在设计塑胶件时,一个非常重要的关注点是尺寸精度是否达到设计要求。
如果达不到,则会带来各种各样的麻烦和问题,例如零部件装不上、装配之后外观间隙过大或过小、或者自攻螺丝支柱拉拔力过小、或者支柱开裂等等。
要解决这些麻烦和问题,幸运的话,通过注塑成型参数调整就可以实现。
而有些时候,仅仅调整参数无法解决问题,我们需要改模具结构、改塑胶件设计、或者更换塑胶材料,这必然导致产品成本增加以及产品开发周期延长。
还有少数情况是,以上方法都无法解决,我们不得不告诉客户,产品品质只能做到如此。
那么,我们如何避免后两种悲催情况发生呢?
我们需要系统化地去学习注塑成型的机理、理解影响塑胶件尺寸精度的相关因素、并通过结构化思维从塑胶材料、塑胶件设计、模具结构和注塑成型工艺等四个方面去提高尺寸精度。
在设计塑胶件时,在不增加成本的前提下,我们需要千方百计地去提高尺寸精度,因为尺寸精度高会带来诸多好处: 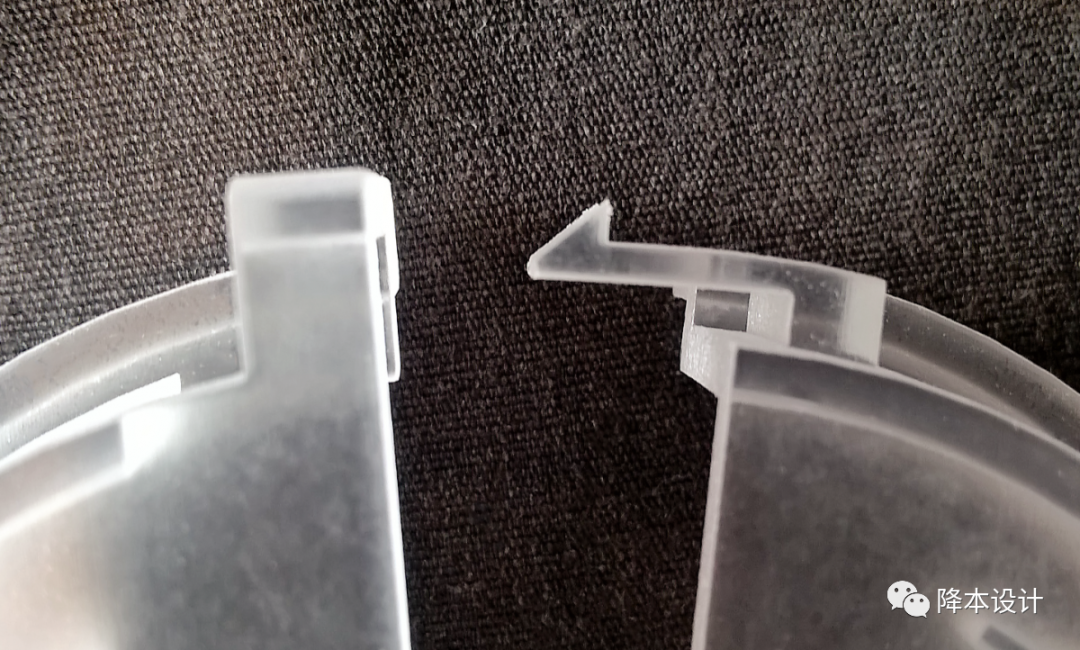
既然尺寸精度高有如此多的好处,是不是意味着我们可以不计成本地去提高精度呢?
显然不是,我们不可以随意做出高精密、甚至超过常规注塑成型制程能力的尺寸精度要求,因为这意味着高成本。 当注塑成型的尺寸精度要求过高、甚至超过注塑成型制程能力时,我们需要: 更精密的模具;
更精密的注塑设备;
更少的模穴数
更频繁的尺寸检测
更频繁的模具零部件替换
更高的不良率
避免高精度要求,体现在塑胶件2D图纸标注上,就是:2D图纸的尺寸公差标注要尽可能宽松,公差越宽松,成本越低。 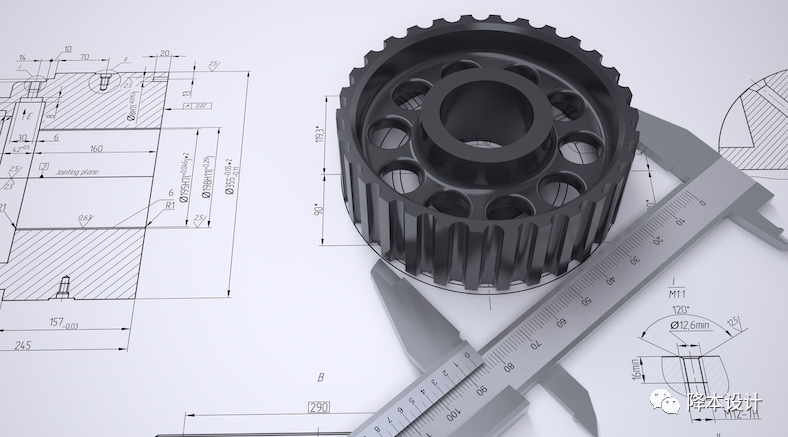
总之,我们在设计塑胶件时,需要想方设法去提高塑胶件尺寸精度;但是,我们不能对塑胶件尺寸精度提出精密要求,特别是超出制程能力的要求。
注塑成型时,常见的尺寸精度(即公差)标准有:
提高塑胶件注塑成型的尺寸精度,我们可以从塑胶材料、产品设计、模具设计和注塑工艺等四大方面入手。
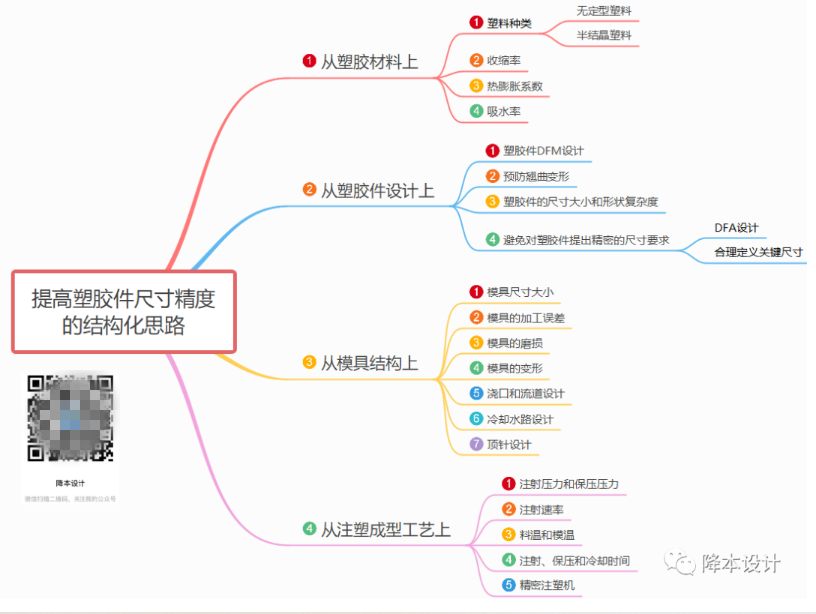
塑胶材料会严重影响塑胶件的尺寸精度。同样一套注塑模具,使用不同塑胶材料进行注塑成型,会得到不同的尺寸精度。 很多时候,在塑胶材料选择时,我们需要在尺寸精度和其它各种物理、化学、电气等性能与成本之间做平衡和取舍。 在塑胶材料中,有四个因素会影响塑胶件的尺寸精度,即塑料种类、收缩率、热膨胀系数和吸水率。如果塑胶件有较高精度的尺寸要求,那么我们可以从这四个因素入手,去选择合适的塑胶材料。 4.1 塑料种类
热塑性塑料可以分为无定型塑料和半结晶塑料两种。 相对于半结晶塑料,无定型塑料的尺寸精度更高。这是因为无定型塑料在加热熔化时保持非晶态,不会经历剧烈的体积变化,收缩较小。 而半结晶塑料在加热熔化时,经历了从结晶固体(致密堆积结构)到无定形熔融流体(低密度结构)的相变,导致体积变化较大。 不同塑料,具有不同收缩率。收缩率越高,就越难保证塑胶件的尺寸精度。 塑料收缩率是塑胶件在高热环境下模具中的尺寸与在室温冷却环境中的尺寸之差的百分比。例如PET的收缩率为2.0%-2.5%,PP塑料的收缩率为1.0%-2.5%,ABS的收缩率在0.3%~0.8%范围内。 所以,一般来说,相对ABS,PE和PP塑胶件的尺寸精度就越差。 下表显示了部分常见塑料的收缩率,表中数值仅供参考和对比。我们在选取塑胶材料时,可以要求塑料供应商提供物性表,在物性表中有准确的收缩率值。 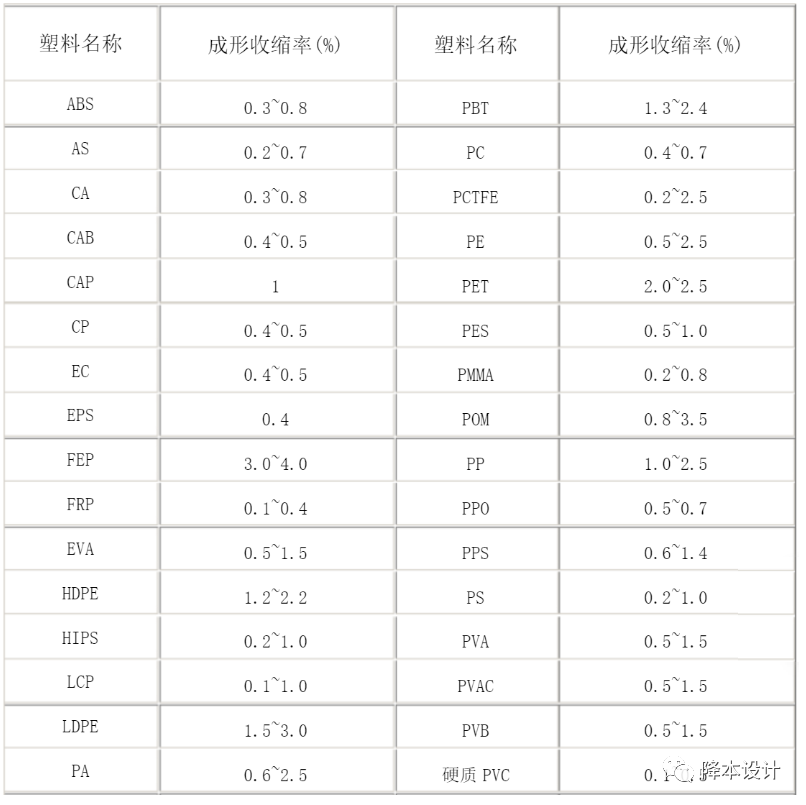
填料会极大影响塑料的收缩率。
玻璃纤维(GF)对塑料成型收缩率的影响最大。GF的加入首先是破坏了塑料的结晶度,影响收缩率;更重要的是GF限制了塑料的结晶收缩。当GF的质量分数达到30%以上时,塑料收缩率大幅降低。 矿物添加剂主要有碳酸钙、滑石粉、云母粉等也有较大影响。 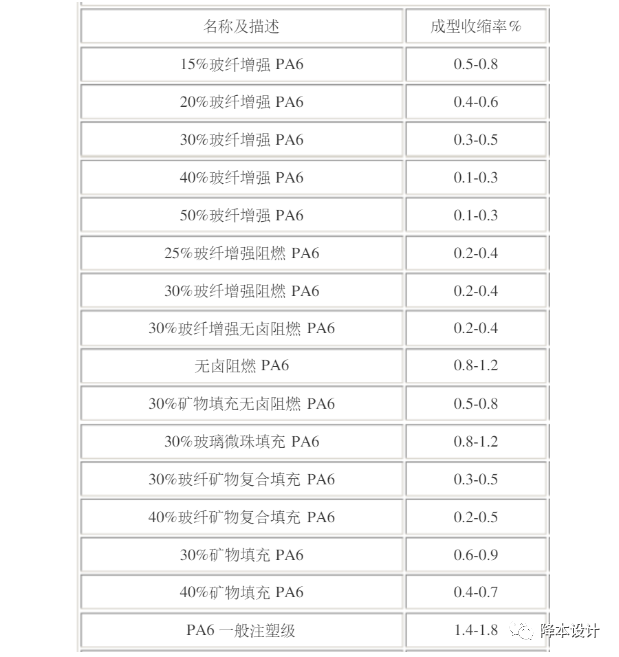
▲塑料PA6的收缩率--可以看出填料对收缩率的影响
大多数塑料都有较高的热膨胀系数(填料有助于减小该系数),塑胶件在使用环境中发生温度变化,那么塑胶件尺寸就会发生相应的变化。 特别是当塑胶件与其它材料(特别是金属)装配时,如果使用环境中的温度会发生极端变化,那么热膨胀系数应该是一个关键因素。 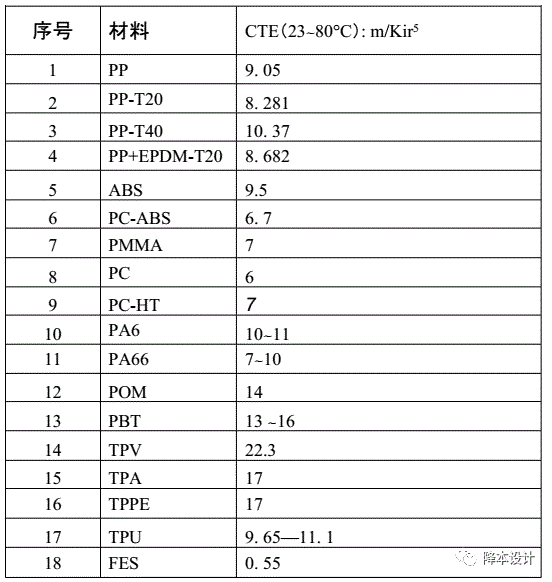
吸水率是指塑料在标准大气压力下吸水的能力。以塑料所吸收的水份来测量,并以百分数表示之。 吸水率会影响塑胶件的尺寸精度。吸水率高的材料,特别是尼龙,在吸水或湿度波动时会改变尺寸,机械性能也会发生改变。 例如,船用发动机中的油门连杆中使用了无填充的尼龙塑料;在湿热的条件下,尼龙连杆吸收了更多的热量和水分之后会变长,从而扰乱化油器的定时功能。解决方案是使用铝替代,顶端包胶注塑PBT。铝不仅重量更轻,而且热膨胀系数更低,这也与发动机缸体的热膨胀系数相匹配。
塑胶件设计,是提高尺寸精度的最关键环节,也是产品设计工程师可以掌控的环节。 工程师必须在产品设计阶段,准确预测塑胶件注塑成型时的尺寸精度,并通过各种优化方法去提高其尺寸精度,这样可以避免后期昂贵的改设计、改模具成本。 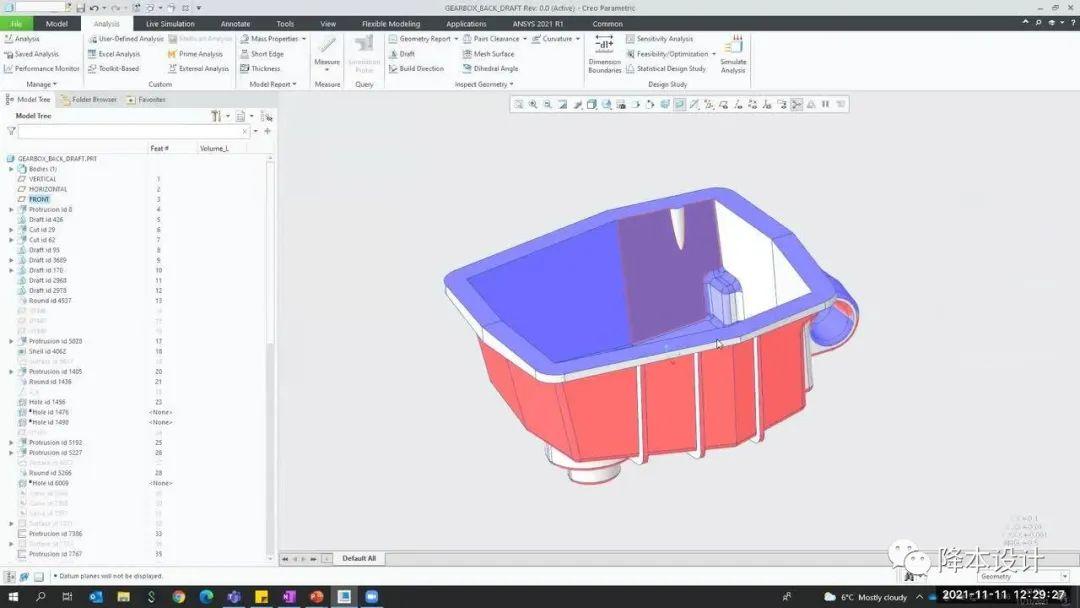
塑胶件设计,必须符合注塑成型的工艺要求,这就是Design for Manufacturing(DFM)。常见的塑胶件DFM设计指南包括零件壁厚、避免尖角、拔模斜度和加强筋等。
遵循DFM设计指南,减少注塑成型时的各种质量缺陷,也非常有助于提高塑胶件的尺寸精度。
以零件壁厚为例。DFM要求塑胶件的零件壁厚在一定范围之内,如果壁厚太厚,例如超过4mm或者5mm以上,塑胶件发生缩水缺陷,显然这会影响该处的尺寸精度。如果同时因此而发生了翘曲变形,那么更会影响尺寸精度。
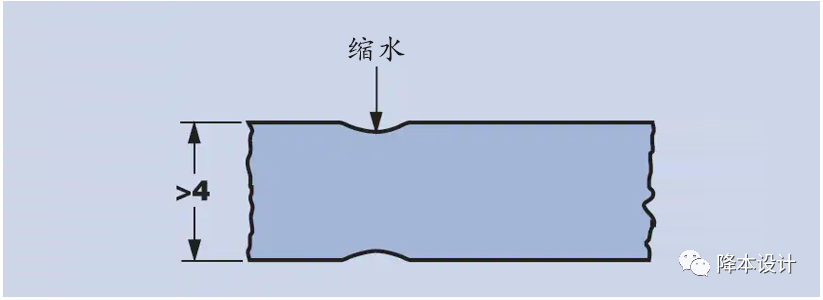
塑胶件在注塑成型时,很容易发生翘曲变形,翘曲变形的一大后果就是塑胶件的尺寸精度会大幅度降低。 为了提高塑胶件尺寸精度,我们需要预防塑胶件发生翘曲变形。
塑胶件尺寸越大,整体收缩越大,控制和保持精密公差就变得更具有挑战性。 塑胶件形状的复杂度会影响模具设计和材料流动,继而影响尺寸精度,因为快速充填、保持合适的模温和均匀冷却,均会影响到尺寸精度控制。 在DFA设计中,我们可以通过增加定位特征、缩短尺寸链等方法,来放松对零部件的公差要求。详情请参考《面向制造和装配的产品设计指南》一书。 在与塑胶件相关的DFA设计,我们也可以采取类似方法,从而允许塑胶件在注塑成型时即使尺寸精度比较低,也可以满足产品设计要求。 DFA设计,从严格意义来说,并不属于提高塑胶件尺寸精度。然而,我觉得这属于围魏救赵,可以变相达到提高塑胶件尺寸精度的目的。 DFA设计--增加定位特征、缩短尺寸链,这是我们在塑胶件设计时必须掌握的设计方法和技巧。 在同一个塑胶件中,不同尺寸的精度并不一样的,尺寸精度受到模具活动的影响。 如果尺寸均在同一个模具型腔中,该尺寸不受模具运动的影响,那么可以获得较高的尺寸精度;如果尺寸在两个型腔上(或者与斜销滑块上),这会额外存在两个型腔(或者与斜销滑块)的组装误差,同时还会受相互之间活动的影响,尺寸精度相对较低。
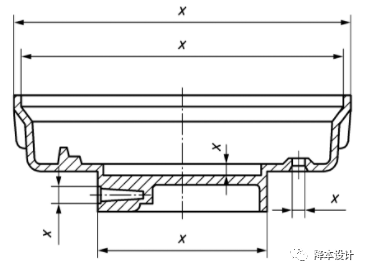
▲尺寸不受模具活动的影响
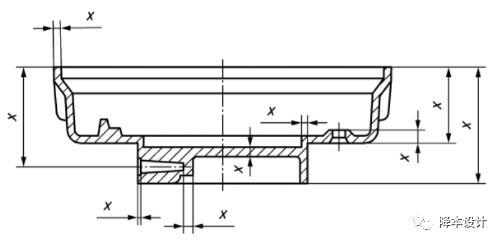
▲尺寸受模具活动的影响
所以,在设计塑胶件时,我们尽量把关键尺寸放置在不受模具活动影响的区域,这样就容易满足尺寸精度的要求。
精心设计的模具结构,对塑胶件尺寸精度,发挥着不可或缺的作用,这包括模具的尺寸大小、模具本身的加工误差、模具的磨损和变形、浇口流道、冷却和顶出机构等。 模具尺寸大小直接反映到塑胶件尺寸上,模具尺寸必须准确设计和加工。 由于塑料收缩率的存在,模具尺寸需要比塑胶件稍微大一些,模具尺寸设计最关键参数就是收缩率。这里有两点需要注意: 1)必须准确定义收缩率。如果收缩率定义错误,那么模具尺寸就会错误,塑胶件的尺寸相应会出错。而对于收缩率的准确定义,我们必须拿到塑胶材料厂商的原始数据。有些时候,如果塑胶件整体尺寸都偏大或偏小,可能的原因之一就是收缩率错误。 2)必须在模具设计一开始就确定收缩率,即一开始就确定塑胶材料选择。不同塑料,其收缩率存在差异。一旦模具开始加工,如果发生材料更换,而更换材料的收缩率存在较大差异,那么塑胶件的尺寸精度必然也出现较大差异,有很大可能不能满足设计要求。 注塑模具的各个零部件需要通过CNC、线切割、EDM、钳工装配和抛光等工艺进行加工,每一个工艺都会存在着加工误差,这个误差最终会反映到塑胶件尺寸精度上。 同时,零部件各种加工工艺的精度和成本不同。如果在模具设计和加工之前,模具工程师能够提前知晓塑胶件中哪些尺寸是关键尺寸、哪些尺寸的精度需要进行管控,那么在模具设计和加工时,就可以对这些尺寸进行重点关注,通过模具设计优化和选择精度更高的加工工艺等方法,从而有利于提高关键尺寸的尺寸精度。 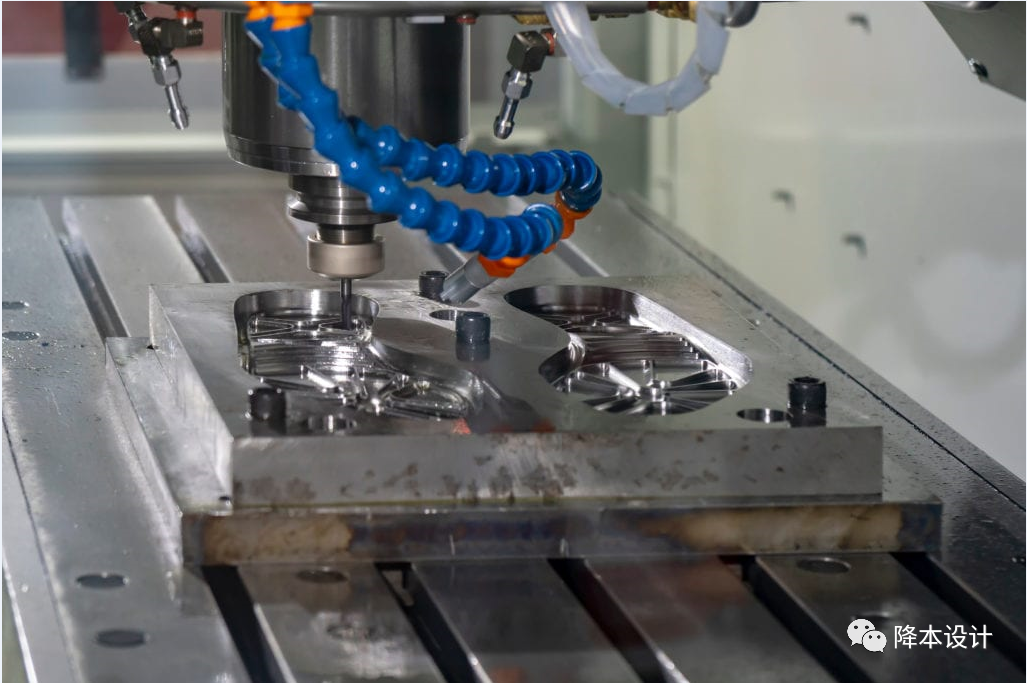
注射模具在长期使用过程中,由于塑料流动、塑胶件脱模以及开合模过程等,都可能使得模具零部件会发生磨损。一旦发生磨损,模具尺寸就相应的发生变化,这会造成塑胶件尺寸精度发生变化。
在注塑成型生产过程中,熔融塑料对注塑模具会产生较高的压力即胀模力,使得模具有沿着分型面胀开的趋势,所以注塑机台必须使用较大的锁模力以平衡胀模力。然而,如果锁模力过大,或者模具本身强度不够,这会造成模具发生变形,这就会影响模具型腔内部的尺寸大小,从而影响塑胶件的尺寸精度。
注塑成型的浇注系统,包括浇口大小和位置、流道类型和尺寸等,应当保证塑胶材料在充填时达到流动平衡。流动不平衡会造成充填不均匀,塑胶件发生翘曲变形等,继而会影响到尺寸精度。 当模具穴数变多时,要保证各个模穴之间的流动平衡,更是一大挑战。 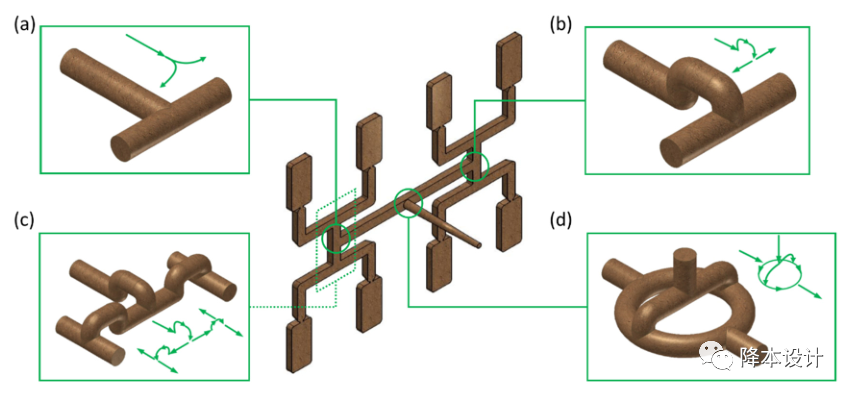
注塑模具的冷却水路需要确保模穴中塑胶件每一个位置,都能达到均匀冷却。不均匀的冷却会导致塑胶件出现缩水、翘曲和变形等,最终会影响塑胶件的尺寸精度。 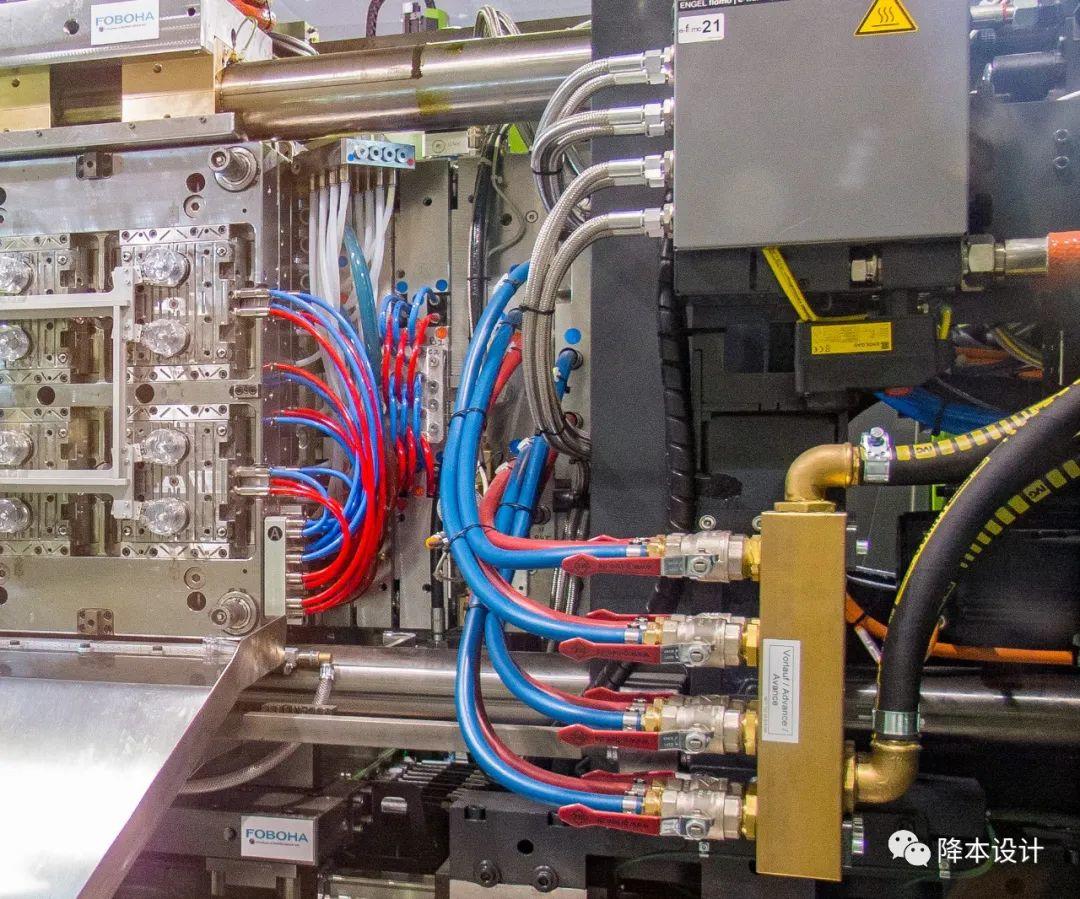
6.7 顶针设计
顶针顶出时,会对塑胶件施加一定的力,需要确保顶针合适的形状或位置。 如果顶针放在塑胶件错误的位置上,例如塑胶件薄弱处、或者最后冷却处,那么有可能会造成塑胶件顶出变形,影响产品尺寸精度。 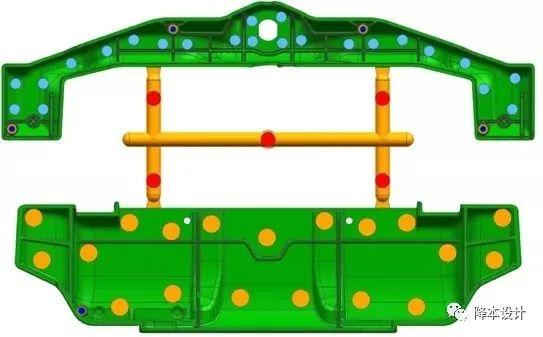
▲顶针位置示意
在注塑成型试模过程中,我们需要反反复复调整注塑成型各个工艺参数值的大小,包括压力、温度和时间等,以获得最佳的外观质量和尺寸精度。
一旦塑胶件的质量尺寸精度符合要求,则必须严格控制和管控相关参数,以确保后续生产时继续保持一致。 注射和保压压力会影响塑胶件的收缩率。可以通过调整注射和保压压力,改变塑胶件收缩率大小,从而改变塑胶件的尺寸大小。 当注射和保压压力较大时,会促使更多的塑胶熔料进入型腔,这会降低塑胶件的收缩率;相反,则会加大收缩率。 注射和保压压力不宜过高,容易造成毛边,同时还会导致塑胶件内部产生很大的内应力。 提高注射速率可成型形状复杂及薄壁塑胶件, 并有利于稳定和提高尺寸精度。高速注射可以使塑料开始流入型腔时的温度和充填完成时的温差减少, 有利于薄壁成型, 减少塑胶件的内应力。 料温和模具温度升高热胀系数增大,结晶度增加,因而收缩率增大。但随着料温和模温的升高,熔体流动性增大,浇口封闭的时间延长,塑胶件密度增加,内应力降低,又使收缩率降低。最后的收缩率是两种倾向综合作用的结果。 需要通过实际调试,以获得最佳的料温和模温,以确保尺寸精度。 注射和保压时间需要足够长,以确保熔料充填足够,而不发生较大的收缩变形。 冷却时间短,塑胶件脱模后收缩大,容易变形,从而会影响尺寸精度。而冷却时间过长,则会降低生产效率,增加塑胶件成本。 如果对塑胶件的尺寸精度要求很高,例如0.01~0.001mm以内,则要求注塑成型工艺参数的精密管控,此时普通注塑机可能就满足不了要求,我们需要使用精密注塑机: