面向装配的设计(Design for Assembly, 简称DFA)是指在产品设计阶段设计产品使得产品具有良好的可装配性,确保装配工序简单、装配效率高、装配质量高、装配不良率低和装配成本低。
特别是对于产品成本的降低,经过近年来在实际咨询项目中的实施,DFA已经证明了是降本设计中强有力的工具。
而DFA在产品开发中的实施和落地依赖的是一条一条的DFA设计指南。
DFA设计指南1.0是2011年在《面向制造和装配的产品设计指南》第一版中发布。经过十年的实际应用和众多工程师反馈,我对DFA有了更深的认识。
在本文中,我将发布DFA设计指南2.0,新的DFA设计指南更加结构化和层次化,更容易实施和落地。
后续有机会我会在《面向制造和装配的产品设计指南》第3版中更新。
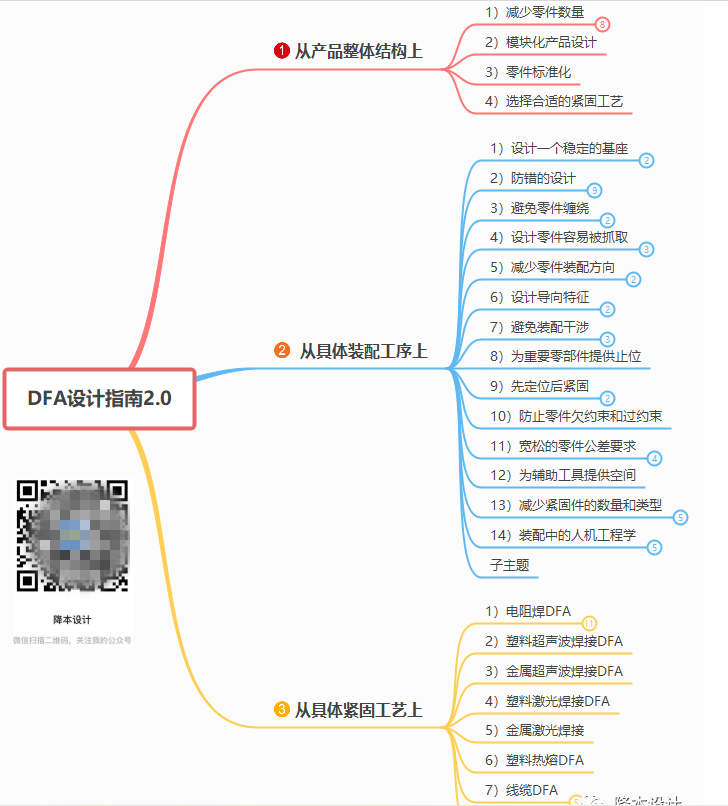
这是《面向制造和装配的产品设计指南》一书中发布的DFA设计指南1.0,总共包括18个DFA设计指南大类,每一大类下面还有具体的指南细节,总共近80条。 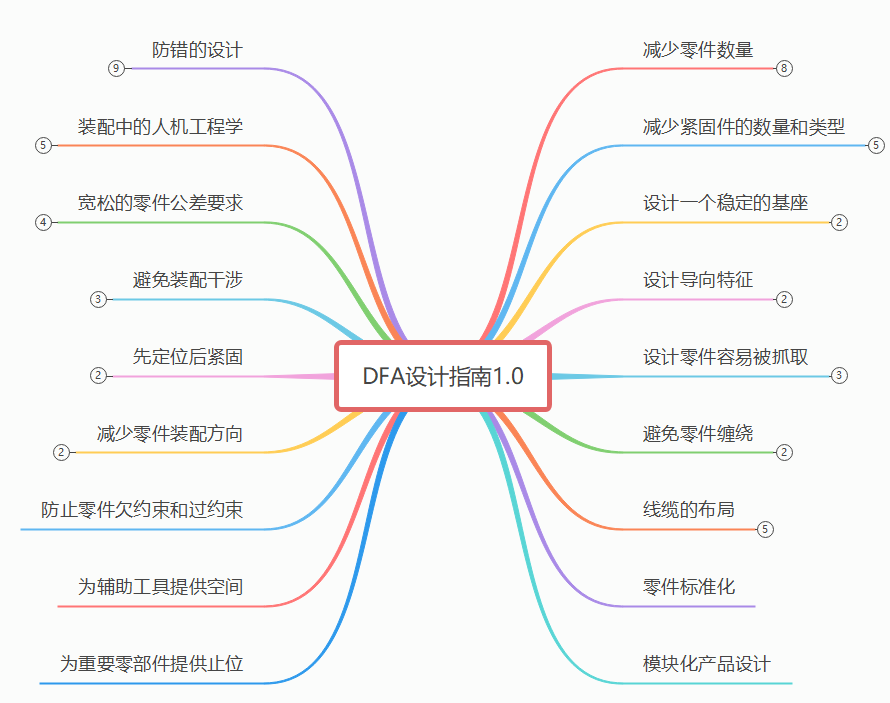
为什么我要升级DFA设计指南?,这主要是因为两方面的启示:
在《金字塔原理》一书中,一篇文章、一份报告、一本书或者一个知识体系等,其内在结构需要遵循四个基本原则:
以上统下:每一层次上的思想必须是对下一层次思想的总结概括。即:主题是下一层次维度的总结概况,维度是下一层次维度或者要点的总结概况。
归纳分组:每一组中的要点或者维度必须属于同一逻辑范畴。
逻辑递进:每一组中的要点或者维度必须按照逻辑顺序排列。
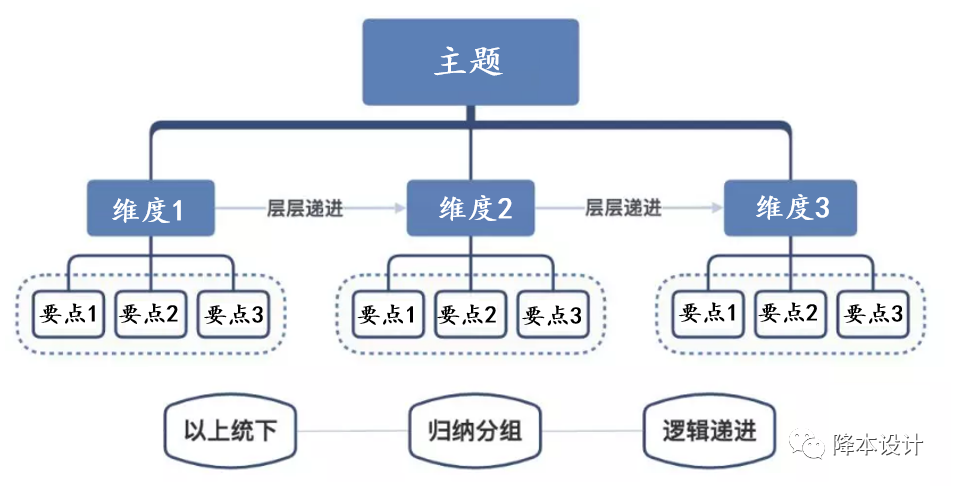
MECE法则:MECE法则,全称Mutually Exclusive Collectively Exhaustive,中文意思是“相互独立,完全穷尽”。
对于一个重大的主题,通过MECE分析法,进行不重叠、不遗漏的分类,从而能够借此有效把握问题的核心,并解决问题。
MECE法则包含两点,第一点是完全穷尽,第二点是相互独立。

如果我们用金字塔原理四个基本原则去对比DFA设计指南1.0,我们会发现有三个主要问题: 1)18类设计指南之间没有归纳分组,仅仅是罗列在一起,看上去比较繁杂; 2)18类设计指南之间没有逻辑顺序;重要性顺序?时间顺序?还是空间结构顺序? 3)DFA设计指南没有穷尽。例如,针对具体紧固工艺的DFA如电阻焊接等,并不在其中。 没有分组和逻辑性,这不利于读者和工程师的理解、以及准确地应用在产品开发中。 没有穷尽,那么就有可能造成产品开发中我们都完完全全遵守了DFA设计指南1.0,然而还会产生装配问题。
有很多读者和工程师向《面向制造和装配的产品设计指南》一书提出了宝贵建议。
在培训和咨询的过程中,我也收到很多非常有价值的反馈。其中一位工程师专家指出,DFA设计指南应当按照装配工序的具体时间先后顺序过程进行,这样会更加有效。 也期待更多的工程师提供建议,让我们一起为中国制造添砖加瓦。
按照金字塔原理,在DFA设计指南2.0中,我把各个设计指南分为三个维度。 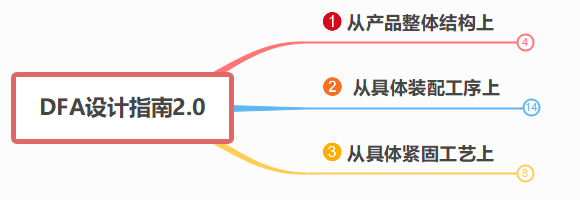
这是宏观上或者广义上的DFA,我们称这一维度DFA设计指南为宏观DFA设计指南。 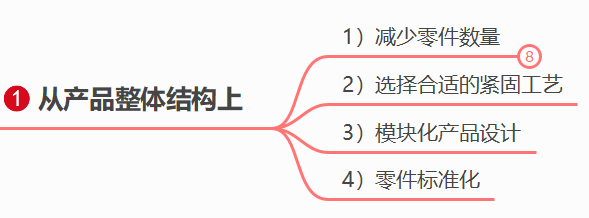
宏观DFA设计指南,是针对产品的整体结构,不是针对具体的装配工序。 这就要求在我们使用宏观DFA设计指南时,需要站得更高更远,需要具备全局观和大局观。 例如,对于产品整体结构,我们需要尽量去“简化产品设计、减少零件数量”,那么我们就针对多个零部件进行思考和分析,看看是否可以把多个零部件合并为1个零部件,以使得产品的整体装配效率更高、成本最低。 从产品整体结构、宏观层面上优化产品的可装配性,对产品的质量和成本的帮助最大,远远超过微观上DFA优化。 从降本设计的角度来说,宏观DFA是降本的最最有力的工具。 相应的,这要求工程师具备较高的设计水平,需要熟悉多种制造工艺和装配工艺,需要具有DFA和成本意识。 这是微观上或者狭义上的DFA,我们称这一维度DFA设计指南为微观DFA设计指南。 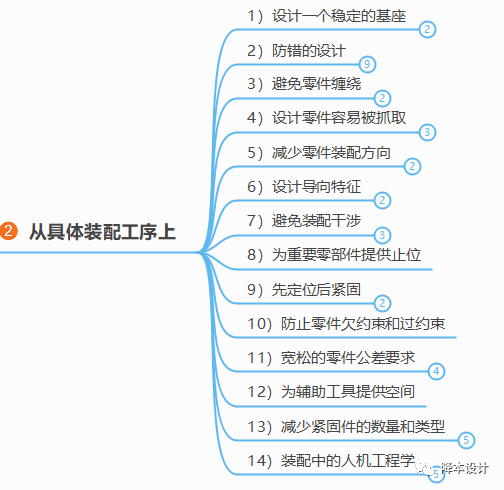
针对每一个装配工序的每一步具体的细微动作,通过微观DFA设计指南,确保每一个动作都是效率高、质量好和成本低等。 同时,因为装配工序每一步动作具有时间先后顺序;相应地,微观DFA设计指南也按照时间先后顺序进行排序,力求让二者具有大致的对应关系。
例如,装配工序的第一步动作是放置好基座零件,那么对于这一步,我们需要微观DFA设计指南“设计一个稳定的基座”,避免基座零件在装配过程中发生晃动,而对装配质量产生影响。 第二步动作是识别需要装配的零件,对于该零件需要遵循设计指南“防错的设计”,这个零件不能与其它零件相似,避免难以识别。 第三步是零件抓取,这一步我们需要“避免零件缠绕”,否则拆分困难。同时,还需要“设计零件使得零件容易抓取”,避免零件太小、太滑、太尖等。 总之,我们把微观DFA设计指南,按照与装配工序过程的相同的时间先后顺序进行排序,让每一个或多个设计指南对应每一步或多步的装配动作。 这会让DFA设计指南更加容易理解,也更容易实施和落地。 当然,这里的对应,只能是理论上的大致对应,很难做到精准的一对一对应。 因为,同一个设计指南,可能会适用装配工序的几个动作。同一个动作,几个设计指南都使用。 例如,设计指南“防错的设计”,在零件识别时需要防错,然而在零件调整到正确位置时,也需要进行防错。 宏观DFA设计指南和微观DFA设计指南属于通用型DFA设计指南,只要存在装配动作,他们都能够适用。 然而,针对紧固工艺,例如电阻焊、超声波焊接、激光焊接和热熔等,它们的原理不同、使用设备不同,对DFA的要求也不同。 于是,我们在DFA中产生出第三个维度,即针对具体紧固工艺的DFA设计指南。 每一种紧固工艺,在遵循通用型DFA指南的基础上,还有着自身特别的DFA设计指南。 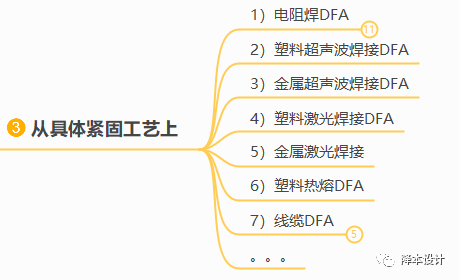
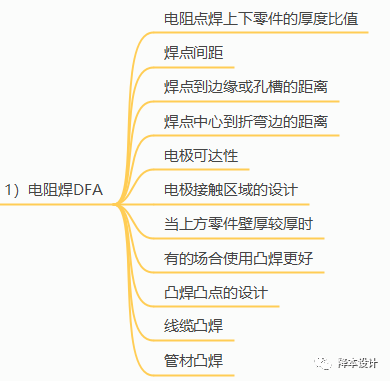
否则,我们仅仅遵循通用型DFA设计指南,而任意设计零件,不去考虑针对电阻焊特有的DFA要求,就容易出现质量问题。 如图所示,把较厚的零件放在较薄的零件上进行焊接,容易使得电流在两个电极和上方板材形成回路,而不经过下方零件,产生分流现象,造成焊接失败。 我们需要遵循电阻焊DFA设计指南之“当上方零件壁厚较厚时”:可以在上方零件上增加缺口,以避免分流现象,同时增加凸点,凸点有利于聚集焊接能量。 不过,针对具体紧固工艺的DFA设计指南还不成系统,网上的资料也不够全面。这些知识还停留在相关行业专家的脑海里。 DFMA检查表是DFMA实施和落地的工具。在产品开发重要关口,利用检查表进行把关,避免不符合制造、装配和成本的设计流入到模具设计制造、生产线规划加工环节。 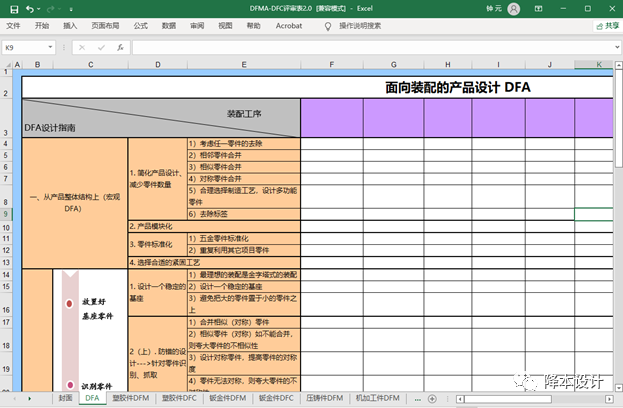