埋置螺母支柱开裂,这应该是在产品开发中最经常碰到、最棘手的问题之一。
螺母埋置之后,支柱都好好的,一拧螺丝就开裂、或放置一段时间开裂、或可靠性测试时开裂、或冬天开裂、或北方开裂、或客户使用过程中开裂。
出现这样的质量事故,轻则生产线停线、延误交期,重则产品召回,给企业带来不可估量的财务损失和品牌信誉损失。
更让人头痛的是,造成支柱开裂的潜在原因众多,而且不易察觉、一个微小的异常就会造成开裂。
要在限定时间内找到解决方案,并不是一件容易的事情。
好好的支柱,怎么就这么容易开裂呢?一点武德都不讲。
本文将从塑料(Resin)、螺母(Insert)、设计(Design)、工艺(Manufacturing)、环境(Enviorment)等五个维度来分析支柱开裂的N个潜在原因。
我把五个维度的首写字母,命名为RIDME模型。
希望工程师以后碰到此类问题,按照RIDME模型的五个维度去思考验证,就能轻轻松松、顺顺利利的把支柱开裂缺陷干掉,找到解决方案。
Rid of me,支柱开裂缺陷似乎在向工程师挑衅:I‘m here, 不服就来干掉我啊。
所以,RIDME模型的中文名就是干掉我模型。
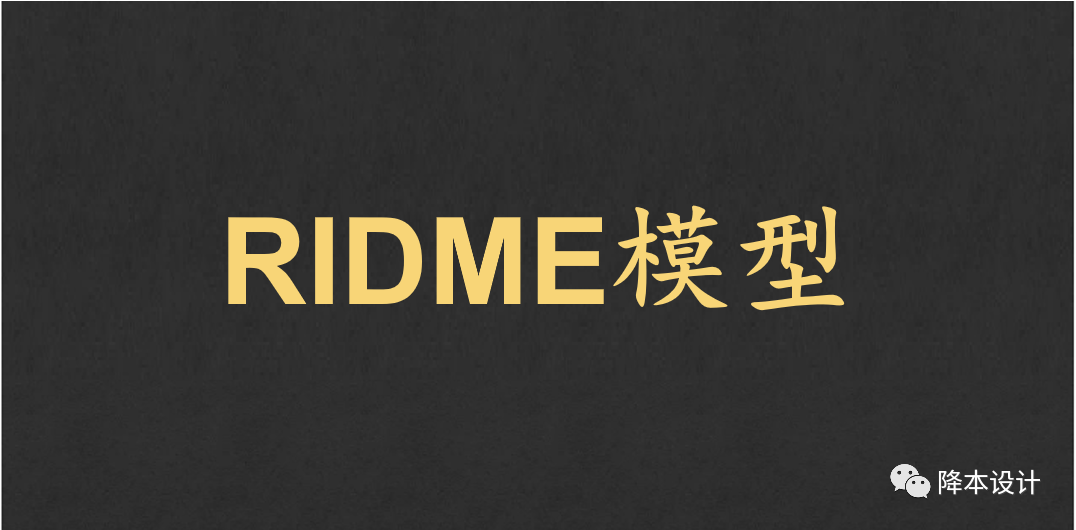
在微 信群、在QQ群、在网络论坛上,经常看到工程师在求助埋置螺柱支柱开裂的问题:
PC+ABS材料,螺丝柱外径9,内径4.6,热熔外径5的M3铜螺母,长度不一,放置久了后螺丝柱子出现应力开裂,请问有遇到类似问题的吗,怎么解决?
注塑成型之后好好的,放置一段时间之后,做高低温测试,有的支柱就开裂了。
为什么塑胶螺丝柱包铜螺母老是爆裂?注塑当时不会出现爆裂,要经过一段时间才会出现爆裂的现象 这个问题使我们很头疼!!求解
已经量产一段时间了,支柱一直没有发现开裂现象。然后新一批产品,突然就有开裂现象发生了。
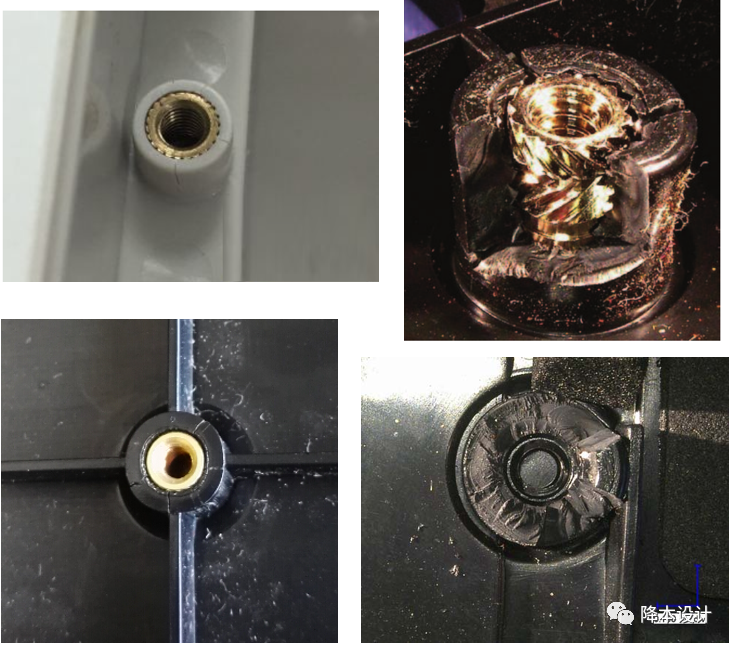
▲支柱开裂的各种情形
有的工程师,冷不丁发一张开裂照片,配上简单描述,就让我帮忙提供解决方案?
我又不是大仙,怎么可能靠一张照片几句话,就知道解决方案呢?


解决支柱开裂问题,并不是一件轻易而举的事情,我们不能靠仅仅靠经验、靠猜测、靠试错去解决。我们必须做到以下两点:
1. 掌握螺母支柱相关知识
在开始具体解决问题之前,我们必须掌握埋置螺母支柱相关结构设计知识的方方面面。这就是我们常说的“磨刀不误砍柴工”。
如果我们没有掌握相关知识,就去着手解决问题,那就会一脸抓瞎,无从下手。
有的工程师会说:时间紧迫,根本上就不允许我去一点点收集资料、从头开始学。
好消息是,埋置螺母相关结构设计知识我已经整理完毕,你只需要花1个小时仔细阅读即可。
推荐阅读:
如何系统化、逻辑化地进行埋植螺母的结构设计?
2. 结构化的解决思路--RIDME模型
碰到埋置螺母支柱开裂等复杂问题,我们必须依靠结构化的解决思路,而不是东一榔头、西一棒槌。
我经常看见的一个错误问题解决情形是:工程师在微 信群求助支柱开裂。有的群友说是支柱尺寸问题,工程师就去测量支柱尺寸;有的工程师说,是不是回料添加多了,工程师就去检查回料。。。。
按照这种方式,除非运气好,否则我们很难在短时间内解决问题。
在对埋置螺母支柱开裂众多问题的分析基础上,我提出了一个结构化的解决模型--RIDME模型。
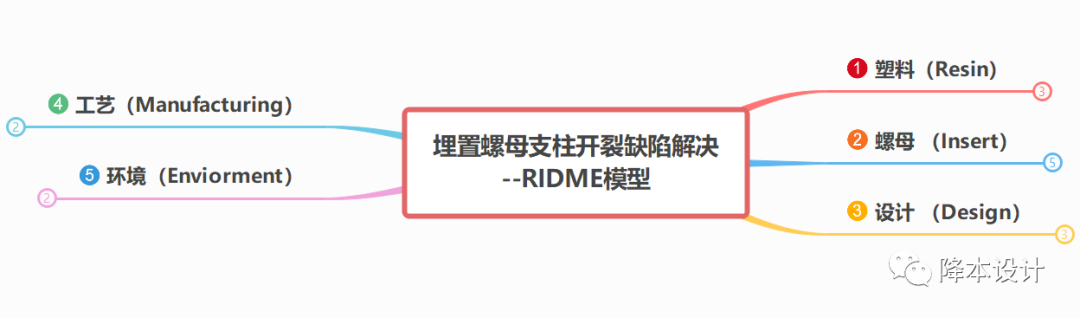
RIDME是埋置螺母支柱开裂问题的五个维度塑料(Resin)、螺母(Insert)、设计(Design)、工艺(Manufacturing)、环境(Enviorment)首写字母的组合,每个维度下面分别包含若干个解决思路。
当我们碰到埋置螺母支柱开裂问题时,我们就可以按照RIDME模型,分别从塑料、螺母、设计、工艺和环境等五个维度去分析问题。
这五个维度排列分先后,然而在分析问题、解决问题的时候,我们可以同时进行,然后针对当前的事实和数据,列出解决方案的优先顺序,然后逐一实施。
通过RIMDE模型,我们看到的解决方案不是一个、两个,而是五个维度下的无数个解决方案,这就会避免根本原因的遗漏。
通过RIMDE模型的结构化问题解决方式,我们才能在短时间之内解决螺母埋置支柱问题。
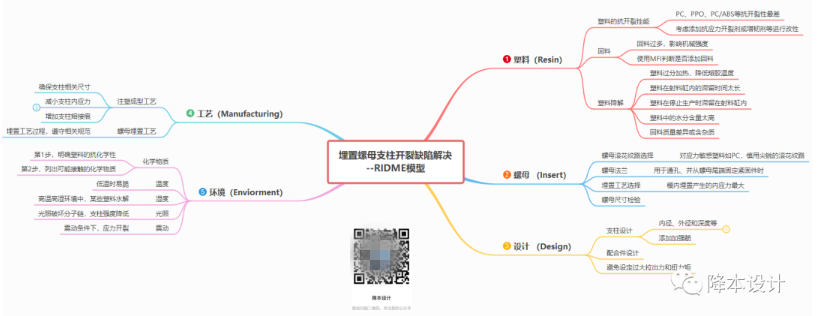
RIDME模型的第一个字母R、或者第一个维度指Resin,塑料。 我们常常碰到的一个现象是,原来用一种材料,没有开裂现象;换一种材料,就开裂了。就是因为塑料的抗开裂性能不一样。 而即使是同一种类型的塑料,由于其配方不同或者填充剂不同,其发生支柱开裂的可能性也存在区别。 当支柱开裂发生时,我们可以考虑同一类型塑料其它不同规格,也可以考虑添加抗应力开裂剂或增韧剂等进行改性,以提高塑料的抗开裂能力。 当使用其它方法都难以解决支柱开裂时,我们可以考虑更换塑胶材料。如果塑胶材料不能替换,至少考虑一下是否可以增加应力开裂剂或增韧剂等。 支柱开裂的原因之一是塑胶材料之中添加了过多的回料。 在当前塑胶材料价格大幅上涨的情况下,同时企业对供应商原料管控不到位时,添加过多回料来降本非常常见,然而这种方式往往蕴藏着风险。 回料对零件机械性能会有影响,其冲击强度、抗拉强度、压缩强度、弯曲强度和剪切强度等、以及耐老化性能随着回料含量的增加而降低。 这是由于回料至少多通过一次注塑成型机的机筒,经历过“加热->熔融”工序,与新料相比,有可能因加热已使树脂分子量降低或添加剂减少。 而且,螺杆的转动给注塑机筒内树脂施加了很大的外力,使得固体填充材料因折断或残缺而变小,特别是玻纤和碳纤等纤维状填充料一折就断。 下图显示了某品牌玻纤增强PBT材料,其某些机械性能随着再生次数逐步降低。
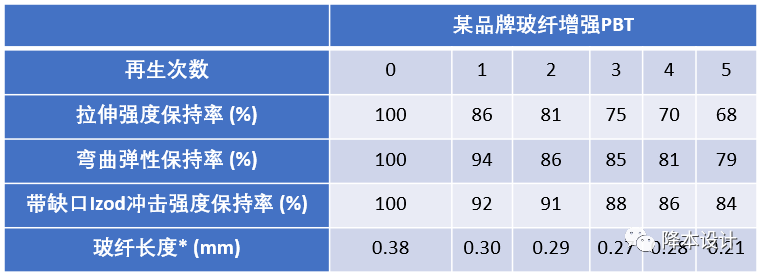
一个常见的方法是测量塑料的熔融指数。熔融指数(Melt Flow Index,MFI),全称熔液流动指数,或熔体流动指数,是指一种表示塑胶材料加工时的流动性能的数值。
具体测试方法为:在一定的载荷(Kg)及温度(°C)下,用指定的时间(10分钟)经过一定直径的管子所流出来的融胶重量(克数)。MFI值越大,表示塑料的流动性越好;反之,则流动性越差。 如果塑料中添加了过多回料,那么MFI值会比成型前塑料MFI值高50%以上。 如果塑料在注塑过程中,由于温度过高或者含水量过高等发生了降解,那么塑料性能会明显降低,支柱容易开裂。
一般来说,我们只需要按照塑料供应商推荐的成型参数等进行注塑,就不会发生降解问题。
RIDME模型中的第二个字母I、或者第二个维度是指Insert,Insert for plastic,螺母。 关于螺母,我们需要关注的是滚花纹路选择、法兰和埋置工艺的选择。 螺母滚花纹路的尖角,埋置时会在塑料中产生内应力。这对半结晶塑料和热固性塑料的影响可能不大,对于无定型塑料就比较致命。 例如下图中,第二种钻石型滚花螺母最容易造成支柱开裂。 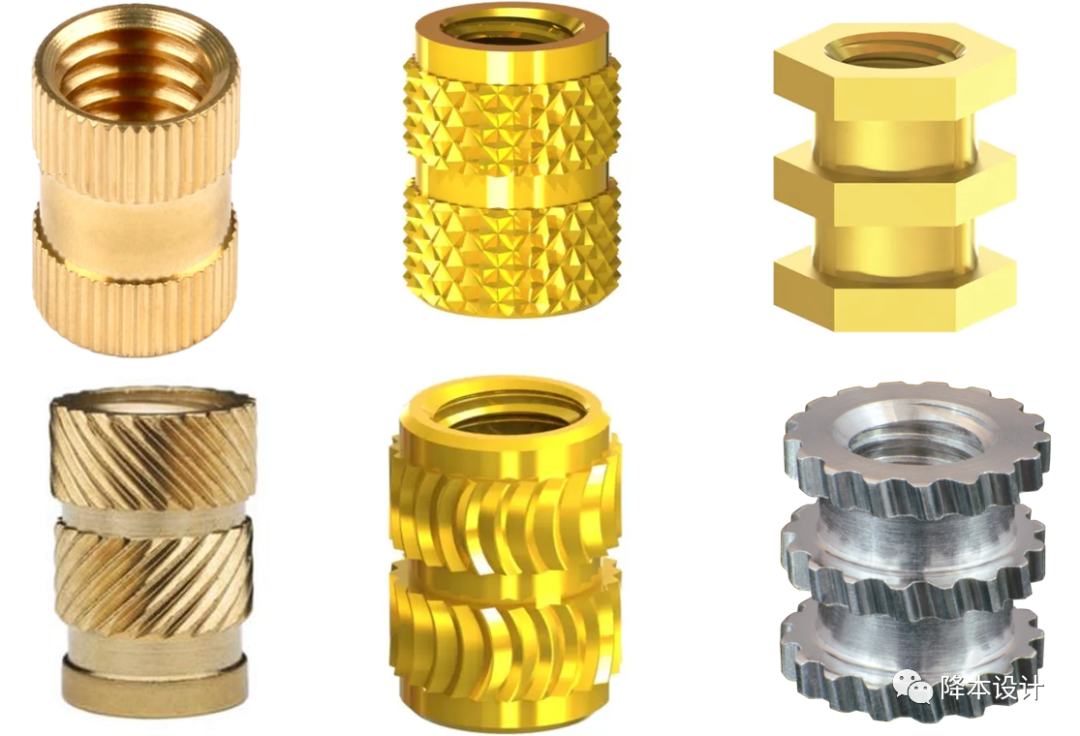
当塑胶件支柱是通孔、并从螺母尾端固定紧固件时,需要选择头部带法兰的螺母。非法兰螺母特别是带锥度的螺母很容易在拧紧时因为直接承受载荷,轻则造成支柱开裂,重则造成螺母被拔出。 埋置类型的两大类型工艺,模内埋置和注塑后埋置,对塑胶支柱产生的内应力不同。 一般来说,模内埋置产生的内应力比较大,注塑后埋置的内应力比较小。 如果是模内埋置造成的支柱开裂,我们可以考虑更换螺母类型,使用注塑后埋置,不过埋置螺母的拉出力和扭力矩的性能以及外观可能会有一定程度的降低。 通过测量,确认来料螺母的相关尺寸符合图纸尺寸要求。
RIDME模型中的第三个字母D、或者第三个维度是指Design,设计。 设计主要是指支柱内径、外径、孔深和加强筋等的设计、以及配合件的设计。
支柱开裂,有很大一部分原因是支柱相关尺寸不符合设计规范。 1)第1步:根据选定螺母类型,找到供应商提供的支柱设计规范 如图所示的两款螺母,分别清楚的标明了支柱的内径、外径、深度、斜度和圆角等的尺寸大小及允许的公差范围。 这一步的关键是千万不要自己臆想,按照自己的经验,内径应该多少外径多少。 因为每一款螺母都是独一无二的,其设计规范要求也不一样。 根据支柱设计规范,判断三维图中支柱的内径、外径、深度、斜度和圆角等是否满足设计规范,以及二维图中相关的公差标注是否一致。 需要检查,每一批次、每一穴、每一个支柱的尺寸,是否符合要求。然后再与开裂的支柱进行变量差异分析,有可能会找出潜在原因。 例如,第N穴中,某个支柱尺寸内径偏小,开裂了。而其它的没有问题。那说明支柱内径尺寸很有可能就是问题发生的根本原因。 可以去检查是因为模具本身此处镶针的尺寸不对,还是因为模具浇口流道的原因,使得此处充填过保。 壁厚较薄,大多数的支柱壁厚都在1mm左右。壁厚太厚,容易产生缩水等缺陷,反而会降低强度。
注塑成型时,支柱上无可避免产生熔接痕。熔接痕的存在会降低支柱强度,熔接痕处强度介于塑料本身强度的10%~90%。
埋置螺母过程中,螺母滚花纹路会导致支柱产生内应力,这也会降低支柱强度。
所以,我们必须千方百计的增加支柱的强度,一个常见方法是在支柱上添加加强筋;一方面补强支柱,另一方面把熔接痕引导到加强筋上,一举两得。
检查配合件螺丝孔的设计。如果螺丝孔设计不对,在把螺丝拉出的同时,也可能会造成支柱开裂。 拉出力和扭力矩,与支柱的抗开裂性,在某种程度来说具有跷跷板效应。 同一种螺母,在埋置方式确定的情况下,其所能达到的拉出力和扭力矩的上限已经确定。如果我们设定过高或者不切实际的标准,则必然要求减小支柱内径,这就增加了支柱开裂的风险。
RIDME模型中的第四个字母M、或者第四个维度,是指Manufacturing,制造工艺,我们需要对相关的制造工艺管控,包括注塑成型工艺管控和螺母埋置工艺管控。 确保每一穴每一个支柱的内径、外径和深度等,都在公差范围之内;当然,如果发现是模具问题,则需要修改模具。 通过注塑成型工艺参数的调整,确保支柱的内应力最小,特别是开裂的支柱; 对于模内埋置来说,对螺母进行预热是降低内应力的一个关键措施。 因为螺母预热后可减少高温熔料与螺母的温度差,在成型中可以使螺母周围的熔料冷却较慢,收缩比较均匀,发生一定的熔料补缩作用,可防止螺母周围产生过大的内应力。 当然,对于内应力,目前业内一个常见的处理方式是进行热处理。不过这种方式需要额外增加成本,不符合降本设计的思想,热处理不是解决支柱开裂的首选解决方案。 通过注塑成型工艺参数的调整,增加支柱熔接痕强度,特别是开裂的支柱; 如果支柱开裂的位置,刚好是熔接痕位置,那么我们更应该想办法去增加熔接痕的强度了。 螺母的埋置工艺,包括模内埋置、超声波埋置、热熔埋置、自攻埋置和压入埋置等,我们需要检查工艺是否按照螺母供应商指定的规范进行。
工艺过程中工装夹具设计、对齐与定位、工艺参数等设置不恰当,均有可能造成支柱开裂。 - 简单零件使用高度方向有绝热材料定位的通用工装;特殊零件制作相应的特殊热熔工装;
- 热熔前应抽检塑胶件支柱孔的直径和深度,必须符合规定的尺寸要求;
- 推荐采用 50W 的可调节温度的加热棒,加热棒使用附表推荐的温度接触铜螺母加热,加热时间为 7-10s;
- 支柱内孔软化时,支柱顶平面及外表面不得软化,将螺母垂直缓慢压入支柱,防止塑胶流动不充分,压入螺母后加热棒应快速垂直提起;
RIDME模型中的第五个字母E、或者第五个维度,是指Enviorment,即环境。 环境是指塑胶件在注塑、表面处理、装配、运输和使用过程中所处的环境状况,包括化学物质、温度、湿度、光照和受力等。 环境应力开裂(Environmental Stress Cracking, ESC)是指在内应力存在下,塑料树脂受化学物质作用发生的降解现象,最终导致塑料组分的损坏。这是一种溶剂诱导型的破坏,是化学物质和机械应力协同作用发生的裂解。 环境应力开裂并不是化学反应,化学物质并不会导致直接的化学攻击或者分子降解。实际上,是化学物质渗透到分子结构并损害了聚合物链的内分子力,从而加快分子断裂。 螺母在埋置过程中,特别是模内埋置,不可避免的在塑胶件支柱内部产生较大的内应力。而一旦支柱在任何环节中与化学物质接触,那么就有可能会发生环境应力开裂。 相对于金属,塑料的抗化学性能比较差。而不同塑料的抗化学性能存在差异。 最理想的状况是,我们找到塑料供应商,让他们提供塑料的抗化学性。 否则,我们只能根据产品在加工和使用场景中可能遇到的化学物质,逐一进行测试,以验证根本原因。 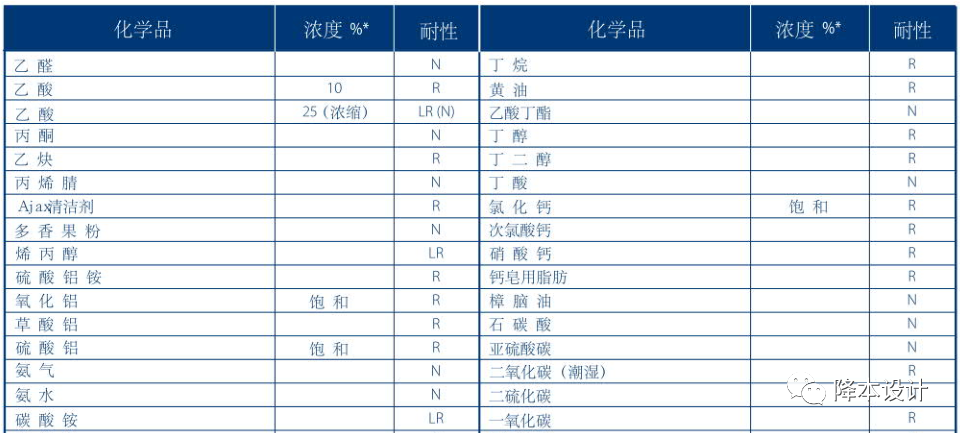
收集、整理塑胶件支柱从注塑成型开始、一直到客户使用环境中,可能接触到的化学物质,包括但不限于: 当然,这一步我们可以针对开裂支柱进行化学物质检测,检测上面是否残留化学物质。
当我们拿到第1和第2点的信息,逐一对照,就可以找到或排除是否是化学物质造成支柱开裂。 螺纹厌氧胶,常用于增加螺丝连接的锁紧防松性能,从而抗震减压,延长产品寿命。在螺丝上涂上厌氧胶后进行装配,固化后在螺纹间隙中形成强韧塑性胶膜,使螺丝锁紧不会松动。 如果锁紧零件都是金属零件,那么使用厌氧胶一般没有问题。 然而,我们有时就习惯性直接把用于金属零件的厌氧胶直接作用于塑胶零件上。那么塑胶支柱在厌氧胶中化学物质作用下,有可能会引起应力开裂。 其实,不少厌氧胶在其说明书中就明确指出该厌氧胶不能用于热塑性塑料。 附上一张塑胶件于化学物质接触而发生的开裂,我们可以看出化学攻击的威力性。 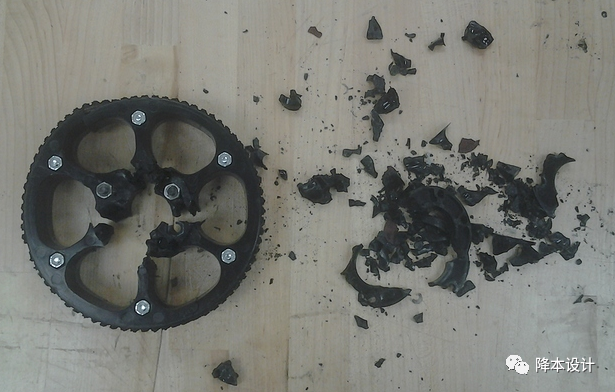
塑料是高分子材料,在常温时表现出硬而韧,在温度比较高的情况下会显示出韧性甚至弹性,一旦温度降低至其玻璃化温度或者脆点以下时,它就会显示出脆性性来。 对于埋置螺母支柱来说,在低温情况下会变脆,如果支柱内部存在内应力,那么低温开裂的情况容易发生。 1)产品夏天都好好的,一到冬天就有支柱开裂的现象发生; 2)产品在南方没问题,一到北方就有支柱开裂的现象发生; 在高温高湿环境中,有些塑料吸水之后会发生水解。在水解过程中,水分子会攻击聚合物的分子链并使其断裂,这会导致材料变脆开裂。当然,这种开裂可能不仅仅限于埋置螺母支裂。 会发生水解的塑料包括PBT、PET、PC、PA6、PA66以及POM等。 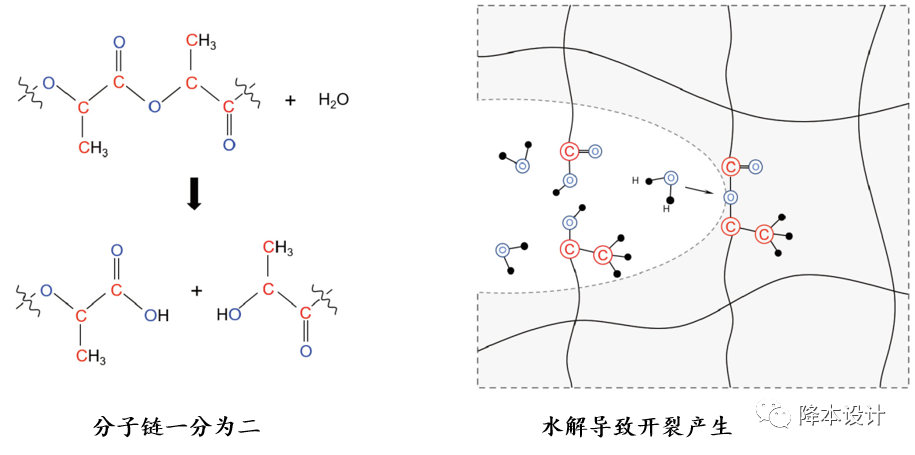
有的塑料不耐光照,紫外线辐射会导致塑料分子链的断裂,造成开裂现象。 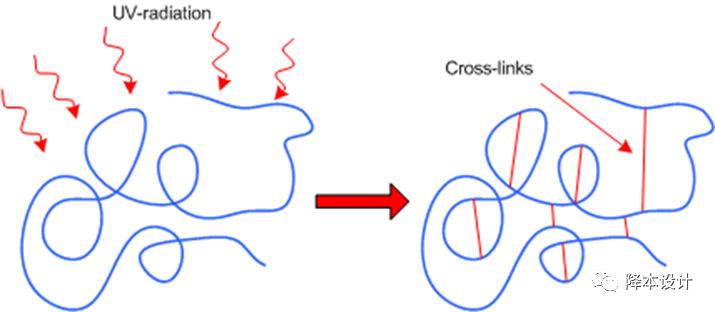
如果产品在使用环境中有震动,而塑胶件支柱中存在内应力,震动有可能会使得支柱开裂。