拉延成形力如何估算?
拉延的成形力如何计算?这还用计算呀,xx软件直接读取即可。随着CAE软件的持续应用和发展,对于板料成形力的计算,多数冲压工程师都选择直接在软件中读取。不得不说,软件输出的结果比较直观,也相对准确。不过,通过CAE软件读取的前提是需要对冲压工艺进行正确的设置和计算,最后得出的结果,这需要花费比较多的时间,更多的是应对正式的冲压工艺排布。那么,在没有CAE软件的时候,或者继续快速给出评估结果的时候,我们该如何计算呢?这时就需要采用拉延成形力计算公式。简单拉延的力由三部分构成:P1 = P2 + P3。P1:是整体的成形力,不满足P1,零件是无法成形的。
P2:是凸模成形力,及零件形状部分的成形力,不满足P2,则零件可能成型不足,部分位置压到位,或者尺寸不稳定等。
P3:是压边圈力,是用于控制拉延材料流动的力,不满足P3,则零件的走料无法得到有效控制,零件可能会出现开裂起皱缺陷。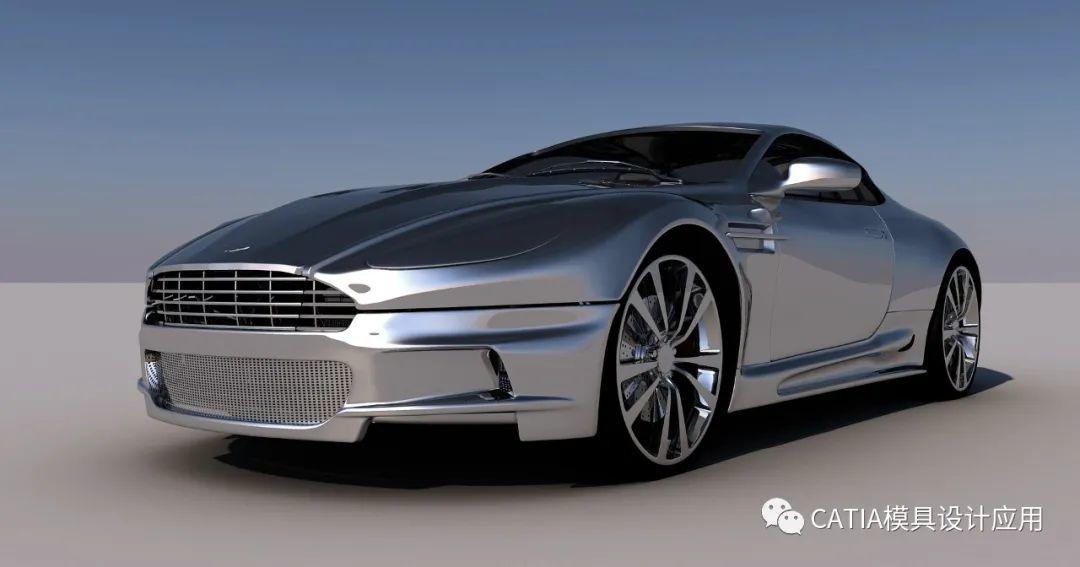
C:拉延系数,一般取值范围为从3.5~5。随着零件成形难度的增加,系数增加。机盖外板、顶盖外板、门外板等造型平坦、拉延深度较浅的零件通常取值为3.5;翼子板、侧围等拉延深度较深的外板通常取4,特别复杂的侧围也会增加为4.5;复杂的内板如门内板,拉伸深度深且形状复杂,则取值为5;其他的一般性内板,选择系数4.5。综上可以看到,该系数认为的被分为4个档次,与零件的特征复杂度及拉伸深度正相关,而实际的零件是很难简单用这四个档次覆盖的,则需要有经验的工程师进行人为调整。L:指的是凸模轮廓的长度,长度越长说明拉深面积越大,这个可以通过测量零件的边界,或者根据经验绘制得来。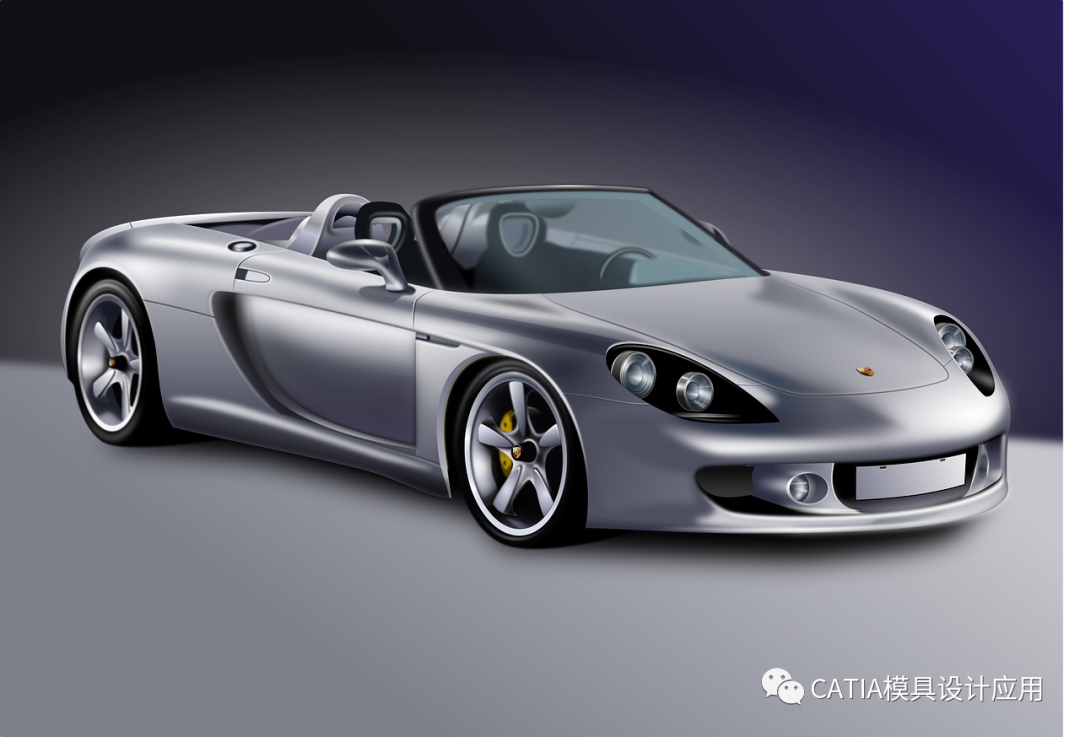
D:是调整系数。通常,对于轮罩外板、前梁等零件,选择0.15;门内板通常选择0.22;门外板、侧围、发盖外板等零件选择0.29。可见,该系数与拉深的深度是负相关的,即越是需要提高压边力来阻挡材料流动的零件,其系数越高。
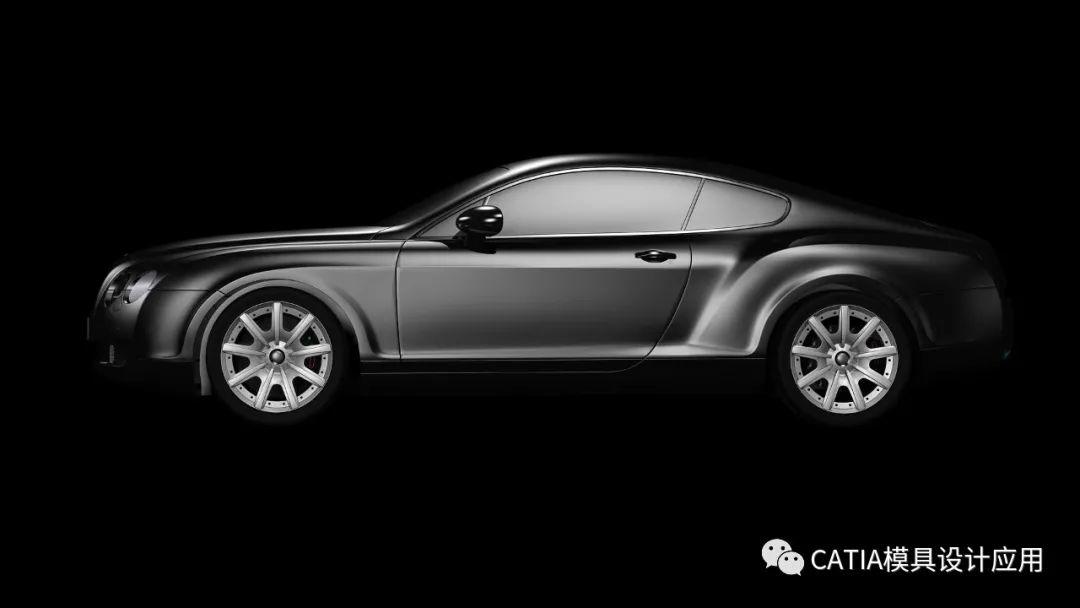
综上,我们可以通过经验公式进行拉延力的计算,但是,不得不说,这里面有很多经验因素,更多的可以适用于压机的选用,若保险起见,在最后还需要增加一个保险系数,以防选择的压机压力不足。其实我目前也更多的到CAE软件中获取自己所需的数值,因为更加可信。本文所谈公式,因笔者经验所限,也未必完全正确,大家辩证参考。 著作权归作者所有,欢迎分享,未经许可,不得转载
首次发布时间:2023-10-12
最近编辑:1年前