金属增材制造(metal additive manufacturing, MAM)技术是一种基于计算机三维数字模型,通过黏结、熔化等方式将材料逐层堆积形成复杂形状零部件的一体化制造技术。金属增材制造技术相比传统制造技术的优势在于其降低了对模具和工装夹具的依赖,缩短了产品的研发周期与制造流程,因此备受关注。根据热源类型,金属增材制造可分为激光增材制造、电子束增材制造以及电弧增材制造,而激光增材制造(laser additive manufacturing, LAM)又进一步分为激光选区熔化技术(selective laser melting, SLM)和激光熔化沉积技术(laser melting deposition, LMD),如图1(a)和图1(b)所示。高温合金因具有优异的高温强度、抗疲劳、抗氧化以及耐腐蚀性能,在航空航天、武器装备、能源、石油化工等领域被广泛使用,采用激光增材制造技术制备航空发动机叶片、涡轮盘、燃烧室等核心部件,有助于创新结构设计、缩短产品研发周期、提高零部件服役性能。
在激光增材制造过程中,金属粉末会经历熔化、凝固、汽化、固态相变等一系列复杂的强非平衡物态变化过程,并且高温度梯度、高冷却速率以及循环加热—冷却效应,极易导致打印件内部产生大的残余应力、裂纹、孔洞等工艺缺陷,显著增加零部件在服役过程中疲劳失效破坏的风险。当前,仅能够保证IN718、IN625等极少数可焊性优异的合金激光增材制造过程中不发生开裂,而CM247LC、IN939、IN738LC等可焊性较差的合金在制造过程中极易发生开裂,如图1(c)所示。然而,可焊性较差合金体系的开裂机理目前尚不完全清楚,关于其裂纹控制策略仍有待进一步研究。
近年来,研究人员围绕激光增材制造高温合金的开裂问题开展了大量研究,裂纹类型可分为凝固裂纹、液化裂纹和固态裂纹三类,但关于其形成机理和控制策略尚未形成统一认识。有鉴于此,本文将对三类裂纹的形貌特征、形成机理及影响因素展开详细论述,并从合金成分优化设计、成形工艺优化设计和后处理工艺优化设计三个方面系统介绍激光增材制造高温合金抗开裂策略的研究思路和最新进展,最后从材料、工艺和设备的角度对激光增材制造高温合金的当前发展趋势和未来研究方向进行展望,以期为高性能合金部件的增材制造提供理论指导。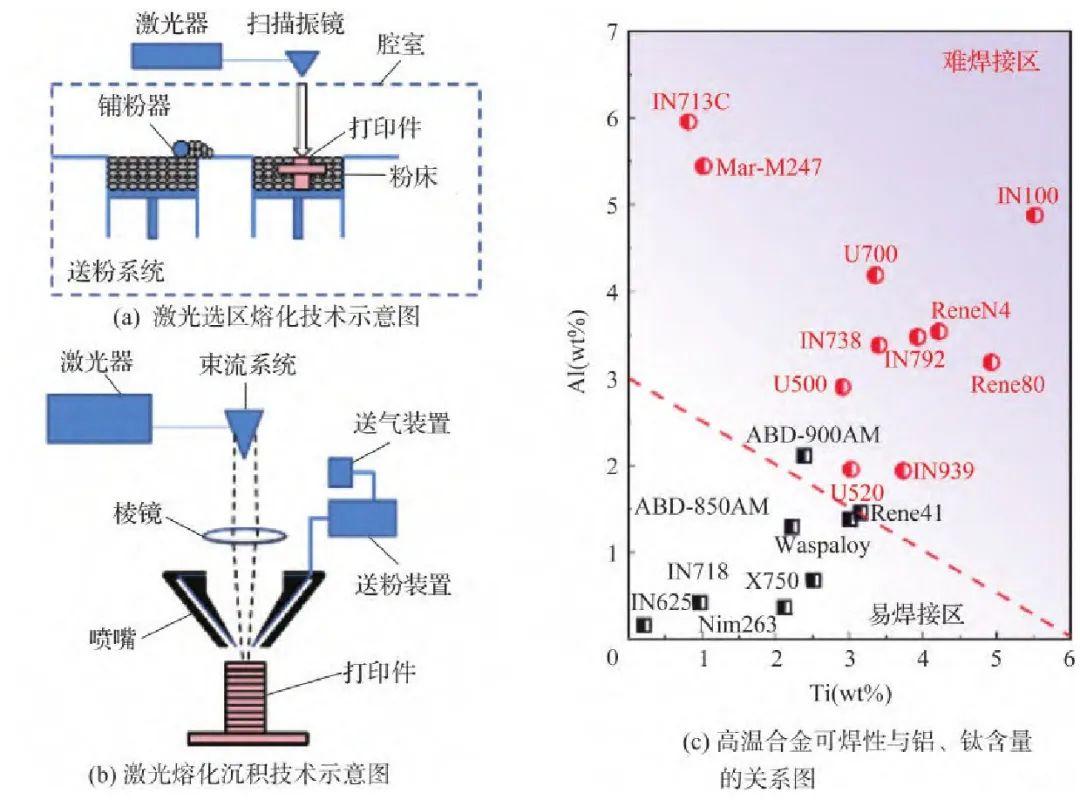
图1 激光增材制造技术示意图及高温合金激光成形能力图
1. 激光增材制造高温合金的裂纹类型及开裂机理
镍基高温合金的开裂现象在传统铸造、焊接等加工工艺中经常出现。造成开裂的原因除了与合金中铝、钛元素含量较高导致可焊性较差相关以外,还与成形工艺类型、参数的选择以及后处理方式密切相关。增材制造过程中伴随强非平衡凝固行为,其高温度梯度、高冷却速率以及循环加热—冷却效应导致合金发生元素偏析、相变以及残余应力累积,厘清这些因素与开裂行为的关系并阐明开裂机理,对于找到有效的裂纹控制策略以解决激光增材制造高温合金开裂问题至关重要。下面从裂纹的形貌特征、形成机理及影响因素三个方面,对液化裂纹、凝固裂纹和固态裂纹三类典型裂纹展开系统介绍。
1.1 液化裂纹
液化裂纹是指合金在凝固过程中经过固液两相区时,晶界位置液相薄膜在残余拉应力作用下发生开裂而形成的沿晶裂纹。液化裂纹多出现在IN738、K465、CM247LC等可焊性较差的镍基高温合金的热影响区,具有明显的沿晶开裂特征。液化裂纹的扩展路径较为曲折,裂纹附近通常伴有严重的元素偏析并形成液相薄膜,如图2(a)至图2(c)所示。由于激光增材制造过程与激光焊接过程较为类似,因此,充分认识激光焊接中液化裂纹形成机理对阐释激光增材制造高温合金中液化裂纹的形成机理具有借鉴意义。Ojo等在研究激光焊接IN738合金液化裂纹时发现,γ΄相的组分液化和γ-γ΄共晶的直接液化是热影响区晶界位置形成液相薄膜的两个主要来源,而残余热应力是形成液化裂纹的主要驱动力。研究指出,在快速加热过程中,晶界处的元素偏析会导致γ΄相无法完全固溶,残余的γ΄相与周围γ基体发生共晶反应,而共晶反应的临界温度相对较低,一旦后续打印过程中的热量累积使局部温度升高至该临界温度,将导致晶界处γ-γ΄共晶发生液化,形成液相薄膜。此时,如果合金内部累积的残余拉应力又恰好超过了液相薄膜开裂所需的临界应力,晶界处就会形成液化裂纹。综上,形成液化裂纹需具备两个条件:一是形成液相薄膜;二是残余拉应力超过液相薄膜开裂所需的临界应力,如图2(d)所示。图2 激光增材制造CM247LC合金液化裂纹的宏观形貌照片及形成机理示意图
影响液化裂纹形成的因素主要包括晶界元素偏析、γ΄相尺寸以及晶界取向差。
(1)晶界元素偏析对液化裂纹形成的影响 对于沉淀强化型镍基高温合金而言,凝固末期组成γ΄相的铝、钛、钽等合金元素容易在枝晶间富集,造成局部热力学行为的改变,从而为枝晶间形成低熔点γ-γ΄共晶提供驱动力。Vitek等研究了铝、钛元素含量对IN625、IN738和Mar-M247合金开裂敏感性的影响。结果表明,IN 625合金因铝、钛元素含量较低,开裂敏感性相对较低,而IN738和Mar-M247合金因铝、钛元素含量较高,开裂敏感性也相对较高。因此,激光增材制造高温合金在成分设计时,应当合理控制铝、钛元素含量,降低开裂敏感性。
高温合金中添加微量硼元素是为了在晶界位置形成硼化物,钉扎晶界,提高晶界结合强度。然而,硼元素也会带来副作用。例如,硼元素富集在晶界位置会促进晶界液化,提高开裂敏感性。这是因为硼元素偏析会降低晶界的液化温度,Xu等借助Scheil模型计算了不同硼元素含量对激光增材制造IN738LC合金凝固温度范围的影响,发现硼元素富集在晶界位置会造成合金固相线温度下降,促进晶界处液相薄膜的产生。另外,硼元素偏析会影响液相薄膜的稳定性。硼元素偏析一方面会降低固液界面能,促进液相沿晶界铺展,另一方面会降低残余液相的表面能,使其在较低温度下依然维持液态,即降低了合金的凝固终止温度。凝固终止温度的降低意味着脆性温度区间的扩大,这将导致合金延展性下降并加剧热影响区晶界位置液相薄膜的开裂。
富钼或铬的碳化物能够有效抑制高温下的晶界滑动,起到稳定晶界的作用,使合金获得优异的高温强度。然而,当碳化物长大到亚微米尺度及以上时,碳化物极易在残余拉应力作用下发生断裂成为裂纹源,造成开裂敏感性的升高。综上所述,增材制造高温合金在合金成分设计时,应当兼顾力学性能和开裂敏感性。
(2)γ΄相尺寸对液化裂纹形成的影响 液相薄膜主要产生于γ΄相组分液化和γ-γ΄共晶直接液化两类情况,如图2(d)所示。其中,γ΄相的组分液化在铸造高温合金中较为常见,而γ-γ΄共晶的直接液化在激光增材制造高温合金中更为普遍。研究认为,这种差异性与γ΄相的尺寸密切相关。γ΄相的尺寸决定了γ΄相与基体之间是否满足共格关系,继而影响γ΄相能否发生组分液化。对于铸造IN738LC合金,晶界处γ΄相较为粗大,为1~2μm,其与基体之间不满足共格关系,位错与γ΄相之间的交互作用方式为Orowan机制,即位错绕过γ΄相颗粒并在相界面处留下位错环。随着位错的累积,相界面因应力集中而发生开裂。而激光增材制造IN738LC合金在高温度梯度、高冷却速率作用下,内部γ΄相尺寸较细小,γ΄相与基体之间通常满足共格或半共格关系,γ΄相的固溶由界面控制,使得组分液化行为被抑制。然而,激光增材制造在打印过程中会不断产生热量的累积,一旦局部温度超过了γ-γ΄共晶反应温度,晶界处同样会形成液相薄膜,并在残余拉应力的作用下发展成裂纹。综上,尽管激光增材制造过程中γ΄相的组分液化能够被抑制,但仍可能发生γ-γ΄共晶的直接液化,引起液相薄膜的产生与开裂。如何有效抑制γ-γ΄共晶的直接液化是解决激光增材制造高温合金液化开裂问题的关键。
(3)晶界取向差对液化裂纹形成的影响 Zhou等借助电子背散射衍射技术统计分析了激光增材制造高温合金中开裂晶界和未开裂晶界的取向差角,发现取向差角为30°~60°的晶界形成裂纹的概率为91.7%,而取向差角为15°~25°的晶界形成裂纹的概率仅为20%,表明合金开裂倾向性随晶界取向差的增大而升高。类似机制也可用于解释激光增材制造CM247LC合金的液化开裂行为。尽管在激光增材制造CM247LC合金的晶界和枝晶界位置均存在γ-γ΄共晶组织,但是液化开裂行为却集中发生于晶界位置。这是因为晶界两侧取向差角较大(>15°),而枝晶界两侧无取向差角或者取向差角很小(2°~5°)。晶界取向差角越大,相邻晶粒之间凝固收缩程度差异也就越大,加剧了液相薄膜的开裂。
综上,抑制液化裂纹的思路包括抑制晶界元素偏析和低熔点共晶相析出、降低大角晶界体积分数以及减小残余应力。
1.2 凝固裂纹
凝固裂纹是指合金在凝固过程中经过固液两相区时,因凝固末期枝晶间液相补缩不足而形成的沿枝晶开裂的裂纹。凝固裂纹的裂纹面之间存在较大缝隙,可以观察到明显的胞状或树枝状形貌,如图3(a)和图3(b)所示。从图3(c)凝固裂纹形成机理示意图中可以看出,凝固裂纹主要发生在糊状区(该区域内材料处于固液两相共存状态)。激光增材制造过程中的高温度梯度和高冷却速率,使得凝固过程倾向于以胞状晶或树枝晶方式生长,进而形成很长的液相通道。随着温度降低,通道中的液相凝固收缩,而枝晶间的高熔点碳化物及大的枝晶会阻碍液相流动,导致枝晶间通道内液相补缩不足,引发凝固裂纹的形成。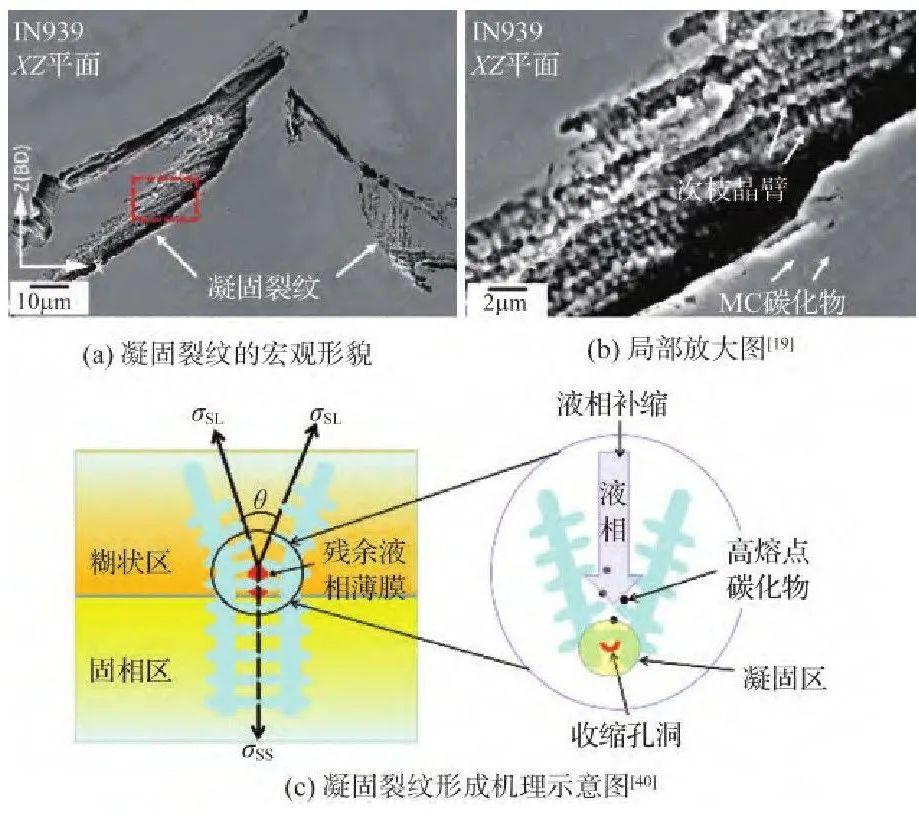
图3 激光增材制造IN939合金凝固裂纹的宏观形貌照片及形成机理示意图
Zhou等借助电子探针显微分析技术考察了激光增材制造高温合金凝固裂纹附近的元素分布,发现铝、钛、钽、铪、钨、碳、硅、氧等元素在裂纹附近均存在不同程度的偏析,据此可以判定凝固裂纹的形成与枝晶界处的元素偏析相关。进一步研究表明,凝固裂纹的形成受到凝固温度范围和凝固末期元素偏析行为的控制。根据Scheil方程,合金的凝固温度范围越宽,固液两相共存区间就越大,越容易形成凝固裂纹。凝固温度范围与合金化程度相关,想要获得较窄的凝固温度范围,就需要合理控制钨、钼、钴、铬、铼等固溶元素的含量。Kou等提出,合金凝固末期的开裂敏感性差异可以用凝固开裂指数(solidification cracking index,SCI)进行描述。图4给出了几种不同类型高温合金的凝固开裂指数与固相摩尔分数fs之间的关系图。从图4(a)可以看出,当fs>0.8时,所有合金的凝固开裂指数在凝固末期均显著升高,表明合金的开裂敏感性急剧增加。对于凝固温度范围较宽的合金,由于液相补缩不足现象更严重,因此开裂敏感性增加也更快。当0.9<fs<0.99< span="">时,不同合金之间的凝固开裂指数差异显著。对于凝固温度范围相当的两类合金,IN718合金的凝固开裂指数较小(921),对应的成形性也更好;而IN738LC合金的凝固开裂指数较大(6681),对应的成形性则相对较差,如图4(b)所示。此外,还可以用凝固开裂指数来描述微量元素铪和锆对合金开裂敏感性的影响。添加铪和锆元素的IN939和CM247LC合金相较于不添加铪和锆的同类合金,凝固末期(0.9<fs<0.99< span="">)的凝固开裂指数较大,这是因为添加铪和锆元素会降低合金固相线温度,扩大凝固温度范围,提高开裂敏感性。然而,去除铪和锆元素又会抑制晶界强化相的析出,造成合金高温强度的下降。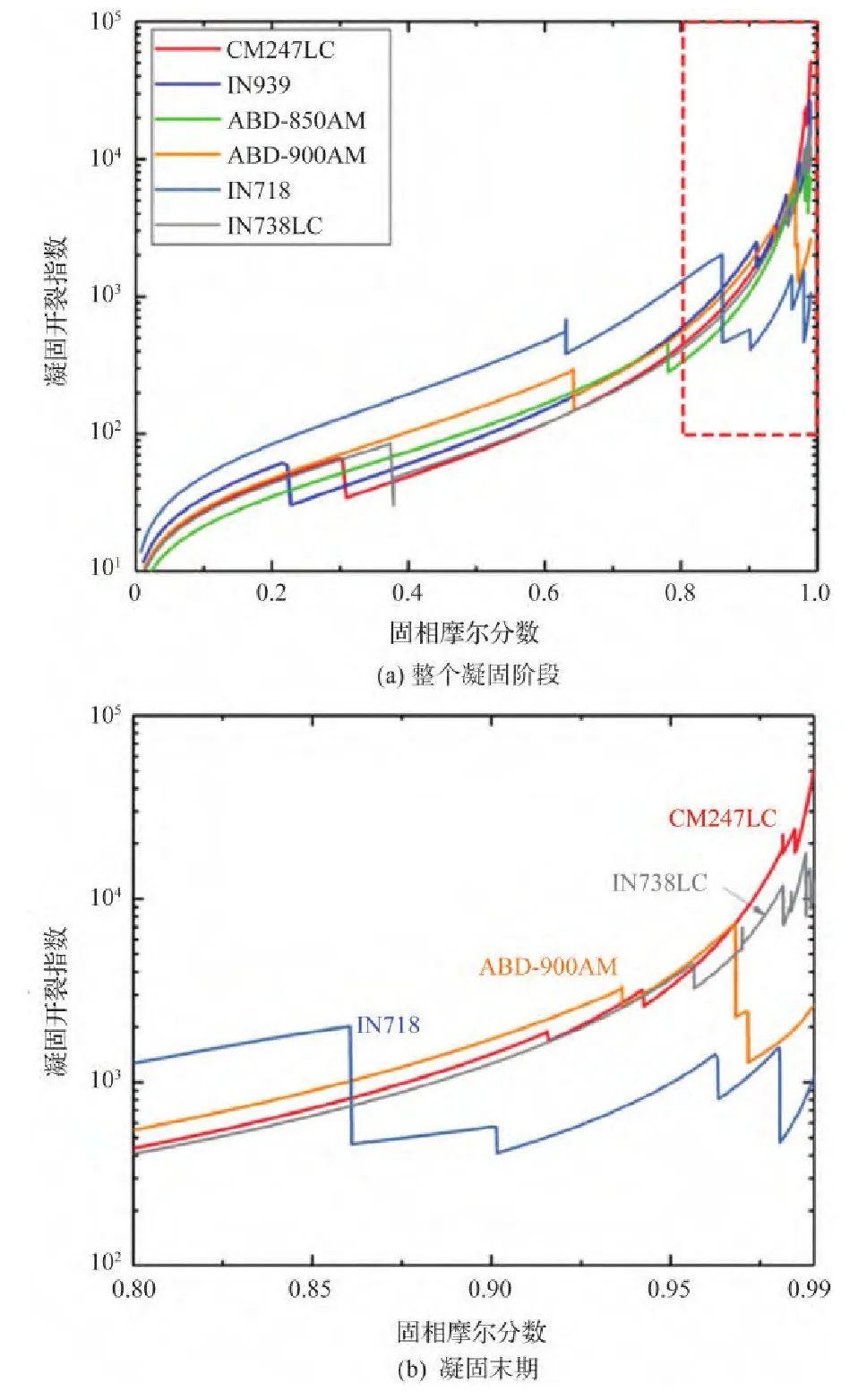
图4 不同类型高温合金的凝固开裂指数与固相摩尔分数之间的关系图
综上,凝固温度范围和凝固末期元素偏析行为均与合金化程度密切相关,且对合金的成形性至关重要。因此,可以根据激光增材制造的工艺特点,重新设计合金成分,包括固溶强化元素和微量元素,以缩窄凝固温度范围、降低凝固末期开裂敏感性,同时兼顾合金的高温强度、疲劳可靠性以及蠕变性能。
1.3 固态裂纹
固态裂纹与液化裂纹和凝固裂纹不同,其主要发生在固相阶段,根据成因不同,可进一步划分为应变时效裂纹和高温失塑裂纹。
(1)应变时效裂纹 应变时效裂纹是指后续打印产生的热循环使前序沉积层处于时效温度区间而不断析出γ΄相,造成合金塑性下降而形成的沿晶裂纹。应变时效裂纹的特点是裂纹面比较光洁,裂纹面两侧形状近似,裂纹路径较为曲折,尺寸较大,可达数百微米,且贯穿多个沉积层,如图5(a)和图5(b)所示。应变时效裂纹的形成与激光增材制造过程中的循环加热—冷却效应密切相关,特别是对于合金化程度较高的镍基高温合金,其在增材制造过程中应变时效开裂敏感性相对更高,更容易形成裂纹,如图5(c)所示。为了降低合金的应变时效开裂敏感性,在进行合金成分设计时,应当合理控制材料的合金化程度。例如,在提高钛、铌、钽等元素含量时,应适当降低铝元素的含量。 图5 激光增材制造CM247LC合金中应变时效裂纹的宏观形貌照片及开裂敏感性关系图
(2)高温失塑裂纹 高温失塑裂纹是指后序打印产生的热循环使前序沉积层经历一段高温区间(为0.5~0.7倍的熔点),该区间内晶界塑性显著下降,晶界在残余应力和相变应力共同作用下发生滑动而形成的沿晶裂纹。高温失塑裂纹在CM247LC和IN738LC等高温合金中较为常见,主要位于三叉晶界位置或者液化裂纹的底部,裂纹尖端呈现楔形,裂纹附近分布有大量纳米氧化物颗粒,如图6所示。 图6 激光增材制造IN738合金中高温失塑裂纹的宏观形貌照片和形成机理示意图
高温失塑裂纹形成因素包括合金成分、晶粒大小、晶界偏析、晶界相析出、晶粒取向、晶界形貌以及环境中氧含量等。目前对于高温失塑裂纹的形成机理尚未达成共识。Zhang等重点研究了晶界形貌和环境中氧含量对高温失塑裂纹的影响。在中温区间,长直形貌的晶界极易发生晶界滑动,导致应变在晶界附近产生累积,一旦累积的应变超过了晶界协调变形的极限,晶界就会发生开裂;相反,曲折形貌的晶界可以通过互锁抑制晶界滑动,借助应力松弛或孪生释放应变,从而使晶粒间变形更加均匀,抑制裂纹的形成。环境中氧含量主要是通过晶界氧化来影响高温失塑裂纹的扩展,主要有两个代表性理论:一是动态致脆理论,该理论认为,氧元素在裂纹前端通过短程扩散形式,不断降低裂纹尖端前缘的晶界结合强度,加速裂纹向前扩展,且该过程是动态进行的;二是应力诱导晶界氧化理论,该理论强调氧元素在应力作用下发生长程扩散,在裂纹尖端前缘形成氧化物,通过氧化物自身断裂或氧化物与基体界面脱黏的形式促进裂纹向前扩展。上述两类理论所涉及的晶界氧化诱导高温失塑裂纹的扩展行为均是在高温、高裂纹尖端应力以及氧元素侵入共同作用下的结果。
综上,为了抑制液化裂纹,应当抑制元素的晶界偏析行为,减少低熔点γ-γ΄共晶的析出,降低残余应力;为了抑制凝固裂纹,在进行合金成分设计时,应当合理控制合金化程度,确保尽可能窄的凝固温度范围和有限的沿晶颗粒增强相;为了抑制固态裂纹,应当适当降低γ΄相的体积分数,以保证一定程度的高温塑性。
2. 激光增材制造高温合金裂纹控制思路及策略
基于对激光增材制造高温合金开裂机理的认识,研究者们围绕控制γ΄相的体积分数和共晶相析出、提高界面结合强度、缩窄凝固温度范围等思路,相继提出了多种有效策略以抑制高温合金的开裂行为,具体包括合金成分优化设计、成形工艺优化设计和后处理工艺优化三个方面。这些举措为开发高性能激光增材制造高温合金奠定了坚实的理论基础。
2.1 合金成分优化设计
(1)合金成分调控 目前,激光增材制造所使用的高温合金成分多是基于传统制造工艺(如铸造、锻造和焊接)而设计的,没有考虑增材制造技术具有的高温度梯度、高冷却速率以及循环加热—冷却的工艺特点,由此引发出合金成分与工艺之间不匹配的问题,无法最大限度发挥激光增材制造技术的优势;此外,铝、钛元素含量较高的镍基高温合金,可焊性差,在增材制造过程中极易开裂。如何根据增材制造技术工艺特点,调整或设计合金成分以制备出无裂纹的高性能合金部件,是当前研究中的热点问题之一。
Tomus等研究了锰、硅元素含量对激光增材制造Hastelloy X合金开裂行为的影响,发现降低锰、硅元素含量可以降低合金开裂敏感性。Harrison等在此基础上开展了更为深入的研究,以Hastelloy X合金成分为基础,通过适当提高固溶强化元素钼、钨的含量,同时降低铁、硅的含量,使得合金可以同时满足固溶强化和抗开裂的需求。试验结果显示,改性后合金的裂纹密度相较于改性前下降了约65%,且合金高温拉伸强度显著提升。
Tang等从成形和成性双重控制的角度出发,提出了“设计驱动合金开发”(alloys-by-design)的理念,以指导开发专门适用于激光增材制造工艺的新型高温合金。借助高通量集成计算工具,研究人员对γ΄相含量、应变时效开裂指数、凝固温度范围和蠕变寿命之间的非线性复杂关系进行了系统评估,从图7(a)和图7(b)所示的合金应变时效开裂指数与γ΄相含量、蠕变寿命之间的关系图可以看出,提高γ΄相含量虽然可以提升合金的蠕变抗力,但同时也会提高合金的开裂敏感性,即合金的成形与成性之间表现出明显的倒置关系。因此,合金成分设计的关键是如何平衡好增材制造高温合金的开裂敏感性和蠕变性能。图7(c)和图7(d)分别给出了Scheil凝固温度范围与蠕变寿命以及应变时效开裂指数之间关系的计算预测结果。在计算中,研究者分别选择4wt%和280K作为应变时效开裂指数和凝固温度范围的上限,其中280K介于IN738LC和IN718合金的凝固温度之间。经过计算,研究者确定了高性能无裂纹合金的成分设计区间,开发出了具有中等体积分数γ΄强化相(20%~30%)的两类新型镍基高温合金ABD-850AM和ABD-900AM,这两类合金在激光增材制造过程中成形性能良好,均无明显开裂现象,且具有优异的高温强度和抗蠕变性能。ABD-900AM的屈服强度在900℃以下均优于IN939,在700℃以下甚至可以超过CM247LC;此外,由于晶界强化元素碳、硼、铪的添加,ABD-900AM的延伸率在1000℃以下均可保持在15%以上,且蠕变寿命在900℃以下优于IN718。研究进一步给出了高性能无裂纹激光增材制造高温合金的一般性成分优化设计准则,即在最大允许的凝固温度范围和应变时效开裂敏感因子范围内,需保证设计出的合金蠕变强度能够满足服役条件所要求的最低容限。
图7 基于计算得到的新型高温合金设计窗口
(2)粉末表面改性 粉末表面改性的理念最早被用于解决激光增材制造高强铝合金(Al6061和Al7075)的开裂问题。Martin等在铝合金粉末的表面通过机械互混的方法涂覆上一层Zr H2纳米细化剂,发现利用表面改性后的铝合金粉末进行打印,可以有效改善高强铝合金的开裂问题,且强度与同类锻件基本相当。分析认为,涂覆在合金粉末表面的纳米颗粒在凝固过程中可以充当异质形核剂,降低形核势垒,促进晶粒生长方式由柱状晶生长转变为等轴晶生长,从而有效抑制裂纹的形成,如图8所示。澳大利亚莫纳什大学的吴鑫华团队在此学术思想的基础上,又相继开发了适用于SLM成形工艺的新型3系、4系、5系铝合金:Al-Si合金、Al-Mg-ScZr合金(Scalmalloy®)和Al-Mn-Sc合金。 图8 粉末表面改性抑制激光增材制造合金开裂行为的原理示意图
粉末表面改性的策略也被用于解决激光增材制造高温合金的开裂问题,并取得了不错的效果。以Hastelloy X(GH3536)镍基高温合金为例,该合金服役温度为540~1000°C,具有优异的抗氧化和高温力学性能,是航空发动机燃烧室部件的关键材料。但是这类合金在增材制造过程中极易发生开裂,造成合金力学性能的显著下降,裂纹类型多为液化裂纹。根据1.1节的介绍,液化裂纹的形成需要满足两个条件:一是在晶界位置形成液相薄膜,二是累积的残余拉应力超过液相薄膜开裂所需的临界应力。基于对液化裂纹开裂机理的认识,Han等通过机械互混的方法,在Hastelloy X高温合金粉末表面涂覆上TiC纳米颗粒,采用表面改性后的合金粉末进行打印,发现合金的开裂行为被有效抑制,且合金的屈服强度和抗拉强度均显著提升。TiC纳米颗粒的引入尽管不能消除晶界位置的碳化物偏析,但是可以改变晶界位置的残余应力大小和分布。均匀分布于基体中的Ti C纳米颗粒能够促进异质形核,提高小角晶界体积分数,这些小角晶界通常由高密度的位错组成,所产生的压应力能够部分抵消残余拉应力,使得晶界位置的应力低于碳化物开裂或液相薄膜开裂所需的临界应力,有效抑制裂纹的形成,改善合金的力学性能。研究人员还进一步考察了不同质量分数纳米颗粒对于Hastelloy X高温合金开裂行为和拉伸性能的影响。发现表面改性后的合金粉末在打印时,开裂行为均能被有效抑制,但当TiC质量分数由1wt%增加到3wt%时,TiC纳米颗粒出现了明显的团聚现象,使得合金孔隙率和缺陷尺寸明显增加,导致合金延伸率显著降低。此外,研究人员还考察了其他类型纳米增强相颗粒对Hastelloy X高温合金开裂行为和拉伸性能的影响。Cheng等利用原位化学方法在Hastelloy X表面涂覆上1wt%Y2O3纳米颗粒,该方法获得的表面改性金属粉末保留了原粉末的圆整度和光洁度,Y2O3纳米颗粒能够在金属粉末表面均匀分散而无明显团聚。利用改性后的金属粉末打印获得的合金样品,开裂行为被有效抑制且组织结构相较于未改性的合金样品更加均匀。拉伸结果显示,合金的强塑性能在粉末表面改性后得到同步提升,其中强度的提升主要来自细晶强化效应和Y2O3纳米颗粒产生的颗粒强化效应,塑性的提升主要来源于裂纹被有效抑制。
综上,合理选择纳米颗粒的类型和含量对于高温合金的成形成性至关重要,一方面需要确保纳米颗粒的稳定性并与基体之间满足良好的共格性,另一方面需要确保纳米颗粒能够均匀涂覆在金属粉末表面而不发生团聚。然而,引入纳米陶瓷颗粒不可避免地会改变合金成分,使材料在工业应用前需要被重新认证,这无形中增加了材料的使用成本。此外,引入纳米陶瓷颗粒促进了异质形核,由此导致的晶粒结构细化对于高温蠕变性能是不利的。因此,如何兼顾增材制造高温合金的抗开裂行为、高温力学性能以及使用成本,是粉末表面改性这一策略当下需要解决的主要难题。
(3)晶界偏析工程 与引入纳米异质颗粒进行粉末表面改性的方法不同,原子尺度晶界偏析工程能够在不显著细化晶粒的情况下,有效抑制激光增材制造高温合金的开裂行为。通常认为,晶界偏析会诱导形成有害的金属间化合物,破坏晶界的完整性。但也有观点认为,铸造过程中因晶界偏析形成的某些金属间化合物反而有助于抑制合金的开裂行为。晶界偏析工程的基本思想是通过综合考虑热力学和动力学条件,操控凝固末期枝晶界和晶界位置的元素偏析,以及随后局部位置的受限相变行为,从而改变枝晶界或晶界位置的残余应力分布状态,最终达到抑制开裂的目的。
高强度、无裂纹的激光增材制造Co-Cr-Fe-Ni高熵合金的制备,是晶界偏析工程在解决合金开裂问题上的成功案例。Sun等将0.5at%的铝粉与Co-Cr-Fe-Ni高熵合金粉末进行机械互混后再打印,有效抑制了合金的开裂行为。研究发现,凝固过程中铝的溶解度会随着温度的降低而下降,造成铝元素在枝晶界和晶界发生富集,促进了连续液相薄膜的形成,如图9(a)所示,并且基体的连续收缩还会在枝晶界和晶界处产生大的残余拉应力。随着温度进一步降低,B2相会在枝晶界和晶界位置逐渐析出,如图9(b)所示,随后在热力学驱动力的作用下发生调幅分解,分解成岛状的B2相和富Cr的BCC相,如图9(c)所示。这一过程中调幅分解引发的相变行为会促进摩尔体积的膨胀,而金属间化合物相的非对称分布会引入更多的几何必须位错,这两个方面产生的应力场能够共同抵消部分残余拉应力,改变枝晶界和晶界位置的残余应力分布状态,甚至由拉应力状态转变为压应力状态,如图9(d)所示,从而有效抑制合金的开裂行为。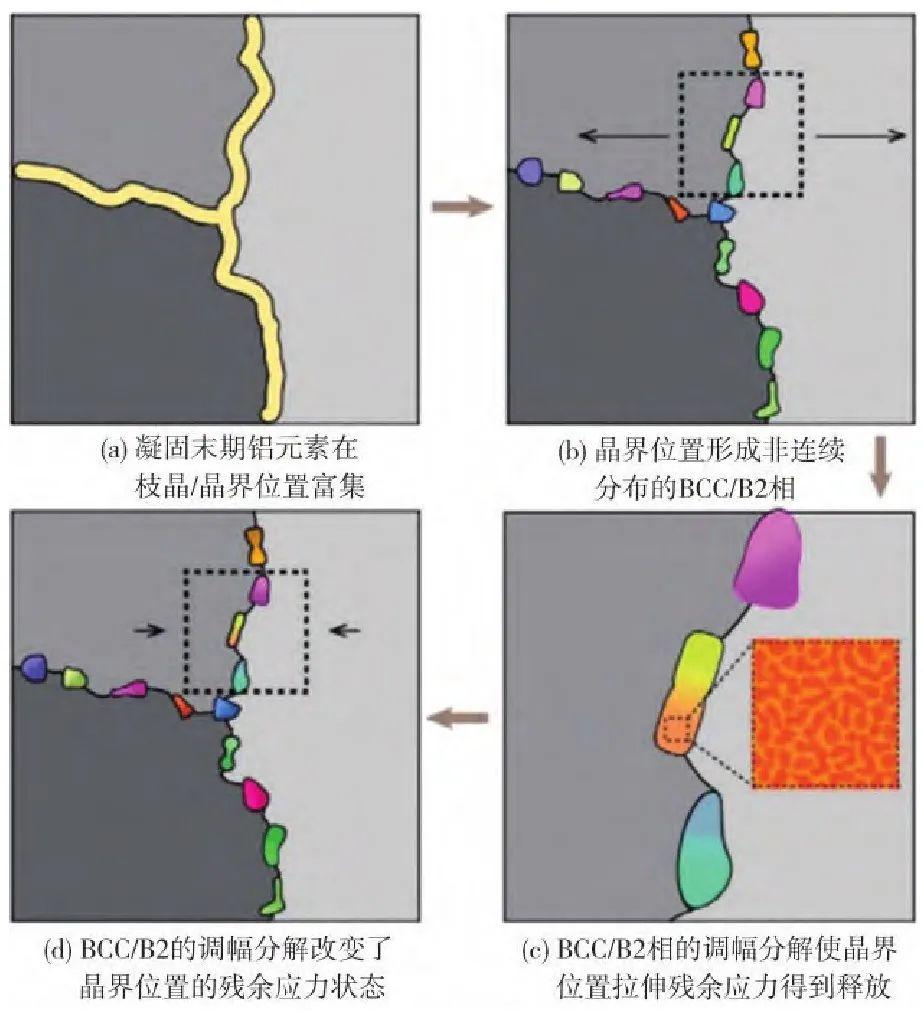
图9 晶界偏析工程解决激光增材制造高熵合金开裂问题的原理示意图
同样地,晶界偏析工程的理念有望被应用于解决激光增材制造高温合金的开裂问题。通过适当调控合金元素,改变枝晶界和晶界位置的元素偏析以及相析出行为,可以对界面位置应力状态进行有效调控,进而获得无裂纹的高性能高温合金。
2.2 成形工艺优化
(1)基板预热 基板预热可以在一定程度上减小激光增材制造过程中熔化区与基材之间的温度梯度,降低残余应力,缓解合金的开裂行为。张洁等通过X射线方法考察了不同预热温度下增材制造IN625合金的开裂行为,发现随着基板预热温度的升高,合金内部残余应力显著下降,裂纹数量随之减少。杨益等在SLM成形Ti Al合金中也观察到了类似现象,合金的裂纹密度在更高的基板预热温度下明显降低。然而,基板预热只能在一定程度上缓解合金的开裂行为,很难从根本上完全消除裂纹。
(2)工艺参数优化 通过调整工艺参数以降低温度梯度和冷却速率,实现凝固模式由柱状晶向等轴晶转变,有望从根本上解决激光增材制造过程中的合金开裂问题。Kontis等研究了晶粒尺寸对合金开裂行为的影响。发现通过调控工艺参数细化晶粒尺寸和提高晶界体积分数,不仅可以使硼、铬、钼等合金元素在枝晶界和晶界位置分布更加均匀,有效抑制元素偏析,保证合金成分浓度低于形成金属间化合物所需的临界浓度;而且可以使残余应力在晶界上分布更加均匀,保证残余应力低于液相薄膜开裂所需的临界应力。进一步统计分析发现,发生开裂的柱状晶尺寸与不发生开裂的等轴晶尺寸之间存在一个临界阈值(100μm),通过调控工艺参数将晶粒尺寸限制在该阈值以下,可以有效抑制合金的开裂行为。此外,Zhang等研究了晶界曲率对合金开裂行为的影响。发现通过降低激光束能量和调整扫描路径为双向往复扫描,激光增材制造IN738合金的外延生长行为和大尺寸柱状晶可以被有效抑制,晶界随之变得更为曲折,合金开裂倾向性得到显著削弱。
对于如何确定合适的工艺参数以获得理想的组织结构,进而有效抑制合金开裂,研究者之间存在不同观点。以激光增材制造IN738LC合金工艺参数优化为例,Montazeri等认为降低能量输入可以减小残余拉应力,有效抑制液化裂纹的形成。而Idowu等认为降低能量输入不仅会形成更多更厚的液相薄膜,而且会提高残余应力,增加合金的开裂倾向性。上述分歧表明,为了建立更为普适性的工艺参数优化准则,激光增材制造合金成分—工艺参数—组织结构之间的内在关系仍有待深入研究。需要强调的是,单纯通过调控工艺参数以抑制高温合金开裂行为的效果是非常有限的。根据Ti-6Al-4V和IN718合金的温度梯度—凝固速率图,要想实现凝固方式的转变,必须使温度梯度降低1~2个数量级。因此,工艺参数的优化设计必须与合金成分的优化设计相结合,才可能发挥更大作用。
(3)激光喷丸技术 激光喷丸技术是在传统喷丸技术基础之上发展起来的一种新型表面改性技术。相较于传统喷丸技术,激光喷丸技术具有高应变率、高能量利用率、稳定性好等特征。激光喷丸技术的工作原理是利用高频、高功率、短脉冲的激光束与材料之间发生交互作用,材料表面在激光辐照下迅速汽化、电离,形成等离子体,等离子体持续吸收能量使得其体积急剧膨胀,产生指向材料内部的强冲击波,由于冲击波的峰值应力通常会高于材料的屈服强度,所以会引起材料表层及亚表层显微组织和应力状态的改变,实现材料表面改性。
激光喷丸技术的最初目标是改善材料的耐磨损、耐腐蚀和抗疲劳性能,以提高工程构件的服役寿命。近期,研究人员将激光喷丸技术与激光增材制造技术相结合,发展了一种新的增材制造—激光喷丸复合制造技术,即在激光增材制造的过程中,每打印数层后进行一次激光喷丸处理,然后再继续打印,如此往复,如图10(a)和图10(b)所示。研究人员发现,运用该技术制备CM247LC镍基高温合金,合金的裂纹密度相较未经处理的同类合金下降了约95%。图10(c)给出了激光喷丸处理抑制开裂的原理示意图。从图中可以看出,激光喷丸处理能够抑制开裂归因于处理后合金表层应力状态由残余拉应力状态转变为残余压应力状态。值得注意的是,激光喷丸处理过程中激光功率以及间隔打印层数的选择与其产生的裂纹闭合效果密切相关。当激光功率较低或者间隔层数较多时,所产生的热量累积和残余热应力将不足以抵消残余拉应力,造成远离激光喷丸处理的位置依然形成大量裂纹;此外,激光喷丸处理会改变局部显微组织,形成周期性变化的组织结构,这可能会对合金的力学性能和腐蚀性能产生重要影响,该方面仍有待深入研究。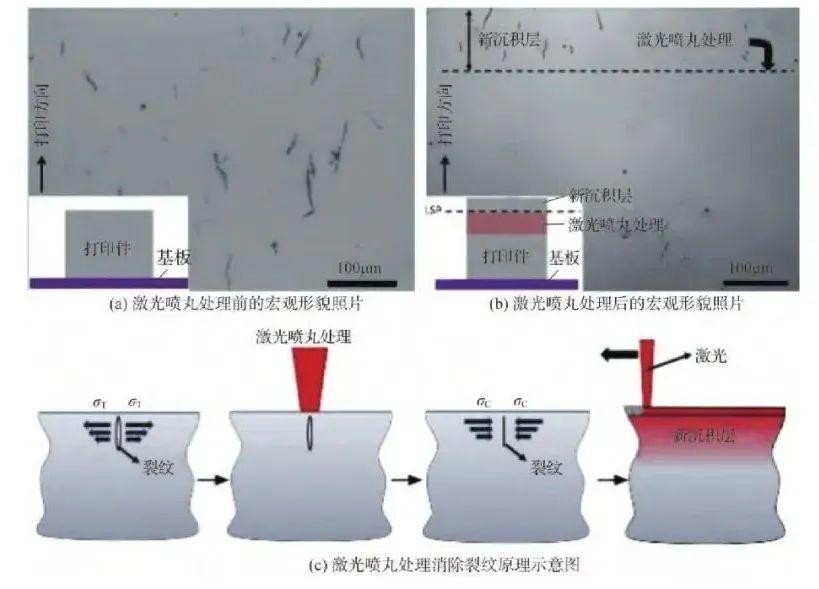
图10 激光喷丸处理前后激光增材制造CM247LC合金的宏观形貌照片及激光喷丸处理原理图
(4)施加外场 激光增材制造过程中施加磁场或超声等外场,可以有效抑制镍基高温合金的开裂行为。以超声为例,熔池液相在高频超声振动下会产生大量气穴,这些气穴会在短时间内快速形核、长大、破裂,产生高强度的超声波,这些声空穴在金属凝固过程中会不断搅动熔池,从而产生更多的异质形核点,促进合金凝固方式由柱状晶生长转变为等轴晶生长。根据1.2节关于凝固裂纹形成机理的介绍,凝固裂纹的形成主要是由大的枝晶和枝晶间分布的高熔点碳化物阻碍液相补缩所致。因此,通过施加外场促进合金凝固方式由柱状晶转变为等轴晶,将有助于抑制凝固裂纹的形成。Todaro等系统研究了施加超声对激光增材制造316L不锈钢和IN625合金组织结构和力学性能的影响规律。经超声处理后,合金的晶粒结构由粗大的柱状晶转变为了细小均匀的等轴晶,开裂行为得到有效抑制,合金的织构效应也被明显削弱。拉伸测试结果显示,相较于没有施加超声处理的同类合金,其强度提升了约12%,且力学性能的各向异性基本消除。这项技术的一大优势是,可以非常方便地实现对特定位置的组织结构和力学性能的调控,如图11所示。
图11 激光增材制造过程中施加超声的原理示意图和效果图
综上,在激光增材制造过程中施加外场是解决高温合金开裂问题的有效手段之一。该方法可以产生以下效果:一是在糊状区施加外场可以促进枝晶破碎,产生更多异质形核点,促进柱状晶凝固方式向等轴晶凝固方式转变,实现晶粒细化;二是利用电磁搅拌或超声振动可以使液相充分搅动,元素分布更加均匀,从而削弱元素偏析效应;三是通过施加外场,可以改变熔池内部的温度场分布,降低残余应力,使应力分布更加均匀。目前,该方法在实际应用中仍然面临许多挑战。如果在SLM成形过程中施加超声,超声振动可能会破坏粉末床的稳定性,引入更多的工艺缺陷。因此,该方法目前主要适用于激光熔化沉积技术。此外,Todaro等在研究中所采用的发声装置为压电式转换器。这种转换器的弊端在于其超声强度会随着打印高度的增加发生周期性衰减,无法打印形状复杂的大尺寸结构部件。可能的解决办法是改用磁致伸缩换能器,通过调节换能器频率自动调谐到可变谐振状态。
2.3 后处理工艺优化
热等静压处理是消除微孔洞和微裂纹最常用的后处理工艺,它的工作原理是借助高温高压使裂纹面压合或者高温固溶扩散实现微裂纹和微孔洞的修复愈合。Han等研究了热等静压处理对SLM成形Hastelloy X合金开裂行为和力学性能的影响。研究发现,经过热等静压处理后(1155℃,100MPa,3h),打印态合金中的裂纹和微孔洞基本消除,然而合金内部发生了明显的再结晶晶粒长大,这导致了合金屈服强度显著下降(约130MPa),但合金部件的高周疲劳寿命因裂纹的消除和残余应力的释放而得到有效改善。
除了会引起晶粒结构粗化以外,热等静压处理对于消除裂纹长度在6μm以上的大尺寸固态裂纹、表面裂纹以及开孔缺陷无能为力。此外,热等静压处理还增加了制造成本,且难以用于复杂形状的增材制造合金部件。因此,从成本、结构粗化、裂纹尺寸、结构件复杂程度等多个角度考虑,采用热等静压工艺消除激光增材制造高温合金开裂行为的策略存在较大局限性。
3. 结论及展望
目前,研究人员在新型激光增材制造高温合金抗开裂问题上已经取得了一些进展,但大部分高温合金的开裂问题仍未得到有效解决,且缺乏普适性的抗开裂策略。从源头上抑制裂纹的形成,是当下解决激光增材制造高温合金开裂问题的重要努力方向。
首先,需要从宏微观尺度厘清高温合金体系中不同类型裂纹的开裂机理,包括熔池、晶粒、胞结构、析出相、元素偏析以及残余应力对开裂行为的影响规律,指导工艺参数的优化设计,进而确定最佳的工艺参数窗口。其次,需要改进现有激光增材制造设备,采用高温预热、微铸锻、激光喷丸处理或施加磁场、超声场等物理场,改善打印过程中残余应力的大小与分布状态,抑制有害元素偏析以及有害相生成,消除裂纹形成的不利条件。基于对合金成分—工艺参数—开裂敏感性—力学性能之间关系的深入认识,开发适用于增材制造工艺特性的新合金体系,从根本上解决高温合金在激光增材制造过程中的开裂问题。最后,传统基于试错法获得最佳成分与工艺参数的策略,既费时又费力,迫切需要热力学计算、机器学习以及材料高通量制备等手段的加入,以建立成分—工艺—缺陷—性能数据库,加速基于增材制造高温度梯度、高冷却速率以及循环加热—冷却效应的新型高温合金的开发,如图12所示。目前已有部分研究人员开展了相关工作,如牛津大学的Tang等通过热力学计算,建立了合金成分—打印性能—力学性能三者之间的关系,通过缩窄凝固温度范围、抑制低熔点共晶相析出、提高合金高温塑性,开发了可分别在850℃和900℃下长期使用的新型高温合金ABD-850AM和ABD-900AM。此外,Murray等也基于前期试验与计算结果,设计了适用于增材制造的新型无裂纹Co-Ni基高温合金,促进了基于增材制造工艺特点的新型高温合金体系的开发。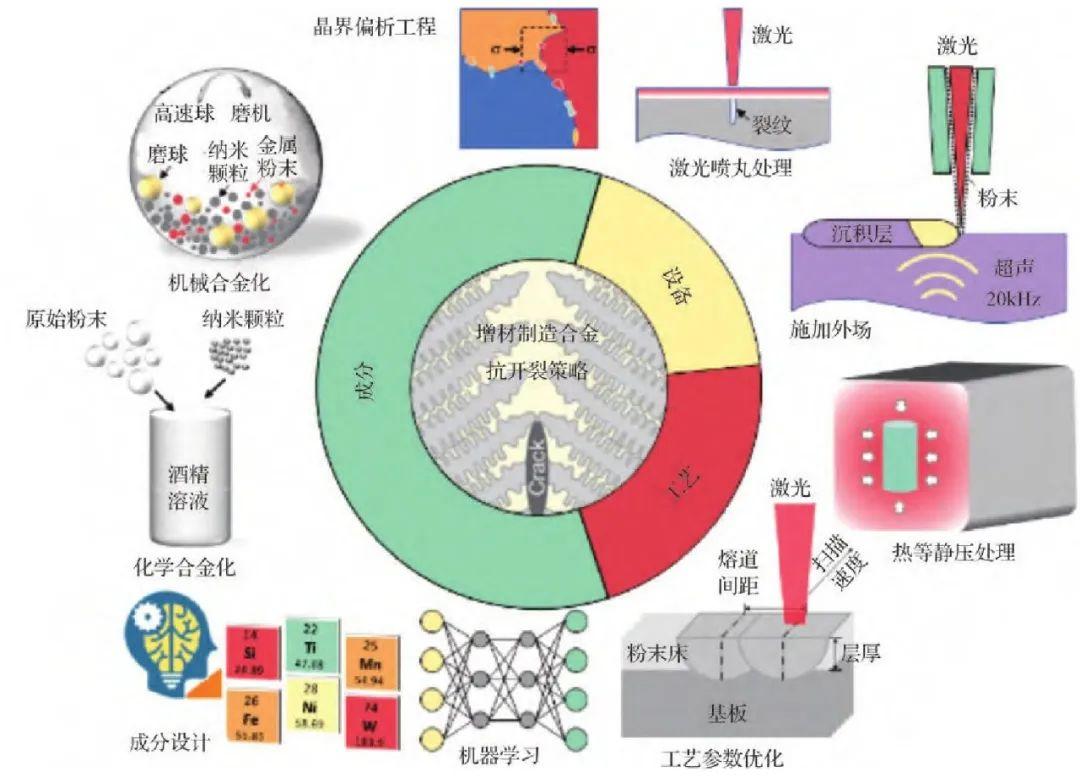
综上所述,在厘清激光增材制造高温合金开裂机理的基础上,通过成分设计、工艺优化与设备改进,开发适用于增材制造的专用高温合金体系,将能够极大地促进增材制造技术在航空航天领域的应用,实现关键核心部件制造技术的突破,推动航空航天制造业转型升级。