塑胶螺丝支柱开裂,这是塑胶件产品开发过程中,工程师必定会遇到的问题之一。 “降本设计”十几个微 信群里,问得最多的就是这个问题了。 而据我观察,不少工程师在碰到此类问题时,往往一筹莫展,不知道怎么解决。 有的工程师回答:可能是支柱内径尺寸太小;于是去测量尺寸; 有的工程师回答:可能是回料添加太多的;于是去问供应商是不是加了太多回料; 有的工程师回答:是不是扭矩太大了?于是去把扭矩减小。 不可否认,这些提示在有些时候很有帮助,如果运气足够好,也许刚好可以解决问题。 但是,在我看来,这种解决问题的方式不够系统化和全局化,东一榔头、西一棒子,问题能否解决完全依靠个人经验、或者身边高手或者群里高手的经验。 如果大家现在依然在用这种方式去解决问题,不用着急,因为在我开始工作的前几年,我也是按照这种方式去解决问题的。 随着经历和阅历的增加,我才慢慢形成了系统化和全局化解决问题的方式。 本文将告诉大家,我是如何利用系统化、全局化的思维方式去看待和解决支柱开裂问题。
塑胶件通过自攻螺丝来进行紧固,这是一种广泛应用紧固工艺。
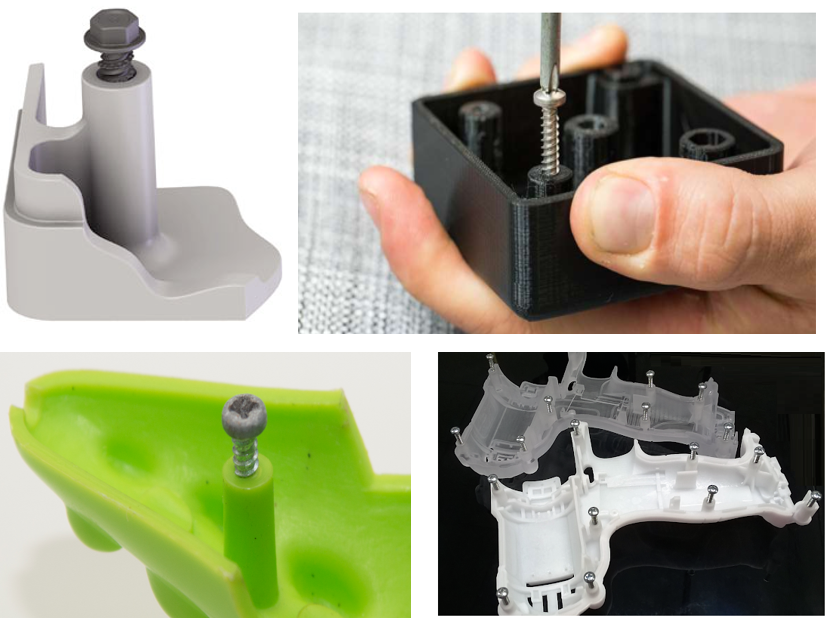
而在使用自攻螺丝进行紧固时,支柱开裂是经常发生的一个质量缺陷。 有的开裂仅仅是在支柱上产生裂纹,而有的是整个支柱从中间断裂。 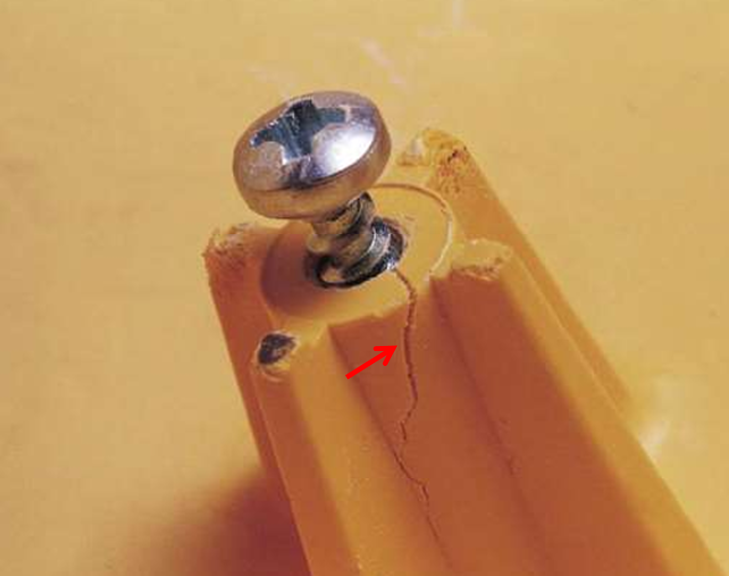
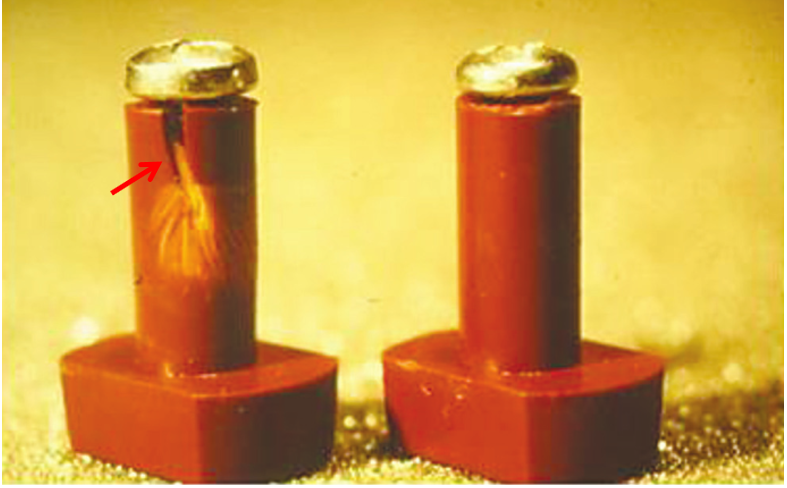
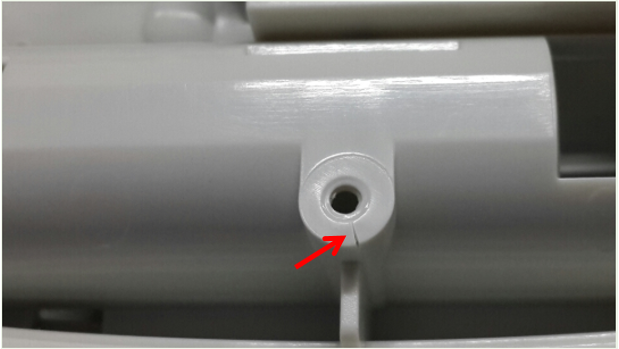


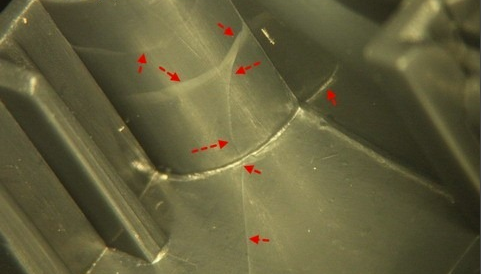
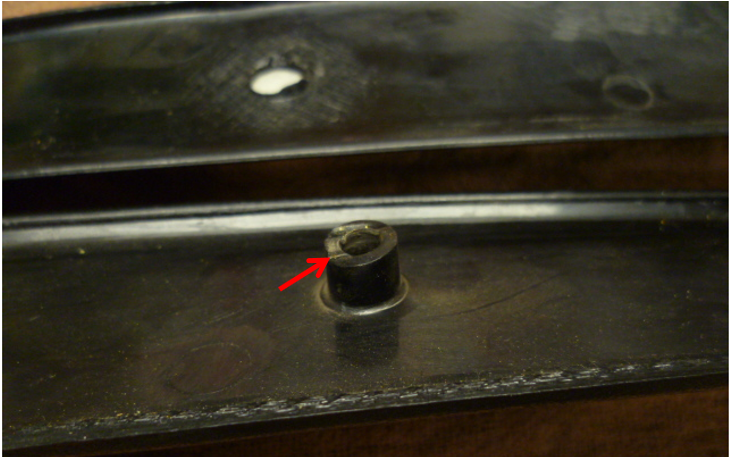
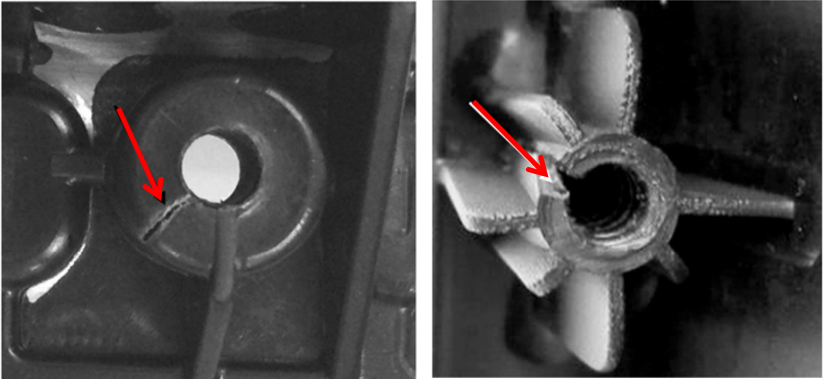
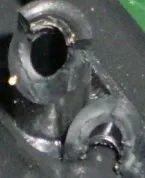
支柱开裂本身就是一个难以解决的问题。
但是支柱开裂时伴随的复杂现象更是让这个难题难上加难。例如:
同样是一副模具,这一穴没有开裂,而另一穴开裂了。
大批量生产几年都没有问题,后来突然出现问题了。
螺丝刚打上时,支柱没有问题;但是过几天之后就出现开裂;
出货检验时没有问题,而客户拿到产品后就发现破裂了。
天气热的时候,没有开裂。冬天的时候,就容易出现开裂。
用ABS没有开裂,用PC就开裂了。
这些现象会让人百思不得其解,如果我们不了解支柱开裂背后的机理,那么我们真的是解决不了这个难题。
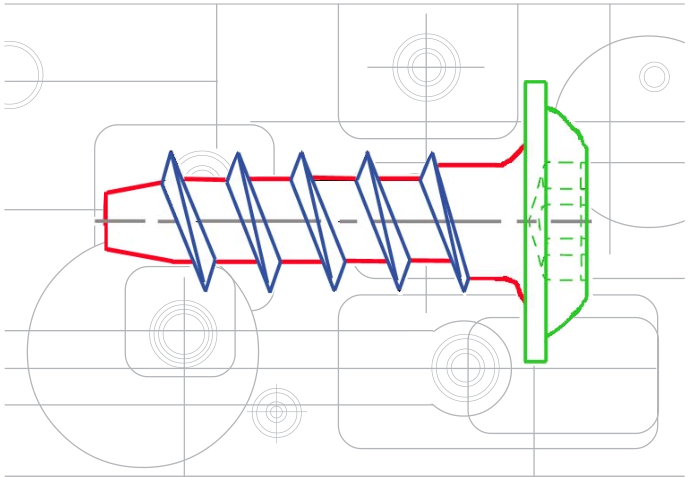
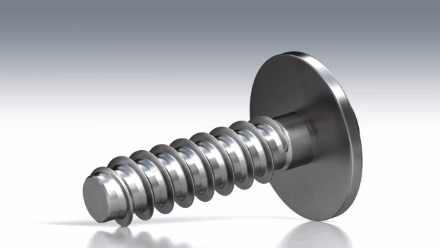
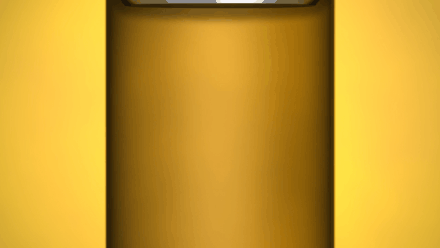
在螺丝拧入过程中,驱动扭矩会转化为作用在塑胶支柱上的力F,F垂直于螺牙平面的方向。 F可以分解为径向力FR(或称为圆周力)和轴向力FA。 当支柱承受的径向力超过了其承受的极限时,支柱发生开裂。 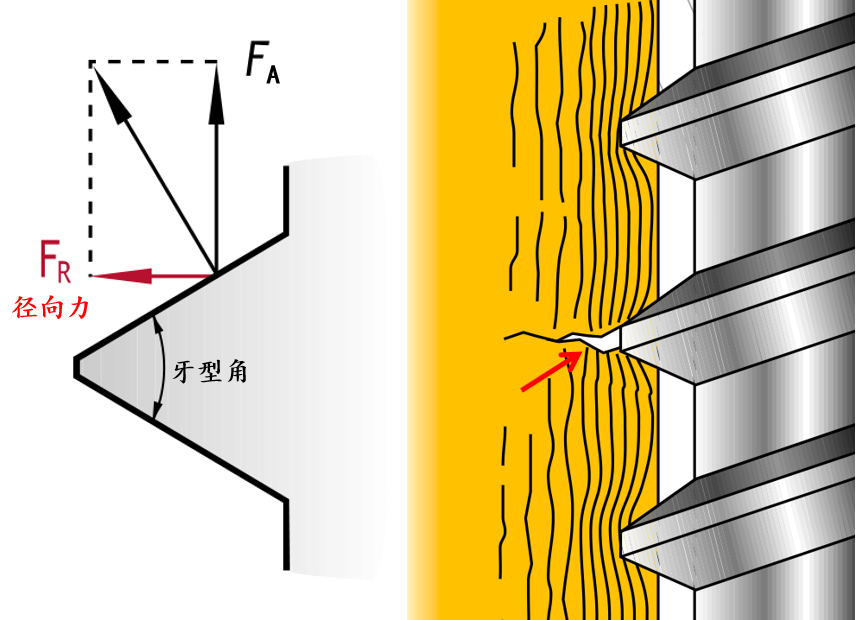
需要特别注意的是,是一个薄薄的支柱壁在默默的承受径向力。 以ABS无玻纤材料为例,内径为3*0.8=2.4mm,外径为2*2.4=4.8mm,承受径向力的支柱壁壁厚仅仅为(4.8-2.4)/2=1.2mm。 更何况1.2mm的薄壁还可能受到注塑成型条件、公差、熔接痕、温度、湿度以及化学物质等多重影响,不发生破裂才是奇怪的现象。 过去的经历告诉我,即使是0.01/0.02mm的内径差异,就有可能造成支柱开裂。 因此,我们务必按照塑胶螺丝供应商提供的支柱设计指南,一成不变的支柱。 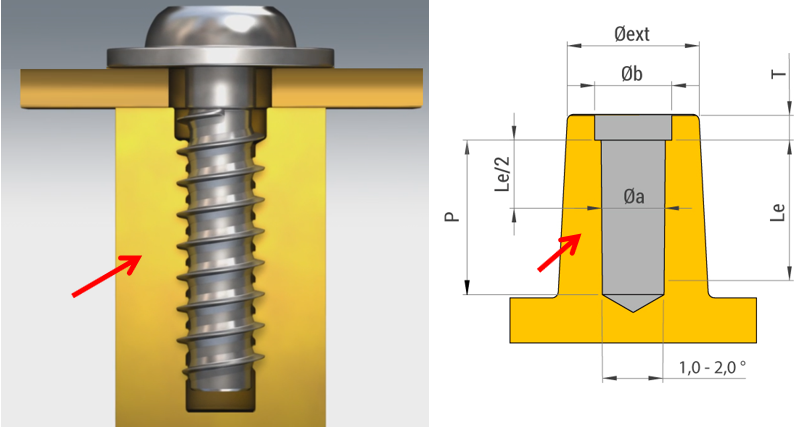
用一句话来总结支柱开裂的机理是:当支柱承受的径向力超过了其承受的极限时,支柱发生开裂。
塑胶件在注塑成型过程中,因为分子链的取向和冷却收缩不一致等原因,会在塑胶件内部产生内应力。
而更多的时候,内应力并不会在塑胶件表面产生痕迹,但是一旦受到外力的作用,就会发生开裂。 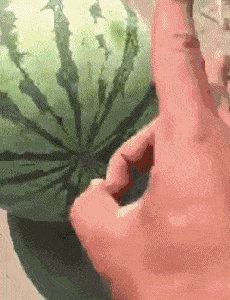
▲西瓜的内应力
螺丝支柱处因为模具结构较为复杂,也比较容易产生内应力。当内应力存在后,螺丝拧入时产生的径向力就会导致支柱开裂。 而支柱根部断裂则更是因为内应力的存在,为此,支柱与零件壁的连接处必须添加一定的圆角。
螺丝支柱在注塑成型过程中、在产品组装过程中、在存储和运输过程中、在使用过程中等如果碰到化学试剂,例如脱模剂、冲压油、润滑剂、以及酒精等,因此而发生环境应力开裂。 一个案例是因为塑胶件很硬,螺丝很难拧紧,而使用了润滑剂来辅助螺丝的组装。 润滑剂确实可以辅助螺丝的组装,但是几个月之后,有的螺丝支柱破裂了。 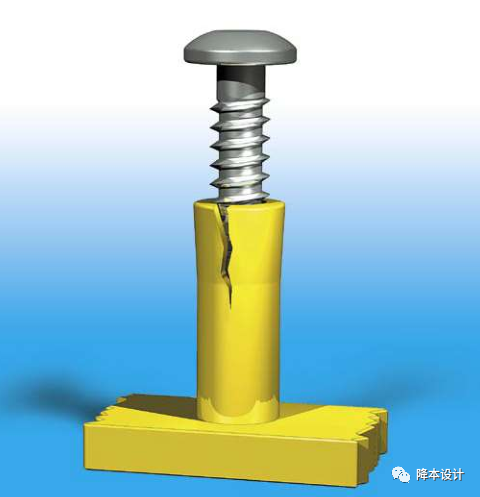
▲支柱因为接触润滑剂而开裂