什么是电池包CCS集成母排?
电动车动力电池通常由若干个单体电芯串并联组装而成,来实现驱动电动车所需的高电压、大电量,电芯的连接是动力电池成组的关键技术。在传统的电池包中,通常使用busbar(母线)来完成电池组的串并联,同时为了实时采集电芯电压、电芯温度和 busbar 温度,需要在电芯或 busbar 表面布置温度传感器和电压采样线束,如像下图所示。
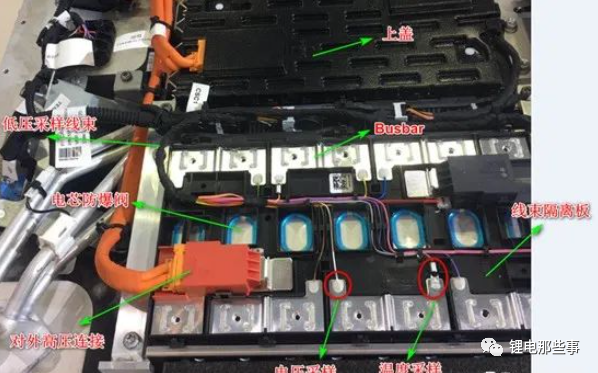
传统线束母排在连接电池包时每一根线束到达一个电极,需要多根线束配合动力电池包中的多个电流信号,挤占较大的电池包空间,且线束在pack装配时依赖人工固定端口,自动化程度低。 因此,随着电池包集成技术的发展,以及自动化组装要求的提高,采用FPC柔性线路板替代电池传统线束的CCS集成母排被广泛使用。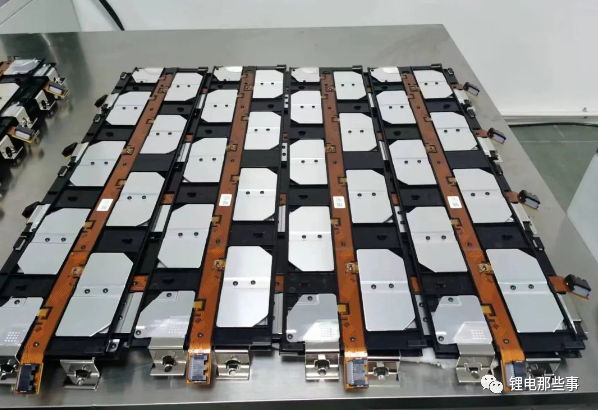
图 采用FPC柔性线路板替代电池传统线束的CCS集成母排一、什么是CCS集成母排
CCS(Cells Contact System,集成母排),主要由信号采集组件(FPC、PCB、FFC等)、塑胶结构件、铜铝排等组成,通过热压合或铆接等工艺连接成一个整体,实现电芯高压串并联,以及电池的温度采样、电芯电压采样功能,通过FPC/PCB和连接器组件提供温度和电压给BMS系统,属于BMS系统的一部分。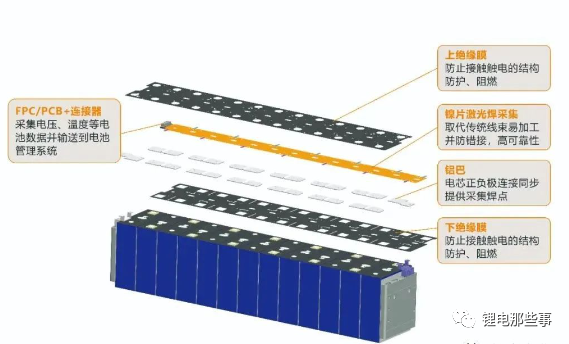
采用FPC等作为信号采集组件的CCS集成母排,具有结构轻薄、集成度高等优点,有利于提升电池包空间利用率及组装效率,符合汽车轻量化、零部件系统集成化及大模组化趋势。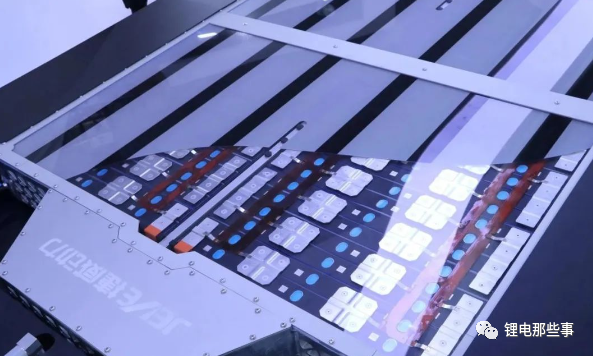
图 上海车展捷威动力“海绵系统”采用CCS集成母排
CCS集成母排采用FPC或PCB等来替代传统的线束连接。与传统线束母排相比,CCS集成母排具有以下优势:
1.一体热压成型,线路密封性好,耐候性好耐潮湿,耐氧化,耐腐蚀等,性能优异,可靠度高;
2. 客户端安装简单,避免了线束过多连接的繁琐,可自动化作业程度高,节约客户装配人工成本;
3.集成度高,体积小,轻薄,节约整体模组空间,使整体模组轻量化,便捷化;
4.共用性强,可制造性强,易于模块化和标准化,节省开发成本;
5.线路有过流保护设计对电池电芯起到保护作用,安全性能高;
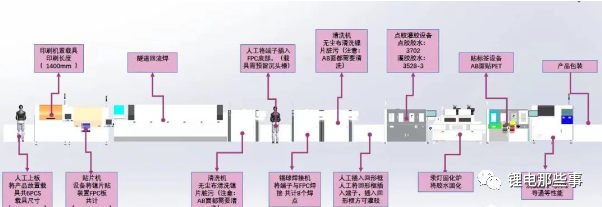
图 新能源汽车动力电池CCS贴片
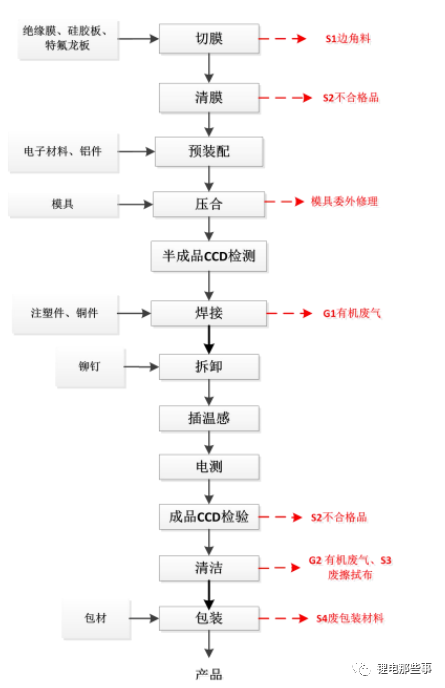
生产工艺流程简述:
切膜:用切膜机对绝缘膜进行切割,制得产品所需要的尺寸,产生边角料S1,同时用切割机将硅胶板、特氟龙板切割成所需要的尺寸。
清膜:切割后的膜片从切膜机中取下来,用眼睛查看膜片是否均匀,清理出不合格膜片。
预装配:硅胶板、特氟龙、绝缘膜片切割完成后,按照要求将特氟龙板、硅胶板、绝缘膜片、电子材料、铝片、铜片等进行分层预组装。
压合:将预组装完成的半成品放入模具,用压机在电加热160ºC下热压,使得绝缘膜、硅胶板等材料紧密粘合。
半成品 CCD(外观和视觉检测设备)检测:主要是对半成品检测异物、划痕、压痕、极耳不良、污染、腐蚀、凹点、极耳烧伤、字符模糊等外观缺陷检测,属于物理检测。
焊接:主要是对金属件和注塑件的焊接,包括激光焊和超声波焊接等,其中金属件加工使用激光焊接,塑料件则采用超声波焊接。
拆卸/插温感:用紧固件铆钉与已焊接压合后的各种外购的铝件、铜件、塑料件、温感设备、进行紧固组装。
成品 CCD 检测:经过上述操作后检测异物、划痕、压痕、极耳不良、污染、腐蚀、凹点、极耳烧伤等外观缺陷检测;
清洁:采用棉布蘸酒精擦拭产品,进行清洁消毒,产生清洁废气G2。
成品检验:产品进行最后检测,均为物理检测。产生不合格品S4,产品经检验合格后包装入库。二、新能源汽车销量攀升,带动FPC/CCS百亿市场
在双碳目标下,全球新能源汽车产业加速发展,新能源汽车销量不断攀升,根据研究机构EVTank发布的数据显示,2022年全球新能源汽车销量达到1082.4万辆,同比增长61.6%。展望未来,EVTank预计全球新能源汽车的销量在2025年和2030年将分别达到2542.2万辆和5212.0万辆,新能源汽车的渗透率价格持续提升并在2030年超过50%。我们根据这一新能源汽车销量预测数据,对 FPC/CCS 的市场空间进行测算:新能源汽车电池模组平均数量:FPC 及 CCS 的单车用量与电池模组设计相关,主流车型以 7-12 个模组的用量居多,我们假设2022年新能源汽车电池模组平均数量约为 9 个,此后由于续航要求的提升,每年电池模组平均数量有所增长。电池模组使用 FPC数量:根据联赢激光微 信 公 众 号数据,单个电池模组对应1个 CCS,1 个 CCS 一般配置 1-2 个 FPC,此处保守假设单个模组使用 1 个 FPC 进行测算。CCS 集 合塑胶结构件、铜铝排等结构件,CCS 单车价值有望达到 FPC的 2-3 倍。FPC 价格:根据奕东电子招股说明书内容,每平方米排版数量分为 15 个以下,15-50 个,50 个以上三类,而每平方米排版越多的 FPC 售价也越高。根据披露数据 2021 年 1-9 月,每平方米 15 个以下的 FPC 单位售价为 878.58 元/平方米,则单个 FPC 售价为 58.57 元以上,假设平均单个 FPC 价格为 60 元,此后每年有所下滑,2022年单个 FPC 价格以55元计算。CCS 单车价值量:根据联赢激光微 信 公 众 号披露,CCS 单车价值量约为 1000-1500 元,保守假设 2022 年为 1100 元,此后随着汽车电池模组平均数量提升+单位售价下滑因素叠加呈现先增后减的态势。最终测算得到 2022年、2025 年FPC与 CCS 的合计市场空间为172.64 亿元和 394.04 亿元,复合增长率约31.7%。
| 2022年 | 2025年 |
新能源汽车销量(万辆) | 1082.4 | 2542.2 |
新能源汽车电池模组平均数量(个) | 9 | 10 |
电池模组使用 FPC 数量(个) | 1 | 1 |
FPC 价格(元/pcs) | 55 | 45 |
单车 FPC 价值量(元) | 495 | 450 |
FPC 市场空间(亿元) | 53.58 | 114.4 |
单车 CCS 价值量(元) | 1100 | 1100 |
CCS 市场空间(亿元) | 119.06 | 279.64 |
三、CCS集成母排产业链相关企业
CCS集成母排产业链包括上游的模切材料、铜铝排、FPC/PCB等和设备厂商,下游的CCS集成母排生产商,以及应用端的动力电池厂商如宁德时代、亿纬锂能、国轩高科、中航新创、捷威动力等,因CCS附加值比单纯的FPC更高,因此也有不少FPC/PCB厂商进一步布局下游集成产品CCS。
©文章来源于锂电产业通