电驱系统温控杂谈(二)
目录
一、为什么要做温升
1.背景
二、重点考核对象
1.重点考核对象
2.重点考核对象-驱动电机转子温升/驱动电机定子温升
3.重点考核对象-IGBT等功率器件温升
4.重点考核对象-高压线束温升
5.重点考核对象-减速器油封唇口温升
6.重点考核对象-减速器支撑轴承温升
三、对电驱传动系统的要求
1.电驱系统设计要求
2.传动系统设计注意事项
四、电驱传动系统设计中的温升考虑
1.温升考虑
2.电驱传动系统-箱体的仿形设计
3.电驱传动系统-箱体储油池设计
五、电驱传动系统的温升控制
1.传动系统热平衡机理
2.运用环境-工况分析
3.合理的温控策略
4.齿轮-优化齿轮结构参数
5.齿轮-精确齿轮修形技术
6.轴承-优选型号-结构参数
7.轴承-安装配合设计
8.轴承-承载分析、发热量计算
9.箱体结构-拓扑优化箱体结构
10.箱体结构-油量存储空间控制
11.箱体结构-散热区域结构优化
12.箱体结构-散热区域结构优化
13.润滑油路:进-回油油路设计
14.润滑油:产品的选用原则
15.润滑油:油量精确控制
16.温控验证措施
六、电驱传动系统验证
1.型式试验-试验验证体系
2.型式试验-试验验证方案
七、电驱传动系统试后确认
1.服役完成后的拆解检查
接上文......
- 箱体的仿形设计-------降低飞溅润滑油的功率损失
- 润滑油储油池设计-------保证润滑的前提下控制搅油发热
- 齿轮副的优化设计-------优化齿形参数、齿宽等,降低搅油损失
- 轴承副的优化选型-------结合载荷、计算,综合评估发热和承载
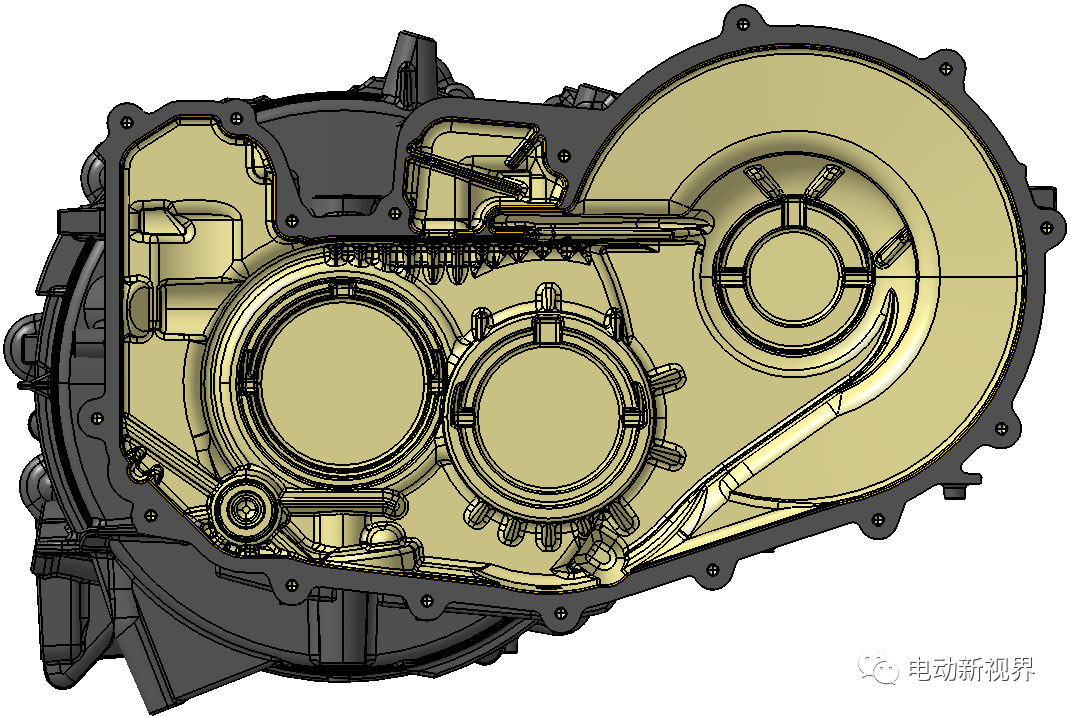
传动系统采用仿圆弧设计,降低搅油损失
结合箱体结构,布置不同的控制参与润滑油油量的结构,将润滑油油池分割为搅油池和辅助储油池。
- 深入掌握传动系统运用过程中的发热、散热机理,研究与传动系统温升相关的影响因素。
- 基于理论分析计算、优化设计传动系统结构、合理选择关键零件,衡量传动系统综合性能、制定合理的传动系统温控方案。

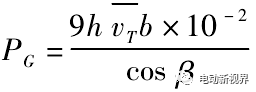
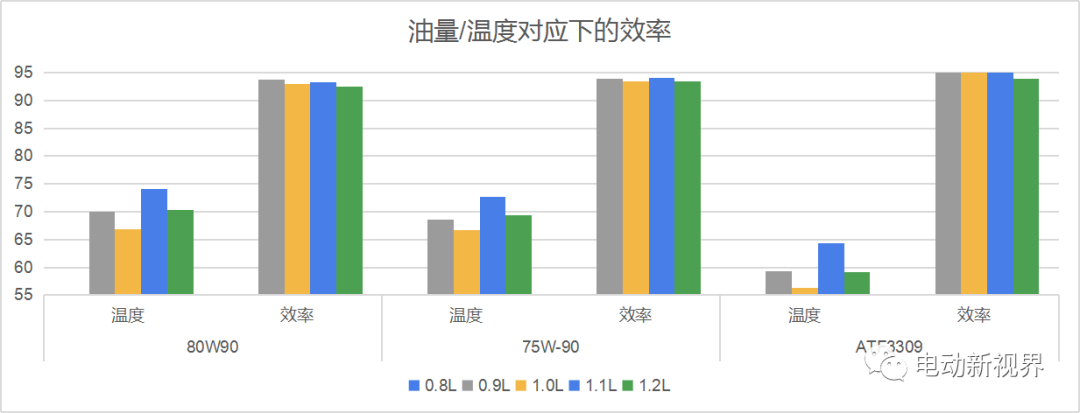
温度难题:润滑与冷却矛盾下的温控
3.合理的温控策略
如何控制传动系统温升
高温情况下如何抑制温升
低温环境下如何保证润滑
掌握热平衡机理
研究传动系统发热源
分析传动系统散热方式
摸清温升影响因素与规律
制定温升控制策略
设计源头入手、控制发热、散热,配合不同技术方案,形成最优温控策略
基于温控目标-------齿轮轮廓设计(渐开线段+齿根曲线)-------刀具设计-------齿轮滚切成型。 多目标优化、增大温控目标权重系数,优化轮缘、轮毂、腹板结构。
通过精确齿轮啮合修形设计,减小啮合冲击,降低啮合时齿面接触温度 修形后两齿轮在啮合过程中滑动系数接近,相对磨损较小,减少啮合发热。
6.轴承-优选型号-结构参数
在有限的结构空间内,选择适用于告诉、重载、轻量化轴承。选用特制轴承,保持架优化设计,滚道、滚子特殊修形及热稳定处理,减小滑动摩擦降低高速旋转时的发热量。
优化设计输入端柱-球轴承配合型式及安装位置,合理控制输出端锥轴承有效跨距,均匀承载,避免两端产生较大温差。 正确的安装和配合、恰当的游隙设计,反复试验验证,选取最佳游隙范围。(过大或过小的游隙均造成轴承异常温升)。
贴合传动系统实际运用工况,准确分析轴承受载情况,摸清轴承转速、当量动载荷与轴承功率损失的关系 结合轴承内部结构,仿真计算轴承滚子-滚道接触处的弹性动态流体损失,模拟轴承运转过程中的热量生成与散失。
在满足箱体强度、轻量化及模态振动特性的要求下,基于多工况模拟箱体内腔润滑油分布状态,对传动系统结构进行拓扑优化,提升热交换率。 根据润滑油在高速状态下的搅动形态与飞溅轨迹,内腔采用仿圆弧光滑过渡设计,减少润滑油的阻力,降低温升。
合理设计箱体内油池结构和空间大小,在保证润滑的同时,控制润滑总油量,减少搅油量。 箱体油池内增加隔腔设计,相对独立分隔润滑油搅动区域和散热区域,加速润滑油,冷却循环。
在满足箱体轻量化的要求下,增大箱体外部散热面积,优化设计散热筋板,提高导热率。
根据箱体内润滑流动状态,在箱体上部合理设计集油槽结构与位置,收集飞溅润滑油,辅助轴承润滑,减少发热量。 在箱体下部轴承安装位置,设置挡油板结构,收集并储存一定油量,用于启动工况下轴承的瞬时润滑,避免因润滑不良造成的轴承温升过快而烧损。
箱体内设计有辅助轴承润滑的进油油路,将飞溅的润滑油导向轴承,经过热交换后通过回油油路流回底部油池,人为设置润滑油润滑冷却循环过程,提高散热率,达到控制轴承温升的目的。
结合传动系统运用工况、工作温度、润滑周期等因素,选择合适粘度等级及性能的润滑油,减少摩擦损失。
依据成熟的运用经验、结合润滑理论计算,设置初始油位与齿轮浸润深度,结果台架试验反复验证,选取最佳实际油位,减少发热量,提高传动效率。 通过基于记忆合集流量调节的温控技术、低温提供足够油量保证轴承齿轮润滑,高温降低油量减小搅油损失。 通过该系统可实现温度、振动、转速、压力、油品等综合多参数的在线监测与数据传输、评价; 覆盖高温 +50℃、高寒 -50℃、风沙、雨水等极端环境模拟试验台,全面验证传动系统温升变化规律。
结合国内/外相关产品实际运营情况及多年来的传动系统研发、制造、试验的经验,确定产品试验验证方案。
定期入库检查,确保传动系统正常
远程温度监控,掌握实时动态
收集相关温升数据,分析评价传动系统寿命判断、预估故障风险
全文完~