盘点特斯拉Model 3 应用的轻量化技术
目前来说,汽车轻量化的路径主要包括使用轻量化材料、采用先进制造工艺以及在设计时考虑轻量化结构三个方面。但一方面汽车设计和制造工艺门槛高,轻量化成本大,另一方面无论是哪一方面的轻量化,最终都要落脚于轻量化的材料以及零部件上。因此轻量化材料及零部件的使用是目前的主要方向。从对特斯拉 Model 3 的轻量化零部件拆分来看,其主要分布在电池壳体件、底盘簧下结构件以及车身件上,材料以铝合金、高强度钢以及工程塑料为主。具体而言,Model 3 在车身上通过减少铝的用量,增加钢材的用量以降低成本和增加安全性,同时通过大幅减轻电池动力系统壳体、导线质量以及底盘簧下系统质量来冲减车身的质量,不同于前作 Model S 的大范围使用铝合金,Model 3 在成本、性能、安全性的约束下,最大程度的实现了整车轻量化目标,轻量化水平居同轴距电动车前列。
1.1. 油车降油耗和电动提续航,轻量化是必由之路
燃油车 2025 年平均油耗要降至 4L/100km。随着全球汽车保有量的迅速增长,面临能源、环境和安全的压力日益加大,节能减排政策也随之不断收紧。根据最新的《乘用车燃料消耗量评价方法及指标》,到 2025 年乘用车平均燃料消耗量要达到 4.0L/100km。企业燃料消耗量与目标消耗量比值要自 2021 的 123%不断下降,到 2025 年需要达到目标值。根据工信部披露数据显示,2019 统计的 144 家乘用车企业中,平均燃料消耗量实际值为 5.56L/100km,燃料消耗量达标的企业仅占 40%。随着节能减排政策的不断收紧,各车企需要采取更多的应对措施以达到降能耗的要求。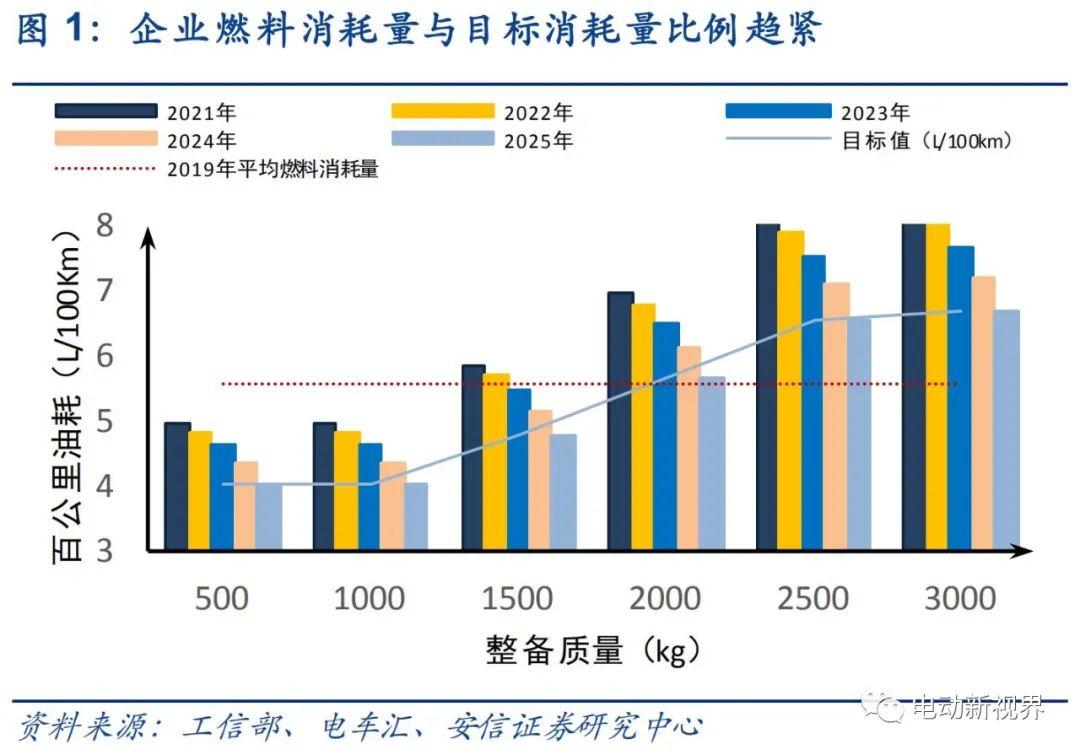
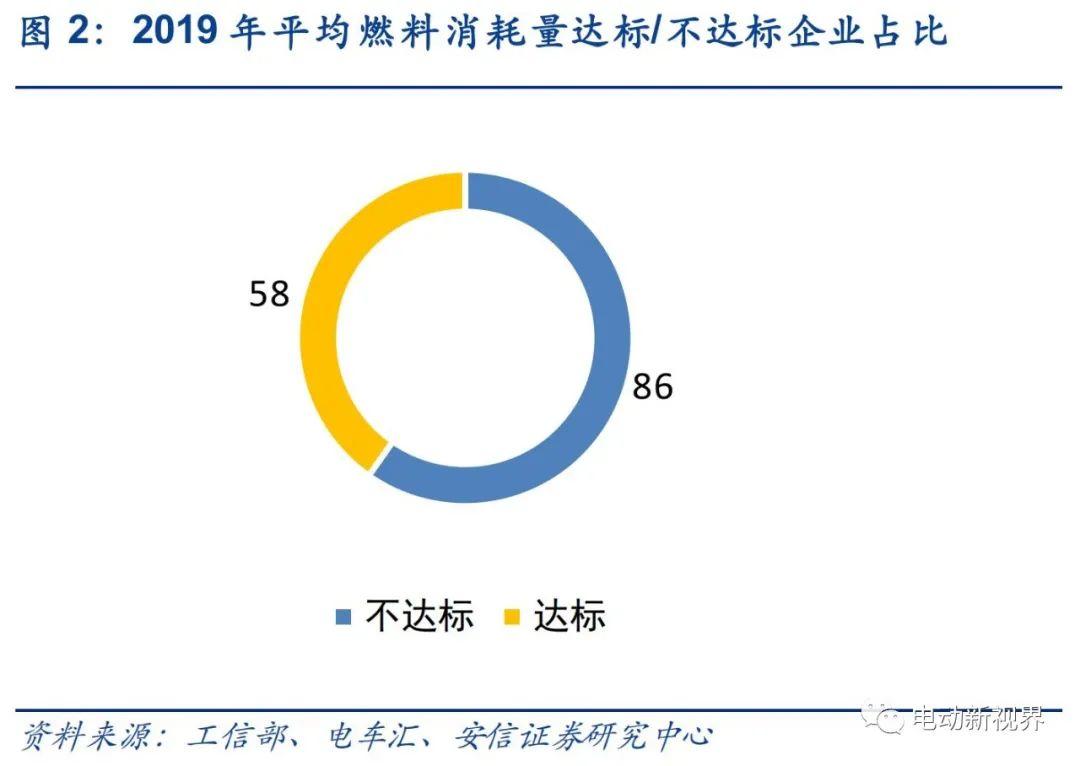
燃油车要达到降油耗目标,轻量化必不可少。根据中汽研节能经济技术分析结果,单靠对发动机、变速器或混动技术来降低燃料消耗水平,无法达到预定的降能耗目标。在影响汽车能源消耗量的因素中,重量最为关键。相关研究表明,燃油汽车车重降低 10%水平下,能够带来 5%-8%的能耗减少以及 10%左右的排放量减少。此外,轻量化带来的成本增量较其他方案也具有可观的比较优势。因此,通过轻量化技术来降低油耗变得十分关键。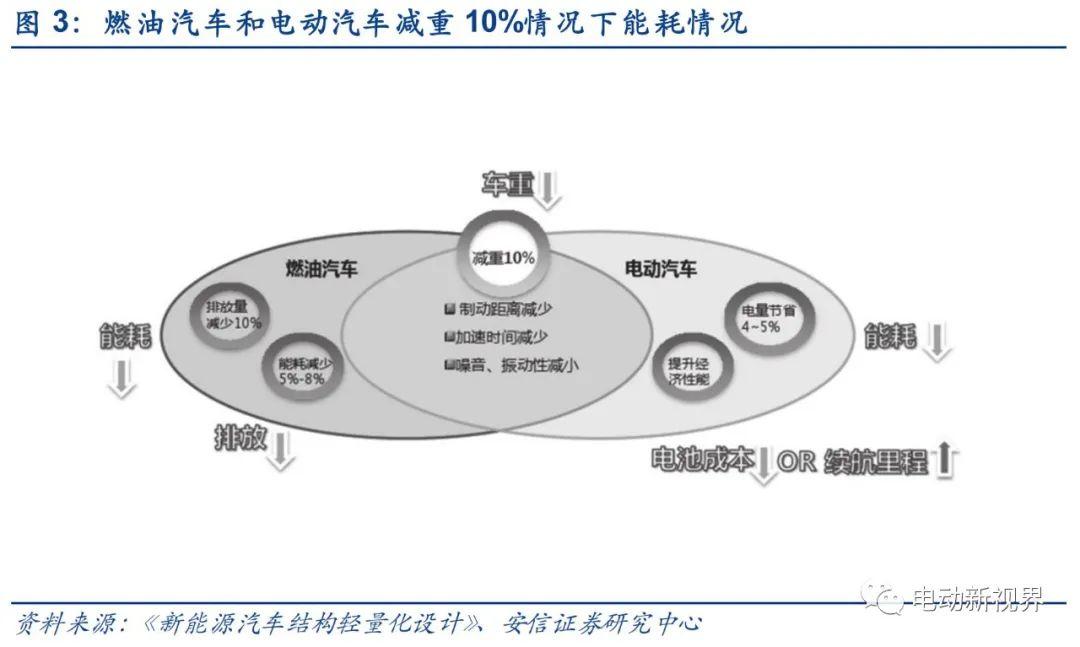
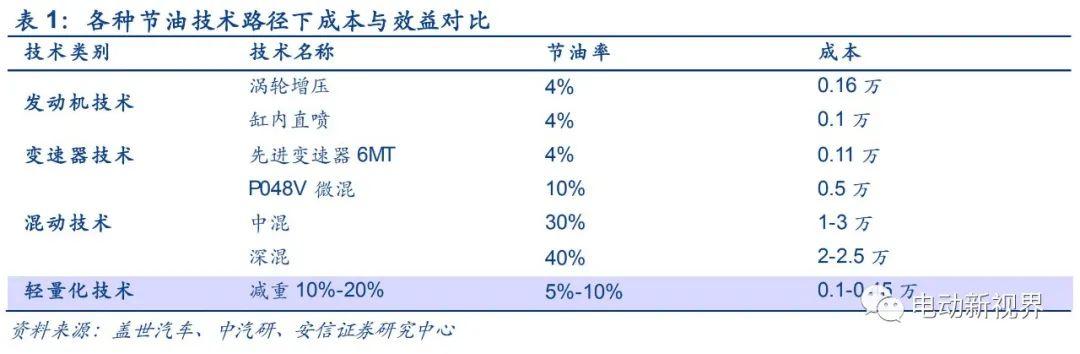
相较于传统燃油车,新能源汽车轻量化更为迫切。新能源汽车是未来确定的大趋势,而续航里程是制约新能源汽车普及的关键因素。由于三电系统的加入,新能源车相比传统车车重增加明显。与此同时,电池的带电量、车重与续航里程直接相关,而电池成本占整车成本的比重超过 30%。在电驱动技术以及电池能量密度方面没有突破性进展的时候,通过减轻车重可以显著提高续航里程或者保持续航里程不变的情况下减少带电量进而降低生产成本。根据华晨汽车工程研究院数据,新能源汽车质量降低 10%,对应续航里程可增加 5%~10%,相应可节约 15%~20%的电池成本以及 20%的日常损耗成本。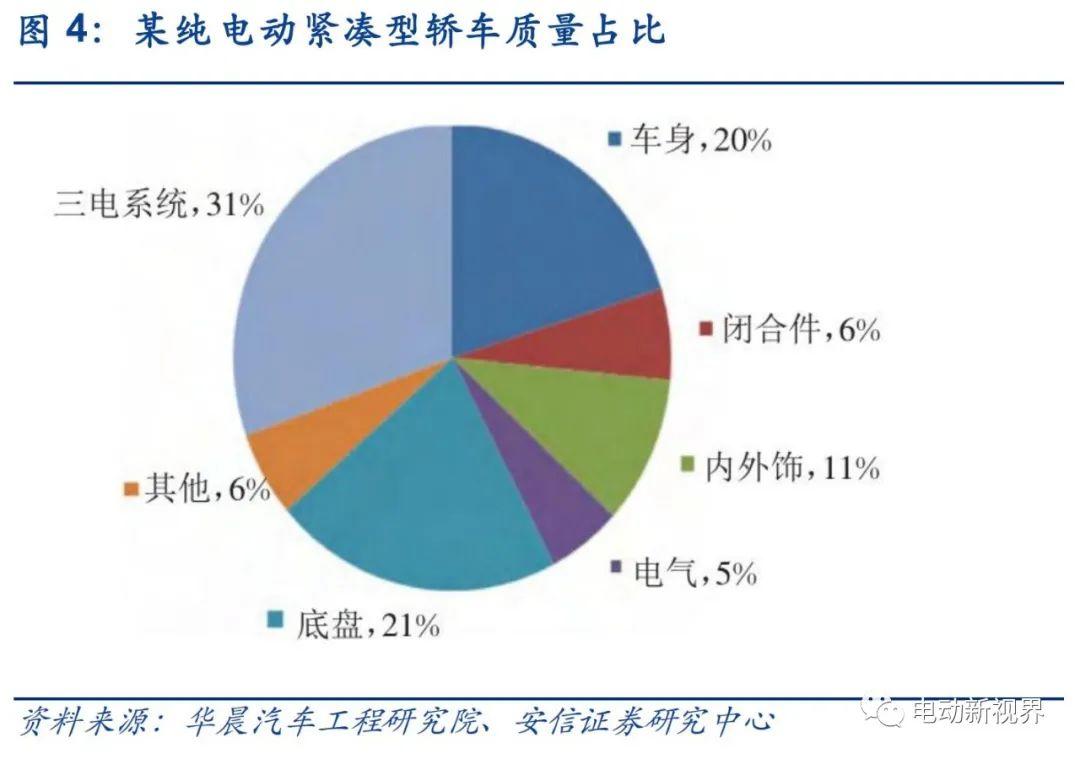
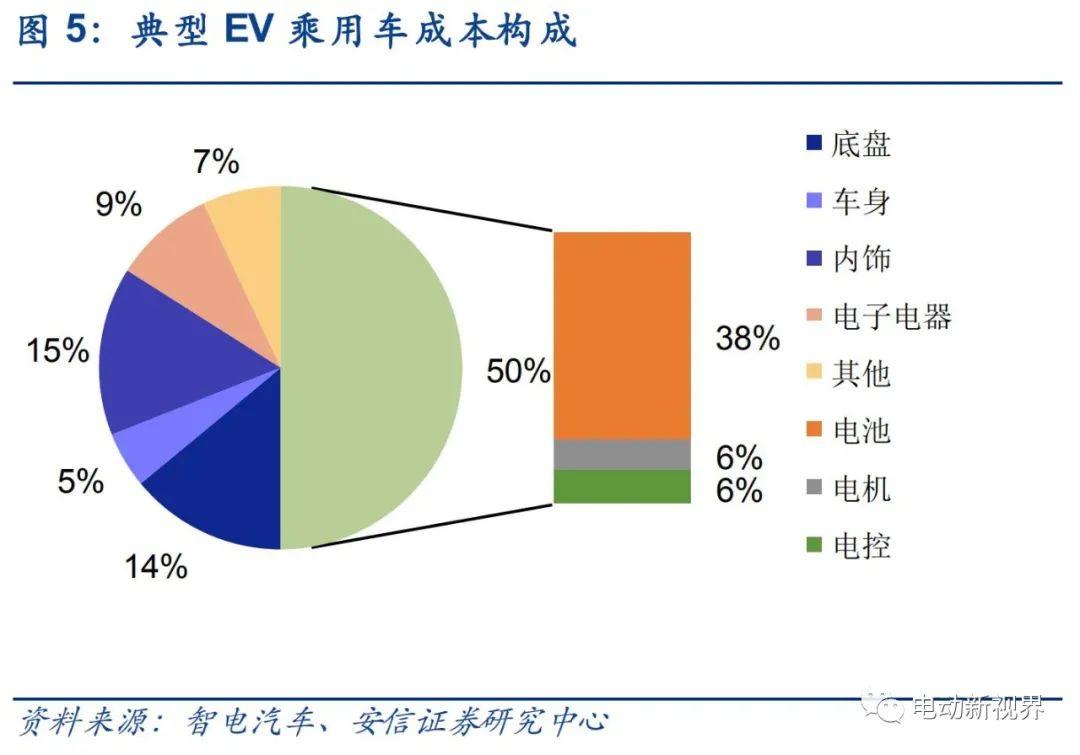
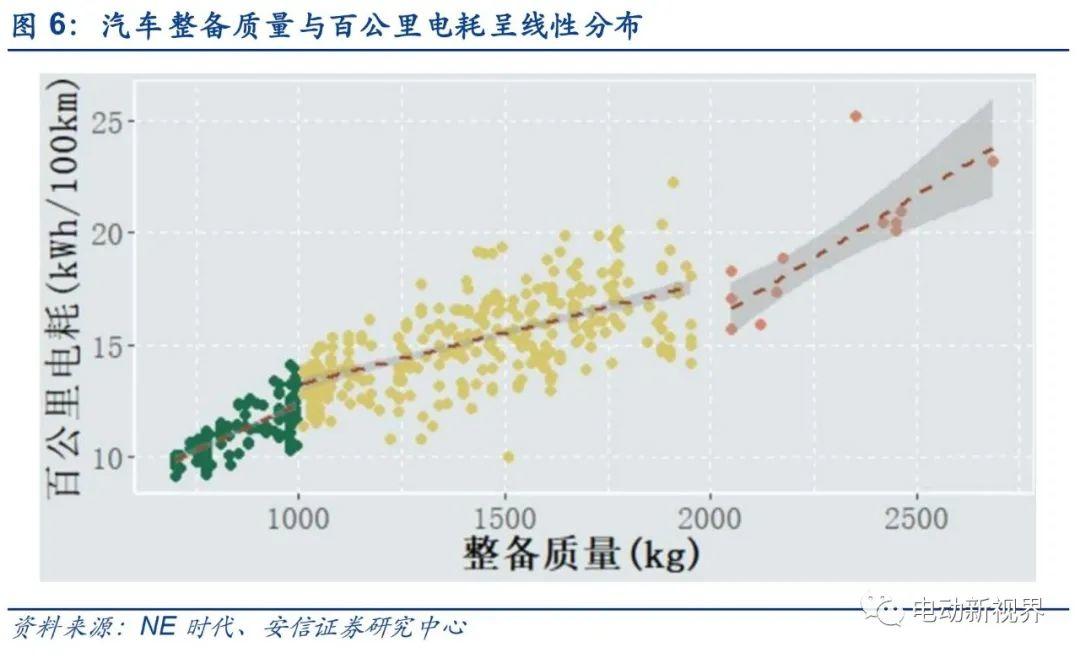
目前来说,新能源汽车轻量化技术主要包括以下三个方面:1)采用轻量化材料,主要包括高强度钢、铝合金、镁合金、高强钢以及碳纤维复合材料、高强度工厂塑料等;2)采用轻量化的制造工艺和连接工艺,一方面在制造工艺上对传统钢材应用热冲压成型、辊压成型等,对铝合金等采用半固态成型、压铸成型等工艺,另一方面采用激光焊接等先进连接工艺,最终达到减少材料用量或零部件数量的目的。3)在结构设计时尽可能考虑轻量化,通过优化车身的空间结构、零部件尺寸形状等减少车身的零部件数量,同时通过新的设计对车身造型及制造进行创新。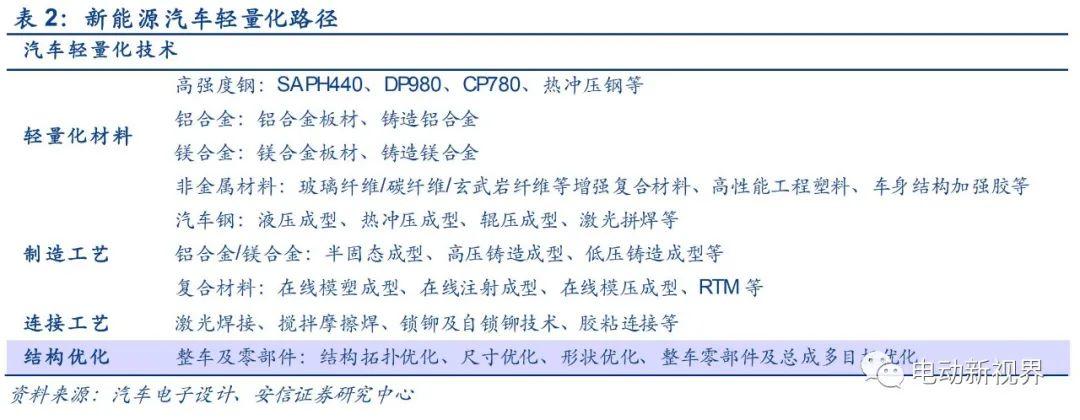
车身轻量化、动力轻量化、底盘轻量化是重点,零部件材料轻量化是落脚点。根据节能与新能源汽车技术路线图规划,国内汽车轻量化的重点包括车身轻量化、动力轻量化以及底盘轻量化、材料轻量化、制作工艺轻量化等。一方面汽车设计和制造工艺门槛高,轻量化成本大,另一方面无论是哪一方面的轻量化,最终都要落脚于轻量化的材料以及零部件上。根据节能与新能源汽车技术路线图规划,到 2030 年,车辆的整备质量要较 2015 年减重 35%,轻量化材料及零部件的使用是重点。
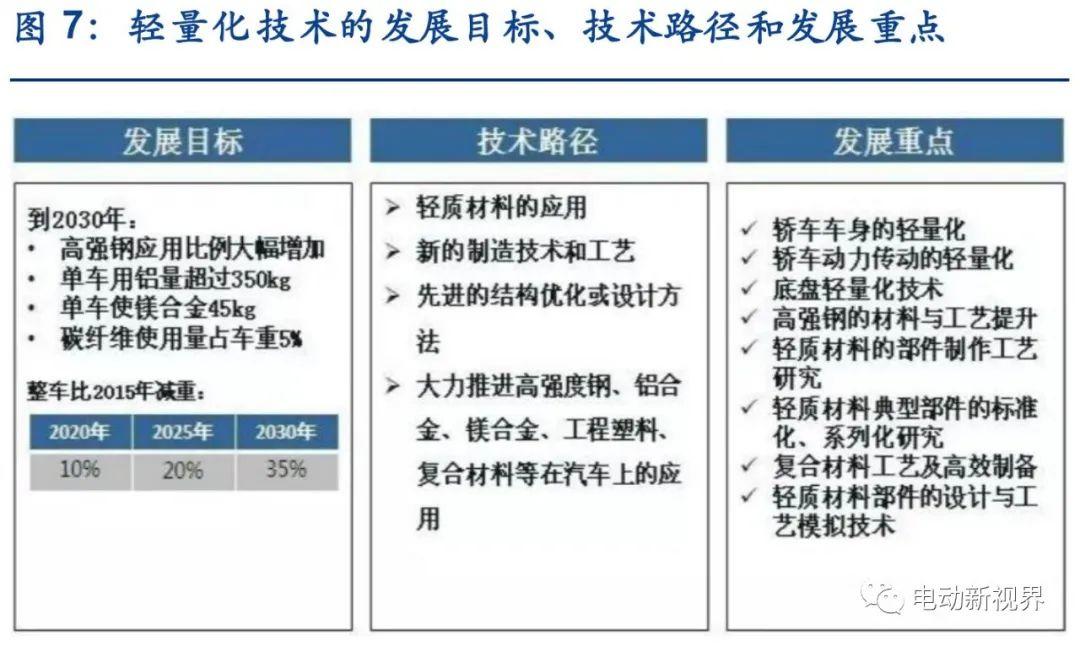
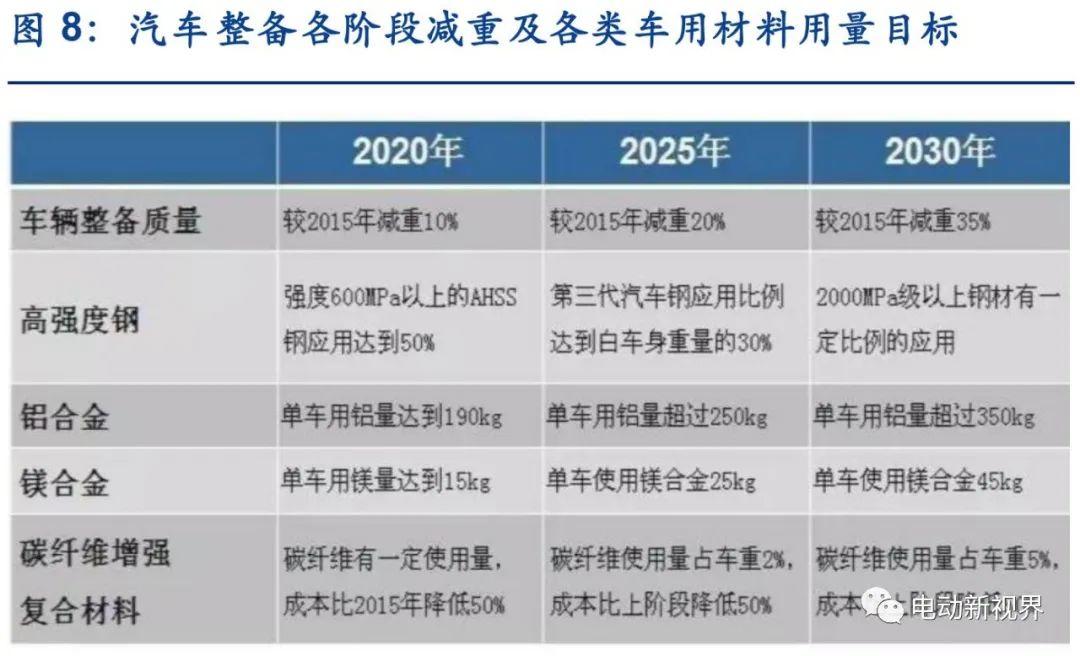
1.3. 为什么关注特斯拉轻量化产业链?
特斯拉作为电动车行业标杆,具有带动示范作用。特斯拉 Model 3 国产化交付后,连着三个月成为销量榜冠军。在 3 月份的市占率高达 13%, 5 月份单月销量破万辆,在国内新能源车市场上一骑绝尘。同时特斯拉作为电动智能汽车行业的标杆,大胆创新,其整车电子电气架构、三电系统、整车 OTA、自动驾驶技术都是各大车企学习追赶的对象。从汽车轻量化的角度看,特斯拉的整车轻量化水平同样居同轴距电动车型的前列。如果能进入特斯拉产业链,则会为相关供应商会带来品牌加成和行业认同,从而为公司发展带来机遇。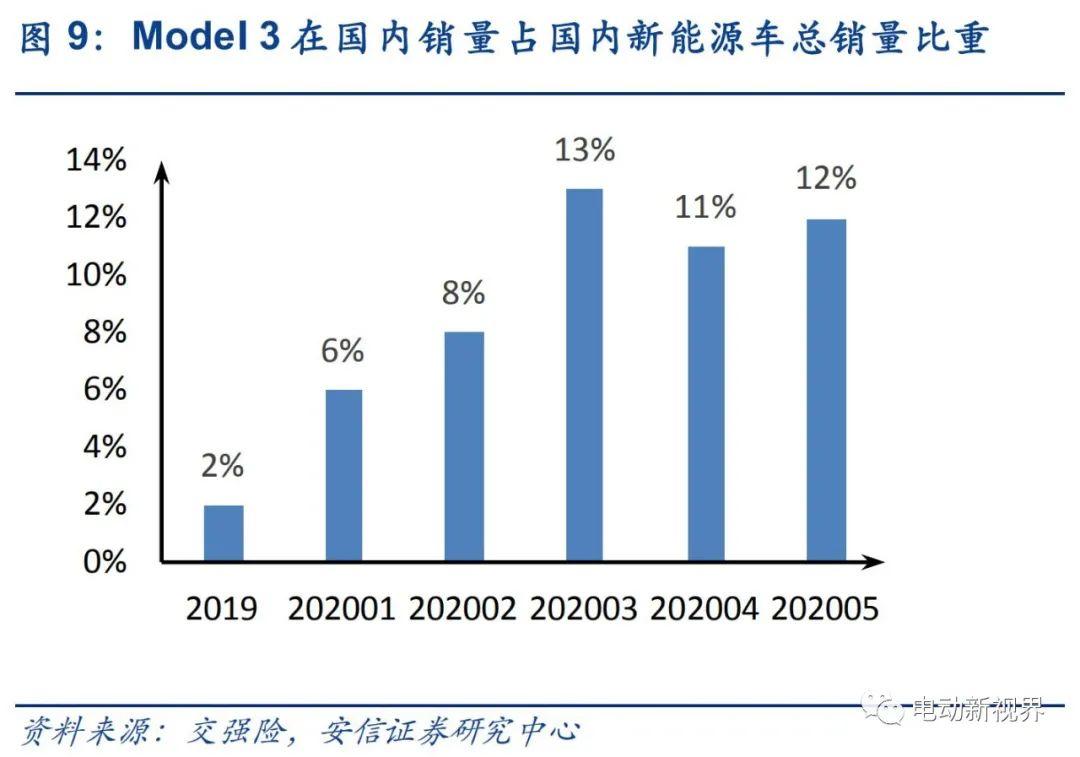
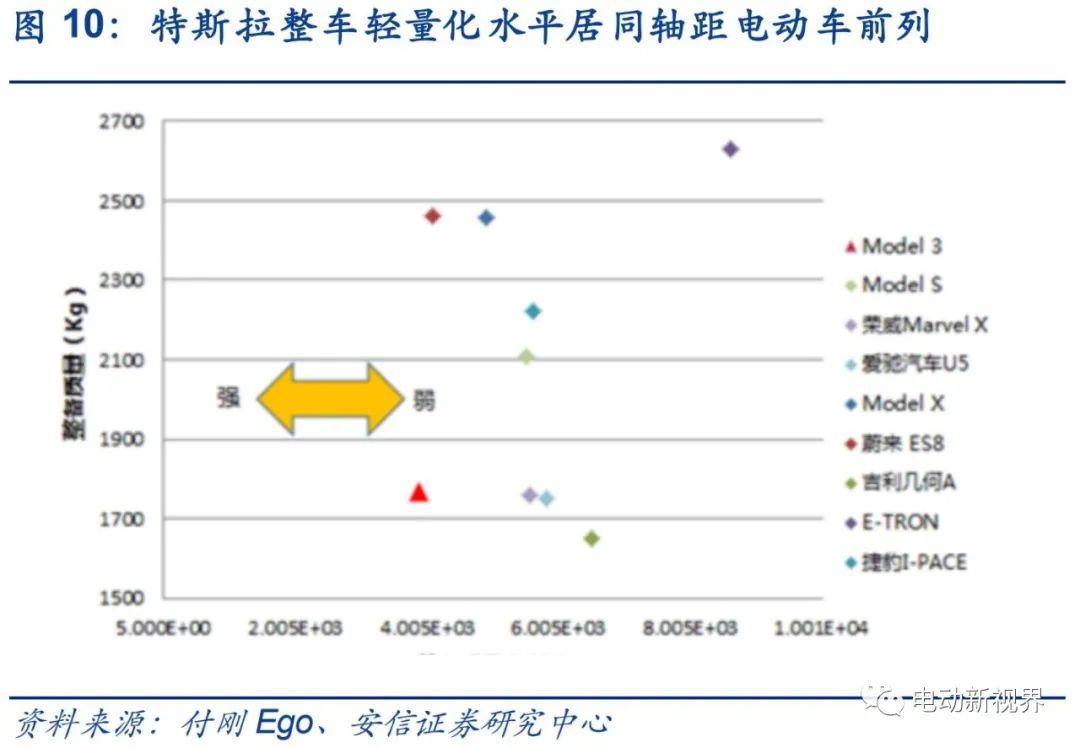
随着产销规模增长,特斯拉有望像苹果一样培养国内产业链以加速降本。2010 年苹果发布颠覆行业的 iPhone4 时,国内还是诺基亚、三星、LG 等国外厂商以及山寨机的天下,国内优质的手机零部件供应链尚未成型。随着苹果进入中国市场以及在中国进行生产后,巨量的订单,培育扶植出一大批国产供应商,如立讯精密、京东方、歌尔股份等,有了上游优质产业链的深厚技术积累后,这些供应商又反哺支持了国内自主品牌智能手机的茁壮成长。作为一个“非典型性”车企,特斯拉无论是从产品体系还是商业模式都越来越像苹果。而目前国内新能源汽车的行业局面也与 10 年前的手机行业颇为类似,随着特斯拉产销的不断提升和传统车企电动车开始发力,其通过国产零部件降本的需求更加迫切,未来有望像苹果一样,带动培养国内产业链发展,进而推动电动车的普及,同时也会培育出一系列优质国产轻量化供应商。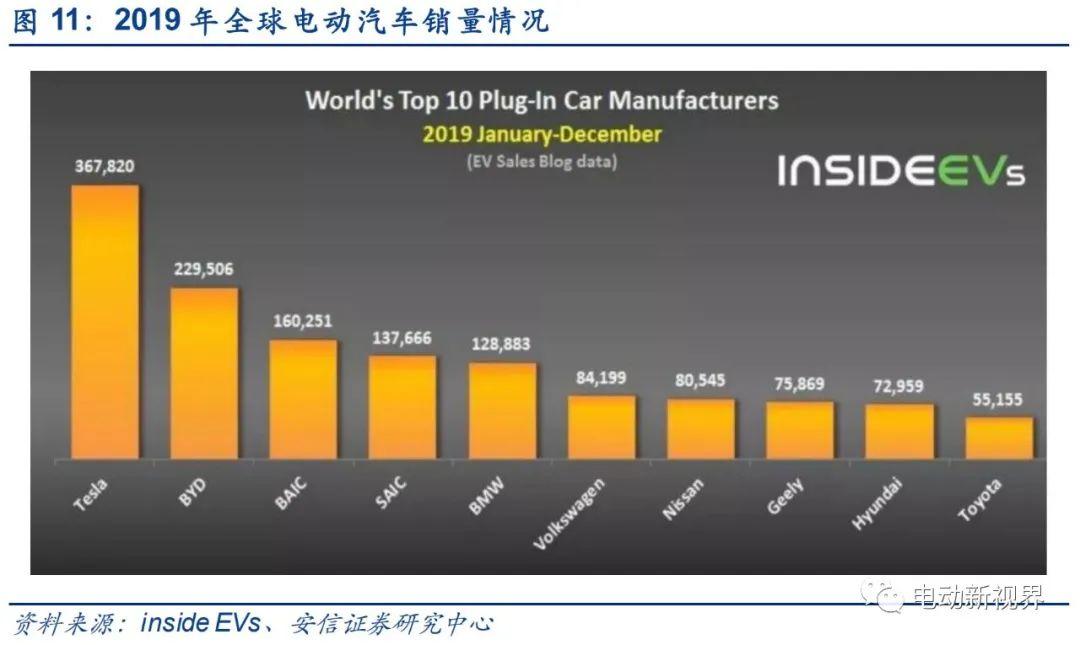
2. 特斯拉轻量化零部件有哪些?
我们以 Model3 为例,从轻量化零部件视角拆解 Model 3。从轻量化层面来看,特斯拉 ModelS 采用了接近全铝的车身底盘,整车轻量化程度十分突出。但一方面,铝合金车身制造工艺复杂,导致成本昂贵。另一方面,Model S 定位高端,并不是走量车型,因此对于国内厂商的借鉴意义有限。而 Model 3 作为一款定位中端的车型,轻量化策略较好的平衡了成本、性能以及安全性,其对轻量化材料/零部件的使用对国内车厂以及零部件供应商具有较强借鉴作用。以长续航版为例,根据博奇发布的数据,Model 3 三电系统、底盘、白车身分别占整车质量的 32.77%、19.79%以及 17.8%。
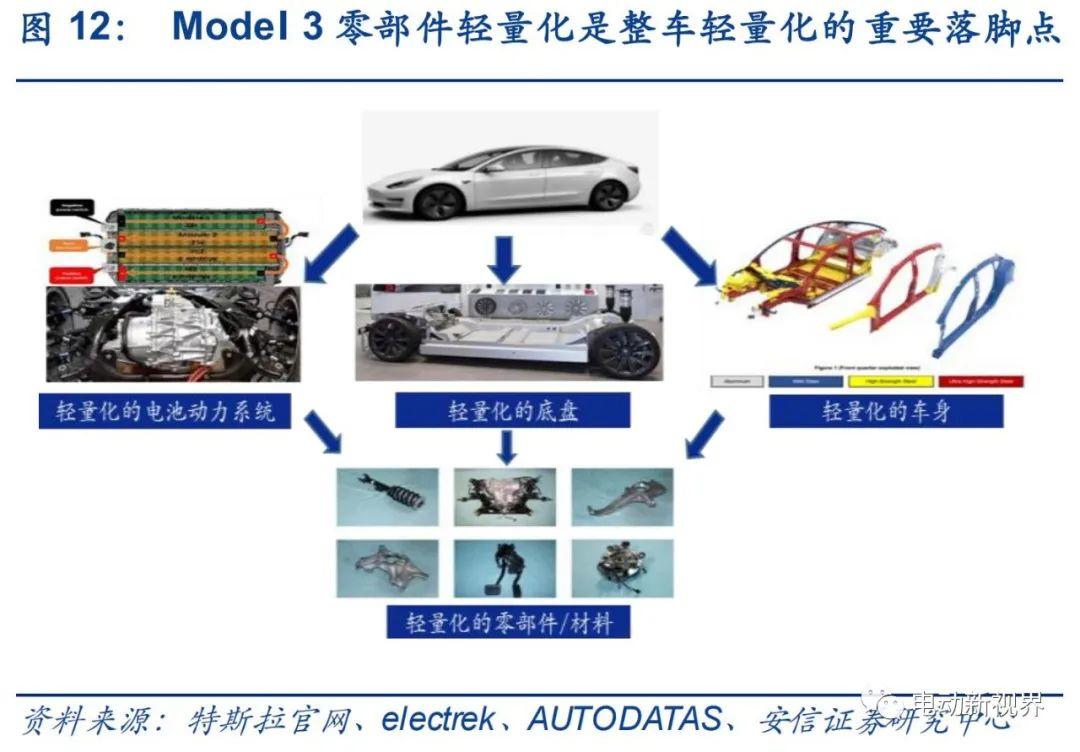
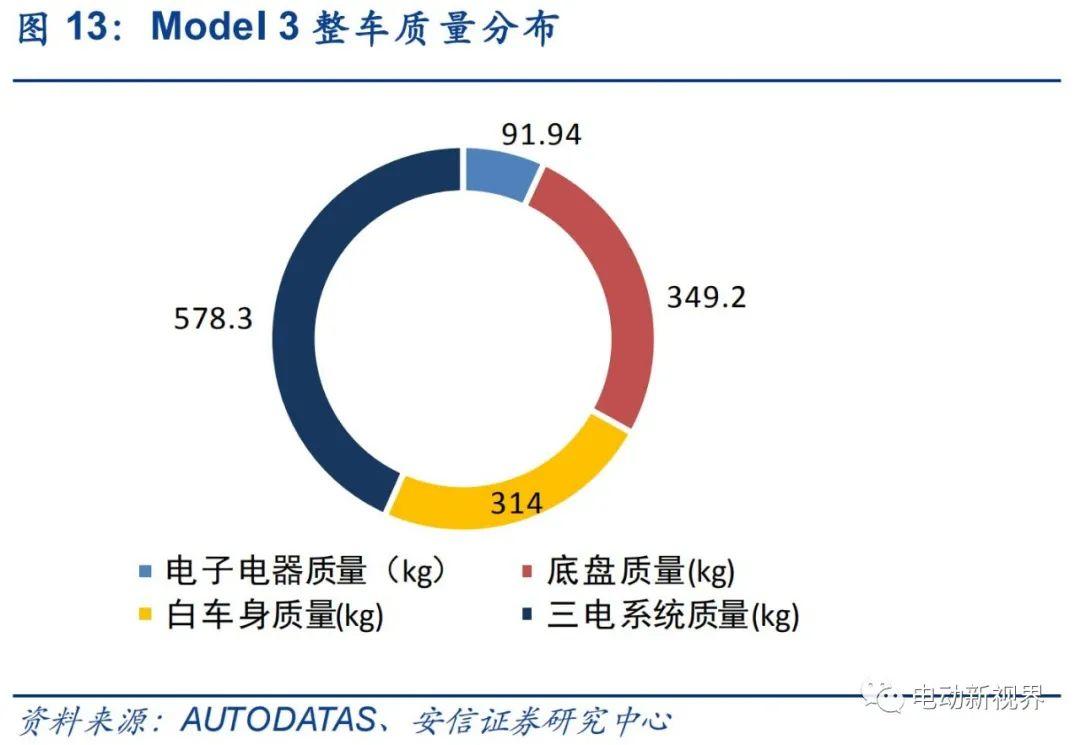
在实现相似电池容量的情况下,Model 3 电池包重量比 Model S 减轻了约 67kg,除了高性能电芯加高集成化的策略外,电池包结构组件的轻量化不容忽视。Model3 长续航版与 ModelS 高性能版的电池带电量基本一致,但 Model 3 长续航版的电池包重量仅有 469.5 公斤,非电池部分重量 169 公斤,而 ModelS 高性能版的电池包重量则达到了 545 公斤,仅电池包上的保护壳就重达 125 公斤。由于车身结构的改进,Model 3 电池包不再需要在底部额外加装类似Model S电池包上的保护壳,电池包的结构组件只需要用来承载电池包自身重量就够了,因此电池结构组件做到了较高的轻量化水平。1)在电池箱体方面,箱体上盖板采用 0.8mm 钢板,箱体底板采用 3.2mm 铝合金,重量只有 29.5kg。BMS 组件上盖板为 1.5mm 铝合金,底座为塑料预埋钣金,电池箱体的总重量仅为 53kg。2)在电池模组结构件上,Model 3 的电池模组主要由 21700 电芯、冷却管以及模组外壳组成。不同于 Model S,Model 3 的电池模组数量减少为四个,同时外壳选择了重量更轻盈的塑料材质。其中,模组上盖板和两边侧板均采用塑料成型件或塑料 2.0,模组底盘采用塑料和 0.8mm 铝合金板材。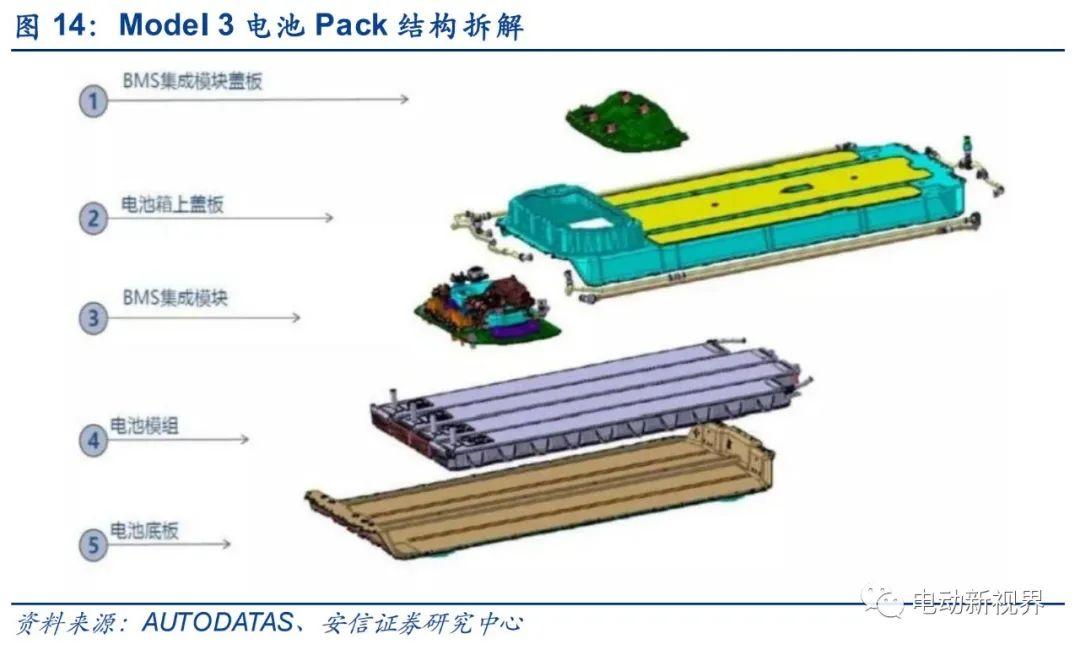
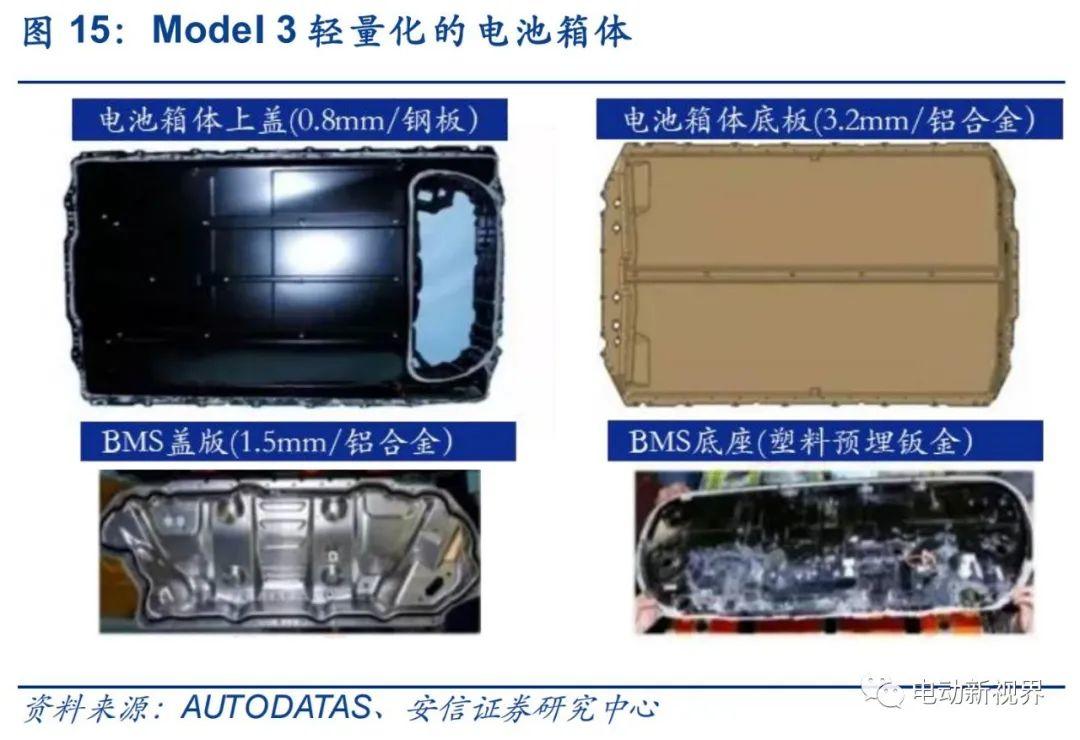
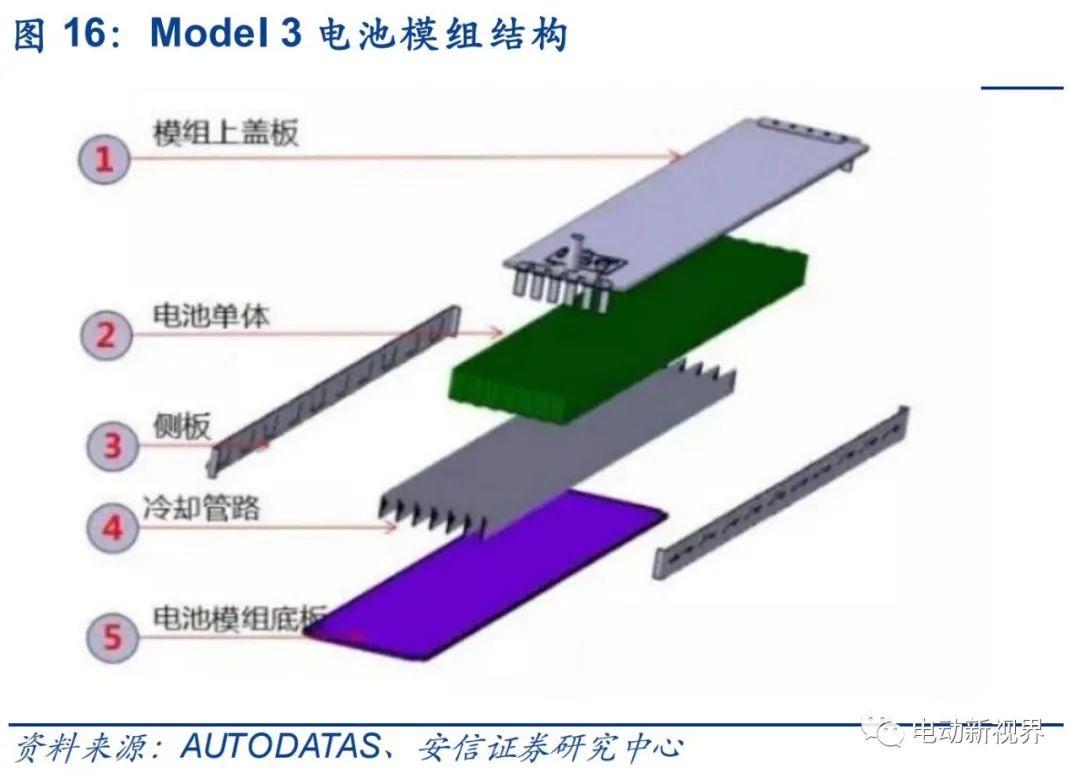
除了电池包结构组件外,Model 3 电机和高压线束也有轻量化。Model 3 通过将电机、电控、减速器进行三合一集成,同时电机壳体和变速箱箱体均采用铝合金材质,进而达到减重目的。随着汽车电动化以及智能化的迅猛发展,线束的轻量化也日益重要。出于轻量化考虑,Model3 的两条高压线束采用了被铜网和铝箔包裹的铝导线。铝和铜的密度比约为 1:3.29,同时铝材比铜材价格低一半。因此在相同体积下,用铝导线代替铜导线可使线束质量减轻三倍,同时大大节约成本。
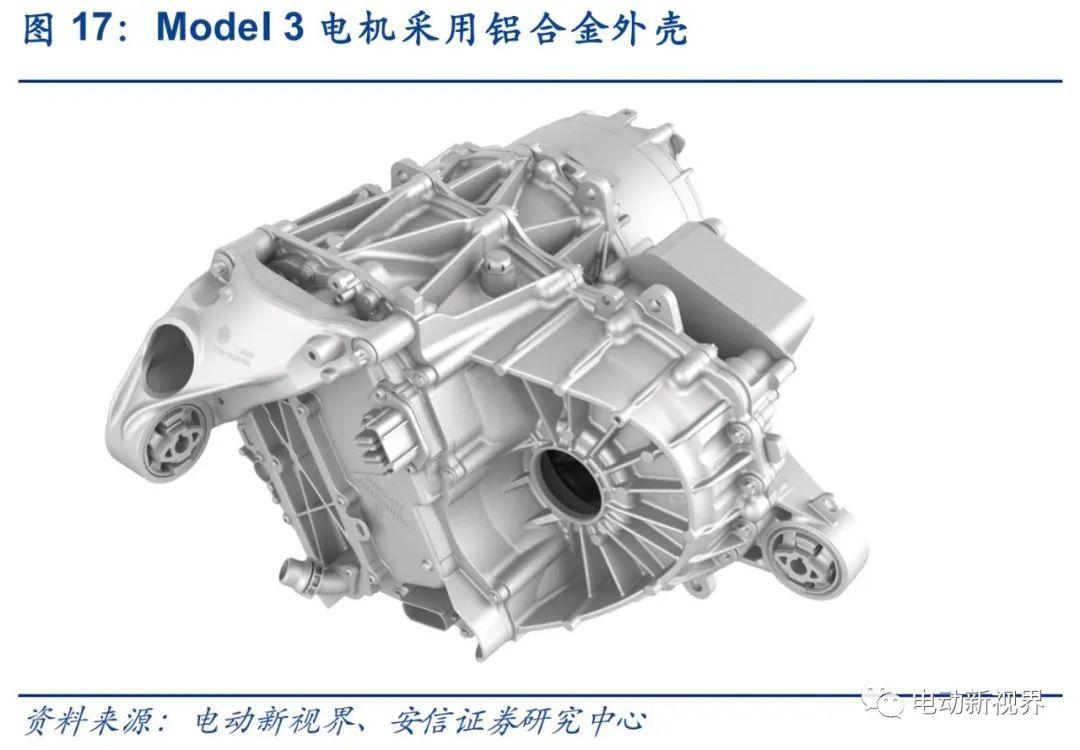
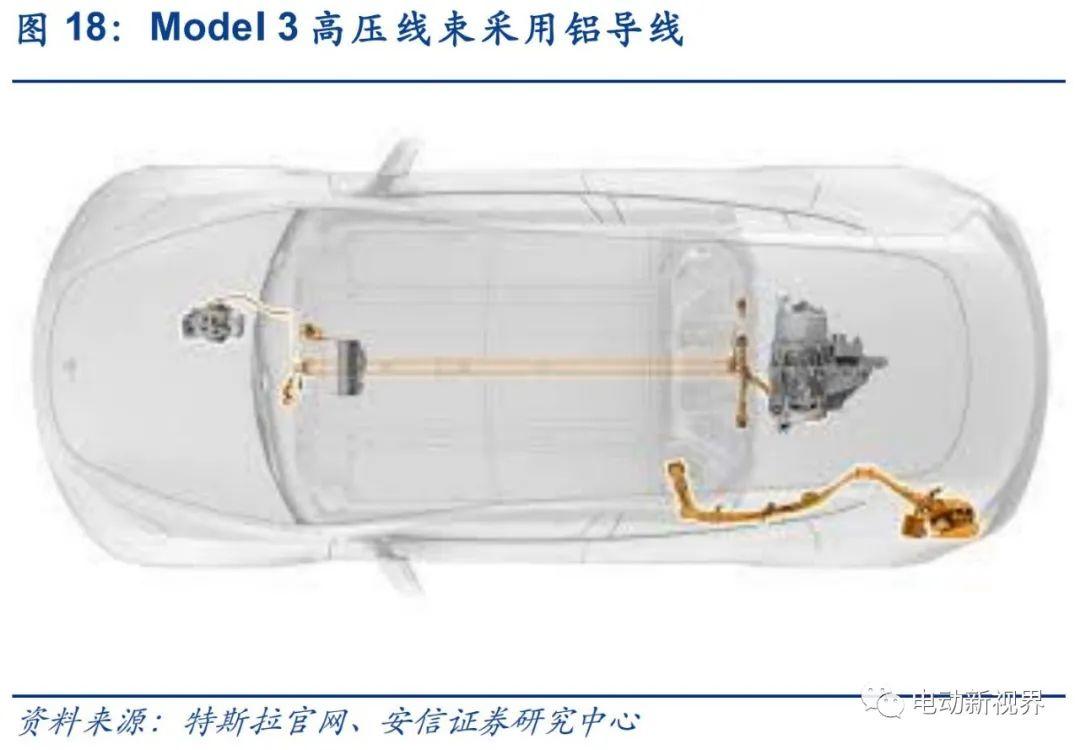
特斯拉并没有像 Model S 一样使用全铝的车身,而是综合考虑了成本、安全以及轻量化等多重目标后,采用了钢铝混合的车身。其中超高强度钢材、高强度钢材以及普通钢材使用量占车身总重 84%,铝合金用量占车身总重的 16%。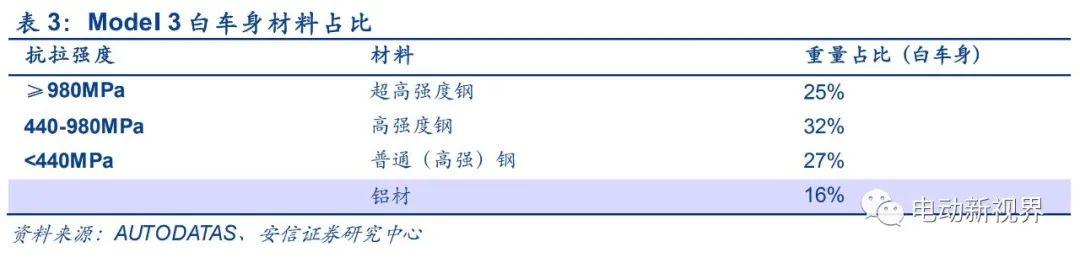
从各材质的分布位臵来看:1)Model 3 前纵梁/A柱/B 柱/后纵梁均采用高强度热冲压钢。如果单纯从轻量化角度来说,铝合金材质无疑是首选材料。但由于高强度钢的高性能、高可塑 性、低成本、制造工艺成熟等优点,Model 3 在其前纵梁/A 柱/B 柱/后纵梁等在碰撞过程需要吸收大量能量的部位采用了高强度热冲压钢材,在保证成本、安全性等因素后,最大限度的实现轻量化。2)车底横梁采用高强度辊压钢。辊压钢相较于冲压钢而言,在生产效率、材料利用率以及轻量化方面更具优势。因此,Model 3 在车底不需要承受高强度碰撞的横梁上采用了辊压钢材,其重量较冲压件可下降 17%以上。3)前后防撞梁/四门前盖/后车底均采用冲压铝材。为了达到车身轻量化的目标, Model 3 将轻质铝引入车身结构中不易受到意外撞击的后车底,同时使用铝合金材质替代了 Model S 上的钢制前后防撞梁。在开闭件上,由于铝板冲压工艺无法完成后行李箱鸭尾造型,因此只有四门前盖采用了铝合金。4)前保险杠支架总成/仪表盘横梁采用塑料或混合材料。与 BMW i3、Bolt 等相比,Model 3 的仪表盘横梁采用了铝镁合金、铝合金、塑料等多种材料,较传统钢材管梁重量可降低 30%-43%左右。除此之外,Model 3 的前端支架采用纤维增强塑料,较钣金材质重量下降 50%以上。
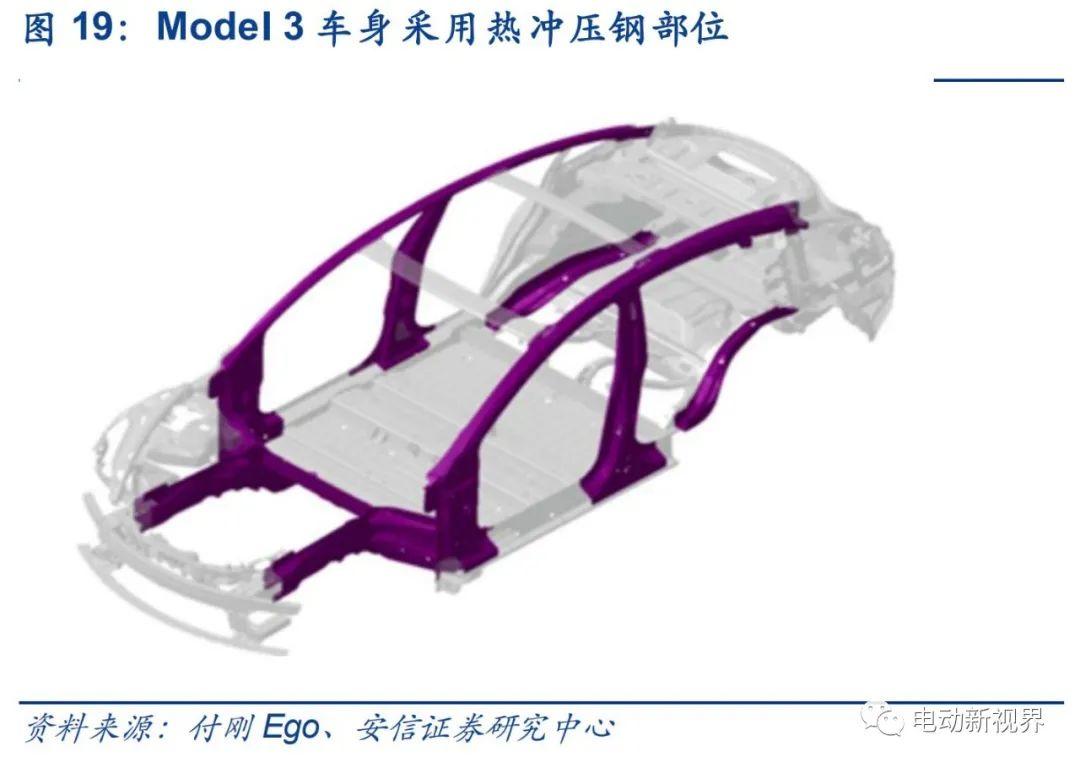
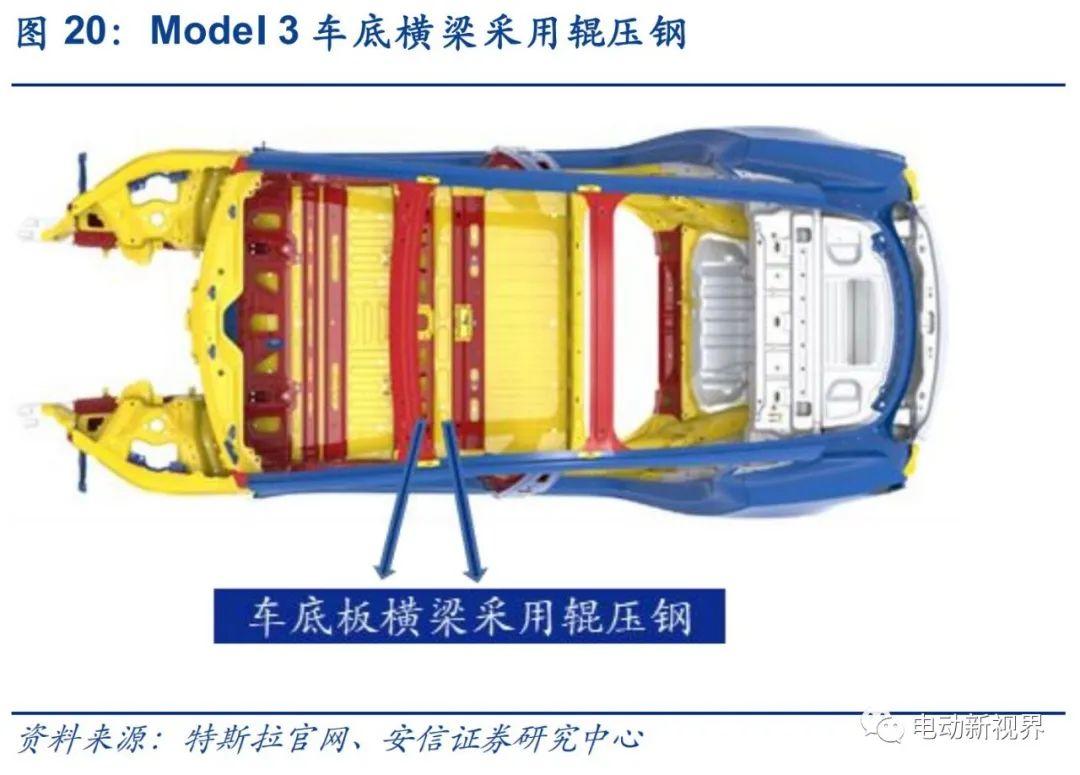
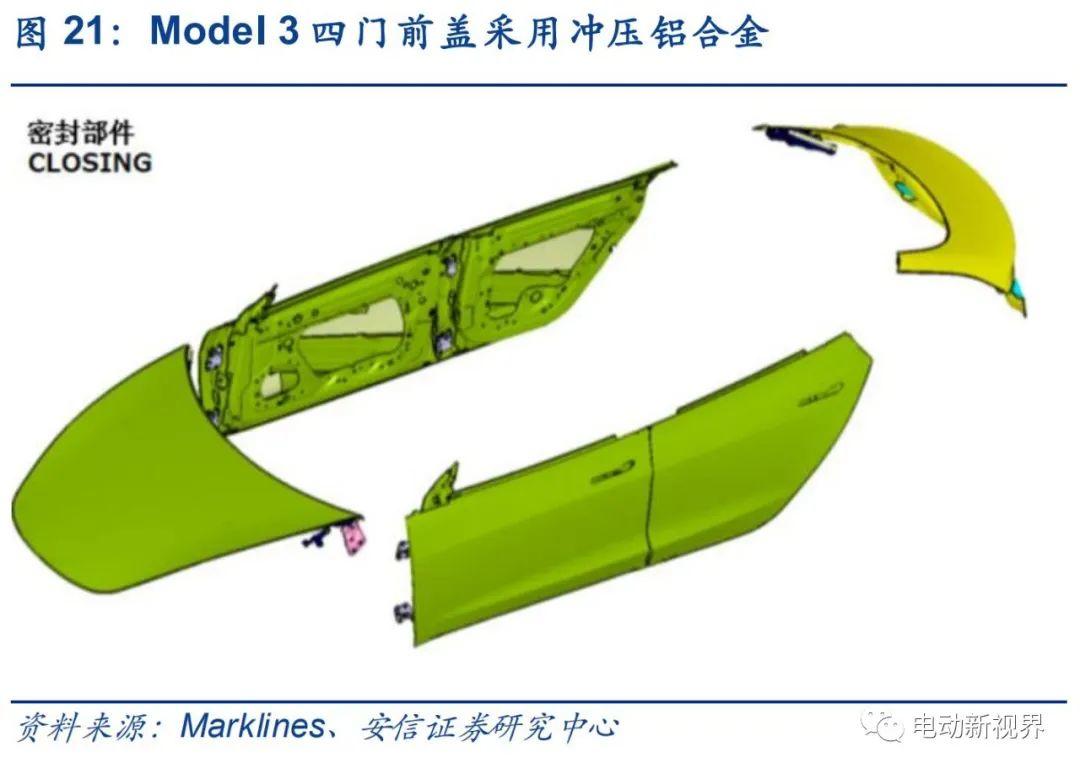
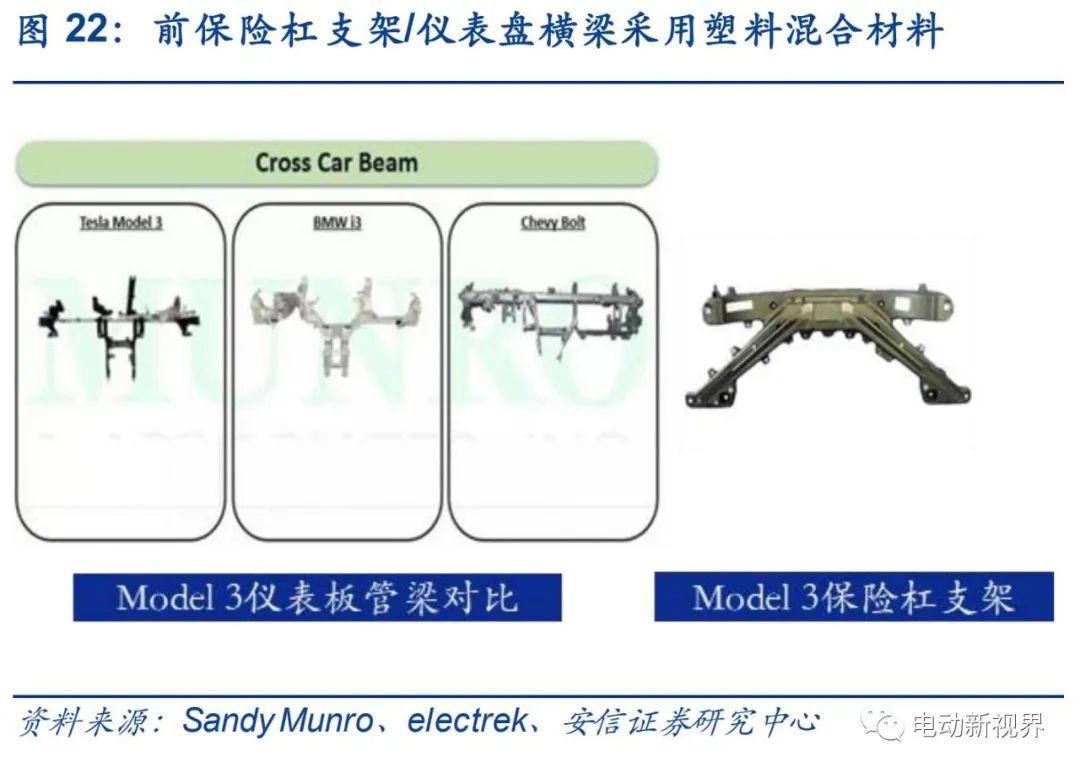
从底盘来看,出于成本等的考虑,Model 3并没有像Model S/X一样大比例使用铝合金材质,但在一些关键部位上,仍然采用了轻量化零部件。1)铝合金控制臂。在汽车悬架系统中,控制臂作为导向和传力元件,负责将车轮上的各种力传递给车身,并保证车轮按一定轨迹运动,决定着轿车的稳定性、舒适性和安全性。Model 3 的前悬下控制臂同特斯拉其他车型一样采用铝合金材质,而前悬的上控制臂则将双层钣金改为单层钣金填充工程塑料,在相同成本下较拼焊方案重量减轻 30%,进一步提升了轻量化程度。2)转向节。转向节承载着汽车所受的各种载荷与力矩,是转向系统中最重要、最精密的零件之一,是保证汽车安全行驶的重要部件,同时也是轻量化的重要方向。因转向节前后构造及受力需求不同,Model 3 的前后转向节分别采用锻造铝合金件和铸造铝合金件来达到轻量化目的。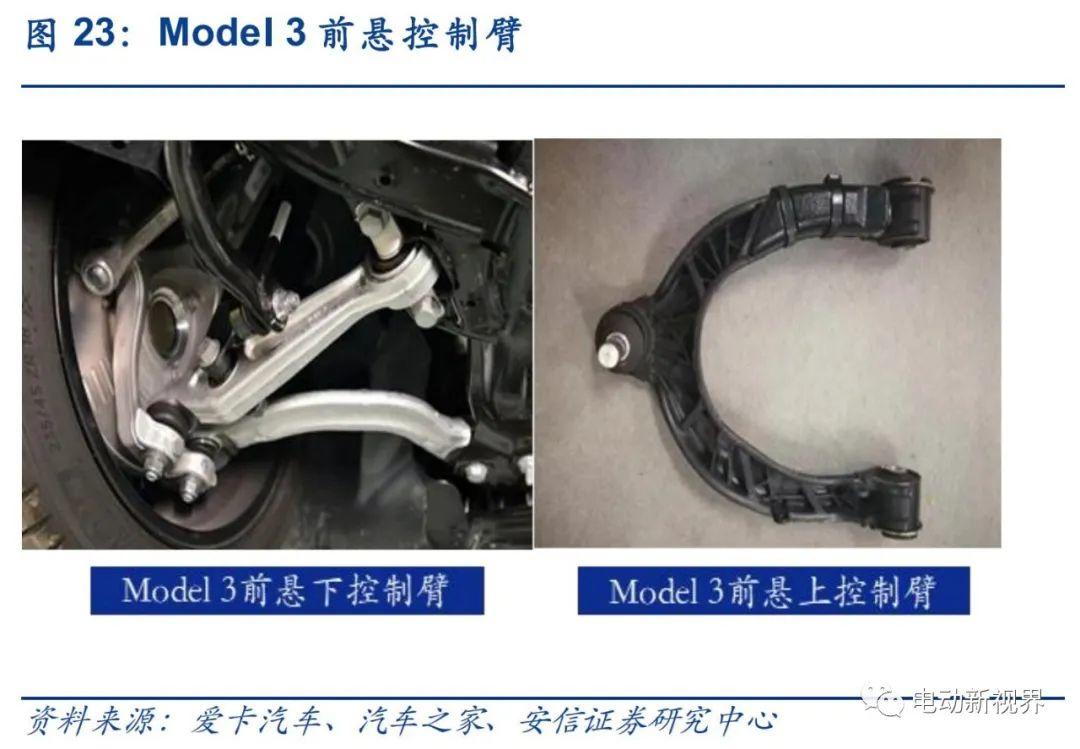
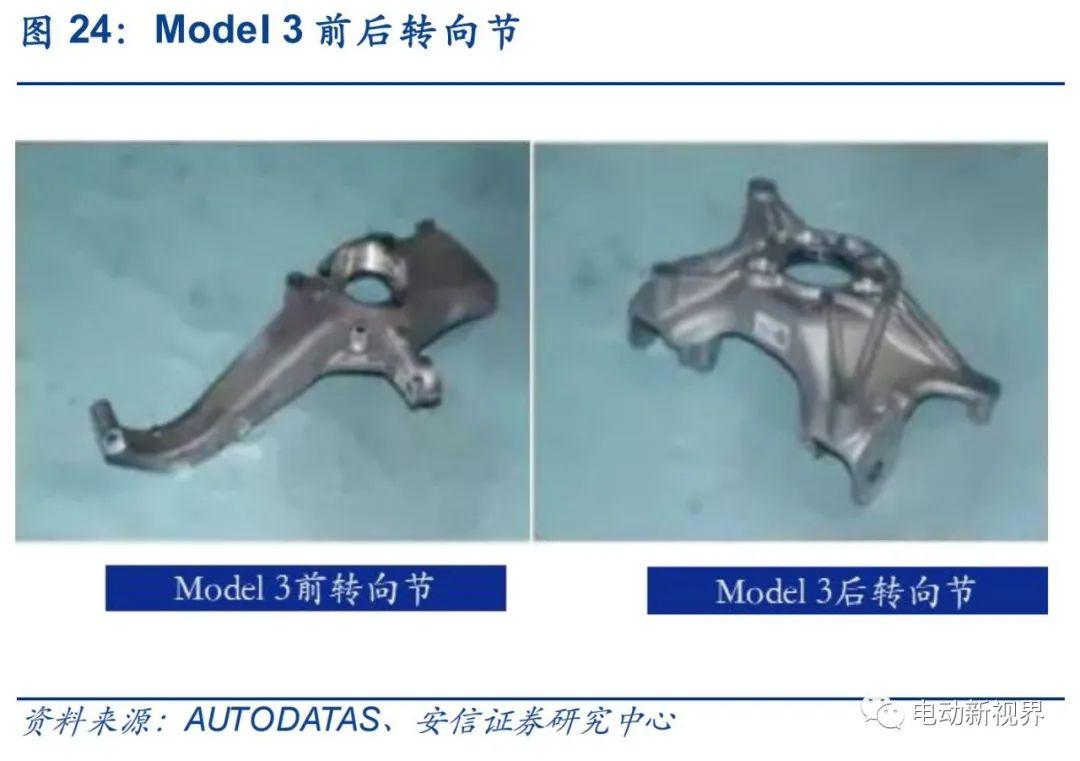
特斯拉的轻量化技术的广泛应用,使得该公司在降本增效方面取得了巨大的成功,最新上市的MODEL Y更是最高降价16.5万,震惊整个汽车行业,被誉为价格屠夫。师夷长技以制夷,虚心学习成功者的经验,才能让我们的汽车行业掌握核心科技,健康的成长壮大。