埋置螺母是常见的一种塑胶件紧固工艺,适用于紧固强度要求高、可靠性高和反复拆卸的场合。
埋置螺母看上去非常简单,不就是在塑胶件支柱上放置一个螺母吗?
在这种思维主导下,不少工程师在进行结构设计时,并不会花费太多心思,随随便便选择一种螺母规格、随随便便设计塑胶件支柱,也从未想过配合件设计还有讲究。 然而,由于金属和塑料的热膨胀系数不同、同时塑胶件支柱本身壁厚较薄(强度低)、注塑过程中又容易产生应力集中等原因,随意结构设计必然导致形形色 色的质量问题,不是螺母的拉出力或扭力矩达不到要求,就是支柱开裂、螺母被拉出等。 本文将系统化、逻辑化地介绍埋置螺母结构设计的方方面面,例如螺母性能要求和设定、螺母关键结构特征、螺母的五种埋置工艺、塑料决定螺母结构、塑胶件支柱设计和配合件设计、以及问题解决指南等,期待能把埋置螺母的结构设计讲清楚、说明白。 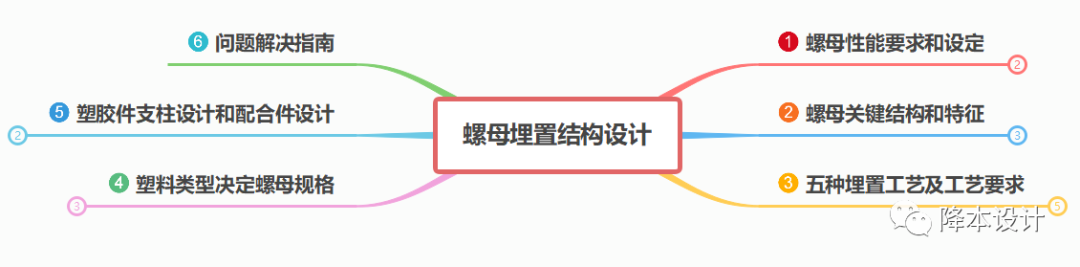
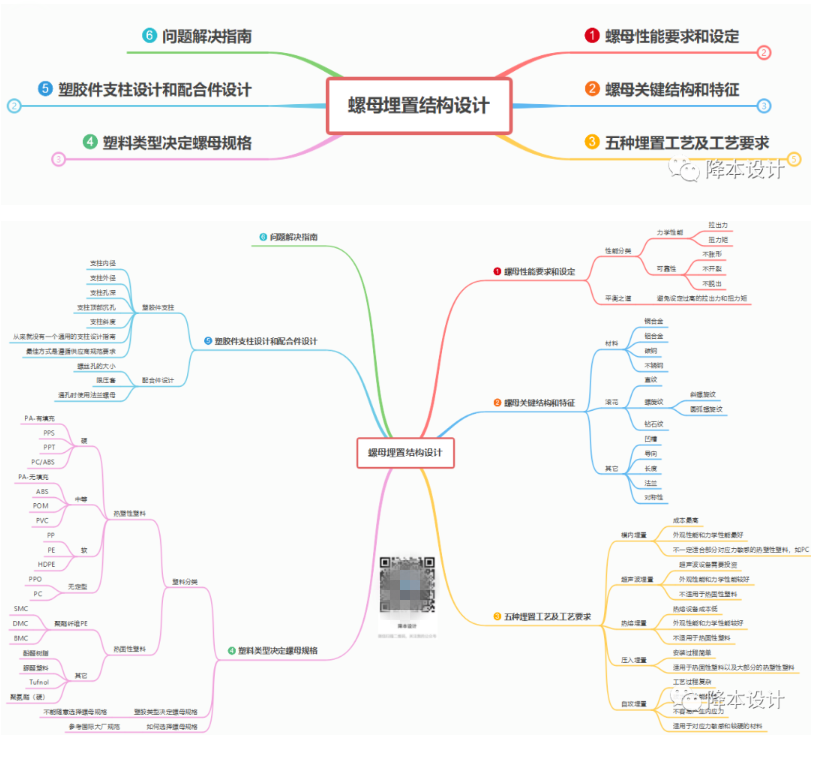
正式开始前,请各位工程师思考下图结构设计是合理的吗?(答案在本文后半段) 如果你的答案是合理的,那么本文的标点符号也许都值得好好读读。
塑胶件埋置螺母的性能要求分为力学性能和可靠性两大部分。 拉出力(pull-out force)是在轴向方向上把螺母从塑胶件支柱中拔出所需的力。 扭力矩(Torque-out)是旋转紧固件,使得埋置螺母从塑胶件支柱中松脱所需的的扭矩。 埋置螺母的可靠性要求,是指螺母埋置于塑胶支柱之后,在长期使用过程中,不会发生支柱胀形、开裂、断裂或螺母脱出等质量缺陷。 一个完美的塑胶件埋置螺母结构设计,一方面需要提供足够的拉出力和扭力矩,另一方面又需要保证可靠性,这取决于以下几个方面: - 塑胶材料的特性,包括塑料种类、软硬程度和填充剂、以及添加二次料的比例等
- 塑胶件的加工过程管控,包括支柱尺寸公差、熔接痕和内应力等
拉出力和扭力矩值的设定必须在合理的范围之内,过大要求可能会产生可靠性问题。 如果拉出力和扭力矩设定过高,则可能需要较深较尖的滚花纹路、或者较小的塑胶件支柱内径,这反过来会导致塑胶件支柱内部应力集中,发生支柱胀形或开裂等缺陷。 如图显示了某螺母厂商的的两款超声波/热熔螺母在通常情况下所能达到的拉出力和扭力矩值,如果我们选用了类似的螺母规格,那么拉出力和扭矩力矩值的设定就应该避免超出图中要求。
一个典型的螺母关键结构和特征包括螺母材料、滚花、凹槽和导向等。 常见的埋置螺母材料包括黄铜、铝、不锈钢和碳钢等,材料不同,价格不同,所适用的环境也不同。 大多数的螺母都是黄铜。尽管黄铜价格比钢贵,然而黄铜容易加工,同时也容易回收。在模内埋置时,如果螺母放错位置,损坏模具的可能性比较少;另外,对于大多数应用来说,黄铜本身的抗腐蚀性可以避免额外的昂贵电镀表面处理。 铝合金螺母比铜螺母轻70%,具有导电性、非磁性,以及良好的耐腐蚀性,耐腐蚀性与铜螺母相当,比不锈钢螺母低。 不锈钢螺母具有最好的耐腐蚀性,适用于高度腐蚀和卫生条件要求高的环境中,如食品、饮料、医疗和海洋工业等,可以替代原本的铜螺母以及二次电镀工艺,以降低成本。 在自助餐厅和餐馆中常见的果汁饮料分配器,因为橙汁和葡萄柚汁等是高度酸性,这就会导致机器中的塑料件产生腐蚀问题。 原本使用铜螺母,然而需要加上昂贵的二次电镀工艺,才能确保耐腐蚀性。 后直接改为不锈钢螺母,从而保证果汁免受任何因腐蚀而产生的杂质。 滚花是指螺母外侧的纹路,滚花用于增加螺母的扭力矩。常见滚花纹路有直纹、螺旋纹和钻石纹、或者各种纹路组合等。 - 直纹:直纹加工简单,成本低,能够提供最大的扭力矩,需要结合凹槽使用,以保证拉出力。
- 螺旋纹:螺旋降低了扭力矩,但是增加了拉出力。30到45度之间的螺旋角是一个最好的平衡,对拉出力有积极影响,同时把扭力矩值的损失降到最小。螺旋具有自我导向功能,埋置时可以自我导向。
- 钻石纹:滚花较浅、滚花面积大,相对于两种左右螺旋纹的组合。
三种滚花纹路,在拉出力和扭力矩的表现上存在差异。很难评价谁优谁劣,我们只是需要在合适的应用环境选择合适的滚花纹路。 滚花纹路通常具有锋利的尖角,在与塑料结合时容易产生应力集中。 这一特性,对于半结晶塑料影响不大,因为半结晶塑料对应力相对不敏感,因此半结晶塑料可以使用各种滚花纹路的螺母。 这对无定型塑料却非常致命,因为无定型塑料对应力非常敏感;无定型塑料在选择螺母类型时,应当避免锋利的滚花纹路。 而对于需要电镀的无定型塑料,电镀时的酸洗会造成支柱严重的开裂现象;最好是先电镀,再埋置螺母。 - 凹槽:在螺母的外部,会有一段或多段凹槽,用于增加螺母的拉出力;
- 导向;在螺母前端,一般会设置一段导向结构,以方便螺母放入塑胶支柱中时,能够自我导向,使得螺母与支柱的轴心对齐;
- 长度:增加螺母长度,可以增加拉出力;螺母的拉出力满足不了要求,有可能就是螺母长度不够;
- 法兰:某些螺母顶端具有法兰,法兰用于增加配合时接触面面积,并替代塑胶件承受载荷;
- 对称性:有的螺母两端对称,这是一种防错的设计,避免在人工组装时装反、或者在自动化组装时减少重新定向的动作。
螺母埋置工艺在塑胶件中可以分为两大类,模内埋置和注塑后埋置,注塑后埋置又包括热熔、超声波、压入和自攻等方式。 模内埋置是在注塑成型时,把螺母提前放置于模具型腔中的导销上并固定,然后注射塑料把螺母外部包裹起来。
模内埋置需要在模具中提前放置螺母,这会增加注塑成型周期,对于昂贵的注塑机费率来说,这是一个非常大的成本浪费。 同时,在滚花纹路尖角处通常会产生内应力,往往需要对螺母进行预热。
另外,一旦螺母放置出错,例如放反或者放偏,可能会导致模具损坏,带来模具修复和停机等。 模内埋置螺母可以设计较大较深的凹槽和滚花纹路,因此可以获得最佳的力学性能和外观性能。 注:这个配图较老,钻石型滚花螺母不是模内埋置的最佳选择。
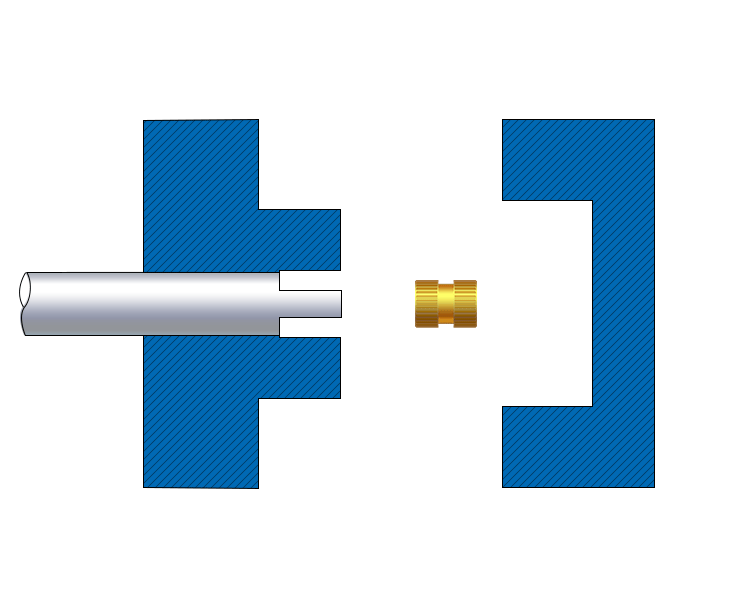
超声波埋置通过超声波振动,使得螺母与塑胶件表面及支柱内侧的分子间摩擦产生热量,导致塑料局部暂时熔化,当焊头通过压力继续把螺母下压时,熔融塑料流入螺母的外部滚花纹路空隙之中,冷却后塑料凝固,从而把螺母埋置于塑胶件中。 与模内埋置和压入埋置相比,超声波埋置的生产周期短、产生的内应力小;可以一次性埋入多个螺母,适用于自动化生产;超声波埋置的性能较好。 因为超声波埋置需要熔化塑料,所以不适用于热固性塑料。 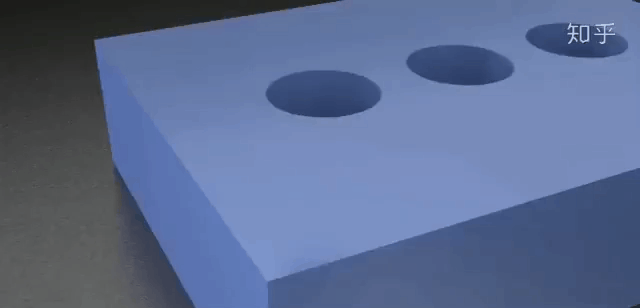
3. 热熔埋置
热熔埋置是同超声波埋置很类似,差别是热熔埋置时依靠热熔机产生的热量去加热塑料,而不是超声波振动。 相对于超声波埋置,热熔埋置的优点是热熔机设备成本低;一次性也可以同时热熔多个螺母,适用于自动化生产。热熔埋置埋置的性能较好。 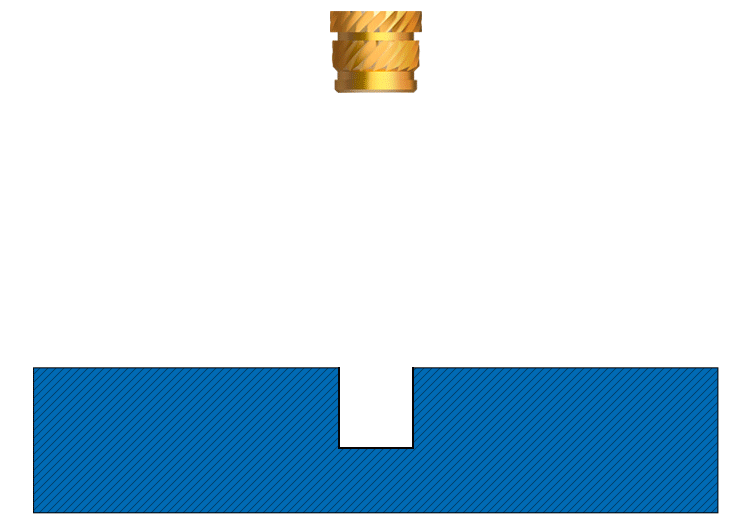
压入埋置是直接把螺母压入到塑胶件支柱中,通过螺母的膨胀迫使滚花纹路插入支柱内侧,从而形成类似螺纹锁紧的效果。 压入埋置的安装过程简单,仅仅需要一次压入,成本低,适用于热固性塑料以及大部分的热塑性塑料。 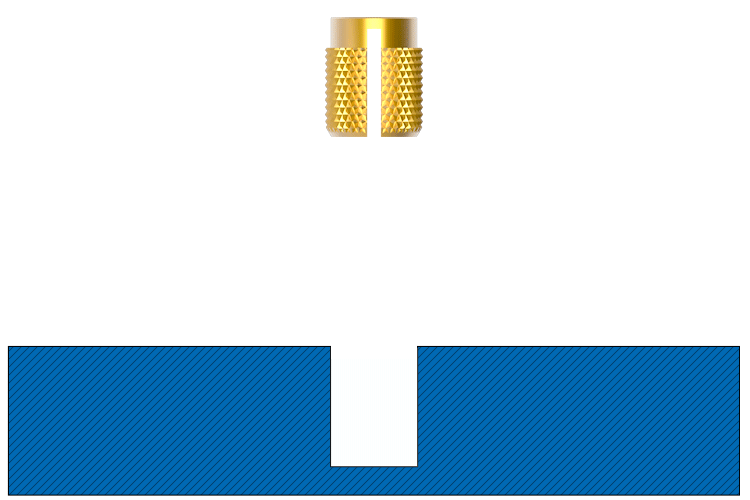
自攻埋置是把侧具有螺牙的螺母自攻拧入塑胶件支柱中。 自攻埋置的工艺过程很较复杂,其拔出力性能最佳,同时不容易产生内应力,适用于对应力敏感和较硬的材料。 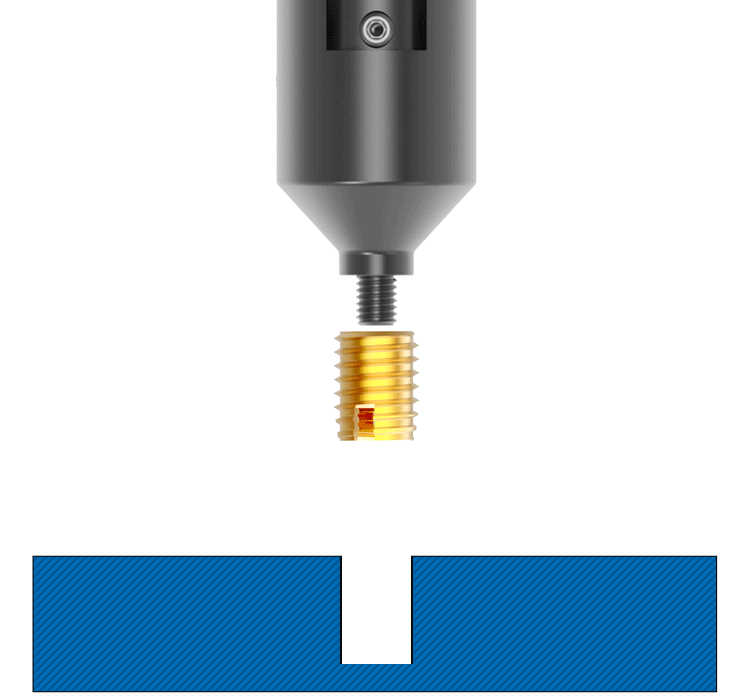
从上面的图形我们可以看出,埋置工艺不同,螺母结构也就不同,反之亦然。 只有某些类型的螺母,既可以使用超声波埋置,也可以使用热熔埋置。
特别注意的是,很多企业把超声波/热熔埋置螺母直接用于模内埋置,这是非常不建议的--支柱开裂就这样不知不觉的产生了。 如图显示了某螺母厂商其不同规格螺母所对应的埋置工艺。(不用在意具体规格是什么,这里仅仅是为了说明螺母规格不同,埋置工艺也不同) 注:★表示“推荐”;●表示“可行”;C表示“联系螺丝供应商” 无论使用哪一种埋置工艺,在埋置时都必须确保螺母轴心与支柱孔轴心对齐和一致。如果二者不一致,会导致螺母在使用时受到侧向力,继而导致支柱开裂。当然,螺母尾端导向特征或者塑胶件支柱带有锥度的内孔有助于对齐。 当螺母完成后,需要确保螺母与塑胶件表面平齐、或者低于塑胶件表面但不超过高出0.15mm。 如果螺母低于塑胶件表面太多时,那么与配合件紧固时,螺母与配合件之间就会存在间隙。在拧紧螺丝的过程中,螺母就会被往上拉,直到间隙被填充,这会严重影响螺母与塑胶件的结合,甚至会造成螺母从塑胶件中被拉出。 如果螺母高于塑胶件表面,那么与另外一个配合件紧固时,配合面不平齐,影响配合效果。 埋置过程中的工艺参数和工装夹具设计等,会严重影响埋置螺母的性能。 所以,我们必须针对每一种埋置工艺,合理管控工艺过程。例如,这是某企业针对热熔埋置螺母的工艺要求: - 简单零件使用高度方向有绝热材料定位的通用工装;特殊零件制作相应的特殊热熔工装;
- 热熔前应抽检塑胶件支柱孔的直径和深度,必须符合规定的尺寸要求;
- 推荐采用 50W 的可调节温度的加热棒,加热棒使用附表推荐的温度接触铜螺母加热,加热时间为 7-10s;
- 支柱内孔软化时,支柱顶平面及外表面不得软化,将螺母垂直缓慢压入支柱,防止塑胶流动不充分,压入螺母后加热棒应快速垂直提起;
最好是咨询螺母供应商,以获取供应商推荐的工艺过程指导。 (这其实就是DFMA中的团队合作,进行面向制造和装配的产品设计时,不能仅仅靠某一职能部门就完成,而是依靠产品开发整个职能部门、甚至供应商等的通力合作)。 否则,如果不遵守相关工艺指导,很容易出现质量问题。例如,对于热熔螺母,当热熔机的温度设置得过高或过低时,就会出现各种缺陷。 螺母埋置于塑胶件之后,拉出力和扭力矩主要取决于是否有足够的塑料充填到螺母外部的滚花纹路和凹槽中。
可以对实物做一个剖面,来判断塑料是否完全充填到滚花纹路和凹槽中。
塑料种类很多,然而不同塑料的软硬程度不同、对应力敏感程度不同,这就使得不同塑料与金属螺母结合时性能表现存着差异,因此对螺母的结构特征和埋置方式等提出了要求。 在进行塑胶件埋置螺母结构设计之前,我们必须弄清楚塑料和螺母二者之间的关系。 热固性塑料在加工过程中发生了不可逆的化学变化;一旦加工成型,就不能通过加热和加压等重新成型。这些塑料坚韧耐热,包括酚醛树脂、尿素和聚酯树脂。 热固性塑料不适用于热熔和超声波,可以使用模内埋置、压入或自攻丝螺母。 热塑性塑料在常温下是坚硬的固体,但在高温下会软化和熔化。常见热塑性塑料有ABS、PC、PVC、PBT、PP和PE等。 热塑性塑料根据分子结构的不同,可以进一步分为无定形塑料和半结晶塑料。 无定形塑料具有无规则分子结构,没有明显的熔点。相反,无定形塑料随着温度升高逐渐软化。由于碳氢化合物的存在,无定形材料对应力敏感,对环境应力开裂的抵抗力差,容易发生开裂缺陷。ABS、PC和PPO是常见的无定形热塑料。 半结晶塑料具有高度有序的结晶分子结构,这些分子结构不会随着温度升高而软化,而是具有一个明确的熔点。该熔点通常高于无定形热塑性塑料的上限。PBT、PP和PE等是常见半结晶塑料。 在塑料中,还会根据需求添加各种各样的添加剂和增塑剂等,以增强塑料的性能,例如强度、稳定性、刚度、导电性、传热性和抗蠕变性等。 然而,添加剂和增塑剂等通常增加了材料的应力敏感性。同时,添加剂通常会提高塑料的流动性或熔点,因此会影响螺母在注塑后的埋置。这种影响不仅与添加剂的类型有关,还与所用的百分比有关。 综合热塑性和热固性、以及软硬程度等,塑料整体可以分为: 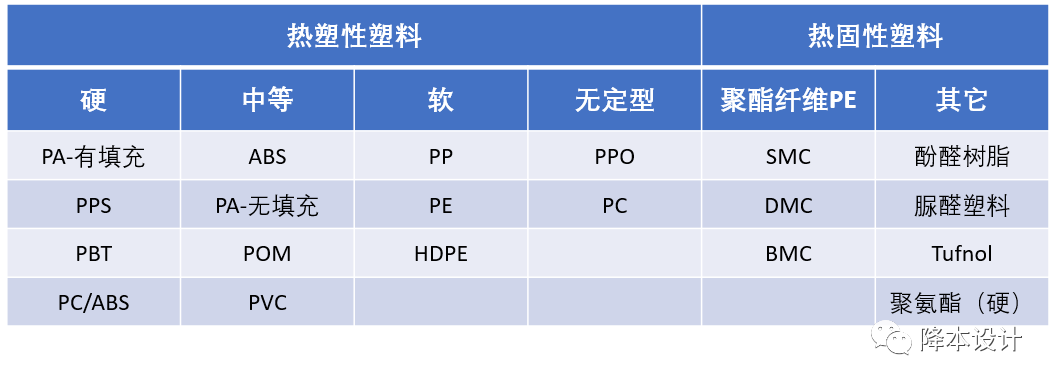
塑料种类不同、软硬程度不同,那么使用的螺母规格不同(包括滚花纹路、埋置类型等)。 如图是某螺母供应商不同螺母规格与所适用的塑料类型的对应关系。(不用在意具体规格是什么,这里仅仅是为了说明塑料不同螺母规格也不同)
注:★表示“推荐”;●表示“可行”;C表示“联系螺丝供应商” 看了这张对应关系图,我们就明白:不根据塑料类型,随意选用埋置螺母,那一定是后患无穷。 例如,上图所示的无定型塑料PC、PPO等,最好选用的螺母其滚花形状为圆弧形、而不是钻石型,以减少模内埋置时产生的内应力。 当我们知道塑料类型之后,那其实螺母选择就比较简单,我们可以参照4.2一节中的关系图,进行选择就可。 可能有的工程师会问,这个关系图是国际大牌的,公司现有的螺母供应商,没有这个关系图怎么办? 这也好办:根据塑料类型,找到这个国际大牌对应的螺母规格,然后我们再找现有供应商相似规格,不就可以了吗? “站在巨人的肩膀上”,不要重新去发明车轮,就是这个原理。