【电动新视界】电机控制器设计中的成本博弈
目 录
一.新能源汽车市场发展现状
2020年1-6月,新能源汽车产销分别完成39.7万辆和39.3万辆,同比分别下降36.5%和37.4%。
1-6月,纯电动汽车产销分别完成30.1万辆和30.4万辆,同比分别下降40.3%和39.2%;
1-6月,插电式混合动力汽车产销分别完成9.5万辆和8.8万辆,同比分别下降20.0%和29.8%;
1-6月,燃料电池汽车产销分别完成390辆和403辆,同比分别下降66.5%和63.4%。
数据表明,从3月份开始,新能源汽车产销呈现恢复性增长态势。
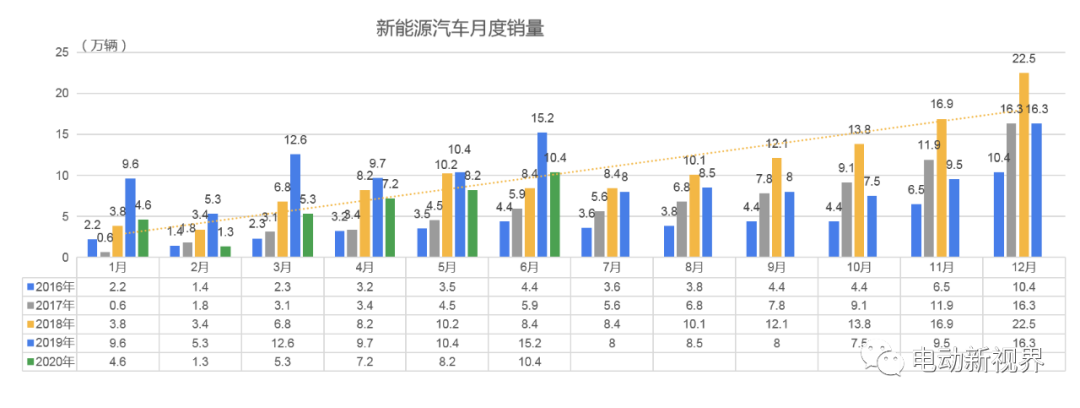
2019年全年,国内新能源汽车电机控制器累计装机量超过了124.2万套,比去年同期下降2.3%,保持了供需两旺的销售态势。
根据美国阿贡实验室公开披露的评估报告,电动汽车电机控制器约占整车生产成本的9%,是除了动力电池外成本支出最高的电动汽车系统零部件。
通过对电机控制器成本结构的分析,我们发现目前IGBT功率模块占据了电机控制器接近40%的成本,除去其是核心部件本身成本比较高的原因外,另外一个很重要的原因在于国内车用高功率半导体主要被外资厂商所占据,如:英飞凌、仙童、富士、三菱、SEMIKRON、Hitachi、东芝 等。不过,以比亚迪、中国中车为代表的国内企业通过不懈的努力和持续的研发投入,目前已有多款新能源汽车专用IGBT模块推向市场,取得了不错的销售成绩,为拉低IGBT模块售价做出了卓越的贡献。 参考美国能源部发布的《电力电子发展路线图》,到2025年新能源汽车电机控制器及功率模块需要达到如下指标:- 单位功率密度增长到100kW/L,要比2020年技术目标13.4kW/L减少87%的体积;
- IGBT功率模块占控制器总成本要降到23%(现在是37%);
- 控制器总成成本比2020年目标3.3$/kW下降18%,达到2.7$/kW。
3.1.1 IGBT模块的选型
目前市场上广泛流通的IGBT模块根据水冷结构和封装模式被分为三种:最早出现的“引线键合、单面冷却”的IGBT模块,依靠传导进行散热。优点:产量大、成本低、性能达标;缺点:功率密度低。因其优秀的性价比,目前仍被商用车电驱厂家广泛采用。 在平面封装IGBT模块之后出现了“平面封装、集成冷却”的IGBT模块,这种模块将之前的间接水冷变成了直接水冷,提高了散热效率,壳体设计者也免除了设计水道的烦恼,应用简单而高效。优点:功率密度高、性能优良;缺点:产能不足,成本稍高,目前只有乘用车才会舍得用这一功率模块。 单面直接水冷还是不能满足持续增加的散热需求,因而双面直接水冷模块应运而生, 双面冷却方案是把温度传感器和电流传感器功能集成,实现对整个模块进行芯片级的管理,同时集成水冷流道的散热结构。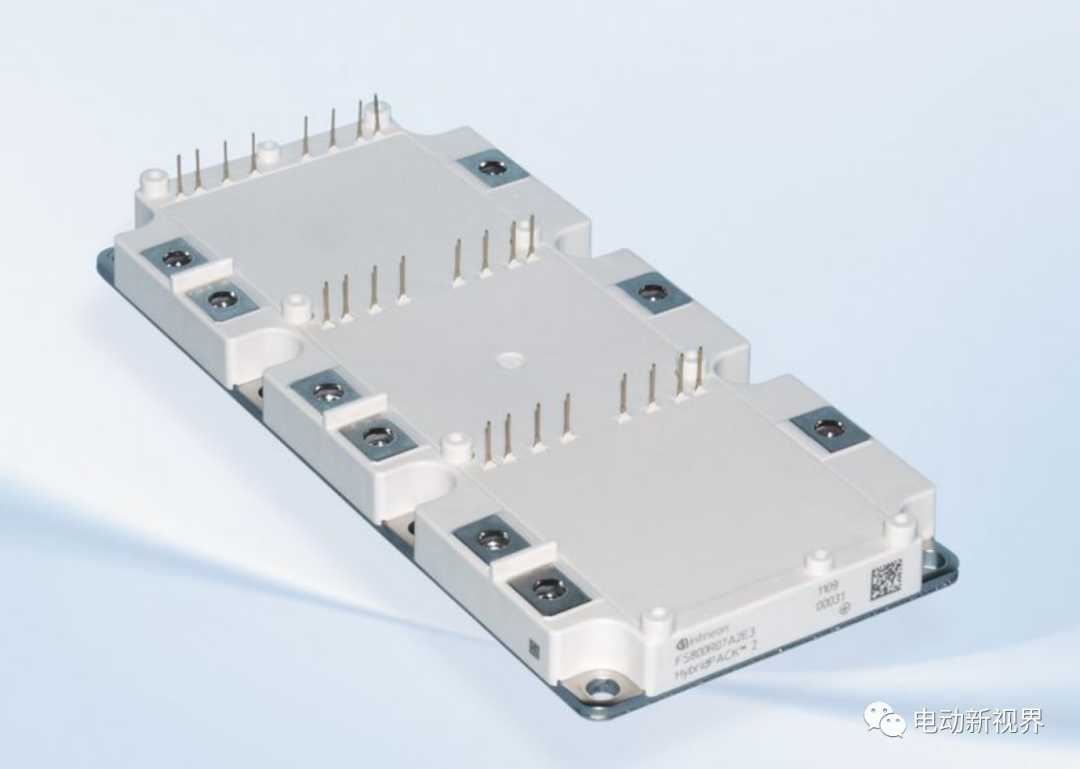
英飞凌单面平板冷却
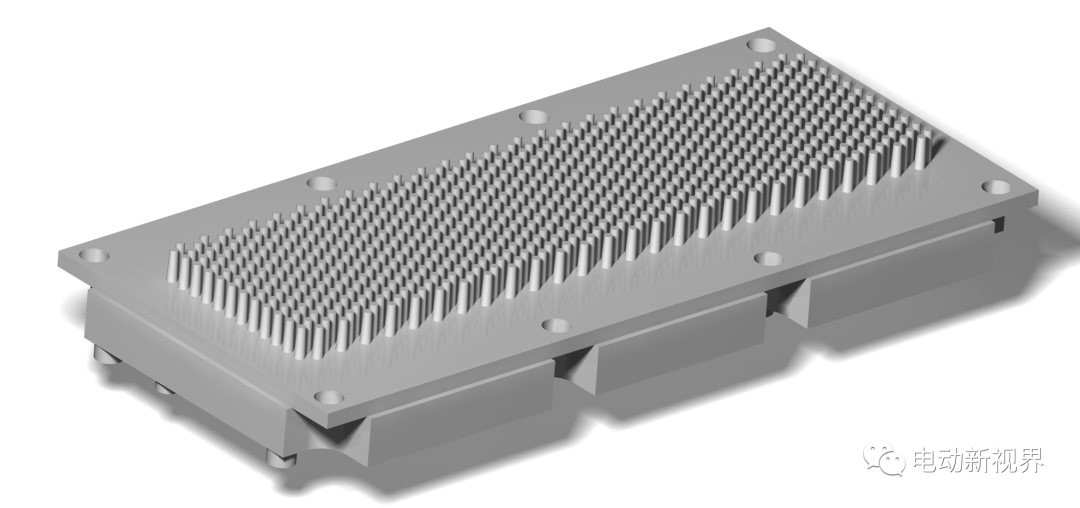
英飞凌集成Pin-Fin直接水冷
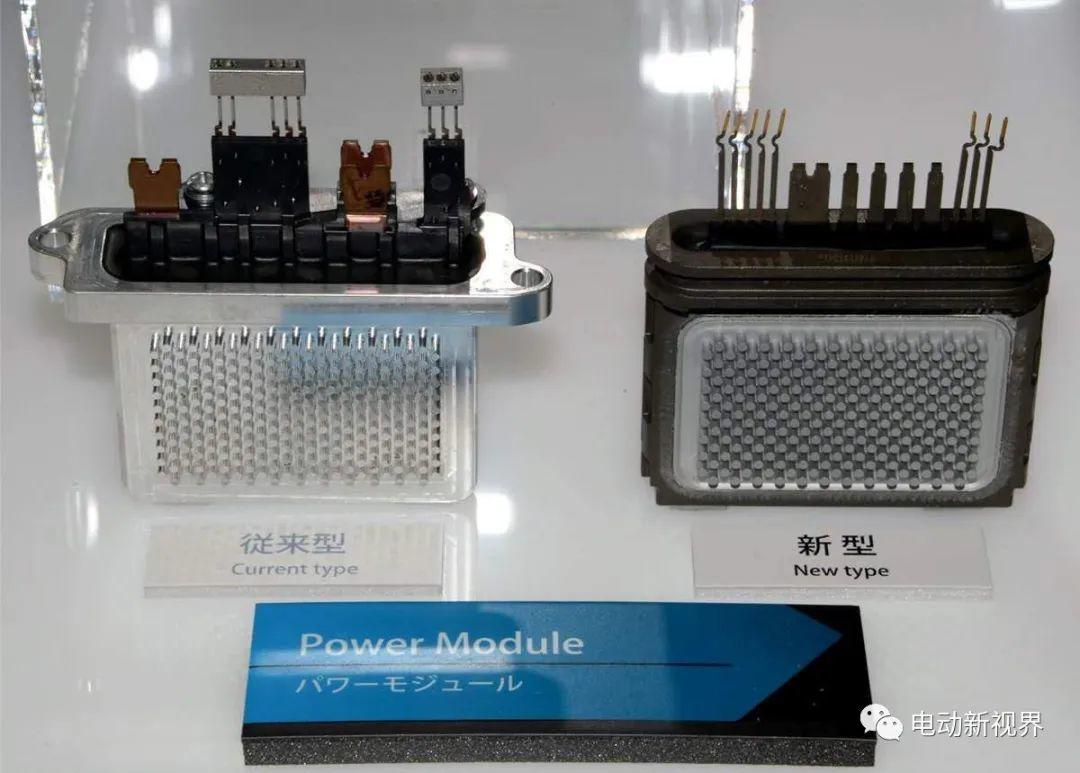
Hitachi集成双面Pin-Fin直接水冷
以散热器内部使用经典的Pin-Fin散热流道方案为例,阐述一下双面水冷模组的优势。水冷设计的重点包括流量的均恒,散热流族限制下的Pin-Fin针形状和大小的优化设计。基于同样的总流量假设,双面水冷较之单面水冷,热阻可以减小32%,同时水路压降跌落也只有其35%。同时,对于双面散热,仅增大27.5%的压力,就能获得双倍于单面水冷的总散热流量。同等条件下,采用双面水冷散热后,输出功率能够增加30%以上。如果采用更优化的水冷板设计,控制器的电流能力能够增加50%甚至更多。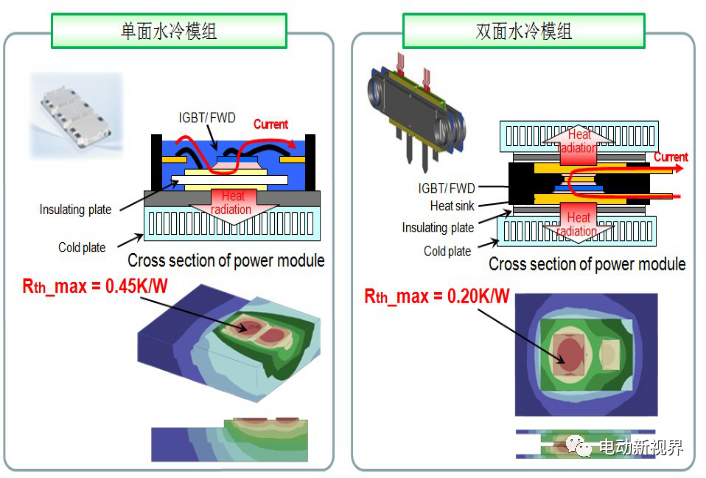
单双面水冷模块性能对比
单面平板冷却的IGBT模块需要壳体上设计水道,壳体设计难度增加,复杂的形体降低了壳体模具使用寿命,增加了维护成本;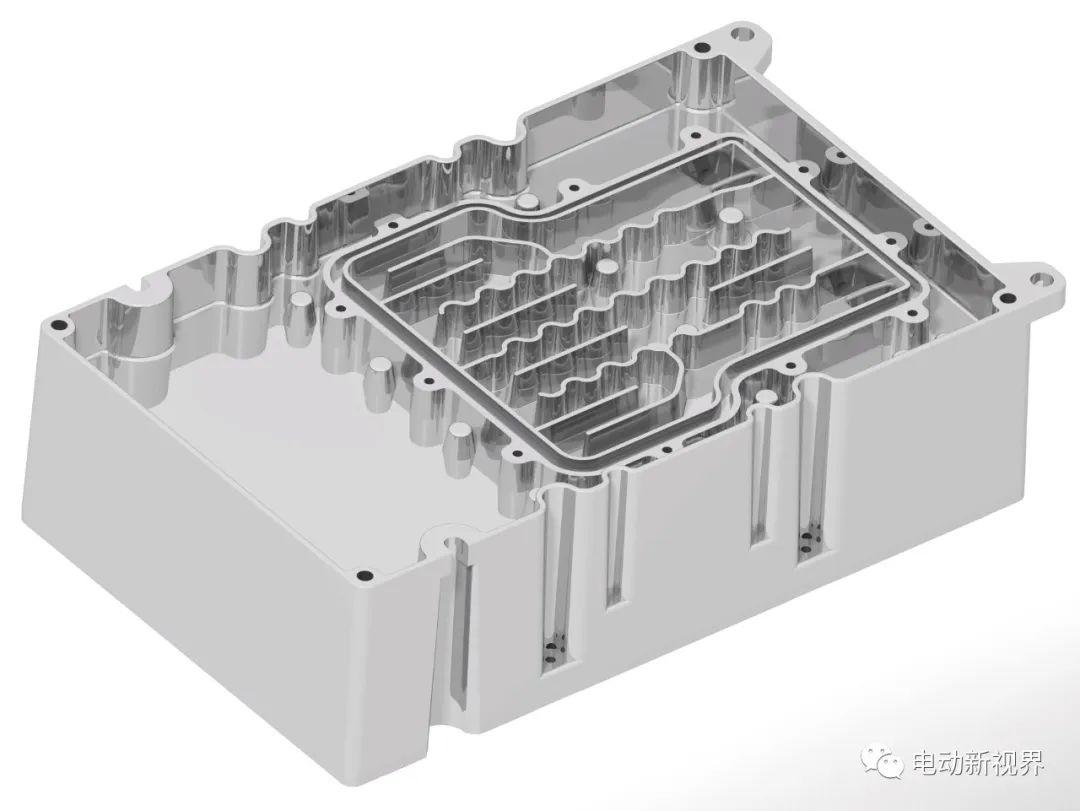
平板冷却水道
集成Pin-Fin直接水冷模块,设计简单,留好密封沟槽即可,综合维护成本较低;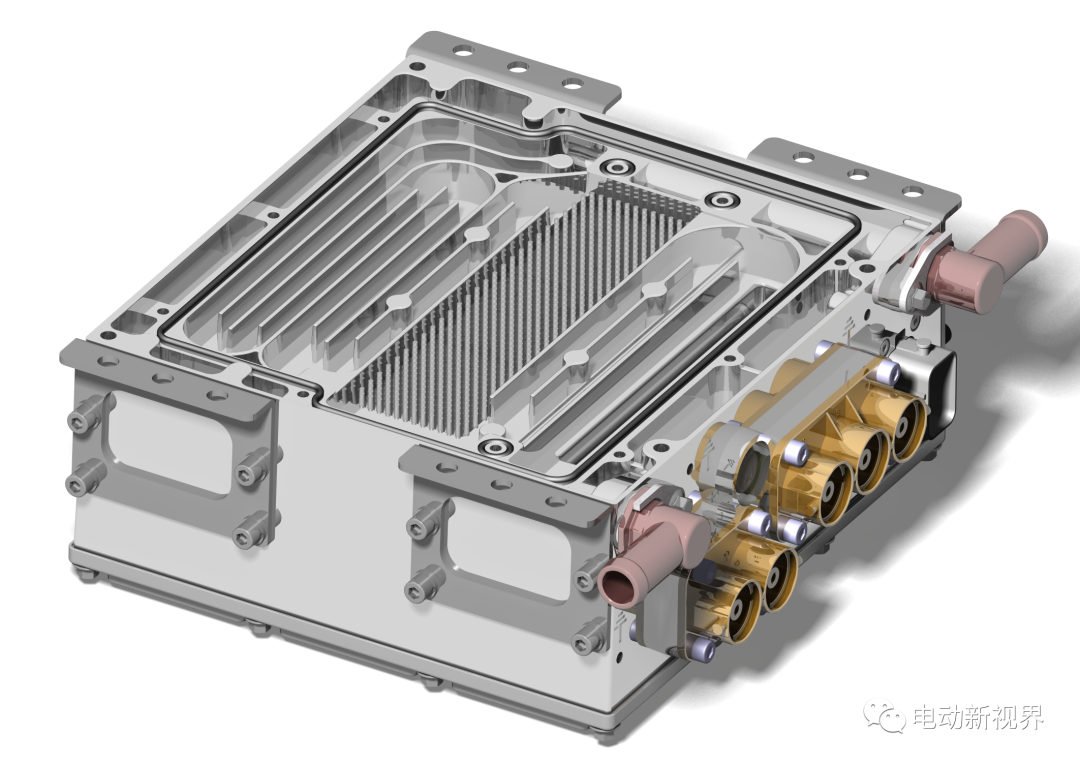
集成Pin-Fin直接水冷壳体
双面Pin-Fin直接水冷模块水道连接设计相对复杂,密封可靠性要求高,模具复杂,成本高。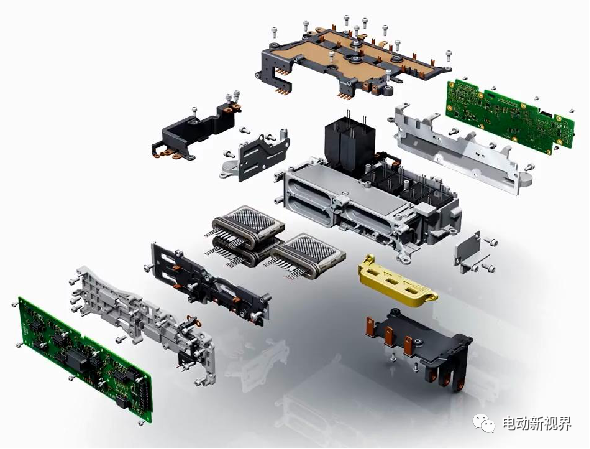
奥迪e-tron双面直接水冷模块控制器爆炸图
电机控制器壳体通常采用铸铝外壳,少量商用车控制器外壳采用钣金拼焊箱体。铸铝外壳又分为高压铸造、低压铸造、重力浇铸等三种工艺实现形式。高压铸造的壳体壁厚在2.5~4mm之间,低压和重力浇铸的壳体壁厚在4~6mm。高压铸造工艺模具费是重力浇铸模具费的2倍多,但产品重量轻,用料少,生产效率高,后期机加费用少,适合大批量生产。低压和重力浇铸产品重量大,生产效率低,后期机加成本高,适合小批量试制阶段。在提倡汽车轻量化和追求产品功率密度的今天,选择高压铸造工艺占绝大多数。 在产品设计时最好将侧面特征尽量集中的一个平面上,这样可以减少抽芯模具数量,降低模具成本和模具的故障率。据测算每增加一个抽芯结构,模具综合维护成本增加3~5万元。
镁铝合金的密度约为1.8g/cm3,是铝合金的2/3,是铁的1/4。它自身具有很多优良的材料特性:比性能好、减震性能好、导电导热性能良好、工艺性能良好、耐蚀性能差、易于氧化燃烧、耐热性差。
其加工过程及腐蚀和力学性能有许多特点:散热快、质量轻、刚性好、具有一定的耐蚀性和尺寸稳定性、抗冲击、耐磨、减振性能好及易于回收;另外还有高的导热和导电性能、无磁性、屏蔽性好和无毒的特点。在相同载荷下,减振性是铝的100倍,钛合金的300~500倍。电磁屏蔽性佳,3C产品的外壳(手机及电脑)要能够提供优越的抗电磁保护作用,而镁合金外壳能够完全吸收频率超过100db的电磁干扰。质感佳,镁合金的外观及触摸质感极佳,使产品更具豪华感,而且,在空气中更不容易腐蚀。
推荐理由:
同时它优秀的电磁屏蔽性更能够提供优越的抗电磁保护作用,可增强整机的EMC屏蔽效果;
目前镁铝合金的材料成本要比铝合金贵10%~15%左右,但它用料更省,其最小壁厚可以做到0.6mm,而铝合金最小壁厚只能做到2-2.5mm;
对于控制器内部的驱动板和控制板之间的屏蔽板材料,镁铝合金也是当之无愧的首选,其综合性能远超铝合金跟铁质钣金件;
镁铝合金的模具成本比铝合金能节省30%~40%,模具寿命几乎是后者的两倍,综合维护成本更低。
端子座盖板与壳体之间,控制器的上下壳体之间需要设置密封圈用来防水防尘,理论上这些缝隙也是电磁防护的薄弱区,应采用导电橡胶进行EMC防护处理,但是导电橡胶密封圈的售价是普通橡胶圈的3~6倍。是否采用,要看EMC的试验效果再去衡量吧。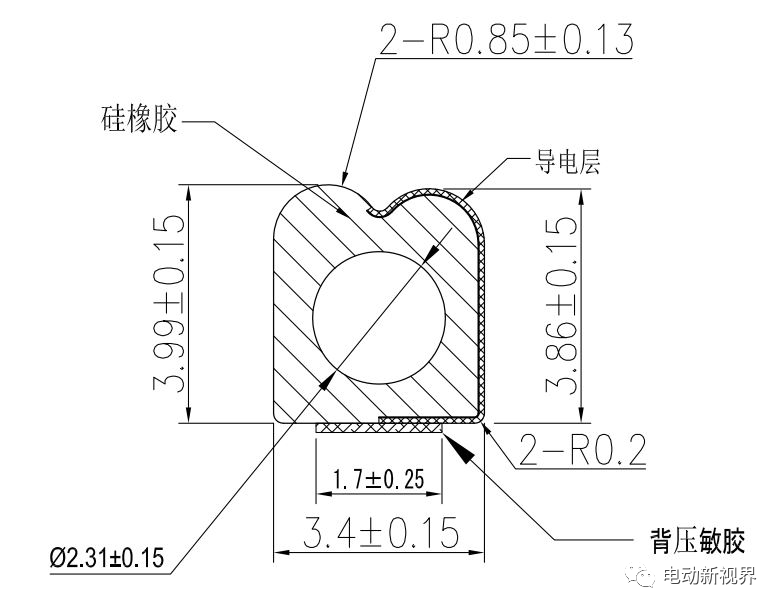
导电橡胶密封圈结构图示例
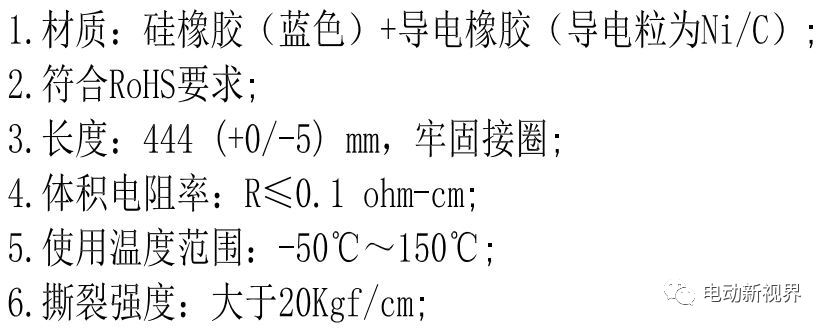
技术要求
因为是静压力密封使用环境,密封圈的截面多种多样。底面大多为全平面设计,接触密封面多个小半圆凸起的,全平方形圈,大半圆凸起的各种形状均有应用实例。
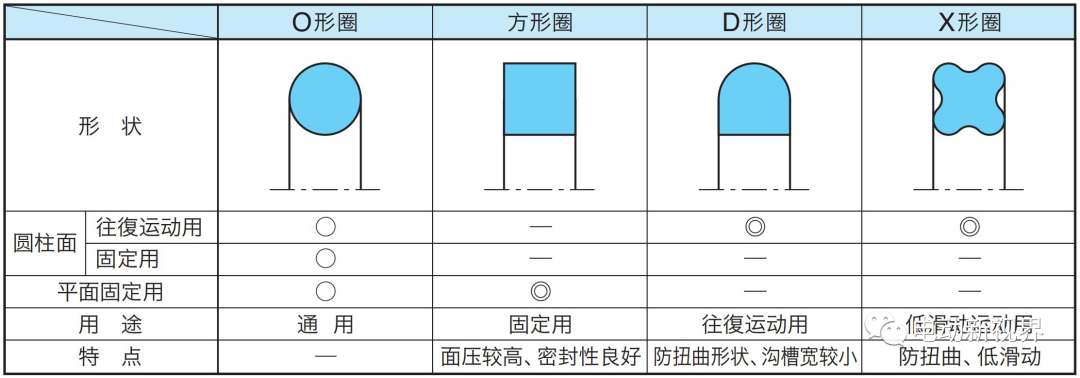
密封圈的截面形状
目前,铜排表面使用镀锡或者镀银,用来提高铜排的耐腐蚀性。在追求高功率密度的压力下,铜排之间的间隙越来越小,为了保障铜排之间的绝缘耐压等级,需要在铜排之间使用耐高压的绝缘介质把彼此隔离开,我目前看到过图示的这两种解决方案。有喷涂绝缘树脂的,抗磨耐拉,强度很好,价格较贵。但铜排之间可以亲如兄弟,不分彼此,像直流铜排是可以用胶水粘在一起进行装配,比较方便。另外的就是绝缘纸方案,吉泰科的控制器中经常使用,性能应该是可以达标的,就是装配性上感觉没有绝缘树脂那种随心所欲,价格怎么样,我也不是很清楚了。 有的公司为了提高载流能力降低铜排发热,避免集肤效应和产生铜排接触变形应力,可采用叠层铜排,效果很好,样件阶段是普通铜排的2-3倍,批量后价格基本持平。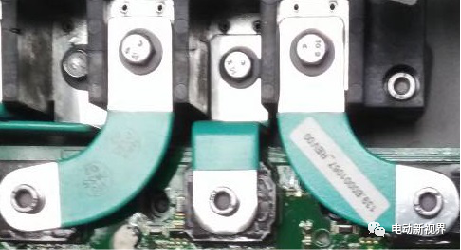
绝缘树脂铜排
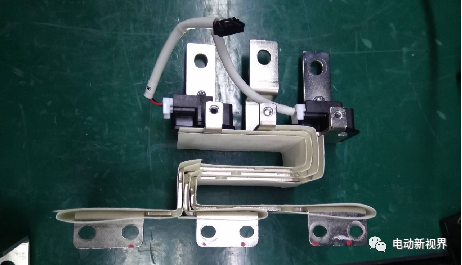
密封圈的截面形状
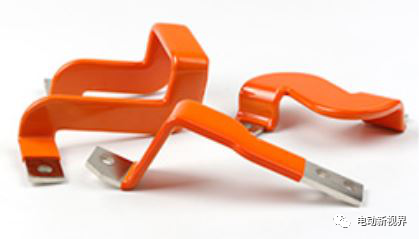
表面浸塑叠层软铜排
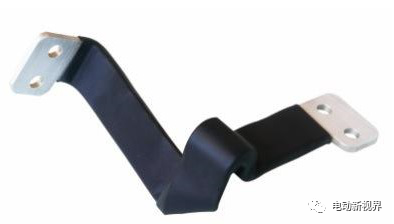
表面浸塑叠层软铜排
3.5 高压线接头选型
- 控制器的高压接头通常有两种选择:格兰头、快插接头。
- 缺点是需要为它们设计转接的端子座及单独的接线盖板,占用空间大。安装时有可能发生异物进入腔体的事故,生产效率偏低。
- 快插接头可以取消端子座和接线盖板,铜排与快插接头直接相连,三相线直接相连的前提是电流传感器要固定在驱动电路板上,这样可以简化设计,提升功率密度。整车厂生产中不用再进行开盖接线工作,极大的提高了生产效率,同时也降低了生产过程可能造成的控制器内部质量问题。
- 缺点是成本稍高,采购成本大概是格兰头方案的2~3倍。
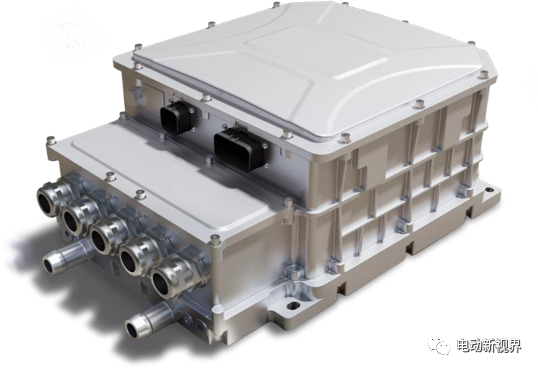
吉泰科格兰头方案电机控制器
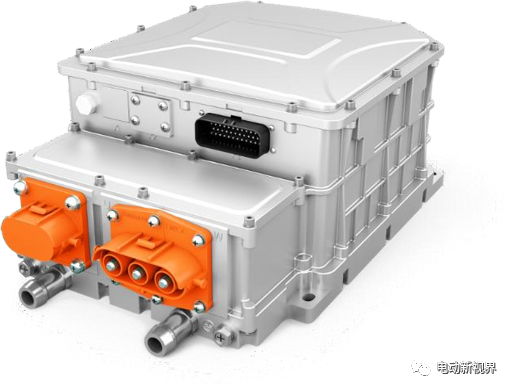
吉泰科快插接头方案电机控制器
作为独立第三方电驱供应商,产品的安装支架最好是单独的,这样可以提高产品的适应性,特别是后期介入的厂家,让整车厂改设计适应你的产品是不太现实的。多数情况下只能自己改产品,如果仅仅是因为安装间距不合适就得再开套模具,那成本基本是无法接受的。如果是只改个安装脚,那就简单多了。在设计阶段规避适配性风险还是很划算的,这也是最经济的控制成本手段之一。 整体安装架方案结构简单,一体模具成型,成本低,比较适用于背靠整车开发平台的初始电驱供应商采用。
现在的控制器内通常设置有至少两块电路板,一块负责三相IGBT模块的驱动控制,一块负责系统控制和保护。在未来将会如AVL的电驱动系统一样,实现合板设计,通过多层板布置及高低压分区等手段来实现功能集成,实现最优化的设计。
在降本增效的压力下,越来越多的厂家尝试用钣金件代替铝合金压铸件做为控制器上盖,既可以降低模具费成本又可以进行系统轻量化。但此设计对模态验证要求颇高,EMC防护效果有所降低,需要综合考量应用前景。
Ⅳ.总结
- 成本的控制是一个综合考量的过程,是一个多方因素博弈的产物,一味追求低成本的解决方案可能带来灾难性的后果,保持合理和理性是最佳的成本控制策略。
- 商用车电控配套厂家拼的是最优的成本控制策略,乘用车电控配套厂家则代表了新技术的发展方向,最佳性能的优先级在成本考量之上,因为它们有更大品牌和性能溢价空间,消费者乐意为增加的成本买单。
- 机械和硬件的设计成本控制都是摆在明面上的,收效有限;有无限潜力的降本增效手段就是软件控制程序的优化,如果软件程序足够先进,则可以在硬件端节省大量的冗余保护设计。
- 软件工程师的价值是可以“无限”挖掘的,他们投入的是有限的人工成本,产出的是实实在在的经济效益,是目前电控相关职业中投产比中性价比最高的职业,没有之一。
全文完~