4680、刀片电池、CTP、One-Stop bettery、弹匣电池系统、大禹电池系统
自从上世纪90年代,索尼正式将锂离子电池商业化以来,锂离子电池技术的原理和基本构型没有出现革命性的进展,但是相关新材料不断涌现,关键装备和生产技术飞速发展,电芯和电池系统设计也不断创新改进,电池单体能量密度从最开始的80Wh/kg到目前近300Wh/kg,电池成本也逐年下降,这也说明锂离子电池技术取得了显著进展。近几年,随着新能源汽车动力电池的快速发展,新电池技术层出不穷,本文汇总整理近2年出现的一些新技术。
2020年9月的电池日上,特斯拉发布4680无极耳大圆柱电池技术。4680电池外壳直径为46 mm,高度为80 mm,相比特斯拉此前采用的2170电池,4680电池体积更大,据官方数据,4680电池的能量密度将提升5倍、输出功率提升6倍,每千瓦时的成本会降低14%,搭载该电池的车型续航里程可提高16%。其主要创新点为: 综合考虑电池能量密度、散热特性和电池成组性能,优化电池的外壳直径为46 mm,高度为80 mm,根据自己的经验估算,21700和4680电池主要参数对比如表1所示: 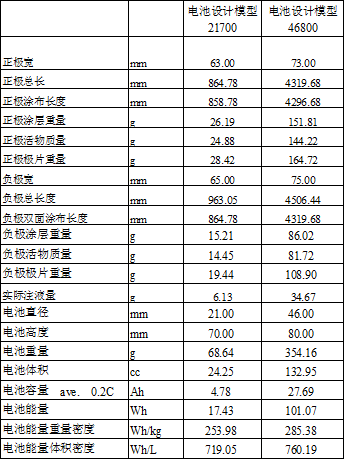
特斯拉4680电池采用无极耳设计结构,具体的电池设计说明如下:电池卷绕时,极片和隔膜的布置方式如图1所示,卷芯两侧分别漏出正、负极集流体,直接通过集流体与电池正负极连接。从极耳角度提高了电池功率特性,在大倍率下电流密度分布均匀。正极极片在涂敷正极材料时一侧边缘不涂布的侧面和负极极片涂覆负极材料时留白的一侧面都作为极耳分别焊接在电池正、负极上,正、负极极片之间通过隔膜隔离开,这样电流在集流体流经的距离短,可以实现高功率密度,极片发热量也小。 电池极耳设计和极片涂布、卷绕加工过程如图2所示,正负极极片制造时,采用连续涂布工艺,在极片两侧留出不涂布的留白区域。 4680电池在能量密度和功率输出方面具有一定优势,但由于卷芯中电极更长,可能会加剧内部电流和温度分布的不均匀性。圆柱直径增加时,由于电池的表面积/体积比降低,可能会导致有效热管理出现问题。为解决这些问题,特斯拉提出了一种“无极耳”集流方式,通过使用集流体箔本身(箔边缘)来实现电流收集,电池内部的电流分布更加均匀。文献报道,通过模拟研究发现采用传统极耳设计的电池以大约1C的倍率放电时,由于沿集流体长度方向的高欧姆损耗,会导致局部电流密度分布非常宽。随着温度的升高,电池电压也存在一定的温度依赖性,集流体中的高欧姆损耗会产生大量热量。若电池没有主动冷却时,在环境热损失最小情况下会导致温度升高80℃。而采用无极耳设计时,电流密度分布相对均匀,沿集流体长度方向的欧姆损耗减少,从而使得电池运行过程中温度仅比环境温度高20℃,比传统极耳设计低60℃。当采用传统的极耳设计时,集流体的欧姆损耗导致的热量损失是无极耳设计时的5倍。 特斯拉的干法电极技术包括三个步骤:(i)干粉末混合,(ii)从粉末到薄涂层成型,(iii)薄涂层与集流体压合到,这三个步骤都没有溶剂。干法电极工艺具有可扩展性,能够适应当前的锂离子电池化学体系以及先进的新型电池电极材料。大量商用负极材料(如硅基材料和钛酸锂(LTO))以及正极材料(如层状三元NMC、NCA、LFP、硫),证明了干电极工艺的稳定性和普适性。采用Maxwell专有的干法工艺进行粉末混合,形成由活性材料、粘合剂和导电添加剂组成的最终粉末混合物,如图3a所示。将该粉末混合物挤出压延以形成连续的自支撑干涂层电极膜,电极膜还能够卷绕成卷状(图3b)。调整薄涂层电极膜的加工条件,可以控制材料负载量和涂层厚度,制备出多种干涂层电极结构。最后,薄电极层与集流体压合在一起,形成电池极片(图3c)。 图3 (a)粉末混合物,(b)成卷的薄电极层,(c)薄涂层与集流体压合的电极 以NMC111为正极,石墨为负极,由于工艺不同,采用了不同的粘结剂,在等浓度下制备了两种类型的电极。0.1C的恒定电流将电池充电至100%SOC,然后在以不同能够倍率放电。在低倍率恒流放电条件下,两种涂层电极的电池放电容量均为105mAh,在0.1C放电时均能保持100%的容量。不同放电倍率测试结果表明,干涂层电极比湿涂层电极输出更大的功率,如图4所示。 (4)CTC 技术(Cell to Chassis,电芯直接集成到车辆底盘上) 4680 电芯以 CTC 的方式直接铺设到了底盘之中,进一步减少电池包的零部件数量和重量,从而增加车辆的续航。马斯克表示采用了CTC技术后,可以节省370个零部件,为车身减重10%,可以将每千瓦时的电池成本降低7%。 刀片电池直接将电池部件拉长像刀片一样集成在电池包的边框上,省去模组和大部分结构件,由电芯直接成包,而且更薄的厚度也进一步降低了穿刺过程中的热量累积,提升了电池包的强度和安全。据比亚迪给出的数据,刀片电池pack较普通磷酸铁锂电池成本下降30%、单位体积能量密度提升50%。 刀片电池内部结构如图6所示,对于刀片状长条形电池,隔板将壳体内部分隔出若干个容纳腔,容纳腔内设有极芯组,极芯组含有一个极芯或两个极芯并联,极芯组之间通过极芯连接件串联连接,极芯连接件贯穿相邻两个极芯组之间的隔板。第一代刀片电池内部共有3组极芯组;隔板上设置有可以通过电解液的注液孔,注液孔连通隔板两侧相邻的两个容纳腔,即使从某一个容纳腔处注入电解液,电解液也能够由注液孔流至其他容纳腔,保证各个容纳腔均能够很好的注入电解液。最终电池长度L=400~2500mm。 常见的新能源汽车,其宽度一般在1米以上,长度则在数米;而新能源汽车的动力电池包,一般放置在新能源汽车的底部;目前市场上的动力电池包,一般都是宽度方向与新能源汽车的宽度大概一致,大概在1米以上。长度则根据新能源汽车的底部预留空间而定,一般都在2米以上。整个动力电池包无论在长度还是宽度方向,都超过1米;而目前单体电池的长度一般在0.3米左右,所以在动力电池包中,需要并排设置至少3个单体电池,甚至更多。并排设置多个单体电池,对每个单体电池均需要添加固定结构,同时,相邻两个单体电池之间需要通过外设的动力连接件进行动力连接。导致单体电池安装结构较多,不仅成本提高,而且导致整体重量上升;同时,单体电池安装结构占用了较多的包体内部空间,造成动力电池包整体容量降低,单体电池并排设置越多,空间浪费就越多。另外,因需要设置多个外置动力连接件进行动力连接,导致内阻增加,提高了动力电池包在使用中的内耗。 单体刀片电池的长度L设计成600mm-2500mm,由于单体电池本体足够的长,在单体电池的外表面设有设有支撑区,可以直接将单体电池支撑到支撑区。汽车底盘上设有向下凹陷的腔体以便装配单体电池,这样,在电池包内无需设置任何加强筋,电池包中放置电池阵列,单体电池与单体电池之间通过胶粘结,直接通过连接的单体电池承担加强筋的作用,极大的简化了电池包的结构,且减少了加强筋占用的空间以及单体电池的安装结构占用的空间,从而进一步提高空间利用率,以进一步提高续航能力。 图7 刀片电池阵列直接布置在汽车底盘的电池容纳腔内组成电池包 通过刀片电池单体的尺寸参数等的设计,可以提升电池的散热效果。刀片电池在同等条件的快充下,其温升较传统电池均有不同程度的降低,具有优于现有技术的散热效果,将该单体电池组装成电池包时,电池包的温升也有所降低。电池包通过单体刀片电池的排布、尺寸参数以等因素的设计,空间利用率能够突破现有电池包的限制,从而实现更高的能量密度。 3、宁德时代:CTP(Cell to Pack)技术 CTP(Cell to Pack)技术,又称无模组设计。直接将多个电芯布置于箱体,无需先将多个电芯组装成模组。零部件数量大幅减少,底盘空间利用率大幅提高,制造成本进一步降低。动力电池高效成组CTP技术打破了行业固有的“单体成组模组再成组电池包” 三级成组设计思维,从电池包结构高度集成、新工艺研发以及热管理优化等方面开发了全新的动力电池高效成组CTP技术,实现两级成组—“单体直接成组电池包”。根据宁德时代公布的资料,其CTP电池包体积利用率提高了15%-20%,电池包零部件数量减少40%,生产效率提升了50%,大幅降低动力电池的制造成本。同时,减少了传统模组的生产工序,生产效率提高20%。量产电池包重量能量密度超过170Wh/kg,同时在研产品电池包重量能量密度达到215Wh/kg。 宁德时代 CTP 技术是将一个大的模块通过若干个塑料散热片分割成小空间, 这些塑料散热片可以像电脑硬盘一样插入小空间。每个电池的侧面还贴有一个导热硅胶垫片, 并且在电池宽度方向的散热板上有一个冷却通道, 可以直接与外部冷却管路连接。这可以减少大约 40%来自模块之间连接线束、 侧板、 底板等的部件。去掉电池模块, 将电池直接集成到电池组中, 可以提高电池组的空间利用率, 减轻电池组的质量, 提高能量密度, 降低成本。宁德时代 CTP 技术电池如图8所示。固定梁将箱体分隔为多个容置腔,电池包包括多个电池单体,且多个电池单体在垂直于高度方向的平面内分为多组,各组电池单体均具有至少两个电池单体且分别设在不同的容置腔内。最底层的电池单体与箱体内底面之间、各组电池单体中的相邻两个电池单体之间、以及约束部件与最顶层的电池单体之间设有粘接层。 1、箱体组件;11、箱体;111、第一翻边;12、固定梁;121、第一安装孔;13、容置腔;2、电池单体;20A、第一组电池单体;20B、第二组电池单体;3、约束部件;31、限位部;32、安装部;321、安装块;322、第二安装孔;4、外盖;41、第二翻边;5、紧固件。 2021年9月17日,中航锂在2021世界新能源汽车大会(WNEVC)上发布了中航锂电面向TWh时代的全新设计技术产品——One-Stop Bettery。采用该项技术的产品,三元锂电池系统电芯能量密度300Wh/kg,pack能量密度240Wh/kg,续航里程可以达到1000km。磷酸铁锂电池系统电芯能量密度200Wh/kg,pack能量密度160Wh/kg,续航里程可以达到700km。 电芯层级:采用了0.22mm的超薄壳体技术、多维壳体成型技术、“无盖板”设计、多功能复合封装技术、模块化极柱、一体式电连接技术、高剪切外绝缘技术、柔性泄压技术,可以实现让空间利用率提升5%、结构重量降低40%、零部件减少25%、成本降低15%。 生产工艺:电芯生产过程中,采用超高速复合叠片、原位无尘装配技术、高速薄璧焊接技术、集流体直连焊接技术,能够让生产效率提升100%、生产空间减少50%、制造成本降低30%、能耗降低60%、异物“零”引入风险。 电池系统:采用无模组技术、极简串联拓扑电连接技术、复合嵌入式箱体技术、高效热管理技术、集成液冷技术、积木拼接成组技术、热失控抑制技术,空间利用率提升5%、能量密度提升10%、零部件减少20%、换热效率提升50%、成本降低10%。 弹匣电池是一项专门提升动力电池安全性的系统性技术,是从电芯本征安全提示,到被动安全强化,再到主动安全防控的一整套安全技术。弹匣电池四大核心包括了超高耐热稳定的电芯、超强隔热的电池安全舱、极速降温的速冷系统以及全时管控的第五代电池管理系统。 通过正极材料的纳米级包覆及掺杂技术、新型添加剂的应用实现SEI膜的自我修复。高安全电解液,自聚合高阻抗界面膜,大幅降低热失控反应热。这一系列关键技术的应用,使电芯的耐热温度提升30%。电芯正极是三元锂材料。 弹匣电池采用超强隔热电池安全仓,网格纳米孔隔热材料,可以使相邻电芯不发生热失控。这个电池安全仓就相当于一个弹匣,把电芯与电芯之间隔开。电池包采用耐高温壳体可承受1400℃高温。 采用全贴合液冷集成系统,高效散热通道设计,高精准导热路径设计,散热面积提升40%,散热效率提高30%。 除了上述的硬件的改善外,BMS软件给弹匣电池的安全性提供了最后一层屏障。最新一代电池管理系统芯片,可实现每秒10次全天候数据采集,相比前代系统提升100倍。可以24小时对电池状态进行监测,发现异常时,立即启动电池速冷系统为电池降温。 针 刺实验实验结果显示:整包在试验过程中热事故信号发出5分钟后,仅出现短暂冒烟(1分钟),无起火和爆炸现象。静置48小时后,电压降至0V,温度恢复至室温。针 刺后只有被刺电芯模块热失控,没有蔓延到其他电芯。打开电池整包,观察内部结构完好。 隔热仓和散热系统也会增加电池包的重量,所以在电芯材料一样的前提下,采用弹匣电池这种结构后,整包的能量密度必然会低于普通三元锂电池包,此外电池包的成本也会明显提高。 大禹电池技术集热源隔断、双向换流、热流分配、定向排爆、高温绝缘、自动灭火、正压阻氧、智能冷切等8个设计理念,在采用全新开发的双层复合材料的电芯以及采用高温绝热复合材料模组的模组的双重防护下,大禹电池技术实现了对热源的高效隔断。此外,智能冷切的设计理念,可以使得在电池管理系统识别到电芯触发热失控的时候,通过BMS和云端双重监控,确保整台车能够及时开启冷切系统,并有效抑制热流的扩散。突破电池本征、PACK设计、BMS 3大维度39个热失控故障节点,全面保障电池安全,实现“控+导=通”热失控安全矩阵,保证在“大容量高镍电芯”“电池包任意位置”“加热两个电芯并连续触发热失控”的情况下都能实现不起火、不爆炸。 电芯方面,所有电芯间采用全新开发的双层复合材料,既能隔离热源,又耐火焰冲击,有效解决了传统气凝胶不耐冲击的痛点。同时结合不同化学体系电芯循环膨胀特性不同,设计双层复合材料,既可有效解决电芯膨胀对空间的需求,又能隔离热源。 模组方面,每个模组间都采用高温绝热复合材料,可阻止火焰冲击和长时间传热传导。防护罩设计定向排爆出口,能快速将模组内部高温气火流排出,避免模组内部热蔓延。 电池发生热失控过程中会产生大量高温、高压气火流,大禹电池技术通过对多种类换流通道设计方案仿真模拟,实现换流强度和比例的精准化设计,有效控制热源按预定轨迹流动,减少对相邻模组的热冲击,可以避免再次引燃。 通过搭建燃烧模型、热力学与流体力学拟合仿真、冲击强度和压力计算等虚拟技术应用,可实现气火流在不同结构通道内的均匀分布。电池包之内设计了纵向通道,纵向通道和底部的换流通道是连通的,在气压的作用下会上下流动。根据热量、气流强度的冲击的大小,温度的变化,按照热源轨迹去流动,避免对相邻的电芯相邻的模组产生急剧性的热冲击,引发第二次热失控。 通过分流、导流、换流将火源快速引导至灭火通道并安全排出。通道内压力和流量均匀化调节,消除了热量集中,使气火流在通道内分层均匀流动。通过定向排爆和换流,可以使高温气体,例如NCM811电池,超过1000℃的高温迅速降到200℃以内。 在电池包的定向排爆出口,设置多层不对称蜂窝状结构,实现火焰快速抑制和冷却,并通过多点化、均布化、小型化设计,有效减小体积、降低重量,提升降温效果,气火流排出到电池包外的温度已经低于100℃。 根据蜂窝孔径及单位气体质量流量,在通道和灭火设计时,灭火的孔径大小尺寸经过多次测试最优化,始终保持包内压力高于包外,避免因氧气进入导致二次燃烧。 因为在热失控过程中,传统设计的高温绝缘层会被烧掉,电池包内的金属部件会起弧。高温绝缘就是对电池包内的高压部件进行绝缘防护。 针对电池安全拥有智能冷却监控和自动冷却启动系统,当电池管理系统识别到电芯已触发热失控,能够通过BMS和云端双重监控,确保整车快速开启冷却系统,抑制热扩散。 大禹电池进行了热失控测试,加热两个电芯连续触发热失控的测试方法。最终结果显示,测试中连续发生3次多个电芯集聚触发热失控,温度最高达到1037℃,电池包内气压达到三次高峰,瞬间最高气压约16kPa,通过灭火系统抑制电池包外溢烟雾最高温度低于100℃,电池包没有起火和爆炸。 著作权归作者所有,欢迎分享,未经许可,不得转载
首次发布时间:2023-09-20
最近编辑:1年前