氢燃料电池生产工艺!
膜电极(MEA)作为氢燃料电池或系统的核心八大件之一,国产化的MEA对整个燃料电池降本非常重要,当然目前国内已经有一些代表性的厂家建立了自己的半自动或者全自动产线。本文基于外部资料的生产工艺给大家做一些分析和介绍,更便于大家理解。 催化剂浆料配置——催化剂涂布到承载体聚合物膜上——热转印到PEM上——去除承接催化剂的聚合膜——密封边框加工——形成MEA
阳极浆料:重量比约15%的Pt-C催化剂、重量比约40%的去离子水和40%的甲醇类有机溶剂、约5%的聚离体溶液做粘合剂。 阴极浆料:重量比约20%的Pt-C催化剂、重量比约35%的去离子水和35%的甲醇类有机溶剂、约10%的聚离体溶液做粘合剂。
说明:分散设备可以用浆式搅拌机、球式搅拌机、超声波分散机等设备。 3)分散搅拌,浆料混合均匀。(阴阳极的成份差异需要分别配制加工) 将阴阳极催化剂浆料分别涂布到载体(一种离型膜)上并固化
2)设备:浆料喷枪或其他替代设备(如转辊式丝网印刷、喷墨印刷、刮刀涂布等等)、加热传送带、IR/DC在线监测设备。
a.阳极膜厚:3~15µm;阴极膜厚:10~30µm d.干燥温度:加热气流约30~70度;加热辊设定约120~160度
加工好的分别附着在聚合物(膜)表面的阴阳极催化剂、质子交换膜卷料(PEM)。
2)设备:传送带、热压辊、去除废料聚合物膜的转辊。(一种定制设备)。
a.承接催化剂层的聚合物膜的品质(离型效果,催化层能不能正常剥离)。 b.供料速度和辊子压力以及温度的组合。(决定催化层和PEM的接着效果)。 上制程加工好的两面涂有阴阳催化剂的卷料、涂布有接着层的密封边框卷料(材料为PI、PET、PEN等) 2)设备:传送带、转向辊、定制的模切辊、层压辊、真空模切辊(可以是一种定制设备)。
a.各辊轴的同向、同轴平行对齐等。(多层料不能跑偏) 目前一般还有以下两种方式:(还有一种GDE的方式:即将催化剂浆料直接涂布到气体扩散层GDL上,本章先不做讨论) 氢燃料电池气体扩散层GDL的生产、MEA贴合工艺
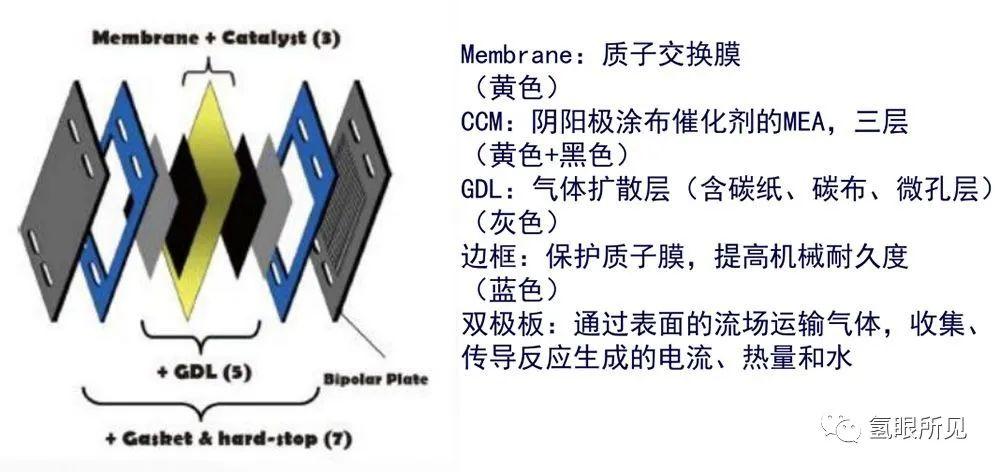
一、GDL生产、与MEA贴合工艺流程总述
- 切碎碳纤维——形成碳纸——碳纸树脂浸渍——石墨化——憎水处理——烧结微孔层——与前制程形成的MEA贴合
- 本GDL工艺从碳纤维开始。碳纤维的制造工艺这里不再描述。
压辊、刀片辊、带有聚合塑料齿的钢辊、碎纤维接料斗。(也可用切断机替代以上设备实现切碎纤维的工艺)
说明:主要是实现碳纤维束切断,可以用其他工艺替代。 工作原理为:图示蓝色聚合塑料齿压住碳纤维,黄色刀片辊图示灰色为切刀切断碳纤维,图示黄色为含有高压气流的聚合塑料齿用来给切割施压和将切断的碎料脱落。 料斗(装碳纤维和粘结剂混合悬浮液)、斜筛网、压辊、加热辊、传送带(如上图设备部件标注)。也可以采用类似无纺布等生产工艺设备替代。 a.悬浮液从料斗均匀分布到筛网上,筛网可以将悬浮物留在网带上,其余溶剂以及水分从网眼向下排出。 c。潮湿碳纸经过多次热辊干燥形成干燥的碳纸同时粘结剂也固化了。 悬浮液的含水量、压延过程间隙和压力的控制、纤维分布状况、粘合剂的均匀分布、碳纸张力等。
碳纸厚度均匀性、材料表面平滑、碳纸湿强度、表面无破坏。 前制程制备好的干燥碳纸、热固性树脂(如酚醛树脂等)
传送辊、压辊、导向辊、隧道式烤炉、浸渍槽等。(可以采用红外干燥以及分切后隔离堆叠的方式去替代)
a.用热固性树脂(例如酚醛树脂)浸渍碳纸,以获得所需的材料强度和孔隙率。此外,经过石墨化处理后,导电性和导热性增加。 c.在150度的隧道式烤炉内挥发残留溶剂并固化树脂。 4.石墨化(为了获得更好的弹性模量和更高的电气以及机械性能、导热性、抗氧化性)
传送辊、烤炉(在氮气或者氩气或者真空状态的环境内,温度约为1400~2000度)。可用惰性或者真空环境的批量碳化设备替代。 a.碳纸在惰性气体环境(氮气、氩气)或在真空中下的熔炉中加热,加热至约1400-2000°C的温度(在间歇过程中超过2000°C)。 b.烤炉内会有不同的温度区,最后在冷却区冷却至常温。 d.工艺时间:自动流水线≤5分钟、间歇式工艺:≤15分钟(以上均在惰性气体或者真空状态下操作)
石墨化过程温度曲线(趋势)管理、去除热解产物的低温石墨化阶段、烤炉的惰性工作环境。
树脂的热解度≥99.5%、产品无死角全覆盖、电导率、碳含量。 前制程石墨化处理后的碳纸、憎水剂(PTFE类、氟乙烯、丙烯(FEP))。
传送辊、隧道烤炉、压辊、导向辊、浸渍槽等。(可以用喷涂、涂布等其他工艺来代替处理) c.GDL中的PTFE可以由悬浮液的比例进行调整。 d.通过烤炉干燥去除剩余溶剂,约在300°C-350°C下烧结将PTFE颗粒结合到基材上。 e.干燥过程的速度影响PTFE在材料中的分布。快速干燥将导致PTFE保留在表面区域,而缓慢干燥能确保整体分布均匀。 6.微孔层MPL烧结(主要作用是反应气体均匀分布和水管理,去除液态水) 前制程憎水处理后的碳纸、MPL材料(由碳或石墨颗粒和聚合物粘合剂(如PTFE)组成,其孔径在100至500 nm之间;碳纸孔径一般在10~30 µm之间)。
传送辊、隧道烤炉、涂布设备、纵向分切刀具、在线摄像监控系统等。(可用的替代设备狭缝涂布、丝网涂布、喷涂等) a.用刮刀将MPL浆料涂布于前制程加工好的材料上,大约厚度<50 µm。 b.采用慢干的方式可以有效改善裂纹,同时增加MPL层的附着力。 c.对干燥后的GDL进行分切,经过CCD进行品质检查,标记缺陷产品,最终采用离型膜分隔包装。 c.烧结过程温度:250~350度(逐渐温升有利于改善干燥效果)
MPL的附着力、干燥温度不能超过其熔点、MPL表面无损平滑。 成品GDL、上章节内容里加工好的MEA、热压粘合剂。
传送辊(带)、导向辊、粘结剂涂布设备、热压辊、刀模辊、纵向切割刀模、交叉切割模。(其他不连续的贴合生产设备、粘合剂涂布设备) a.CCM在两侧连接到GDL,然后分离。形成带保护膜层的MEA。。 b.将粘合剂涂抹在GDL上,根据需要的几何形状对GDL进行冲切孔。 c.冲切好孔位的GDL定位在MEA密封边框的顶部和底部。 f.由于材料的特性导致该加工过程位置精度不是很好管控,需要特别注意公差管理。
b.接触压力:1.000 ~10.000 kgf/cm²。 整个加工系统轴向、径向角度和偏移量的管控,供料速度、热压温度和压力、以及时间的组合管理,主动压力持续时间。
GDL的位置精度、连接强度、切割几何形状的精确度。 氢燃料电池金属双极板(BPP)制作工艺
不锈钢板原材料表面处理(镀层)——流场结构成型——分离切割——焊接——气密性测试——密封垫片加工——成品 不锈钢板原材料(根据自行设计决定厚度)、镀层靶材(这里是指PVD工艺靶材)
传送带、板材清洁设备、真空镀(PVD)设备、X光在线监测设备。 说明:镀层可选替代材料如氮化钛、氮化铬、非晶形碳等;工艺也可以用化学镀(CVD)、渗氮处理、电镀等方式替代。 b.将清洁好的板材送入PVD设备炉腔内。(真空或者惰性气体工作环境) c.采用例如金、钛、铝等靶材,被炉腔内等离子体形成的离子轰击。靶材的原子溶解,移动到基底(此处为原材料)并扩散到其表面形成镀层。 b.真空压力:1x10-1-1x10-7mBar。 模具(流场形状)、液压成型机、传送供料系统。(该制程有热压、拉伸、辊对辊成型、冲压等工艺方式可替代) a.将镀好的板材送入成型机台内,并在模具下方定位。 上下模夹紧力、成型(水)压力、基材拉伸性能、流场的几何形状尺寸、机台的稳定性。
无破损、流场均匀一致、产品一致性、(流场外形)无回弹变形。 传送带、激光切割机(可用冲切、剪切、远程激光等替代工艺)
c.激光是X-Y table可移动式,通过移动实现几何形状的加工。 d.对于有没有做过镀层的材料都可以实现切割(有些厂家将镀层工艺放在后续)
c.进给速度:在壁厚为0.2 mm时,20-300米/分钟(切割) 激光类型、加工精度、切割速度、激光聚焦、产品污染管控。
机器人激光焊接机、工作台。(可用粘结贴合、钎料助焊、添加剂制造等工艺替代) a.两块儿半极板焊接(连接)在一起形成双极板(BPP)。 b.利用聚焦的激光束产生高能量使得金属熔化形成焊接缝。 c.为了避免焊接过程材料氧化,需要在惰性环境下进行。 半极板的定位和拉紧放平、焊缝热影响区的控制、焊点的工艺温度、激光的波长、惰性工作环境的类型。
组件翘曲变形度、焊接点的强度、介质密封焊接、没有粉末痕迹。 前制程焊接好的双极板(BPP)、测试用的气体介质(空气、氮气、氦气等)。
泄漏检测仪(带有端板)。(可用流量测试、超声波检测等其他程序替代) b.利用泄漏测试仪,将加工好的BPP置于真空室内,充满试验介质(如氦等),然后测量其分压。 c.在试验室中试验介质分压升高时,可使用质谱仪检漏仪(MSLD)识别双极板的泄漏。 d.在压降测试中,将空气作为测试介质送入被测对象,并通过系统中的气压下降检测其泄漏。 e.通过泄漏试验的基本条件应由产品需求标准确定。通过泄漏试验后,双极板的生产就完成了。 c.测试灵敏度:3*10-2mBar/秒(空气),2x10-6 mBar/秒(氦气)。 说明:这个工序有很多种加工方式:比如点胶、印刷、模内成型、以及预制件粘结等。当然都需要去材料和工艺对应。 前制程经泄漏测试的BPP、密封胶(有多种可选材料但也需要和加工工艺对应)。
b.印刷机上的刮刀将密封材料挤压到产品需求区域(网版工艺设计决定涂布区域)。 c.网版图像区边缘溢出或渗透(避免污染非密封需要区),所以网版设计的经验很重要,可以通过图形的调整来得到改善。 印刷速度、印刷网版高度(网版与承印物之间距离)、印刷剂量。
密封材料印刷区的位置精度、统一均匀、干膜厚度、材料的固化。 氢燃料电池电堆的(PEMFC)的生产组装工艺
堆叠和预装配——压缩——张紧——泄漏测试——定型装配——活化和测试——成品 准备好的原料、半成品零部件,具体包括MEA(含GDL)模组、BPP、后端板、拉杆(或包扎钢带)、集流板、绝缘板等。
说明:可替代的堆叠方式有人工堆叠、全自动供料堆叠、机械手精准定位堆叠、旋转机械手堆叠方式。 a.开始时先将下端板和集流板、绝缘板放到组装工作台上定位好。(也有将绝缘板和端板做成一体的结构) b.需注意MEA、BPP的产品可追溯性,可以引入Barcode系统等。 c.将MEA、BPP(含密封垫片)、MEA、BPP这样依次循环堆叠,直到达到设计所需求的数量为止。(当然有些厂商有将GDL和密封垫分离于MEA或者BPP,也没关系依次堆叠就好) d.最后,将有介质接口的端板以及集流板、绝缘板堆叠在最上层。
a.燃料电池数量:每千瓦2–10个单电池。目前常见的是每千瓦3~5片。 每个单体电池厚度约1~2mm(和性能相关,仅供参考)、组装定位的精准、无损坏。 带有压板的可控压力的液压机(设备)。可替代的设备有气压计、伺服液压机、螺旋压力机等等。 b.通过施加压力,各个部件(包含密封垫)被压紧,以产生密封的效果。 d.压力的合理调节和管控既保证被充分压紧又避免因过载而损坏。 e.均匀压紧是对电堆功率密度和寿命保证的基本要求。 a.压力:最大160 kN,且施加压力一定要均匀。 压力和路径的精度:最大+/-2%、无尘工作环境、施压移动速度、定位精度
无破损、压力均匀,紧密性、每个单体1~2mm(取决于产品性能)。 c.一般采用金属或者碳纤维的拉力带,并有序均匀分布拉紧固定。 d.拉带的连接处有焊接、连接头、夹具或者异形弯曲结构来固定连接。
e.拉带也可以和端板面上凹槽进行搭配固定,并用螺丝锁住。
拧紧顺序、紧固扭矩、由于变形导致张拉不均匀、端板的厚度。 不受破坏的张力带、电池或端板无断裂或裂纹、均匀的压力分布。 a.采用压降测试或者流量测试来检测电堆的密封性能。 b.将测试介质气体输入到电堆和泄漏测试设备(如图所示)。 c.采用压降法:在关闭介质气体输入后观察压力变化来判断分析泄漏状况 d.流量测试法:打开介质气体输入,观察终端流量变化分析判断泄漏状况。 e.既要确定电堆整体密封性能,也要判断单体泄漏状况。
a.阳极氢气泄漏率:最大1x10-2 Pa m³/秒。 输气管道和进料管线的密封性、部件损坏、张拉不均匀、环境压力和温度、防尘等。 说明:针对整堆的泄漏测试我们国内也有完整严谨的国标。 CVM(数据采集单元)以及触点连接的导电树脂等、正负极电流收集模块、各输入输出接口连接板。 说明:由于电堆有裸堆、模块儿等形态存在,所以以上部件有些是选配
b.CVM采集电压触点一般用导电树脂连接到电梯电池上,也有采用焊接或者夹具等方式。 e.外壳盖也是配电盘,也包含所有介质输入和输出以及传感器和高压电缆等连接。 外壳拆装的便利性、单电池的电压的精确监控和良好的导电性。 电子负载、水泵、散热风扇、离子交换器、空滤、空压机(鼓风机)、加湿系统。 说明:以上设备目前也有一套完整的测试台架可以替代。
b.测试系统需要有符合需求的氢气以及空气供给,还有独立的电子负载。 c.在活化过程可以采用恒流。恒压。变载以及不同湿度下进行有规律切换来进行(之前有篇单独谈电堆活化的文章,有兴趣请去翻阅)。 e.特别说明:某些时候活化后需要再次进行泄漏测试。
a.活化时间大约持续2~4小时,不同的活化方式有较大差异。 d.工作温度:55-75°C(这里一般指低温PEM燃料电池)。 氢气纯度、供应量的保证、温度管理、各连接管路密封、环境温度和压力。
著作权归作者所有,欢迎分享,未经许可,不得转载
首次发布时间:2023-06-21
最近编辑:1年前