宁德时代:方形铝壳电池顶盖设计
方形电池的各个零部件组成如图1所示,主要包括顶盖,铝壳,卷芯组成,顶盖和壳体通过激光焊接组成一个密封的整体。
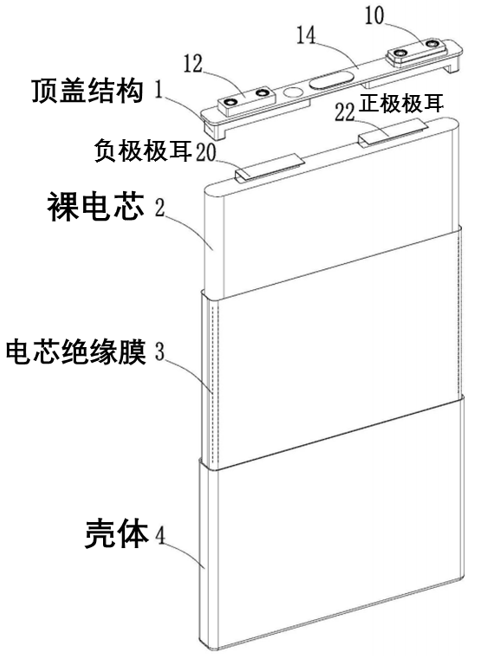
方形电池的顶盖如图2所示,其结构主要由顶盖板,正、负极柱,防爆装置,注液孔等组成,一般极柱部分包含翻转片装置(OSD),电流切断结构(CID)和短路装置(Fuse)等机构。
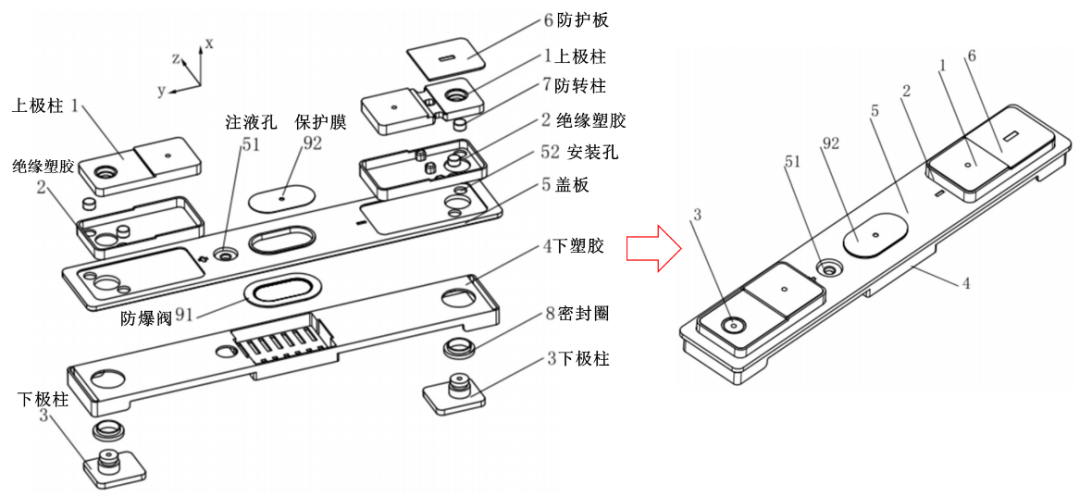
本文根据宁德时代顶盖方面的专利资料,介绍顶盖各部分的基本原理与结构设计,以此进行系统学习并与大家分享。注液口主要用于顶盖与壳体焊接之后,向电芯内部注入电解液,然后再采用激光焊接将密封钉封住注液口。在顶盖焊接之后密封检查时,一般也是通过注液口通入氦气,检测电池内部的压力变化,从而判断焊接密封性。现有电池中,电池顶盖的注液孔密封采用密封钉或密封球与注液孔过盈配合实现密封。但是,过盈配合会导致密封钉与注液孔壁之间发生摩擦,产生的金属颗粒和毛刺可能掉入电池内部引起电池短路。为了避免因金属颗粒和毛刺掉入电池内部引起电池短路,装配时过盈量需要控制在很小的范围内,因此对机加工的精度要求非常高,不易实现。为了解决此问题,宁德时代设计了一种注液口密封钉,密封钉包括金属部和与金属部组装在一起的橡胶部,金属部和橡胶部与注液孔的接触处均为过盈配合;注液孔内开设有凹陷,密封钉的橡胶部对应设有可卡合于凹陷部中的突出部,如图3所示。密封钉可以在低温下冷却装配,可以有效防止金属毛刺和颗粒的产生,防止接触界面的破坏,实现注液孔的可靠密封;橡胶部的设置可以有效阻止金属毛刺和颗粒落入电池壳体内,可以保证电池的安全性能;采用机械密封结构,无需激光焊接,工艺简单,可以显著降低成本,当然这种密封钉也可以焊接封死。而且,密封钉橡胶部分可以为圆柱锥形、灯笼型”的弧形结构等多种不同的形状。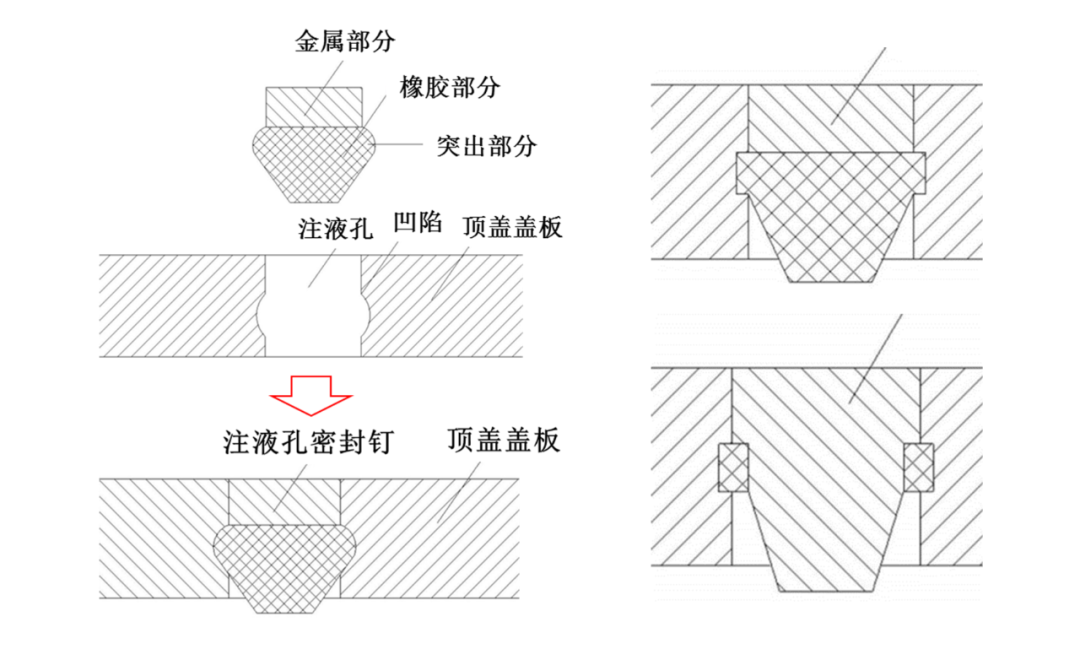
铝材被广泛应用在动力电池中作为壳体。但是,由于铝的电位和电池正极电位之间存在一定差值,因此铝壳很容易在底部出现腐蚀问题。将铝壳和正极极柱直接导通可以消除二者的电位差而避免铝壳腐蚀。因此,一般电池顶盖上对应正极极柱和负极极柱处有两个极柱穿孔,正极极柱从一个极柱穿孔中穿出并与顶盖片电导通,负极极柱从另一个极柱穿孔穿出并与顶盖片电绝缘,负极柱附近设置有短路部件,当动力电池内部压力增大时,短路部件向上动作,使动力电池的正负极形成回路,并在回路中产生较大的电流,使得连接部件熔断,从而切断主回路。正极与铝壳之间的电阻很小,为毫欧姆级别,电池发生短路时的回路电流很大,容易出现打火而引发电池着火,存在较大的安全隐患。目前,动力电池通常在铝壳的顶盖片和电池正极极柱之间添加导电塑胶或者是碳化硅,来增加铝壳和正极之间的导通电阻。宁德时代设计了正极极柱和顶盖片之间的PTC热敏电阻,如图4所示,正极极柱和顶盖片彼此电隔离,并通过PTC热敏电阻实现电连接。PTC热敏电阻为环形,套在正极极柱上,内壁与正极极柱的周壁紧密接触;顶盖片冲压有环形的PTC热敏电阻收容槽,PTC热敏电阻镶嵌在顶盖片的PTC热敏电阻收容槽中而与顶盖片紧密接触。PTC热敏电阻在常规条件下具有较小的电阻,保证在动力电池发生外短路时,能尽快消耗电池的内部能量。利用PTC热敏电阻的阻值随温度变化的特性,随着电池外短路时间的增加,温度升高,PTC热敏电阻处的电阻会逐渐变大,这使得短路电流逐渐减少,避免了过高热量对电阻形成的热冲击,因此既不存在小电阻易于熔断的问题又能避免温度过高导致的电池着火或电阻熔断等问题。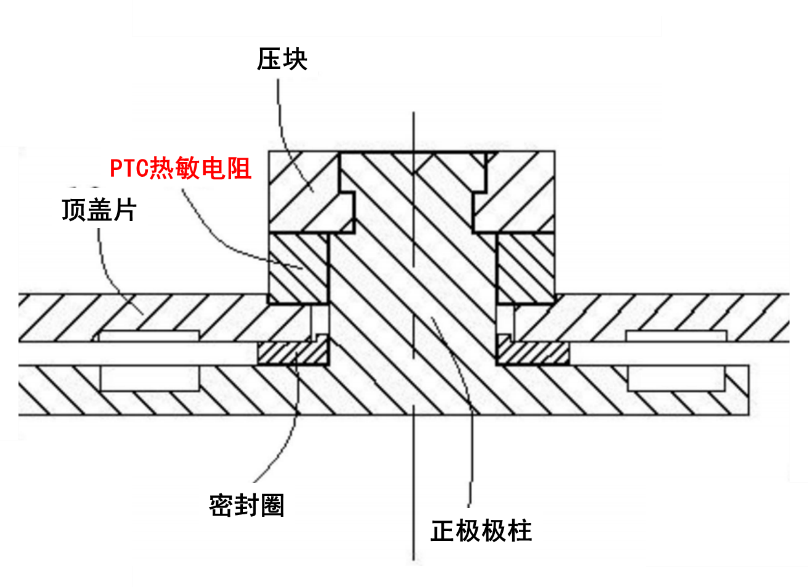
如图5所示,正极极柱通过电阻与顶盖片电连接,负极极柱与顶盖片电绝缘,但是在负极极柱设置翻转片16和短路结构。当电池电池内部压力超过基准压力时翻转片16翻转并接触翻转片连接部1044,以使负极柱和正极极柱通过顶盖片电连接,相当于将裸电芯的正极片和负极片与动力电池的外部进行短路,由此减少裸电芯的充电状态。短路大电流再将正负极极柱的熔断部件熔化,切断电流回路。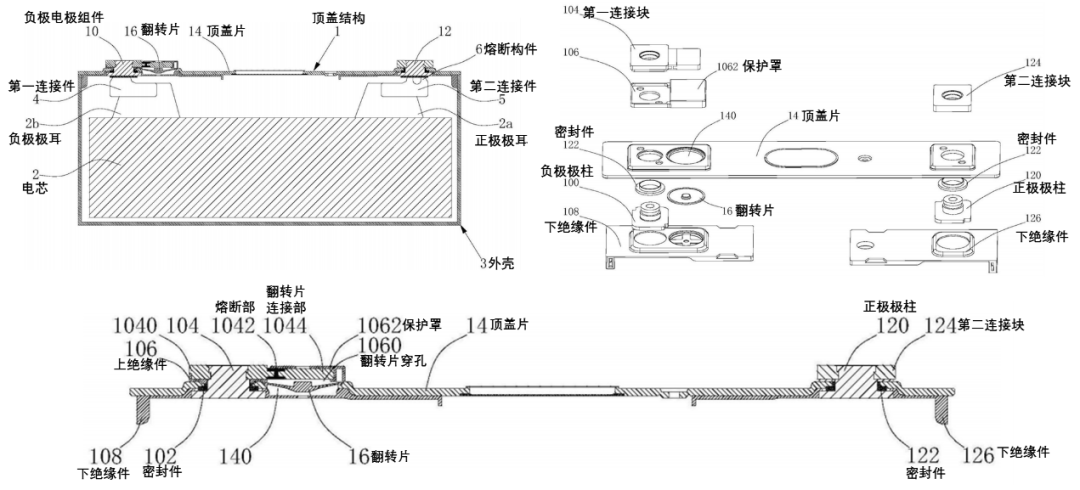
通常,为了解决电池针 刺滥用问题,在正极极柱和顶盖片之间设置有电阻,使正极极柱通过该电阻与顶盖片电连接,当动力电池在针 刺的情况下,如果正极极柱与顶盖片间的电阻过小,则穿钉时外短路的电流过大,穿钉点容易打火,造成电芯失控,因此穿钉时,正极极柱和顶盖片之间需要一个大电阻。当动力电池过充时,当电芯内部气压增大一定值,短路部件向上动作,使电芯正负极连通短路,利用较大的回路电流来熔断连接部件,从而切断主回路。然而,如果直接将正负极连通短路,由于回路中的电阻过小,则回路中的电流会过大(例如,超过10000A),短路部件很容易熔掉,短路部件在连接部件熔断之前就熔掉了,使得回路电流消失,无法熔断连接部件;但如果回路中的电阻过大,则又会造成回路中的电流过小(例如,小于500A),连接部件不会熔断,起不到阻止动力电池继续充电的作用,因此在应对动力电池过充时,显然无法直接采用接入大电阻的方式降低电流。为了同时满足动力电池过充与针 刺问题,宁德时代重新优化了动力电池顶盖结构,在正、负极极柱同时设置翻转片短路结构,使动力电池在过充和穿钉情况下均能够构成具有合适阻值的回路。如图6所示,第一极柱为正极,第二极柱为负极。第一极柱100的顶端穿过顶盖片50,但第一极柱100不与顶盖片50直接接触电连接,二者之间通过第一绝缘连接件102进行固定,并且第一极柱100通过第一电阻30与顶盖片50之间始终保持电连接。而负极极柱200与顶盖片50电绝缘,正负极极柱分别设置翻转片短路结构。第一电阻的阻值比所述第二电阻以及所述第三电阻的阻值之和至少大1000倍。第一电阻的阻值为1~100000Ω,第二电阻以及所述第三电阻的阻值之和为0.1~100mΩ正极极柱短路部件60以及负极极柱路部件70是两个重要的电路开关。正极极柱短路部件60不发生动作时,该电池顶盖的电路结构为针 刺保护电路。当发生穿钉现象时,壳体内部气压不足以使正极极柱短路部件60发生动作时,钉子会将动力电池内部的负极片与外壳以及顶盖片50导通,顶盖片50又通过第一电阻30与第一电极组件10的第一极柱100导通,再通过正极极耳2a最终回到裸电芯内部的正极片,形成穿钉回路。第一电阻30的阻值一般为1~100000Ω。在穿钉回路中,由于有第一电阻30的存在,能够有效减小穿钉回路当中的电流,有效避免因电流过大,导致穿钉点打火,引燃电解液,最终导致动力电池起火的情况发生。而当正极极柱短路部件60以及负极极柱短路部件70同时翻转接入电路时,该动力电池顶盖的电路结构将会转变为过充保护电路。当发生过充现象时,由于电路中需要产生较大的电流来熔断熔断构件,而第一电阻30的阻值过大,因此此时的过充保护电路中应避免将第一电阻30直接串联到电路中。与此同时,为了避免电流过大而先造成第一短路部件60以及第二短路部件70削顶或熔断,此时的电路中又需要接入一个第二电阻40,这个第二电阻40的阻值不能过大,一般不能超过第一电阻30阻值的1/1000,较为优选的是在0.1~100mΩ范围内。当第一短路部件60与第一延伸部104b接触并电连接后,能够形成一条低电阻支路和一条高电阻支路,而第一电阻30则位于高电阻支路中,从而降低整个过充保护电路中的阻值。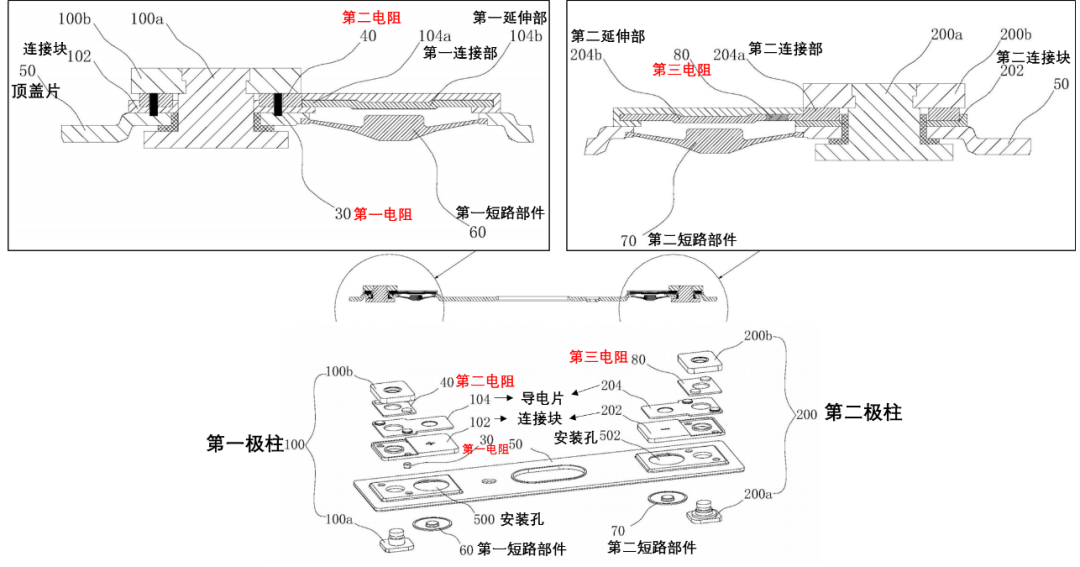
解决硬壳动力电池过充问题而普遍采用的方案是,在电芯失效之前切断电池主回路(电流切断结构,CID),防止电池继续充电以保证电池安全。宁德时代在正极主回路设置一个气压翻转片及集成CID于一体的导电片。导电片四周与裸电芯极耳通过焊接连接,导电片的CID部分与翻转片通过焊接连接于一体,翻转片与正极柱或者顶盖片通过焊接相连把电流导向正极端子。当电池过充,内部气压增大,推动翻转片扯断CID,把翻转片与导电片断开。如图7所示,翻转片204通过绝缘件200固定在顶盖片10的下方,在电路连接上,翻转片204与电流切断结构206的底部直接接触,二者为电连接,翻转片204四周与电芯极耳通过焊接连接。在正常状态下,电流仅能够通过翻转片204以及电流切断结构206传递至顶盖片10和正极极柱上。在电池内部压力超过基准压力时,翻转片204能够在压力作用下向上翻转,同时推动电流切断结构206,直至将电流切断结构206沿着薄弱区破坏,使其丧失电流传输能力,从而实现过流保护功能。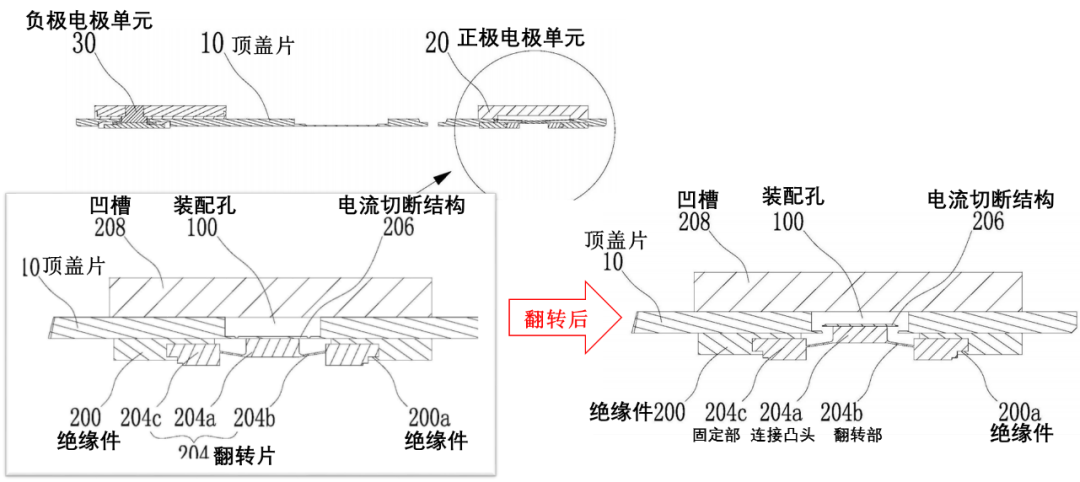
锂离子电池的电芯中的水含量超标、SEI膜不稳定、对锂离子电池的过充,过放、锂离子电池发生短路、挤压等滥用情况时,会造成锂离子电池内部产气、着火,甚至爆炸。目前解决这些问题的通常方法是在锂离子电池的顶盖上增加一个防爆阀,锂离子电池出现上述情况内部产生气体,当锂离子电池内部气体压力达到防爆阀的爆破压力时,顶盖上的防爆片破裂,从而使锂离子电池内部气体从防爆阀口排出,防止锂离子电池因为胀气导致爆炸。宁德时代开发了温敏防爆阀,如图8所示,顶盖上预留一个防爆孔,防爆片密封防爆孔并固定在顶盖上,防爆片包括三层:内侧的温敏材料层,具体材质为聚丙烯(PP)、聚乙烯对苯二甲酸脂(PET)、高密度聚乙烯(HDPE)、聚氯乙烯(PVC)、低密度聚乙烯(LDPE)、聚苯乙烯(PS)、聚碳酸酯(PC)中的一种;中间层为铝、铜、不锈钢等金属片;外层为尼龙保护层。另外防爆装置还包括导热片,一端连接防爆片,另一端连接电池的电芯。该防爆装置工作原理为:当电池内部的温度超过温敏材料的软化温度时,温敏材料软化,从而电池内的产气压力使防爆片破裂或脱开顶盖,以排出电池内的产气。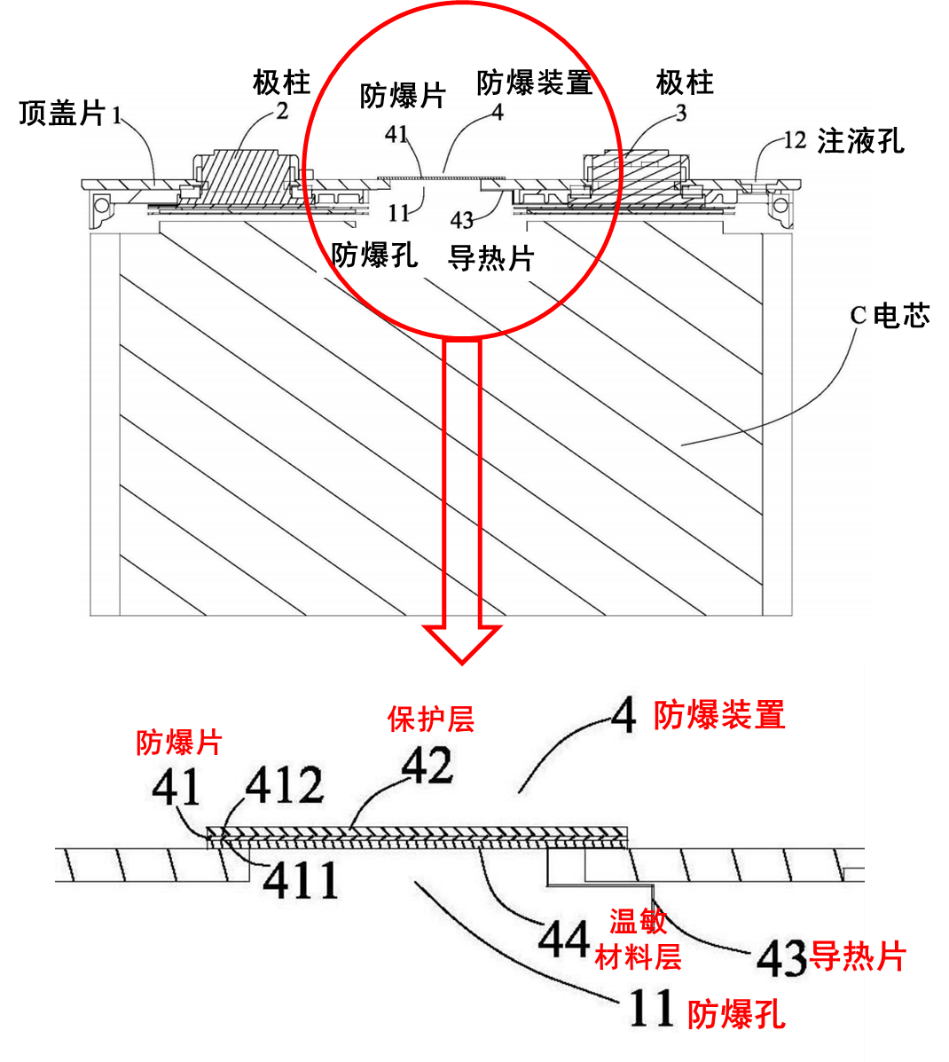