在DFMA培训、咨询和推广的十余年经历中,我看到了大多数工程师和企业对DFMA的认可和期待。
在认可和期待同时,有的工程师从实际出发,表达了对DFMA增加工作量的担忧: DFMA看上去确实不错,但是现在项目进度要求都很紧,昨天老板把设计要求丢过来,今天就要设计好,明天图纸就要发出去,能开模的那种
。
产品设计需要考虑功能、外观、可靠性和用户需求等等,已经让我焦头烂额了,每天加班到12点,头发已经掉了一半了。
如果还要去考虑DFMA,岂不是要加班到深夜,头发掉光?
这样的担忧不无道理,产品开发过程中明文规定要使用的工具实在太多;作为一名工程师,我曾经不得不加班加点去完成公司流程中规定的一些华而不实的文件要求,实在是浪费时间和精力。
不过,DFMA不是这样的工具。
对初学者来说,DFMA可能会增加产品绘图时的工作量;但是,如果我们熟悉DFMA之后,在产品绘图时就引入DFMA的理念,就不会增加工作量。
同时,我们需要思考的是,如果我们在产品设计时不考虑DFMA,那么这必然造成产品在制造和装配过程中出现质量问题,我们不得不反反复复地进行设计修改,这反而会造成工作量增加。
工欲善其事,必先利其器。
DFMA正是产品开发过程中,减少工程师工作量必不可少的利器。
不少工程师,大概是在看到DFMA评审表时,觉得DFMA的内容那么多,需要一个一个零件、一个一个工序的去评审、去改图,觉得DFMA会增加工作量。 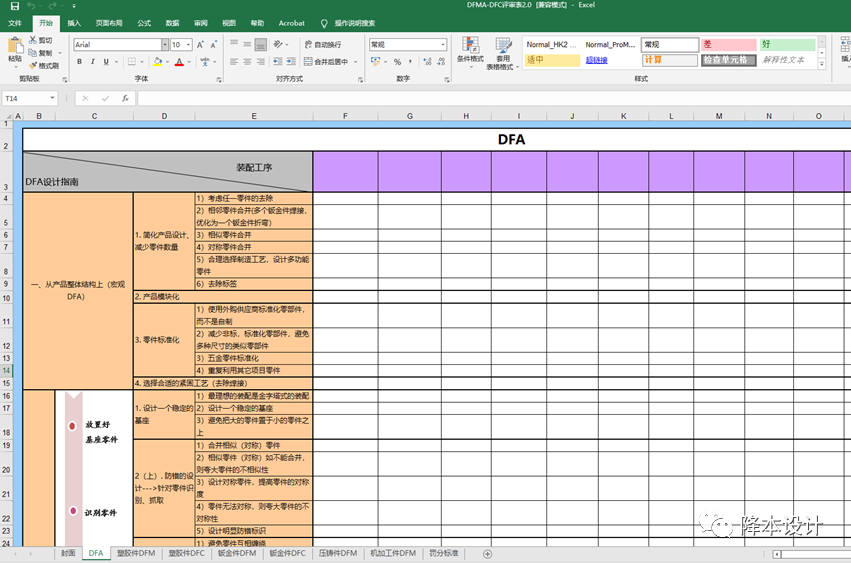
当然,如果我们是初学者,对DFMA没有基本认识,每一条设计指南,我们都需要去查书查资料、去弄明白真正的含义,显然这会增加工作量。 而如果知道最基本的DFMA认识,只需要在绘图时把DFMA知识融合进去,根本上就不会增加工作量。 例如,塑胶件DFM设计指南中,需要保证壁厚均匀,在绘图时注意到这一点,工作量根本上就不会增加。 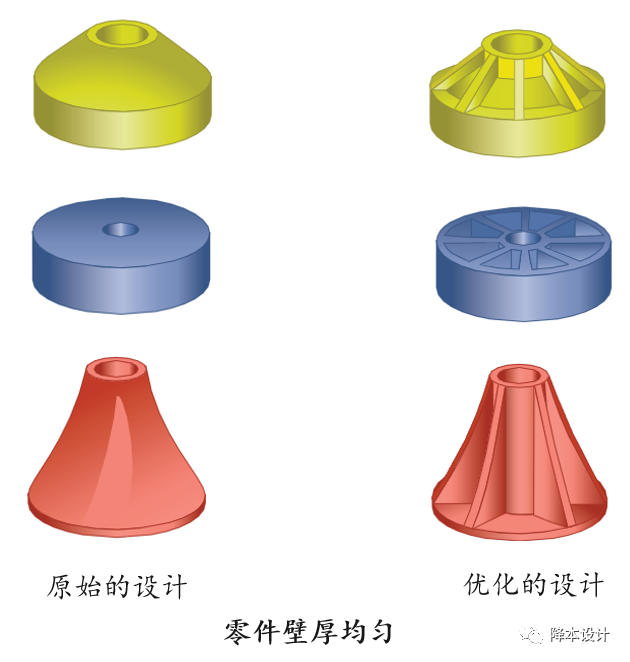
在产品开发时,我们要把事情一次性做对,这就要求在产品设计时考虑到方方面面的需求,这就是Design For X。 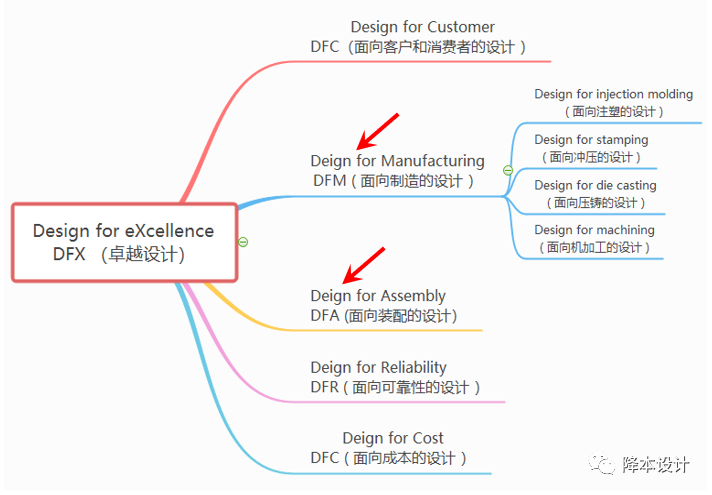
如果我们在产品设计时,把绝大多数的精力都放在如何去满足用户需求、满足可靠性等方面,而忽视了制造和装配的需求,那么一旦产品在生产时出现问题,那么我们就不得不返回来修改设计,这反而会增加我们的工作量。 我在职业生涯的初期,就是因为没有DFMA的认识,就曾经犯了无数个这样的错误。 一个典型的错误就是在一个按钮在设计时没有考虑到DFA中的防错要求,最后在批量生产时出现按钮装反的现象,而不得去改设计改模具。 总之,如果我们不考虑DFMA,这会造成我们不能一次性把事情做对,会反反复复的修改设计,最终我们的工作量反而会大增。