在燃气轮机研制阶段,需要对零部件设计进行多次改进迭代。为解决传统加工方式周期长、成本高的问题,将增材制造技术应用于燃气轮机研制过程中。借助于金属3D 打印设备,开展了燃气轮机关键部件增材制造成型研究;借助于非金属3D 打印机,开展了燃气轮机模型的成型研究。结果显示,增材制造技术能够实现具有非常复杂几何结构的零部件的高效、快速成型,而不必借助额外的工装。将增材制造技术应用于燃气轮机研制过程有助于快速实现产品设计迭代,缩短研发周期、节约研制成本、提高产品性能,适应于先进高性能燃气轮机发展趋势。
增材制造是近年来快速发展的一种数字制造技术[1] 。根据美国测试和材料协会(American Society of Testing Materials,ASTM)标准,增材制造被定义为“一种借助三维模型数据制造零件的方法,通常是将材料一层一层地连接起来,而不是通过机械加工的方式”[2] 。相比于传统加工方式,增材制造技术能够实现具有非常复杂几何结构的零部件的高效、快速成型,而不必借助于额外的工装或工具[3-4] 。另外,采用增材制造技术可以减少组件数量、减轻零件质量、提高零件强度。在航空领域有些非承力部件有减重的需求,借助增材制造技术可实现一些具有空间周期性的内嵌网格结构、蜂窝结构及其他形式多孔结构的零件的快速成型,而在增材制造技术出现以前,这类结构是无法被加工出来的。在燃气轮机低排放燃烧室的研制过程中,需要对燃烧室结构方案进行多次改进迭代,而其中一些零部件(如旋流器)结构复杂,采用传统加工方式只能通过铸造实现[5] 。而铸造周期长且开模成本高,客观上影响了低排放燃烧室研制迭代的周期。将增材制造技术应用于燃气轮机燃烧室的研制能够缩短研制周期,加快产品迭代设计进程,节省研制成本。在低排放燃烧室的研制过程中,由于贫燃预混方案的采用,极易引发振荡燃烧现象。为抑制振荡燃烧,往往采用蜂窝吸声结构(如图1)。而类似这种多孔结构,只能采用增材制造技术加工[6] 。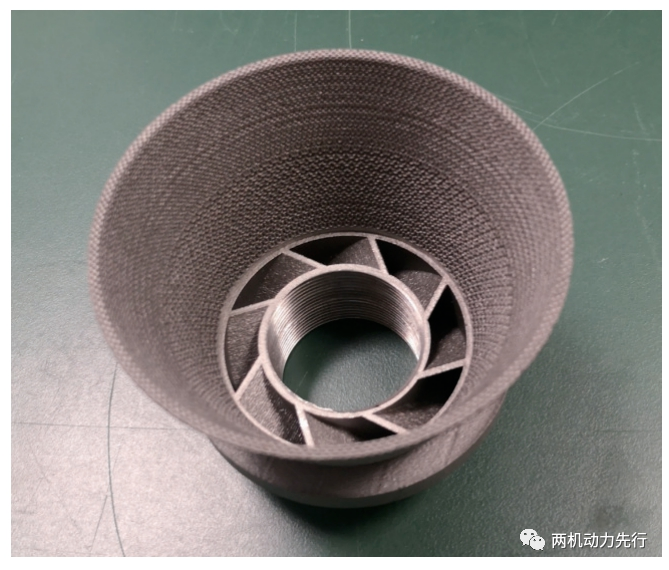
美国通用电气公司(General Electric Company,GE)和德国西门子公司针对增材制造技术在燃气轮机研制中的应用开展了大量的研究,并取得了相当丰富的研究成果。GE 于2016 年成立了GE Additive 公司,并开始研制基于增材制造的LEAP发动机燃油喷嘴(图2)。采用传统方式制造的LEAP 喷嘴结构复杂,由20 多个组件构成,每个组件需要单独加工,最后组装在一起,生产周期长。采用增材制造技术后,组件数量由20 多个减少为1 个,燃油喷嘴的质量较之前减轻25%,喷嘴强度提高5 倍,成本节省30%。截至2021 年8 月,GE 奥本工厂已累计生产3D 打印LEAP 喷嘴超过10 万件[7] 。图2 GE 研制的LEAP 发动机3D 打印燃油喷嘴[8] GE 于2018 年试飞的ATP 发动机采用了大量3D 打印零件(图3),涵盖了机油箱、轴承座、框架、排气机匣、燃烧室、换热器和固定流道等部件。将855 个传统加工零件(占总零件数的35%)替换为12 个增材制造零件。这些3D 打印零件均采用了拓扑优化结构,在保证结构强度的前提下使得发动机质量更轻,油耗节省20%[8] 。
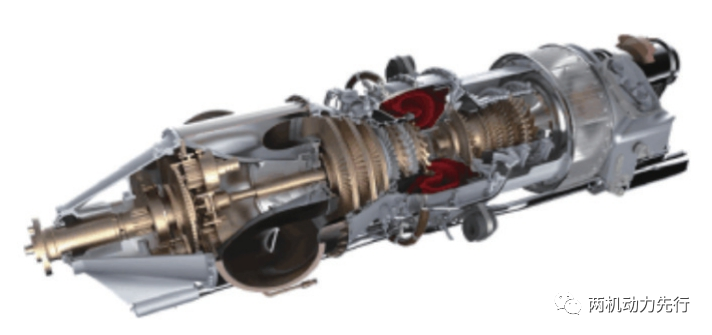
图3 采用大量3D 打印零件的ATP 发动机[8] 西门子SGT-700/800 燃烧室前端采用激光选区熔化(selective laser melting,SLM)技术制造后,由原来的13 个组件和18 个焊接处缩减为1 个组件和2 个焊接处[9] ,交付周期缩短了15%,修复速度提升60%,整套燃烧器的制造速度提升85%。西门子公司突破了基于增材制造的涡轮导叶和工作叶片的研发和应用技术,使用增材制造技术生产的转子叶片已经通过满负荷核心机试验的考核[10] 。叶片安装在西门子公司的SGT-400 工业燃气轮机上,输出功率为13 MW。试验中使用的叶片由材料解决方案公司负责生产。该增材制造叶片使用的是多晶镍超合金粉末,可以经受高温、高压和高转速工况下产生的巨大离心力。经试验检验,产品的表面粗糙度、精度和材料参数等对确保部件运行起到关键作用的指标得到验证。中国船舶集团有限公司第七〇三研究所是我国船用及工业燃气轮机研发基地,其燃气轮机专业研究方向已覆盖研发设计、成型工艺、软件开发、试验验证等多个领域,正尝试将增材制造技术逐步应用于船用及工业燃气轮机关键部件的研发设计与加工制造。目前在用燃气轮机研制过程中重点开展了金属材料增材制造领域中的SLM 技术和非金属材料领域中的熔融沉积(fused deposition modeling,FDM)技术研究,并取得了较为丰富的研究成果。SLM 是金属增材制造技术中最常见的一种形式。其主要步骤如下[11] 。1)前处理:首先设计打印零件的CAD 数字模型,将CAD 模型转化为STL 文件,借助Magics 或其他同类软件将STL 文件切片处理输出SLI 切片文件,随后将SLI 文件导入打印机。2)成型:成型过程如图4 所示。首先在打印机成型舱内成型平台上铺一层很薄(通常为0.04 mm左右)的金属粉末,铺粉完毕后,高能量密度的激光束会根据导入的模型信息熔化选定区域内的金属粉末。为保护金属在熔化过程中不被氧化,成型舱内要被充入高纯度的保护性气体(氩气或氮气)。该层激光扫描完成后,成型平台下降一个层厚,铺上新一层粉末,开始下一轮激光扫描。该过程将被不断重复,直至整个零件被成型出来。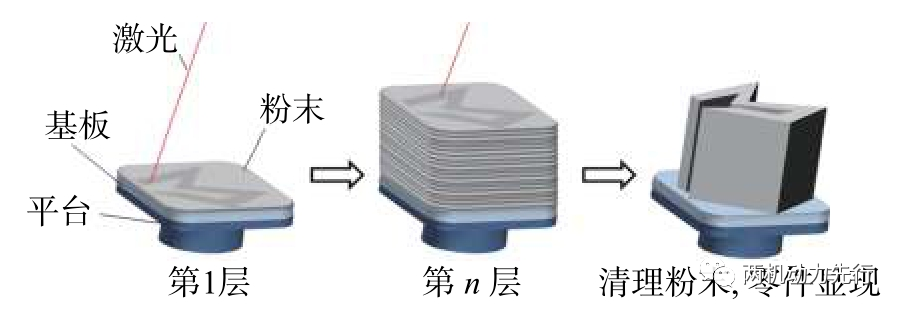
3)后处理:成型后的零件一般需要进行后处理,主要流程包括粉末清理、固溶热处理、线切割、支撑去除、表面质量改善、零件尺寸检验和无损检验(荧光检验、X 射线检验等)。根据材料特性和零件类型,工艺路线可调整。由于生产过程中的剩余金属粉末可回收再利用,SLM 技术相比于传统加工方式可大幅节省原材料的消耗。本文重点采用了SLM 技术开展了燃气轮机燃烧室零部件的设计、加工及试验验证。FDM 技术的成型过程如图5,原理是将丝状的热塑性材料(通常为ABS、PLA),通过带加热的喷头加热熔化,喷头在计算机的控制下,移动到成型区域的指定位置,将熔融状态的材料铺覆在上一层已凝固的材料上,这样的过程不断重复,直到整个零件被打印出来[13-14] 。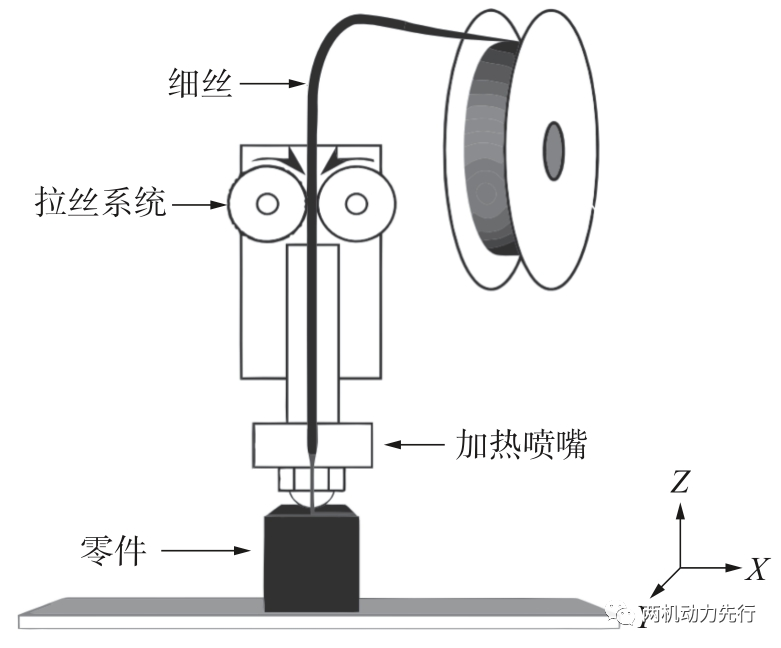
本文采用基于FDM 技术的非金属材料增材制造技术,实现了燃烧室零部件的打印成型。燃烧室旋流器若采用铸造方式生产,生产周期长达5 个月且开模成本很高,在研发设计设计段,需要反复改进设计,导致研发成本高、研发周期长。为缩短研发设计周期,采用SLM 增材制造技术进行旋流器成型。旋流器增材制造研制流程为:旋流器增材制造结构优化设计—金属粉末材料选取—SLM 增材制造工艺参数调试—产品成型—后处理及相关检验—产品性能试验验证。为了适应SLM 技术成型的要求,对原有旋流器结构进行了适应性调整:将旋流器外部结构(图6)优化为支撑最小化菱形结构。在不影响产品性能的前提下,提高成型的成功率。考虑到燃烧室部件属于高温部件,采用镍基高温合金GH3536作为成型材料,可耐温950 ℃。采用SLM 技术成型的旋流器通过了关键尺寸检验、荧光检验,并通过了旋流器流量试验测试。最终,基于SLM 技术成型的旋流器(图7)将生产周期压缩到2 个月以内,节约了生产成本,缩短了设计迭代周期。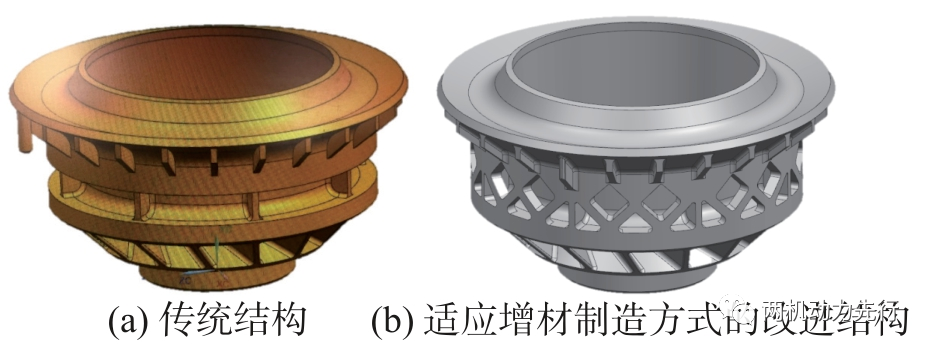
火焰筒混合器结构复杂,包含多个冷却环带结构,还有非均匀布置的气膜冷却孔,如图8 所示。若采用铸造方式生产,因零件壁厚较小(约2 mm),液态金属流动性差,不能一体成型,否则会产生大量的疏松、裂纹等缺陷,只能分段铸造,需要开设多个模具,铸造成功率较低,制造成本非常高。为解决这一问题,研发借助SLM 技术制造混合器。为满足更高的耐温要求,打印材料采用GH5188(耐温1 000 ℃)。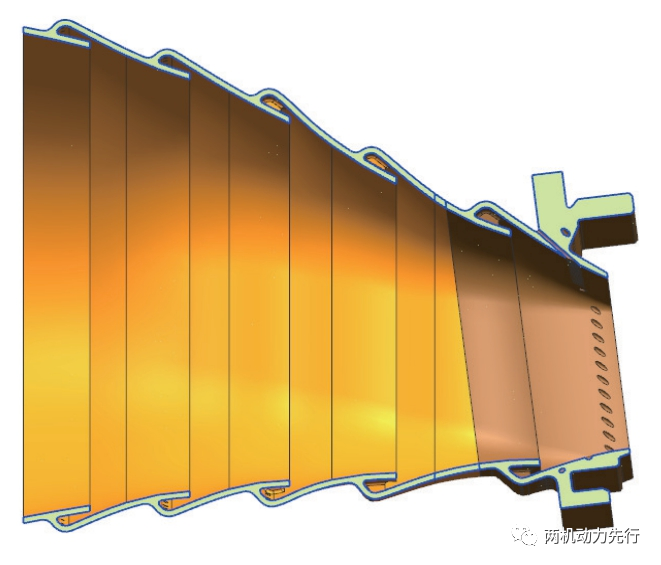
研究中开展了混合器的结构优化设计,在不影响产品使用性能的前提下,对局部结构进行微调,显著提高了3D 打印成型成功率;通过恰当的摆放实现了无支撑方案成型。整个混合器采用增材制造一体成型,减少了焊缝,有效降低了由焊接带来的变形。混合器增材制造实物如图9 所示。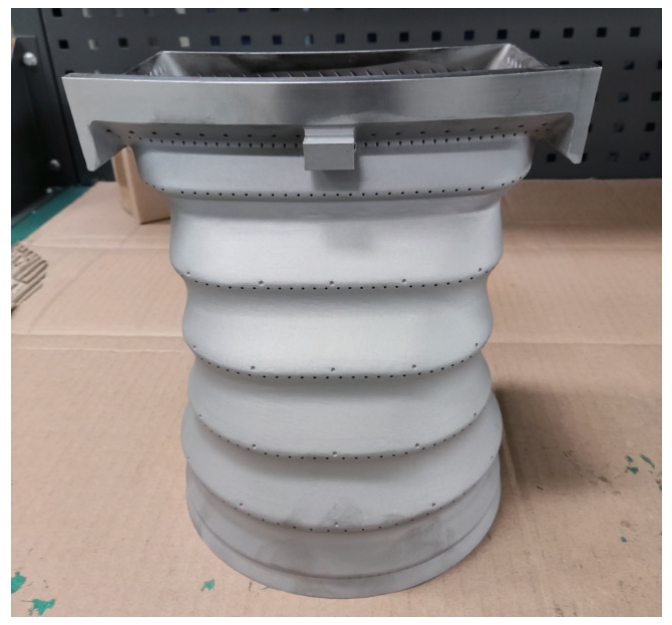
基于SLM 制造的某型火焰筒尾部,通过了三维尺寸扫描、荧光检测。该技术解决了复杂薄壁零件采用传统加工方式制造困难的问题,并节约了生产成本,提高了研发设计迭代速度。传统火焰筒筒身示意如图10 所示,传统火焰筒筒身采用一定数量的锥筒及混合器、嵌入件、冷却环、座圈等拼接焊接而成。混合器采用薄板材冲压制成;嵌入件、冷却环、座圈则采用铸造成型,铸造需要开模,周期长、成本高,且铸造成功率较低;锥筒使用薄板母材滚压成型后焊接成锥筒形状,组装焊接前需要保证每个锥筒的尺寸精度,且锥筒为薄壁件,所以对焊接工艺要求极高;每个锥筒上分布有60~120 个气膜冷却孔,需要通过电火花打孔成型。这些工艺导致用传统加工方式生产火焰筒工序繁多、生产周期长。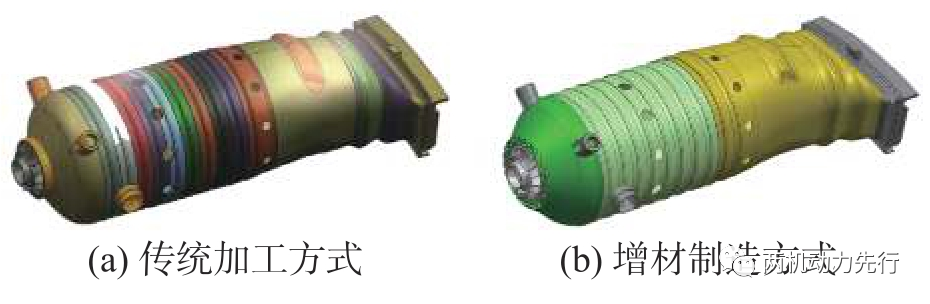
在低排放燃烧室的研制过程中,设计阶段需要对火焰筒的主燃孔、掺混孔以及冷却孔的大小、位置、分布方式进行多次调整,以达到更优越的性能,提高火焰筒的生产效率,缩短生产周期。为解决这一问题,开展SLM 技术在火焰筒生产的实例研究(图11),打印材料为GH3128。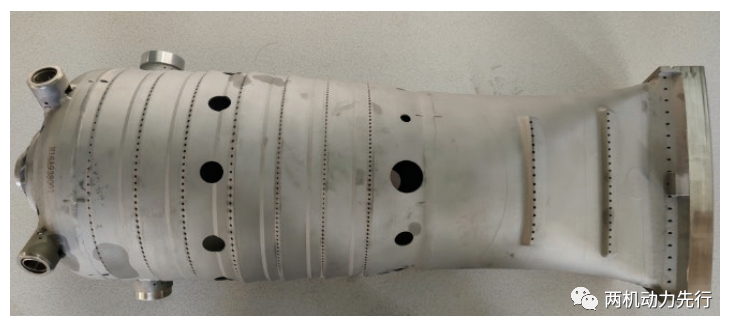
在基于SLM 成型的一体化火焰筒结构设计中,将原有通过焊接相连的锥筒合并为一个整体,大幅减少了焊接工序;3D 打印成型实现了主燃孔、掺混孔及气膜冷却孔的直接成型,节省了电火花打孔工序。如采用传统的加工方式,火焰筒包含30 多个零组件,生产周期长达8 个月;采用增材制造技术后,零部件数量缩减至13 个,生产周期可缩短至3 个月。燃烧室旋流喷嘴结构非常复杂,旋流叶片由复杂曲面构成,叶片内部含有流道内腔。采用传统加工方式制造,需要采用铸造和机械加工相结合的方式,在少量生产的情况下成本高[15] 。为解决这一问题,研究采用SLM 技术生产旋流喷嘴(图12),为满足耐温需求,打印材料为GH5188。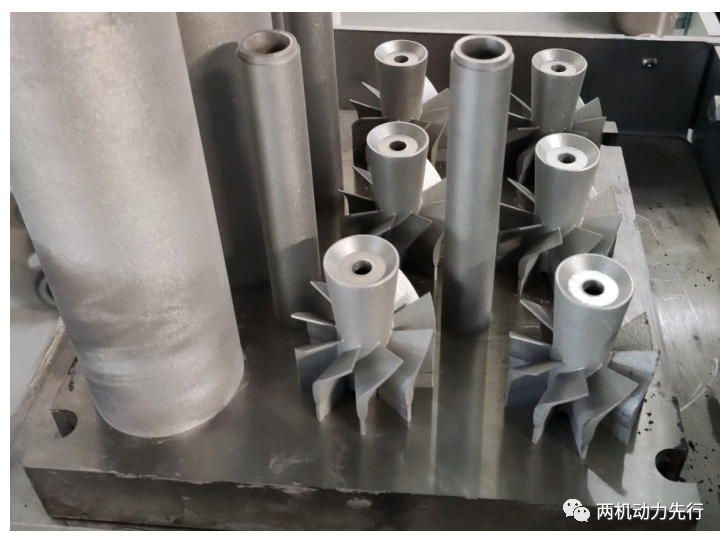
为提高成型成功率,减少支撑数量,采用了将旋流喷嘴叶轮、外筒、燃料杆分别成型,然后焊接的方式加工。打印件通过了三维尺寸扫描、荧光检测,将旋流喷嘴的加工周期缩短50%以上。燃气轮机涡轮导叶内部有非常复杂的冷却通道(图13),若采用铸造方式成型,成本高、生产周期长、成功率低。为解决这一问题,研究采用SLM 技术直接成型,材料为GH3625。在研究过程中,为提高成型成功率,多次对涡轮叶片的摆放角度进行调整;为提升表面粗糙度,对叶片表面进行了喷砂处理。零件通过了外形尺寸的检测,满足设计要求。通过增材制造成型的涡轮叶片如图14 所示。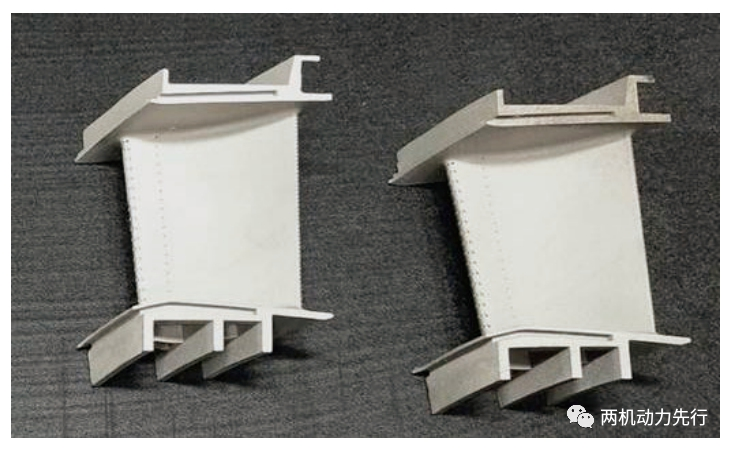
基于非金属材料的FDM 技术常用于展示教学模型、铸造模具的快速成型。在燃气轮机研发过程中,可用于打印方案设计模型,便于观察复杂零部件内部结构、分析装配关系等。基于非金属材料的FDM 技术,对某型号火焰筒进行了改进设计,并打印了火焰筒1/4 剖切模型,如图15 所示。该火焰筒模型主体部分为一体化打印成型,旋流器、座圈、定位器单独打印并粘接在主体部分上。该模型可用于火焰筒结构展示使用,能够非常直观地看到火焰筒的结构细节。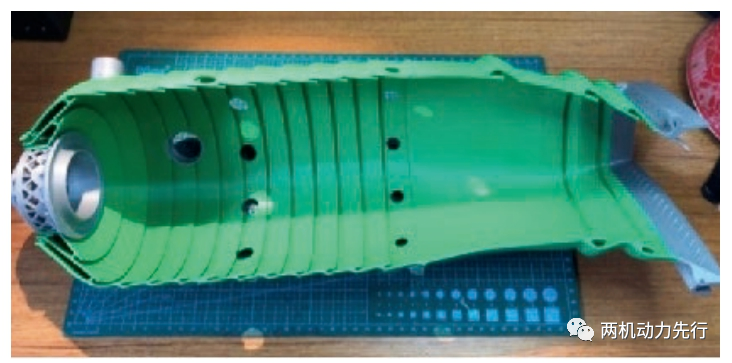
在开展某型燃气喷嘴增材制造适应性改进设计过程中,将FDM 技术应用于方案模型的打印中(图16)。为便于观察喷嘴内部流道详细结构,打印模型为2 个半剖模型,可通过销钉组合在一起。
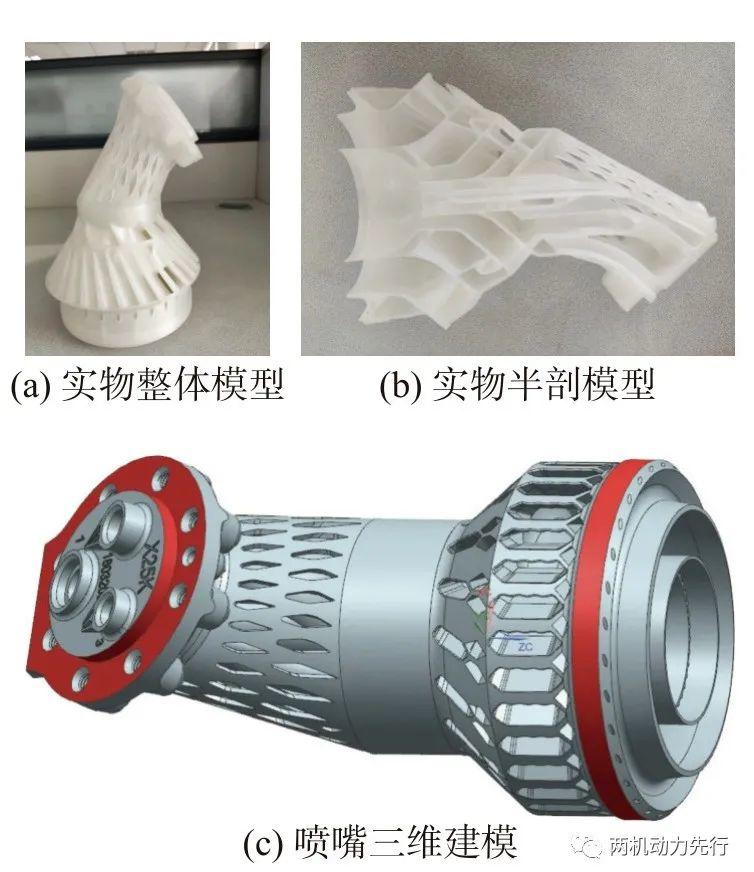
基于FDM 技术开展了某型燃气轮机展示模型的设计及打印工作,如图17 所示,对真实尺寸燃气轮机按比例缩放,并对一些结构细节进行简化。模型整体由2 000 多个零部件组成,总质量约18 kg。此外,还打印了某型燃气轮机动力涡轮的展示模型如图18 所示,模型转子部分可在电机驱动下旋转。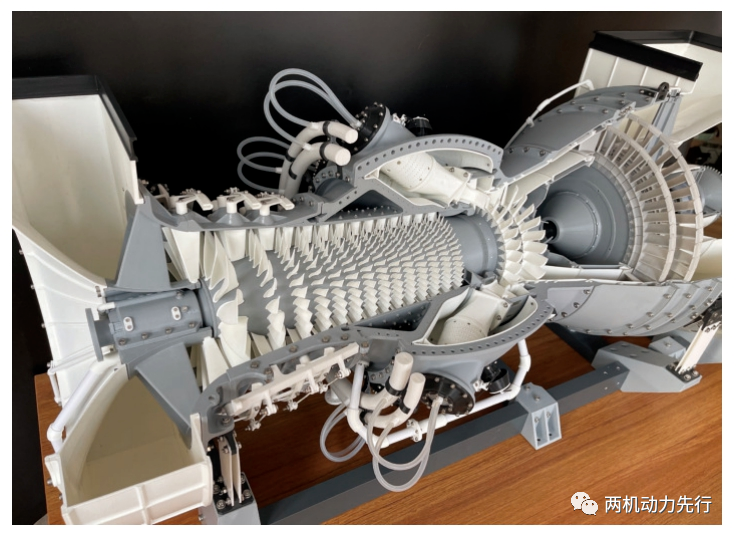
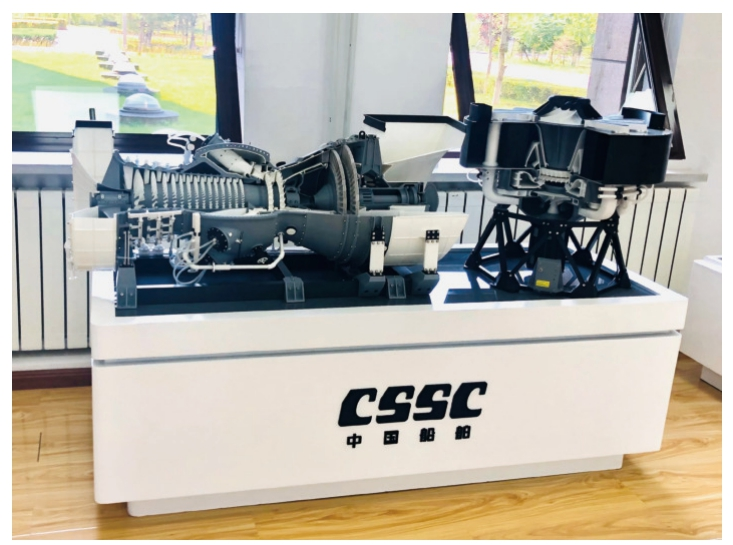
图18 基于FDM 制造的展示用燃气轮机模型(左)和动力涡轮模型(右) 本文依托中国船舶集团有限公司第七〇三研究所在船用及工业燃气轮机领域的研发基础,尝试将增材制造技术运用到燃气轮机部件的制造中。基于金属材料的SLM 技术,成功实现了旋流器、火焰筒尾部、火焰筒、旋流喷嘴等零部件的成型;基于非金属材料的FDM 技术,成功实现了火焰筒、燃气喷嘴、燃气轮机整机及动力涡轮模型的成型。在研究过程中,研发团队结合自身专业优势,将增材制造思想融入部件结构设计中,使得改进后的零部件既能满足其功能性要求,又能提高打印成型的成功率,燃烧室部件生产周期得到显著缩短,提升了研发设计效率。在研究过程中形成了一定的技术积累,为后续的研究奠定了基础。另外,在研究过程中发现,增材制造技术并不适用于所有类型的零件。包含大量实体部分的零件,在基于SLM 技术成型过程中,由于烧结横截面过大,导致热量积累,散热困难,会引起零件成型过程中变形翘曲,导致成型失败。此类问题有待于进一步解决。燃气轮机设计制造领域是设计密集型产业,无论是前期的设计过程,还是后期的维修保养过程,都涉及到复杂结构非标准零件的快速成型。未来增材制造技术与燃气轮机设计的相互融合有助于两者的协同发展。结合全球主要的燃气轮机制造商(美国GE、德国西门子、日本三菱)对增材制造技术在燃气轮机燃烧室部件研发生产中的应用情况,预计增材制造技术在燃气轮机燃烧室的未来应用研究重点包括:1)燃气轮机热端部件的维修、备件按需打印;2)增材制造思想与燃烧室部件设计思想的深度融合;3)探索更多新型高温合金材料的增材制造应用;4)更大尺寸燃烧室部件的快速、高效成型。