一定的硬度,令其不易产生缩水。但若缩水问题较为严重,适度冷却将无法消除,就要采取冻水激冷的方法,使塑胶件表面迅速硬化才可能防止缩水,但内部缩孔还会存在。象PP这样表层较软的材料,由于真空和收缩力的作用,塑胶件还会有缩水的可能,但缩水的程度已大为减轻。
气体辅助注塑成型是通过把高压气体引入到塑胶件的厚壁部位,在注塑件内部产生中空截面,完全充填过程、实现气体保压、消除制品缩痕的一项新颖的塑料成型技术。传统注塑工艺不能将厚壁和薄壁结合在一起成型,而且塑胶件残余应力大,易翘曲变形,表面有缩水。
气辅技术通过把厚壁的内部掏空,成功地生产出厚壁、偏壁塑胶件,而且制品外观表面性质优异,内应力低,轻质高强,可以解决缩水问题。本篇文章的部分内容参考《面向制造和装配的产品设计指南》一书。1. 免责声明:部分图片来源于网络,仅供学习用,侵权删。
2. 原创作品,欢迎转载,抄袭必究。如需转载,请联系作者,转载要求不能修改内容和保留文末作者及公 众号信息。