近日,西南交通大学在基于同步辐射X射线三维成像的增材钛合金旋转弯曲疲劳损伤演化原位表征及性能评价方面取得重要进展,并在国际疲劳Top期刊International Journal of Fatigue发表题为 “Rotating bending fatigue mechanisms of L-PBF manufactured Ti-6Al-4V alloys using in situ X-ray tomography” 论文。本研究创新性设计了国际上首台基于同步辐射X射线三维成像的旋转弯曲疲劳损伤原位表征装置,建立了一种全新的基于成像数据的旋转弯曲疲劳裂纹扩展速率测试方法,明确了微观组织缺陷与孔隙缺陷在低孔隙率增材钛合金旋转弯曲疲劳裂纹萌生中的竞争关系,最终提出了基于断裂力学并考虑微观组织缺陷特征的增材钛合金旋转弯曲疲劳性能评价方法。轨道交通运载系统全国重点实验室博士生吴正凯为论文第一作者、硕士生何子昂为第二作者,吴圣川研究员为通讯作者,中国航发商发雷力明研究员和中国航发北京航空材料研究院刘昌奎研究员等为共同作者。该工作得到国基金大科学装置联合基金 (U2032121) 资助。钛合金在航空航天、深海舰船、轨道交通等领域应用前景广阔。随着金属增材制造技术的快速发展,增材钛合金在旋转弯曲部件中的应用日益迫切。例如,航空发动机中的燃汽轮机叶片和转轴等零部件主要承受旋转弯曲疲劳载荷。然而,旋转弯曲疲劳载荷引起的梯度应力分布特征与传统轴向疲劳明显不同,而且增材制造钛合金特有的微观组织与孔隙缺陷特征与传统制造材料具有本质区别,导致目前对增材钛合金在旋转弯曲疲劳载荷下的损伤机制认识严重不足。扫描电镜(SEM)和电子背散射衍射(EBSD)等传统表征技术可观察材料“静态”损伤情况,具有表面性、局域性、破坏性等缺点。高时空分辨X射线三维成像可实现对材料内部损伤演化的原位动态表征,优势显著。论文创新性设计了一种基于同步辐射成像的原位旋转弯曲疲劳装备,深入研究了激光粉末床熔化(L-PBF)成形Ti-6Al-4V钛合金的旋转弯曲疲劳机制。本工作通过研制高时空分辨X射线三维成像的原位旋转弯曲疲劳试验装置探索了增材制造材料及部件在旋转弯曲疲劳加载条件下的疲劳损伤机制及抗疲劳断裂性能评价方法。
高时空精度的同步辐射光源具有非破坏性穿透大块金属材料结构的技术优势,而研制原位旋转弯曲疲劳装置是开展原位疲劳试验研究的必要条件。针对国内外在原位成像旋转弯曲疲劳试验装置领域的技术空白,本论文创新性开展了原位旋转弯曲疲劳加载结构设计和系统控制研究,确定了以“悬臂梁式”单点弯曲为加载原理的立式对称加载结构,以“伺服电机+涡轮丝杠”相组合的方式成功实现了旋转弯曲疲劳加载。随后,基于同步辐射X射线三维成像技术和原位旋转弯曲疲劳试验装置,重点观测了L-PBF制造Ti-6Al-4V钛合金在旋转弯曲疲劳加载下不同循环周次下的内部缺陷演化与疲劳裂纹扩展行为,通过对获取的不同疲劳寿命阶段的同步辐射CT图像进行可视化三维重构及定量化分析,进而计算出试样在旋转弯曲疲劳载荷下的裂纹扩展速率(FCG)。最后,再采用SEM、EBSD等二维材料表征技术对微观组织特征及疲劳断口形貌进行分析,结合材料孔隙缺陷分布和旋转弯曲应力分布特征,对旋转弯曲疲劳裂纹萌生机制进行了深入探讨,最终建立了低孔隙密度下致旋转弯曲疲劳失效的评价方法。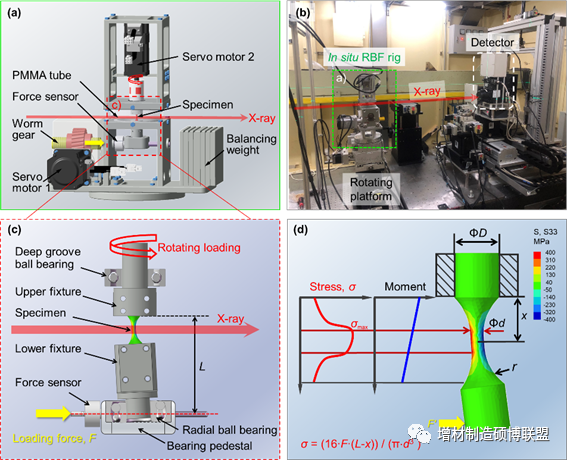
图 1:原位成像旋转弯曲疲劳机:(a) 原位试验装置设计原理图;(b) 上海光源BL13HB线站原位试验现场图;(c) 旋转弯曲疲劳加载原理图;(d) 旋转弯曲疲劳试样应力分布及计算方法。
试验结果表明,在去应力退火热处理后,L-PBF成形Ti-6Al-4V钛合金材料的相对密度极高(大于99.99%),其在沿垂直建造方向上的微观组织为初生β柱状晶,柱状晶内部组织为魏氏体集束和少量网篮组织构成的混合组织。采用原位成像旋转弯曲疲劳装置得到的疲劳数据与公开发表文献中旋弯疲劳数据具有基本一致的分布特征,且基于成像数据获取的裂纹扩展速率与标准试验结果相近,证明了该原位试验装置及数据的可靠性。旋转弯曲疲劳载荷下的裂纹形貌呈典型的螺旋状或阶梯状,且观察到了单裂纹萌生以及多裂纹萌生与裂纹合并现象。同步辐射CT和断口SEM观测结果表明,旋转弯曲疲劳裂纹均萌生于试样微观组织而不非传统意义上的孔隙缺陷。对裂纹源特征及关键区域孔隙尺寸特征进一步分析,发现缺陷容限评价方法——Kitagawa-Takahashi(KT)图对极低孔隙率L-PBF成形Ti-6Al-4V钛合金的旋转弯曲疲劳性能评价不再适用,这与旋转弯曲加载下试样高应力区域体积减小及其内部低孔隙率特征相关。在此条件下,由多个具有相同或相近晶体取向的板条α相组成的具有共享滑移系特征的α colony组织成为循环应力下试样表面最薄弱区域,这是导致疲劳裂纹萌生的主要原因。进一步地,基于微观组织与孔隙缺陷之间的疲劳裂纹萌生竞争机制,提出可将裂纹源处微观组织特征定义为微观组织缺陷,从而建立了考虑微观组织缺陷特征的增材钛合金旋转弯曲疲劳性能评价方法。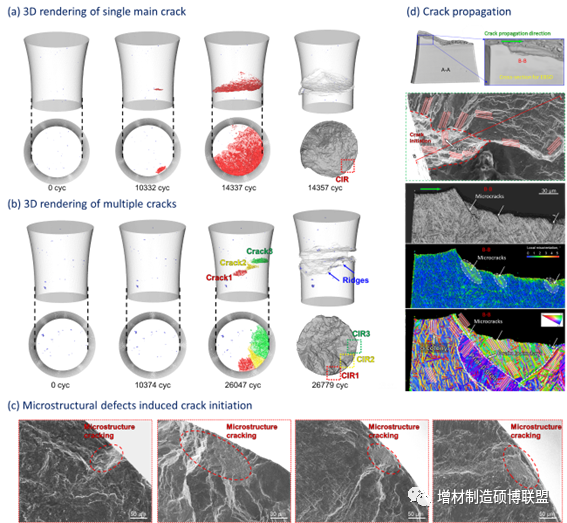
图 2:旋转弯曲载荷下增材钛合金疲劳裂纹萌生与扩展:(a) 单一裂纹与 (b) 多裂纹萌生与扩展的三维成像表征;(c) 微观组织缺陷导致裂纹萌生; (d) 微观组织对裂纹扩展过程的影响。
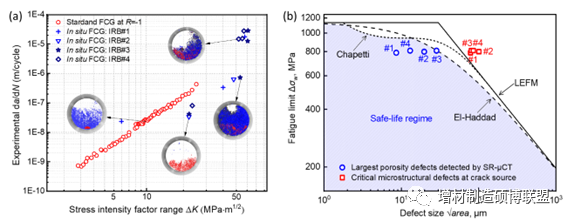
图 3:(a)基于成像数据的裂纹扩展速率测试;(b)考虑微观组织缺陷的旋转弯曲疲劳性能评价K-T图。 本研究创新性设计了领域内首台基于同步辐射X射线三维成像的原位旋转弯曲疲劳试验装置,建立了基于三维成像数据的旋转弯曲疲劳裂纹扩展速率测试方法,阐明了微观组织缺陷与孔隙缺陷在增材钛合金旋转弯曲疲劳裂纹萌生机制中的竞争关系,最终提出了考虑微观组织缺陷特征的增材钛合金旋转弯曲疲劳性能评价方法。研究结果为增材制造钛合金旋转弯曲加载材料及部件的疲劳性能可靠评估和寿命准确预测提供了一种新思路。