本田飞度混合动力系统i-MMD技术解析
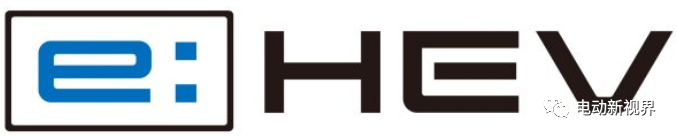
本田 e:HEV的品牌Logo
i-MMD技术路线
本田将电动汽车技术的命名为Honda e Technology,并将e:HEV的名称推出HEV。目的在于渗透HEV的品牌形象。并将2020年上市的新款Fit(在部分海外市场以Jazz的名称推出)开始采用。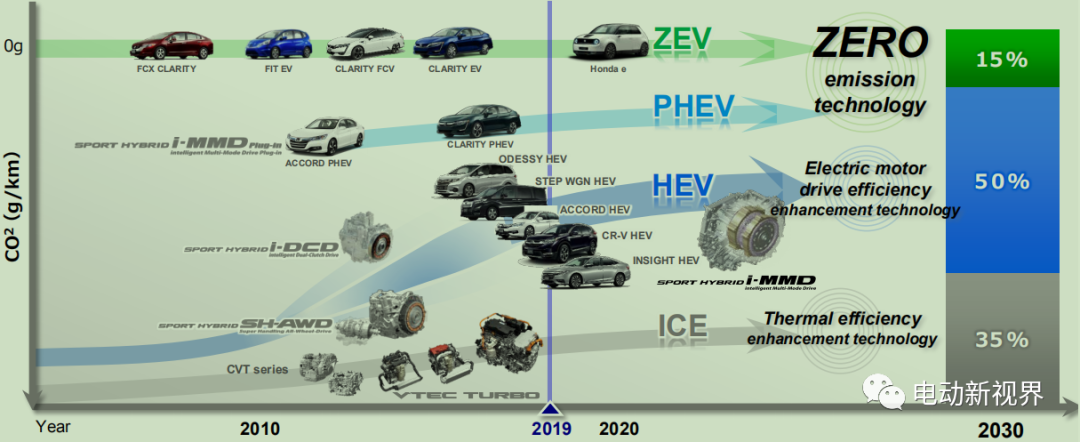
i-MMD技术的路线图
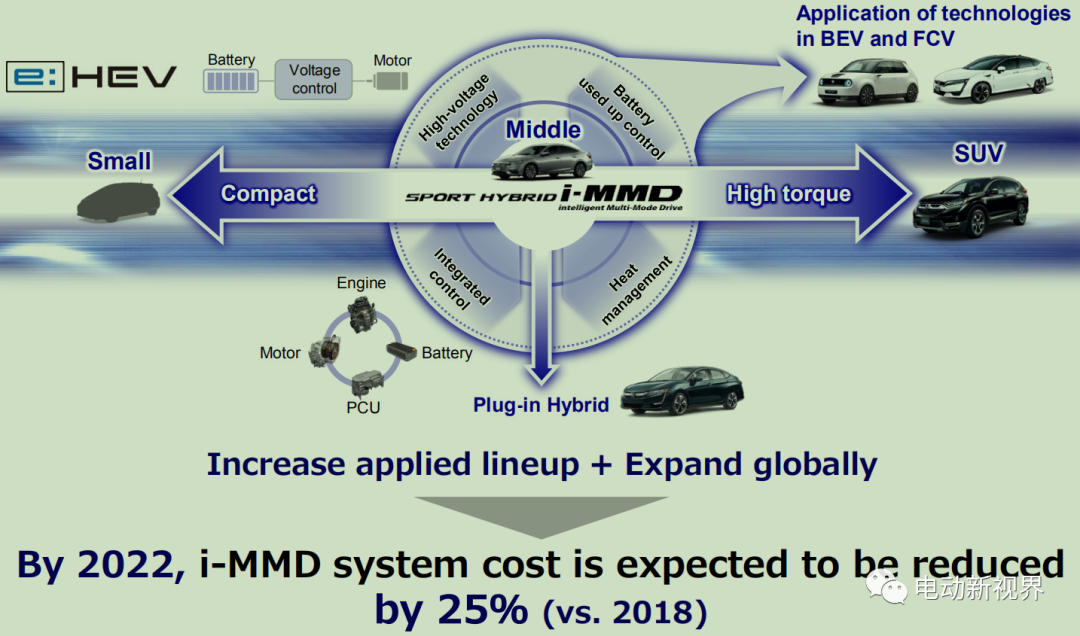
i-MMD技术的路线图
二、第四代Fit HEV车型简述
1.车型介绍
本田2020年2月推出新款FIT。FIT作为本田全球战略紧凑车型,本次为全新改款升级后的第4代车型。新款FIT围绕4个舒适性进行开发(视野舒适性、座椅舒适性、乘坐舒适性、使用舒适性)进行开发。本文仅对动力总成及车型进行介绍。
2.底盘介绍
新款Fit前部采用麦弗逊支柱式悬架,后部采用扭力梁式悬架 -前悬架采用高响应弹簧,通过减少衬套和连杆的摩擦力,可应对路面上细微的不平整; -后悬架采用H型扭力梁。将在车身上的固定点从单固定点变更为铝压铸支架双固定点。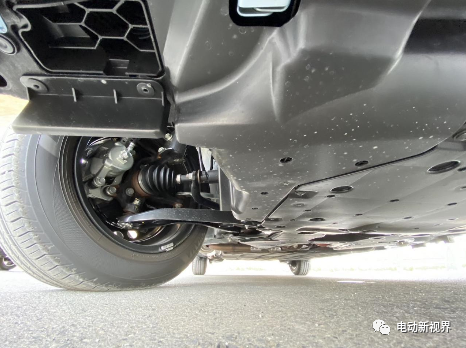
前悬架为麦弗逊独立悬架
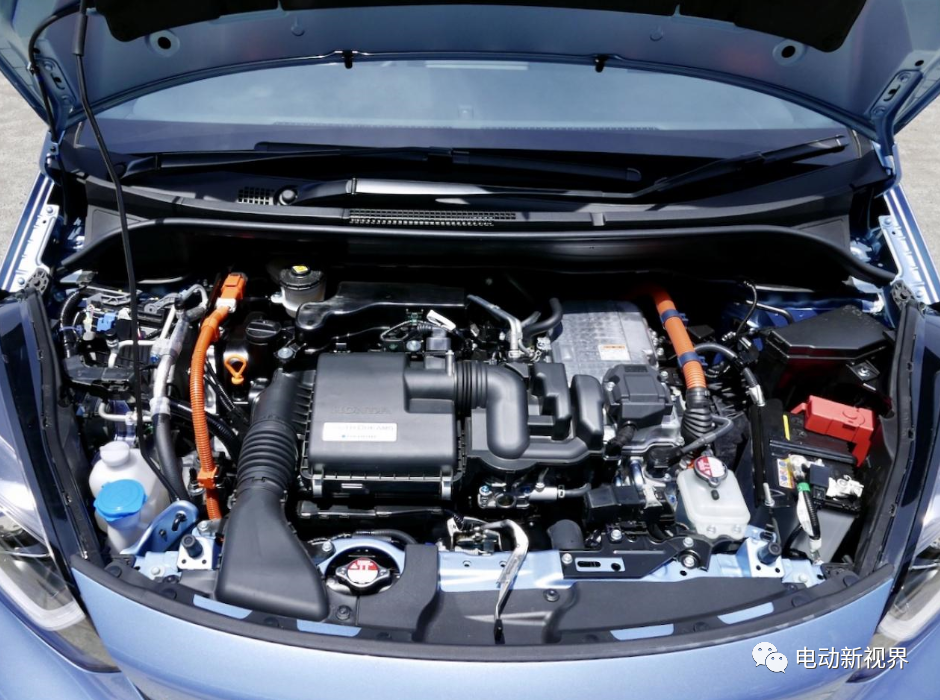
发动机舱
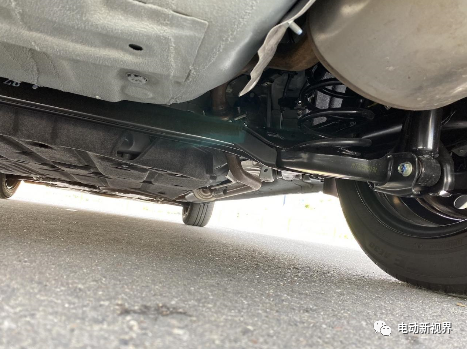
后悬架为扭力梁式非独立悬
Fit HEV四驱系统架构-DPS(Dual Pump System)1.后驱动单元并未采用电动化驱动单元,依然采用传统耦合式驱动系统;可能基于后排空间及成本考虑所致;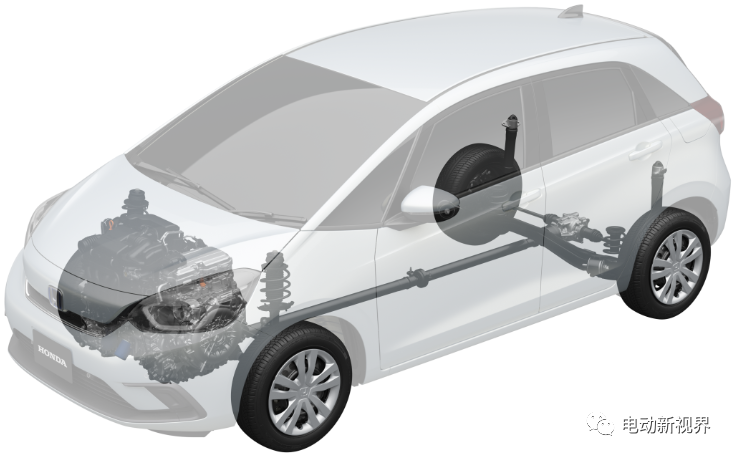
Fit HEV 四驱架构-1
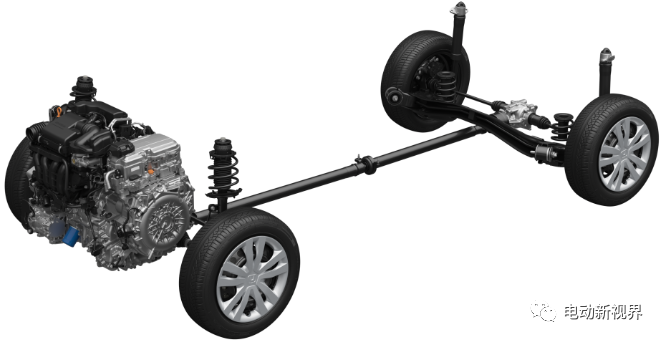
Fit HEV 四驱架构-2
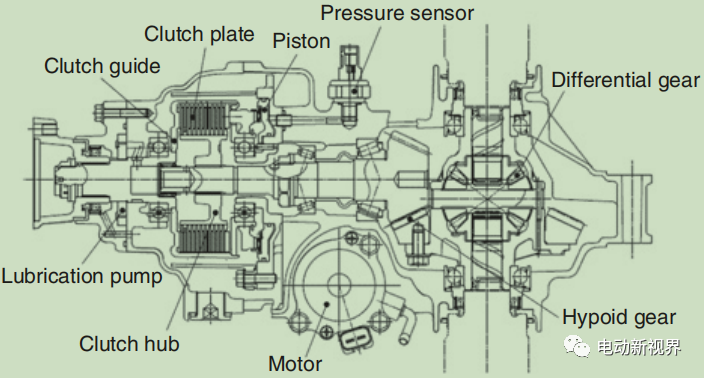
Fit HEV 四驱DPS系统-3
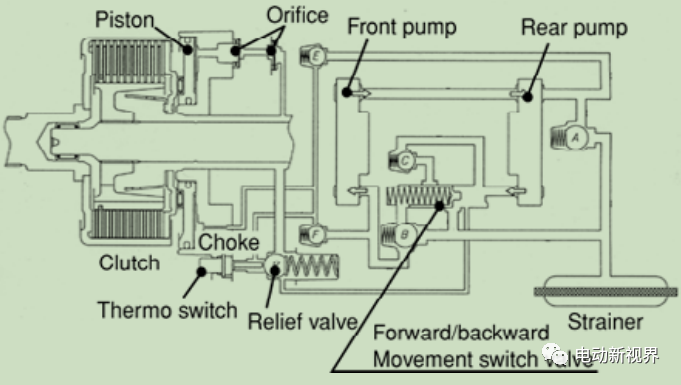
Fit HEV 四驱DPS系统-4
- HOME车型:采用沙发等优质材料以及真皮方向盘,打造出居家般的舒适空间;
- NESS车型:采用独特的内外饰配色以及高防水材料座椅,更加彰显活力;
- LUXE车型:采用真皮座椅,车身关键部位铂金色调镀铬显现出高级感;
- CROSSTAR车型:针对户外运动爱好者采用SUV外观设计以及防水性能座椅。
4.车型参数介绍
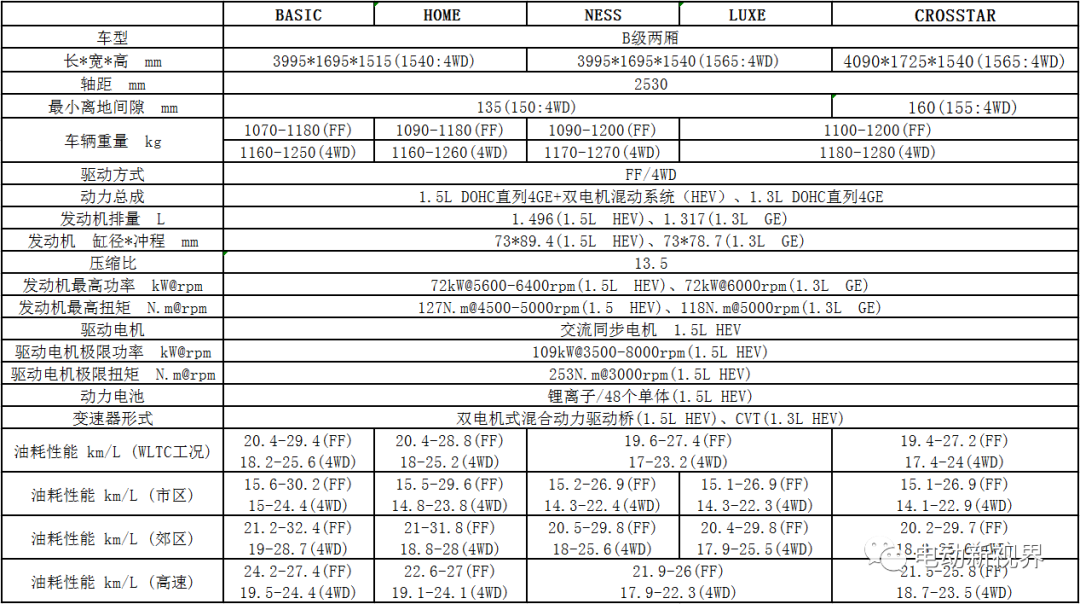
Fit HEV 四驱DPS系统-4
HEV HEV版采用阿特金森循环(米勒循环)1.5L直列4GE组合双电机的串并联混合动力系统。- 上一代系统搭载单电机+7速DCT的并联系统,但新款车型采用大幅降低油耗的双电机式(SH-iMMD);
- i-MMD通过电机驱动低中速区域,在高速行驶一级突然加速时仅通过发动机或电机与发动机混合驱动行驶,在高效区域通过电机与发动机驱动行驶可降低油耗;
- 与以往相比,电机工作区域增加,提高了静音性以及加速性能,可以低油耗向用户提供更舒适的行驶;
- i-MMD此前一直用于C~D细分区间车型,在用于B细分区间车型时对系统进行了小型化*在电机转子中,通过采用磁性粒子微细化后的高性能永磁体和新开发的树脂优化转子内磁路提高了磁通密度。在定子中,通过实现绕组膜的高耐压化,降低开关损耗(减少原来的1/5),电机实现了高扭矩化-高功率化*通过驱动用于发电用的两个电机,使定子宽度(Insight相比)与原来相比缩小12%以上*提高锂离子电池性能(最高功率与原来相比提升62%),实现冷却系统以及ECU的小型化,IPU的容积缩小25%以上。此外,通过减少功率半导体并内置12V DC~DC转换器使PCU的容积也缩小10%以上。

Fit HEV 动力总成-1
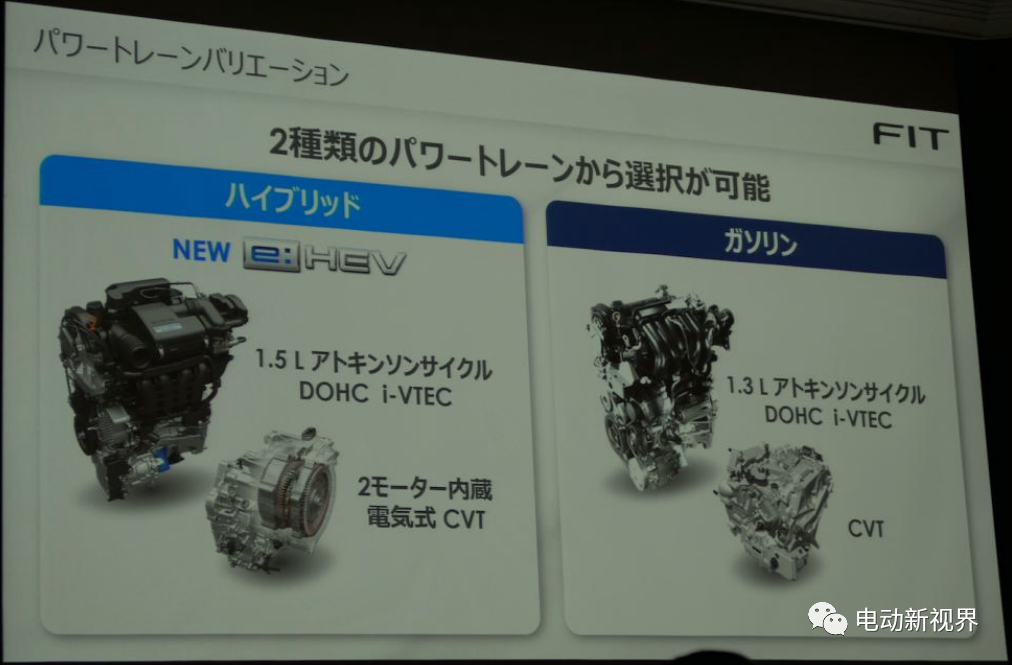
Fit HEV 动力总成-2
- 为了向用户提供低油耗的舒适驾驶,HEV车型的动力总成将单电机+7速DCT并联系统变更为新一代双电机串并联混合动力系统。本田以C到D细分车型为中心,设定追求低油耗的串并联式双电机系统,并扩大搭载车型。
- 利用阿特金森循环(米勒循环)的专用发动机匹配,采用搭载与发动机直接连接的离合器的电子CVT;阿特金森循环发动机减少了泵送损失,从而降低了油耗。
- 发动机与发电用电机联结,对锂离子电池充电。通过离合器向驱动轮传递发动机的动力,通过分离,凭借电机进行驱动;
- 根据离合器与电机控制设定了3种行驶模式。当处于启动以及市区低速巡航时以EV模式;在急加速时,利用发动机(高效率范围运转)发电的同时以电机驱动;高速巡航时联结离合器,利用发动机进行驱动。在各种行驶模式下,充分利用动力总成所擅长的部分,实现最低水平油耗。
- 为了将新系统应用于B细分区间车型,将搭载于C细分区间以上车型的SH i-MMD进行了改良。推进驱动电机以及电池系统、PCU等的大功率*高效率化,从而使整个系统实现了小型化;
- 使用发动机驱动与电机驱动的高效率工作区域,发挥出平稳加速性能。HEV车型的最佳油耗为29.4km/L(WLTC工况)。
燃油车的动力总成采用1.3L直列4缸汽油发动机,匹配CVT。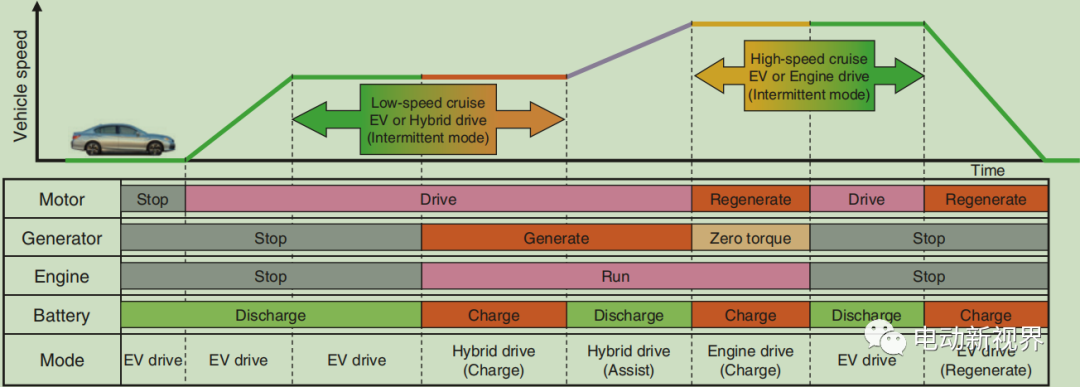
i-MMD工作模式
三、2014款Fit HEV车型简述
1.动力总成介绍
本田的i-DCD混动系统由1.5L阿特金森循环发动机、7速双离合变速箱,以及兼具驱动电机和发电机功能的电机、集成IPU的锂离子电池组和空调压缩机等共同组成。
单电机HEV系统 Sport Hybrid i-DCD(Intelligent Dual Clutch Drive)是将7速DCT与驱动电机组合的并联式系统。7速DCT的奇数挡一侧与驱动电机联结,借助离合器,可实现与发动机的动力分离。奇数挡一侧仅靠电机即可实现EV行驶,偶数挡一侧也可进行电机辅助。除可利用齿轮较高的动力传递效率之外,还可通过DCT降低变速时的扭矩损失,进而实现高效率。与传统单电机系统相比,效率提高30%以上。 在新一代的混动系统开发中,考虑到换挡时间更少的问题,i-DCD混动系统采用DCT变速箱代替了原IMA混动系统的CVT变速箱。 两套混动系统的核心部分是在-7DCT中集成一驱动电机,也就是我们常说的P2.5构型。
混动系统的7DCT都是由双离合器、轴系结构、换挡执行器、离合器执行器,油泵和驱动电机组成。 1.i-DCD混动系统的7DCT采用干式双离合器,以提高传动效率; 2.齿轮的具体 位置和传动比不同,但基本结构相同。 3.换挡执行器、离合器执行器和油泵的布置位置不同。
1.奇数输入轴和偶数输入轴平行布置:奇数离合器同轴连接奇数输入轴,奇数输入轴上依次布置奇数齿轮和同步器;偶数离合器通过惰轮连接异轴的偶数输入轴,偶数输入轴上依次布置偶数齿轮和同步器。 2.中间轴齿轮同时啮合两输入轴档位齿轮:采用一个中间轴,中间轴上的三个齿轮分别同时连接2挡和3挡齿轮,4挡和5挡齿轮,6挡和7挡齿轮,在轴系布置上可有效缩短轴向长度。 3.采用行星排作为1挡齿轮:奇数轴连接太阳轮作为输入,1挡同步器可将齿圈与箱体固定,行星架作为输出与3挡齿轮连,就可以在3挡的传动比的基础上增加一个行星排的减速传动比,从而实现1挡。这里需要思考的是,为什么采用复杂的行星排来代替简单的1挡输入齿轮?笔者尝试做了一个理解:一方面可通用中间轴上1挡和3挡的啮合齿,有效减短中间轴的长度,为后端安装电机让出空间;另一方面加入行星排的传动比,可使奇数输入轴和中间轴的中心距更小,使得结构更加紧凑; 4.设立独立倒档轴:倒档轴并没有借用其他齿轮,而是单独设计倒档轴,轴上有单边同步器和输出齿轮,并设有驻车齿轮,从而优化空间。主减齿轮减速增扭,差速器输出至轮端。
5.驱动电机集成在后端:扁平式油冷的驱动电机集成在7DCT箱体中,同轴布置在变速箱后端,其转子和奇数输入轴连接介入动力,定子固定在箱体上。并将1挡的行星排布置在转子内部,使结构紧凑。 3.液压系统-换挡系统介绍
HCU:离合器的控制采用的是舍弗勒的静液力离合执行器HCA,两个电液执行器分别控制两个离合器的分离和接合;GA:DCT的换挡同样采用舍弗勒的换挡执行器GA,两组电机分别控制选档和换挡动作。共计八个拨头分别控制7个前进挡和一个倒档。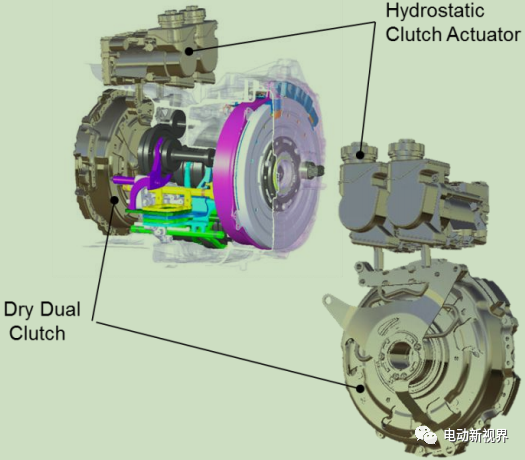
液压系统
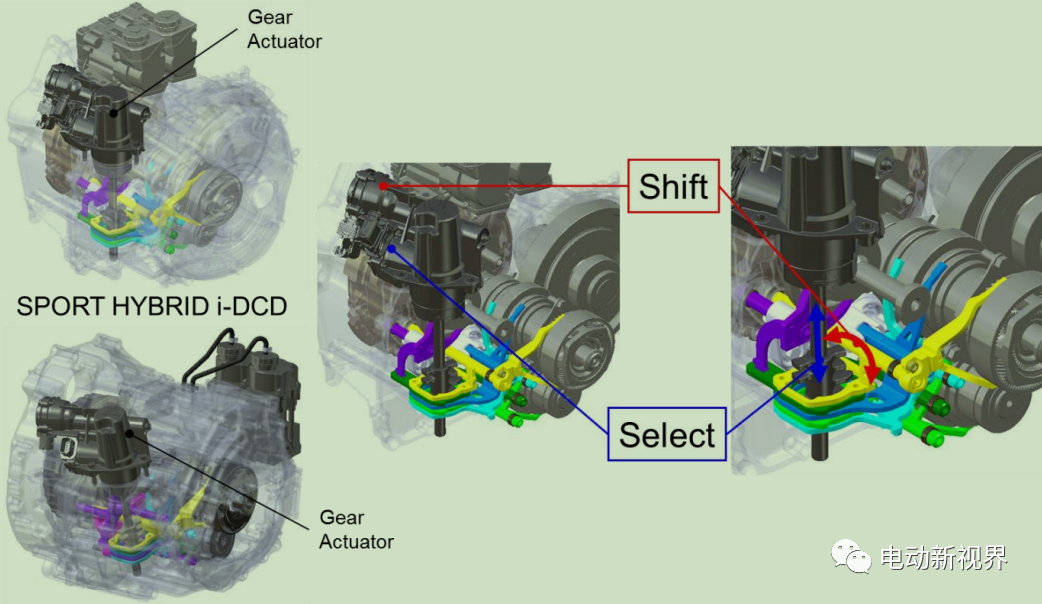
换挡系统
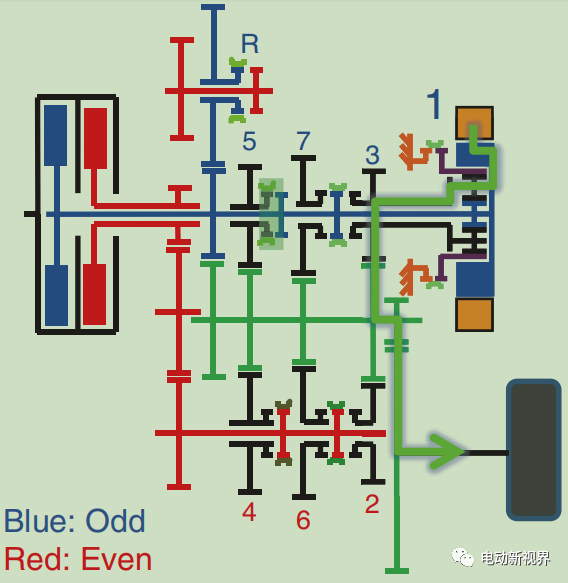
EV行驶模式
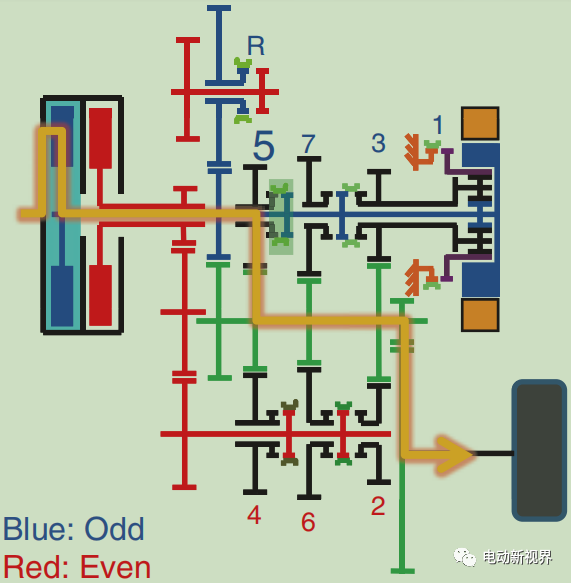
发动机驱动模式
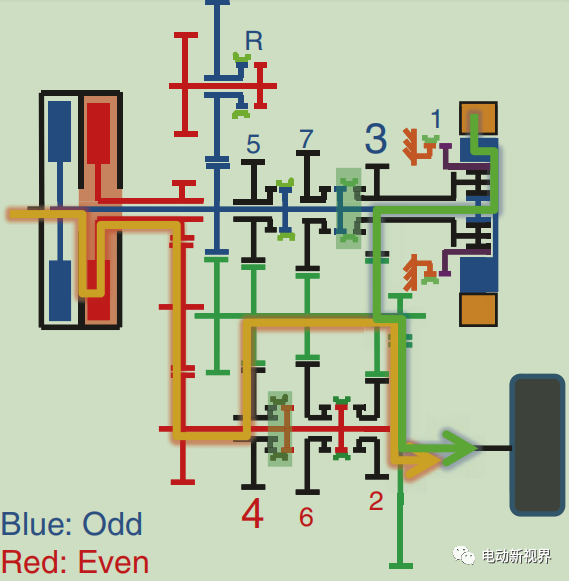
混动驱动模式
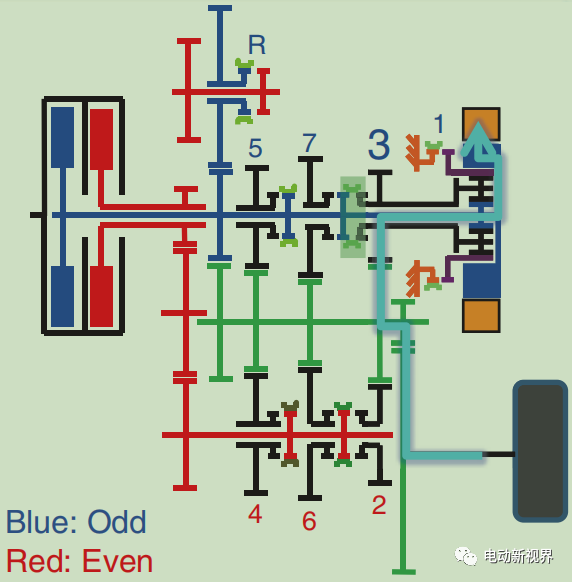
制动能量回收
EV行驶模式
当驱动电机单独驱动时,两个离合器均不接合,结合1挡、3挡、5挡和7挡同步器通过奇数轴输出,实现不同传动比(事实上只会采用少数档位)。 同传统DCT相同,结合不同的离合器和同步器,实现7个不同传动比的前进模式。
当发动机和驱动电机共同输出动力时,可存在多种混动模式。笔者不在累赘,有兴趣的读者可自行思考;