模内埋置螺母有很多种规格,要选择出最合适是一种可不是一件容易的事情。如图所示规格,应该是大家经常选用的一种。
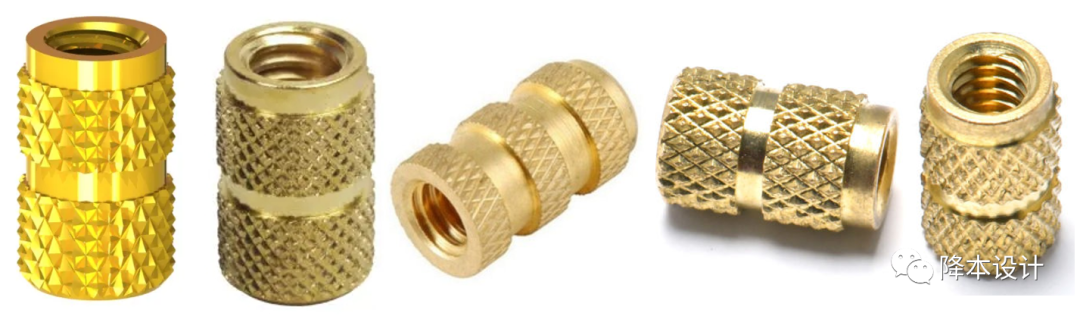
它们具有两个典型细节特征:
1)滚花纹路为钻石型
2)螺母首尾不对称设计
然而,这种常见规格的螺母,一定是模内埋置最好的选择吗?
在模内埋置时,会存在三方面风险:
1)产生内应力,造成支柱开裂
2)不对称设计,增加防错成本
3)滚花纹路相互碰撞而产生金属碎屑,造成注塑停机
钻石型滚花纹路的众多尖端,在注塑成型时,产生无数个应力集中点,在螺丝拧紧时外力作用下,很容易使得支柱开裂。 在塑胶件DFM设计之中,一个最基本的设计指南是避免尖角。在注塑过程中,塑胶熔料在尖角处的流态发生急剧变化而产生较大内应力,并残留在尖角处,这就是应力集中。 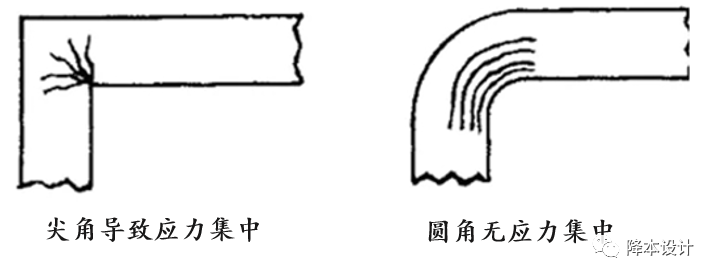
应力集中处在外力的作用,很容易发生断裂。如图所示的一个塑胶件,就是因为尖角的存在而发生了断裂。 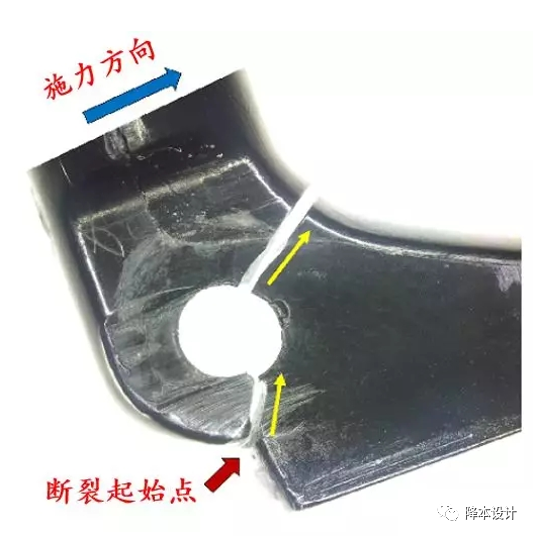
而钻石型滚花纹路尖端,在塑胶件支柱中就形成了无数个尖角,尖角处应力集中。如果螺母没有预热使其膨胀,这会导致塑料更大的收缩,更增加应力集中的程度。 而在螺丝拧紧过程中,支柱不可避免的会承受到外力;或者在温度变化时,因为塑料和金属的热胀冷缩系数不一致,也会产生外力。 如图显示了一个塑胶件支柱的剖面,从图中可以看出,其开裂处正是埋置螺母滚花纹路的尖端。
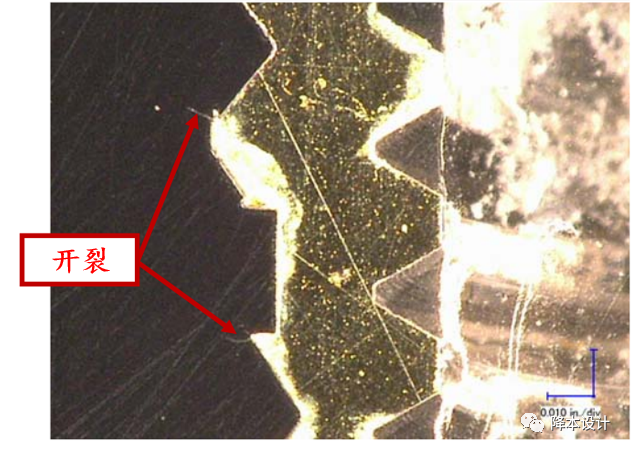
因此,对于模内埋置螺母来说,钻石型滚花纹路并不是最好的选择。对于半结晶塑料和热固性塑料,这可能不是问题。 然而对于某些无定型塑料,例如PC、ABS等,这可能就非常致命,支柱发生开裂的现象不可避免。 针对这一风险,其实有更多的非钻石型滚花可供选择,例如直螺纹、左右螺旋纹、圆弧纹,以及较大较深的滚花纹路和凹槽等,特别后两种滚花的应力最小。 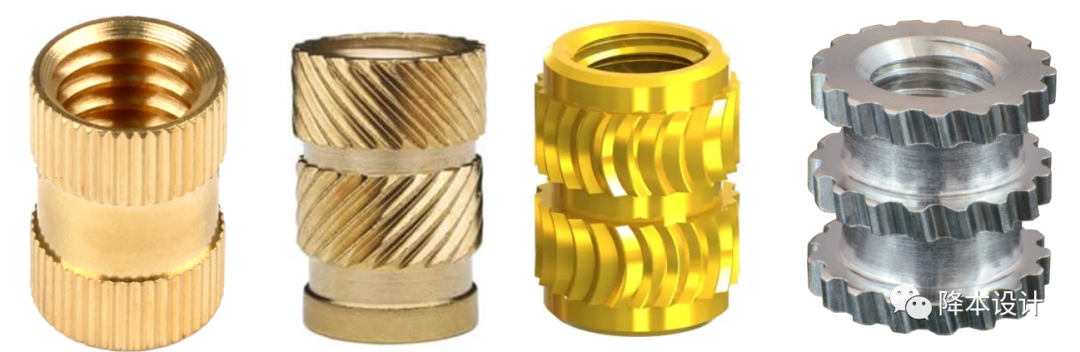
▲避免钻石型螺母
在模内成型时,埋置螺母是通过定位针放置于模具中,然后合模开始注塑成型。
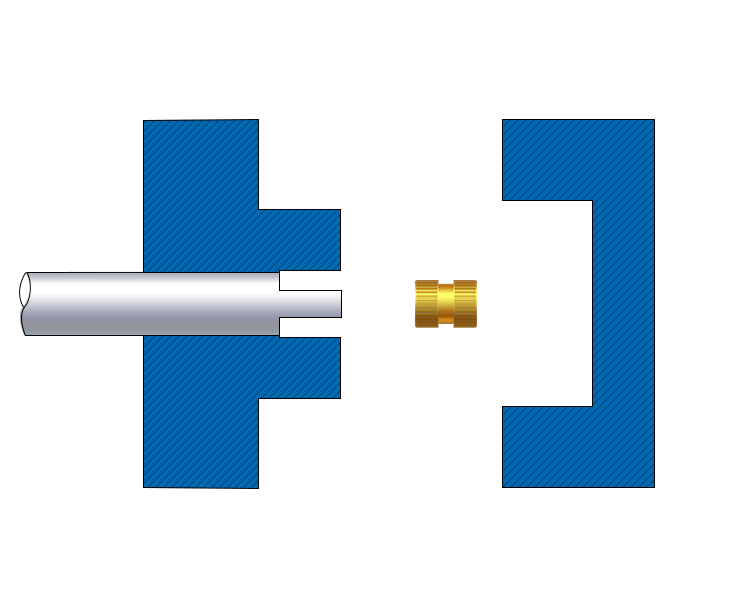
埋置螺母的首尾两端不对称,即不防错,这将带来很大的问题。
因为一旦把埋置螺母首尾放反,那么埋置螺母很有可能与模具发生干涉,合模时把模具损坏;或者,即使放反后不影响合模,能够正常注塑,然而成型后螺母首尾不一致,造成整个塑胶件报废。
如果采用人工放置,这一方面因为埋置螺母本身尺寸较小,同时首尾两端的不对性较小(即很难一眼看出首尾),使得操作人员很难辨别首尾,增加放置时间。而放置时间的增加,则意味着注塑成型周期的增加,产品成本增加。 而如果采用自动化生产,使用设备或机器手放置,则需要增加额外的调整首尾方向的设备投资。 如果在设计允许情况下,使用首尾对称的埋置螺母,这样就不必区分首尾,不用担心防错,自然就会避免防错成本的支出。 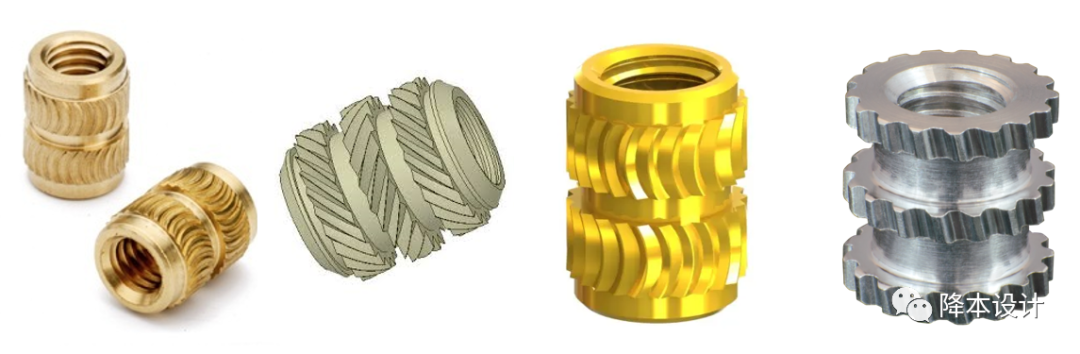
在运输、在自动化上料过程中,由于钻石滚花纹路的尖端较细较小,容易因为互相碰撞而产生金属碎屑。 ▲振动盘上料过程中零件会互相碰撞(示意图,零件非埋置螺母) 这些碎屑如果被带入到注塑模具中,就很容易造成合模问题或其它质量问题,不得不进行停机检修。 为了避免碎屑进入到模具中,可能需要在输送线的底部增加一层网,起到筛子的作用,碎屑在上料过程中通过而落下;然后再在下一层增加胶粘剂,以收集碎屑。 更好的办法是直接更改螺母的钻石型滚花纹路,使用较大纹路,例如螺旋纹、圆弧纹、或者较大较深的其它滚花纹路和凹槽等均可。 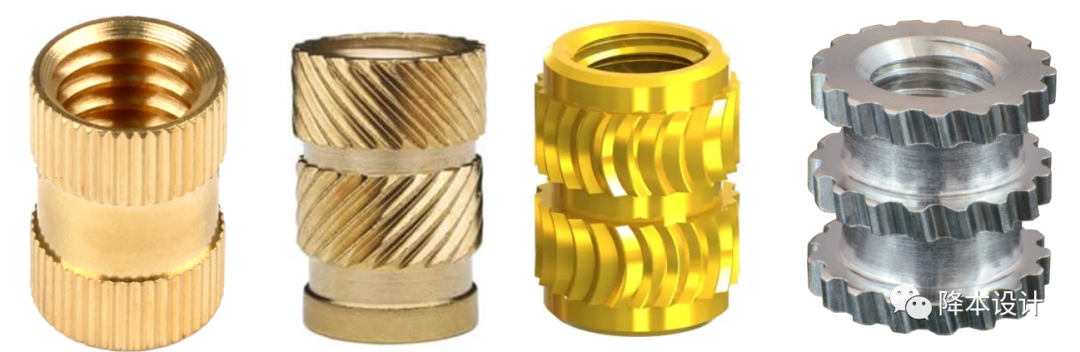
▲较大纹路的螺母
产品结构设计的成败,往往就在于细节,这些细节可能是零件上的某一个特征,可能是某个0.01mm尺寸的设计。
而准确把握细节,并不在于我们把这些细节知识点死记硬背、熟记于心。
再强的大脑,也没办法记住所有的细节。
我们需要反其道而行之,放弃记住所有细节,给大脑减负和预留空间;通过建立相关知识体系,框架化和结构化,降维打击,我们才能把细节做好。
正如我在上一篇文章中所做的事情:
如何系统化、逻辑化地进行埋植螺母的结构设计?
----END---
来源:降本设计