干货 | 为了缩短注塑成型周期而降本,有些企业真的是“丧心病狂”
导读:
有的工程师或企业在设计塑胶件时,对于注塑成型周期丝毫不在意,认为再长的周期都是理所当然。
而有的工程师或者企业对于注塑成型周期锱铢必较,能够缩短1秒甚至0.5秒就是成功,总是千方百计想办法去缩短。而这当中有些企业缩短成型周期的方法可以用“丧心病狂”来形容。本篇文章介绍德国一家叫做Linde的企业“不择手段”缩短注塑成型周期的方法--使用液态二氧化碳冷却、缩短冷却时间继而缩短成型周期,降低塑胶件成本。生产已经在如此的尽力去降本了。作为产品设计,难道还无动于衷吗?
在注塑成型周期中,冷却时间占据了60~80%的比例。因此,要缩短注塑成型周期,最有效方法是缩短冷却时间。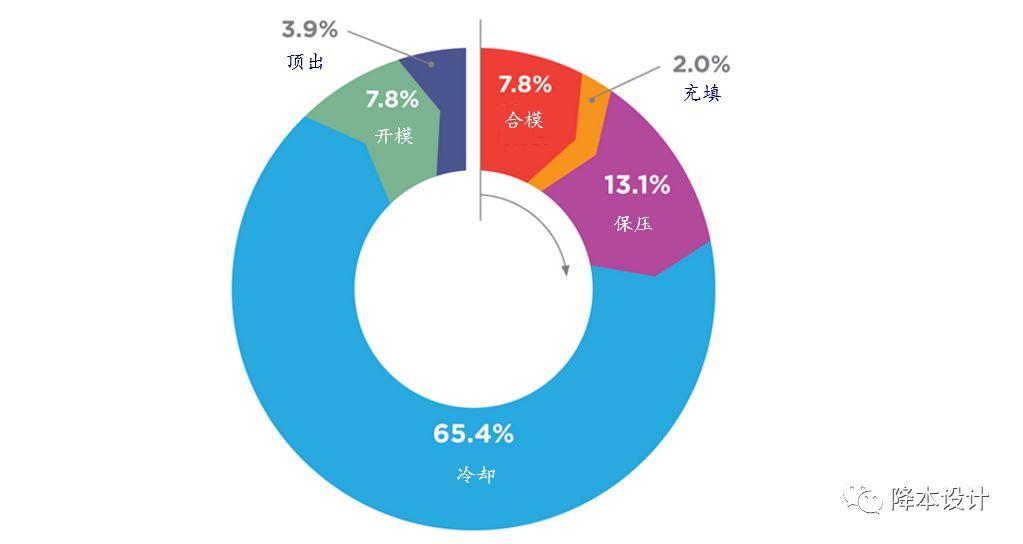
▲冷却时间在注塑成型周期中占绝大部分比例
1)第一个方向是从塑胶件设计的方向;目前在这个方向的研究不多,重视度也不够;工程师也基本上没有意识;2)第二个方向是从注塑模具和注塑生产的方向;有很多的研究专注于这个方向,并取得很大的成功。本文介绍的随形冷却、仿血管冷却和液态二氧化碳冷却就是其中之一。在注塑成型过程中,由于塑胶件结构的原因或者模具结构的原因(例如冷却水路很难触及或者冷却效果差),塑胶件上常常有热斑区域(温度过高的区域)。热斑区域最后冷却,这会急剧增加冷却时间,从而造成成型周期的增加。例如,如图所示是一个汽车滤油器PA66外壳。红色箭头所示处材料堆积严重,壁厚达到11mm。该区域不但壁厚,同时在模具上该处对应着模具镶块,普通冷却水路很难触及,冷却效果差,那么在注塑成型时就是热斑区域。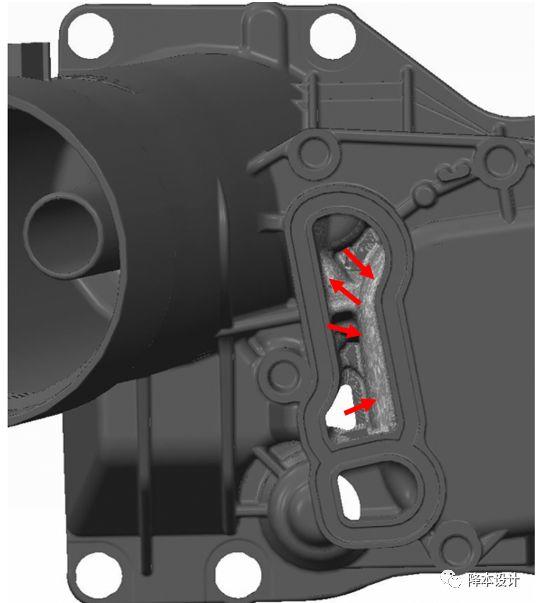
▲汽车滤油器PA66外壳
用红外线测温仪测量顶出的塑胶件,发现塑胶件表面温度最高的点处于上图所示的箭头处,证明了该处为热斑,冷却时间最长。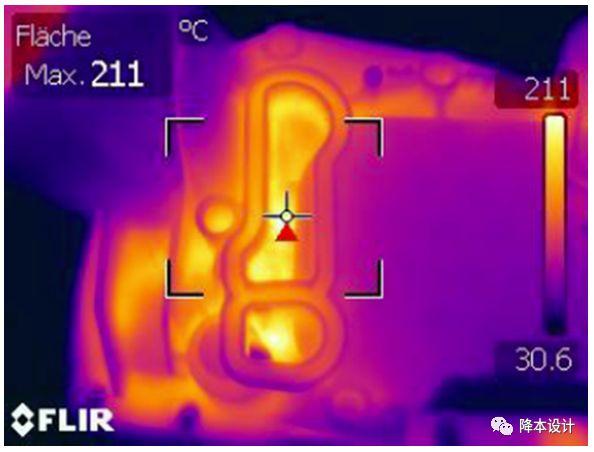
▲最热区域
对于类似汽车滤油器PA66外壳的局部过热的冷却,显然仅仅使用最普通的冷却水路在这里不可行,因为普通冷却水路一般在直径5mm以上,根本上触及不到热斑区域。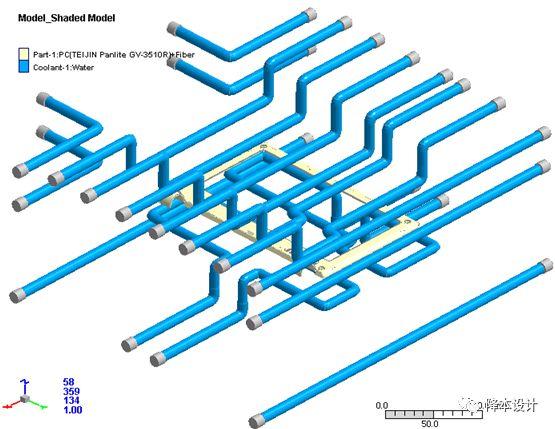
▲普通冷却水路
在普通的冷却水路上再连接两个铍铜入子,铍铜具有高导热,通过铍铜入子把热量从热斑区域转移到冷却水路带走,从而进行间接冷却。采用随形冷却,把直径2.5mm总长445mm的水路完全贴合热斑热区域的表面,使得水路与塑胶件的距离保持一致,从而达到一种均匀冷却的效果。在随形冷却的基础上更进一步;首先布置一根直径3mm的水路为主动脉,然后分支为2根直径为2.12mm的亚动脉,各再进一步分支为两条直径为1.5mm的毛细血管,整个冷却水路全长480mm。▲第2)3)4)种冷却方式
显然,第4种的冷却方式效果最好,能够最大限度的缩短冷却时间,从而缩短注塑成型周期。其实,使用仿血管冷却已经足够“变态”了,但是偏偏还有企业在研究液态二氧化碳冷却,你说这是不是“丧心病狂”啊?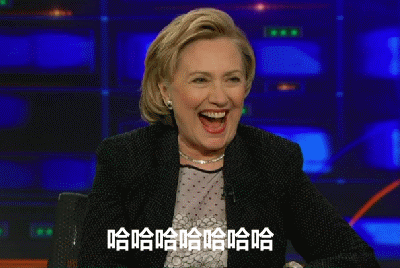
水路直径通常要求5mm直径以上。水路直径过小容易造成堵塞或者要求非常高的水压;
只有空间允许的情况下才能使用水路;但这并不是冷却效率最高的方式;
热斑区域通常是水路很难触及的区域,冷却效率低甚至根本上就没有冷却,这会造成整个注塑成型周期急剧增加。塑胶件成本也相应的急剧增加。
针对传统水路存在的问题,德国一家叫做Linde(林德)的企业开发了液态二氧化碳冷却技术。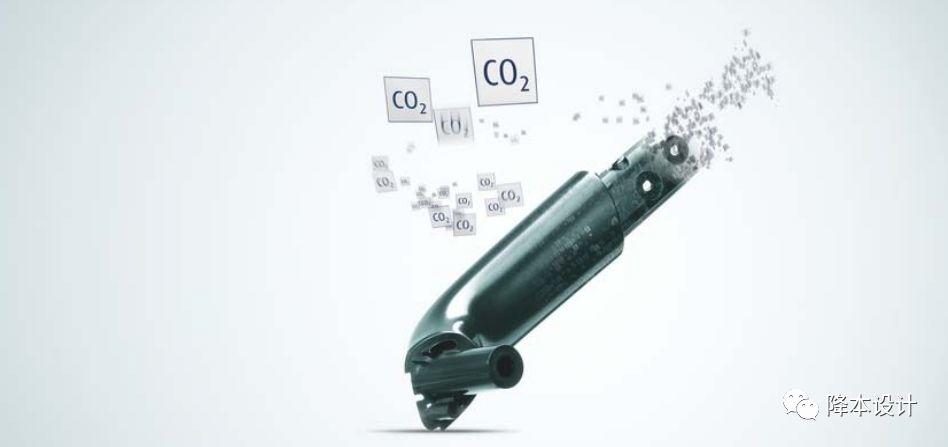
液态二氧化碳冷却并非是完全替代传统水路,仅仅是针对针对传统水路很难触及或者冷却效果差的塑胶件热斑区域,例如较长的型芯、入子、顶针和滑块等。当塑胶件开始冷却时,液态二氧化碳在极高的压力下输入到薄而灵巧的不锈钢毛细管中,直达塑胶件最需要冷却的热斑区域。在毛细管顶部,在“膨胀室”中,毛细管末端的液态二氧化碳膨胀会产生温度约为-78°C的二氧化碳气体,从而提供非常高的局部冷却能力,使得热斑区域快速冷却,达到缩短注塑成型周期的目的。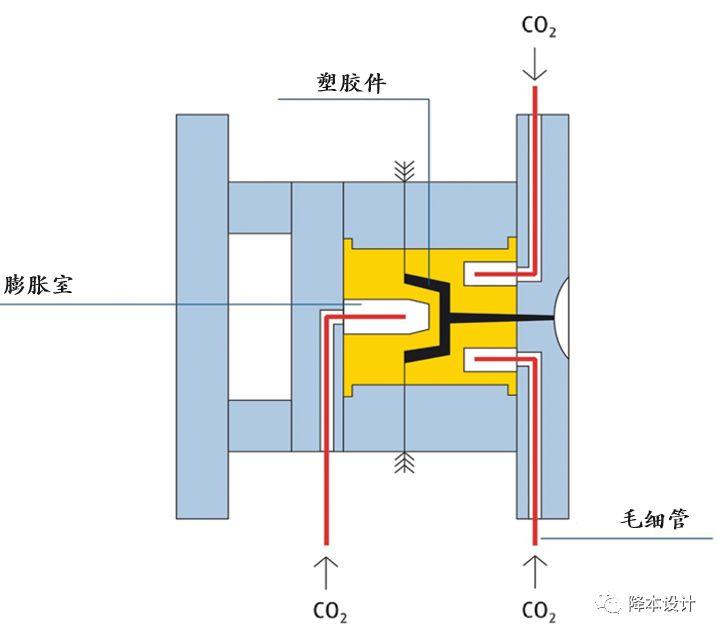
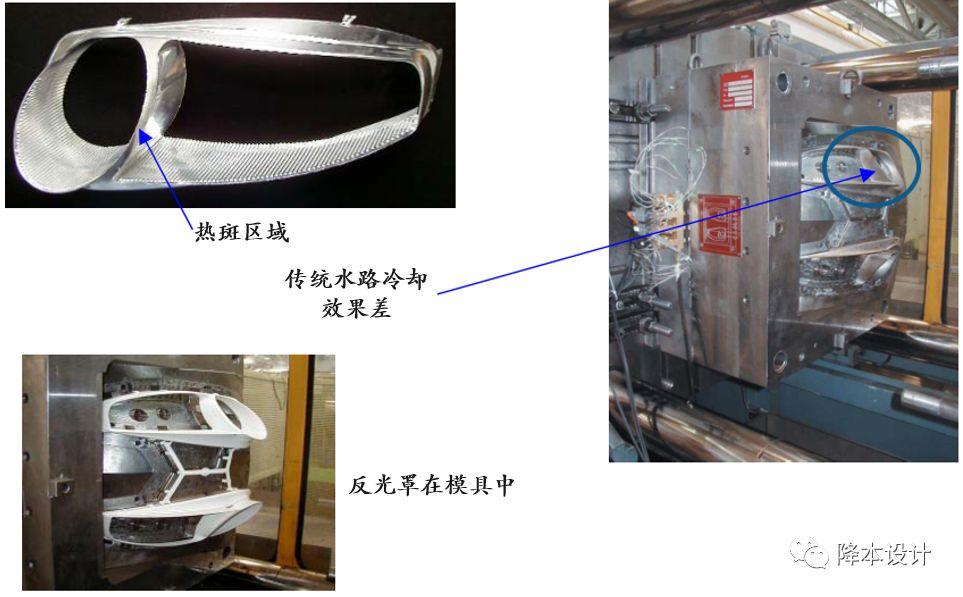
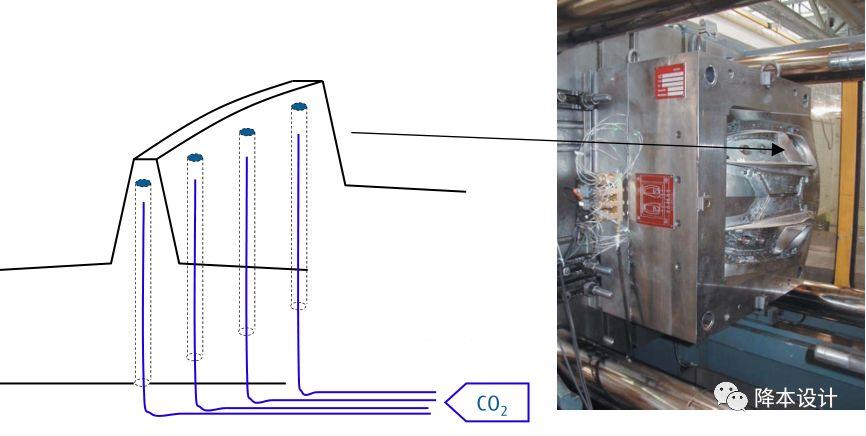
其它一些成功应用案例包括各种门把手、水管和车架等。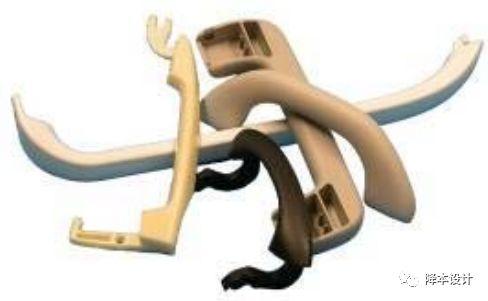
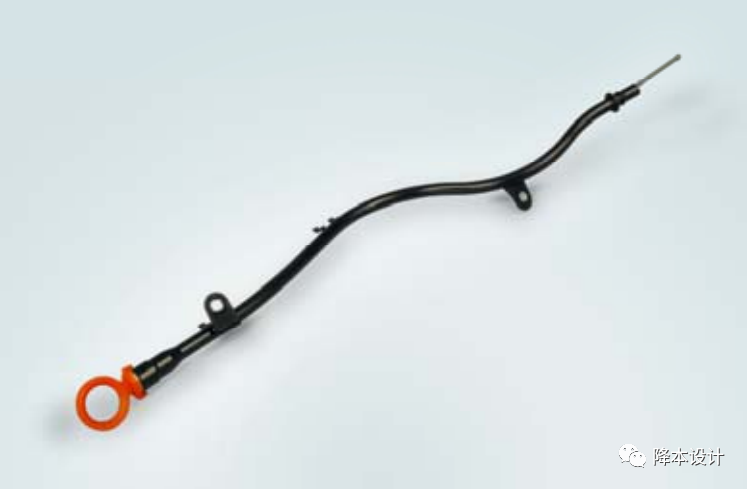
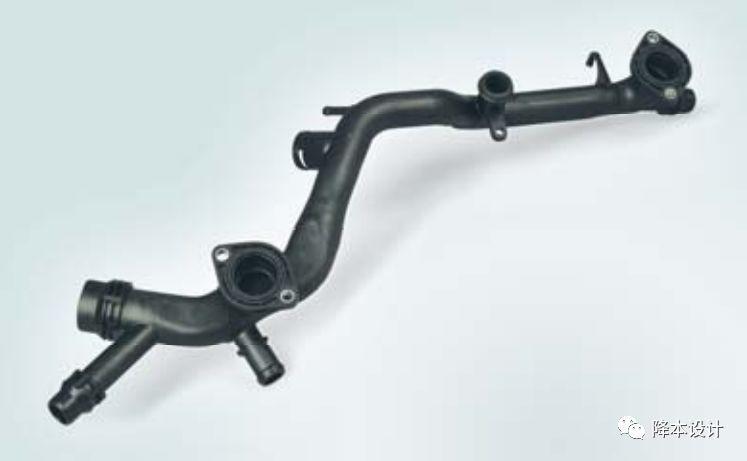
本文并不是为了推广液态二氧化碳冷却技术,我也并没有实际接触过这种技术。同时,我也并非注塑模具专家。不过我有了解到国内有企业在使用这种技术,自行开发相关设备,并在实际应用中取得了成功。本文的目的是告诉大家:缩短注塑成型周期对于塑胶件的降本非常重要,如果能够在产品设计时通过设计优化,例如壁厚均匀、把壁厚的地方掏空,就能大幅度缩短成型周期,从而降本,何乐不为呢?从设计角度进行降本可以达到事半功倍的效果。如果设计不好,再牛的模具设计和注塑生产技术都弥补不了。即使要弥补,估计也得付出非常昂贵的代价。在我培训和咨询的很多客户中,我看到很多塑胶件设计案例,不是壁厚不均匀、就是部分区域壁厚过厚,没有一丁点降本意识。当我问工程师为什么这样设计时,工程师根本上就没有意识到这是一个问题:图纸画着画着就不均匀了,就局部过厚了。注塑模具和注塑生产方面已经在穷尽方法和手段来降低成本,但是产品设计还远远没有这个意识,现在该采取行动了。从阅读《面向成本的产品设计:降本设计之道》开始吧,里面不但有注塑成型周期以及注塑成本的计算方法,同时还有一系列塑胶件降本设计的方案。1)https://onlinelibrary.wiley.com/doi/full/10.1002/pen.25024http://read.nxtbook.com/wiley/plasticsengineering/julyaugust2015/spotcoolingwithco2.html3) https://www.linde-gas.com/en/products_and_supply/plastic_rubber_solutions/plastinum_temp_s.html
1. 免责声明:部分图片来源于网络,仅供学习用,侵权删。
2. 原创作品,欢迎转载,抄袭必究。如需转载,请联系作者,转载要求不能修改内容和保留文末作者及公 众号信息。