选材,即选择合适的材料,是降本最常用的一种方法。如果应用恰当,会带来非常可观的降本,特别是在塑料金属原材料暴涨的最近几年。
不过,有的工程师一看到选材降本,就把选材等同于国产代替进口、或者更换一个便宜供应商等。
事实上,选材还有其它维度,例如在满足性能要求下,通过材料类型的变更,从而实现降本。
当然,通过材料类型变更降本,难度和挑战比较大。
本文介绍一个成功应用于汽车BC柱装饰件的材料类型变更的案例,使用高光免喷涂PC/PMMA/ASA塑料代替PC/ABS+喷漆或ABS+PMMA双色注塑,实现了每年2000万成本的节省。
汽车BC柱装饰件,当前主流材料有两种,一种是使用PC/ABS、然后喷漆;另一种是结构件为ABS+GF、外观件为PMMA,双色注塑。 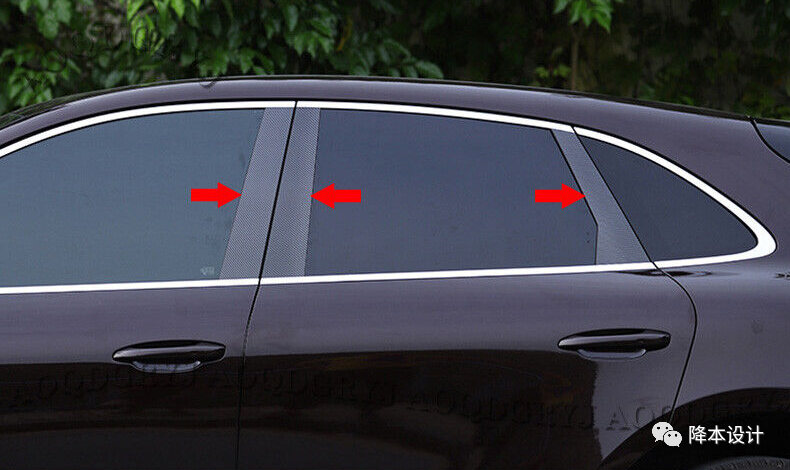
汽车BC柱装饰件,现阶段最主流的材料是PC/ABS材料、在外观面上喷漆。 - 喷漆不良率高,成本高。喷漆容易产生缩孔,橘纹、咬底、颗粒、浮色和发花等各种外观品质缺陷,不良率很高;这些不良产品,就是成本上的巨大浪费。
- 注塑成型之后,还需要喷漆,人工、设备成本增加,生产周期长。
- 喷漆使用化工溶剂会污染环境,环保性差,受环保政策管控严格。
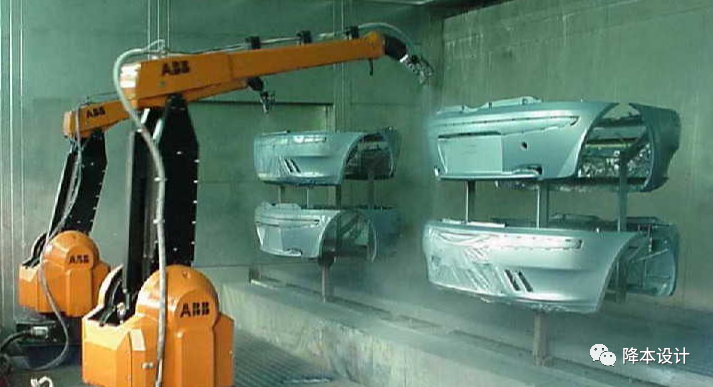
1.2 第二种:结构件ABS+GF、外观件PMMA,双色注塑 由于喷漆成本高、生产周期长以及环保等问题,目前有少量汽车BC柱装饰件,其结构件使用ABS+GF、外观件使用PMMA,然后二者通过双色注塑在一起。 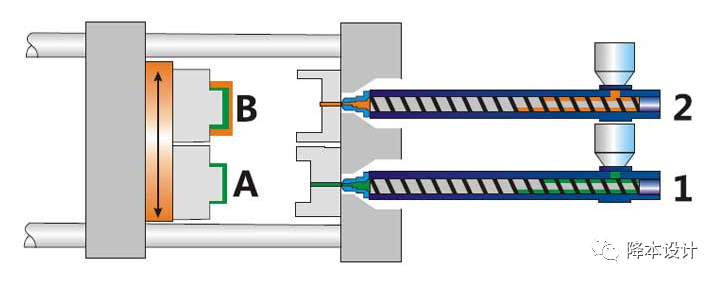
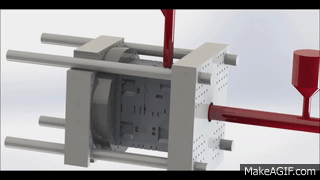
鉴于第一种主流材料喷漆产生的缺陷、以及第二种材料生产周期长等缺陷,目前有企业成功使用了高光免喷涂塑料PC/ASA/PMMA,实现每年2000万的成本节省。 - 一次注塑成型,生产周期短,无需二次喷涂,生产成本低。
- 在满足高光、耐候性、耐刮擦性等前提下,具有更高的耐热温度、和更高的冲击强度。
- 耐候性、耐刮擦性能满足要求,但比当前主流材料稍差。
- 注塑模具的设计和工艺参数的调整较复杂,要求工程师必须具备相关经验,否则容易出现外观缺陷。
在当前的成功应用案例中,一辆车总共有6个装饰件使用高光免喷涂材料PC/ASA/PMMA,总体成本相对于主流PC/ABS+喷漆,可以降低100元以上。 按一年20万销量,该塑料选型可以带来2000万的成本节省。 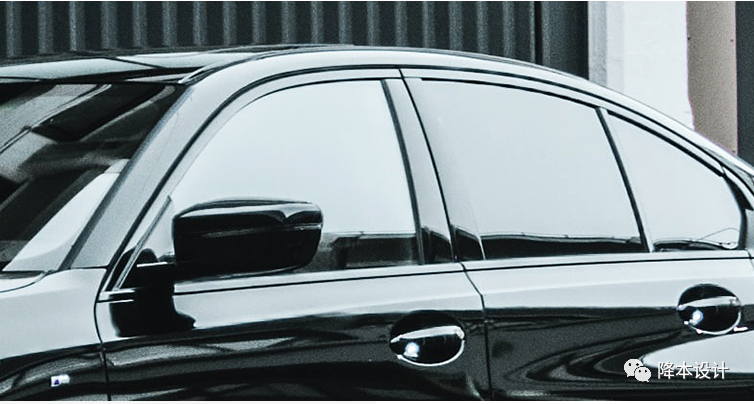